Processing of the Kansk-Achinsk Brown Coal Into Synthetic Fuel
Total Page:16
File Type:pdf, Size:1020Kb
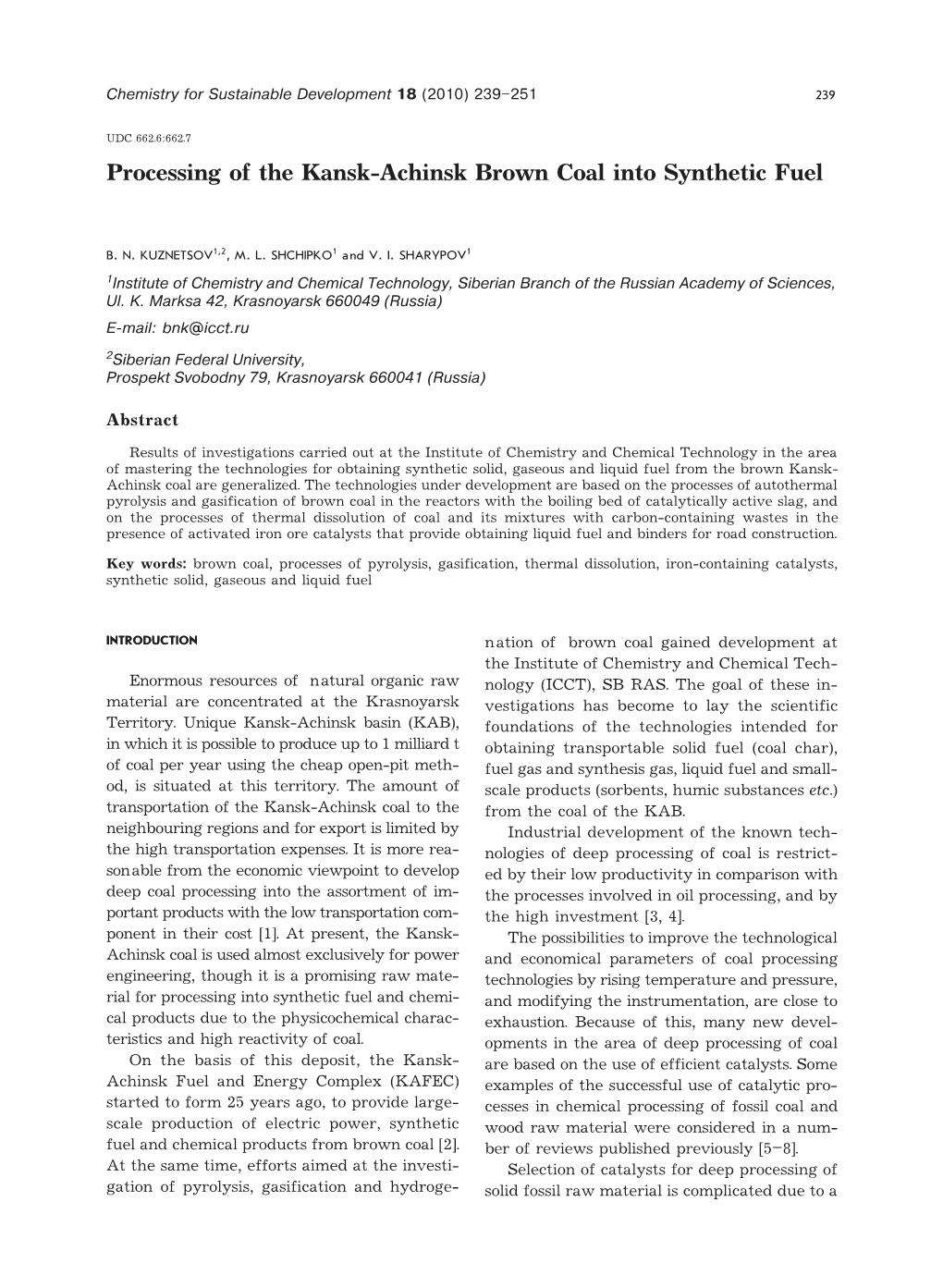
Load more
Recommended publications
-
Sociocultural and Linguistic Contexts of the Russian Sign Language Functioning in Krasnoyarsk Krai
Journal of Siberian Federal University. Humanities & Social Sciences 2020 13(3): 296-303 DOI: 10.17516/1997-1370-0565 УДК 16.21.27 Sociocultural and Linguistic Contexts of the Russian Sign Language Functioning in Krasnoyarsk Krai Liudmila V. Kulikova and Sofya A. Shatokhina Siberian Federal University Krasnoyarsk, Russian Federation Received 21.02.2020, received in revised form 25.02.2020, accepted 06.03.2020 Abstract. The article contains an ethnographic description of the conditions governing the use of the regional sign language in Krasnoyarsk Krai within the modern sociolinguistic context. The subject of the discussion is the problem of the linguistic design of sign languages in general, including some features of Russian Sign Language. The study provides statistical information and legal norms for the use of this iconic communication system. A study of the current state of Russian Sign Language functioning in Krasnoyarsk Krai allows us to talk about a change in the status of this sign language, an increasing interest in issues related to its applied significance, and reinforces the need to develop new theoretical approaches to its institutionalization. Keywords: Russian Sign Language, fingerspelling, regional variants, Krasnoyarsk krai, language policy. This research is supported by the Russian Foundation for Basic Research (RFBR), Grant No. 20-012-00321 “Regional sign languages: multimodal electronic corpus (the case of the communicative space of Eastern Siberia)”. Research area: linguistics. Citation: Kulikova, L.V., Shatokhina, S.A. (2020). Sociocultural and linguistic contexts of the Russian Sign Language functioning in Krasnoyarsk Krai. J. Sib. Fed. Univ. Humanit. Soc. Sci., 13(3), 296-303. DOI: 10.17516/1997-1370-0565. -
Load Article
Arctic and North. 2018. No. 33 55 UDC [332.1+338.1](985)(045) DOI: 10.17238/issn2221-2698.2018.33.66 The prospects of the Northern and Arctic territories and their development within the Yenisei Siberia megaproject © Nikolay G. SHISHATSKY, Cand. Sci. (Econ.) E-mail: [email protected] Institute of Economy and Industrial Engineering of the Siberian Department of the Russian Academy of Sci- ences, Kransnoyarsk, Russia Abstract. The article considers the main prerequisites and the directions of development of Northern and Arctic areas of the Krasnoyarsk Krai based on creation of reliable local transport and power infrastructure and formation of hi-tech and competitive territorial clusters. We examine both the current (new large min- ing and processing works in the Norilsk industrial region; development of Ust-Eniseysky group of oil and gas fields; gasification of the Krasnoyarsk agglomeration with the resources of bradenhead gas of Evenkia; ren- ovation of housing and public utilities of the Norilsk agglomeration; development of the Arctic and north- ern tourism and others), and earlier considered, but rejected, projects (construction of a large hydroelectric power station on the Nizhnyaya Tunguska river; development of the Porozhinsky manganese field; place- ment of the metallurgical enterprises using the Norilsk ores near Lower Angara region; construction of the meridional Yenisei railroad and others) and their impact on the development of the region. It is shown that in new conditions it is expedient to return to consideration of these projects with the use of modern tech- nologies and organizational approaches. It means, above all, formation of the local integrated regional pro- duction systems and networks providing interaction and cooperation of the fuel and raw, processing and innovative sectors. -
The Ethno-Linguistic Situation in the Krasnoyarsk Territory at the Beginning of the Third Millennium
View metadata, citation and similar papers at core.ac.uk brought to you by CORE provided by Siberian Federal University Digital Repository Journal of Siberian Federal University. Humanities & Social Sciences 7 (2011 4) 919-929 ~ ~ ~ УДК 81-114.2 The Ethno-Linguistic Situation in the Krasnoyarsk Territory at the Beginning of the Third Millennium Olga V. Felde* Siberian Federal University 79 Svobodny, Krasnoyarsk, 660041 Russia 1 Received 4.07.2011, received in revised form 11.07.2011, accepted 18.07.2011 This article presents the up-to-date view of ethno-linguistic situation in polylanguage and polycultural the Krasnoyarsk Territory. The functional typology of languages of this Siberian region has been given; historical and proper linguistic causes of disequilibrum of linguistic situation have been developed; the objects for further study of this problem have been specified. Keywords: majority language, minority languages, native languages, languages of ethnic groups, diaspora languages, communicative power of the languages. Point Krasnoyarsk Territory which area (2339,7 thousand The study of ethno-linguistic situation in square kilometres) could cover the third part of different parts of the world, including Russian Australian continent. Sociolinguistic examination Federation holds a prominent place in the range of of the Krasnoyarsk Territory is important for the problems of present sociolinguistics. This field of solution of a number of the following theoretical scientific knowledge is represented by the works and practical objectives: for revelation of the of such famous scholars as V.M. Alpatov (1999), characteristics of communicative space of the A.A. Burikin (2004), T.G. Borgoyakova (2002), country and its separate regions, for monitoring V.V. -
Economic Commission for Europe Inland Transport Committee Draft Proposal of Amendments to European Agreement Concerning the Inte
INF.3/Add.1 Economic Commission for Europe Inland Transport Committee Working Party on the Transport of Dangerous Goods Ninety-third session 12 September 2012 Geneva, 5-9 November 2012 Item 6(b) of the provisional agenda Proposals for amendments to Annexes A and B of ADR: miscellaneous proposals Draft Proposal of amendments to European Agreement concerning the International Carriage of Dangerous Goods by Road Transmitted by the International Dangerous Goods and Containers Association (IDGCA) Addendum INF.3/Add.1 2 INF.3/Add.1 3 INF.3/Add.1 4 INF.3/Add.1 Routes and volumes of bulk cargo transportation by multimodal transport in flexible bulk containers MK-14-10 Item Route (kind of transport) Distance, km Qty, th. No. tonnes -1- -2- -3- -4- 1. Astrakhan – Taganrog commercial seaport (Russia): 937 36.7 Granulated sulfur (Cl. 4.1, No.OOH 1350) 1.1 Motor transport: Plant "Astrakhangazprom" – River port in 27 36.7 Set. Buzan on the Volga (Russia) 1.2 River-sea vessel: River port in Set. Buzan – Taganrog 910 36.7 commercial seaport (Russia) 2. Astrakhan – Tuapse commercial seaport (Russia): 1,249/1,036 28.05 Granulated sulfur (Cl. 4.1, No.OOH 1350) 2.1 Open railway car: Enterprise "Astrakhangazprom" – 1,249/1,036 28.05 Tuapse/Taganrog commercial seaport (Russia) 3. Gorlovka – Mariupol commercial seaport (Ukraine): coal- 176 181.3 tar pitch (Cl. 9 No.OOH 3077) 3.1 Support service open railway car: Through the territory of 1 181.3 Gorlovka "Smolopererabatyvayushchy zavod" (Ukraine) 3.2 Open railway car: Gorlovka "Smolopererabatyvayushchy 175 181.3 zavod" – Mariupol commercial seaport (Ukraine) 4. -
From Collecting to Studying the Folklore of Siberian Estonians and Latvians: Background
doi:10.7592/FEJF2014.58.background FROM COLLECTING TO STUDYING THE FOLKLORE OF SIBERIAN ESTONIANS AND LATVIANS: BACKGROUND Anu Korb In December 2008, the joint conference of Estonian and Latvian researchers of culture, ‘Compatriots in Siberia’, was held at the Estonian Literary Mu- seum (for the abstracts see The Estonian–Latvian Conference 2008). At the conference, an idea was put forward to compile a collection of articles based on the research of compatriots of these two countries in Siberia, to introduce the corresponding work and studies to a wider audience. The publication is now presented as a special issue of journal Folklore: Electronic Journal of Folklore. The articles published in this volume are authored by folklorists and ethnolo- gists from Estonia and Latvia. Among the conference participants were also linguists and teachers Lidia Leikuma, Alekseis Andronovs, Kristine Zute and Mara Mortuzane, who have carried out a study on the Latgalian language in the Latgale region of Krasnoyarsk Krai; Eta Nikolaeva and Solveta Logina, who have analysed the activities of winter workshops in Achinsk, Krasnoyarsk Krai; and ethnologist Igor Tõnurist, who has studied folk music practices and folk musicians in Siberia. At the conference two documentaries were screened: Liene Linde and Dainis Juraga’s No Country for Catholics, and Andres Kor- jus’s On Foreign Lands: Native Estonians in Siberia. In the White Hall of the University of Tartu History Museum, joint exhibition of the Estonian Literary Museum and the Estonian Academy of Arts, titled Siberi eestlased / Estonians in Siberia, was displayed (the curators of the exhibition were Anu Korb and Kadri Viires). -
Download Article
Advances in Social Science, Education and Humanities Research (ASSEHR), volume 103 2017 International Conference on Culture, Education and Financial Development of Modern Society (ICCESE 2017) The Formation of Professional Music Education in the System of Academic Traditions in Yeniseisk Province Evgenya Tsareva Maria Chikhacheva Krasnoyarsk State Institute of Arts Krasnoyarsk State Institute of Arts Krasnoyarsk, Russia Krasnoyarsk, Russia E-mail: [email protected] E-mail: [email protected] Abstract—The case study presented in the article analyzes Functioning and development of academic traditions in unpublished archive materials and scientific papers to the society requires a complex system of musical investigate the role that music education has played in the communication. Asafiev B.V. pointed out three main formation of regional system of academic traditions in components of its base - the activity of the three main Yeniseisk Province. The authors examine professional music subjects: the composer, performer and listener. [1] However, education establishing in Krasnoyarsk region in the period of an essential link in the "chain" is an educator. Thus, among imperial and Soviet past. Analyzing local materials from social the main elements forming the academic musical culture are: and cultural perspectives gives new results in the study of composer creativity, performance, listener and education, historical events. Along with that, it illuminates the importance which in turn become the whole system for the element base of self-organizational processes in the development of regional of a lower order. culture and fully covers the role of musical and educational institutions in successful development of the academic model in This multicomponent structure, provided that each of the Yeniseisk province in the light of "center-periphery" problem. -
Transport Assets
Company overview Strategic report Commodity market Business overview Sustainable Corporate Risk report Shareholder information IFRS financial statements Appendix overview development governance TRANSPORT ASSETS Nornickel owns a modern transport infrastructure capable of handling most challenging freight logistics tasks and ensuring continuity and sustainability of operations. Nornickel’s transportation and logistics assets cover the full range of transportation and freight forwarding services. 1 Murmansk Transport 3 Norilsk Airport, Norilsk 5 Krasnoyarsk Transport 7 Bystrinsky Division (Murmansk Avia, NordStar Airlines Division, Krasnoyarsk Transport terminal, 6 heavy-duty (100% stake) River Port (89% stake) Division ice-class vessels) and Nornickel-ERP LLC 2 Arkhangelsk 4 Polar Transport Division 6 Yenisey River Shipping 8 Lesosibirsk Port Transport Division (Dudinka Port) Company (82% stake) (51% stake) 1 4 3 6 2 8 5 7 96 97 Company overview Strategic report Commodity market Business overview Sustainable Corporate Risk report Shareholder information IFRS financial statements Appendix «NORNICKEL» overview development governance Annual report 2019 FREIGHT SHIPPING SERVICES Nornickel has a unique Arctic fleet comprising Dry cargo transportation by Nornickel’s fleet five dry cargo vessels and one Yenisey heavy-duty (mln t) ice-class tanker (ARC 7 as per the classification of the Russian Maritime Register of Shipping). ‘19 1.3 0.2 231.5 The vessels are capable of breaking through Arctic ‘18 1.2 0.2 1.4 ice up to 1.5 m thick without icebreaker support. ‘17 1.1 0.2 1.3 The Yenisey tanker carries gas condensate exports For Nornickel For third parties from the Pelyatkinskoye gas condensate deposit to European ports, and makes commercial voyages to other destinations. -
Bringing HIV Care Closer to a Patient: Results of Krasnoyarsk Experience
Bringing HIV Care Closer to a Patient: Results of Krasnoyarsk Experience Irina Tirikova Краевой центр СПИД, г. Красноярск 2016 European HIV Nursing Conference Barcelona Location of Krasnoyarsky Krai in Russia Krasnoyarsky Kray is the second largest subject of the Russian Federation, and covers 14% of its territory Length of Krai 3000 km, and maximal width – 1500 km Population - 2 893 923. HIV dinamics in the Russian Federation, Siberian Federal District and Krasnoyarsky Kray (newly identified cases per 100 000 population) SFD Kray RF HIV in Krasnoyarsky Krai Taymyr 29 297 cases of HIV infection have been registered in (Arctic Krasnoyarsky Kray, as of 01/09/2016. Ocean) Area Most affected cities and towns: Krasnoyarsk, Norilsk (the largest city in the world above Polar Circle), Yeniseysk, Norilsk Sosnovoborsk and Achinsk Major transmission routes: 56% - IDUs 43% - Unprotected Sex (heterosexual) 1% - vertical and MSM 63% - Men Yeniseys district 37% - Women Yeniseysk Age groups: Lesosibirsk Kezemsky 15-30 y.o – 52% area 31-45 y.o. – 45% KRASNOYARSK ARV initiation: CD4<350 cells Achinsk Borodino Sosnovoborsk Structure of the AIDS Center in Krasnoyarsk Clinical Department Department of Laboratory Inf.Dis. Physician – 7 psychosocial services - Immunoferment assays, ELISA Pediatrician – 1 Chief of department - internist - Immunology STI specialist – 1 Infectious Diseases Doctor - Biochemical profiles and CBC Gynecologist – 2 Psychologist - 2 - Bacterial Psychiatrist - PCR TB doctor – 1 Social worker Feldsher– 1 Feldsher Nurse – 12 Nurse - 2 2 -
Coal Mine Methane Country Profiles, Chapter 26, Updated March 2020
RUSSIAN FEDERATION 26 RUSSIAN FEDERATION 26.1 Summary of Coal Industry With the world’s largest natural gas reserves and second-largest coal reserves (see Table 26-1), Russia plays an important role in coal mine methane (CMM) research and project development. Russian coal and gas exports have continued to grow and are focused on the rapidly growing East Asian energy market. With the Russian government’s 2009 decree on increased power generation, CMM development was highlighted as a way for Russian companies to increase earnings while decreasing pollution. On September 23, 2019, Russia, the fourth-largest contributor of greenhouse gases globally, ratified the Paris Agreement on Climate Change. Although the geographic isolation of Russia’s coalfields is a barrier to CMM production, pre- existing pipelines and strong natural gas markets in Europe and Asia, coupled with rising domestic natural gas prices, may help incentivize CMM capture and utilization projects in Russia. 26.1.1 ROLE OF COAL IN RUSSIA • Coal accounts for 13.2 percent of Russia’s total primary energy consumption. • Coal production increased by 43.7 percent between 2007 and 2017 (Figure 26-1). • Russia’s electricity generation in 2017 was split between natural gas (52.3 percent), oil (21.9 percent), coal (13.2 percent), nuclear (6.5 percent), and hydroelectric (5.9 percent) (BP, 2018). Table 26-1. Russia’s Coal Reserves and Production Sub- Anthracite & Total bituminous & Global Rank Indicator Bituminous (million Lignite (# and %) (million tonnes) tonnes) (million tonnes) Estimated Proved Coal 69,634 90,730 160,364 2 (15.5%) Reserves (2017) Annual Coal Production 431.76 6 (5.5%) (2018) Sources: BP (2018), S&P Global Platts (2019). -
Features of Logistics Formation in the Yenisei Province
E3S Web of Conferences 217, 11015 (2020) https://doi.org/10.1051/e3sconf/202021711015 ERSME-2020 Features of logistics formation in the Yenisei province Yuliya Lukinykh1,* and Dmitry Kuskashev2 1Krasnoyarsk State Pedagogical University named after V.P.Astafiev, 89 Lebedevoy str., 660049, Krasnoyarsk, Russia 2Krasnoyarsk State Agrarian University, 117 Lenina str., 600000, Krasnoyarsk, Russia Abstract. The article deals with the features of logistics formation in the Yenisei province in the late XIX – early XX century. The measures aimed at ensuring food supply and basic necessities to the population, restraining the growth of prices, through the implementation of a mechanism for their regulation are considered. The article analyzes transport logistics as a link in the economic system of the Yenisei province, namely: the transport problems of the period under review are listed, the importance of the construction of the Trans-Siberian railway and the development of navigation are emphasized. The conclusion is made about the prerequisites for the economic development of the Yenisei province in the XXth century. 1 Introduction Changes taking place at the present stage in the economic and social life of Russia are directly related to the formation and development of capitalism in Russian society, and this, in turn, causes the need for a deeper understanding of the socio-economic aspect of Russian history. In this regard, the history of Russia in the XIX century occupies a special place, since it was during this period that our country's transition to capitalism took place. For a deep and objective understanding of the country's development, its economic, social, political, and cultural life, more detailed regional historical works are needed. -
Assessing the Interrelation Between Socio-Economic and Innovative-Technological Development, Institutional Conditions and Urbanization Processes in the Resource-Based
Journal of Siberian Federal University. Humanities & Social Sciences … (201… …) 000 ~ ~ ~ УДК 332.055:325.111(571.51) Assessing the Interrelation between Socio-Economic and Innovative-Technological Development, Institutional Conditions and Urbanization Processes in the Resource-Based Regions Using Dynamic Economic and Statistical Models Anna Semenova, Evgenia Bukharova, Irina Popelnitskaya, Natalia Nepomnyashchaya and Veronica Razumovskaya* Siberian Federal University 79/10 Svobodny Prospekt, Krasnoyarsk, 660041 Russia Received 12.11.2018, received in revised form 16.11.2018, accepted 19.11.2018 Relying on the current terms and patterns of development of any given region, strategic goals of the country’s spatial development and its institutional environment, urbanization impact on the economic and innovative-technological modernization of the territory is not identical. This research aims statistic data-based measurement of quantitative indicators which determine interrelation between the process of urbanization and dimensions for economic, innovative- technological and socio-cultural development of the regions with resource economy. In the framework of system analysis urbanized territories are considered as multi-component complex systems. Today’s tendencies in the practice of forecasting, planning and monitoring urbanized territories are focused on tackling a multi-criteria and multi-dimensional problem with a complicated system of constraints which is, traditionally, not judgment-based. This paper observes takes on modeling interrelation between the factors of socio-economic development and the level of urbanization in municipal settlements in the resource region – Krasnoyarskiy Krai – and on integrated ranking of urbanized territories based on dynamic changes of these factors. Keywords: resource-based economy, socio-economic and ecological development of urbanized territories, spatial development, living comfort, dynamic economic and statistical modeling, institutional conditions. -
July 2017 978.24 Kb
№ 32 July 2017 The corporate journal of AgroCentre Grand machinery showcase events as part Impressive of Demo Road Show 2017 have taken place in Voronezh and Penza oblasts. catwalk Pages 6-7 Hot topics: AgroCentre’s employees have undergone training held P by Kverneland in Germany….............................................................р. 2 P Michelin premier partner conference in Poland..............................р. 4 P Pioneers! AgroCentre customers — owners of unique machinery…..р. 8 Largesse and a vast machinery range have created the P signature feel of Siberian Field Day.................................................р. 9 www.agrozentr.ru 1 THE corporate JOURNAL № 32 July 2017 NEWS Clash of Titans A massive tracked tractor testing titled Clash of the Titans has been held in the fields of Studenetskiy Flour Mill OJSC. Penza branch of AgroCentreZakharovo has taken part in the contest and won it. except for the first being progress was measured using a somewhat more sloping. This GPS-navigator.’ did not prevent them from ‘It was a pitched battle, but we demonstrating brilliant results, gained the lead virtually on the though: the tractor delivered outset’, shares his impressions the best performance among Konstantin Karnaukhov, Service the rivals: 4.20 ha/h with the Department Technician of 12-body reversible plough AgroCentreZakharovo. ‘It was and 6.59 ha/h with the disc tricky to maintain the order in the cultivator. A total of 77.63 queue at the headlands at first, ha was cultivated with the but then we got the hang of it.’ machine over the testing period. ‘Along a straight line, the An average fuel consumption GPS- navigated tractor ran without amounted to 21.5 l/ha with the any issues: you simply sat and Service department day and to a disc cultivator plough and to 14.41 l/ha with watched’, adds Evgeniy Mikulich, technicians Konstantin on the second one.