Reaching Zero with Renewables
Total Page:16
File Type:pdf, Size:1020Kb
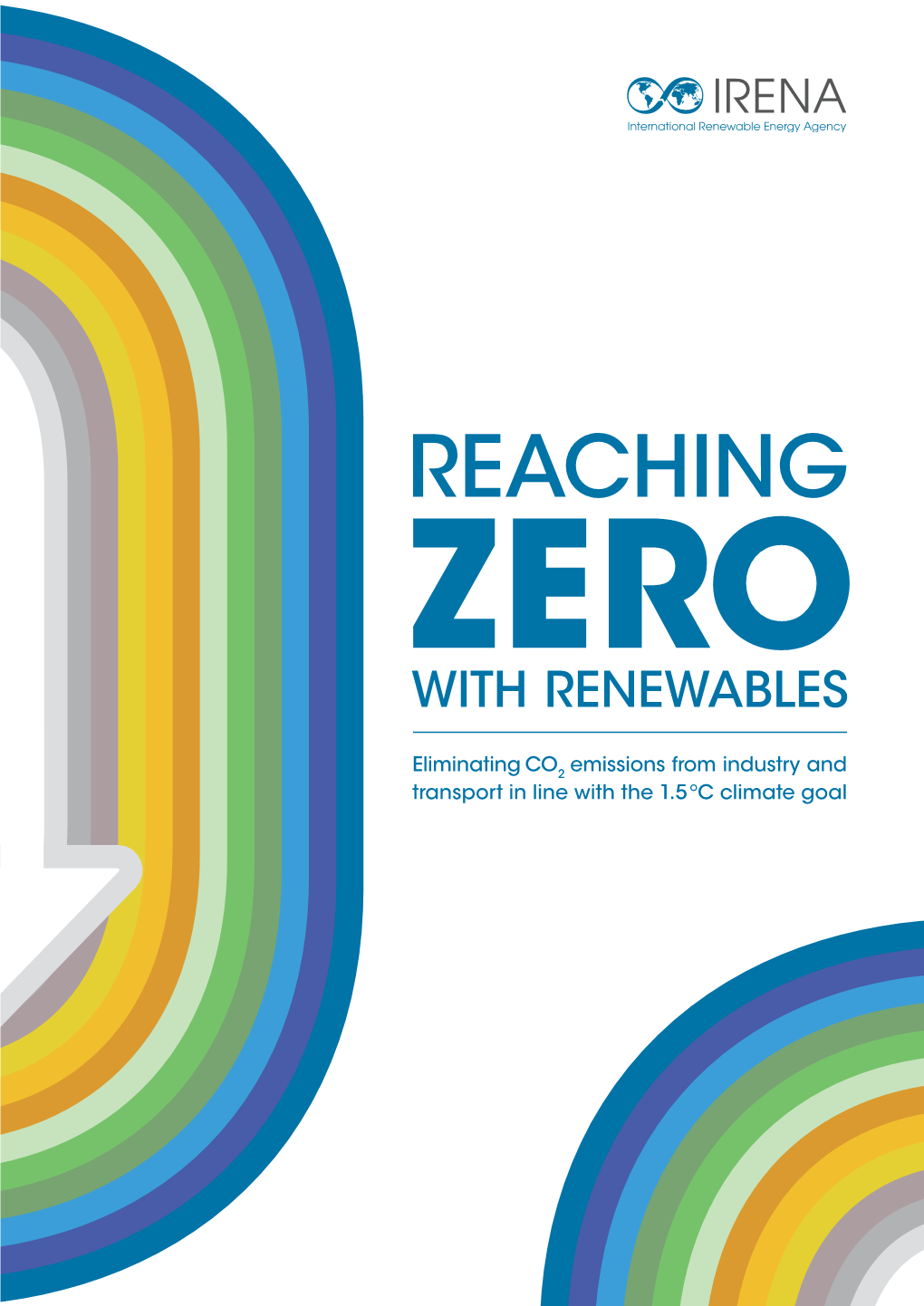
Load more
Recommended publications
-
Capture and Reuse of Carbon Dioxide (CO2) for a Plastics Circular Economy: a Review
processes Review Capture and Reuse of Carbon Dioxide (CO2) for a Plastics Circular Economy: A Review Laura Pires da Mata Costa 1 ,Débora Micheline Vaz de Miranda 1, Ana Carolina Couto de Oliveira 2, Luiz Falcon 3, Marina Stella Silva Pimenta 3, Ivan Guilherme Bessa 3,Sílvio Juarez Wouters 3,Márcio Henrique S. Andrade 3 and José Carlos Pinto 1,* 1 Programa de Engenharia Química/COPPE, Universidade Federal do Rio de Janeiro, Cidade Universitária, CP 68502, Rio de Janeiro 21941-972, Brazil; [email protected] (L.P.d.M.C.); [email protected] (D.M.V.d.M.) 2 Escola de Química, Universidade Federal do Rio de Janeiro, Cidade Universitária, CP 68525, Rio de Janeiro 21941-598, Brazil; [email protected] 3 Braskem S.A., Rua Marumbi, 1400, Campos Elíseos, Duque de Caxias 25221-000, Brazil; [email protected] (L.F.); [email protected] (M.S.S.P.); [email protected] (I.G.B.); [email protected] (S.J.W.); [email protected] (M.H.S.A.) * Correspondence: [email protected]; Tel.: +55-21-3938-8709 Abstract: Plastic production has been increasing at enormous rates. Particularly, the socioenvi- ronmental problems resulting from the linear economy model have been widely discussed, espe- cially regarding plastic pieces intended for single use and disposed improperly in the environment. Nonetheless, greenhouse gas emissions caused by inappropriate disposal or recycling and by the Citation: Pires da Mata Costa, L.; many production stages have not been discussed thoroughly. Regarding the manufacturing pro- Micheline Vaz de Miranda, D.; Couto cesses, carbon dioxide is produced mainly through heating of process streams and intrinsic chemical de Oliveira, A.C.; Falcon, L.; Stella transformations, explaining why first-generation petrochemical industries are among the top five Silva Pimenta, M.; Guilherme Bessa, most greenhouse gas (GHG)-polluting businesses. -
Pv/Battery Waste Management in the Context of Rural Electrification Support on Pv/Battery Waste Management for a Rural Electrification Program
PV/BATTERY WASTE MANAGEMENT IN THE CONTEXT OF RURAL ELECTRIFICATION SUPPORT ON PV/BATTERY WASTE MANAGEMENT FOR A RURAL ELECTRIFICATION PROGRAM Amy Author, Bode Author, and Catherine Author National Renewable Energy Laboratory David Author and Emily Author Other Organization Document elaborated by Factor November 2016 PV/BATTERY WASTE MANAGEMENT IN THE CONTEXT OF RURAL ELECTRIFICATION SUPPORT ON PV/BATTERY WASTE MANAGEMENT FOR A RURAL ELECTRIFICATION PROGRAM Document elaborated by Factor November 2016 This publication was reproduced from the best available copy submitted by the subcontractor and received no editorial review at NREL. NOTICE This report was prepared as an account of work sponsored by an agency of the United States government. Neither the United States government nor any agency thereof, nor any of their employees, makes any warranty, express or implied, or assumes any legal liability or responsibility for the accuracy, completeness, or usefulness of any information, apparatus, product, or process disclosed, or represents that its use would not infringe privately owned rights. Reference herein to any specific commercial product, process, or service by trade name, trademark, manufacturer, or otherwise does not necessarily constitute or imply its endorsement, recommendation, or favoring by the United States government or any agency thereof. The views and opinions of authors expressed herein do not necessarily state or reflect those of the United States government or any agency thereof. This report is available at no cost from the National Renewable Energy Laboratory (NREL) at www.nrel.gov/publications. Available electronically at SciTech Connect http:/www.osti.gov/scitech Available for a processing fee to U.S. -
Fortificants
GFF5.qxd 14/11/06 16:44 Page 93 PA RT I I I Fortificants: physical characteristics, selection and use with specific food vehicles GFF5.qxd 14/11/06 16:44 Page 94 GFF5.qxd 14/11/06 16:44 Page 95 Introduction By providing a critical review of the fortificants that are currently available for fortification purposes, Part III of these guidelines is intended to assist pro- gramme managers in their choice of firstly, a suitable food vehicle and secondly, a compatible fortificant. Having established – through the application of appro- priate criteria – that the nature of the public health risk posed by a micronutri- ent deficiency justifies intervention in the form of food fortification, the selection of a suitable combination of food vehicle and fortificant(s), or more specifically, the chemical form of the micronutrient(s) that will added to the chosen food vehicle, is fundamental to any food fortification programme. Subsequent chap- ters (Part IV) cover other important aspects of food fortification programme planning, including how to calculate how much fortificant to add to the chosen food vehicle in order to achieve a predetermined public health benefit (Chapter 7), monitoring and impact evaluation (Chapters 8 and 9), marketing (Chapter 10) and regulatory issues (Chapter 11). In practice, the selection of a food vehicle–fortificant combination is governed by range of factors, both technological and regulatory. Foods such as cereals, oils, dairy products, beverages and various condiments such as salt, sauces (e.g. soy sauce) and sugar are particularly well suited to mandatory mass fortifica- tion. These foods share some or all of the following characteristics: • They are consumed by a large proportion of the population, including (or especially) the population groups at greatest risk of deficiency. -
Implementation of Electrofuel Production at a Biogas Plant Case Study at Borås Energi & Miljö Master’S Thesis Within the Sustainable Energy Systems Programme
Biogas Digester Rawgas Gas upgrade Gas CO2 Biogas Organic waste Sabatier reactor Implementation of electrofuel production at a biogas plant Case study at Borås Energi & Miljö Master’s Thesis within the Sustainable Energy Systems programme TOBIAS JOHANNESSON Department of Energy and Environment Division of Physical Resource Theory Chalmers University of Technology Göteborg, Sweden 2016 FRT 2016:03 master’s thesis Implementation of electrofuel production at a biogas plant Case study at Borås Energi & Miljö Master’s Thesis within the Sustainable Energy Systems programme tobias johannesson supervisors: Stavros Papadokonstantakis & Camilla Ölander Examiner Maria Grahn Department of Energy and Environment Division of Physical Resource Theory chalmers university of technology Göteborg, Sweden 2016 Implementation of electrofuel production at a biogas plant Case study at Borås Energi & Miljö Master’s Thesis within the Sustainable Energy Systems programme TOBIAS JOHANNESSON FRT 2016:03 © TOBIAS JOHANNESSON, 2016 Department of Energy and Environment Division of Physical Resource Theory Chalmers University of Technology SE-412 96 Göteborg Sweden Telephone: + 46 (0)31-772 10 00 Cover: Schematic picture over a simplified biogas process with an implemented Sabatier reactor. Chalmers Reproservice Göteborg, Sweden 2016 Implementation of electrofuel production at a biogas plant Case study at Borås Energi & Miljö Master’s Thesis within the Sustainable Energy Systems programme TOBIAS JOHANNESSON Department of Energy and Environment Division of Physical Resource Theory Chalmers University of Technology Abstract One way to decrease the emissions of greenhouse gases is to use a renewable vehicle fuel, such as biogas. By separating methane from carbon dioxide in raw gas in a gas upgrading system, biogas is produced. -
Gas Fermentation of C1 Feedstocks: Commercialization Status and Future Prospects
Review Gas fermentation of C1 feedstocks: commercialization status and future prospects Leonardo V. Teixeira, Liza F. Moutinho, and Aline S. Romão-Dumaresq, SENAI Innovation Institute for Biosynthetics, Technology Center for Chemical and Textile Industry, Rio de Janeiro, Brazil Received December 04, 2017; revised June 04, 2018; accepted June 05, 2018 View online at Wiley Online Library (wileyonlinelibrary.com); DOI: 10.1002/bbb.1912; Biofuels, Bioprod. Bioref. (2018) Abstract: The increasing emissions of carbon dioxide, methane and carbon oxide (collectively referred as C1 compounds) are likely to configure a major contribution to global warming and other envi- ronmental issues. The implementation of carbon capture and storage (CCS) is considered a crucial strategy to prevent global warming, but the overall costs of currently available CCS technologies are still prohibitive for its large-scale deployment. Using microorganisms capable of assimilating C1 com- pounds for producing value-added products could be an important driver for mitigating emissions and minimizing their deleterious consequences, while simultaneously deriving additional economic benefits from these compounds. This review summarizes the main microorganisms and metabolic routes being investigated, with special focus on both the products targeted and the current industrial initiatives. There are a number of companies investing in these routes and in some instances commercial deploy- ment was identified. Despite the variety of commercially-appealing products, genetic manipulation -
Role of Natural Gas Networks in a Low-Carbon Future
The Role of Gas Networks in a Low-Carbon Future December 2020 Contents Executive Summary ...................................................................................................................................... 3 The Role of Natural Gas ............................................................................................................................... 6 Natural Gas Today .................................................................................................................................... 6 The Potential Role of Natural Gas Networks in a Low-Carbon Future .................................................... 7 Local Distribution Company Strategies to Decarbonize Gas ....................................................................... 8 Increasing Energy Efficiency and Optimizing Energy Use ...................................................................... 9 Reducing Methane Emissions Across the Value Chain .......................................................................... 15 Decarbonizing Gas Supply ..................................................................................................................... 19 Carbon Capture, Utilization, and Sequestration .......................................................................................... 24 Conclusion .................................................................................................................................................. 26 M.J. Bradley & Associates | Strategic Environmental Consulting Page | 1 -
Syngas Derived from Lignocellulosic Biomass Gasification As An
processes Review Syngas Derived from Lignocellulosic Biomass Gasification as an Alternative Resource for Innovative Bioprocesses Cosetta Ciliberti 1, Antonino Biundo 1,2, Roberto Albergo 3 , Gennaro Agrimi 1,2 , Giacobbe Braccio 3, Isabella de Bari 3 and Isabella Pisano 1,2,* 1 Department of Bioscience, Biotechnology and Biopharmaceutics, University of Bari, Via Edoardo Orabona, 4, 70125 Bari, Italy; [email protected] (C.C.); [email protected] (A.B.); [email protected] (G.A.) 2 Interuniversity Consortium for Biotechnology (CIB), 34100 Trieste, Italy 3 Italian National Agency for New Technologies, Energy and Sustainable Economic Development (ENEA), Division of Bioenergy, Biorefinery and Green Chemistry, C.R. Trisaia S.S. 106 Jonica, 75026 Rotondella (MT), Italy; [email protected] (R.A.); [email protected] (G.B.); [email protected] (I.d.B.) * Correspondence: [email protected] Received: 3 November 2020; Accepted: 24 November 2020; Published: 28 November 2020 Abstract: A hybrid system based on lignocellulosic biomass gasification and syngas fermentation represents a second-generation biorefinery approach that is currently in the development phase. Lignocellulosic biomass can be gasified to produce syngas, which is a gas mixture consisting mainly of H2, CO, and CO2. The major challenge of biomass gasification is the syngas’s final quality. Consequently, the development of effective syngas clean-up technologies has gained increased interest in recent years. Furthermore, the bioconversion of syngas components has been intensively studied using acetogenic bacteria and their Wood–Ljungdahl pathway to produce, among others, acetate, ethanol, butyrate, butanol, caproate, hexanol, 2,3-butanediol, and lactate. Nowadays, syngas fermentation appears to be a promising alternative for producing commodity chemicals in comparison to fossil-based processes. -
Assessing the Role of Carbon Dioxide Removal in Companies' Climate
Net Expectations Assessing the role of carbon dioxide removal in companies’ climate plans. Briefing by Greenpeace UK January 2021 ~ While a few companies plan to deliver CDR Executive in specific projects, many plan to simply purchase credits on carbon markets, summary which have been beset with integrity problems and dubious accounting, even where certified. To stabilise global temperatures at any level – whether 1.5˚C, 2˚C, 3˚C or 5˚C Limits and uncertainties – carbon dioxide (CO2) emissions must The IPCC warns that reliance on CDR is a major reach net zero at some point, because risk to humanity’s ability to achieve the Paris goals. of CO2’s long-term, cumulative effect. The uncertainties are not whether mechanisms to remove CO2 “work”: they all work in a laboratory According to the Intergovernmental at least. Rather, it is whether they can be delivered Panel on Climate Change (IPCC), at scale, with sufficient funding and regulation, to store CO2 over the long term without unacceptable limiting warming to 1.5˚C requires net- social and environmental impacts. zero CO2 to be reached by about 2050. To illustrate the need for regulation, the carbon A small proportion of emissions is likely to be dioxide captured by forests is highly dependent on unavoidable and must be offset by carbon dioxide their specific circumstances, including their removal (CDR), such as by tree-planting (afforestation/ species diversity, the prior land use, and future reforestation) or by technological approaches like risks to the forest (such as fires or pests). In some bioenergy with carbon capture and storage (BECCS) cases, forests and BECCS can increase rather than or direct air carbon capture with storage (DACCS). -
Electrification Futures Study: Scenarios of Electric Technology Adoption and Power Consumption for the United States
Electrification Futures Study: Scenarios of Electric Technology Adoption and Power Consumption for the United States Trieu Mai, Paige Jadun, Jeffrey Logan, Colin McMillan, Matteo Muratori, Daniel Steinberg, Laura Vimmerstedt, Ryan Jones, Benjamin Haley, and Brent Nelson Electrification Futures Study: Scenarios of Electric Technology Adoption and Power Consumption for the United States Trieu Mai, Paige Jadun, Jeffrey Logan, Colin McMillan, Matteo Muratori, Daniel Steinberg, and Laura Vimmerstedt National Renewable Energy Laboratory Ryan Jones and Benjamin Haley Evolved Energy Research Brent Nelson Northern Arizona University Suggested Citation Mai, Trieu, Paige Jadun, Jeffrey Logan, Colin McMillan, Matteo Muratori, Daniel Steinberg, Laura Vimmerstedt, Ryan Jones, Benjamin Haley, and Brent Nelson. 2018. Electrification Futures Study: Scenarios of Electric Technology Adoption and Power Consumption for the United States. Golden, CO: National Renewable Energy Laboratory. NREL/TP-6A20-71500. https://www.nrel.gov/docs/fy18osti/71500.pdf. iii This report is available at no cost from the National Renewable Energy Laboratory (NREL) at www.nrel.gov/publications. NOTICE This work was authored in part by the National Renewable Energy Laboratory, operated by Alliance for Sustainable Energy, LLC, for the U.S. Department of Energy (DOE) under Contract No. DE-AC36- 08GO28308. Funding provided by U.S. Department of Energy Office of Energy Efficiency and Renewable Energy Office of Strategic Programs. The views expressed in the article do not necessarily represent the views of the DOE or the U.S. Government. This report is available at no cost from the National Renewable Energy Laboratory (NREL) at www.nrel.gov/publications. U.S. Department of Energy (DOE) reports produced after 1991 and a growing number of pre-1991 documents are available free via www.OSTI.gov. -
Renewable Energy Resorces for Climate Change Mitigation
Raghuvanshi et al.: Renewable energy resources for climate change mitigation - 15 - RENEWABLE ENERGY RESOURCES FOR CLIMATE CHANGE MITIGATION S.P. RAGHUVANSHI * – A.K. RAGHAV – A. CHANDRA Indian Institute of Technology Delhi, Hauz Khas, New Delhi, India. (phone : +91-11-26591227) *Corresponding author e-mail: [email protected] (Received 13rd November 2006 ; accepted 4 th July 2007) Abstract. Climate change has been identified as one of the greatest challenge by all the nations, government, business and citizens of the globe. The threats of climate change on our green planet ‘Earth’ demands that renewable energy share in the total energy generation and consumption should be substantially increased as a matter of urgency. India’s energy development programme has been put under severe pressure with the ever-increasing demand supply gap. Due to predominance of fossil fuels in the generation mix, there are large negative environmental externalities caused by electricity generation. So it has become imperative to develop and promote alternative energy sources that can lead to sustainability of energy and environment system. Renewable electricity has become synonymous with CO2 reduction. Present communication provides a brief description about such alternative and sustained energy sources, i.e., renewable energy resources, their potential and achievements in India. Also role as important tool for climate change mitigation . Keywords: Renewable energy, GHGs, Climate change, Carbon dioxide, mitigation Introduction Climate change has implications for both human and natural systems and could lead to significant changes in resource use production and economic activity. In response to the impact and possible affects of climate change international, regional, national and local initiatives are being developed and implemented to limit and mitigate GHGs concentration in the Earth’s atmosphere. -
National Policies and the Role of Communities, Cities and Regions
CLIMATE CHANGE AND RENEWABLE ENERGY NATIONAL POLICIES AND THE ROLE OF COMMUNITIES, CITIES AND REGIONS A report from the International Renewable Energy Agency (IRENA) to the G20 Climate Sustainability Working Group (CSWG) JUNE 2019 © IRENA 2019 Unless otherwise stated, material in this publication may be freely used, shared, copied, reproduced, printed and/or stored, provided that appropriate acknowledgement is given to IRENA as the source and copyright holder. Material in this publication that is attributed to third parties may be subject to separate terms of use and restrictions, and appropriate permissions from these third parties may need to be secured before any use of such material. ISBN: 978-92-9260-136-2 Citation: IRENA (2019), Climate Change and Renewable Energy: National policies and the role of communities, cities and regions (Report to the G20 Climate Sustainability Working Group (CSWG)), International Renewable Energy Agency, Abu Dhabi. About IRENA The International Renewable Energy Agency (IRENA) is an intergovernmental organisation that supports countries in their transition to a sustainable energy future and serves as the principal platform for international co-operation, a centre of excellence, and a repository of policy, technology, resource and financial knowledge on renewable energy. IRENA promotes the widespread adoption and sustainable use of all forms of renewable energy, including bioenergy, geothermal, hydropower, ocean, solar and wind energy, in the pursuit of sustainable development, energy access, energy security and low-carbon economic growth and prosperity. www.irena.org Acknowledgements G20 Climate Sustainability Working Group members provided valuable comments and suggestions on this study. The report was prepared by Elisa Asmelash and Ricardo Gorini. -
Standard Reference Materials Price and Availability List IMPORTANT NOTICE to PURCHASERS and USERS of NBS STANDARD REFERENCE MATERIALS
o A UNITED STATES NBS SPECIAL PUBLICATION DEPARTMENTucrnn 1 ivitii 1 urOF COMMERCE PUBLICATION 260 [ A SUPPLEMENT JANUARY, 1972 Standard Reference Materials Price and Availability List IMPORTANT NOTICE TO PURCHASERS AND USERS OF NBS STANDARD REFERENCE MATERIALS The Office of Standard Reference Materials no longer issues the Quarterly Insert Sheets to update the current issue of the SRM Catalog. Instead a Standard Reference Material Availability and Price List is issued semiannually. The format has been changed to improve readability and the List is organized as follows: Section I - A list of all classes of materials currently available arranged by Standard Reference Material (SRM), Research Material (RM), and General Material (GM) numbers, together with type, unit of issue, and current price. Section Ila — A list of all classes of materials that have been issued since the Catalog (July 1970) was published, arranged by SRM, RM, and GM numbers together with catalog category. Section lib — A short description, arranged by catalog category, of all SRM's issued since the Catalog (July 1970) was published and therefore not contained therein. For ease of reproduction, tables have been condensed and are, in general, not in the same format used in the catalog. (Please note that the values shown are nominal values. The actual values certified are given on the Certificate which accompanies the material.) The unit of issue and price are given after the description of each SRM. Section llla — A list, arranged by SRM numbers, of recently issued certificates (final or revised versions). Section Illb — A list, arranged by SRM, RM, and GM numbers, of all items that have gone out of stock since the effective date of the current catalog.