NON DESTRUCTIVE TESTING of SOFT BODY ARMOR Karan Bhise Purdue University
Total Page:16
File Type:pdf, Size:1020Kb
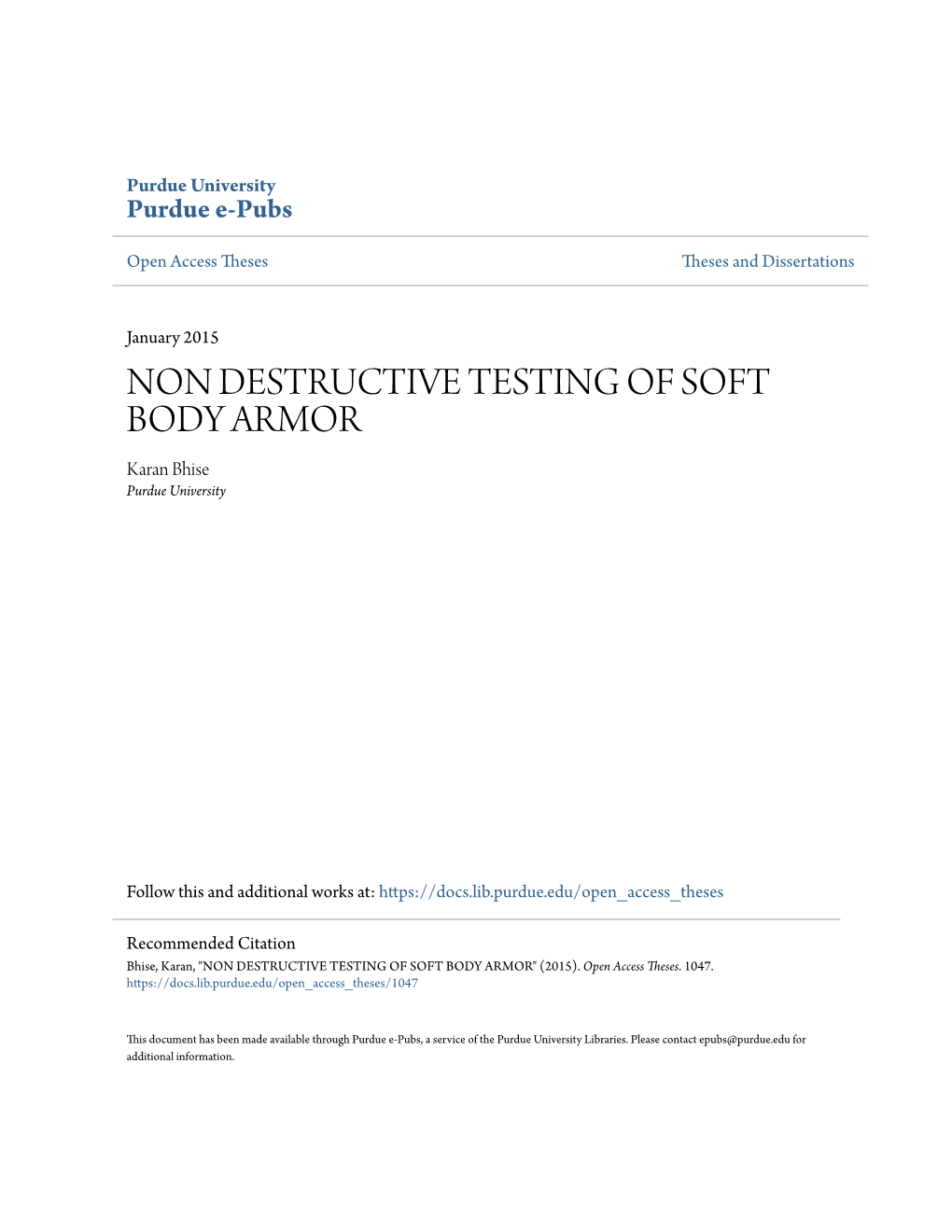
Load more
Recommended publications
-
Is Behind Armour Blunt Trauma a Real Threat to Users of Body Armour? a Systematic Review
Review J R Army Med Corps: first published as 10.1136/jramc-2013-000161 on 13 November 2013. Downloaded from Is behind armour blunt trauma a real threat to users of body armour? A systematic review 1 1 2 Editor’s choice Debra J Carr, I Horsfall, C Malbon Scan to access more free content 1Impact and Armour Group, ABSTRACT Department of Engineering and Introduction Behind armour blunt trauma (BABT) has Key messages Applied Science, Cranfield fi Defence and Security, Cranfield been de ned as a non-penetrating injury caused by the rapid deformation of body armour. There has been an University, Defence Academy of ▸ Non-perforating impacts on body armour can the United Kingdom, increasing awareness of BABT as an injury mechanism in result in a behind armour blunt trauma (BABT) Shrivenham, Wiltshire, UK both the military and civilian worlds; whether BABT 2 fi injury. Home Of ce Centre for results in serious injuries is debatable. Applied Science and ▸ Body armour standards typically describe the Method A systematic review of the openly accessible Technology, St Albans, measurement of back-face signature (BFS) in literature was conducted using the Preferred Reporting Hertfordshire, UK ‘clay’; BFS does not equate to a severity of Items for Systematic Reviews and Meta-Analyses method BABT injury in humans. Correspondence to to investigate those injuries classified as BABT and their ▸ There is no evidence of life-threatening BABT Dr D J Carr, Impact and severity. Armour Group, Department of injuries caused to people impacted against Results 50 sources were identified that included pertin- Engineering and Applied body armour designed to defeat the projectile Science, Cranfield Defence and ent information relevant to this systematic review on in question. -
Fm 90-40 (515
ARMY, MARINE CORPS, NAVY NLW ORPS C CO NE M I B R A A T M MULTISERVICE PROCEDURES D FOR THE E D V N TACTICAL EMPLOYMENT OF E A L O M P M NONLETHAL WEAPONS MENT CO FM 90-40 MCRP 3-15.8 NWP 3-07.31 USCG PUB 3-07.31 AIR LAND SEA OCTOBER 1998 APPLICATION CENTER DISTRIBUTION RESTRICTION: Approved for public release; distribution is unlimited. MULTISERVICE TACTICS, TECHNIQUES, AND PROCEDURES FOREWORD This publication has been prepared under our direction for use by our respective commands and other commands as appropriate. WILLIAM W. HARTZOG J. E. RHODES General, USA Lieutenant General, USMC Commander Commanding General Training and Doctrine Command Marine Corps Combat Development Command G. S. HOLDER Rear Admiral, USN Commander Naval Doctrine Command PREFACE 1. Scope employment of NLW during exercises and contingencies. This publication describes multiservice tactics, techniques, and procedures (MTTP) b. The United States (US) Army, for consideration and use during the Marine Corps, Navy, and Coast Guard tactical employment of nonlethal weapons approved this multiservice publication. (NLW) in support of warfighting personnel conducting training and tactical operations. 4. Implementation Plan This publication— Participating service command offices a. Provides an overview of NLW. of primary responsibility (OPRs) will review this publication, validate the b. Provides NLW system description/ information, and reference and incorporate interoperability. it in service manuals, regulations, and curricula as follows: c. Describes the capabilities of NLW. Army. The Army will incorporate the d. Discusses training with the NLW procedures in this publication in US Army capability set. training and doctrinal publications as directed by the commander, US Army e. -
Ballistic Composites – Protecting the Protectors
Reinforced Plastics Volume 61, Number 2 March/April 2017 www.reinforcedplastics.com FEATURE Ballistic composites – protecting the protectors George Marsh It seems scarcely credible that thin polymer fibers, bound together in resin, can stop projectiles ranging from a hand-gun bullet to a high-power rifle round, but they can and have done so, saving many lives in the process. Composite body armor protects a wide range of civilians from security guards to police officers and from bailiffs to VIPs. But of course, it is military forces who are the leading user group. degraded. Second is a slowing phase and third is the catching of Traditional solutions for 20th Century military armor, based the round so that it is retained within the protective garment. chiefly on steel and ceramic plates, were really too heavy for Laminates are designed to maximize the effectiveness of these soldiers, indeed for many vehicles as well. Composites have in- stages. Outer layers that provide controlled delamination on creasingly proved to be the answer, being much lighter for the impact are effective in deforming the tip of a projectile, thereby same stopping power and more pliable. Certain polymer compo- blunting it. Certain non-polymer composites, for instance those sites show, when appropriately engineered, remarkable energy that are ceramic based, may be harder than polymer composites dissipation properties, being able to absorb the kinetic energy and therefore more effective in this phase. Even so, reinforced from bullets and other high-speed projectiles before these can plastics often provide the best balance of weight, anti-ballistic harm their human targets. -
United States Patent (10) Patent No.: US 8.490,212 B1 Asher Et Al
USOO8490212B1 (12) United States Patent (10) Patent No.: US 8.490,212 B1 Asher et al. (45) Date of Patent: Jul. 23, 2013 (54) QUICK RELEASE GARMENT 4,697.285 A 10/1987 Sylvester 5,060,314 A 10, 1991 Lewis 5,259,093 A 11/1993 D'Annunzio (75) Inventors: Matthew Asher, Imperial, MO (US); 5,331,683 A * 7/1994 Stone et al. ........................ 2.25 Carl James Quinlan, Maysville, NC 5,495,621 A 3, 1996 Kibbee (US) 5,512.348 A 4/1996 Mazelsky 5,516,234 A 5/1996 Duchesne (73) Assignee: Eagle Industries Unlimited, Inc., 5,785,0115,724,707 A 7/19983, 1998 Gitterman,Kirk et al. III Fenton, MO (US) 5,806.740 A 9/1998 Carlson 5,897,468 A 4/1999 Lumpkin (*) Notice: Subject to any disclaimer, the term of this 5,966,747 A 10/1999 Crupi et al. patent is extended or adjusted under 35 93.9 A 538 aXOal. U.S.C. 154(b) by 1899 days. 6,098,196 A 8/2000 Logan 6,138,277 A * 10/2000 Gillen et al. ...................... 2,102 (21) Appl. No.: 11/671,068 6,164.048 A 12/2000 Rhodes 6,185,738 B1 2/2001 Sidebottom (22) Filed: Feb. 5, 2007 6,308,334 B1 10/2001 Maas 6.421,833 B2 7/2002 Khanamirian et al. (51) Int. Cl. (Continued) (52) it.to: (2006.01) FOREIGN PATENT DOCUMENTS Src.w. 2/2.5: 2/462 CA 642244 6, 1962 (58) Field of Classification Search OTHER PUBLICATIONS S. licati - - - - - file? - - - - - - - - - - i. -
Glossary of Terms: the Things They Carried
Glossary of Terms: The Things They Carried “The Things They Carried” rucksack A kind of knapsack strapped over the shoulders. foxhole A hole dug in the ground as a temporary protection for one or two soldiers against enemy gunfire or tanks. perimeter A boundary strip where defenses are set up. heat tabs Fuel pellets used for heating C rations. C rations A canned ration used in the field in World War II. R & R Rest and recuperation, leave. Than Khe (also Khe Sahn) A major battle in the Tet Offensive, the siege lasted well over a month in the beginning of 1968. Khe Sahn was thought of as an important strategic location for both the Americans and the North Vietnamese. American forces were forced to withdraw from Khe Sahn. SOP Abbreviation for standard operating procedure. RTO Radio telephone operator who carried a lightweight infantry field radio. grunt A U.S. infantryman. hump To travel on foot, especially when carrying and transporting necessary supplies for field combat. platoon A military unit composed of two or more squads or sections, normally under the command of a lieutenant: it is a subdivision of a company, troop, and so on. medic A medical noncommissioned officer who gives first aid in combat; aidman; corpsman. M-60 American-made machine gun. PFC Abbreviation for Private First Class. Spec 4 Specialist Rank, having no command function; soldier who carries out orders. M-16 The standard American rifle used in Vietnam after 1966. flak jacket A vestlike, bulletproof jacket worn by soldiers. KIA Abbreviation for killed in action, to be killed in the line of duty. -
Certified for Publication in the Court of Appeal of The
Filed 12/17/09 CERTIFIED FOR PUBLICATION IN THE COURT OF APPEAL OF THE STATE OF CALIFORNIA SECOND APPELLATE DISTRICT DIVISION THREE THE PEOPLE, B204646 Plaintiff and Respondent, (Los Angeles County Super. Ct. No. NA073164) v. ETHAN SALEEM, Defendant and Appellant. APPEAL from a judgment of the Superior Court of Los Angeles County, John David Lord, Judge. Reversed. Gerald Peters, under appointment by the Court of Appeal, for Defendant and Appellant. Edmund G. Brown, Jr., Attorney General, Dane R. Gillette, Chief Assistant Attorney General, Pamela C. Hamanaka, Assistant Attorney General, Lance E. Winters and Roberta L. Davis, Deputy Attorneys General, for Plaintiff and Respondent. _________________________ Defendant and appellant, Ethan Saleem, appeals the judgment entered following his conviction for possession of body armor by a person previously convicted of a violent felony, with prior serious felony and prior prison term findings (Pen. Code, §§ 12370, 667, subd. (b)-(i), 667.5.)1 He was sentenced to state prison for a term of eight years. We reverse Saleem‘s conviction. Section 12370 is unconstitutionally void for vagueness because it does not provide fair notice of which protective body vests constitute the body armor made illegal by the statute. BACKGROUND Viewed in accordance with the usual rule of appellate review (People v. Ochoa (1993) 6 Cal.4th 1199, 1206), the evidence established the following. 1. Saleem’s arrest. On January 23, 2007, at about 3:00 a.m., Los Angeles Police Officer Jeffrey Rivera and his partner were on patrol in Wilmington. Rivera was in the passenger seat of their marked patrol car. He saw an approaching vehicle make a quick right turn and pull off to the side of the road. -
“Big Boomers”—Rifle Power Designed Into Handguns
“BIG BOOMERS” Rifle Power Designed Into Handguns Violence Policy Center The Violence Policy Center (VPC) is a national non-profit educational organization that conducts research and public education on violence in America and provides information and analysis to policymakers, journalists, advocates, and the general public. This report was authored by VPC Senior Policy Analyst Tom Diaz. This report was funded in part with the support of The Herb Block Foundation and The Joyce Foundation. Past studies released by the VPC include: • When Men Murder Women: An Analysis of 2006 Homicide Data (September 2008) ! American Roulette: Murder-Suicide in the United States (April 2008) ! Black Homicide Victimization in the United States: An Analysis of 2005 Homicide Data (January 2008) ! When Men Murder Women: An Analysis of 2005 Homicide Data (September 2007) ! An Analysis of the Decline in Gun Dealers: 1994 to 2007 (August 2007) ! Drive-By America (July 2007) ! A Shrinking Minority: The Continuing Decline of Gun Ownership in America (April 2007) ! Black Homicide Victimization in the United States: An Analysis of 2004 Homicide Data (January 2007) ! Clear and Present Danger: National Security Experts Warn About the Danger of Unrestricted Sales of 50 Caliber Anti-Armor Sniper Rifles to Civilians (July 2005) ! Safe At Home: How D.C.’s Gun Laws Save Children’s Lives (July 2005) ! The Threat Posed to Helicopters by 50 Caliber Anti-Armor Sniper Rifles (August 2004) ! United States of Assault Weapons: Gunmakers Evading the Federal Assault Weapons Ban (July -
The BJA/PERF Body Armor National Survey (2009)
The BJA/PERF Body Armor National Survey: Protecting the Nation’s Law Enforcement Officers PHASE II FINAL REPORT TO BJA | AUGUST 9, 2009 PERF Project Staff: Bruce Taylor, Ph.D., Research Director | Bruce Kubu, Survey Director | Kristin Kappleman, Research Associate | Hemali Gunaratne, Boston Police Department | Nathan Ballard, Research Assistant | Mary Martinez, Research Assistant Bureau of Justice Assistance U.S. Department of Justice The BJA/PERF Body Armor National Survey: Protecting the Nation’s Law Enforcement Officers Phase II Final Report to BJA August 9, 2009 PERF Project Staff: Bruce Taylor, Ph.D., Research Director Bruce Kubu, Survey Director Kristin Kappleman, Research Associate Hemali Gunaratne, Boston Police Department Nathan Ballard, Research Assistant Mary Martinez, Research Assistant This publication was supported by the Bureau of Justice Assistance. The points of view expressed herein are the authors’ and do not necessarily represent the opinions of the Bureau of Justice Assistance or individual Police Executive Research Forum members. Police Executive Research Forum, Washington, D.C. 20036 Copyright 2009 by Police Executive Research Forum All rights reserved Edited by Craig Fischer Cover and interior design by Dave Williams Contents Executive Summary ........................................................................1 Introduction ....................................................................................5 Review of Relevant Literature ...................................................... 6 Research Methods -
The U.S. Citizen-Soldier and the Global War on Terror: the National Guard Experience
SEPTEMBER 2007 Strengthening the humanity and dignity of people in crisis through knowledge and practice The U.S. Citizen-Soldier and the Global War on Terror: The National Guard Experience By Larry Minear SEPTEMBER 2006 Strengthening the humanity and dignity of people in crisis through knowledge and practice The Feinstein International Center develops and promotes operational and policy responses to protect and strengthen the lives and livelihoods of people living in crisis-affected and -marginalized communities. FIC works globally in partnership with national and international organizations to bring about institutional changes that enhance effective policy reform and promote best practice. This and other reports are available online at fi c.tufts.edu. The U.S. Citizen-Soldier and the Global War on Terror: The National Guard Experience By Larry Minear © 2007 Feinstein International Center. All Rights Reserved. Fair use of this copyrighted material includes its use for non-commercial educa- tional purposes, such as teaching, scholarship, research, criticism, commentary, and news reporting. Unless otherwise noted, those who wish to reproduce text and image fi les from this publication for such uses may do so without the Feinstein International Center’s express permission. However, all commercial use of this material and/or reproduction that alters its meaning or intent, without the express permission of the Feinstein International Center, is prohibited. “In-Country” by Brian Perry, copyright © 2006 by Brian Perry, from OPERATION HOMECOMING, edited by Andrew Carroll. Used by permission of Random House, Inc. For on line information about other Random House, Inc. books and authors, see the Internet Web Site at http://www.randomhouse.com. -
FM 3-19.15, Civil Disturbance Operations
FM 3-19.15 CIVIL DISTURBANCE OPERATIONS Headquarters, Department of the Army April 2005 DISTRIBUTION RESTRICTION: Approved for public release; distribution is unlimited. This publication is available at Army Knowledge Online (www.us.army.mil) and General Dennis J. Reimer Training and Doctrine Digital Library at (http://www.train.army.mil) *FM 3-19.15 (FM 19-15) Field Manual Headquarters No. 3-19.15 Department of the Army Washington, DC, 18 April 2005 Civil Disturbance Operations Contents Page PREFACE .................................................................................................................. iv Chapter 1 OPERATIONAL THREATS OF THE CIVIL DISTURBANCE ENVIRONMENT...... 1-1 General Causes for Civil Unrest............................................................................... 1-1 Crowd Development................................................................................................. 1-2 Gatherings................................................................................................................ 1-2 Crowd Building ......................................................................................................... 1-4 Dispersal Process of a Gathering ............................................................................ 1-4 Crowd Dynamics ..................................................................................................... 1-5 Crowd Types ............................................................................................................ 1-6 Crowd Tactics -
NIJ Level IIIA
RESTRICTED TENDER SPECIFICATION OF FLAK JACKET (NIJ LEVEL IIIA) 1. Name of the Item Flak Jacket (NIJ Level IIIA). 2. Purpose The main purpose of the Flak Jacket is to provide protection and safety of the wearer from various harms and injuries caused by fragments from exploded munitions and different weapons. 3. Quantity : 700 in no (Large: 100 in no, Medium: 500 in no and Small: 100 in no). 4. Year of Manufacture : 2021 or later. 5. Brand/Model : To be mentioned. 6. Name of Manufacturer : Name and full address is to be mentioned. 7. Country of Origin : Australia, Canada, Denmark, France, Germany, Italy, Japan, Singapore, Turkey, Netherlands, Norway, Sweden, USA, UK (To be mentioned). 8. Manufacturing Country : Australia, Canada, Denmark, France, Germany, Italy, Japan, Singapore, Turkey, Netherlands, Norway, Sweden, USA, UK (To be mentioned). 9. Qualification of Bidder. Only the enlisted supplier of DGDP can submit quotation from the genuine manufacturer or their authorized dealer(s). Manufacturer’s authorization Certificate is to be submitted with the offer. In case of dealer, manufacturer has to authorise the dealer and dealer has to authorize the supplier. In this regard both authorization certificates is to be submitted with the offer. 10. Description. The Flak Jacket must fulfill the requirement of National Institute of Justice (NIJ) Standard. The ballistic material is polyethylene (Dyneema) or Aramid (Twaron/ Kevlar), which offers protection of NIJ IIIA. All portions of the jacket without the Armour panel must qualify minimum NIJ protection level IIIA. the outer cover of the jacket should be Digital Combat cloth and shuld be removable for washing /cleaning. -
Ballistics & Polyurea Coatings
TECHNOLOGY REPORT: Ballistics & Polyurea Coatings written by: Dudley J. Primeaux, II, PCS, CCI Director of Education and Development and Todd A. Gomez, PCS VersaFlex is a proud and participating member of the following trade associations and groups: POLYUREA WHITE PAPER The Impact: Traveling Faster than the Speed of Sound, Protective Coatings at Work Dudley J Primeaux II, PCS, CCI and Todd Gomez, PCS VersaFlex Incorporated, 686 S. Adams Street, Kansas City, KS 66105 USA www.versaflex.com Learning Objectives: Discuss history and new advances related to polyurea spray coating systems in ballistic applications, present the history of this application work, achieve an un- derstanding that the polyurea technology is: not bullet proof, offers elastomeric qualities for protection, protects crucial substrates, and possess ballistic qualities. Abstract: When protective coatings are considered for application work, normal uses such as concrete coating, waterproofing, abrasion protection; steel corrosion protection; and, other protective applications are the norm. However, there is a whole world of other uses for protective coatings including personal protection applications. The reality is that coating systems are being used for a variety of government, military, police and personal protection applications with excellent results. And the “polyurea” technology has been leading the way in this application area. And while there has been some misleading information presented or implied over the years, this presentation will discuss the history related to this subject and polyurea, and will present the truth and facts, polyurea coating and lining systems are NOT bullet proof, but does have ballistic qualities! INTRODUCTION “The heart Ramon. Don’t forget the heart.