KSU Laboratory Safety Manual
Total Page:16
File Type:pdf, Size:1020Kb
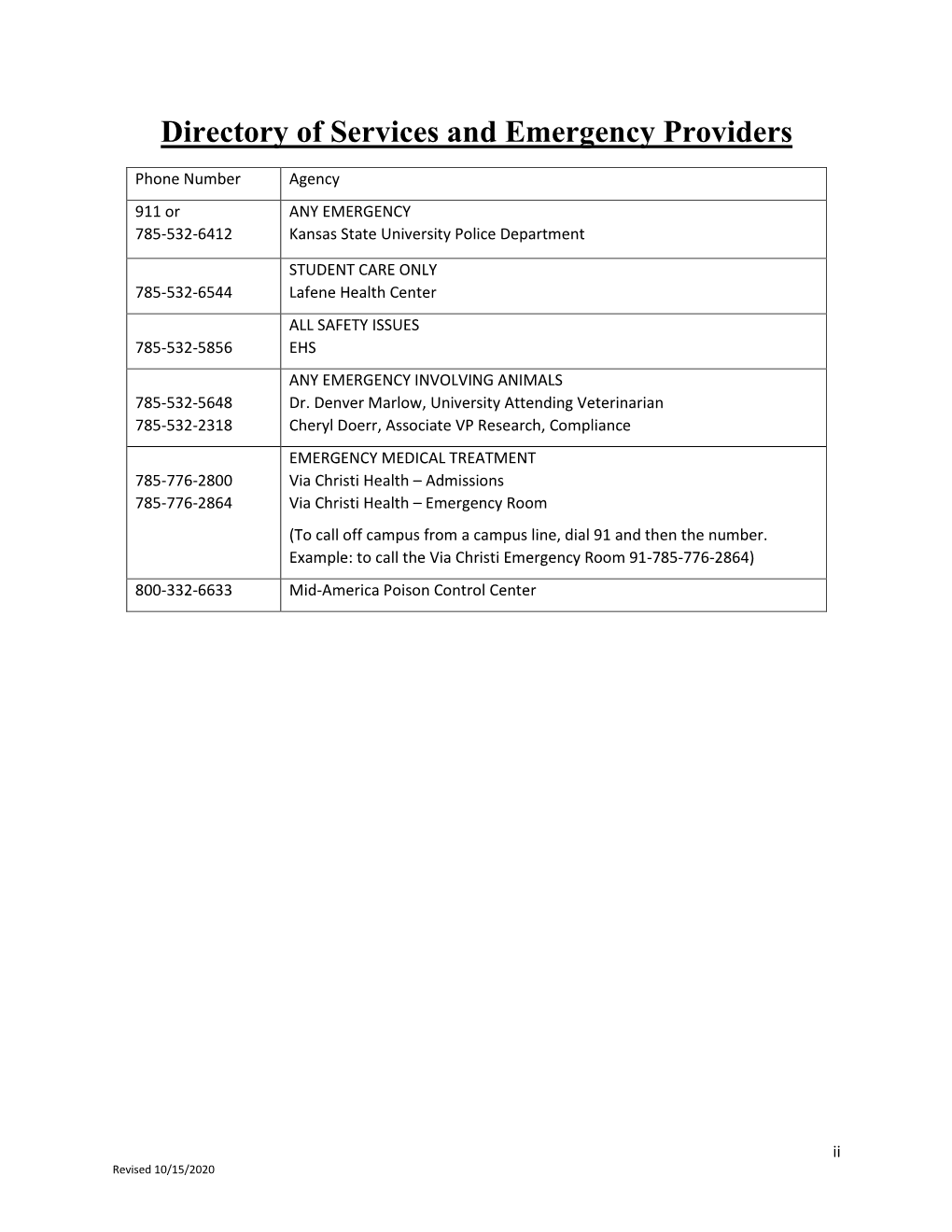
Load more
Recommended publications
-
Hazardous Laboratory Chemicals Disposal Guide
Third Edition HAZARDOUS LABORATORY CHEMICALS DISPOSAL GUIDE Third Edition HAZARDOUS LABORATORY CHEMICALS DISPOSAL GUIDE Margaret-Ann Armour LEWIS PUBLISHERS A CRC Press Company Boca Raton London New York Washington, D.C. This edition published in the Taylor & Francis e-Library, 2005. To purchase your own copy of this or any of Taylor & Francis or Routledge’s collection of thousands of eBooks please go to http://www.ebookstore.tandf.co.uk/. Library of Congress Cataloging-in-Publication Data Armour, M.A. (Margaret-Ann) Hazardous laboratory chemicals disposal guide/Margaret-Ann Armour.—3rd ed. p. cm. Includes bibliographical references. ISBN 1-56670-567-3 1. Chemical laboratories—Waste disposal. 2. Hazardous substances. I. Title. QD64.A76 2003 542′.89–dc21 2002043358 This book contains information obtained from authentic and highly regarded sources. Reprinted material is quoted with permission, and sources are indicated. A wide variety of references are listed. Reasonable efforts have been made to publish reliable data and information, but the authors and the publisher cannot assume responsibility for the validity of all materials or for the consequences of their use. Neither this book nor any part may be reproduced or transmitted in any form or by any means, electronic or mechanical, including photocopying, microfilming, and recording, or by any information storage or retrieval system, without prior permission in writing from the publisher. The consent of CRC Press LLC does not extend to copying for general distribution, for promotion, for creating new works, or for resale. Specific permission must be obtained in writing from CRC Press LLC for such copying. Direct all inquiries to CRC Press LLC, 2000 N.W. -
Microbial Dissolution and Stabilization of Toxic Metals and Radionuclides In
840 Experientia 46 (1990), Birkh~iuser Verlag, CH-4010 Basel/Switzerland Reviews 34 Trevors, J. T., Stratton, G. W., and Gadd, G. M., Cadmium transport, 38 Tsezos, M., and Volesky, B., The mechanism of uranium biosorption resistance and toxicity in bacteria, algae and fungi. Can. J. Microbiol. by Rhizopus arrhizus. Biotechnol. Bioeng. 24 (1982) 385-401. 32 (1986) 447-464. 39 Wainwright, M., and Grayston, S. J., Accumulation and oxidation of 35 Tsezos, M., Recovery of uranium from biological adsorbents-desorp- metal sulphides by fungi, in: Metal-Microbe Interactions, pp. 119- tion equilibrium. Biotechnol. Bioeng. 26 (1984) 973-981. 130. IRL Press, Oxford 1989. 36 Tsezos, M., Absorption by microbial biomass as a process for removal of ions from process or waste solutions, in: Immobilization of Ions by Bio-sorption, pp. 201-218. Ellis Horwood, Chichester 1986. 37 Tsezos, M., and Volesky, B., Biosorption of uranium and thorium. 0014-4754/90/080834-0751.50 + 0.20/0 Biotechnol. Bioeng. 22 (1981) 583-604. Birkhfiuser Verlag Basel, 1990 Microbial dissolution and stabilization of toxic metals and radionucfides in mixed wastes A. J. Francis Department of Applied Science, Brookhaven National Laboratory, Upton (New York 11973, USA) Summary. Microbial activity in mixed wastes can have an appreciable effect on the dissolution or precipitation of toxic metals and radionuclides. Fundamental information on microbial dissolution and stabilization (immobilization) of toxic metals and radionuclides, in particular actinides and fission products, in nuclear wastes under various microbial process conditions, e.g., aerobic, denitrifying, iron-reducing, fermentative, sulfate-reducing, and methanogenic conditions is very limited. Microbial transformations of typical waste components such as metal oxides, metal coprecipitates, naturally occurring minerals, and metal organic complexes are reviewed. -
Physical and Chemical Properties of Platinum Group Metals 2 Chapter 2 | Physical and Chemical Properties of Platinum Group Metals Contents
PHYSICAL AND CHEMICAL PROPERTIES OF PLATINUM GROUP METALS 2 CHAPTER 2 | PHYSICAL AND CHEMICAL PROPERTIES OF PLATINUM GROUP METALS CONTENTS 2.1 OVERVIEW OF PGMS 04 2.2 METALLIC PGMS 05 2.3 COMPOUNDS OF PLATINUM GROUP METALS 06 SIMPLE COMPOUNDS 06 COMPLEX COMPOUNDS 07 REFERENCES 13 2 CHAPTER 2 | PHYSICAL AND CHEMICAL PROPERTIES OF PLATINUM GROUP METALS SUMMARY • Six elements of Groups 8, 9, and 10 in the periodic table constitute the platinum group metals (PGMs): platinum (Pt), palladium (Pd), rhodium (Rh), ruthenium (Ru), iridium (Ir), and osmium (Os). • The physical and mechanical properties of the PGMs and their compounds indicate a wide range of properties with widely varying densities and solubilities (see Table 2-1). • Metallic forms of PGMs are generally considered to be ‘inert’, i.e., not chemically reactive. However, this is dependent in part on dimensional characteristics. Thus, while massive metal forms have low chemical reactivity, fi nely-divided metal powders with high surface area show greater reactivity. • Simple binary compounds exist for each of the PGMs. They also form a vast array of complex coordination compounds in which the central metal atom is bound to a variety of ligands by coordinate bonding, including halides, sulphur, amines, and other atoms and groups. • This unique coordination chemistry has made PGM compounds of great industrial value, but also can have implications for the health of workers exposed to certain of these compounds due to the linkages with biological behaviour and toxicity (see Chapter 6). • The complex halogenated platinum compounds (CHPS) are among those which are industrially and toxicologically important. -
STUDIES in the DIPHENYL SERIES by JOSEPH LAVERIE, B.Sc
STUDIES IN THE DIPHENYL SERIES by JOSEPH LAVERIE, B.Sc., A.R.I.C. A thesis submitted in fulfilment of the requirements for the degree of Doctor of Philosophy in the Faculty of Science of Glasgow University. JUNE, 1949. ProQuest Number: 13870131 All rights reserved INFORMATION TO ALL USERS The quality of this reproduction is dependent upon the quality of the copy submitted. In the unlikely event that the author did not send a com plete manuscript and there are missing pages, these will be noted. Also, if material had to be removed, a note will indicate the deletion. uest ProQuest 13870131 Published by ProQuest LLC(2019). Copyright of the Dissertation is held by the Author. All rights reserved. This work is protected against unauthorized copying under Title 17, United States C ode Microform Edition © ProQuest LLC. ProQuest LLC. 789 East Eisenhower Parkway P.O. Box 1346 Ann Arbor, Ml 48106- 1346 The author wishes to express his thanks to Professor W.M. Gumming, O.B.E., D.Sc., P.R.I.C., M.I.Chem.E., F.R.S.E., and to Dr. I.V. Hopper, B.Sc., Ph.D., A.R.C.S.I., F.R.I.C., for their supervision, interest and encouragement throughout the course of this research. He also wishes to thank the Governors of the Royal Technical College, Glasgow, for the research facilities granted to him. STUDIES IN THE DIPHENYL SERIES. PAGE SUMMARY ......................................... 1 GENERAL INTRODUCTION ........................... 8 Nomenclature . ................. 8 Methods of preparation of Diphenyl Derivatives • • .12 A Symmetrical Diphenyls • • • . .13 B Unsymmetrical Diphenyls • • 16 m i I INTRODUCTION . -
SYNTHESES Volume XIV Editors AARON WOLD JOHN K
INORGANIC SYNTHESES Volume XIV Editors AARON WOLD JOHN K. RUFF Professor of Engineering Associate Professor of Chemistry and Chemistry University of Georgia Brown University, Providence, R.I. Athens, Ca. INORGANIC SYNTHESES Volume XIV McCRAW-HILL BOOK COMPANY New York St. Louis San Francisco Diisseldorf Johannesburg Kualo Lumpur London Mexico Montreal New Delhi Panama Rio de Janeiro Singapore Sydney Toronto INORGANIC SYNTHESES, VOLUME XIV Copyright 0 1973 by McGraw-Hill, Inc. All Rights Rewved. Printed in the United States of America. No part of this publication may be reproduced, stored in a retrieval system, or transmitted, in any form or by any means, electronic, mechanical, photocopying, recording, or otherwise. without the prior written permission of the publisher. Library of Congress Catalog Card Number 39-23015 07-07 1320-0 1234567890 KPKP 76543 To RONALD NYHOLM and DAVID WADSLEY CONTENTS Reface ........................................... xi Notice to Contributors ................................... xiii Chapter One PHOSPHORUS COMPOUNDS ............... 1 1 . Phosphine ....................................... 1 2 . tert-Butyldichlorophosphineand Di-tert-butylchlorophosphinc......... 4 A . tert-Butyldichlorophosphinc ......................... 5 B . Di-tert-butylchlorophosphinc ......................... 6 3. 1.2-Bis(phosphino)ethane ............................. 10 4 . Tctramcthyldiphosphineand Flexible Aliphatic (Dimethylphosphino) Ligands ........................... 14 A . TetramethyldiphosFhine............................. 15 B . -
The Preparation and Characterization of Some Alkanethiolatoosmium Compounds Harold Harris Schobert Iowa State University
Iowa State University Capstones, Theses and Retrospective Theses and Dissertations Dissertations 1970 The preparation and characterization of some alkanethiolatoosmium compounds Harold Harris Schobert Iowa State University Follow this and additional works at: https://lib.dr.iastate.edu/rtd Part of the Inorganic Chemistry Commons Recommended Citation Schobert, Harold Harris, "The preparation and characterization of some alkanethiolatoosmium compounds " (1970). Retrospective Theses and Dissertations. 4357. https://lib.dr.iastate.edu/rtd/4357 This Dissertation is brought to you for free and open access by the Iowa State University Capstones, Theses and Dissertations at Iowa State University Digital Repository. It has been accepted for inclusion in Retrospective Theses and Dissertations by an authorized administrator of Iowa State University Digital Repository. For more information, please contact [email protected]. 71-14,258 SCHOBERT, Harold Harris, 1943- THE PREPARATION AND CHARACTERIZATION OF SOME ALKANETHIOLATOOSMIUM COMPOUNDS. Iowa State University, Ph.D., 1970 Chemistry, inorganic University Microfilms, A XEROX Company, Ann Arbor, Michigan THIS DISSERTATION HAS BEEH MICROFILMED EXACTLY AS RECEIVED THE PREPARATION AND CHARACTERIZATION OF SOME ALKANETHIOLATOOSMIUM COMPOUNDS by Harold Harris Schobert A Dissertation Submitted to the Graduate Faculty in Partial Fulfillment of The Requirements for the Degree of DOCTOR OF PHILOSOPHY Major Subject: Inorganic Chemistry Approved: Signature was redacted for privacy. Signature was redacted for -
Hazardous Laboratory Chemicals Disposal Guide
Third Edition HAZARDOUS LABORATORY CHEMICALS DISPOSAL GUIDE Third Edition HAZARDOUS LABORATORY CHEMICALS DISPOSAL GUIDE Margaret-Ann Armour LEWIS PUBLISHERS A CRC Press Company Boca Raton London New York Washington, D.C. This edition published in the Taylor & Francis e-Library, 2005. To purchase your own copy of this or any of Taylor & Francis or Routledge’s collection of thousands of eBooks please go to http://www.ebookstore.tandf.co.uk/. Library of Congress Cataloging-in-Publication Data Armour, M.A. (Margaret-Ann) Hazardous laboratory chemicals disposal guide/Margaret-Ann Armour.—3rd ed. p. cm. Includes bibliographical references. ISBN 1-56670-567-3 1. Chemical laboratories—Waste disposal. 2. Hazardous substances. I. Title. QD64.A76 2003 542′.89–dc21 2002043358 This book contains information obtained from authentic and highly regarded sources. Reprinted material is quoted with permission, and sources are indicated. A wide variety of references are listed. Reasonable efforts have been made to publish reliable data and information, but the authors and the publisher cannot assume responsibility for the validity of all materials or for the consequences of their use. Neither this book nor any part may be reproduced or transmitted in any form or by any means, electronic or mechanical, including photocopying, microfilming, and recording, or by any information storage or retrieval system, without prior permission in writing from the publisher. The consent of CRC Press LLC does not extend to copying for general distribution, for promotion, for creating new works, or for resale. Specific permission must be obtained in writing from CRC Press LLC for such copying. Direct all inquiries to CRC Press LLC, 2000 N.W. -
Insights Into the Electronic Structure of $ {\Rm Oso} 2$ Using Soft and Hard
PHYSICAL REVIEW MATERIALS 3, 025001 (2019) Insights into the electronic structure of OsO2 using soft and hard x-ray photoelectron spectroscopy in combination with density functional theory Anna Regoutz,1,* Alex M. Ganose,2,3,4 Lars Blumenthal,1,5 Christoph Schlueter,3,† Tien-Lin Lee,3 Gregor Kieslich,6 Anthony K. Cheetham,7 Gwilherm Kerherve,1 Ying-Sheng Huang,8,‡ Ruei-San Chen,9 Giovanni Vinai,10 Tommaso Pincelli,10 Giancarlo Panaccione,10 Kelvin H. L. Zhang,11 Russell G. Egdell,12 Johannes Lischner,1,5 David O. Scanlon,2,3,4 and David J. Payne1,§ 1Department of Materials, Imperial College London, South Kensington, London SW7 2AZ, United Kingdom 2Department of Chemistry, University College London, 20 Gordon Street, London WC1H 0AJ, United Kingdom 3Diamond Light Source Ltd., Diamond House, Harwell Science and Innovation Campus, Didcot OX11 0DE, United Kingdom 4Thomas Young Centre, University College London, Gower Street, London WC1E 6BT, United Kingdom 5Thomas Young Centre for Theory and Simulation of Materials, United Kingdom 6Department of Chemistry, Technical University of Munich, Lichtenbergstraße 4, Garching, Germany 7Functional Inorganic and Hybrid Materials Group, Department of Materials Science & Metallurgy, University of Cambridge, 27 Charles Babbage Road, Cambridge CB3 0FS, United Kingdom 8Department of Electric Engineering, National Taiwan University of Science and Technology, Taipei 6, Taiwan 9Graduate Institute of Applied Science and Technology, National Taiwan University of Science and Technology, Taipei 106, Taiwan 10Laboratorio -
Increase in Osmiophilia of Axonal Membranes of Crayfish As a Result of Electrical Stimulation, Asphyxia, Or Treatment with Reducing Agents
INCREASE IN OSMIOPHILIA OF AXONAL MEMBRANES OF CRAYFISH AS A RESULT OF ELECTRICAL STIMULATION, ASPHYXIA, OR TREATMENT WITH REDUCING AGENTS CAMILLO PERACCHIA and J . DAVID ROBERTSON From the Department of Anatomy, Duke University Medical Center, Durham, North Carolina 27706. Dr. Peracchia's present address is the Department of Physiology, University of Rochester Medical Center, Rochester, New York 14642 ABSTRACT Certain axonal membranes of crayfish abdominal nerve cord display ultrastructural changes if the axons are fixed, during electrical stimulation, by aldehydes followed by osmium . Such changes are characterized by an increase in electron opacity and thickness of the unit membranes' dense strata in the axon surface, endoplasmic reticulum, and outer mitochon- drial membranes . The electron opacity completely disappears if the sections are treated with hydrogen peroxide solutions . This suggests that the changes represent an increase in the membranes' reactivity for osmium . An unmasking of SH groups could explain such increased osmiophilia, since SH groups are very reactive with osmium, while disulfide bonds are considerably less reactive . This hypothesis was tested by treating control, glutaraldehyde- fixed nerve cords with disulfide reducing agents . In these preparations an increase in electron opacity and thickness was observed to be localized in the same axonal membranes which reacted as a result of electrical stimulation . The phenomenon did not appear if the SH groups were blocked by maleimide or N-ethylmaleimide before treatment with osmium . These findings seem to suggest that certain axonal membranes of crayfish contain proteins rich in sulfur whose SH groups are unmasked as a result of electrical stimulation. In pre- liminary experiments an increase in osmiophilia localized in the same membranes with the same characteristics and distribution was observed also in axons from nerve cords asphyxi- ated either in vitro or in the living animal . -
A Mehtod for the Seperation and Gravimetric Determination of Osmium
. 1 RP286 A METHOD FOR THE SEPARATION AND GRAVIMETRIC DETERMINATION OF OSMIUM By Raleigh Gilchrist ABSTRACT A procedure for the separation and gravimetric determination of osmium is described. This procedure involves the separation of osmium from other metais by distillation as the volatile tetroxide and its recovery from solution by hydro- lytic precipitation. A very suitable reagent for the quantitative absorption of the distilled tetroxide was found to be 6 normal hydrochloric acid saturated with sulphur dioxide. The recovery of osmium was accomplished by precipitating the hydrated dioxide from a boiling solution at acidities ranging from pH 1.5 to 6.3, after sulphite compounds had been decomposed by repeated evaporation with hydrochloric acid. The hydrated dioxide was impregnated with ammonium chloride to prevent mechanical loss when ignited to metal under hydrogen. The thiourea test devised b}' Chugaev for the detection of small quantities of osmium was modified so that it could be applied to solutions containing nitric acid. The test was found to be sensitive to 1 part in 5,000,000 parts of solution, which is 50 times as sensitive as stated by Chugaev, CONTENTS Page I. Introduction 422 1. Method of Ruff and Bornemann 425 2. Method of Ogburn and Miller 426 II. Object of the investigation 427 III. Preparation of osmium compounds for use in the experiments 428 IV. Precipitation of hydrated osmium dioxide by hydrolysis 430 V. Effect of exposure of osmium sponge to the air 430 VI. Qualitative experiments to determine the completeness of pre- cipitation of hydrated osmium dioxide 43 VII. Detection of minute quantities of osmium by reaction with thiourea 43 VIII. -
German Legislation on Azo Dyes
German Legislation on Azo Dyes Environmental protection and product DyStar's products are continuously mo- safety are becoming increasingly impor- nitored to make sure they meet statutory tant criteria in the purchase of textiles, requirements throughout the world. due to the emotive nature of the debate and greater consumer concern. DyStar sets standards in environmental responsibility. DyStar has not had to This publication provides general infor- make any changes to its product range mationaboutazodyestohelpputthe to comply with the amendments to the issue on a more factual basis. Here you German Consumer Goods Ordinance. will find some background notes about What better evidence could there be that the German Consumer Goods Ordinance, together with a list of the amines and with DyStar products dyestuffs involved. Information is also you’re on the safe side. provided about the test methods used for textiles, as well as an overview of other By buying and using dyes and pigment national regulations relating to azo dyes. preparations from DyStar, you can be sure you comply with the German Consumer Goods Ordinance and other statutory regulations. None of our azo dyes generate banned amines following azo bond cleavage. So consumers can be confident that textiles dyed and printed correctly with DyStar products are safe. Contact us if you would like further information. Your local DyStar representative or our central ecology team will be happy to help you. CONTENTS ECOLOGY Toxicological background 2 List of „banned“ azo dyes 7 Azo dyes 3 Azo pigments 8 The German Consumer Goods Ordinance 4 Consumer goods 8 Listed amines 5 International legislation 9 Draft for 6th Amendment 5 Annex: Analytical detection Tables of „banned“ of „banned“ azo dyes 6 azo colourants 12 Azo dyestuffs Amendments to the German affected by the ban. -
Fingerprint Source Book Chapter 5 Alternative Finger Mark
Fingerprint Source Book – Chapter 5: Alternative finger mark development techniques Chapter 5: Alternative finger mark development techniques 5.1 Alternative blood enhancement techniques 1. History 1.1 The history of the development of blood dyes has been outlined in Chapter 3.1, Acid dyes, of this Fingerprint Source Book. 2. Theory 2.1 General theory 2.1.1 The theory associated with the action of protein stains (in particular the acid dyes), in enhancing traces of blood is described in Chapter 3.1, Acid dyes (acid black 1, acid violet 17, acid yellow 7). 2.1.2 There are other reagents that react with the amines present in blood to give coloured or fluorescent products, the most well known of these being ninhydrin and 1,8-diazafluoren-9-one (DFO). They both react similarly with amino acids to form products that contain two deoxygenated molecules of the starting product bridged by a nitrogen atom, which is donated from the amine [1,2]. O O N N - N - N O O N N The reaction products with ninhydrin (left) and 1,8-diazafluoren-9-one (right) and amines. 2.1.3 While the reaction mechanisms and products have similarities, the method of their visualisation is entirely different. Ninhydrin, under the right conditions, produces an intensely coloured product called ‘Ruhemann’s purple’ after the discoverer and DFO a pale pink, extremely fluorescent product. Ruhemann’s purple can be made to fluoresce by complexing it with metal salts but this additional process is still not as sensitive as DFO [3]. DFO requires heat for the reaction to proceed [4] while ninhydrin will react at room temperature provided moisture is available, although the process proceeds much faster at elevated temperatures and humidities.