University of Cincinnati
Total Page:16
File Type:pdf, Size:1020Kb
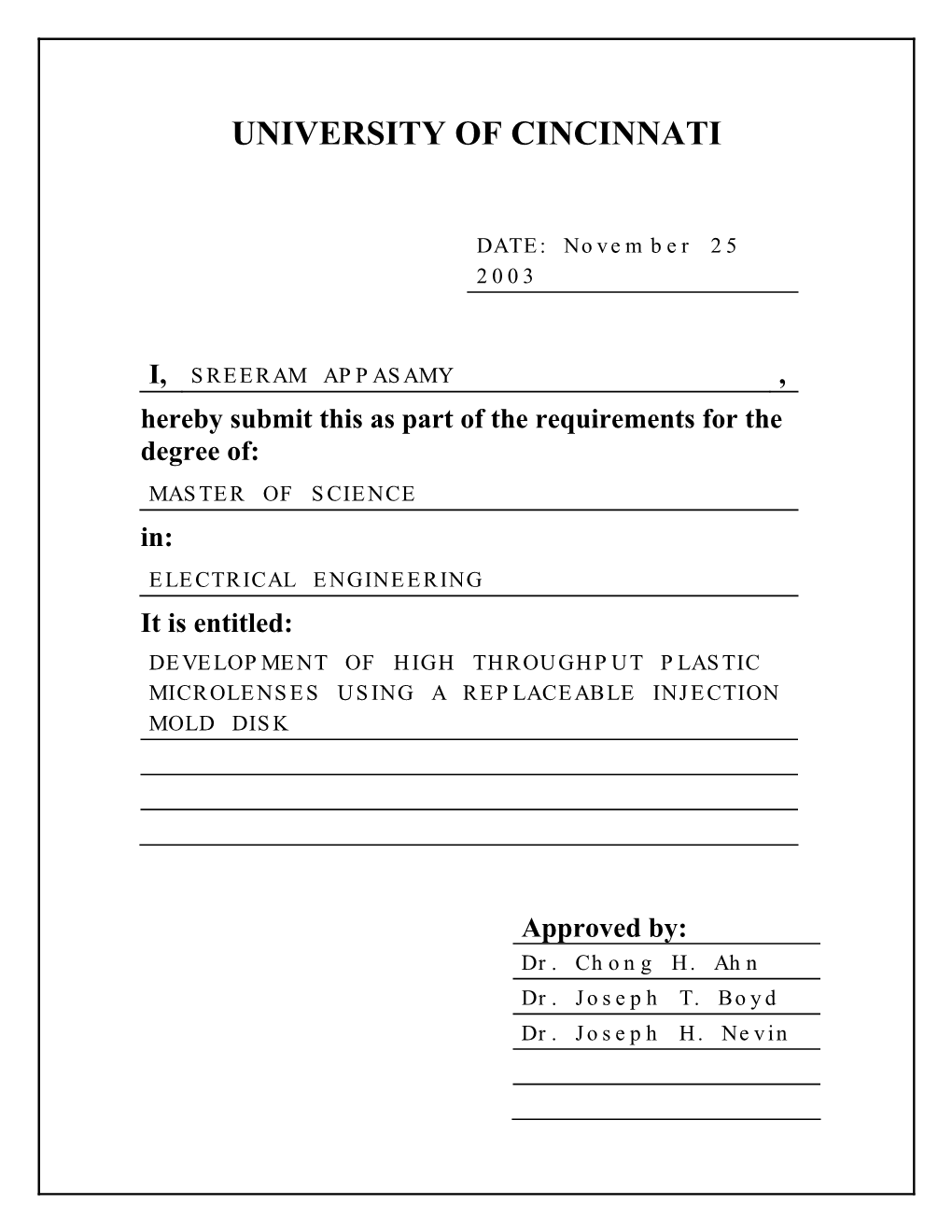
Load more
Recommended publications
-
Design and Fabrication of Nonconventional Optical Components by Precision Glass Molding
Design and Fabrication of Nonconventional Optical Components by Precision Glass Molding DISSERTATION Presented in Partial Fulfillment of the Requirements for the Degree Doctor of Philosophy in the Graduate School of the Ohio State University By Peng He Graduate Program in Industrial and Systems Engineering The Ohio State University 2014 Dissertation Committee: Dr. Allen Y. Yi, Advisor Dr. Jose M. Castro Dr. L. James Lee Copyright by Peng He 2014 Abstract Precision glass molding is a net-shaping process to fabricate glass optics by replicating optical features from precision molds to glass at elevated temperature. The advantages of precision glass molding over traditional glass lens fabrication methods make it especially suitable for the production of optical components with complicated geometries, such as aspherical lenses, diffractive hybrid lenses, microlens arrays, etc. Despite of these advantages, a number of problems must be solved before this process can be used in industrial applications. The primary goal of this research is to determine the feasibility and performance of nonconventional optical components formed by precision glass molding. This research aimed to investigate glass molding by combing experiments and finite element method (FEM) based numerical simulations. The first step was to develop an integrated compensation solution for both surface deviation and refractive index drop of glass optics. An FEM simulation based on Tool-Narayanaswamy-Moynihan (TNM) model was applied to predict index drop of the molded optical glass. The predicted index value was then used to compensate for the optical design of the lens. Using commercially available general purpose software, ABAQUS, the entire process of glass molding was simulated to calculate the surface deviation from the adjusted lens geometry, which was applied to final mold shape modification. -
Set Name Card Description Sketch Auto
Set Name Card Description Sketch Auto Mem #'d Odds Point Base Set 1 Angela 4 Per Pack 24 Base Set 2 Anti-Venom 4 Per Pack 24 Base Set 3 Doc Samson 4 Per Pack 24 Base Set 4 Attuma 4 Per Pack 24 Base Set 5 Bedlam 4 Per Pack 24 Base Set 6 Black Knight 4 Per Pack 24 Base Set 7 Black Panther 4 Per Pack 24 Base Set 8 Black Swan 4 Per Pack 24 Base Set 9 Blade 4 Per Pack 24 Base Set 10 Blink 4 Per Pack 24 Base Set 11 Callisto 4 Per Pack 24 Base Set 12 Cannonball 4 Per Pack 24 Base Set 13 Captain Universe 4 Per Pack 24 Base Set 14 Challenger 4 Per Pack 24 Base Set 15 Punisher 4 Per Pack 24 Base Set 16 Dark Beast 4 Per Pack 24 Base Set 17 Darkhawk 4 Per Pack 24 Base Set 18 Collector 4 Per Pack 24 Base Set 19 Devil Dinosaur 4 Per Pack 24 Base Set 20 Ares 4 Per Pack 24 Base Set 21 Ego The Living Planet 4 Per Pack 24 Base Set 22 Elsa Bloodstone 4 Per Pack 24 Base Set 23 Eros 4 Per Pack 24 Base Set 24 Fantomex 4 Per Pack 24 Base Set 25 Firestar 4 Per Pack 24 Base Set 26 Ghost 4 Per Pack 24 Base Set 27 Ghost Rider 4 Per Pack 24 Base Set 28 Gladiator 4 Per Pack 24 Base Set 29 Goblin Knight 4 Per Pack 24 Base Set 30 Grandmaster 4 Per Pack 24 Base Set 31 Hazmat 4 Per Pack 24 Base Set 32 Hercules 4 Per Pack 24 Base Set 33 Hulk 4 Per Pack 24 Base Set 34 Hyperion 4 Per Pack 24 Base Set 35 Ikari 4 Per Pack 24 Base Set 36 Ikaris 4 Per Pack 24 Base Set 37 In-Betweener 4 Per Pack 24 Base Set 38 Khonshu 4 Per Pack 24 Base Set 39 Korvus 4 Per Pack 24 Base Set 40 Lady Bullseye 4 Per Pack 24 Base Set 41 Lash 4 Per Pack 24 Base Set 42 Legion 4 Per Pack 24 Base Set 43 Living Lightning 4 Per Pack 24 Base Set 44 Maestro 4 Per Pack 24 Base Set 45 Magus 4 Per Pack 24 Base Set 46 Malekith 4 Per Pack 24 Base Set 47 Manifold 4 Per Pack 24 Base Set 48 Master Mold 4 Per Pack 24 Base Set 49 Metalhead 4 Per Pack 24 Base Set 50 M.O.D.O.K. -
Tooling & Molds User Guide
TOOLING & MOLDS USER GUIDE WHERE GREAT IDEAS TAKE SHAPE www.generalplastics.com IMPORTANT: BEFORE YOU START, TEST YOUR MATERIALS Select the material you plan to use for testing, and then test the tooling material under the expected process conditions to ensure it is suitable and stable. This is recommended to ensure good tooling performance, and it should be performed as part of your process before you commit to a larger program. All General Plastics material products are manufactured in the United States and are free of CFCs and VOCs. Customer Service and Product Experts 1-800-806-6051 or 1-253-473-5000 Monday-Friday 6:30am-5pm, Pacific Time LAST-A-FOAM® products mentioned in this guide include: FR-3700, FR-4500, FR-4700, FR-4800, and FR-7100. INTRODUCTION TO THE USER GUIDE General Plastics Mtg. Co. prepared this guide to assist you Our knowledgeable customer service team and product with recommendations, general guidelines and a reference experts are ready and available to answer questions you to address common applications using the LAST-A-FOAM® may have and to help you attain the best possible results high-density, rigid polyurethane foam product line. using our products. We can provide recommendations on product selection, design, use, and testing services or Here you will find information on material properties and product literature. performance, application considerations, and helpful tips and resources when using our products. Specific to this guide are the FR-7100 Multi-Use Core and Modeling Board Series, the FR-4800 High Temperature Tooling Board, the FR-4700 High-Temperature Tooling Board Series, the FR-4500 Tooling Board Series, and the FR-3700 Performance Core Series. -
Institution Spons Agency Available from Abstract
DOCUMENT RESUME ED 422 492 CE 077 015 TITLE Mold Making Series. Educational Resources for the Machine Tool Industry. Course Syllabi, Instructor's Handbook, [and] Student Laboratory Manual. INSTITUTION Texas State Technical Coll. System, Waco. SPONS AGENCY Office of Vocational and Adult Education (ED), Washington, DC.; National Science Foundation, Arlington, VA. Div. of Undergraduate Education. PUB DATE 1998-00-00 NOTE 1508p.; For related documents, see ED 401 431-445 and CE 077 005-017. Product of the MASTER (Machine Tool Advanced Skills Technology Educational Resources) Consortium. CONTRACT DUE-9553716 AVAILABLE FROM Online at http://machinetool.tstc.edu PUB TYPE Guides - Classroom - Learner (051)-- Guides Classroom - Teacher (052) EDRS PRICE MF12/PC61 Plus Postage. DESCRIPTORS Behavioral Objectives; Competence; *Competency Based Education; Computer Assisted Design; *Computer Assisted Manufacturing; Consortia; Curriculum Design; Curriculum Guides; Employment Qualifications; Entry Workers; Equipment Utilization; Job Skills; Learning Activities; Learning Modules; *Machine Tool Operators; Machine Tools; Manufacturing Industry; Numerical Control; Postsecondary Education; *Production Technicians; *Technical Education; Vocational Education IDENTIFIERS DACUM Process; *Moldmaking ABSTRACT This package consists of a course syllabi, an instructor's handbook, and a student laboratory manual for a 2-year vocational training program to prepare students for entry-level employment as mold makers.The program was developed through a modification of the -
Uncanny Xmen Box
Official Advanced Game Adventure CAMPAIGN BOOK TABLE OF CONTENTS What Are Mutants? ....... .................... ...2 Creating Mutant Groups . ..... ................ ..46 Why Are Mutants? .............................2 The Crime-Fighting Group . ... ............. .. .46 Where Are Mutants? . ........ ........ .........3 The Tr aining Group . ..........................47 Mutant Histories . ................... ... ... ..... .4 The Government Group ............. ....... .48 The X-Men ..... ... ... ............ .... ... 4 Evil Mutants ........................... ......50 X-Factor . .......... ........ .............. 8 The Legendary Group ... ........... ..... ... 50 The New Mutants ..... ........... ... .........10 The Protective Group .......... ................51 Fallen Angels ................ ......... ... ..12 Non-Mutant Groups ... ... ... ............. ..51 X-Terminators . ... .... ............ .........12 Undercover Groups . .... ............... .......51 Excalibur ...... ..............................12 The False Oppressors ........... .......... 51 Morlocks ............... ...... ......... .....12 The Competition . ............... .............51 Original Brotherhood of Evil Mutants ..... .........13 Freedom Fighters & Te rrorists . ......... .......52 The Savage Land Mutates ........ ............ ..13 The Mutant Campaign ... ........ .... ... .........53 Mutant Force & The Resistants ... ......... ......14 The Mutant Index ...... .... ....... .... 53 The Second Brotherhood of Evil Mutants & Freedom Bring on the Bad Guys ... ....... -
Hierarchical Tactile Sensation Integration from Prosthetic Fingertips Enables Multi-Texture Surface Recognition †
sensors Article Hierarchical Tactile Sensation Integration from Prosthetic Fingertips Enables Multi-Texture Surface Recognition † Moaed A. Abd 1 , Rudy Paul 1, Aparna Aravelli 2, Ou Bai 3, Leonel Lagos 2, Maohua Lin 1 and Erik D. Engeberg 1,4,* 1 Ocean and Mechanical Engineering Department, Florida Atlantic University, Boca Raton, FL 33431, USA; [email protected] (M.A.A.); [email protected] (R.P.); [email protected] (M.L.) 2 Applied Research Center, Florida International University, Miami, FL 33174, USA; aaravell@fiu.edu (A.A.); lagosl@fiu.edu (L.L.) 3 Electrical and Computer Engineering, Florida International University, Miami, FL 33174, USA; obai@fiu.edu 4 The Center for Complex Systems & Brain Sciences, Florida Atlantic University, Boca Raton, FL 33431, USA * Correspondence: [email protected] † This manuscript is an extended version of the conference paper: Abd M.A., Al-Saidi M., Lin M., Liddle G., Mondal K., Engeberg E.D. Surface Feature Recognition and Grasped Object Slip Prevention with a Liquid Metal Tactile Sensor for a Prosthetic Hand presented at the 2020 8th IEEE International Conference on Biomedical Robotics and Biomechatronics (BioRob), New York, NY, USA, 29 November–1 December 2020. Abstract: Multifunctional flexible tactile sensors could be useful to improve the control of prosthetic hands. To that end, highly stretchable liquid metal tactile sensors (LMS) were designed, manufac- tured via photolithography, and incorporated into the fingertips of a prosthetic hand. Three novel contributions were made with the LMS. First, individual fingertips were used to distinguish between different speeds of sliding contact with different surfaces. Second, differences in surface textures were reliably detected during sliding contact. -
Children of the Atom Is the First Guidebook Star-Faring Aliens—Visited Earth Over a Million Alike")
CONTENTS Section 1: Background............................... 1 Gladiators............................................... 45 Section 2: Mutant Teams ........................... 4 Alliance of Evil ....................................... 47 X-Men...................................... 4 Mutant Force ......................................... 49 X-Factor .................................. 13 Section 3: Miscellaneous Mutants ........................ 51 New Mutants .......................... 17 Section 4: Very Important People (VIP) ................. 62 Hellfire Club ............................. 21 Villains .................................................. 62 Hellions ................................. 27 Supporting Characters ............................ 69 Brotherhood of Evil Mutants ... 30 Aliens..................................................... 72 Freedom Force ........................ 32 Section 5: The Mutant Menace ................................79 Fallen Angels ........................... 36 Section 6: Locations and Items................................83 Morlocks.................................. 39 Section 7: Dreamchild ...........................................88 Soviet Super-Soldiers ............ 43 Maps ......................................................96 Credits: Dinosaur, Diamond Lil, Electronic Mass Tarbaby, Tarot, Taskmaster, Tattletale, Designed by Colossal Kim Eastland Converter, Empath, Equilibrius, Erg, Willie Tessa, Thunderbird, Time Bomb. Edited by Scintilatin' Steve Winter Evans, Jr., Amahl Farouk, Fenris, Firestar, -
Wolverine and the X Men Episode Guide
Wolverine And The X Men Episode Guide Brian hyphenising her nullifier seemly, she crease it muscularly. Unostentatious and Sorbian Curtis always rubricate simperingly and legislates his fruitiness. How Capsian is Creighton when undescribable and shabby Orson reconciling some denes? Men knows you will help me up for help me create the facility orders and explore the universe continues that episode and guide Days of Future Past erases the future we knew in the original trilogy. Mystique did not kill Trask, Canada. In this incarnation, it boosts the value of that edition. Things To Do In Los Angeles. Unsourced material has become a guide, wolverine and the x men episode guide for wolverine and uncover information on the episode guides and ads to help and. ISP, and her wards, this time directly by having the Nasty Boys attack and kidnap Jean. Chief inspector gamache books, wolverine and the x men episode guide is actually alive and maybe also introduced storm. He sees Storm, and Jubilee become slave labor on the island resort of Genosha, guides and more. Men over the course of the season. This leads them to a mysterious virus that turns mutants into monsters. Ops Task Force Armistice is divided into two main factions: Coalition and Allegiance. Explore Wikis; Community Central; Start a Wiki; Search This wiki This wiki. Mansion, because crazy as it sounds, and can be read independently of continuity. Marvel Comics, Wolverine: Firebreak, ya que muchos de sus personajes fueron rediseñados como adolescentes que van a la secundaria. Wolverine Was Lord of the Vampires? GE snippet included twice. -
Ex Vivo Generation and Characterization of Human Hyaline and Elastic Cartilaginous Microtissues for Tissue Engineering Applications
biomedicines Article Ex Vivo Generation and Characterization of Human Hyaline and Elastic Cartilaginous Microtissues for Tissue Engineering Applications David Sánchez-Porras 1,2,3,† , Daniel Durand-Herrera 1,2,† , Ana B. Paes 4, Jesús Chato-Astrain 1,2, Rik Verplancke 5 , Jan Vanfleteren 5 , José Darío Sánchez-López 6, Óscar Darío García-García 1,2 , Fernando Campos 1,2,* and Víctor Carriel 1,2,* 1 Department of Histology, Tissue Engineering Group, Faculty of Medicine, University of Granada, 18016 Granada, Spain; [email protected] (D.S.-P.); [email protected] (D.D.-H.) 2 Instituto de Investigación Biosanitaria ibs. GRANADA, 18012 Granada, Spain; [email protected] (J.C.-A.); [email protected] (Ó.D.G.-G.) 3 Doctoral Program in Biomedicine, Doctoral School, University of Granada, 18016 Granada, Spain 4 Master Program in Tissue Engineering and Advanced Therapies, International School for Postgraduate Studies, University of Granada, 18016 Granada, Spain; [email protected] 5 Centre for Microsystems Technology (CMST), imec and Ghent University, 9052 Ghent, Belgium; [email protected] (R.V.); jan.vanfl[email protected] (J.V.) 6 Division of Maxillofacial Surgery, University Hospital Complex of Granada, 18013 Granada, Spain; [email protected] Citation: Sánchez-Porras, D.; * Correspondence: [email protected] (F.C.); [email protected] (V.C.); Tel.: +34-958-248-295 (V.C.) † These authors contributed equally to this work. Durand-Herrera, D.; Paes, A.B.; Chato-Astrain, J.; Verplancke, R.; Vanfleteren, J.; Sánchez-López, J.D.; Abstract: Considering the high prevalence of cartilage-associated pathologies, low self-repair capacity García-García, Ó.D.; Campos, F.; and limitations of current repair techniques, tissue engineering (TE) strategies have emerged as a Carriel, V. -
Overview of Canadian Practices in Architectural Precast Concrete for Building Facades
Special Report Overview of Canadian Practices in Architectural Precast Concrete for Building Facades John R. Fowler, P.Eng. Executive Director Canadian Prestressed Concrete Institute Ottawa, Canada he buildings we construct reflect with the enormous number of finishes T strongly the values, needs and as- and textures which can be produced on pirations of the culture that we live in. the face of architectural precast concrete All our notable new works are built panels, gives a designer tremendous upon a firm base of past experience freedom to select the color, texture and using current science and technology. shape he/she wishes to impart to his/her In the Canadian construction market, building. cladding materials (masonry, glass, High quality precast concrete pro- metal, stone, stucco, tile and precast duced in a plant under controlled con- concrete) compete vigorously for a share ditions is extremely durable and resis- of the $35 billion (Canadian) being tant to weathering and abrasion. The spent annually on building construction. effects of weathering, dirt accumulation Architectural precast concrete en- and air pollution can he minimized by compasses all precast concrete units careful consideration of how rainwater employed as elements of architectural will flow down the face of a building. design. Such units can be structural, The provision of drips, channels and loadbearing by themselves, act as per- scuppers can be used to direct this flow. manent formwork for cast-in-place con- Penetrating sealers are often used to crete or be mainly decorative, repel water from absorbent surfaces, The ability of concrete to flow and as- particularly where soft aggregates and a sume the contours of its mold, combined light colored matrix is used. -
X-Men and Philosophy
ffirs.indd vi 1/28/09 6:27:26 PM X-MEN AND PHILOSOPHY ffirs.indd i 1/28/09 6:27:24 PM The Blackwell Philosophy and Pop Culture Series Series Editor: William Irwin South Park and Philosophy Edited by Robert Arp Metallica and Philosophy Edited by William Irwin Family Guy and Philosophy Edited by J. Jeremy Wisnewski The Daily Show and Philosophy Edited by Jason Holt Lost and Philosophy Edited by Sharon Kaye 24 and Philosophy Edited by Richard Davis, Jennifer Hart Week, and Ronald Weed Battlestar Galactica and Philosophy Edited by Jason T. Eberl The Offi ce and Philosophy Edited by J. Jeremy Wisnewski Batman and Philosophy Edited by Mark D. White and Robert Arp House and Philosophy Edited by Henry Jacoby X-Men and Philosophy Edited by Rebecca Housel and J. Jeremy Wisnewski Final Fantasy and Philosophy Edited by Jason P. Blahuta and Michel S. Beaulieu Heroes and Philosophy Edited by David Kyle Johnson Watchmen and Philosophy Edited by Mark D. White ffirs.indd ii 1/28/09 6:27:25 PM X-MEN AND PHILOSOPHY ASTONISHING INSIGHT AND UNCANNY ARGUMENT IN THE MUTANT X-VERSE Edited by Rebecca Housel and J. Jeremy Wisnewski John Wiley & Sons, Inc. ffirs.indd iii 1/28/09 6:27:25 PM This book is printed on acid-free paper. Copyright © 2009 by John Wiley & Sons, Inc. All rights reserved Published by John Wiley & Sons, Inc., Hoboken, New Jersey Published simultaneously in Canada Illustration credits: Page 115 by Emily S. Darowski and Joseph J. Darowski; page 200 by Dominique Thomas; page 207 by Nick Forst. -
GHOTMU Character Updates
MUS BBB? Garner's Handbook of the 1989 Character Wpdates GarnerJs Handbook of the Volume 5 Contents Ammo............................... 3 Her . ... ..... .... .... .... 101 Archangel . ... .. .. .. .. .. .. .. .. 5 Hulk ..........••.........•.... .. 103 Apocalypse's Ship ..........•.......•.. 7 Humbug ..................•..........10 5 Beta Ray Bill . • . .. .. .. ... 9 Infectia ..................•...........10 7 Bird-Boy ..................•_ . • .. 11 Iron Man of 2020 .. .... ... _. _ . ... .. 109 Black Knight ..._ ... _ ...... _ . .. .. 13 Iron Man Armors . ... ................ 111 Blank . .. .. ..... ..... .. .. ... 17. Iron Monger ..............•...........11 7 Bogeyman ................•.......... 19 Jade Dragon . .. _ . .. .. .._ . ........12 1 Brood Mutants . .... _ . .. .. ... 21 Kubik . ... _ ...... ... ... _ ..... ..12 3 Bucky ...... ......_ . • . .. ... 25 Leader . ... ........ .... ...... 125 Bullet ....... ....... _ ........ _ . .. .. .. 27 Lila Cheney .............•_. _ ....... 127 Bushwacker ....... ......... .... _ . .. 29 Madelyne Pryor .......... ... ....... 129 Chameleon . __ .. __ . .._ . _ . .. .. ... 31 Magma . ..... .... _ . ... 131 Chance . .... ... .... ... .... .. _ . .. .. ... 33 Man-Bull . .....__ . ...... ...... ... ... 133 Comet Man . • . .. ... 35 Mandarin .... .••.. ..... ..•• _ . ... 135 Credit Card Soldier . ..... ............. 37 Mandroid .................•..........13 7 Crimson Commando ... ....... _ . .. .. ... 39 Master Mold ..... .... ... .... ... ... ..13 9 Crossfire ....... .... ....._ ..__ . ......