Progress and Status of Hydrometallurgical and Direct Recycling of Li-Ion Batteries and Beyond
Total Page:16
File Type:pdf, Size:1020Kb
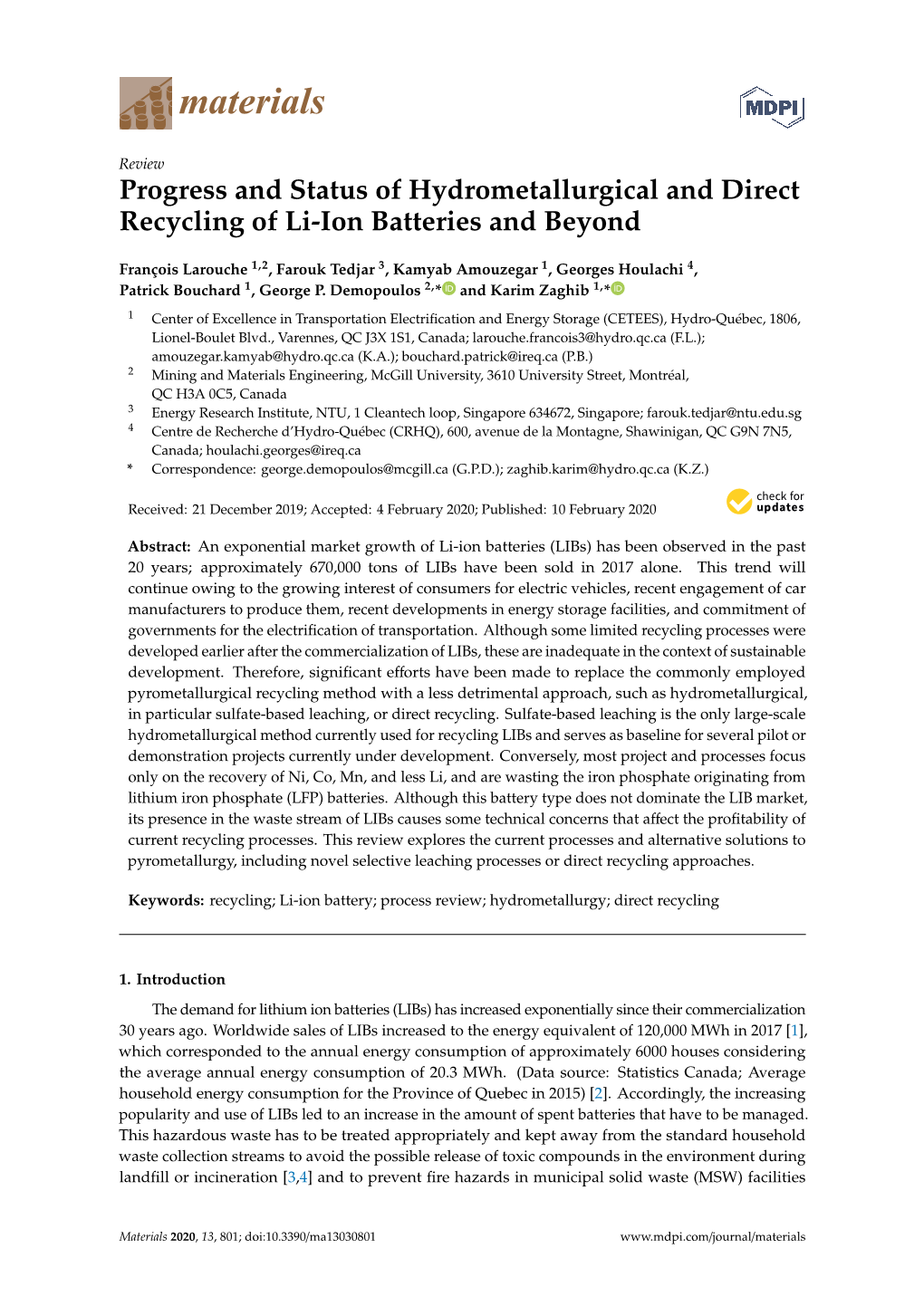
Load more
Recommended publications
-
Principles of Extractive Metallurgy Lectures Note
PRINCIPLES OF EXTRACTIVE METALLURGY B.TECH, 3RD SEMESTER LECTURES NOTE BY SAGAR NAYAK DR. KALI CHARAN SABAT DEPARTMENT OF METALLURGICAL AND MATERIALS ENGINEERING PARALA MAHARAJA ENGINEERING COLLEGE, BERHAMPUR DISCLAIMER This document does not claim any originality and cannot be used as a substitute for prescribed textbooks. The information presented here is merely a collection by the author for their respective teaching assignments as an additional tool for the teaching-learning process. Various sources as mentioned at the reference of the document as well as freely available material from internet were consulted for preparing this document. The ownership of the information lies with the respective author or institutions. Further, this document is not intended to be used for commercial purpose and the faculty is not accountable for any issues, legal or otherwise, arising out of use of this document. The committee faculty members make no representations or warranties with respect to the accuracy or completeness of the contents of this document and specifically disclaim any implied warranties of merchantability or fitness for a particular purpose. BPUT SYLLABUS PRINCIPLES OF EXTRACTIVE METALLURGY (3-1-0) MODULE I (14 HOURS) Unit processes in Pyro metallurgy: Calcination and roasting, sintering, smelting, converting, reduction, smelting-reduction, Metallothermic and hydrogen reduction; distillation and other physical and chemical refining methods: Fire refining, Zone refining, Liquation and Cupellation. Small problems related to pyro metallurgy. MODULE II (14 HOURS) Unit processes in Hydrometallurgy: Leaching practice: In situ leaching, Dump and heap leaching, Percolation leaching, Agitation leaching, Purification of leach liquor, Kinetics of Leaching; Bio- leaching: Recovery of metals from Leach liquor by Solvent Extraction, Ion exchange , Precipitation and Cementation process. -
Understanding Fluid–Rock Interactions and Lixiviant/Oxidant Behaviour for the In-Situ Recovery of Metals from Deep Ore Bodies
School of Earth and Planetary Science Department of Applied Geology Understanding Fluid–Rock Interactions and Lixiviant/Oxidant Behaviour for the In-situ Recovery of Metals from Deep Ore Bodies Tania Marcela Hidalgo Rosero This thesis is presented for the degree of Doctor of Philosophy of Curtin University February 2020 1 Declaration __________________________________________________________________________ Declaration To the best of my knowledge and belief, I declare that this work of thesis contains no material published by any other person, except where due acknowledgements have been made. This thesis contains no material which has been accepted for the award of any other degree or diploma in any university. Tania Marcela Hidalgo Rosero Date: 28/01/2020 2 Abstract __________________________________________________________________________ Abstract In-situ recovery (ISR) processing has been recognised as a possible alternative to open- pit mining, especially for low-grade resources. In ISR, the fluid–rock interaction between the target ore and the lixiviant results in valuable- (and gangue-) metal dissolution. This interaction is achieved by the injection and recovery of fluid by means of strategically positioned wells. Although the application of ISR has become more common (ISR remains the preferential processing technique for uranium and has been applied in pilot programs for treating oxide zones in copper deposits), its application to hard-rock refractory and low-grade copper-sulfide deposits is still under development. This research is focused on the possible application of ISR to primary copper sulfides usually found as deep ores. Lixiviant/oxidant selection is an important aspect to consider during planning and operation in the ISR of copper-sulfide ores. -
(12) United States Patent (10) Patent No.: US 7.449,161 B2 Boryta Et Al
USOO74491.61B2 (12) United States Patent (10) Patent No.: US 7.449,161 B2 Boryta et al. (45) Date of Patent: Nov. 11, 2008 (54) PRODUCTION OF LITHIUM COMPOUNDS 4,207,297 A * 6/1980 Brown et al. ............. 423,179.5 DIRECTLY FROM LITHIUM CONTAINING 4,243,641 A * 1/1981 Ishimori et al. .......... 423/179.5 BRINES 4.261,960 A * 4/1981 Boryta ............. ... 423,179.5 4,271,131. A * 6/1981 Brown et al. ...... ... 423,179.5 4,274,834. A 6/1981 Brown et al. .............. 23,302 R (75) Inventors: Daniel Alfred Boryta, Cherryville, NC 4,463,209 A * 7/1984 Kursewicz et al. .......... 585/467 (US); Teresita Frianeza Kullberg, 4,465,659 A * 8/1984 Cambridge et al. ......... 423,495 Gastonia, NC (US); Anthony Michael 4,588,565 A * 5/1986 Schultze et al. .......... 423,179.5 Thurston, Edmond, OK (US) 4,747.917 A * 5/1988 Reynolds et al. ............ 205,512 4,859,343 A * 8/1989 Frianeza-Kullberg (73) Assignee: Chemetall Foote Corporation, Kings et al. .......................... 210,679 Mountain, NC (US) 4,980,136 A * 12/1990 Brown et al. ... 423,179.5 5,049,233 A 9, 1991 Davis .......................... 216.93 (*) Notice: Subject to any disclaimer, the term of this 5,219,550 A * 6/1993 Brown et al. ............. 423 (419.1 patent is extended or adjusted under 35 5,599,516 A * 2/1997 Bauman et al. .......... 423/179.5 U.S.C. 154(b) by 0 days. 5,939,038 A * 8/1999 Wilkomirsky ............... 423,276 5.993,759 A * 1 1/1999 Wilkomirsky ........... -
The Secondary Phosphate Minerals from Conselheiro Pena Pegmatite District (Minas Gerais, Brazil): Substitutions of Triphylite and Montebrasite Scholz, R.; Chaves, M
The secondary phosphate minerals from Conselheiro Pena Pegmatite District (Minas Gerais, Brazil): substitutions of triphylite and montebrasite Scholz, R.; Chaves, M. L. S. C.; Belotti, F. M.; Filho, M. Cândido; Filho, L. Autor(es): A. D. Menezes; Silveira, C. Publicado por: Imprensa da Universidade de Coimbra URL persistente: URI:http://hdl.handle.net/10316.2/31441 DOI: DOI:http://dx.doi.org/10.14195/978-989-26-0534-0_27 Accessed : 2-Oct-2021 20:21:49 A navegação consulta e descarregamento dos títulos inseridos nas Bibliotecas Digitais UC Digitalis, UC Pombalina e UC Impactum, pressupõem a aceitação plena e sem reservas dos Termos e Condições de Uso destas Bibliotecas Digitais, disponíveis em https://digitalis.uc.pt/pt-pt/termos. Conforme exposto nos referidos Termos e Condições de Uso, o descarregamento de títulos de acesso restrito requer uma licença válida de autorização devendo o utilizador aceder ao(s) documento(s) a partir de um endereço de IP da instituição detentora da supramencionada licença. Ao utilizador é apenas permitido o descarregamento para uso pessoal, pelo que o emprego do(s) título(s) descarregado(s) para outro fim, designadamente comercial, carece de autorização do respetivo autor ou editor da obra. Na medida em que todas as obras da UC Digitalis se encontram protegidas pelo Código do Direito de Autor e Direitos Conexos e demais legislação aplicável, toda a cópia, parcial ou total, deste documento, nos casos em que é legalmente admitida, deverá conter ou fazer-se acompanhar por este aviso. pombalina.uc.pt digitalis.uc.pt 9 789892 605111 Série Documentos A presente obra reúne um conjunto de contribuições apresentadas no I Congresso Imprensa da Universidade de Coimbra Internacional de Geociências na CPLP, que decorreu de 14 a 16 de maio de 2012 no Coimbra University Press Auditório da Reitoria da Universidade de Coimbra. -
Lithium Isotope Effects Upon Electrochemical Release from Lithium Manganese Oxide
Available online at www.sciencedirect.com ScienceDirect Energy Procedia 71 ( 2015 ) 140 – 148 The Fourth International Symposium on Innovative Nuclear Energy Systems, INES-4 Lithium isotope effects upon electrochemical release from lithium manganese oxide Koji OKANOa, Yuta TAKAMIa, Satoshi YANASEa, Takao OIa,* a Faculty of Science and Technology, Sophia University, 7-1 Kioicho, Chiyodaku, Tokyo, 102-8554 Japan Abstract Lithium was electrochemically released from lithium manganese oxide (LiMn2O4) to an electrolyte solution, a 1:2 v/v mixed solution of ethylene carbonate (EC) and ethylmethyl carbonate (EMC) containing 1 M lithium perchlorate or sodium perchlorate (EC/EMC/LiClO4 or EC/EMC/NaClO4) to observe the lithium isotope effects that accompanied the lithium release. The lighter isotope of lithium, 6Li, was preferentially fractionated to the electrolyte solution phase, with the value of the lithium isotope separation factor ranging from 0.989 to 0.971 at 25 ºC. The degree of the lithium isotope fractionation was slightly smaller in the LiMn2O4-EC/EMC/NaClO4 system than in the LiMn2O4-EC/EMC/LiClO4 system. The present systems are in great contrast with the lithium cobalt oxide (LiCoO2)-the electrolyte solution systems concerning the direction and magnitude of the lithium isotope effects, which seems mostly ascribable to the structural difference between LiMn2O4 and LiCoO2ࠋ © 20152014 TheThe Authors. Authors. Published Published by Elsevierby Elsevier Ltd. Ltd.This is an open access article under the CC BY-NC-ND license Selection(http://creativecommons.org/licenses/by-nc-nd/3.0/ and peer-review under responsibility). of the Tokyo Institute of Technology. Selection and peer-review under responsibility of the Tokyo Institute of Technology Keywords: lithium isotopes; isotope effects; lithium manganese oxide; separation factor; lithium ion secondary batteries; ethylene carbonate 1. -
A Study of Lithium Precursors on Nanoparticle Quality
Electronic Supplementary Material (ESI) for Nanoscale. This journal is © The Royal Society of Chemistry 2021 Electronic Supplementary Information Elucidating the role of precursors in synthesizing single crystalline lithium niobate nanomaterials: A study of lithium precursors on nanoparticle quality Rana Faryad Ali, Byron D. Gates* Department of Chemistry and 4D LABS, Simon Fraser University, 8888 University Drive Burnaby, BC, V5A 1S6, Canada * E-mail: [email protected] This work was supported in part by the Natural Sciences and Engineering Research Council of Canada (NSERC; Grant No. RGPIN-2020-06522), and through the Collaborative Health Research Projects (CHRP) Partnership Program supported in part by the Canadian Institutes of Health Research (Grant No. 134742) and the Natural Science Engineering Research Council of Canada (Grant No. CHRP 462260), the Canada Research Chairs Program (B.D. Gates, Grant No. 950-215846), CMC Microsystems (MNT Grant No. 6345), and a Graduate Fellowship (Rana Faryad Ali) from Simon Fraser University. This work made use of 4D LABS (www.4dlabs.com) and the Center for Soft Materials shared facilities supported by the Canada Foundation for Innovation (CFI), British Columbia Knowledge Development Fund (BCKDF), Western Economic Diversification Canada, and Simon Fraser University. S1 Experimental Materials and supplies All chemicals were of analytical grade and were used as received without further purification. Niobium ethoxide [Nb(OC2H5)5, >90%] was obtained from Gelest Inc., and benzyl alcohol (C7H7OH, 99%) and triethylamine [N(C2H5)3, 99.0%] were purchased from Acros Organics and Anachemia, respectively. Lithium chloride (LiCl, ~99.0%) was obtained from BDH Chemicals, and lithium bromide (LiBr, ≥99.0%), lithium fluoride (LiF, ~99.9%), and lithium iodide (LiI, 99.0%) were purchased from Sigma Aldrich. -
Hydrometallurgy – the Basis of Radiochemistry
The Interaction Between Nuclear Chemistry and Hydrometallurgy A Strategy for the Future By Tor Bjørnstad and Dag Øistein Eriksen April 2013 A short history of radiochemistry • 1898: Marie and Pierre Curie discovered Po and Ra by chemical separations of dissolved uranium ore • 1923: de Hevesy uses 212Pb as a tracer to follow the absorption in the roots, stems and leaves of the broad bean • 1929: Ellen Gleditsch appointed professor in inorganic chemistry. Established radiochemistry in Norway in 1916. • 1938: Hahn proves fission of uranium as Ba is separated from irradiated uranium solution • 1940: First transurane produced: Np by McMillan and Abelson • Nuclear power requires separation of fission products Primus.inter.pares AS Nuclear chemistry has contributed to the development of hydrometallurgy The need for safe, remote handling of the laborious separations required in the nuclear sector boosted innovation in: • Solvent extraction: – Continuous, counter current process enabled large quantities to be processed – Contactors like mixer-settlers were developed • Ion exchange to perform difficult purifications Primus.inter.pares AS Hydrometallurgy and nuclear chemistry Nuclear (radio-)chemistry offers special methods useful in hydrometallurgy: • Use of radioactive tracers, i.e. radioactive isotopes of the elements studied – Particularly important in liquid-liquid extraction • Neutron activation can be used on all phases: solid, aqueous-, organic phases (and gas) • AKUFVE-method very efficient in measuring extraction kinetics • Many "hydrometallurgical" elements have suitable isotopes for use as tracers – In addition, e.g. Eu(III) can be used as tracer for Am(III), and 3+ 3+ Nd has equal ionic radius as Am Primus.inter.pares AS Some strategic metals • Lithium for batteries – Scarcity of Li may be a reality. -
Treatment and Microscopy of Gold
TREATMENT AND MICROSCOPY OF GOLD AND BASE METAL ORES. (Script with Sketches & Tables) Short Course by R. W. Lehne April 2006 www.isogyre.com Geneva University, Department of Mineralogy CONTENTS (Script) page 1. Gold ores and their metallurgical treatment 2 1.1 Gravity processes 2 1.2 Amalgamation 2 1.3 Flotation and subsequent processes 2 1.4 Leaching processes 3 1.5 Gold extraction processes 4 1.6 Cyanide leaching vs. thio-compound leaching 5 2. Microscopy of gold ores and treatment products 5 2.1 Tasks and problems of microscopical investigations 5 2.2 Microscopy of selected gold ores and products 6 (practical exercises) 3. Base metal ores and their beneficiation 7 3.1 Flotation 7 3.2 Development of the flotation process 7 3.3 Principles and mechanisms of flotation 7 3.4 Column flotation 9 3.5 Hydrometallurgy 10 4. Microscopy of base metal ores and milling products 10 4.1 Specific tasks of microscopical investigations 11 4.2 Microscopy of selected base metal ores and milling products 13 (practical exercises) 5. Selected bibliography 14 (Sketches & Tables) Different ways of gold concentration 15 Gravity concentration of gold (Agricola) 16 Gravity concentration of gold (“Long Tom”) 17 Shaking table 18 Humphreys spiral concentrator 19 Amalgamating mills (Mexican “arrastra”, Chilean “trapiche”) 20 Pressure oxidation flowsheet 21 Chemical reactions of gold leaching and cementation 22 Cyanide solubilities of selected minerals 23 Heap leaching flowsheet 24 Carbon in pulp process 25 Complexing of gold by thio-compounds 26 Relation gold content / amount of particles in polished section 27 www.isogyre.com Economically important copper minerals 28 Common zinc minerals 29 Selection of flotation reagents 30 Design and function of a flotation cell 31 Column cell flotation 32 Flowsheet of a simple flotation process 33 Flowsheet of a selective Pb-Zn flotation 34 Locking textures 35 2 1. -
Synthesis, Reactivity, and Catalysis of Group 3 and Lanthanide Alkyl Complexes
Synthesis, Reactivity, and Catalysis of Group 3 and Lanthanide Alkyl Complexes By Daniel Steven Levine A dissertation submitted in partial satisfaction of the requirements for the degree of Doctor of Philosophy in Chemistry in the Graduate Division of the University of California, Berkeley Committee in charge: Professor T. Don Tilley, Co-Chair Professor Richard A. Andersen, Co-Chair Professor Alexis T. Bell Summer 2016 Abstract Synthesis, Reactivity, and Catalysis of Group 3 and Lanthanide Alkyl Complexes by Daniel Steven Levine Doctor of Philosophy in Chemistry University of California, Berkeley Professor T. Don Tilley, Co-Chair Professor Richard A. Andersen, Co-Chair Chapter 1. A series of scandium dialkyl complexes, (PNP)ScR2 (R = neopentyl, trimethylsilylmethyl), supported by the monoanionic, chelating PNP ligand (2,5- bis(dialkylphosphinomethyl)pyrrolide; alkyl = cyclohexyl, tert-butyl) was synthesized and the reactivities of these complexes toward simple hydrocarbons was investigated. The scandium– carbon bonds undergo σ-bond metathesis reactions with hydrogen and these complexes are catalysts for the hydrogenation of alkenes. Reactions with primary amines led to formation of amido complexes that undergo cyclometalation via σ-bond metathesis, without involvement of an imido complex intermediate. A variety of carbon-hydrogen bonds are also activated, including sp-, sp2-, and sp3-C–H bonds (intramolecularly in the latter case). Levine, D. S.; Tilley, T. D.; Andersen, R. A. Organometallics 2015, 34 (19), 4647. Chapter 2. Terminal group 3 methylidene complexes are generated by thermolysis of monoanionic PNP-supported scandium and yttrium dialkyl complexes. The reaction mechanism has been probed by deuterium-labeling experiments and DFT calculations. Abstraction of a γ- hydrogen from one alkyl group by the other affords a metallacyclobutane that undergoes [2+2] cycloreversion, analogous to a key step in the olefin metathesis reaction, to generate a methylidene complex and isobutene. -
Identification and Description of Mineral Processing Sectors And
V. SUMMARY OF FINDINGS As shown in Exhibit 5-1, EPA determined that 48 commodity sectors generated a total of 527 waste streams that could be classified as either extraction/beneficiation or mineral processing wastes. After careful review, EPA determined that 41 com modity sectors generated a total of 354 waste streams that could be designated as mineral processing wastes. Exhibit 5-2 presents the 354 mineral processing wastes by commodity sector. Of these 354 waste streams, EPA has sufficient information (based on either analytical test data or engineering judgment) to determine that 148 waste streams are potentially RCRA hazardous wastes because they may exhibit one or more of the RCRA hazardous characteristics: toxicity, ignitability, corro sivity, or reactivity. Exhibit 5-3 presents the 148 RCRA hazardous mineral processing wastes that will be subject to the Land Disposal Restrictions. Exhibit 5-4 identifies the mineral processing commodity sectors that generate RCRA hazardous mineral processing wastes that are likely to be subject to the Land D isposal Restrictions. Exhibit 5-4 also summarizes the total number of hazardous waste streams by sector and the estimated total volume of hazardous wastes generated annually. At this time, however, EPA has insufficient information to determine whether the following nine sectors also generate wastes that could be classified as mineral processing wastes: Bromine, Gemstones, Iodine, Lithium, Lithium Carbonate, Soda Ash, Sodium Sulfate, and Strontium. -
Characterization and Recovery of Copper from Smelting Slag
CHARACTERIZATION AND RECOVERY OF COPPER FROM SMELTING SLAG A. P. GABRIEL*, L. R. SANTOS*, A.C. KASPER*, H. M. VEIT* * Materials Engineering Department, Engineering School, Universidade Federal do Rio Grande do Sul (UFRGS), Porto Alegre, Brazi SUMMARY: 1. INTRODUCTION. 2. EXPERIMENTAL. 2.1 Hazardousness test. 2.2 Chemical and mineralogical characterization. 2.3 Leaching 3. RESULTS AND DISCUSSION 3.1 Hazardousness Test. 3.2 Chemical and mineralogical characterization. 3.3 Leaching. 4. CONCLUSION. REFERENCES. 1. INTRODUCTION The generation of industrial solid waste constitutes an environmental problem that requires efforts for adequate disposal. Currently, in Brazil, solid waste management is standardized, with a classification determining the management according to its hazardous characteristics. ABNT NBR 10004 is a Brazilian Standard to solid waste and classifies its as: Class I (hazardous), Class II - A (non - hazardous and non - inert) and Class II - B (non - hazardous and inert) according to the concentration of elements that have potential risks to the environment and public health (ABNT NBR 10,004, 2004) A process with a large generation of wastes is the production of copper. Several studies in the last decades investigated routes to recovery copper and other metals of interest from the slag (solid waste from the foundry). In the case of primary production, the slag has copper contents between 0.5 and 2% and the volume generated is twice the refined metal (Schlesinger et al., 2011) In addition to primary copper production, there is a significant rate of the copper production from scrap/waste metal. Secondary copper production in Brazil in 2014 reached 23,600 tons, representing around 9% of domestic production. -
Hydrometallurgical Processing of Manganese Ores: a Review
Journal of Minerals and Materials Characterization and Engineering, 2014, 2, 230-247 Published Online May 2014 in SciRes. http://www.scirp.org/journal/jmmce http://dx.doi.org/10.4236/jmmce.2014.23028 Hydrometallurgical Processing of Manganese Ores: A Review Alafara A. Baba1,2*, Lateef Ibrahim1*, Folahan A. Adekola1, Rafiu B. Bale2, Malay K. Ghosh3, Abdul R. Sheik3, Sangita R. Pradhan3, Olushola S. Ayanda4, Ismail O. Folorunsho2 1Department of Industrial Chemistry, University of Ilorin, Ilorin, Nigeria 2Department of Geology and Mineral Sciences, University of Ilorin, Ilorin, Nigeria 3Hydro & Electrometallurgy Department, Institute of Minerals and Materials Technology, Bhubaneswar, India 4Department of Chemistry, Faculty of Applied Sciences, Cape Peninsula University of Technology, Cape Town, South Africa Email: *[email protected], *[email protected] Received 26 January 2014; revised 2 March 2014; accepted 12 March 2014 Copyright © 2014 by authors and Scientific Research Publishing Inc. This work is licensed under the Creative Commons Attribution International License (CC BY). http://creativecommons.org/licenses/by/4.0/ Abstract Hydrometallurgy is the most suitable extractive technique for the extraction and purification of manganese as compared to all other techniques including biometallurgy and pyrometallurgical processes. In the hydrometallurgical processing of manganese from its ore, the leach liquors often contain divalent ions such as iron, manganese, copper, nickel, cobalt and zinc along with other impurities which make manganese very difficult to separate. The processes employed for solu- tion concentration and purification in the hydrometallurgical processing of manganese include precipitation, cementation, solvent extraction and ion exchange. Solvent extraction also proves more efficient and it plays vital roles in the purification and separation of the manganese as com- pared to all other techniques.