Ignition System - Wikipedia 8/28/20, 1 16 PM
Total Page:16
File Type:pdf, Size:1020Kb
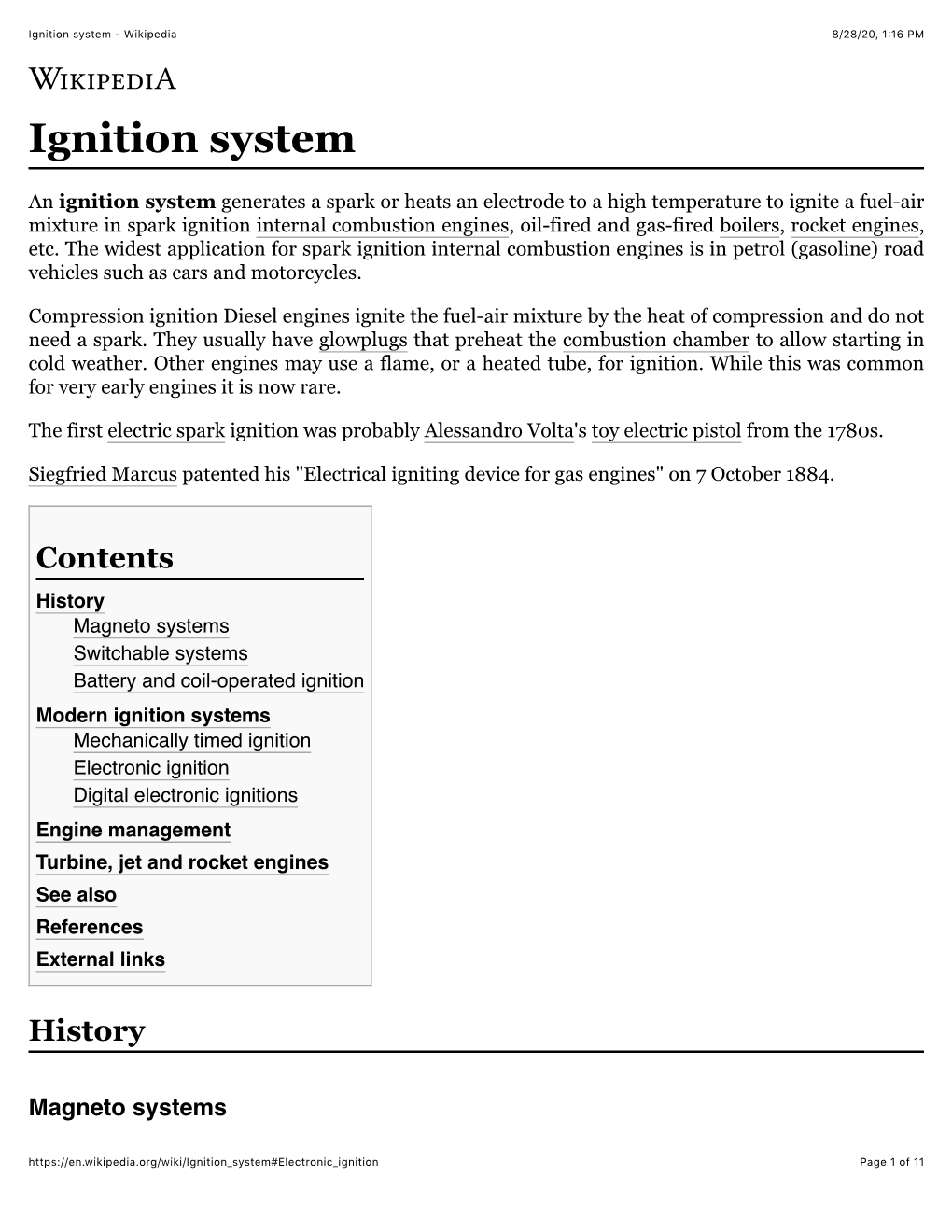
Load more
Recommended publications
-
Spark Plug Condition Chart
Spark Plug Condition Chart Normal Mechanical Damage Oil Fouled May be caused by a foreign object that Too much oil is entering the combustion has accidentally entered the combus- Combustion deposits are slight chamber. This is often caused by piston tion chamber. When this condition is and not heavy enough to cause rings or cylinder walls that are badly discovered, check the other cylinders to any detrimental effect on engine worn. Oil may also be pulled into the prevent a recurrence, since it is possi- performance. Note the brown to chamber because of excessive clear- ble for a small object to "travel" from greyish tan color, and minimal ance in the valve stem guides. If the one cylinder to another where a large amount of electrode erosion which PCV valve is plugged or inoperative it degree of valve overlap exists. This clearly indicates the plug is in the can cause a build-up of crankcase pres- condition may also be due to improper correct heat range and has been sure which can force oil and oil vapors reach spark plugs that permit the piston operating in a "healthy" engine. past the rings and valve guides into the to touch or collide with the firing end. combustion chamber. Overheated Insulator Glazing Pre-Ignition A clean, white insulator firing tip and/or excessive electrode ero- Usually one or a combination of several sion indicates this spark plug con- Glazing appears as a yellowish, var- dition. This is often caused by over engine operating conditions are the nish-like color. This condition indicates prime causes of pre-ignition. -
A Computer Simulation of Induction Heat Treating Systems Is Discussed
Optimal Design of Internal Induction Coils Dr. Valentin Nemkov(1), Eng. Robert Goldstein (1), Dr. Vladimir Bukanin(2) (1)Centre for Induction Technology, Inc. 1388 Atlantic Blvd. Auburn Hills, MI 48326 USA www.induction.org (2)St. Petersburg Electrotechnical University (SPbETU), Prof. Popova str., 5, 197376, St. Petersburg, Russia ABSTRACT Internal induction heating coils are not so well studied as external. Three main induction coil styles were proposed in pioneering works many years ago: Cylindrical coils, Hair-pin coils and Rod-type coils [1, 2]. It was clear from the very beginning that electromagnetic parameters of the coils of two first styles might be strongly improved by application of magnetic cores. However it was not clearly shown what parameters may be improved and how much, as well as what are the optimal designs of induction coils. Current presentation contains short consideration and comparison of all three styles of coils followed by a detailed analysis of cylindrical internal (ID) coils using modern computer simulation tools. It is shown that it isn’t sufficient to only consider the influence of magnetic core on electrical efficiency of the coil head. The cores reduce dramatically current demand for transfer of required power into the workpiece. In turn it results in strong reduction of voltage drop and power losses in the whole supplying circuitry: coil leads, busswork and matching transformer. Plus much smaller capacitor battery is required. Computer simulation is simple for single-turn cylindrical ID coils and several computer packages may be used. Computer simulation of multi-turn cylindrical ID coils, which are the most common, is a much more complicated task, due to the return leg. -
The Starting System Includes the Battery, Starter Motor, Solenoid, Ignition Switch and in Some Cases, a Starter Relay
UNIT II STARTING SYSTEM &CHARGING SYSTEM The starting system: The starting system includes the battery, starter motor, solenoid, ignition switch and in some cases, a starter relay. An inhibitor or a neutral safety switch is included in the starting system circuit to prevent the vehicle from being started while in gear. When the ignition key is turned to the start position, current flows and energizes the starter's solenoid coil. The energized coil becomes an electromagnet which pulls the plunger into the coil. The plunger closes a set of contacts which allow high current to reach the starter motor. The charging system: The charging system consists of an alternator (generator), drive belt, battery, voltage regulator and the associated wiring. The charging system, like the starting system is a series circuit with the battery wired in parallel. After the engine is started and running, the alternator takes over as the source of power and the battery then becomes part of the load on the charging system. The alternator, which is driven by the belt, consists of a rotating coil of laminated wire called the rotor. Surrounding the rotor are more coils of laminated wire that remain stationary (called stator) just inside the alternator case. When current is passed through the rotor via the slip rings and brushes, the rotor becomes a rotating magnet having a magnetic field. When a magnetic field passes through a conductor (the stator), alternating current (A/C) is generated. This A/C current is rectified, turned into direct current (D/C), by the diodes located within the alternator. -
Diagram 1 IGNITION SYSTEM MAINTENANCE on GASEOUS GENERATOR SYSTEMS
Information Sheet #103 IGNITION SYSTEM MAINTENANCE ON GASEOUS GENERATOR SYSTEMS Generator systems, when arranged as an engine connected to an AC alternator to generate electrical power, have a variety of engine types to choose from. One engine frequently found in generator systems is a spark ignition engine. Spark ignition engines utilize a variety of fuels for their combustion cycle, with the most common fuel on medium to heavy duty being Natural Gas and Liquid Petroleum. Smaller units are frequently gasoline powered. Whatever the fuel, all spark ignition engines work on the Buckeye Power Sales same principle of combustion and have unique components for ignition. Should these components not be maintained in proper Reliable Power Professionals Since 1947 running order, emergency power, when required, will be reduced, or even lost. 1.0 KEY COMPONENTS WITHIN A SPARK IGNITION ENGINE: Gaseous generator sets are a very reliable power supply for prime and standby power applications, but as for any prime mover, or reciprocating engine, they have components within their ignition system that have to be maintained to ensure trouble free operation. (See Diagram 1) The principal components within a spark ignition engine are: 1.1 SPARK PLUG – Most EPA compliant gaseous/gasoline powered reciprocating engines operate on the 4-stroke Otto-Cycle. To ignite the fuel on the combustion cycle, they use a spark plug. There is one spark plug per cylinder, for example a Vee eight-cylinder engine will have 8-spark plugs, and a straight 6-cylinder engine will have -
Ignition System
IGNITION SYSTEM The ignition system of an internal combustion engine is an important part of the overall engine system. All conventional petrol[[1]] (gasoline)[[2]] engines require an ignition system. By contrast, not all engine types need an ignition system - for example, a diesel engine relies on compression-ignition, that is, the rise in temperature that accompanies the rise in pressure within the cylinder is sufficient to ignite the fuel spontaneously. How it helps It provides for the timely burning of the fuel mixture within the engine. How controlled The ignition system is usually switched on/off through a lock switch, operated with a key or code patch. Earlier history The earliest petrol engines used a very crude ignition system. This often took the form of a copper or brass rod which protruded into the cylinder, which was heated using an external source. The fuel would ignite when it came into contact with the rod. Naturally this was very inefficient as the fuel would not be ignited in a controlled manner. This type of arrangement was quickly superseded by spark-ignition, a system which is generally used to this day, albeit with sparks generated by more sophisticated circuitry. Glow plug ignition Glow plug ignition is used on some kinds of simple engines, such as those commonly used for model aircraft. A glow plug is a coil of wire (made from e.g. nichrome[[3]]) that will glow red hot when an electric current is passed through it. This ignites the fuel on contact, once the temperature of the fuel is already raised due to compression. -
Installation Instructions SUPERCHARGER ‘90-’93 Mazda Miata Part# 999-000, 999-005, 999-010, 999-015
Installation Instructions SUPERCHARGER ‘90-’93 Mazda Miata Part# 999-000, 999-005, 999-010, 999-015 440 Rutherford St. P.O. Box 847 Goleta, CA 93117 1-888-888-4079 • FAX 805-692-2523 • www.jacksonracing.com INSTALLATION TIME IN AS LITTLE AS 4 HOURS regularly (every 3000 miles or so), you should FOR EXPERIENCED MECHANICS, AROUND 5 have no trouble. If in doubt, check your engine’s TO 6 HOURS FOR “OCCASIONAL” MECHAN- compression. You should have at least 135psi of ICS. compression in each cylinder with no more than a 10% variance between any two cylinders or with a TOOLS REQUIRED: 3/8” Drive Socket set w/ 10% increase in any cylinder after a tablespoon of 17mm, 14mm, 13mm, 12mm, 10mm & 8mm sock- oil is poured in. Your cooling system should be up ets; Deep sockets (14mm or 9/16”, 10mm): to par (50/50 mix of water and new coolant). Phillips and Standard screwdriver, 10mm, 12mm, Basically, if you have a good engine, it will be very and 17mm open end wrench; 5mm Allen wrench happy with this supercharger. with a 3/8” drive; paper clip; a box to store your OLD PARTS in. A 1/4” drive socket set will be use- BEFORE INSTALLING THIS SYSTEM: ful with some of the tight working areas. A timing A. Drive your fuel tank empty and refill with 92 light will be needed to set the ignition timing. Octane major brand gasoline. If you can only find 91 Octane, see step #3 under “Adjustments” at the A NOTE ON ADDING A SUPERCHARGER TO end of these instructions. -
Installation Instructions Vertex® Electronic Distributor
Installation Instructions Vertex® Electronic Distributor This product is applicable to pre-1966 California and pre-1968 federally certified passenger cars. It is also applicable to non-emission controlled trucks and similar vehicles. It is not intended for use on any emission- controlled vehicles operated on highways or roadways, unless otherwise noted. Caution/Important Information: Please read and understand all of the information provided in these instructions before attempting the installation. Ensure that your vehicle is equipped with an (ignition ballast resistor) or a (integral loom resistance wire) in the wire harness between the ignition switch and the coil (+) terminal. Check a service manual for your vehicle to locate the ignition ballast resistor or loom resistance wire. If your vehicle is not equipped with an ignition ballast resistor, install a Vertex® Ignition Ballast Resistor (PN 967000) in the wire between the +12VDC ignition switch and the coil (+) terminal. Failure to use an (ignition ballast resistor) or (loom resistance wire) will eventually destroy the internal electronics in the Vertex® Distributor and is not covered under the warranty. Parts included in this kit: (1) Vertex® Electronic Distributor (1) Vertex® Ballast Resistor (PN 967000) General Information: Rotation-Rotation of the original distributor and your new Vertex® Distributor should be the same. This may be checked by observing the distributor rotor while cranking the engine with the starter and comparing the observed rotation with the arrow on the distributor cap. Distributor Firing Order-Wire position numbers in the Vertex® cap indicate the sequence of firing of the distributor. These are not to be interpreted as the firing order of the engine. -
Download (PDF)
Nanotechnology Education - Engineering a better future NNCI.net Teacher’s Guide To See or Not to See? Hydrophobic and Hydrophilic Surfaces Grade Level: Middle & high Summary: This activity can be school completed as a separate one or in conjunction with the lesson Subject area(s): Physical Superhydrophobicexpialidocious: science & Chemistry Learning about hydrophobic surfaces found at: Time required: (2) 50 https://www.nnci.net/node/5895. minutes classes The activity is a visual demonstration of the difference between hydrophobic and hydrophilic surfaces. Using a polystyrene Learning objectives: surface (petri dish) and a modified Tesla coil, you can chemically Through observation and alter the non-masked surface to become hydrophilic. Students experimentation, students will learn that we can chemically change the surface of a will understand how the material on the nano level from a hydrophobic to hydrophilic surface of a material can surface. The activity helps students learn that how a material be chemically altered. behaves on the macroscale is affected by its structure on the nanoscale. The activity is adapted from Kim et. al’s 2012 article in the Journal of Chemical Education (see references). Background Information: Teacher Background: Commercial products have frequently taken their inspiration from nature. For example, Velcro® resulted from a Swiss engineer, George Mestral, walking in the woods and wondering why burdock seeds stuck to his dog and his coat. Other bio-inspired products include adhesives, waterproof materials, and solar cells among many others. Scientists often look at nature to get ideas and designs for products that can help us. We call this study of nature biomimetics (see Resource section for further information). -
Owner's M Anua
OWNER’S M ANUA Thank you for purchasing the HONDA GV400 vertical engine. If any trouble should develop with your unit, consult the dealer from whom you purchased it. i @ IWNOA MOTOR CO., LTD. iggo is!@ - _~- _ .___ _II tamw * To prevent fire hazards and to provide adequate ventilation, keep the engine at least 3 ft away from buildings and other equipment, during operation. Ir Do not place flammable objects, such as, gasoline, matches, etc., close to the engine while it is running. * Refuel in a well ventilated area with the engine stopped. Gasoline is flammable and explosive under certain conditions. * Do not smoke or allow flames or sparks where the engine is refueled or where gasoline is stored. * Do not overfill the tank. There should be no fuel in the filler neck. Make sure that the filler cap is closed securely. * If any fuel is spilled, make sure the area is dry before starting. * Operate the engine on a level surface to prevent fuel spillage. * This engine is not equipped with a spark arrester, and operation may be illegal in some areas. Check local laws and regulations before operation. * Exhaust contains poisonous carbon monoxide gas. Avoid inhalation of exhaust gases. Never run the engine in a closed garage or confined area. Every 100 operating Hrs. First 20 operating Hrs. I Every 20 operating Hrs. CHANGE ENGINE OIL . CLEAN AIR CLEANER . CHANGE ENGINE OIL l CLEAN SPARK PLUG AND CHECK GAP Breaker type CD1 type L 0.6 - 0.7 mm 0.9 - 1.0 mm ImaffKAwj *JE type 1 (0.024 - 0.027 in) (0.035 - 0.039 in) .C(LJ$Jji@ \/-- Cycle, valve arrangement 4Stroke, side valve * For replacement, use BMdA or l BPMdA or BPMRdA Displacement cm3 (cu in) 406 (28.1) BMRdA spark (NGK) plug WW Max. -
Autosaver (PDF)
P881-220840 EPA-AA-TBB-511-81-3 I EPA Evaluation of the Autoraver under Section 511 of the Motor Vehicle Information and Coat Saving8 Act Edward Anthony Barth May, 1981 Test and Evaluation Branch Emirrion Control Technology Division Office of Mobile Source Air Pollution Control Environmental Protection Agency -2- 6560-26 EPA-AA-TEB-511-81-3 ENVIRONMENTAL PROTECTION ACENCY [40 CFR Part 610) FUEL ECONOHYRETROFLT WVLCES Announcement of Fuel Economy Retrofit Device Evaluation for “Autosaver” AGENCY: Environmental Protection Agency (EPA). ACTION: Notice of Fuel Economy Retrofit Device Evaluation. s UMARY : This document annwnces the conclusions of the EPA evaluation of the “Autosaver” device under provisions of Section 511 of the Motor Vehicle Information and Cost Savings Act. -3- BACKGROUND LNFORMATZON: Section 511(b)(l) and’ Section 511(c) of the Motor Vehicle Information and Cost Savings Act (15 U.S.C. 2011(b)) requires that: 1 fi * (b)(l) “Upon application of any manufacturer of a retrofit device (or ’i . prototype thereof), upon the’ requast of the Federal Trade Commission I pursuant to subsection (a), or upon his own motion, the EPA Administrator shall evaluate, in accordance with rules prescribed under subsection (d), any retrofit device to determine whether the retrofit device increases fuel economy and to determine whether the <cpresentations (if any) made with respect to such retrofit devices are accurate.” (cl “The EPA Administrator shall publish in the Federal Register a summary of the results of all tests conducted under this section, together with the EPA Administrator’s conclusions as to - (1) the effect of any retrofit device on fuel ecor,orny; (2) the effect of any such device on emissions of air pollutants; and (3) any other information which the Admfnfstrator determines to be relevant in evaluatirg such device.” EPA publf shed final regulations establishing procedures for conducting fuel economy retrofit device evaluations on Elarch 23, 1979 144 FR 179461. -
Precision Spray Asphalt Distributor Owner
Calder Brothers Corporation Serial # Page1 Model: Precision Spray 944-N-P2C---S-D00000 to Current V2.2 PRECISION SPRAY ASPHALT DISTRIBUTOR OWNER / OPERATOR / PARTS MANUAL Precision Spray Serial Number: Precision Spray Specification Number: Chassis Serial Number: Sold & Serviced by: Calder Brothers Corporation Serial # Page2 Model: Precision Spray 944-N-P2C---S-D00000 to Current V2.2 TABLE OF CONTENTS Section A – Safety: ........................................................................................Pages 3-13 Section B – Specifications: ............................................................................Pages 14-19 Section C – Controls & Accessories:.............................................................Pages 20-27 Section D – Operations:.................................................................................Pages 28-37 Section E – Fuels & Lubrication:...................................................................Pages 38-40 Section F – Transportation & Theft Deterrents: ............................................Pages 41-44 Section G – Troubleshooting: ........................................................................Pages 45-56 Section H – Service:.......................................................................................Pages 57-67 Section I – Storage:........................................................................................Pages 68-70 Section J – Parts Manual:...............................................................................Pages 71-84 Section K – Warranty -
Tecumseh V-Twins
TECUMSEH V-TWIN ENGINE TABLE OF CONTENTS CHAPTER 1. GENERAL INFORMATION CHAPTER 2. AIR CLEANERS CHAPTER 3. CARBURETORS AND FUEL SYSTEMS CHAPTER 4. GOVERNORS AND LINKAGE CHAPTER 5. ELECTRICAL SYSTEMS CHAPTER 6. IGNITION CHAPTER 7. INTERNAL ENGINE AND DISASSEMBLY CHAPTER 8. ENGINE ASSEMBLY CHAPTER 9. TROUBLESHOOTING AND TESTING CHAPTER 10. ENGINE SPECIFICATIONS Copyright © 2000 by Tecumseh Products Company All rights reserved. No part of this book may be reproduced or transmitted, in any form or by any means, electronic or mechanical, including photocopying, recording or by any information storage and retrieval system, without permission in writing from Tecumseh Products Company Training Department Manager. i TABLE OF CONTENTS (by subject) GENERAL INFORMATION Page Engine Identification ................................................................................................ 1-1 Interpretation of Engine Identification ...................................................................... 1-1 Short Blocks ............................................................................................................ 1-2 Fuels ........................................................................................................................ 1-2 Engine Oil ................................................................................................................ 1-3 Basic Tune-Up Procedure ....................................................................................... 1-4 Storage ...................................................................................................................