Official Program
Total Page:16
File Type:pdf, Size:1020Kb
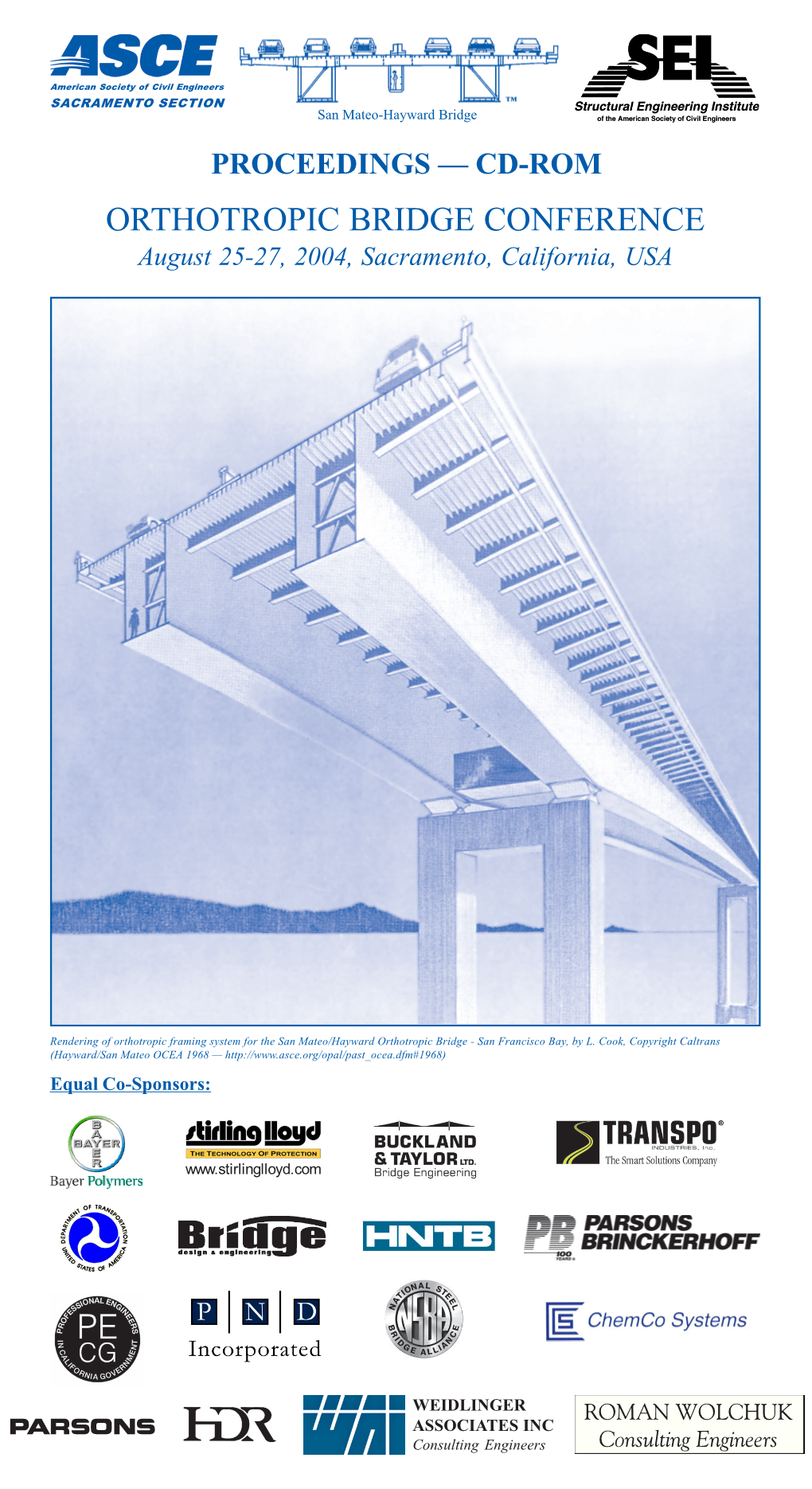
Load more
Recommended publications
-
Urgently for Publication (Procurement Procedures) Annoucements Of
Bulletin No�4 (183) January 28, 2014 Urgently for publication Annoucements of conducting (procurement procedures) procurement procedures 001143 000833 Luhansk National Agrarian University SOE “Prydniprovska Railway” 91008 Luhansk, Luhansk National Agrarian University 108 Karla Marksa Ave., 49600 Dnipropetrovsk Yevsiukova Liudmyla Semenivna, Bublyk Maryna Borysivna Ivanchak Serhii Volodymyrovych tel.: (095) 532–41–16; tel.: (056) 793–05–28; tel./fax: (0642) 96–77–64; tel./fax: (056) 793–00–41 e–mail: [email protected] Website of the Authorized agency which contains information on procurement: Website of the Authorized agency which contains information on procurement: www.tender.me.gov.ua www.tender.me.gov.ua Website which contains additional information on procurement: www. tender. uz.gov.ua Website which contains additional information on procurement: www.lnau.lg.ua Procurement subject: code 33.17.1 – repair and maintenance of other Procurement subject: code 06.20.1 – natural gas, liquefied or in a gaseous vehicles and equipment (services in modernization of machine ВПР–02 state (gas exclusively for production of heat energy which is consumed with conducting major repair) – 1 unit by budget institutions and organizations), 1327,0 thousand m3 Supply/execution: on the territory of the winner of the bids; during 10 months from Supply/execution: at the customer’s address; till 31.12.2014 the moment of signing the act of delivery of track machine to modernization with Procurement procedure: procurement from the sole participant repair, but -
Modernization of Pedagogical Higher Education by Innovative Teaching Instruments
MODERNIZATION OF PEDAGOGICAL HIGHER EDUCATION BY INNOVATIVE TEACHING INSTRUMENTS Seminar on the implementation of tasks of the 1st package. June 11-12, 2018 About Kyiv There are many ancient and modern sights in Kyiv. Historical centers and districts of Kyiv tell us about the city’s distant past. Buildings in Kyiv - living witnesses of the flow of time and events of the present. Numerous monasteries and temples of the City decorate it and create an atmosphere of purity and holiness. There are many monuments that have become a kind of architectural landmarks of the capital. Due to the large number of parks and green areas, the image of Kyiv is so unique. Streets and squares of Kyiv remember the joy and sad moments in the history of our city. The diversity of Kyiv monuments does not stop to amaze and admire. All of this – identity of the Kyiv, which makes it so unique and loved among Ukrainians and tourists. More than 70 parks and 200 gardens are located on the territory of Kyiv, making our capital one of the greenest cities in Europe and even around the world. Kyiv is a city with an extraordinary atmosphere. This is the city where we fall in love and in which we fall in love. If you were born and live here - you are probably the patriot of the capital of Ukraine. And if you come here as a tourist – if You visiting Kyiv once, you’ll want to come back here again and again! How to get to the city / from the airport / train station From the Airport By Sky Bus You can get Sky Bus from the International airport "Boryspil" to Kyiv (via Kharkivska metro station to the Central Railway Station, South Terminal). -
The Ukrainian Weekly, 2021
Part 3 of THE YEAR IN REVIEW pages 7-13 THE UKRAINIAN WEEKLY Published by the Ukrainian National Association Inc., a fraternal non-profit association Vol. LXXXIX No. 5 THE UKRAINIAN WEEKLY SUNDAY, JANUARY 31, 2021 $2.00 Ukraine celebrates Unity Day Ukraine’s SBU suspects former agency colonel of plotting to murder one of its generals by Mark Raczkiewycz KYIV – On January 27, the Security Service of Ukraine (SBU) said it had secured an arrest warrant for Dmytro Neskoromnyi, a former first deputy head of the agency, on suspicion of conspiring to murder a serving SBU general. Mr. Neskoromnyi, a former SBU colonel, allegedly plotted the assassination with currently serving Col. Yuriy Rasiuk of the SBU’s Alpha anti-terrorist unit. The alleged target was 38-year-old Brig. Gen. Andriy Naumov. Mr. Naumov heads the agency’s internal security department, which is responsible for preventing corruption among the SBU’s ranks. RFE/RL In a news release, the SBU provided video RFE/RL A human chain on January 22 links people along the Paton Bridge in Kyiv over the and audio recordings, as well as pictures, as Security Service of Ukraine Brig. Gen. Dnipro River that bisects the Ukrainian capital, symbolizing both sides uniting when evidence of the alleged plot. The former col- Andriy Naumov the Ukrainian National Republic was formed in 1919. onel was allegedly in the process of paying “If there is a crime, we must act on it. $50,000 for carrying out the murder plot. by Roman Tymotsko (UPR), Mykhailo Hrushevskyy. And, in this case, the SBU worked to pre- Mr. -
The Ukrainian Weekly 2012, No.39
www.ukrweekly.com INSIDE: l Russia’s “soft power with an iron fist” – page 3 l The Ukrainian minority in Poland, 1944-1947 – page 9 l Tennis championships at Soyuzivka – page 11 THEPublished U by theKRAINIAN Ukrainian National Association Inc., a fraternal W non-profit associationEEKLY Vol. LXXX No. 39 THE UKRAINIAN WEEKLY SUNDAY, SEPTEMBER 23, 2012 $1/$2 in Ukraine Foreign Relations Ukraine’s 2012 parliamentary elections: Committee approves Two parties that might make the cut Tymoshenko resolution by Zenon Zawada Special to The Ukrainian Weekly WASHINGTON – A resolution intro- duced by U.S. Sen. Jim Inhofe (R-Okla.), a KYIV – Polls indicate that at least four member of the Senate Foreign Relations political parties will qualify for the 2012 Committee, and co-sponsored by U.S. Verkhovna Rada. Another two parties have Sen. Dick Durbin (D-Ill.), Senate majori- a chance of surpassing the 5 percent ty whip, on September 19 unanimously threshold on election day, October 28: the passed the Senate Foreign Relations Ukraine – Forward! party launched by Luhansk oligarch Natalia Korolevska and Committee. The resolution, S. Res. 466, the Svoboda nationalist party launched by calls for the unconditional release of Oleh Tiahnybok. political prisoner and former Ukrainian At the moment, however, both parties Prime Minister Yulia Tymoshenko. would fail to qualify. Ukraine – Forward! “Tymoshenko was a key revolution- would earn 4 percent of the votes for ary in Ukraine’s 2004 Orange closed party lists, while Svoboda would get Revolution and is a pro-Western reform- about 3.8 percent, according to a poll er,” said Sen. -
The Ukrainian Weekly 2003, No.14
www.ukrweekly.com INSIDE:• Kyiv library holds largest collection of children’s publications — page 3. • Ukrainians active at session of U.N.’s commission on women — page 5. • Taras Shevchenko and his neighbors in Washington — page 15. Published by the Ukrainian National Association Inc., a fraternal non-profit association Vol. LXXI HE KRAINIANNo. 14 THE UKRAINIAN WEEKLY SUNDAY, APRIL 6, 2003 EEKLY$1/$2 in Ukraine Controversy arises over whether battalion, TDemographer advisesU Ukrainian groups W to take a close look at U.S. Census stats and Ukraine, are part of U.S.-led coalition by Roman Woronowycz it could enter the area of conflict. by Andrew Nynka mated that only 116,000 speak Ukrainian Kyiv Press Bureau Petro Symonenko, the head of the at home. Communist Party, said that President KERHONKSON, N.Y. – A closer KYIV – The Communist parliamentary Bush’s enumeration of Ukraine as part of “We’re missing out,” Dr. Wolowyna faction introduced a draft bill in the look at U.S. Census data shows that said, referring to those organizations that the coalition is evidence that Ukrainian Verkhovna Rada on April 2 ordering the many Ukrainian organizations could be require their members to speak Ukrainian authorities had deceived the nation and had recall of the Ukainian army’s special con- ignoring hundreds of thousands of self- or look down on members who don’t use more on their mind than simply a peace- tamination clean-up battalion currently declared Ukrainians living in the United that language. Some 777,000 self- keeping effort. States, a specialist in the field of demo- declared Ukrainians, or roughly 87 per- being deployed to Kuwait. -
Of the Public Purchasing Announcernº26(100) June 26, 2012
Bulletin ISSN: 2078–5178 of the public purchasing AnnouncerNº26(100) June 26, 2012 Announcements of conducting procurement procedures � � � � � � � � � 2 Announcements of procurement procedures results � � � � � � � � � � � � 59 Urgently for publication � � � � � � � � � � � � � � � � � � � � � � � � � � � � � � � � � � 123 Bulletin No�26(100) June 26, 2012 Annoucements of conducting 14411 Public Joint–Stock Company “Chornomornaftogaz” procurement procedures 52/1 Kirova Ave./Sovnarkomovskyi Lane, 95000 Simferopol, the Autonomous Republic of Crimea Kudik Volodymyr Valeriiovych, Terenia Viktor Moiseiovych, Savchenko Oksana 14377 Main Health Care Department of Donetsk Oblast Volodymyrivna State Administration tel.: (0652) 52–37–92, (06558) 9–70–47, 9–70–40 34 Pushkina Blvd., 83105 Donetsk, Donetsk Oblast Website of the Authorized agency which contains information on procurement: Hrachkova Alla Viktorivna www.tender.me.gov.ua tel./fax: (062) 334–25–67; Procurement subject: code 35.11.9 – repair and maintenance services, e–mail: [email protected] modernization and dismantling of vessels, platforms and jack–up drilling Website of the Authorized agency which contains information on procurement: rigs” (maintenance of tug/supply vessel “DON”) www.tender.me.gov.ua Supply/execution: drilling and developing base of exploration and exploitation Website which contains additional information on procurement: drilling department of the National Joint Stock Company “Chornomornaftogaz”: www.donzdrav.gov.ua the Autonomous Republic of Crimea, Chornomorskiy -
Ukraine's Foreign Affairs Minister Has High Praise for Constructive Atmosphere in Relations with U.S
INSIDE:• UCCA, UCC to send election observers to Ukraine — page 3. • $25,000 literary award is presented — page 12. • New exhibit focuses on life in the Chornobyl zone — page 13. Published by the Ukrainian National Association Inc., a fraternal non-profit association Vol. LXXIV HE KRAINIANNo. 12 THE UKRAINIAN WEEKLY SUNDAY, MARCH 19, 2006 EEKLY$1/$2 in Ukraine Ukraine’s foreign affairs minister has high praise T U YushchenkoW denounces negative tone for constructive atmosphere in relations with U.S. of Party of the Regions campaign by Yaro Bihun Economy Minister Arsenii Yatseniuk, by Zenon Zawada recognized as a free market economy by Special to The Ukrainian Weekly sign a bilateral World Trade Organization Kyiv Press Bureau the United States and the European accession agreement here on Tuesday, Union,” the president said. “Had that WASHINGTON – “I cannot recall March 7, the U.S. House of KYIV – President Viktor Yushchenko existed before?” such an exceptionally constructive and Representatives vote to free Ukraine criticized the negative tone of the Party The U.S. Congress’s recent moves to of the Regions election campaign, stating positive atmosphere in our relations.” from the economic shackles of the graduate Ukraine from the Jackson- that the party lacks an agenda that can That was how Foreign Affairs Minister Jackson-Vanik Amendment on Vanik Amendment will allow for exports intellectually compete with the govern- Borys Tarasyuk, who says that in one way Wednesday, March 8, and the Senate pas- to grow by $200 million, Mr. ment’s program. or another he has been involved in sage of the House version of that legisla- Yushchenko said. -
Aerospace Now and the Future
Participating Organizations: Foreign Affairs and International Trade Canada “Arsenal” Central Design Office, State Enterprise Crimean Astrophysical Observatory G.V. Kurdyumov Institute for Metal Physics Department of the High Temperature Thermogas-dynamics Institute of Engineering Thermophysics Institute of Geological Sciences “Scientific Centre for Aerospace Research of the Earth”, State Enterprise V. M. Glushkov Institute of Cybernetics Institute of Hydro-Mechanics Institute of Physics Lashkaryov Institute of Semiconductor Physics Institute of Technical Mechanics Instrument-Making Research Technological Institute, State Enterprise Karpenko Physico-Mechanical Institute Kharkiv State Aircraft Manufacturing Company “Khartron”, Joint Stock Company “Kommunar Association” State Research and Production Company “Kyivprylad“ Production Association, State Enterprise Lviv Center of NASU-NSAU Institute for Space Research National Aerospace University “Kharkiv Aviation Institute” named by N.Ye.Zhukovskiy National Aviation University National Space Facilities Control and Test Center National Youth Aerospace Education Center “PRYRODA" State Research and Production Center “Radio Measurement Research Institute”, Joint Stock Company Space Research Institute “TechResource-Motors”, R&D Enterprise “Ukrainian Scientific Research Institute of Manufacturing Engineering”, Public Joint Stock Company O. Makarov Yuzhny Machine-Building Plant Production Association (YUZHMASH) “Ukrkosmos”, State Enterprise “Yuzhnoye” State Design Office, State Enterprise INSTITUTIONAL -
IRF Annual Report for 2009
International Renaissance Foundation Black 2009 Annual Report P349, ABOUT THE INTERNATIONAL RENAISSANCE FOUNDATION he International Renaissance Foundation (IRF) is an integral part of the Open Society Institute network (established by American philanthropist George Soros) that incorporates national and regional foundations in more than thirty countries around the world, including Africa, Central and Eastern Europe and the former TSoviet Union. IRF was founded in 1990. The mission of the International Renaissance Foundation – is to promote open democratic society in Ukraine Black by providing financial and organizational support for important civil society initiatives. IRF remains one of the largest donor foundations in Ukraine, supporting civil society organizations working in areas that are part of the Foundation’s priorities. Every year, IRF provides up to $7 million in support to NGOs P349, in different regions of Ukraine. In addition to offering grants to other organizations, IRF also pursues its own (operational) activities, implementing projects in its target sectors that are also selected by public representatives. The Foundation is also well-known as an expert organization, initiator of effective projects, open discussions and catalyst of social change. Openness and transparency of donor activities, and conformity with the needs of society are the main principles that guide the work of the International Renaissance Foundation. The public is involved in the distribution of Foundation funds for the needs of building a democratic open society through participation in the Executive Board and IRF Program Boards. IRF distributes the majority of its grants to non-governmental organizations after open competitions are held for projects pursuing the program priorities set by leading representatives of local civil society The IRF Board is the main public body that forms the strategy for the entire organization. -
Of the Public Purchasing Announcernº4(78) January 24, 2012
Bulletin ISSN: 2078–5178 of the public purchasing AnnouncerNº4(78) January 24, 2012 Announcements of conducting procurement procedures � � � � � � � � � 2 Announcements of procurement procedures results � � � � � � � � � � � � 70 Urgently for publication � � � � � � � � � � � � � � � � � � � � � � � � � � � � � � � � � � 124 Bulletin No�4(78) January 24, 2012 Annoucements of conducting 01500 Subsidiary Company “Naftogazservice”, procurement procedures NJSC “Naftogaz Ukrainy” 2 Lunacharskoho St., 02002 Kyiv tel.: (067) 444–69–72; 01498 Subsidiary Company “Naftogazservice”, tel./fax: (044) 531–12–57; NJSC “Naftogaz Ukrainy” e–mail: [email protected] 2 Lunacharskoho St., 02002 Kyiv Website of the Authorized agency which contains information on procurement: tel.: (067) 444–69–72; www.tender.me.gov.ua tel./fax: (044) 531–12–57; Procurement subject: code 50.30.2 – services in retail trade of parts e–mail: [email protected] and equipment for cars, 2 lots Website of the Authorized agency which contains information on procurement: Supply/execution: at the customer’s address; during 2012 www.tender.me.gov.ua Procurement procedure: open tender Procurement subject: code 50.20.1 – services in maintenance and repair Obtaining of competitive bidding documents: at the customer’s address, reception of passenger cars, 6 lots room Supply/execution: Kyiv and Kyiv Oblast, during 2012 Submission: at the customer’s address, reception room Procurement procedure: open tender 20.12.2011 09:30 Obtaining of competitive bidding documents: at the customer’s -
Ukrainian Is Losing Ukrainian Energy Supplies 6 Language Schools 14 Viewers 44 Ukrainian International Monthly Edition Week №2 (14) February 2011
NLG TERMINAL PAGE DONETSK PARENTS PAGE WHY BOOB TUBE PAGE COULD DIVERSIFY DO BATTLE FOR UKRAINIAN IS LOSING UKRAINIAN ENERGY SUPPLIES 6 LANGUAGE SCHOOLS 14 VIEWERS 44 Ukrainian international monthly edition Week №2 (14) FEBRUARY 2011 www.tyzhden.ua featuring selected content from the economist for free distribution currenT affairs|contentS Trends & Talk The main chance Terminal stumbling block Ukraine’s Government is using the Events, Quotes, The Three-Martini Launch idea of a liquid gas terminal as a Numbers Building an NLG terminal in Ukraine could be a move to powerful geopolitical card— diversifying gas suppliers—or one that it may not have the 4 just a waste of taxpayer money 6 courage to play 9 ideologues Ethnic Parents to the cleansing, Barricades Ideological Splits then and Donetsk officials are The ruling party now eager to close down could be facing a Ukrainian schools even if showdown between they are 95% filled with its pragmatic and students. But parents pro-Russian wings are fighting back 10 12 14 Crooked In a Captious Land Demobilization 2011 Lawmaking Kyiv’s policy towards A massive layoff of officers A “minor” the Crimean Tatars could leave Ukraine’s army violation of the remains controversial weaker and its police more Constitution grows and inconsistent corrupt into a scandal with criminal undertones 16 18 22 If not NATO, then Russia? Mr. Yanukovych goes to among The pols The ability of the public purse to Washington pay for defense is just one of the The Yanukovych Administra Learning Democracy tests of its “non-aligned” status tion’s image in the West is German historian Frank that Kyiv is failing made by Americans, paid for by Golczewski talks about Ukrainians and watched closely the WWI era and the by Russians benefits of pluralism 22 24 28 neighbors The Land of the Dancing with When Evil turns to Good Nebbish bears Patriarch Filaret talks Leonidas Russians have never BP’s Russian about raider attacks on Donskis: been a free people. -
Sutherland Philatelics SOVIET SATELLITES, REPUBLICS
SUTHERLAND PHILATELICS, PO BOX 448, FERNY HILLS D C, QLD 4055 Page 1 SG Michel Year Air Imp Particulars MUH Mint MNG Fine Used Used Sutherland Philatelics PO Box 448 Ferny Hills D C, Qld 4055 Australia ABN: 69 768 764 240 website: sutherlandphilatelics.com.au e-mail: [email protected] phone: international: 61 7 3851 2398; Australia: 07 3851 2398 SOVIET SATELLITES, REPUBLICS, SUCCESSOR STATES List Structure: ARMENIA, AZERBAIJAN, BELARUS, GEORGIA, KAZAKHSTAN, KYRGYZSTAN, MOLDOVA, TAJIKISTAN, TRANSCAUCASIAN FEDERATION, TURKMENISTAN, UKRAINE, UZBEKISTAN, WEST UKRAINE, OTHER SATELLITES, POs ABROAD A separate List exists for the Baltic States [ESTONIA, LATVIA, LITHUANIA] To find an item in this list, please use Adobe's powerful search function. We obtain our stock from collections we purchase. We do not have a Russia / USSR supplier. We list all items we have in stock, including broken sets, and singles from sets. Prices subject to change without notice. Please note that GST (currently 10%) is applicable from 1 July 2000. International sales are GST free. The prices in this list INCLUDE GST All prices are in Australian dollars. E&OE CREDIT CARDS: VISA & MASTERCARD ACCEPTED -- MIN $30 SUTHERLAND PHILATELICS, PO BOX 448, FERNY HILLS D C, QLD 4055 Page 2 SG Michel Year Air Imp Particulars MUH Mint MNG Fine Used Used ARMENIA National Republic Russian Arms overprinted - imperforate 3 1B 1919 k. 60. k / 1k orange 37 31 3k Arms optd with Armenian monogram (without frame) (black) 12.75 National Motives - Arms, Mt Ararat, Spinning - unissued