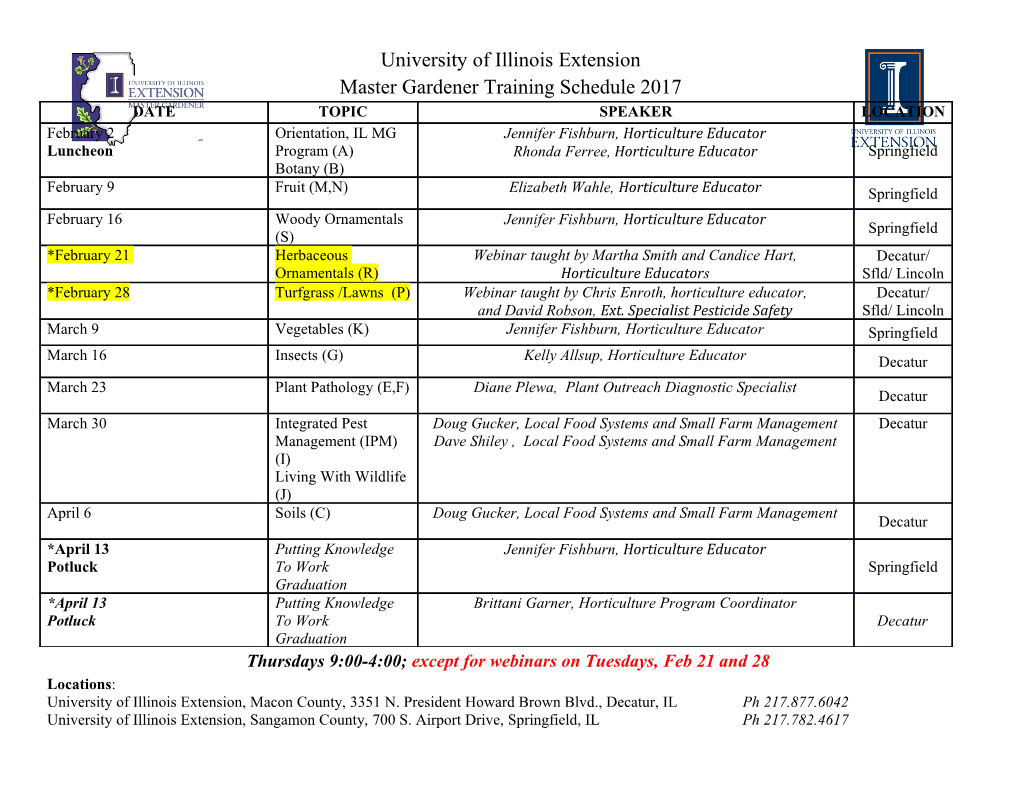
Recep Eren, Gülcan Özkan, Comparison of Heald Frame Motion Mehmet Karahan* Generated by Rotary Dobby Department of Textile Engineering Faculty of Engineering and Architecture and Crank & Cam Shedding Motions University of Uludag, Abstract * Uludag University, Vacational School of Technical Sciences, Mechanism models are introduced for rotary dobby, crank & cam shedding motions. Textile Program, Equations governing heald frame motion are derived. Heald frame motion curves are Görükle Campus, obtained and compared with each other. It is shown that higher heald frame maximum Görükle, 16059 Bursa, TURKEY velocity & maximum acceleration, as well as a longer approximate heald frame dwell, are E-mail: [email protected] generated by the rotary dobby rather than the crank or cam shedding motions, due to the intermittent nature of the rotary dobby shaft’s motion. Key words: rotary dobby, cam shedding motion, crank shedding motion, weaving, weaving machine. n Introduction frame dwell period, the maximum heald tween its foremost and rearmost positions. frame speed and the maximum heald The slider crank mechanism converts the Shedding is one of the principal op- frame acceleration. angular displacement of link 4 to the lin- erations in the weaving process, which ear displacement of the heald frame. The separates warp yarns into two layers to foremost position of link 4 corresponds form an opening for weft insertion called n Working principle of crank, to the bottom position, and the rearmost a shed. Crank, cam and dobby are shed- cam and rotary dobby position of link 4 corresponds to the upper ding motions which use a heald frame shedding motions position of the heald frame. Heald frames system for lifting warp yarns up or down Figure 1 shows a schematic view of the change position in each loom revolution, to form a shed. Crank and cam shedding crank shedding motion. It consists of a and therefore the crank’s shedding motion motions are mainly used on high-speed crank rocker mechanism (A ABB ) and generates a heald frame motion only for air-jet and water-jet weaving machines 0 0 a slider crank mechanism (B CD). The plain weave. for weaving fabrics with plain and basic 0 crank (link 2) rotates at half of the loom’s weaves. Despite the widespread use of speed. The crank’s continuous rotation is Figure 2 shows a cam shedding motion, negative dobby on air-jet and water- transmitted to link 4 by link 3. During one which consists of a double shedding cam jet looms in industry, the use of rotary revolution of the crank, link 4 swings be- (2 and 2’), an oscillating follower (link 4) dobby (i.e., positive dobby) with air-jet looms has been widened in recent years, due to the increase in rotary dobby run- ning speeds. An increase in loom speeds imposes higher demands on heald frame design, due to the increase in inertial forces. New heald frame designs which Figure 1. Crank can resist higher mechanical stresses type of shedding have been developed and demonstrated motion; A0ABB0 in the exhibitions, and used especially - crank rocker me- chanism, B0CD on high-speed air jet weaving ma- - slider crank mech- chines. anism, 2 - crank, 3, 4, 5 - links, 6 - heald Heald frame motion characteristics, and frame. therefore the inertial forces affecting heald frames, differ depending on the type of shedding motion. This is of im- portance in designing the heald frames to be used with different type of shedding motions. No publication was found in the literature of a comparative study of heald frame motion characteristics of different type of shedding motions. This paper deals with heald frame motion character- istics generated by crank, cam and rotary dobby shedding motions. Mathematical equations are derived, and the heald frame’s displacement, velocity and ac- Figure 2. Positive cam shedding motion; the first drawing was taken from ref. [1];A 0ABB0, celeration are calculated and compared B0CDD0 - four bar mechanisms; D0EF - slider crank mechanism, 2, 2’ - double shedding with each other according to the heald cam; 3, 3’ - rollers; 4 - oscilating follower; 5, 6, 7, 8, 9 - links; 10 - heald frame. 78 FIBRES & TEXTILES in Eastern Europe October / December 2005, Vol. 13, No. 4 (52) FIBRES & TEXTILES in Eastern Europe October / December 2005, Vol. 13, No. 4 (52) 79 clockwise rotation of the followers. The tary dobby. In this case, link f of the rotary followers’ dwell at the end positions cor- dobby corresponds to link 4 of the motion responds to the dwell of the heald frames transmission mechanism. The foremost at the upper and lower shed positions. position of link f of the rotary dobby cor- responds to the higher position of a heald Figure 3 shows a rotary dobby cross sec- frame, and the rearmost position of link tion. Link b is fixed to the dobby shaft. A f corresponds to the lower position. As a metal piece (d) is pivoted on the eccentric result, the counterclockwise rotation of (link c) and can rotate around its pivot link g of the pattern selection mechanism axis. A spring (not shown in the figure) corresponds to the higher position of the Figure 3. Fimtextile Type RD 3000 rotary heald frames, and the clockwise rotation dobby cross-section [2]; b - link fixed to forces the metal piece to rotate in the dobby shaft; c - eccentric link; d - metal clockwise direction, and hence the metal to the lower position. piece; e, f, g, h - links; j - electromagnet. piece presses on link b. There is a ball bearing between links b and c (not seen In contrast to the continuous rotation at with two rollers (3 and 3’) and a motion in the figure). There is also a ball bearing a constant speed of the drive shaft of the transmission mechanism to the heald between link c and link e. Links g and h, crank- and cam-shedding motions, the frame. This type of cam shedding motion the electromagnet (j) and the metal piece rotary dobby shaft has to rotate intermit- is called a positive cam shedding motion, (d) constitute the pattern selection mecha- tently with 180° increments to allow the in which both the upward and downward nism. Link g can rotate around its pivot by engagement or disengagement of the movement of heald frames are carried the action of the electromagnet (j) via link metal piece with link b. A mechanism out by cams. There are as many double h. If link g is rotated in an anticlockwise called the ‘modulator’ is used to convert shedding cams and motion transmission direction, then the metal piece rotates in the continuous rotation of a loom main mechanisms as there are heald frames. the clockwise direction, and its bottom tip shaft to the intermittent movement of the Each double cam has its own rollers, becomes engaged in the groove on link b. rotary dobby shaft. which are mounted on a common fol- If link g is rotated in a clockwise direc- lower with a certain angle. When a cam tion, it presses the upper tip of the metal n Derivation of equations continuously rotates in a clockwise direc- piece and disengages it from link b by ro- for heald frame motion tion, a follower swings in clockwise and tating the metal piece (d) in an anticlock- counter-clockwise directions, and dwells wise direction. When the engagement The motion equation of a heald frame at the end positions when necessary (de- happens, link f rotates in an anticlockwise will be derived with respect to the loom’s pending on the weave). The clockwise direction during the 180° rotation of the main shaft angle for each shedding mo- rotation of the follower (link 4) causes dobby shaft (i.e., link 1). Link f dwells at tion as follows. link 6 to rotate in a clockwise direction its foremost position during the 180° rota- also, and likewise the anticlockwise rota- tion of the dobby shaft, if the engagement Crank shedding motion tion of the follower (link 4) rotates link 6 does not occur. The dobby shaft stops The crank type of shedding motion in an anti-clockwise direction. The mo- after every 180° degree rotation, and the consists of a crank rocker mechanism tion of link 6 is transmitted to link 8 by pattern selection mechanism engages or (A0ABB0) and a slider crank mechanism link 7. As |B0C|=|D0D| and |B0D0|=|CD|, disengages the metal piece with link b. (B0CD). Figure 4 shows parameters rep- the motion of link 8 is the same as that If the engagement happens, then link f resenting angular and linear positions of link 6. Finally, the motion of link 8 is moves to the other position. Otherwise, of the links of crank rocker and slider transmitted to the heald frame (link 10) it remains in the same position. The mo- crank mechanisms. The angular position by link 9. Heald frames move upwards tion transmission mechanism of the cam of the link 4 (ϕ4) is obtained with respect when the followers rotate clockwise shedding mechanism can also be used as a to angular position of the link 2 (ϕ2) as and they are lifted down with the anti- motion transmission mechanism for a ro- follows [3]. Figure 4. Parametric representation of crank shedding motion; Figure 5. Parametric representation of motion transmission A0ABB0 - crank rocker me-chanism, B0CD - slider crank mechanism, mechanism; A0ABB0, B0CDD0 - four bar mechanisms; D0EF - 2 - crank, 3, 4, 5 - links, 6 - link representing heald frame; s - hold slider crank mechanism; 7, 8, 9 - links; 10 - link representing heald frame displacement. frame; s - hold frame displacement. 78 FIBRES & TEXTILES in Eastern Europe October / December 2005, Vol.
Details
-
File Typepdf
-
Upload Time-
-
Content LanguagesEnglish
-
Upload UserAnonymous/Not logged-in
-
File Pages6 Page
-
File Size-