Extraction of Wax from Sorghum Bran •
Total Page:16
File Type:pdf, Size:1020Kb
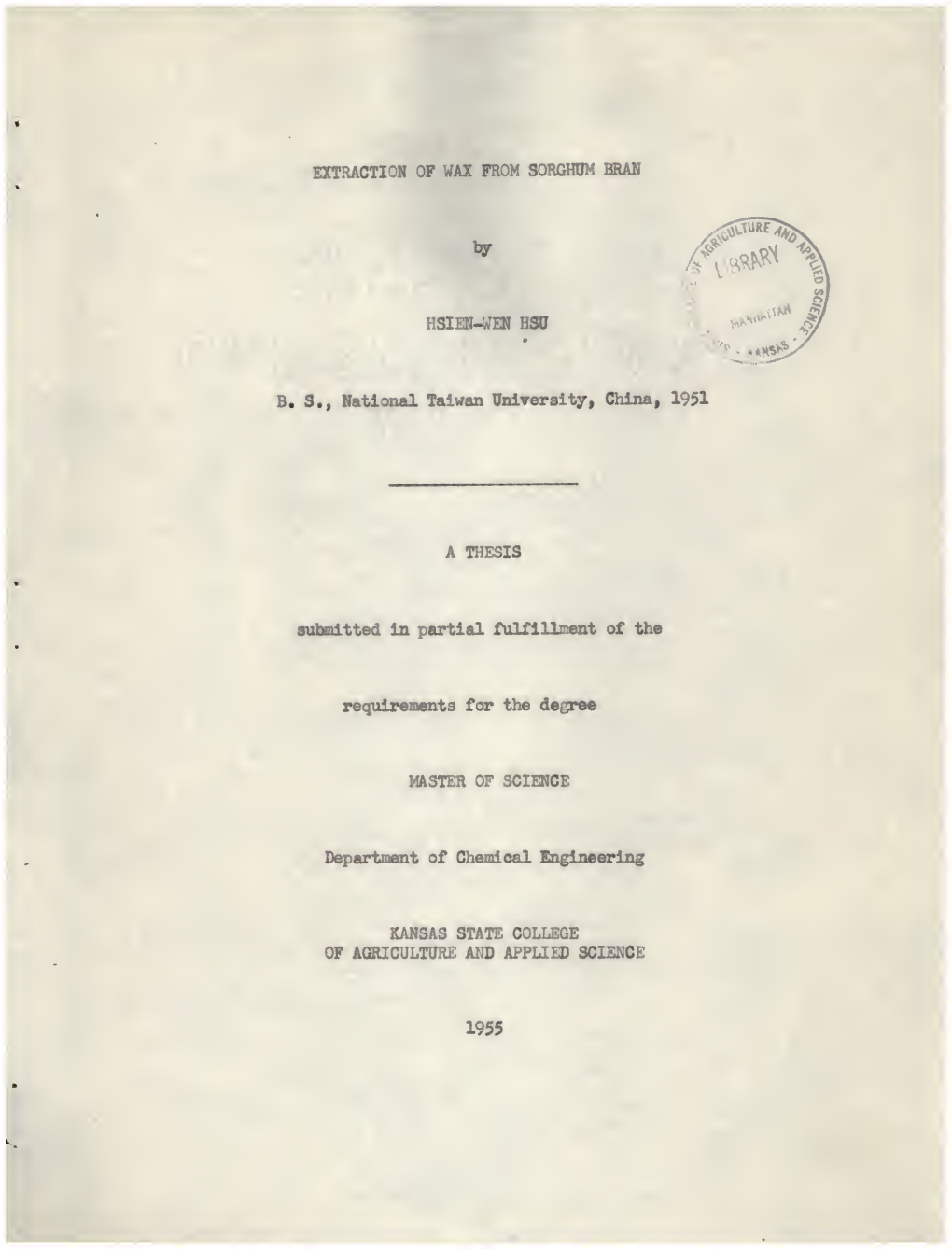
Load more
Recommended publications
-
The Separation of Three Azeotropes by Extractive Distillation by An-I Yeh A
The separation of three azeotropes by extractive distillation by An-I Yeh A thesis submitted in partial fulfillment of the requirement for the degree of Master of Science in Chemical Engineering Montana State University © Copyright by An-I Yeh (1983) Abstract: Several different kinds of extractive distillation agents were investigated to affect the separation of three binary liquid mixtures, isopropyl ether - acetone, methyl acetate - methanol, and isopropyl ether - methyl ethyl ketone. Because of the small size of the extractive distillation column, relative volatilities were assumed constant and the Fenske equation was used to calculate the relative volatilities and the number of minimum theoretical plates. Dimethyl sulfoxide was found to be a good extractive distillation agent. Extractive distillation when employing a proper agent not only negated the azeotropes of the above mixtures, but also improved the efficiency of separation. This process could reverse the relative volatility of isopropyl ether and acetone. This reversion was also found in the system of methyl acetate and methanol when nitrobenzene was the agent. However, normal distillation curves were obtained for the system of isopropyl ether and methyl ethyl ketone undergoing extractive distillation. In the system of methyl acetate and methanol, the relative volatility decreased as the agents' carbon number increased when glycols were used as the agents. In addition, the oxygen number and the locations of hydroxyl groups in the glycols used were believed to affect the values of relative volatility. An appreciable amount of agent must be maintained in the column to affect separation. When dimethyl sulfoxide was an agent for the three systems studied, the relative volatility increased as the addition rate increased. -
Distillation 65 Chem 355 Jasperse DISTILLATION
Distillation 65 Chem 355 Jasperse DISTILLATION Background Distillation is a widely used technique for purifying liquids. The basic distillation process involves heating a liquid such that liquid molecules vaporize. The vapors produced are subsequently passed through a water-cooled condenser. Upon cooling, the vapor returns to it’s liquid phase. The liquid can then be collected. The ability to separate mixtures of liquids depends on differences in volatility (the ability to vaporize). For separation to occur, the vapor that is condensed and collected must be more pure than the original liquid mix. Distillation can be used to remove a volatile solvent from a nonvolatile product; to separate a volatile product from nonvolatile impurities; or to separate two or more volatile products that have sufficiently different boiling points. Vaporization and Boiling When a liquid is placed in a closed container, some of the molecules evaporate into any unoccupied space in the container. Evaporation, which occurs at temperatures below the boiling point of a compound, involves the transition from liquid to vapor of only those molecules at the liquid surface. Evaporation continues until an equilibrium is reached between molecules entering and leaving the liquid and vapor states. The pressure exerted by these gaseous molecules on the walls of the container is the equilibrium vapor pressure. The magnitude of this vapor pressure depends on the physical characteristics of the compound and increases as temperature increases. In an open container, equilibrium is never established, the vapor can simply leave, and the liquid eventually disappears. But whether in an open or closed situation, evaporation occurs only from the surface of the liquid. -
Standard Operating Procedures
Standard Operating Procedures 1 Standard Operating Procedures OVERVIEW In the following laboratory exercises you will be introduced to some of the glassware and tech- niques used by chemists to isolate components from natural or synthetic mixtures and to purify the individual compounds and characterize them by determining some of their physical proper- ties. While working collaboratively with your group members you will become acquainted with: a) Volumetric glassware b) Liquid-liquid extraction apparatus c) Distillation apparatus OBJECTIVES After finishing these sessions and reporting your results to your mentor, you should be able to: • Prepare solutions of exact concentrations • Separate liquid-liquid mixtures • Purify compounds by recrystallization • Separate mixtures by simple and fractional distillation 2 EXPERIMENT 1 Glassware Calibration, Primary and Secondary Standards, and Manual Titrations PART 1. Volumetric Glassware Calibration Volumetric glassware is used to either contain or deliver liquids at a specified temperature. Glassware manufacturers indicate this by inscribing on the volumetric ware the initials TC (to contain) or TD (to deliver) along with the calibration temperature, which is usually 20°C1. Volumetric glassware must be scrupulously clean before use. The presence of streaks or droplets is an indication of the presence of a grease film. To eliminate grease from glassware, scrub with detergent solution, rinse with tap water, and finally rinse with a small portion of distilled water. Volumetric flasks (TC) A volumetric flask has a large round bottom with only one graduation mark positioned on the long narrow neck. Graduation Mark Stopper The position of the mark facilitates the accurate and precise reading of the meniscus. If the flask is used to prepare a solution starting with a solid compound, add small amounts of sol- vent until the entire solid dissolves. -
Laboratory Rectifying Stills of Glass 2
» LABORATORY RECTIFYING STILLS OF GLASS 2 By Johannes H. Bruun 3 and Sylvester T. Schicktanz 3 ABSTRACT A complete description is given of a set of all-glass rectifying stills, suitable for distillation at pressures ranging from atmospheric down to about 50 mm. The stills are provided with efficient bubbling-cap columns containing 30 to 60 plates. Adiabatic conditions around the column are maintained by surrounding it with a jacket provided with a series of independent electrical heating units. Suitable means are provided for adjusting or maintaining the reflux ratio at the top of the column. For the purpose of conveniently obtaining an accurate value of the true boiling points of the distillates a continuous boiling-point apparatus is incor- porated in the receiving system. An efficient still of the packed-column type for distillations under pressures less than 50 mm is also described. Methods of operation and efficiency tests are given for the stills. CONTENTS Page I. Introduction 852 II. General features of the still assembly 852 III. Still pot 853 IV. Filling tube and heater for the still pot 853 V. Rectifying column 856 1. General features 856 2. Large-size column 856 3. Medium-size column 858 4. Small-size column 858 VI. Column jacket 861 VII. Reflux regulator 861 1. With variable reflux ratio 861 2. With constant reflux ratio 863 VIII. The continuous boiling-point apparatus 863 IX. Condensers and receiver 867 X. The mounting of the still 867 XI. Manufacture and transportation of the bubbling-cap still 870 XII. Operation of the bubbling-cap still 870 XIII. -
Fractional Distillation (Ideal) 1-Propanol/2-Propanol at 760 Torr
Statistical Molecular Thermodynamics Christopher J. Cramer Video 10.7 Azeotropes and Immiscible Phases Fractional Distillation (Ideal) 1-propanol/2-propanol at 760 torr (from Video 10.5) bp as a function of composition x1−propanol(Solution) y1−propanol (Vapor) At 90 °C (between the two pure component boiling points) € the composition of the liquid is 59 mol% 1-propanol (point a) and the vapor is 45 mol% 1-propanol (point b) Fractional distillation: vapor is condensed and revaporized many times a to b to c to d to ... and finally you get to the pure lower boiling component at the top (the coolest point) of a distillation head! Fractional Distillation (Non-Ideal) benzene/ethanol at 760 torr Using Dalton’s/Raoult’s laws: * P2 x2P2 b b y = = a a 2 760 torr lim x2→1 760 torr d c d c and Dalton’s/Henry’s laws: f e e P2 x2kH,2 y2 = = 760 torr lim x2→0 760 torr bp as a function of composition Deviation from ideality permits the vapor phase to be enriched in either component depending on liquid composition. Distillation of benzene-rich mixture Distillation of ethanol-rich mixture Fractional distillation: vapor is condensed and revaporized many times a to b to c to d to e to f, but, irrespective of initial composition, ultimately an azeotropic composition is reached (about 55:45 above) that cannot be further separated by distillation! Self-assessment What purification can be accomplished for a liquid mixture that is not already at the azeotropic composition? Self-assessment Explained If not already at the azeotropic composition, the azeotrope at the top of b b a a the distillation head will be carrying away a greater fraction of one component than d is present in the liquid. -
Crude Oil Distillation
fact sheet Crude oil distillation Crude oil is a complex mixture of hydrocarbon molecules of all different shapes and lengths. This rich soup is where we get petrol for our cars, bitumen for our roads, and oils for our engines, amongst many other things. To create any of the thousands of useful things made from oil different hydrocarbons have to be separated. methane This is done by separating or refining using a distillation process. Hydrocarbons Hydrocarbons are molecules made from carbon and hydrogen atoms. With a chain of carbon as their ‘backbone’, hydrocarbons differ in their length and can form chains, branches or even rings. This backbone can range from just one carbon atom in length to more than 60 atoms. cyclohexane Methane has a single carbon atom; cyclohexane has six carbon atoms in a ring; and octane has eight carbon atoms in a chain. Even slight differences in length and structure of hydrocarbon molecules can give different chemical and physical properties. The refining process separates molecules according to their different boiling points. Hydrocarbons are jumbled together as thick black crude oil. The most efficient way to separate them into smaller fractions is by a process called fractional distillation. octane Hydrocarbons are found as solids, liquids and gases based on their length Short hydrocarbons (one to A backbone of five or more carbons Once a hydrocarbon gets so four carbons) are gases at room will give you a liquid hydrocarbon. large and cumbersome that it temperatures because they have Shorter liquid hydrocarbons will boil has a backbone of more than 20 such low boiling points. -
CHEM 344 Distillation of Liquid Mixtures
CHEM 344 Distillation of liquid mixtures 1. Distillation basics The vaporization of a liquid and condensation of the resulting vapor is the basis of distillation. Organic liquids containing small amounts (<15%) of impurities or non-volatile substances are easily purified by simple distillation, as are liquid mixtures where the difference in boiling point of the components is >70 oC. Fractional distillation is more useful for separating mixtures of liquids where the boiling points of the components differ by <70 oC (see later). A typical simple distillation setup is shown in Figure 1. It consists of a flask containing the liquid to be distilled, an adapter to hold a thermometer and to connect the flask to a water-cooled condenser, and a flask to hold the condensed liquid (the distillate). Figure 1: Apparatus for a simple distillation. 1.1 The distillation flask The distillation flask is a round-bottom flask. The liquid to be distilled should fill the distillation flask to ~50-60% of its capacity. To promote even heating of the liquid, a boiling chip or a magnetic stir bar is added before heat is applied to the distillation flask. The irregular chips provide sites for bubbles of vapor to form, or alternatively the liquid is agitated with the magnetic stirrer as it is being heated. Never add a boiling chip or a stir bar to a hot liquid! Doing so can cause a seemingly calm liquid to boil suddenly and violently. 1 1.2 The distilling adapter The adapter connects the distillation flask, the condenser, and the thermometer. This type of adapter is often referred to as a distillation head. -
Fractional Distillation for the Laboratory and Industry
ll distillations attempt to separate a lower boiling material (A) from a higher boiling material (B). Packed columns are “packed” A with a material that creates a large surface area within the distillation column. Vapors rise through the column, are condensed by the condenser and fall back down the column. This material is called the condensate. The descending condensate “wets” the packing. Ascending vapors rise through the wet packing and are forced into intimate contact with the condensate. This intimate contact causes the vapor to become enriched in the lower boiling material. This process is often called rectification. A A A AA AA A AA A A AA A A A AA A AA A B/R Instrument Corporation B/R Instrument was founded in 1966 by Roger Roark, Sr. and B A A A A A A B B Harry Brown, Jr. Originally a manufacturer of general glass- A A A AA A A B A A AA AA ware, the company began to specialize in the manufacture B B A A A A A AA AA A A A of spinning band distillation systems in 1968 under a DuPont B A B B B B patent. Since then the company has grown steadily in the A A A A distillation and laboratory equipment markets and now A B A B A B A A A AA distributes products to customers throughout the world. A B A A AA A A A B B A AA A Located in Easton, Maryland on the beautiful Eastern B A A A A A A A B A AA B A Shore of the Chesapeake Bay, the B/R facility encompasses A AA © 2004, B/R Instrument Corporation B A B AA A 14,700 square feet (1,370 square meters) and houses manu- B B A B B A B B A A B A A B A A B A A facturing, sales, engineering, service and administrative A A A A A B B A divisions. -
Distillation Strategies: a Key Factor to Obtain Spirits with Specific Organoleptic Characteristics
DISTILLATION STRATEGIES: A KEY FACTOR TO OBTAIN SPIRITS WITH SPECIFIC ORGANOLEPTIC CHARACTERISTICS Pau Matias-Guiu Martí ADVERTIMENT. L'accés als continguts d'aquesta tesi doctoral i la seva utilització ha de respectar els drets de la persona autora. Pot ser utilitzada per a consulta o estudi personal, així com en activitats o materials d'investigació i docència en els termes establerts a l'art. 32 del Text Refós de la Llei de Propietat Intel·lectual (RDL 1/1996). Per altres utilitzacions es requereix l'autorització prèvia i expressa de la persona autora. En qualsevol cas, en la utilització dels seus continguts caldrà indicar de forma clara el nom i cognoms de la persona autora i el títol de la tesi doctoral. No s'autoritza la seva reproducció o altres formes d'explotació efectuades amb finalitats de lucre ni la seva comunicació pública des d'un lloc aliè al servei TDX. Tampoc s'autoritza la presentació del seu contingut en una finestra o marc aliè a TDX (framing). Aquesta reserva de drets afecta tant als continguts de la tesi com als seus resums i índexs. ADVERTENCIA. El acceso a los contenidos de esta tesis doctoral y su utilización debe respetar los derechos de la persona autora. Puede ser utilizada para consulta o estudio personal, así como en actividades o materiales de investigación y docencia en los términos establecidos en el art. 32 del Texto Refundido de la Ley de Propiedad Intelectual (RDL 1/1996). Para otros usos se requiere la autorización previa y expresa de la persona autora. En cualquier caso, en la utilización de sus contenidos se deberá indicar de forma clara el nombre y apellidos de la persona autora y el título de la tesis doctoral. -
Fractional Distillation
FRACTIONAL DISTILLATION Fractional distillation is the separation of a mixture of miscible compounds by their boiling point, by heating to high enough temperatures. Industrial uses of Fractional Distillation Main article: Oil refinery#operation Chemical engineering schematic of industrial Continuous Binary Fractional Distillation Distillation is the most common form of separation technology in the chemical industry. In most chemical processes, the distillation is continuous steady state, where batch fractionation is not as economical. New feed is always being added to the distillation column and products are always being removed. Unless the process is disturbed due to changes in feed, heat, ambient temperature, or condensing, the amount of feed being added and the amount of product being removed are normally equal. This is known as continuous, steady-state fractional distillation. Application of continuous distillation Refineries The most widely used industrial applications of continuous, steady-state fractional distillation are in petroleum refineries, petrochemicalplants and natural gas processing plants. File:ShellMartinez.jpg Equipment Cross-sectional diagram of operating industrial Distllation Tower with trays Industrial distillation is typically performed in large, vertical cylindrical columns known as "distillation towers" or "distillation columns" with diameters ranging from about 65 centimeters to 6 meters and heights ranging from about 6 meters to 60 meters or more. The distillation towers have liquid outlets at intervals up the column which allow for the withdrawal of different fractions or products having differentboiling points or boiling ranges. The "lightest" products (those with the lowest boiling point) exit from the top of the columns and the "heaviest" products (those with the highest boiling point) exit from the bottom of the column. -
Summary. on FRACTIONAL DISTILLATION WITH
FRACTIONAL DISTILLATION WITH REGULATED STILLHEADS. 301 jectionable since CuSO4 in the presence of KMnOl liberates all the Br from KBr.’ The following tests show the reliability of the method: ‘TABLEV. NO. Mg. Br. Mg. CN. Mg. Fe(CN)siV. Results. I 0.0 ... ... Absolutely no color 2-5 I .o ... ... Negative 6-7 1.5 ... ... Fair 8-16 2.0-3.0 ... ... Good I 7-20 4 .*IO. 0 ... ... Strong color 21-25 2 .O ... ... Good 26 4.0 ... ... Excellent 27 I .o 500 ... Negative 28-30 2 .o 500 ... Excellent 31 I .o ... 5- Negative 32-34 2 .o ... 5- Excellent 35 2 .O 1.50 150 Good 36 2 .O IO0 100 Good 37 2 .O 200 200 Good 38 2 .O 50 50 Good The average time required for the completion of a test was 15 min. Summary. I. Attention has been called to the interference of thiocyanates, cyanides and ferrocyanides in the detection of bromides’ by the ordinary methods. 2. The interference offered by each of these substances has been de- termined. 3. A rapid method has been devised which is capable of detecting 2 mg. of bromine in the presence of 500 mg. of each of the interfering substances. 4. Numerous test experiments show the method to be trustwo’rthy. NEW YORK, N. Y. ON FRACTIONAL DISTILLATION WITH REGULATED STILL- HEADS. [FIRST COMMUNICATION. J CASES IN WHICH THE BOILING-POINT CURVE PASSES THROUGH A MAXIMUM OR A MINIMUM. BY M. A. ROSANOPPAND C. W. BACON. Received December 31. 1914. Section I. Introductory. A recent joint communication2 outlined a theory of fractional distilla- tion based on a new relationship between the slopes of the total pressure curve and the relative compositions of the liquid mixtures and the corre- sponding vapors. -
Steam Distillation of Toluene – Benzil Mixture
© Professor Kathleen V. Kilway and Robert Clevenger, Department of Chemistry, University of Missouri – Kansas City, 2006 2. Distillation J.R. Mohrig, Technique 12 Boiling points and distillation C.N. Hammond, 173-174 (general introduction) and P.F. Schatz: 176-180 (distillation and separation of mixtures) 194-196 (steam distillation) 203-205 (sources of confusion) Vocabulary: Vaporization The process of turning a liquid into vapor. Condensation The process of turning a vapor into a liquid. Azeotrope It is a mixture of two or more liquids, which boils at a constant boiling point. This procedure has been adapted from the macroscale procedure described in Macroscale and Microscale Organic Chemistry Experiments by Kenneth L. Williamson. In a nutshell: Normally, we distill solvents (the liquid in which we run the reaction) from a drying agent to dry the solvent if water is undesirable using a simple distillation. A fractional distillation is used to distill two or more components with similar boiling points. The Laboratory Techniques in Organic Chemistry’s authors (J.R. Mohrig, D.G. Alberg, G.E. Hofmeister, P.F. Schatz, and C.N. Hammond, pg 164) describes steam distillation as the “codistillation with water” and “allows the distillation of relatively nonvolatile organic compounds without complex vacuum systems; it is especially useful for separating volatile organic compounds from nonvolatile inorganic salts or from the leaves and seeds of plants”. Background What is distillation? It is the separation of liquids by vaporization and subsequent condensation of the vapors into a separate container. You are probably familiar with this process because it is used in the fragrance as well as the alcohol industry.