Small Gas Turbines Chapter 3 Starting
Total Page:16
File Type:pdf, Size:1020Kb
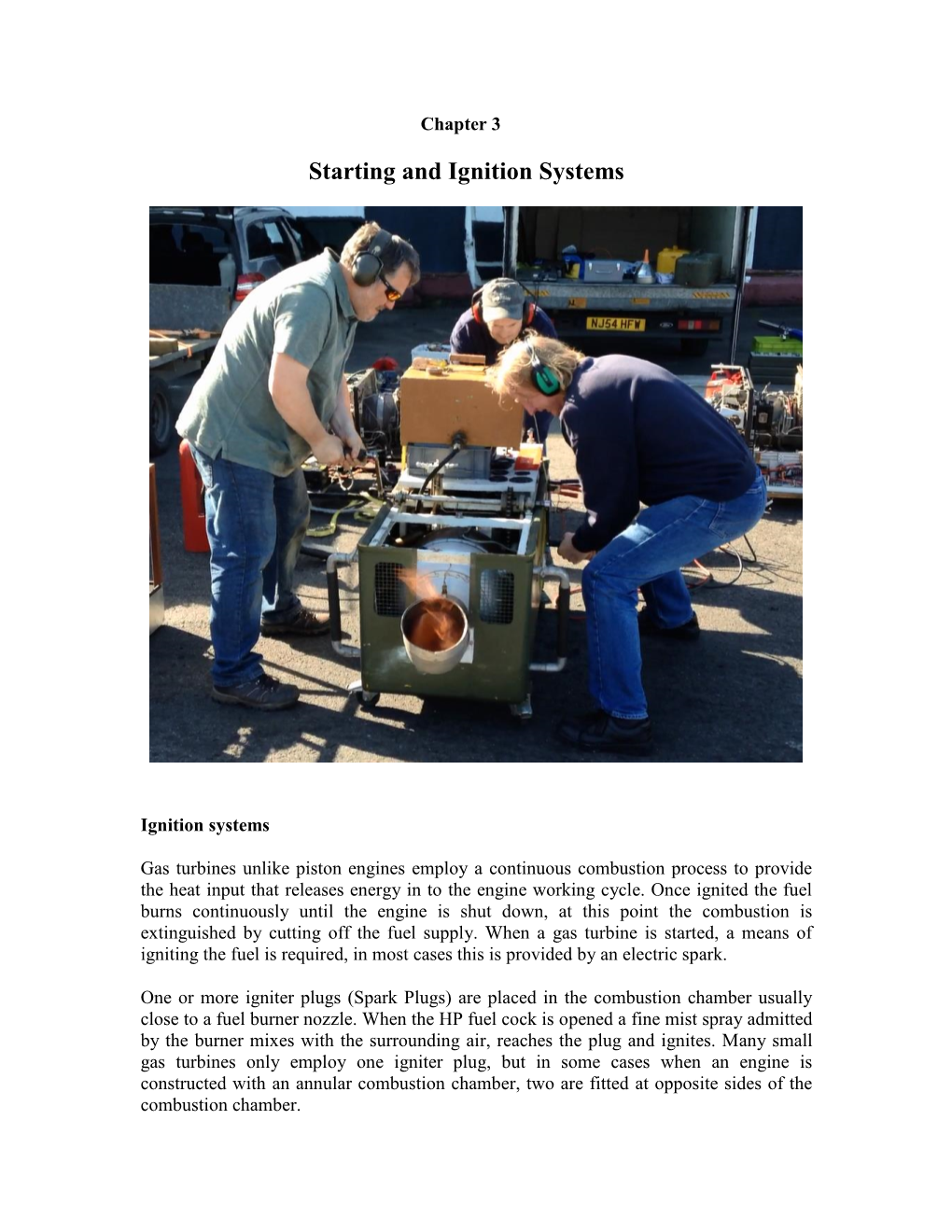
Load more
Recommended publications
-
Decision 2005/07/R
DECISION No 2005/07/R OF THE EXECUTIVE DIRECTOR OF THE AGENCY of 19-12-2005 amending Decision No 2003/19/RM of 28 November 2003 on acceptable means of compliance and guidance material to Commission Regulation (EC) No 2042/2003 on the continuing airworthiness of aircraft and aeronautical products, parts and appliances, and on the approval of organisations and personnel involved in these tasks THE EXECUTIVE DIRECTOR OF THE EUROPEAN AVIATION SAFETY AGENCY, Having regard to Regulation (EC) No 1592/2002 of 15 July 2002 on common rules in the field of civil aviation (hereinafter referred to as the Basic Regulation) and establishing a European Aviation Safety Agency1 (hereinafter referred to as the “Agency”), and in particular Articles 13 and 14 thereof. Having regard to the Commission Regulation (EC) No 2042/2003 of 28 November 2003 on the continuing airworthiness of aircraft and aeronautical products, parts and appliances, and on the approval of organisations and personnel involved in these tasks.2 Whereas: (1) Annex IV Acceptable Means of Compliance to Part- 66 Appendix 1 Aircraft type ratings for Part-66 aircraft maintenance licence (hereinafter referred to as Part-66 AMC Appendix I) is required to be up to date to serve as reference for the national aviation authorities. (2) To achieve this requirement the text of Part-66 AMC Appendix I should be amended regularly to add new aircraft type rating. (3) The regular amendment of Part-66 AMC Appendix I is considered as a permanent rulemaking task for the Agency. This decision represents the first update according to an accelerated procedure accepted by AGNA and SSCC. -
How Understanding a Railway's Historic Evolution Can Guide Future
College of Engineering, School of Civil Engineering University of Birmingham Managing Technical and Operational Change: How understanding a railway’s historic evolution can guide future development: A London Underground case study. by Piers Connor Submitted as his PhD Thesis DATE: 15th February 2017 University of Birmingham Research Archive e-theses repository This unpublished thesis/dissertation is copyright of the author and/or third parties. The intellectual property rights of the author or third parties in respect of this work are as defined by The Copyright Designs and Patents Act 1988 or as modified by any successor legislation. Any use made of information contained in this thesis/dissertation must be in accordance with that legislation and must be properly acknowledged. Further distribution or reproduction in any format is prohibited without the permission of the copyright holder. Managing Technical & Operational Development PhD Thesis Abstract The argument for this thesis is that patterns of past engineering and operational development can be used to support the creation of a good, robust strategy for future development and that, in order to achieve this, a corporate understanding of the history of the engineering, operational and organisational changes in the business is essential for any evolving railway undertaking. It has been the objective of the author of this study to determine whether it is essential that the history and development of a railway undertaking be known and understood by its management and staff in order for the railway to function in an efficient manner and for it to be able to develop robust and appropriate improvement strategies in a cost-effective manner. -
CAR Part II Chapter 7 Aircraft Maintenance Engineer Licensing to (Mainly)
NOTICE OF PROPOSED AMENDMENT 2019-01 Issue 01 Date of Issue: 14 April 2019 SUBJECT; CAR PART II CHAPTER 7 – CAR 66 AIRCRAFT MAINTENANCE ENGINEER LICENSING REASON; The GCAA has recently conducted a review of (CAR PART II Chapter 7) as a result of a Consultative Committee outcome (OTTG). The review has concluded that, there is a need to amend CAR Part II Chapter 7 Aircraft Maintenance Engineer Licensing to (mainly): 1. Introduce the category L licence for hot air balloons with its associated basic knowledge and training requirements; 2. further clarify on the examination process and basic knowledge/experience requirements for the issue and validity of a CAR 66 licence. 3. Transfer content of Appendix 1 to CAR 66.70 into CAR 66.50 and CAR 66.70 including the applicable AMC and GM; 4. create an appendix to identify limitations added to a CAR 66 licence and further define the reason and applicability for each limitation and the implications. The proposed initial entry into force date of the amendment is 01 August 2019. The layout and paragraph numbering may change through the NPA process; however the content will remain the same. This notice is published to announce to the public this amendment and to entitle all concerned parties to: 1. Review the attached proposed regulation; and 2. Submit their comments online through the GCAA website within 30 days from the date of this NPA. Comments must be submitted through the GCAA Website – E-Publication – Notice of Proposed Amendment, using the Action of “Submit NPA Feedback Request.” Comments and Responses may be viewed in the Comments Response Document CRD pertaining to this NPA on the GCAA website. -
CRD) to Notice of Proposed Amendment (NPA) 03-2006
Comment Response Document (CRD) to Notice of Proposed Amendment (NPA) 03-2006 for amending the Executive Director Decision No. 2005/07/R of 19 December 2005 on acceptable means of compliance and guidance material to Commission Regulation (EC) No 2042/2003 of 20 November 2003 on the continuing airworthiness of aircraft and aeronautical products, parts and appliances, and on the approval of organisations and personnel involved in these tasks APPENDIX I AIRCRAFT TYPE RATINGS FOR PART-66 AIRCRAFT MAINTENANCE LICENCE CRD to NPA 03/2006 Explanatory Note I. General 1. The purpose of the Notice of Proposed Amendment (NPA) 03/2006, dated 20 April 2006 was to propose an amendment to Decision N° 2005/07/R of the Executive Director of the Agency of 19 December 2005 on acceptable means of compliance and guidance material to Commission Regulation (EC) No 2042/2003 of 20 November 2003 on the continuing airworthiness of aircraft and aeronautical products, parts and appliances, and on the approval of organisations and personnel involved in these tasks (ED Decision 2005/07/R). II. Consultation 2. The draft Executive Director Decision (ED Decision) amending ED Decision 2005/07/R was published on the web site (www.easa.europa.eu) on 21 April 2006. By the closing date of 2 June 2006, European Aviation Safety Agency (the Agency) had received 107 comments from 20 National Aviation Authorities, professional organisations and private companies. III. Publication of the CRD 3. All comments received have been acknowledged and incorporated into a Comment Response Document (CRD). This CRD contains a list of all persons and/or organisations that have provided comments and the answers of the Agency. -
C:\Drive D from Old Hard Drive\
Reminiscenses of MC - IXION REMINISCENCES OF MOTOR CYCLING: ‘IXION’ The work includes many fascinating cartoon draw- First published 1920-1927 pp. 312 ings and some photographs, and all those interested in early transport will find the works truly fascinating. Here reprinted are two small volumes Motor Cycle Reminiscences and Further Motor Cycle Reminiscences ISBN 0 85409 886 0 £3.00 NET written by ‘Ixion’ of ‘The Motor Cycle’ who was one of the lead•ing motoring journalists. EP Publishing Limited Other titles include: The author recounts in these two titles, now reissued MOTOR CYCLE CAVALCADE ‘Ixion’ £2.50 as a single volume, his impres•sions of 30 years and MY MOTORING REMINISCENCES S.F. Edge £3.50 over 300,000 miles on the road. He was one of the first THE COMPLETE MOTORIST A.B. Filson Young £4.00 motor cyclists when the general public regarded the ROLLS-ROYCE CATALOGUE 1910-11 £10.00 pioneers as incomprehensible lunatics, and no wonder, if INSTRUCTIONS FOR THE PRACTICAL WORKING OF TRAC- one reads the problems they had to overcome. TION ENGINES AND ROAD ROLLERS £1.00 In the early days even the pedal cycle tended to be SENTINEL STEAM WAGGONS Alley & MacLellan, Ltd. £2.00 faster, and the uplift beneath early motor cycling must BALLOONS’& AIRSHIPS A. Hildebrandt £4.25 have been equiva•lent to a religion, or they would never VELOCIPEDES ‘Velox’ £1.25 have borne its manifold disagreeables as they did. One A ROYAL ROAD S. Fay £2.00 could divide these pioneers into three kinds, the engi- GREAT GREAT WESTERN W.J. -
Faculty of Engineering
FACULTY OF ENGINEERING DEPARTMENT OF ELECTRIC-ELECTRONIC ENGINEERING EE400 GRADUATION PROJECT (Energy Conservation) Submitted by : Aziz Mesut YENiGUN ( 20112023 ) Submitted to : Assoc. Prof. Dr. Ozgur Cemal OZERDEM Nicosia-2014 LIBRARY CONTENTS f.),"(" INTRODUCTION ~f ABSTRACT 2 CHEPTERl POWER INVERTER 3 1.1 Input and output 3 1.1.1 Input voltage .•........•......••...•••.•..•..•••.•...•••..•....•.....••..... 3 1.1.2 Output waveform ...................................................•. 3 1.1.2.1 Square wave .••.•..•...........•..•.•....•........•........•.....•.. 4 Fig . 1.1.2.1 Square wave ....•................................•.•..... 4 1.1.2.2 Sine wave .....••..•.•.•....•.•..•..................•................•..• 4 Fig. 1.1.2.2 sinus wave •....•••..••..•..•.•••••••.••.....•.•.•••... 4 1.1.2.3 Modified sine wave •••••••••••••••••••••••••••••••••••••••••••••••• 5 Fig. 1.1.2.3 modifield sine wave .•..•..•.••......•...•••••.•..•.• 5 1.1.2.4 Other waveforms ....•..•.....•.••••...••.•••..•.........•.•.•.....• 6 1.1.3 Output frequency .•.......•.•.. °' •••••••••••••••••••••••••••••••••••••••• 6 1.1.4 Output voltage ..........•.•••.•...•.••..••.•.•.••.••••..•.•.....•.••..•.. 6 1.1.5 Output power ...••..•..•.•.•..••••••..•.•••••••.•.......••.•..••••.•..••.. 7 1.2 Applications 7 1.2.1 DC power source utilization •.....•..•.•..•...•.•..••••.•.....•..•...• 7 1.2.2 Uninterruptible power supplies ....•.......•.••.......•..•..........•• 7 1.2.3 Electric motor speed control .•.•....•........••••.•....•..••••...•.•.•. 7 1.2.4 Power grid ....•••.....•............••.••.•.......•.••.........•••........ -
Oiiragm Lt` R2
ALTITUDE TESTING CHAMBERS NEWNES @V[Ig OiiragM Lt`r2 EDITOR : F. J. CA MM AUGUST 1949 A CONTROL -LINE JET-PROPELLED MODEL AIRCRAFT IN FLIGHT. SEE PAGE 346, Studies in Electricity and Magnetism Elements of Mechanics World of Models Jet Reaction Power Models Woodturning Letters from Readers Model Engineering Practice Simple Electronics Cyclist Section CleVPS etc.,etc. %AOWE dips, stainless produced. clips, wehave bronze range ITSS,VOIS clips, ownspecification. steel theenormous your and size from clipto shape selection any inevery tiny design show a can yourdisposal. Herewe Department is at Research e-Aperience Our of clip-making (9-3 years Two popular types. In range of sines to grip from Delivery from Stock. No, 80 No. 300 A drawing boardslip. Platedfinish' de- livery ( Stock. 4/- dovz. z. Plus P.T. The roost informativepsstvefr:.:enrxedt-. bookhe n yet 2,.Wings 10/6 ".shed Sole Makers : HERBERT TERRY & SONS LTD. REDDITCH. London Birmingham Manchester August, 1949 NEWNES PRACTICAL MECHANICS 325 THE " ZYTO " I5in. MOTORISED SAWBENCH IFYOU TAKE PHOTOGRAPHS WITH TOTALLY ENCLOSED MOTOR GET THIS JOHNSON 1-20 TANK AND FOR CROSSCUTTNG, RIPPING, DEVELOP YOUR FILMS INDAYLIGHT MITREING, BORING, GROOVING, etc. You lose half the fun of photography if you do not develop Brief Specification: Saw -table 24in. x t8in., with rise and your own negatives and make your own prints.Itis much fall motion for grooving, etc. Takes cheaper to do the work yourself and you see your results 15in. saw. Long ripping fence with more quickly. fine adiustment: Heavy spindle bored to take dowel bits, etc. J-20 TANK, az illustrated below, is for all size -20 roll films.Holds h.p. -
Doctorat Paristech T H È S E L'école Nationale Supérieure Des
École doctorale n° 396 : Économie, Organisations & Société Doctorat ParisTech T H È S E pour obtenir le grade de docteur délivré par l’École nationale supérieure des mines de Paris Spécialité “ Sciences de Gestion ” présentée et soutenue publiquement par Frédéric ARNOUX le 22 janvier 2013 Modéliser et organiser la conception innovante : Le cas de l’innovation radicale dans les systèmes d’énergie aéronautiques Directeur de thèse : Armand HATCHUEL Co-encadrement de la thèse : Mathias BEJEAN Jury T M. Mathias BEJEAN, Maitre de conférences, IRG, Université Paris Est Créteil Examinateur M. Albert DAVID, Professeur, DRM, Université Paris-Dauphine Rapporteur H M. Antoine DRACHSLER, Chef de service Avant-Projets, Turbomeca Examinateur M. Armand HATCHUEL, Professeur, Centre de Gestion Scientifique, Mines ParisTech Examinateur È M. Jérémy LEGARDEUR, Professeur, ESTIA Rapporteur M. Michel NAKHLA , Professeur, EMI, Agro ParisTech Examinateur S M. François PELLERIN, Docteur en Physique des surfaces, Sudinnove Suffragant E MINES ParisTech Centre de Gestion Scientifique 60 boulevard Saint Michel, 75006 Paris 2 MINES ParisTech n’entend donner aucune approbation ni improbation aux opinions émises dans cette thèse. Ces opinions doivent être considérées comme propres à l’auteur. 3 4 A mes parents, 5 6 REMERCIEMENTS Je voudrais saluer ici les personnes qui de près ou de loin ont contribué à la concrétisation de ce travail de thèse de doctorat. Je tiens tout d’abord à adresser mes remerciements les plus sincères à mon directeur de thèse, Armand Hatchuel, qui a accepté de m’accompagner tout au long de cette expérience. Merci pour sa confiance, sa disponibilité, ses conseils et ses intuitions. Au travers de nos discussions, il m’a apporté une connaissance approfondie des divers aspects du sujet. -
Low Voltage Distribution Transformers
Your Presenters > Thomas Patzner Product Manager, Low Voltage Transformers > Marquette University – Electrical Engineering > Apprentice Electrician > Low Voltage Transformers - Co-op (Square D Company) (lab testing, inoperative trouble shooting, designing of units) - Application Engineer (Square D Company) - Sales Engineer (Jefferson Transformer) - Marketing (Square D Company) - Product Manager (Square D Company) 8 The Energy Policy and Conservation Act of 1975 (EPCA), as amended, prescribes energy conservation standards for various consumer products and certain commercial and industrial equipment, including distribution transformers. 9 EPACT 1992 • Authorized Department of Energy to evaluate Distribution Transformers Market Response • Energy Star – added Distribution Transformers to program – 1994 • NEMA – publishes Standard for Higher Efficient Transformers - 1996 • States Mandated NEMA Standard Level for Low Voltage Products (1999 through 2005) Department of Energy • DOE start analysis process • Advance Notice of Public Ruling – July, 2004 10 EPACT 2005 • Authorized DOE to mandate efficiency levels on Distribution Transformers • Low Voltage Transformers – Mandated to TP1 standard effected Jan, 2007 Market Response • Energy Star Program discontinued May, 2007 Department of Energy • DOE stop all work being done on Low Voltage units from the EPACT1992 • DOE finalized Medium Voltage Final Rule – 2007 – mandating levels effected Jan, 2010 • 10 CFR 431 includes how to test the distribution transformers • 10 CFR 429 -CERTIFICATION, COMPLIANCE, AND 11 ENFORCEMENT… COMMERCIAL AND INDUSTRIAL EQUIPMENT Distribution transformer means a transformer that— (1) Has an input voltage of 34.5 kV or less; (2) Has an output voltage of 600 V or less; (3) Is rated for operation at a frequency of 60 Hz; and (4) Has a capacity of 10 kVA to 2500 kVA for liquid-immersed units and 15 kVA to 2500 kVA for dry-type units; but… Liquid-immersed distribution transformer means a distribution transformer in which the core and coil assembly is immersed in an insulating liquid.