Recent Progress on Plant-Inspired Soft Robotics with Hydrogel Building Blocks: Fabrication, Actuation and Application
Total Page:16
File Type:pdf, Size:1020Kb
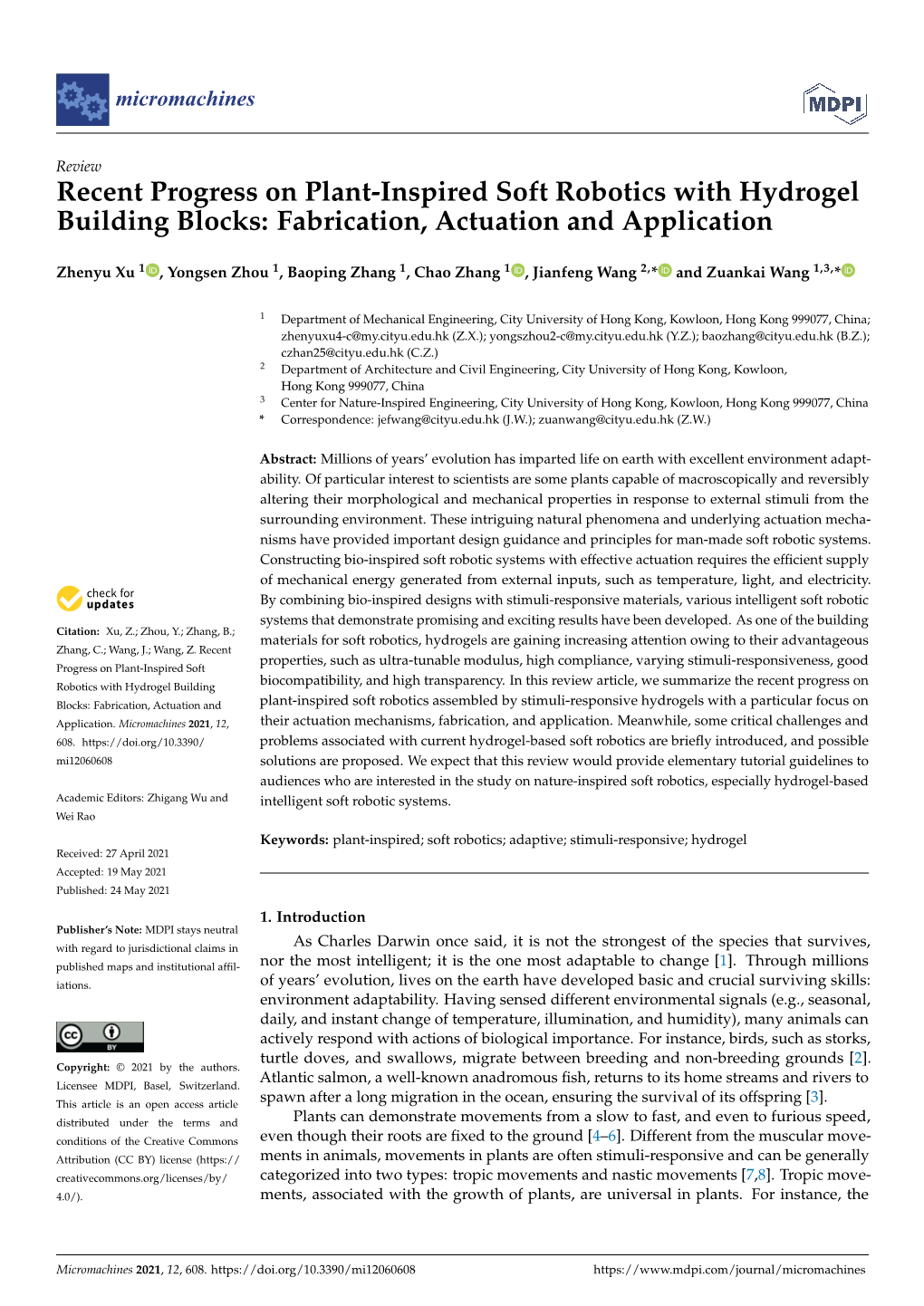
Load more
Recommended publications
-
Phytochrome Effects in the Nyctinastic Leaf Movements of Albizzia Julibrissin and Some Other Legumes1 2 William S
Plant Physiol. (1967) 42, 1413-1418 Phytochrome Effects in the Nyctinastic Leaf Movements of Albizzia julibrissin and Some Other Legumes1 2 William S. Hillman and Willard L. Koukkari Biology Department, Brookhaven National Laboratory, Upton, New York 11973 Received June 5, 1967. Summnary. Participation of phytochrome 'is evident in the nyctinastic responise of leaves of Albizzia julibrissin (silk-tree), Albizzia lophantha, Leucaena glauca, Poinciana gilliesi and Calliandra inequilatera; closure of excised pairs of pinnules upon darkening is rapid following red illumination and slow following far-red. Under good conditions the difiference is obvious within 10 minutes. These observations conifirm a report by Fondeville, Borthwick, and Hendricks on the sensitive plant, Mimosa pudica, but indicate that the efifect bears no necessary relationship to the anomalous sensitivity of Mimosa. In A. julibrissin, phytochrome control is mnarked in experiments conducted early in the daily 12-hour light period and appears absent, or nearly so, toward the end of the light period, perhaps due to interaction with an endogenous circadian rhythm. Effects of leaf maturity and of the position of a pinnule-pair within a leaf are also evident. Tih-ese results are not easily reconciled with hypotheses of phytochrome action through gene activation and nucleic acid synthesis, but are consistent with hypothess ibased onl permeability changes and membrane properties. The mgnitude and reproducibility of the response in A. jutlibrissin suggest its use as a lajboratory exercise; this and related systems should prove valuable for eventuai identification of the mechanism of phytochrome action. Fondeville, Borthwick, and Hendricks (2) re- pinnately twice-compound leaves generally similar in ported on a role of phytochrome in the nyctinastic character to those of Mimosa pudica, (but not obviously response of the sensitive plant, Mimnosa pudica: closure sensitive to the touch. -
Arxiv:1508.05435V1 [Physics.Bio-Ph]
Fast nastic motion of plants and bio-inspired structures Q. Guo1,2, E. Dai3, X. Han4, S. Xie5, E. Chao3, Z. Chen4 1College of Materials Science and Engineering, FuJian University of Technology, Fuzhou 350108, China 2Fujian Provincial Key Laboratory of Advanced Materials Processing and Application, Fuzhou 350108, China 3Department of Biomedical Engineering, Washington University, St. Louis, MO 63130 USA 4Thayer School of Engineering, Dartmouth College, Hanover, New Hampshire, NH 03755, USA 5Department of Energy, Environmental, and Chemical Engineering, Washington University, St. Louis, MO 63130 USA ∗ (Dated: August 25, 2015) The capability to sense and respond to external mechanical stimuli at various timescales is es- sential to many physiological aspects in plants, including self-protection, intake of nutrients, and reproduction. Remarkably, some plants have evolved the ability to react to mechanical stimuli within a few seconds despite a lack of muscles and nerves. The fast movements of plants in response to mechanical stimuli have long captured the curiosity of scientists and engineers, but the mechanisms behind these rapid thigmonastic movements still are not understood completely. In this article, we provide an overview of such thigmonastic movements in several representative plants, including Dionaea, Utricularia, Aldrovanda, Drosera, and Mimosa. In addition, we review a series of studies that present biomimetic structures inspired by fast moving plants. We hope that this article will shed light on the current status of research on the fast movements of plants and bioinspired struc- tures and also promote interdisciplinary studies on both the fundamental mechanisms of plants’ fast movements and biomimetic structures for engineering applications, such as artificial muscles, multi-stable structures, and bioinspired robots. -
(Catclaw) Mimosa Managed Forests (Mimosa Pigra L.,Syn
Black (Catclaw) Mimosa Managed Forests (Mimosa pigra L.,Syn. Mimosa pellita Kunch ex Willd.) Victor Maddox, Ph.D., Postdoctoral Associate, Mississippi State University Randy Westbrooks, Ph.D., Invasive Species Specialist, U.S. Geological Survey John D. Byrd, Jr., Ph.D., Extension/Research Professor, Mississippi State University Fig. 1. Black, catclaw, or lollipop mi- Fig. 2. Black Mimosa Showing Hairy Stems and Fig. 3. Black Mimosa Showing Flowerhead and Bristly mosa is a sprawling shrub native to Bipinnate Leaves (USDA APHIS PPQ Archive, Fruit (USDA APHIS PPQ Archive, USDA APHIS PPQ, Central America. USDA APHIS PPQ, Bugwood.org. Bugwood.org) Introduction Problems Caused Black, catclaw, or lollipop mimosa (Mimosa pigra L.,Syn. Mimosa pellita Kunch ex Willd.) is a sprawling shrub native to Central America. Other common names include giant sensitive-plant and shamebush. It was introduced into Florida sometime prior to 1953 and escaped. It is not clear if it was introduced into Florida as an ornamental or the introduction was accidental. It has proved to be a serious invasive plant in wetlands in Thailand, Australia, and Florida. Having spines and forming dense thickets to 20’ high, it can displace native species and form a barrier to animal and human activity. Although it can be a serious weed in wetlands, it may also inhabit drier sites. The presence of spines on stems and leaves may implicate it as a threat in pastures. Regulations Black mimosa is a Federal Noxious weed in the United States. It is a Class A noxious weed in Alabama, North Carolina, and Vermont and a Noxious weed in Florida and Hawaii. -
Control and Coordination Class
BY SMT. RENUKA BALA BHAKAT AECS , NARWAPAHAR TYPES OF MOVEMENTS 1. TROPIC MOVEMENTS 2. NASTIC MOVEMENTS Movement of plant towards the stimulus is called tropic movement . Phototropism – Movement of plant towards light is called phototropism. Shoot grow towards light. Shoot is positively phototropic while root is negatively phototropic . Movement of plants in response to gravity is called geotropism . Roots are positively geotropic and shoots are negatively geotropic . Growth of plants towards water is called hydrotropism . Roots grow towards water. Movement of plants towards chemicals is called chemotropism . Growth of pollen tube towards ovule is an example of chemotropism. Nastic movement is not a directional movement of the plant part with response to the stimulus. In nastic movement, from whichever direction the stimulus is applied, it affects all the parts of the organ of a plant equally and they always move in the same direction . Mimosa pudica (touch me not) Plant hormones are signal molecules, produced within plants, that occur in extremely low concentrations. Plant hormones control all aspects of plant growth and development, from embryogenesis to regulation of organ size, pathogen defense, stress tolerance and reproductive development. The auxin group of hormones has a wide range of uses in a plant. Auxin molecules are found in all tissues in a plant. However, they tend to be concentrated in the meristems, growth centres which are at the forefront of growth. These centres release auxin molecules, which are then distributed towards the roots. In this way, the plant can coordinate its size, and the growth and development of different tissues based on the gradient of the auxin concentration. -
Botany for Gardeners Offers a Clear Explanation of How Plants Grow
BotGar_Cover (5-8-2004) 11/8/04 11:18 AM Page 1 $19.95/ £14.99 GARDENING & HORTICULTURE/Reference Botany for Gardeners offers a clear explanation of how plants grow. • What happens inside a seed after it is planted? Botany for Gardeners Botany • How are plants structured? • How do plants adapt to their environment? • How is water transported from soil to leaves? • Why are minerals, air, and light important for healthy plant growth? • How do plants reproduce? The answers to these and other questions about complex plant processes, written in everyday language, allow gardeners and horticulturists to understand plants “from the plant’s point of view.” A bestseller since its debut in 1990, Botany for Gardeners has now been expanded and updated, and includes an appendix on plant taxonomy and a comprehensive index. Twodozen new photos and illustrations Botany for Gardeners make this new edition even more attractive than its predecessor. REVISED EDITION Brian Capon received a ph.d. in botany Brian Capon from the University of Chicago and was for thirty years professor of botany at California State University, Los Angeles. He is the author of Plant Survival: Adapting to a Hostile Brian World, also published by Timber Press. Author photo by Dan Terwilliger. Capon For details on other Timber Press books or to receive our catalog, please visit our Web site, www.timberpress.com. In the United States and Canada you may also reach us at 1-800-327-5680, and in the United Kingdom at [email protected]. ISBN 0-88192-655-8 ISBN 0-88192-655-8 90000 TIMBER PRESS 0 08819 26558 0 9 780881 926552 UPC EAN 001-033_Botany 11/8/04 11:20 AM Page 1 Botany for Gardeners 001-033_Botany 11/8/04 11:21 AM Page 2 001-033_Botany 11/8/04 11:21 AM Page 3 Botany for Gardeners Revised Edition Written and Illustrated by BRIAN CAPON TIMBER PRESS Portland * Cambridge 001-033_Botany 11/8/04 11:21 AM Page 4 Cover photographs by the author. -
Insecticidal and Repellent Activities of Mimosa Pudica L. (Fabaceae) Against Cryptolestes Pusillus (Schon) (Coleoptera: Cucujidae)
Int.J.Curr.Microbiol.App.Sci (2020) 9(9): 2222-2235 International Journal of Current Microbiology and Applied Sciences ISSN: 2319-7706 Volume 9 Number 9 (2020) Journal homepage: http://www.ijcmas.com Original Research Article https://doi.org/10.20546/ijcmas.2020.909.277 Insecticidal and Repellent Activities of Mimosa pudica L. (Fabaceae) against Cryptolestes pusillus (Schon) (Coleoptera: Cucujidae) Ujjwal Kumar Mondol and W. Islam* Institute of Biological Sciences, University of Rajshahi, Bangladesh *Corresponding author ABSTRACT The insecticidal and repellent activities were observed by residual film method and surface K eyw or ds film application methods respectively. Leaf, stem and root of Mimosa pudica L. were Insecticidal, screened through Petroleum ether, chloroform, ethyl acetate and methanol extracts against repellent activities, flat grain beetle, Cryptolestes pusillus (Schon.). The plant extracts showed less to high Residual film 2 mortality by using 0.25, 0.50, 1.0 and 2.0 mg/cm doses and the root extract showed most method, Surface potency. In 72 h of exposure, chloroform extract of root showed the lowest LD50 value film application (2.024 mg/cm 2) and 95% confidence limit was 1.730-2.292. In case of leaf, stem and root method, Mimosa the highest mortality was recorded in chloroform extracts were 73.3, 70.0, 80.0%; 80.0, pudica, 76.7, 90.0% and 90.0, 86.7, 96.7% respectively in 24, 48 and 72 h. The repellency Cryptolestes response among the three parts of the tested plant was different (p<0.05) and dose effect pusillus was more effective than exposure effect. -
NATIVE NAMES and USES of SOME PLANTS of EASTERN GUATEMALA Mid HONDURAS
NATIVE NAMES AND USES OF SOME PLANTS OF EASTERN GUATEMALA MiD HONDURAS. By S. F. BLAKE. INTRODUCTION. In the spring of 1919 an Economic Survey Mission of the United States State Department, headed by the late Maj. Percy H. Ashmead, made a brief examination of the natural products and resources of the region lying between the Chamelec6n Valley in Honduras and the Motagua VaUey in Guatemala. Work was also done by the botanists of the expedition in the vicinity of Izabal on Lak.. Izaba!. Descriptions of the new species collected by the expedition, with a short account of its itinerary, have already been published by the writer,' and a number of the new forms have been illustrated. The present list is based · wholly on the data and specimens collected by the botanists and foresters of this expedition-H. Pittier, S. F. Blake, G. B. Gilbert, L. R. Stadtmiller, and H. N. Whitford-and no attempt has been made to incorporate data from other regions of Central America. Such information will be found chiefly in various papers published by Henry Pittier,' J. N. Rose,' and P. C. Standley.' LIST OF NATIVE NAllES AND USES. Acacia sp. CACHITO. eoaNIZuELO. ISCAN.... L. FAAACEJ..E. Acacla sp. I....&GAR'l"O. SANPlWBANO. FABACE'·. A tree up to 25 meters high and 45 em. to diameter. The wood is lISed for bunding. Acalypha sp. Co8TII I A DE PANTA. EUPHOllBlAc!:a. 'Contr. U. S. Not. Herb. 24: 1-32. pl •. 1-10, ,. 1-4. 1922. • Ensayo oobre las plantas usuatee de Costa Rica. pp. 176, pk. -
Plant-Environment Interactions: from Sensory Plant Biology to Active
Signaling and Communication in Plants Series Editors František Baluška Department of Plant Cell Biology, IZMB, University of Bonn, Kirschallee 1, D-53115 Bonn, Germany Jorge Vivanco Center for Rhizosphere Biology, Colorado State University, 217 Shepardson Building, Fort Collins, CO 80523-1173, USA František Baluška Editor Plant-Environment Interactions From Sensory Plant Biology to Active Plant Behavior Editor František Baluška Department of Plant Cell Biology IZMB University of Bonn Kirschallee 1 D-53115 Bonn Germany email: [email protected] ISSN 1867-9048 ISBN 978-3-540-89229-8 e-ISBN 978-3-540-89230-4 DOI: 10.1007/978-3-540-89230-4 Library of Congress Control Number: 2008938968 © 2009 Springer-Verlag Berlin Heidelberg This work is subject to copyright. All rights are reserved, whether the whole or part of the material is concerned, specifically the rights of translation, reprinting, reuse of illustrations, recitation, broadcasting, reproduction on microfilms or in any other way, and storage in data banks. Duplication of this publication or parts thereof is permitted only under the provisions of the German Copyright Law of September 9, 1965, in its current version, and permission for use must always be obtained from Springer-Verlag. Violations are liable for prosecution under the German Copyright Law. The use of general descriptive names, registered names, trademarks, etc. in this publication does not imply, even in the absence of a specific statement, that such names are exempt from the relevant protective laws and regulations and therefore free for general use. Cover design: WMXDesign GmbH, Heidelberg, Germany Printed on acid-free paper 9 8 7 6 5 4 3 2 1 springer.com František Baluška dedicates this book to Prof. -
Mimosa Pudica As an Experimental Organism for Botany Lab
This article reprinted from: Emmons, C.L. 2006. Mimosa pudica as an experimental organism for Botany Lab. Pages 351-353, in Tested Studies for Laboratory Teaching, Volume 27 (M.A. O'Donnell, Editor). Proceedings of the 27th Workshop/Conference of the Association for Biology Laboratory Education (ABLE), 383 pages. Compilation copyright © 2006 by the Association for Biology Laboratory Education (ABLE) ISBN 1-890444-09-X All rights reserved. No part of this publication may be reproduced, stored in a retrieval system, or transmitted, in any form or by any means, electronic, mechanical, photocopying, recording, or otherwise, without the prior written permission of the copyright owner. Use solely at one’s own institution with no intent for profit is excluded from the preceding copyright restriction, unless otherwise noted on the copyright notice of the individual chapter in this volume. Proper credit to this publication must be included in your laboratory outline for each use; a sample citation is given above. Upon obtaining permission or with the “sole use at one’s own institution” exclusion, ABLE strongly encourages individuals to use the exercises in this proceedings volume in their teaching program. Although the laboratory exercises in this proceedings volume have been tested and due consideration has been given to safety, individuals performing these exercises must assume all responsibilities for risk. The Association for Biology Laboratory Education (ABLE) disclaims any liability with regards to safety in connection with the use of the exercises in this volume. The focus of ABLE is to improve the undergraduate biology laboratory experience by promoting the development and dissemination of interesting, innovative, and reliable laboratory exercises. -
Weed Risk Assessment for Mimosa Pudica L. (Fabaceae)
Weed Risk Assessment for Mimosa United States pudica L. (Fabaceae) – Sensitive plant Department of Agriculture Animal and Plant Health Inspection Service August 1, 2014 Version 1 Dried pods (top), plant habit (bottom), flower, leaves, and stem of M. pudica (right). [Photo source: top and bottom Starr and Starr (2005-2009), and right, K. A. Rawlins, invasive.org]. Agency Contact: Plant Epidemiology and Risk Analysis Laboratory Center for Plant Health Science and Technology Plant Protection and Quarantine Animal and Plant Health Inspection Service United States Department of Agriculture 1730 Varsity Drive, Suite 300 Raleigh, NC 27606 Weed Risk Assessment for Mimosa pudica Introduction Plant Protection and Quarantine (PPQ) regulates noxious weeds under the authority of the Plant Protection Act (7 U.S.C. § 7701-7786, 2000) and the Federal Seed Act (7 U.S.C. § 1581-1610, 1939). A noxious weed is defined as “any plant or plant product that can directly or indirectly injure or cause damage to crops (including nursery stock or plant products), livestock, poultry, or other interests of agriculture, irrigation, navigation, the natural resources of the United States, the public health, or the environment” (7 U.S.C. § 7701-7786, 2000). We use weed risk assessment (WRA)— specifically, the PPQ WRA model (Koop et al., 2012)—to evaluate the risk potential of plants, including those newly detected in the United States, those proposed for import, and those emerging as weeds elsewhere in the world. Because the PPQ WRA model is geographically and climatically neutral, it can be used to evaluate the baseline invasive/weed potential of any plant species for the entire United States or for any area within it. -
Common Name- Lajalu Botanical Name- Mimosa Pudica
Common Name- Lajalu Botanical Name- Mimosa pudica Classification: Kingdom - Plantae Unranked- Angiosperm Unranked- Eudicots Unranked- Rosids Order - Fabales Family - Fabaceae Genus - Mimosa Species - pudica Key Characters: 1- It is “shy, bashful or shrinking”; also called sensitive plant,sleepy or shy plant. 2- It is a creeping annual or perennial herb. 3- The compound leaves folded inward and droop when touched or shaken, defending themselves from harm and re-open a few minute later. 4- Stem is erect, slender, branching. 5- Leaves are bipinnately compound with one or two pinnae hairs and 10-20 leaflets per pinna. 6- The petioles are also prickly. 7- Pedunculate pale pink or purple flower heads arise from the leaf axils. 8- The seeds have hard seed coast which restrict germination. Common Name- Zombi pea, Wild pea Botanical Name- Vigna vaxillata Classification: Kingdom - Plantae Unranked - Angiosperms Unranked - Eudicots Unranked - Rosids Order - Fabales Family - Fabaceae Genus - Vigna Species - vaxillata Key Characters: 1- The habit is strong twinner. 2- Stem usually clothed with spreading silky hairs. 3- Leaflets three, acute at the apex obliquely and spreadly cuneate. 4- Flowers pink or purplish 2 to 4 flowered peduncles, keel prolonged into an uncurved beak. Common Name- Morning Glories Botanical Name- Cassia tora Classification: Kingdom - Plantae Unranked- Angiosperm Unranked- Eudicots Unranked- Rosids Order - Fabales Family - Fabaceae Tribe - Cassieae Sub-tribe - Cassiinae Genus - Cassia Species - tora Key Characters: 1- It is herb, annual, erect, 30-60 cm high. 2- Leaflets obovate, oblong, glaucous. 3- Flowers are yellow, axillary or in pairs. 4- Pods are 0.5 cm, obliguely septate. 5- Seeds are 25-30 Rhombord. -
Seed Law Rules & Regulations
GEORGIA SEED LAW AND RULES AND REGULATIONS Georgia Department of Agriculture Gary W. Black Commissioner of Agriculture AGRICULTURAL INPUTS DIVISION GEORGIA DEPARTMENT OF AGRICULTURE 19 M. L. KING JR. DRIVE SW, ROOM 410 ATLANTA, GA 30334 PHONE: 404-656-5584 FAX: 404-463-8568 Revised May 14, 2018 TABLE OF CONTENTS Article 2 SALE AND TRANSPORTATION OF SEEDS Section Page 2-11-20 Short title 2-11-21 Definitions 2-11-22 Labeling requirements 2-11-23 Prohibited acts 2-11-24 Records 2-11-25 Powers and duties of Commissioner 2-11-26 Licensing authority; penalties 2-11-27 Reserved 2-11-28 Rule-making authority 2-11-29 Reserved 2-11-30 Seizure 2-11-31 Injunctions 2-11-32 Exemption 2-11-33 Applicability 2-11-34 Penalties Article 3 CERTIFICATION OF SEEDS AND PLANTS 2-11-50 Legislative intent 2-11-51 Definitions 2-11-52 Designation of agency; liability 2-11-53 False certification Page 1 SEED ARBITRATION COUNCIL 2-11-70 Purpose 2-11-71 Definitions 2-11-72 Labeling requirements 2-11-73 Filing complaints 2-11-74 Council membership 2-11-75 Hearings and investigations 2-11-76 Findings and recommendations 2-11-77 Rules and regulations RULES AND REGULATIONS Chapters & Rules Page 40-12-1 Definitions 40-12-2 Seed testing protocol & statistical tolerances 40-12-3 Standards 40-12-4 Limitations on noxious weed seeds 40-12-5 Labeling requirements 40-12-6 Seed arbitration 40-12-7 Charges for seed sample assay 40-12-8 Seed dealer license fees Page 2 Official Code of Georgia Annotated TITLE 2 CHAPTER 11 SEEDS AND PLANTS ARTICLE 2 SALE AND TRANSPORTATION OF SEEDS Revised July 1, 2012 2-11-20.