Comparison of Heald Frame Motion Generated by Rotary Dobby And
Total Page:16
File Type:pdf, Size:1020Kb
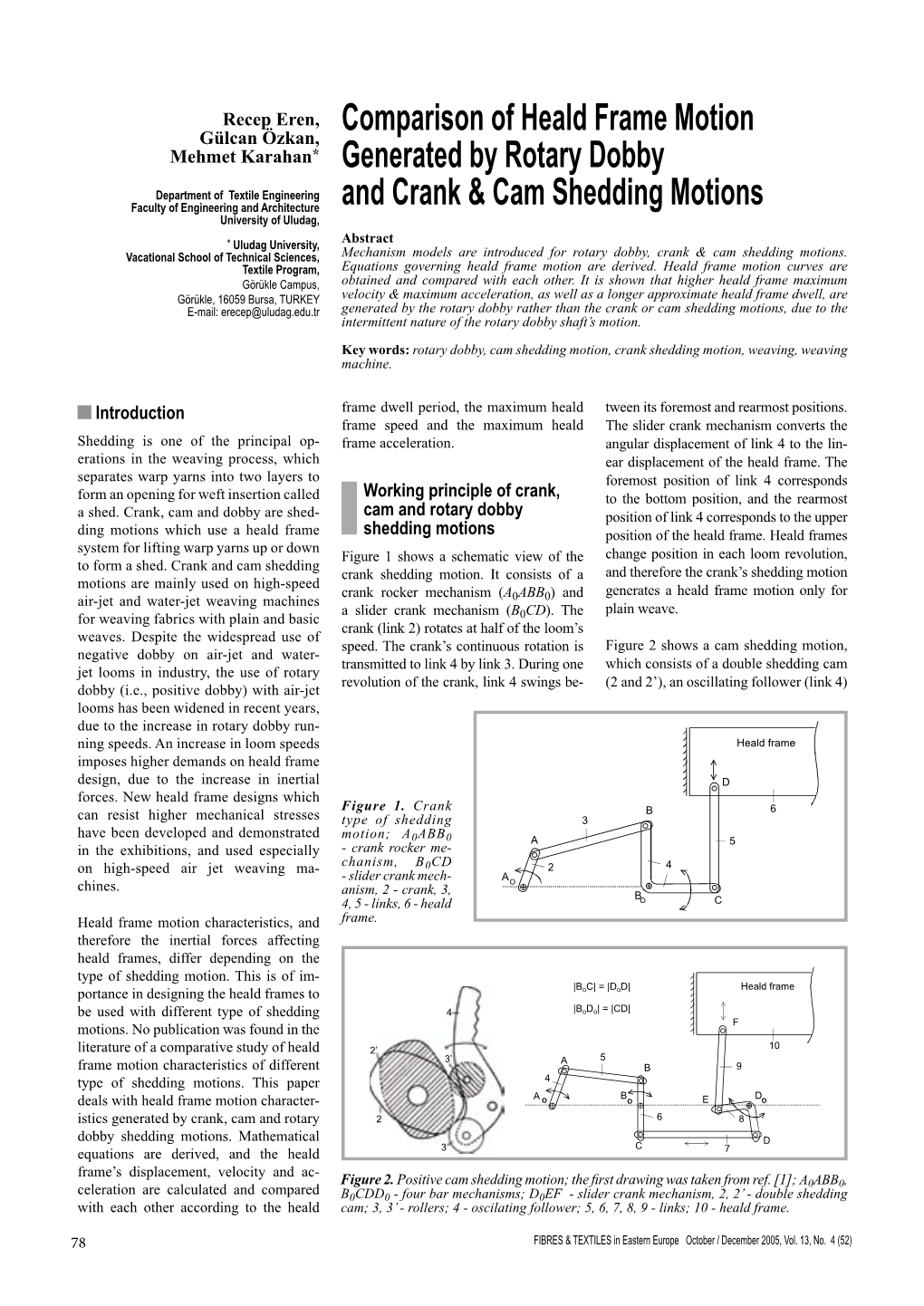
Load more
Recommended publications
-
M.Tech Program in Textile Engineering (First Year) W.E.F
D. K .T. E. Society’s Textile and Engineering Institute, Ichalkaranji (An Autonomous Institute) Department of Textiles DKTE Society’s TEXTILE & ENGINEERING INSTITUTE Rajwada, Ichalkaranji - 416115 (An Autonomous Institute) Curriculum (Structure and Syllabus) for M.Tech Program In Textile Engineering (First Year) w.e.f. August 2019 Ichalkaranji. Page 1 D.K.T.E. Society’s Textile and Engineering Institute, D. K .T. E. Society’s Textile and Engineering Institute, Ichalkaranji (An Autonomous Institute) Department of Textiles M. Tech. (Textile Engineering) Semester – I – Structure Teaching Scheme Sr. Course Name of the Course Group Theory Tutorial Practical Credit No. Code Hrs / Hrs / Hrs / Total week week week 1 TEL 501 High performance Fibres D 3 3 3 Advanced Computer Programming 2 TEL 502 D 3 3 3 and Applications 3 TEL 503 Theory of Textile Structures D 3 3 3 4 TEL EL1 Elective-I D 3 3 3 5 TEL EL2 Elective - II D 3 3 3 6 TED 511 Mini Project -I F 7* 7 7 Total 15 7 22 22 * Mini project involves field trials, experimental work, hence it is considered as full credit List of Electives -I List of Electives -II TEL551 Advanced Yarn Manufacturing TEL554 Advanced Fabric Manufacturing TEL552 Advanced Chemical Processing TEL555 Surface Treatment of Textiles TEL553 Apparel Engineering TEL556 Fibre Reinforced Composite Ichalkaranji. Page 2 D.K.T.E. Society’s Textile and Engineering Institute, D. K .T. E. Society’s Textile and Engineering Institute, Ichalkaranji (An Autonomous Institute) Department of Textiles M. Tech. (Textile Engineering) Semester – II – Structure Teaching Scheme Sr. Course Name of the Course Group Theory Tutorial Practical Credit No. -
B.Sc. Costume Design and Fashion FIBRE to FABRIC
B.Sc. CDF – Fibre to Fabric B.Sc. Costume Design and Fashion Second Year Paper No.3 FIBRE TO FABRIC BHARATHIAR UNIVERSITY SCHOOL OF DISTANCE EDUCATION COIMBATORE – 641 046. B.Sc. CDF – Fibre to Fabric 2 B.Sc. CDF – Fibre to Fabric CONTENT UNIT LESSON PAGE TITLE OF THE LESSON NO. NO. NO. UNIT I Textiles 1 7 Fibres 2 13 UNIT II Natural Fibres 3 27 Other Natural Fibres 4 35 Animal Fibres 5 47 Rayon 6 64 Synthtic Fibres 7 76 UNIT III 8 Introduction to spinning 93 Opening And Cleaning 9 103 Yarn Formation 10 114 Yarn MAINTENANCE 11 128 UNIT IV Weaving Preparatory Process 12 143 Drawing –In & Weft Preparation 13 155 Looming 14 163 Woven Fabric Basic Design 15 174 16 Woven Fabric Fancy Design 182 UNIT V Knitting 17 193 Non Woven 18 207 Other Fabrics 19 222 3 B.Sc. CDF – Fibre to Fabric (Syllabus) PAPER 3 FIBER TO FABRIC UNIT - I Introduction to the field of Textiles – major goals – classification of fibers – natural & chemical – primary and secondary characteristics of textile fibers UNIT - II Manufacturing process, properties and uses of natural fibers – cotton,linen,jute,pineapple, hemp, silk, wool, hair fibers, Man-made fibers – viscose rayon, acetate rayon, nylon, polyester, acrylic UNIT - III Spinning – definition, classification – chemical and mechanical spinning – ,opening, cleaning, doubling, carding, combing, drawing, roving, spinning Yarn classification – definition, classification – simple and fancy yarns, sewing threads and its properties UNIT - IV Woven – basic weaves – plain, twill, satin. Fancy weaves – pile, double cloth, leno, swivel, lappet, dobby and Jacquard Weaving technology – process sequence – machinery details UNIT - V Knitting type of knitting passage of material Knitting structure .Non-woven – felting, fusing, bonding, lamination, netting, braiding & calico, tatting and crocheting 4 B.Sc. -
View Course Detail
Department of Textile and Fibre Engineering TXL130 Polymer Chemistry methods of fibre mixing and blending. Principles of carding. Machine 3 Credits (3-0-0) elements and operations in card. Sliver formation, Sliver packaging, fibre configurations in sliver. Objectives, principles and methods The course will deal with chain and step growth polymerization of roller drafting. Purpose and principle of condensation of fibres. methods, polymer’s macromolecular architecture, molecular weight of Causes of mass variation of sliver and control. Automation and recent polymers, copolymerization, cross-linked polymers, general structure developments in blowroom, card and draw frames. Fibre opening, and characteristics of polymers, properties of fiber forming polymers carding and drawing for wool, jute and other fibres. Modification in and their applications. process parameters for processing blended fibres in blowroom, card and drawframe. TXL111 Textile Fibres 3 Credits (2-0-2) TXP221 Yarn Manufacture Laboratory-I Classification of fibres. Basic structure of a fibre. General properties 1 Credit (0-0-2) of a fibre such as moisture absorption, tenacity, elongation, initial modulus, yield point, toughness, elastic recovery. Relationship between Pre-requisites: TXL111 polymer structure and fiber properties. Detailed chemical and physical Experiments related to the lecture course entitled “Yarn Manufacture structure of natural fibres: cotton, wool and silk, their basic properties. I (TXL221)”. Introduction to important bast and leaf fibres. Basic introduction to Fibre spinning. Introduction Manmade and synthetic fibres: TXL222 Yarn Manufacture-II Viscose, Acetate, Acrylic, Nylon, polyester. High Performance Fibres. 3 Credits (3-0-0) Laboratory exercises would include experiments on fibre identification Pre-requisites: TXL221 through physical appearance, microscopic (optical, SEM), and burning Fibre fractionation and combing. -
SHEDDING FAQ 1) A) for a 5 up 3 Down Twill Weave, the Crank Shaft
SHEDDING FAQ 1) a) For a 5 up 3 down twill weave, the crank shaft, bottom shat and tappet shaft r.p.m. is X, Y and Z. Determine X: Y: Z. b) For a 4 up 2 down twill weave, the crank shaft, bottom shat and tappet shaft r.p.m. is X, Y and Z respectively. Determine X: Y: Z. 2) Why the lift of the back heald is more than that of front heald when the plain woven fabric is manufactured? Why the heald reversing rollers are having different diameters in a plain loom? 3) Calculate the lift of the cam controlling the back heald from the following particulars: Throw (lift) of the cam for the front heald = 10 cm The distance between the front and back heald = 2.5 cm The distance between the fulcrum and bowl on the treadle = 20 cm The distance between the bowl and the fastening point of the back heald = 20 cm Diameter of small reversing roller = 5 cm Diameter of large reversing roller = 6cm 4) What are early shedding and late shedding? What kind of shedding would be preferred for weaving the following i. Silk fabrics from filament yarns ii. Cotton fabric with very high areal density 5) Explain how the following profiles of shade depth are achieved with different shedding timing. Which profile will you choose for silk warp and why? 6) What is staggering of healds? How is it implemented in a loom with cam shedding mechanism? How warp breaks are reduced by this technique? 7) Derive the expression for strain in the warp yarn during the shedding operation if the total shed length is ‘L’, shed symmetry parameter is ‘i’ and vertical movement of the heald during shedding is ‘2h’. -
Strong Support for Air Jet Loom Operations T-Tech Japan Corp.’S Preparatory Machines, Including the Sizing Machines, Are Top-Level Performers and the Best-Quality
Balanced high productivity, value-addition, and energy saving at a high level Higher speed operation and extensive reduction in electrical and air consumption Higher Speed Energy Conservation Outstanding features for ultra i-Weave high-speed and low vibration With the “i-Weave,” provided as standard for High speed operation is the essential asset of the ZAX9200i, high-speed performance is air jet looms. accompanied with energy saving by optimizing In addition to stable operation at high speeds, the three basics of weft insertion for air jet looms: nozzle, valve, and control technology. faster than the ZAX9100, the ZAX9200i has low vibration and saves electricity. With a variety of optional devices, higher- grade performance is available. The “ -Weave” is the fruit of weft insertion ■ Soft weft insertion at high speed i technology backed by Tsudakoma’s 40-year Proven benefit based on actual operation. A accumulated air jet knowledge and our sales 4-link beating motion that works excellently success. at ultra-high speed is used for narrow looms. A 6-link beating motion with more time allowance for weft insertion is used for wider looms, thus achieving more stable weft insertion. ■ Reduced floor vibration Using CAE analysis, Tsudakoma designed a new robust frame structure. By employing the offset rocking shaft with less moment of inertia and a hollow reed holder, beating is well- balanced. Floor vibration can be reduced. ■ Clear shedding The beating stroke is shortened and the driving parts that are the most essential for the weaving machine to run at high speed are additionally reinforced. By placing the heald frame as close to the cloth fell as possible while keeping the shedding amount, the shedding angle is increased and defective shedding is reduced. -
Weaving Booklet Edited
TEXTILE WEAVING © 2012 Cotton Incorporated. All rights reserved; America’s Cotton Producers and Importers. Textile Weaving 1 INTRODUCTION ........................................................................................................ 3 2 WARP PREPARATION .............................................................................................. 4 2.1 Direct Warping ..................................................................................................... 4 2.2 Indirect Warping ................................................................................................... 4 2.3 Slashing ............................................................................................................... 5 2.4 Drawing-In ............................................................................................................ 8 2.5 Tying-In ................................................................................................................ 9 3 WEAVING ................................................................................................................... 9 3.1 Shedding .............................................................................................................. 9 3.1.1 Cam Shedding .............................................................................................. 9 3.1.2 Dobby Shedding .......................................................................................... 10 3.1.3 Jacquard Shedding .................................................................................... -
Class 139 Textiles: Weaving 139 - 1
CLASS 139 TEXTILES: WEAVING 139 - 1 1 R MISCELLANEOUS 34 ..Warp frames 1 A .Reed and fell gauges 35 WARP MANIPULATION 1 B .Inspecting devices 36 .Fluid treatment 1 D .Pick measuring and counting 37 .Pile 1 E .Loom driving, reversing and 38 ..Loop hook disconnecting mechanism 39 ..Transverse wire 1 F .Reweaving 40 ...Wire control 1 C .Loom cleaning 41 ....Including end motions 2 PILE TUFTING 42 .....End motions 3 .Around warp 43 ...Separate cutting mechanism 4 ..Oriental knot 44 ...Pile wires 5 ...Warp traversing 45 ...Oiling 6 ...Portable supply 46 ..Longitudinal wire, traversing 7 R .Portable supply 47 ...Anchored release end 8 ..Including tuft presenting 48 .Traversing 9 ...Tuft presenting 49 ..Lappet 10 ....Tube frames 50 ..Leno or gauze 7 A ..Tuft yarn carrier 51 ...Doup heddle 7 B ..Carrier chain mechanism 52 ....Heddles 7 C ..Transfer device 53 ...Needle-eye heddle 7 D ..Gripper means 54 ..Selvage 7 E ..Tuft forming means 55.1 .Shedding 7 F ..Cutter means 56 ..Disconnecting mechanism 7 G ..Tube brake means 57 ..Pushed harness 11 SPECIAL-TYPE LOOMS 58 ...Double-acting cam 457 .Circular, progressive shedding 59 ..Jacquard 458 ..Longitudinal shedding 60 ...Knotted cord 459 ..Shuttle 61 ...Multiple cylinder 14 ..Open back 62 ...Group control 15 ..Contacting shuttle and shed 63 ...Locked open shed control 64 ...Mid closing 16 ..Radial heddle movement 65 ...Double lift 17 .Open-back shed 66 R ..Dobby 17.5 .Supplemental open-back shed 67 ...Vibrating griff 18 .Vertical shed 68 ....Jacquard pattern 19 ..Seed-corn stringers 69 ....Mid closing -
Course Template
Curriculum Revision for B. Tech. (Textile Technology) Programme Dept. of Textile Technology Indian Institute of Technology Delhi 2013-2014 Tentative Schedule of Undergraduate Courses (The courses in red colour are the Institute core and programme linked core courses. These slots are fixed by The Institute.) Sem Lecture lecture lecture lecture Lecture/ Other Other Other L T P TOTAL Other I Maths-1 / 2 EE / CS PH / CY Mechanics Intro. to Graphics / Language / (3-1-0)4 (3-0-2)4 (3-0-4)5 / NONE Engg / Prog Prod. Real. None (3-0-2)4 (0-0-2)1 (0-0-4)2 (0-0-4)2 II Maths-2 / 1 CS / EE CY / PH NONE / Intro to Prod Real./ Language / (3-1-0)4 (3-0-2)4 (3-0-4)5 Mechanics Engg/ Prog Graphics None (3-0-2)4 (0-0-2)1 (0-0-4)2 (0-0-4)2 III PL EA/EA PL EA/ES Poly. Chem. PL EA/ES Text. fibres HUL ?? AML120 AML130 / (3-0-0)3 AML150 / (2-0-2)3 (3-0-2)4 (3-1-2)5 (3-1-2)5 IV Yarn Manf.-I Fabric Tech. TP &F Biology Structure Yarn Manf. Fabric Prep. & (3-0-0)3 Manf. I (3-0-0)3 (3-0-2)4/ Env. Property Lab -I Manf. Lab I Finishing Lab (3-0-0)3 (2-0-0)2 (3-0-0)3 (0-0-2)1 (0-0-2)1 (0-0-3)1.5 V Yarn Manf.-II Fabric Tech. Tex. -
Section 4.1 Negative Tappet Cam Shedding Motion
Section 4.1 Negative Tappet Cam Shedding Motion 4.1.1 Levelling Operation............................................................ 4.1-3 [ 1 ] Preparatory Operation .............................................. 4.1-3 [ 2 ] Levelling Operation................................................... 4.1-4 [ 3 ] Levelling Tool Maintenance ...................................... 4.1-6 4.1.2 Shed Close Timing ............................................................ 4.1-7 [ 1 ] Shed Close Timing ................................................... 4.1-7 [ 2 ] Shed Size ................................................................. 4.1-7 4.1.3 Shed Size .......................................................................... 4.1-8 [ 1 ] Shed Size ................................................................. 4.1-8 [ 2 ] Cam Combination..................................................... 4.1-9 [ 3 ] Adjusting the Shed Size ........................................... 4.1-10 4.1.4 Springs and Related Sections ........................................... 4.1-11 [ 1 ] Rope Installation Position......................................... 4.1-11 [ 2 ] Springs ..................................................................... 4.1-11 4.1.5 Healed Frames .................................................................. 4.1-15 [ 1 ] Height of Heald Frames............................................ 4.1-15 4.1.6 Modifying the Fabric Texture.............................................. 4.1-17 [ 1 ] Removing and Installing the Negative Tappet -
Terrorists Destroy World Trade Center, Hit Pentagon
EE P1JW255001-4-A00100-1---SB P1JW255001-4-A00100-1---SB P1JW255001-4-A00100-1---SB SB **** BLACK 09/12/2001 s 2001 Dow Jones & Company, Inc. All Rights Reserved. ! VOL. CCXXXVIII NO. 51 EE/PR 1111 WEDNESDAY, SEPTEMBER 12, 2001 WSJ.com iiii $1.00 TERRORISTS DESTROY WORLD TRADE CENTER, HIT PENTAGON IN RAID WITH HIJACKED JETS Nation Stands What’s News— Death Toll, Source of Devastating Attacks Remain Unclear; iii iii U.S. Vows Retaliation as Attention Focuses on bin Laden In Disbelief 7 By David S. Cloud Vt. 7 Business and Finance World-Wide 7 And Neil King BOSTON: American Airlines The Wall Street Journal N.H. And Horror Staff Reporters of Flight 11, a Boeing 767, leaves LL MAJOR U.S. FINANCIAL mar- By successfully attacking the most promi- Boston at 7:59 a.m. EDT for Los kets closed yesterday and remain BUSH PROMISED action against ter- New York A rorist attacks in the Eastern U.S. nent symbols of American power—Wall Street Mass. Boston Angeles. This flight, with 92 closed today in the wake of the terrorist and the Pentagon—terrorists have wiped out people aboard, including 11 The death toll from the hijacked-jet at- crew, becomes the first plane to Streets of Manhattan attack on the World Trade Center. The tacks that destroyed the World Trade Cen- any remaining illusions that America is safe Conn. hit the World Trade Center. near-panic reaction in the global mar- from mass organized violence. ter’s towers in New York and damaged the Pennsylvania Resemble War Zone kets that remained open suggested that Pentagon outside Washington was impos- That realization alone will alter the way NEW YORK: At about 8:50 a.m., Flight 11 from the U.S. -
Cam Motion Tuning of Shedding Mechanism for Vibration Reduction
Gazi University Journal of Science GU J Sci www.gujs.org 23(2): 227-232 (2010) Cam Motion Tuning of Shedding Mechanism for Vibration Reduction of Heald Frame Sadettin KAPUCU 1, M. Taylan DAŞ 2♠, Ali KILIÇ 1 1Gaziantep University, Faculty of Engineering, Department of Mechanical Engineering, Gaziantep, Turkey 2Roketsan Missile Co. Ankara, Turkey Received: 20.02.2009 Revised: 20.09.2009 Accepted: 21.09.2009 ABSTRACT This paper presents a new approach to eliminate the residual vibration of shedding system and the associated mechanism that connects the heddle shafts with the cam mechanisms. Effective cam design method which is based on motion design of the cam pitch curve by “blends” of the traditional profiles, formed by superimposing three functions; a cycloid, a ramped versine, and a ramp called as ramp-plus-ramped cycloid-plus-ramped versine is proposed in this study. This function is reshaped using the system’s natural frequency and damping ratio to yield almost zero residual vibration of the heddle shaft. The proposed method is then compared with the well known cam curves and its applicability is shown by simulation and experimental results. The results show that the proposed method is quite effective for fast vibration free motion of the heald frame. Key Words : Shedding system, Cam tuning, Motion design, Residual vibration elimination . 1. INTRODUCTION design of the cam-follower mechanism. Generally speaking, the cam is designed for a constant drive speed Weaving is the process in which yarn is converted into and a flywheel attached to keep the drive speed as fabric. The process of weaving is divided into three constant as possible. -
Air Jet Loom Zax9100
Professional ZAX9100 AIR JET LOOM Professional ZAX9100 AIR JET LOOM The spectacular debut will lead the new era of weaving. The pioneer for the Weave Navigation. Tsudakoma introduces the new model ZAX9100 Professional, integrating their advanced technology and vast expertise of air jet weaving. Energy savings Careful attention has been paid to design the ZAX9100 for energy saving. The offset Ultimate weaving support! rocking shaft with less moment of inertia, We incorporated the world’s fi rst “Weave Navigation System.” the hollow reed holder, and a lower load in the driving oil bath save energy. Air We provided the ZAX9100 with the weaving technology with ease. Tsudakoma’s consumption was also reduced 10% by world’s fi rst “Weave Navigation System.” original systems guide the ZAX9100 to adopting newly designed solenoid valves Tsudakoma has embodied their the best weaving condition even during for every two sub-nozzles and realizing a accumulated wealth of weaving expertise operation. shorter air passage. (Compared with our in this system. Simple operation on the conventional model) “Navi-Board” reproduces professional 2 With the newly designed air jet loom, anyone can easily weave high-quality fabric using the Weave Navigation System. In pursuit of the ultimate user-friendly loom, Tsudakoma developed the new ZAX9100 air jet loom. The ZAX9100 is completely new. We re-thought all the basics. We redesigned each section of the loom from the ground up including the frame structure, the shedding, the beating, the weft insertion, the let-off and the take-up motion. Our accumulated experience has given form to a very new air jet loom.