8. Roman Chain-Mail
Total Page:16
File Type:pdf, Size:1020Kb
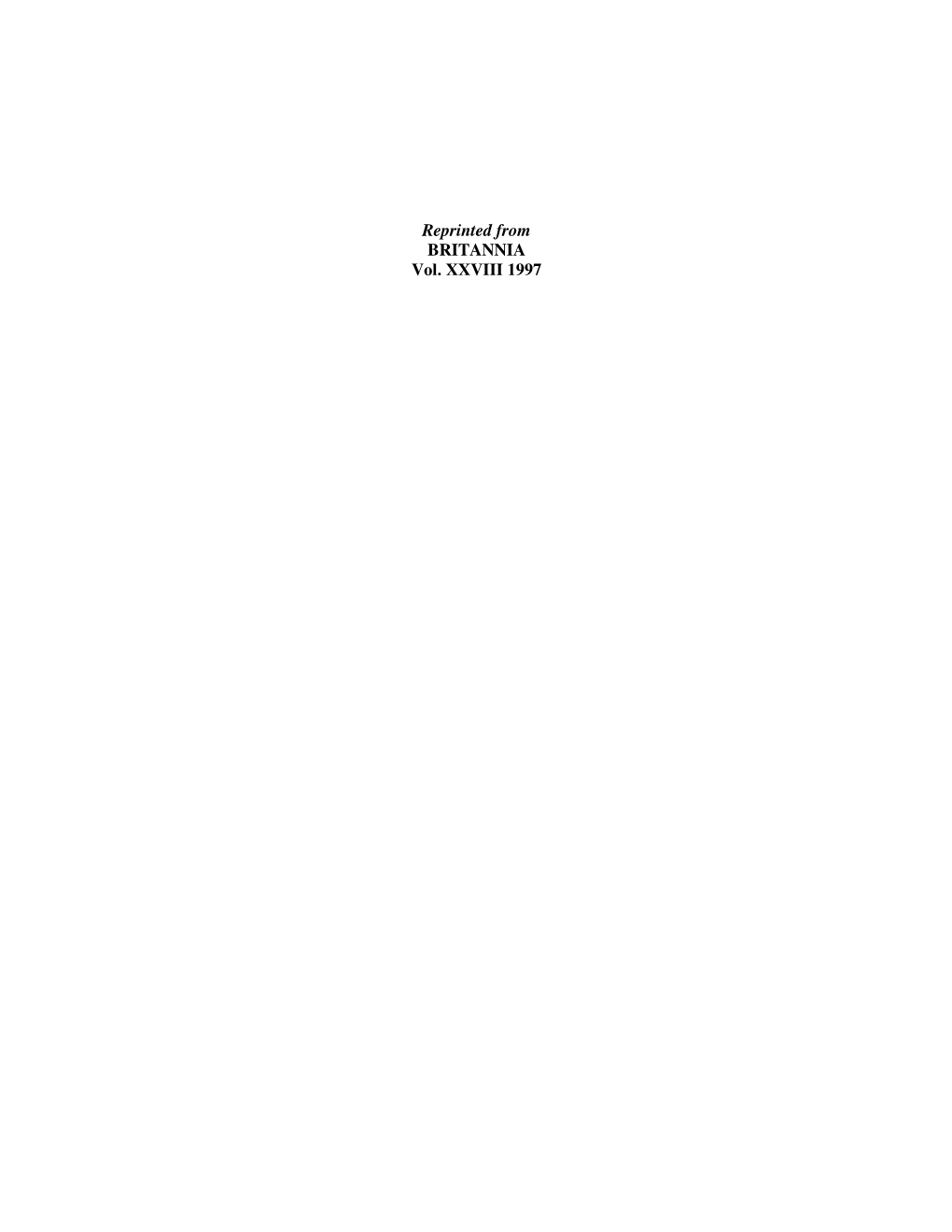
Load more
Recommended publications
-
The Jewelry Department
I)1:PARTMEM STORE MERCll'Vs'DlSE TWA-NUALS i-,:i!.iiililliliiil!i:i: Courtesy of International Studio Coml) in Gold and Horn ( Frcncli Design) DEPARTMENT STORE MERCHANDISE MANUALS THE JEWELRY DEPARTMENT BEULAH ELFRETH KENNARD, M.A. Editor of Series; Director of Department Store Courses, New York University; Chairman of Committee on Merchan- dise Courses for New York City Public Schools; Former Educational Director of the Department Store Education Association. ASSISTED BY E. LILLIAN HUTCHINSON, B. A. Secretary Department Store Education Association CONSULTING EDITOR LEE GALLOWAY, Ph.D. Associate Professor Commerce and Industry, New York University; Secretary of National Association of Corpora- tion Schools; Director Educational Courses, National Commercial Gas Association. NEW YORK THE RONALD PRESS COMPANY 1917 40fX>G Copyright, 1917, by The Ronald Press Company ^^ \"\ X Sljia ^tv\SB tfl Sfbtrat^b to Mrs. Henry Ollesheimer, Miss Virginia Potter, Miss Anne Mor- gan, and other organizers of the Department Store Education As- sociation, who desiring to give greater opportunity for advance- ment to commercial employees and believing that all business efficiency must rest upon a solid foundation of training and education gave years of enthusiastic service to the testing of this belief. EDITOR'S PREFACE This series of department store manuals has been pre- pared for the purpose of imparting definite and authen- tic information to that growing army of salespeople who are not satisfied to be mere counter servers — to those who realize that their vocation is one of dignity and opportunity, and that to give satisfactory service to the customer they must possess a thorough knowledge of the goods they sell, as well as a knowledge of how best to P^ f\ sell them. -
Hollow Comb Rivets Made from Stripdrawn Copper Wire and Two Possible Antler Draw Plates from 11Th–12Th C. Sigtuna, Sweden
Omslag 2019/2_Omslag 3/2004 (kopia) 2019-05-20 11:32 Sida 1 Innehåll F 57 Gardeła, L. et al. The spur goad from kort meddelande O R Skegrie in Scania, Sweden. Evidence of 115 Scheglov, A. Omarbetning av Olaus Petris N elite interaction between Viking Age krönika: Ett politiskt vittnesbörd – och V Ä Scandinavians and Western Slavs. heraldiskt? N N 75 Loftsgarden, K. The prime movers of iron E production in the Norwegian Viking and recensioner N 2 Middle Ages. 118 Larsson, B.T. & Broström, S-G. Nämforsens 0 1 9 88 Wärmländer, S.K.T.S. & Söderberg, A. Hällristningar – Sveriges största och äldsta / 2 Hollow comb rivets made from strip- hällristningsområde med 2600 figurer FORN drawn copper wire and two possible ant- (The rock of Nämforsen). Anmälan av ler draw plates from 11th–12th c. Sigtuna, V. Mantere. Sweden. 120 Ahlström, C. The Viking Age. A time of many faces. Anmälan av L. Gardeła. debatt 123 Ljung, C. Under runristad häll: Tidig- 100 Kjellström, R. Stalofrågan – en personlig kristna gravmonument i 1000-talets slutkommentar. Sverige. Anmälan av P. Carelli. VÄNNEN 107 Lovén, C. Var Beowulf gute? JOURNAL OF SWEDISH ANTIQUARIAN RESEARCH 2019/2 issn 0015-7813 Omslag 2019/2_Omslag 3/2004 (kopia) 2019-05-20 11:32 Sida 2 Utgiven av Till författaren Kungl. Vitterhets Historie och Antikvitets Akademien i samarbete med Historiska museet. fornvännen välkomnar manuskript i nordisk arkeologi och äldre tiders konstvetenskap med an grän sande Fornvännen finns på webben i sin helhet från första årgången och publiceras löpande där ämnen. Bidrag kan vara avfattade på de skandinaviska språken samt engelska, tyska och franska. -
Silverwork and Jewelry, H Wilson Edited by W R Lethaby, 1903
NYPL RESEARCH LIBRARIES 3 3433 07217841 V THE ARTISTIC CRAFTS SERIES OF TECHNICAL HANDBOOKS EDITED BY W. R. LETHABY SILVERWORK AND JEWELRY THE ARTISTIC CRAFTS SERIES OF TECHNICAL HANDBOOKS. Edited by W. R. Lethaby. TTHE series will appeal to handicraftsmen in the industrial -'- and mechanic arts. It will consist of authoritative state- ments by experts in every field for the exercise of ingenuity, taste, imagination—the whole sphere of the so-called "de- pendent arts." BOOKBINDING AND THE CARE OF BOOKS. A Handbook for Amateurs, Bookbinders, and Librarians. By Douglas Cpckerell. With 1 20 Illustrations and Diagrams by Noel Rooke, and 8 collotype reproductions of bindings. i2mo. net postage, 12 cents additional. ^1.25 ; SILVERWORK AND JEWELRY. a Text- Book for Students and Workers in Metal. By H. Wilson. With 160 Diagrams and 16 full-page Illustrations. i2mo. $1.40 net; postage, 12 cents additional. In Preparation : CABINET-MAKING AND DESIGNING. By C. Spooner. D. APPLETON AND COMPANY, NEW YORK. I THE NEW YORK PUBLIC LIBRAP'"' ASTOR, LENOX AND TILDEN FOUNDATIONS. Cambridge. The Foundress' Cup : Christ's College, SILVERWORK AND JEWELRY A TEXT-BOOK FOR STUDENTS AND WORKERS IN METAL BY H. WILSON. WITH DIAGRAMS BY THE AUTHOR AND OTHER ILLUSTRATIONS NEW YORK D. APPLETON AND COMPANY 1903 THE NEW YORK P!ir^''- LIBRARY 357689 ASTOR, LENOX AND T1LD€N FOUWPATION8. R 1503. L Copyright, 1903 By D. Appleton and Company c, .... -'y^ii fights reserved ' r c Published February, 1903 "An Art can only be learned in the workshop of those who are winning their bread by itJ*^ —Samuel Butler (* Erewhon "). -
The Late Roman Army Free
FREE THE LATE ROMAN ARMY PDF Gabriele Esposito | 150 pages | 07 Jul 2016 | Winged Hussar Publishing | 9780996365796 | English | United States Roman army of the late Republic - Wikipedia By Steven Wills. It offers significant lessons in how not to manage the army of a great power. Cutting the retirement benefits of a small professional force in favor of smaller taxes for the elite and greater benefits for the masses served only to weaken the desire of Roman citizens to serve. When the Roman citizenry would not join in the numbers required to protect the Empire, Roman elites turned to conscription, which produced only disgruntled recruits, and mass recruitment of barbarian tribes such as the Goths, Visigoths and The Late Roman Army. These tribesmen could be paid less and did not require expansive pensions as an incentive to serve. These three mistakes in the management of the late Roman Imperial Army should serve as a powerful warning to American elites seeking inexpensive solutions to the maintenance of American military power. While some military The Late Roman Army can always be reduced, a great power that seeks very low-cost solutions does so at its own peril. The Roman Army began providing pensions to retiring soldiers during the fall of the Roman Republic in the late first century B. These promises often included financial The Late Roman Army, exemption from taxes and grants of land from captured enemy territory. Augustus reduced the Roman Army to a voluntary, professional force of approximatelyactive duty soldiers and a similar The Late Roman Army of auxiliary troops. -
Jewelers' Equipment & Tools
PAGE 109 Jewelers’ Equipment & Tools Saw Blades Anchor brand jeweler’s saw blades. Sizes: #4, #3, #2, 1/0, #2/0, #3/0, #4/0, #5/0, #6/0 - from largest (#4) to finest (#6/0) $3.75/144 10% discount assortable/12 gross Deluxe Saw Frame Throat and front mounted screw to adjust blade ten- Hardwood sion precisely. 3” throat. Sawblade $10.75 each Holder Rotates for easy selection. $13.50 each Adjustable Sawframe With 2.75” throat. $ 5.95 each WIRE DRAWING PLATES 8.5” specially hardened steel for shaping and reduc- ing jewelry wire. Round Hole Draw Plate, 82 holes (pictured above) $10.80 each, $116.64/12 Chromed Steel Sawframes Half-Round Hole Draw Plate, 30 holes Top Quality; great value! $12.50 each, $135.00/12 Hexagon Hole Draw Plate, 30 holes Adjustable sawframe with a 3” throat $12.50 each, $135.00/12 $ 8.50 each Marquise Hole Draw Plate, 30 holes $12.50 each, $135.00/12 Pear-shape Hole Draw Plate, 30 holes $12.50 each, $135.00/12 6” Adjustable Rectangle Hole Draw Plate, 30 holes Saw Frame $12.50 each, $135.00/12 $11.95 each Square Hole Draw Plate, 30 holes $ 12.50 each, $135.00/12 Triangle Hole Draw Plate, 30 holes $12.50 each, $135.00/12 PAGE 110 Tungsten Soldering Pick Draw Tongs Perfect for platinum’s higher temperatures. Non- Heavy duty, hand-forged. stick. Will not discolor or contaminate gold, silver 8” Draw Tongs ............$14.85 each or platinum. 10” Draw Tongs ..........$18.95 each $ 5.50 each Best Quality Titanium Solder Pick With anodized, non-roll hexagonal handles for non- stick use with gold & silver. -
The Military Reforms of Gaius Marius in Their Social, Economic, and Political Context by Michael C. Gambino August, 2015 Directo
The Military Reforms of Gaius Marius in their Social, Economic, and Political Context By Michael C. Gambino August, 2015 Director of Thesis: Dr. Frank Romer Major Department: History Abstract The goal of this thesis is, as the title affirms, to understand the military reforms of Gaius Marius in their broader societal context. In this thesis, after a brief introduction (Chap. I), Chap. II analyzes the Roman manipular army, its formation, policies, and armament. Chapter III examines Roman society, politics, and economics during the second century B.C.E., with emphasis on the concentration of power and wealth, the legislative programs of Ti. And C. Gracchus, and the Italian allies’ growing demand for citizenship. Chap. IV discusses Roman military expansion from the Second Punic War down to 100 B.C.E., focusing on Roman military and foreign policy blunders, missteps, and mistakes in Celtiberian Spain, along with Rome’s servile wars and the problem of the Cimbri and Teutones. Chap. V then contextualizes the life of Gaius Marius and his sense of military strategy, while Chap VI assesses Marius’s military reforms in his lifetime and their immediate aftermath in the time of Sulla. There are four appendices on the ancient literary sources (App. I), Marian consequences in the Late Republic (App. II), the significance of the legionary eagle standard as shown during the early principate (App. III), and a listing of the consular Caecilii Metelli in the second and early first centuries B.C.E. (App. IV). The Marian military reforms changed the army from a semi-professional citizen militia into a more professionalized army made up of extensively trained recruits who served for longer consecutive terms and were personally bound to their commanders. -
Cavalry Equipment of the Roman Army in the First Century A.D
Originally published in Coulston, J.C. (ed.) 1988: Military Equipment and the Identity of Roman Soldiers. Proceedings of the Fourth Roman Military Equipment Conference, BAR International Series 394, Oxford CAVALRY EQUIPMENT OF THE ROMAN ARMY IN THE FIRST CENTURY A.D. M.C. Bishop INTRODUCTION The main aim of this paper is to identify and describe the elements that went together to make up Roman military horse (or riding) harness in the first century A.D.1 Closely linked with this, however, will be a consideration of just how much the archaeological evidence can tell us about the military use of mounts.2 It is to be hoped that the present work will at least serve to generate new interest in cavalry equipment and provoke discussion about the functions of its various components. There are two main source areas for the study of Roman military horse equipment: monuments depicting its use and artefacts recovered from the archaeological record. Pictorial evidence, most notably that represented by sculpture, can be used to show how the various elements of horse harness functioned as a whole. The value of such depictions is hotly debated, but it is generally true that funerary monuments tend to give a more accurate picture than official sculpture, although both categories vary widely in quality.3 Two types of tombstone, the 'Reiter' and the 'Totenmahl' are characteristic of the first century A.D. (although not exclusively so):4 these show, in the first instance, the deceased cavalryman riding his mount in combat, often with a cowering barbarian being trampled beneath the horse;5 the other type depicts the dead man enjoying a funerary banquet in the afterlife in an upper scene, whilst his horse is paraded in all its equipment in a lower.6 Totenmahl depictions usually show the horse being controlled from behind by means of long-reins and with its saddle covered by an overblanket, whilst the trooper's calo carries spare spears (javelins?). -
Create Your Own Armour [PDF]
Romans at Ham Hill Ham Hill is a 390 acre Country Park managed by South Somerset District Council that encompasses the largest Iron Age hill fort in Europe including a 19 roomed Roman villa and medieval settlements. Lorica squamata (scale armour) Many troops wore torso armour and there were three main types. Lorica squamata (and has been found at Ham Hill), Lorica hamata, which is made from small iron rings and Lorica segmentata, which is what you can see on the left. Lorica segmentata was worn by the Roman army from around 9BC until 2AD. An undergarment was usually worn to protect the wearer from bruising and shock and this was called a subarmalis. Roman helmet There are many designs of Roman helmet (Galea) and this one is loosely based on a design of the Imperial Gallic, a helmet that was in service to the Roman army from the late 1st century BC until the early 2nd century AD. Roman Gladius First used by the Spannish, the gladius was primarily used as a stabbing weapon. It has a v-shaped tip, which was great for finding the gaps between ribs or cartilage! Both sides were also kept razor-sharp and it was a deadly slashing weapon. Romans used the gladius in formation and always carried it in their right hand to compliment the carrying of their large shields (Scutum) in their left. It is still considered to be one of the important swords of history. Find more activities at www.southsomerset.gov.uk/childrensactivities Create your own Armour Armour keeps you protected in battles, a little bit like how face masks are helping protect our front line workers such as doctors and nurses while they confront Coronavirus. -
Armour Lorica Segmentata the Legionaries Were Equipped with A
Armour Lorica segmentata The legionaries were equipped with a version of the Newstead type lorica segmentata based on a plan drawn by Michael Bishop in 2001. This version already had the huge lobate hinges on the shoulder plates, but instead of a series of slots it still relied on copper-alloy tie-loops and leather laces for tying together the girth hoops. The Newstead type was probably introduced in the Antonine period (mid- to second half of the 2nd century). According to finds from Carlisle (GB) and Eining (G), versions of this type of armour were in use at least until the middle of the third century. No finds are known from Castra Regina/Regensburg, but given the short distance to the fort at Eining (about two days of marching), the legionaries from III ITALICA were certainly equipped with it. The Newsteads turned out to be very reliable. One of them suffered from a ripped internal leather strap due to the weight of the shield, but this specific cuirass had been a prototype with rather weak leather straps. (the damaged ‘prototype’) Two other cuirasses suffered from a similar accident (a rivet was pulled out of a leather strap), but this happened only in the final week and was caused by the same unorthodox way of carrying the shield with a leather strap running over the left shoulder. (the ‘prototype’ after field-repair) Due to a misunderstanding, the cuirass for the centurion was not completed in time. Luckily, he still had a Corbridge cuirass in reserve. The Corbridge was already outdated around 200 AD, but a few examples may still have seen service. -
Download Information Pack
THE ERMINE STREET GUARD INFORMATION PACK CONTACT DETAILS E-Mail - [email protected] Website - www.erminestreetguard.co.uk Telephone - 01452 862235 About The Ermine Street Guard Since its formation in 1972, the Guard has become the leading society studying the Roman Army and its equipment. Authenticity and Research Each piece of kit is made as authentically as is practicable based on recent research. The majority of the equipment is made by Guard Education members to high standards of workmanship Public displays are given at major Roman sites throughout Great Britain and Eu- and accuracy and is continually being added rope. The displays include aspects of the Roman soldier’s training, the shooting to and improved as new information and finds of artillery pieces and a static army camp display. At selected venues the Guard become available. The Guard works closely is also joined by fully equipped Roman cavalrymen. with leading academics in the field to ensure the kit is correct based on current research. Please contact the Guard for further details of venues or visit the website. Roman Officers Centurio The Centurio was the Officer in charge of a Century of 80 men. A Century never consisted of 100 men, and in Republican times only consisted of 60 men. The Centurio was normally a career soldier who had worked his way up through the ranks and was tough and experienced. In battle he would lead from the front, which meant they had a high mortality rate. The equipment reflected his high status and was designed to make him easy to pick out in battle. -
Basic Metal Toolkit
Intro to Metalsmithing Basic Metal Toolkit Jeweler’s Saw $20.00 Saw Blades 4.75 Vernier Caliper 10.50 Steel Metric Ruler 7.95 Hardwood Ring Mandrel 16.00 Scribe 8.95 Plier & Cutter Kit 29.00 Needle File Kit 14.95 Dividers 11.00 Bur Life 5.50 A Pin Vise 9.95 Bench Pin with Anvil 16.95 Twist Drills 6.45 Center Punch 8.95 B Hammer Kit 59.00 C Sand Paper Assortment 17.60 D Pocket Wire Gauge 14.95 Steel Square 4.55 Optivisor 6.45 Metalsmith Essentials - Tim McCreight 15.00 Estimated Total $288.45 ! A. Can substitute beeswax for Bur Life! B. Can make your own from an old nail.! C. You can pick up hammers from home improvement stores and alter them.! !D. You can buy sandpaper at home improvement stores for less and in bulk.! ! "1 of "7 Intro to Metalsmithing Measurement Resources Conversion Website www.convert-me.com Will convert units of distance and length instantly. Metric Conversions www.metric-conversions.org Excellent free resource to convert from Imperial to Metric ! ! Formulas! ! "2 of "7 Intro to Metalsmithing ! Terminology (Small List)! ! Alloy Mixture of metals; sterling silver is an allow of fine silver and copper. Annealing The process of heating and then cooling metal to make it softer and thus easier to work with. Base Metal Nonprecious metal, such as aluminum, copper, iron and nickel. Bezel The rim of metal that is used to secure a stone in a rub-over setting. Blank A flat shape cut from sheet metal. -
A COMPANION to the ROMAN ARMY Edited By
ACTA01 8/12/06 11:10 AM Page iii A COMPANION TO THE ROMAN ARMY Edited by Paul Erdkamp ACTA01 8/12/06 11:10 AM Page i A COMPANION TO THE ROMAN ARMY ACTA01 8/12/06 11:10 AM Page ii BLACKWELL COMPANIONS TO THE ANCIENT WORLD This series provides sophisticated and authoritative overviews of periods of ancient history, genres of classical lit- erature, and the most important themes in ancient culture. Each volume comprises between twenty-five and forty concise essays written by individual scholars within their area of specialization. The essays are written in a clear, provocative, and lively manner, designed for an international audience of scholars, students, and general readers. Ancient History Published A Companion to the Roman Army A Companion to the Classical Greek World Edited by Paul Erdkamp Edited by Konrad H. Kinzl A Companion to the Roman Republic A Companion to the Ancient Near East Edited by Nathan Rosenstein and Edited by Daniel C. Snell Robert Morstein-Marx A Companion to the Hellenistic World A Companion to the Roman Empire Edited by Andrew Erskine Edited by David S. Potter In preparation A Companion to Ancient History A Companion to Late Antiquity Edited by Andrew Erskine Edited by Philip Rousseau A Companion to Archaic Greece A Companion to Byzantium Edited by Kurt A. Raaflaub and Hans van Wees Edited by Elizabeth James A Companion to Julius Caesar Edited by Miriam Griffin Literature and Culture Published A Companion to Catullus A Companion to Greek Rhetoric Edited by Marilyn B. Skinner Edited by Ian Worthington A Companion to Greek Religion A Companion to Ancient Epic Edited by Daniel Ogden Edited by John Miles Foley A Companion to Classical Tradition A Companion to Greek Tragedy Edited by Craig W.