Assessing the Quality of Iron Ores for Bloomery Smelting: Laboratory Experiments
Total Page:16
File Type:pdf, Size:1020Kb
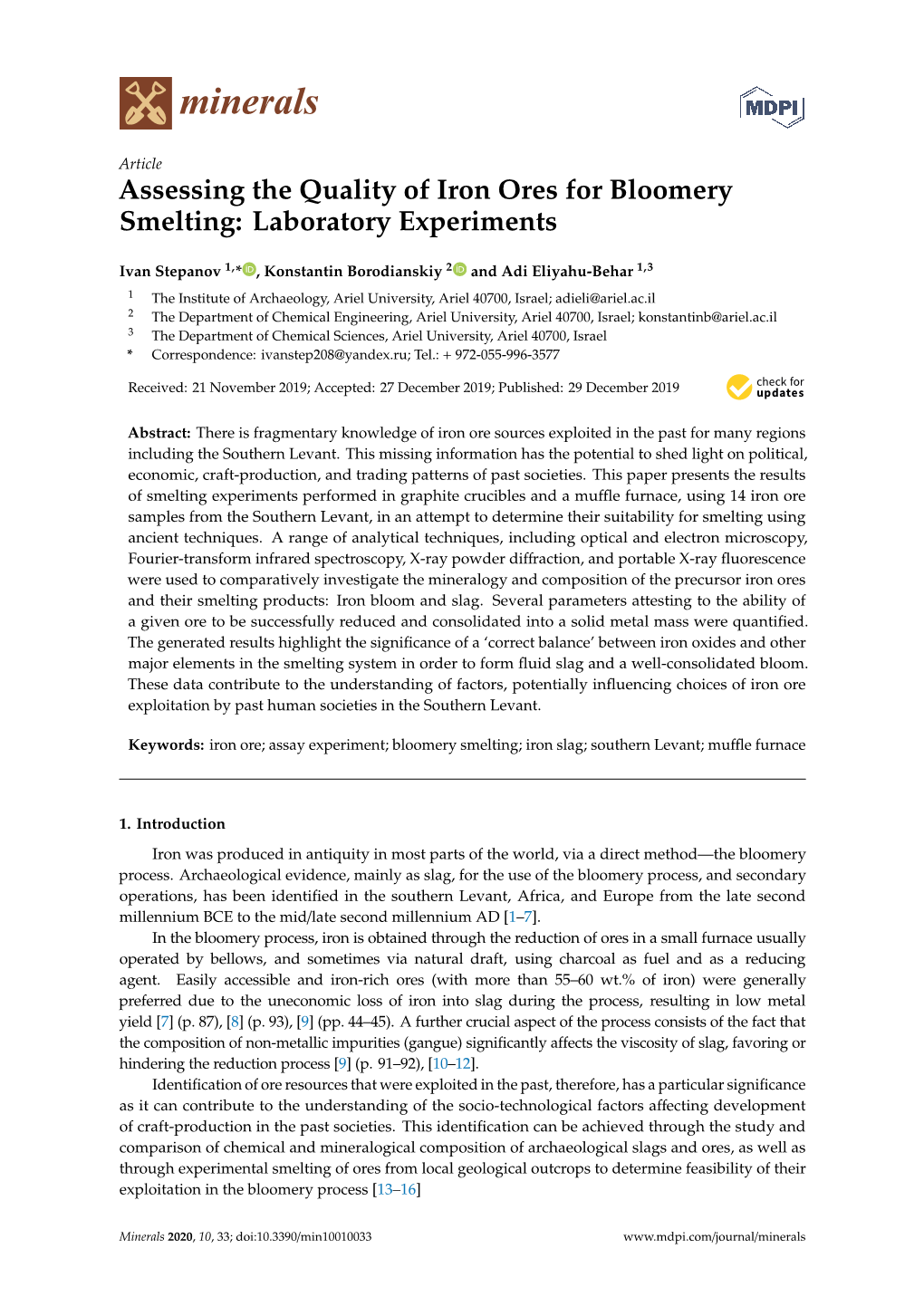
Load more
Recommended publications
-
Influence of Temperature and Water Content on Microstructure Evolution
Contributions to Mineralogy and Petrology (2018) 173:5 https://doi.org/10.1007/s00410-017-1429-y ORIGINAL PAPER Synthesis of monticellite–forsterite and merwinite–forsterite symplectites in the CaO–MgO–SiO2 model system: influence of temperature and water content on microstructure evolution P. Remmert1 · W. Heinrich1 · B. Wunder1 · L. Morales1 · R. Wirth1 · D. Rhede1 · R. Abart2 Received: 17 September 2017 / Accepted: 28 November 2017 / Published online: 21 December 2017 © The Author(s) 2018. This article is an open access publication Abstract Homogeneous single crystals of synthetic monticellite with the composition Ca0.88Mg1.12SiO4 (Mtc I) were annealed in a ◦ piston-cylinder apparatus at temperatures between 1000 and 1200 C , pressures of 1.0–1.4 GPa, for run durations from 10 min to 24 h and applying bulk water contents ranging from 0.0 to 0.5 wt% of the total charge. At these conditions, Mtc I breaks down to a fine-grained, symplectic intergrowth. Thereby, two types of symplectites are produced: a first symplectite type (Sy I) is represented by an aggregate of rod-shaped forsterite immersed in a matrix of monticellite with end-member composition (Mtc II), and a second symplectite type (Sy II) takes the form of a lamellar merwinite–forsterite intergrowth. Both symplectites may form simultaneously, where the formation of Sy I is favoured by the presence of water. Sy I is meta- stable with respect to Sy II and is successively replaced by the latter. For both symplectite types, the characteristic spacing of the symplectite phases is independent of run duration and is only weeakly influenced by the water content, but it is strongly ◦ ◦ ◦ temperature dependent. -
A History of Tailings1
A HISTORY OF MINERAL CONCENTRATION: A HISTORY OF TAILINGS1 by Timothy c. Richmond2 Abstract: The extraction of mineral values from the earth for beneficial use has been a human activity- since long before recorded history. Methodologies were little changed until the late 19th century. The nearly simultaneous developments of a method to produce steel of a uniform carbon content and the means to generate electrical power gave man the ability to process huge volumes of ores of ever decreasing purity. The tailings or waste products of mineral processing were traditionally discharged into adjacent streams, lakes, the sea or in piles on dry land. Their confinement apparently began in the early 20th century as a means for possible future mineral recovery, for the recycling of water in arid regions and/or in response to growing concerns for water pollution control. Additional Key Words: Mineral Beneficiation " ... for since Nature usually creates metals in an impure state, mixed with earth, stones, and solidified juices, it is necessary to separate most of these impurities from the ores as far as can be, and therefore I will now describe the methods by which the ores are sorted, broken with hammers, burnt, crushed with stamps, ground into powder, sifted, washed ..•. " Agricola, 1550 Introduction identifying mining wastes. It is frequently used mistakenly The term "tailings" is to identify all mineral wastes often misapplied when including the piles of waste rock located at the mouth of 1Presented at the 1.991. National mine shafts and adi ts, over- American. Society for Surface burden materials removed in Mining and Reclamation Meeting surface mining, wastes from in Durango, co, May 1.4-17, 1.991 concentrating activities and sometimes the wastes from 2Timothy c. -
Laboratory Furnaces and Dryers
CATALOG Laboratory furnaces and dryers Art of heating TABLE OF CONTENTS Our business partners 4 LAC – who we are 5 How to select a furnace 6 Choosing a furnace according to batch processing technology 8 Furnaces for temperatures 120 – 850 °C S – Dryers up to 200 and 300 °C 10 PP – Tempering furnace up to 450, 650 or 850 °C 12 Furnaces for temperatures 650 – 1340 °C PKR - Gas-tight chamber furnace up to 950 and 1100 °C 14 PKRC - Gas-tight chamber furnace with air circulation up to 950 and 1100 °C 16 LZ – Ashing furnace up to 1100 °C 18 LE – Economy laboratory furnace up to 1100 °C 20 L – Universal laboratory furnace up to 1200 °C 22 LMH – Horizontal muffle furnace up to 1200 °C 24 LMV – Vertical muffle furnace up to 1200 °C 26 LG - Gravimetric furnace up to 1200 °C 28 PKE - Hardening furnace up to 1280 °C 30 LT – Tube furnace up to 1300 °C 32 LSP – Five-zone gradient furnace up to 1300 °C 34 LH - Laboratory furnace up to 1340 °C 36 Furnaces for temperatures 1200 – 1800 °C LHS – Laboratory furnace with silit rods for up to 1400 and 1500 °C 38 VP – High-temperature furnace for up to 1600, 1700 and 1800 °C 40 Custom-made furnaces for special applications CHTZ - Small workplace for chemical heat treatment of non-ferrous materials up to 950 °C 42 SKM - Hardening work-station laboratory table up to 1340 °C 43 LH 30 atyp - Hardening furnace up to 1200 °C 44 L 09 atyp - Bottom-loading laboratory chamber furnace up to 1200 °C 45 PKE 25 atyp - Hardening chamber furnace with protective gas supply container up to 1200 °C 46 LT 50 atyp - Tube furnace with programmable servo-drive up to 1300 °C 47 LT 150 and LT 300 atyp - Activating tube furnace with glass retort up to 450 °C 47 LT 90 atyp - Tube furnace for mechanical testing of materials up to 1100 °C 47 Measurement and regulation 48 What (not) to choose – description of accessories 50 OUR PARTNERS 100 NEJLEPŠÍCH ČESKÝCH FIREM ROKU 2015 4 LAC – WHO WE ARE LAC – Who We Are We have over 240 employees and have produced more than 13,000 furnaces and dryers. -
Smelting Iron from Laterite: Technical Possibility Or Ethnographic Aberration?
Smelting Iron from Laterite: Technical Possibility or Ethnographic Aberration? T. O. PRYCE AND S. NATAPINTU introduction Laterites deposits (orlateriticsoilsastheyarealsocalled)arefrequently reported in Southeast Asia, and are ethnographically attested to have been used for the smelting of iron in the region (Abendanon 1917 in Bronson 1992:73; Bronson and Charoenwongsa 1986), as well as in Africa (Gordon and Killick 1993; Miller and Van Der Merwe 1994). The present authors do not dispute this evidence; we merely wish to counsel cautioninitsextrapolation.Modifyingour understanding of a population’s potential to locally produce their own iron has immediate ramifications for how we reconstruct ancient metal distribution net- works, and the social exchanges that have facilitated them since iron’s generally agreed appearance in Southeast Asian archaeological contexts during the mid-first millennium b.c. (e.g., Bellwood 2007:268; Higham 1989:190). We present this paper as a wholly constructive critique of what appears to be a prevailingperspectiveonpre-modernSoutheastAsianironmetallurgy.Wehave tried to avoid technical language and jargon wherever possible, as our aim is to motivate scholars working within the regiontogivefurtherconsiderationtoiron as a metal, as a technology, and as a socially significant medium (e.g., Appadurai 1998; Binsbergen 2005; Gosden and Marshall 1999). When writing a critique it is of course necessary to cite researchers with whom one disagrees, and we have done this with full acknowledgment that in modern archaeology no one person can encompass the entire knowledge spectrum of the discipline.1 The archaeome- tallurgy of iron is probably on the periphery of most of our colleagues’ interests, but sometimes, within the technical, lies the pivotal, and in sharing some of our insights we hope to illuminate issues of benefit to all researchers in Metal Age Southeast Asia. -
Chapter 11 Applications of Ore Microscopy in Mineral Technology
CHAPTER 11 APPLICATIONS OF ORE MICROSCOPY IN MINERAL TECHNOLOGY 11.1 INTRODUCTION The extraction of specific valuable minerals from their naturally occurring ores is variously termed "ore dressing," "mineral dressing," and "mineral beneficiation." For most metalliferous ores produced by mining operations, this extraction process is an important intermediatestep in the transformation of natural ore to pure metal. Although a few mined ores contain sufficient metal concentrations to require no beneficiation (e.g., some iron ores), most contain relatively small amounts of the valuable metal, from perhaps a few percent in the case ofbase metals to a few parts per million in the case ofpre cious metals. As Chapters 7, 9, and 10ofthis book have amply illustrated, the minerals containing valuable metals are commonly intergrown with eco nomically unimportant (gangue) minerals on a microscopic scale. It is important to note that the grain size of the ore and associated gangue minerals can also have a dramatic, and sometimes even limiting, effect on ore beneficiation. Figure 11.1 illustrates two rich base-metal ores, only one of which (11.1b) has been profitably extracted and processed. The McArthur River Deposit (Figure I 1.1 a) is large (>200 million tons) and rich (>9% Zn), but it contains much ore that is so fine grained that conventional processing cannot effectively separate the ore and gangue minerals. Consequently, the deposit remains unmined until some other technology is available that would make processing profitable. In contrast, the Ruttan Mine sample (Fig. 11.1 b), which has undergone metamorphism, is relativelycoarsegrained and is easily and economically separated into high-quality concentrates. -
HISTORY of METALLURGY 2Nd Edition
A HISTORY OF METALLURGY 2nd Edition A HISTORY OF METALLURGY Second Edition R. F. Tylecote MANEY FOR THE INSTITUTE OF MATERIALS Book B0789 First published in paperback in 2002 by Maney Publishing 1 Carlton House Terrace London SW1Y 5DB for the Institute of Materials First published in 1976 Reprinted in 1979 2nd edn published 1992 © The Institute of Materials 1992 All rights reserved ISBN 1-902653-79-3 Printed and bound in the UK by Antony Rowe Ltd v Contents Preface to the Second Edition vii Foreword viii Acknowledgements ix Introduction xi 1 Metals and ores in the Neolithic period 1 2 The technique and development of early copper smelting 7 3 The Early Bronze Age 18 4 The Full Bronze Age 35 5 The Early Iron Age 47 6 The Roman Iron Age 62 7 The Migration and medieval period 75 8 Post-medieval metallurgy 95 9 The Industrial Revolution; AD 1720-1850 122 10 More recent times; AD 1850-1950 164 11 The contributions of the scientists 177 Appendixes: 188 Technical Glossary 188 Note on units of weight, stress, and hardness 190 Table of elements 190 Approximate date of start of metal ages 191 Chinese chronology 191 Journals consulted and abbreviations 191 Principal works consulted 193 Maps 1-6 194-198 Subject and name index 199 vii Preface to the Second Edition The first edition was published in 1976 and an enormous increase in the general interest in the subject of archeometallurgy has taken place since then. Much of this relates to the early phases and has been discussed in Proceedings of International Conferences. -
Stitial Oxide Ions Synthesized by Direct Crystallization
La2Ga3O7.5: a metastable ternary melilite with a super-excess of inter- stitial oxide ions synthesized by direct crystallization of the melt Jintai Fan, Vincent Sarou-Kanian, Xiaoyan Yang, Maria Diaz-Lopez, Franck Fayon, Xiaojun Kuang, Michael Pitcher, Mathieu Allix To cite this version: Jintai Fan, Vincent Sarou-Kanian, Xiaoyan Yang, Maria Diaz-Lopez, Franck Fayon, et al.. La2Ga3O7.5: a metastable ternary melilite with a super-excess of inter- stitial oxide ions synthe- sized by direct crystallization of the melt. Chemistry of Materials, American Chemical Society, 2020, 32 (20), pp.9016-9025. 10.1021/acs.chemmater.0c03441. hal-02959774 HAL Id: hal-02959774 https://hal.archives-ouvertes.fr/hal-02959774 Submitted on 7 Oct 2020 HAL is a multi-disciplinary open access L’archive ouverte pluridisciplinaire HAL, est archive for the deposit and dissemination of sci- destinée au dépôt et à la diffusion de documents entific research documents, whether they are pub- scientifiques de niveau recherche, publiés ou non, lished or not. The documents may come from émanant des établissements d’enseignement et de teaching and research institutions in France or recherche français ou étrangers, des laboratoires abroad, or from public or private research centers. publics ou privés. La2Ga3O7.5: a metastable ternary melilite with a super-excess of inter- stitial oxide ions synthesized by direct crystallization of the melt Jintai Fan,1,2 Vincent Sarou-Kanian,1 Xiaoyan Yang,3 Maria Diaz-Lopez,4,5 Franck Fayon,1 Xiaojun Kuang,3,6 Michael J. Pitcher1* and Mathieu Allix1* 1 CNRS, CEMHTI UPR3079, 45071 Orléans, France 2 Shanghai Institute of Optics and Fine Mechanics, Chinese Academy of Science, Shanghai, 201800, P. -
Optical Properties of Common Rock-Forming Minerals
AppendixA __________ Optical Properties of Common Rock-Forming Minerals 325 Optical Properties of Common Rock-Forming Minerals J. B. Lyons, S. A. Morse, and R. E. Stoiber Distinguishing Characteristics Chemical XI. System and Indices Birefringence "Characteristically parallel, but Mineral Composition Best Cleavage Sign,2V and Relief and Color see Fig. 13-3. A. High Positive Relief Zircon ZrSiO. Tet. (+) 111=1.940 High biref. Small euhedral grains show (.055) parallel" extinction; may cause pleochroic haloes if enclosed in other minerals Sphene CaTiSiOs Mon. (110) (+) 30-50 13=1.895 High biref. Wedge-shaped grains; may (Titanite) to 1.935 (0.108-.135) show (110) cleavage or (100) Often or (221) parting; ZI\c=51 0; brownish in very high relief; r>v extreme. color CtJI\) 0) Gamet AsB2(SiO.la where Iso. High Grandite often Very pale pink commonest A = R2+ and B = RS + 1.7-1.9 weakly color; inclusions common. birefracting. Indices vary widely with composition. Crystals often euhedraL Uvarovite green, very rare. Staurolite H2FeAI.Si2O'2 Orth. (010) (+) 2V = 87 13=1.750 Low biref. Pleochroic colorless to golden (approximately) (.012) yellow; one good cleavage; twins cruciform or oblique; metamorphic. Olivine Series Mg2SiO. Orth. (+) 2V=85 13=1.651 High biref. Colorless (Fo) to yellow or pale to to (.035) brown (Fa); high relief. Fe2SiO. Orth. (-) 2V=47 13=1.865 High biref. Shagreen (mottled) surface; (.051) often cracked and altered to %II - serpentine. Poor (010) and (100) cleavages. Extinction par- ~ ~ alleL" l~4~ Tourmaline Na(Mg,Fe,Mn,Li,Alk Hex. (-) 111=1.636 Mod. biref. -
ITP Mining: Energy and Environmental Profile of the U.S. Mining Industry: Chapter 4: Iron
Energy and Environmental Profile of the U.S. Mining Industry 4 Iron The chemical element iron is the fourth most common element in the Earth's crust and the second most abundant metal. About five percent of the Earth's crust is composed of iron. The metal is chemically active and is found in nature combined with other elements in rocks and soils. In its natural state, iron is chemically bonded with oxygen, water, carbon dioxide, or sulfur in a variety of minerals. Forms of Iron Minerals, Ores, and Rocks Iron occurs mainly in iron-oxide ores. Some ores are a mixture of minerals rich in iron. Other iron ores are less rich and have a large number of impurities. The most important iron ore- forming minerals are: • Magnetite - Magnetite (Fe3O4) forms magnetic black iron ore. There are large deposits of magnetite in Russia and Sweden. • Hematite - Hematite (Fe2O3) is a red iron ore. Hematite occurs in almost all forms, from solid rock to loose earth. It is the most plentiful iron ore and occurs in large quantities throughout the world. • Goethite - Goethite (Fe2O3.H2O), a brown ore, contains iron. • Limonite - Limonite (Fe2O3.H2O) is a yellow-brown iron ore. Limonite is a collective term for impure goethite and a mixture of hydrated iron oxides. Iron 4-1 Energy and Environmental Profile of the U.S. Mining Industry Taconite contains low-grade iron in fine specks and bands. It is an extremely hard and flinty - containing about 25 - 30 percent iron. The iron in taconite occurs principally as magnetite and hematite and finely dispersed with silica in sedimentary deposits. -
Carbothermic Reduction of Ore-Coal Composite Pellets in a Tall Pellets Bed
minerals Article Carbothermic Reduction of Ore-Coal Composite Pellets in a Tall Pellets Bed Xin Jiang *, Guangen Ding, He Guo, Qiangjian Gao * and Fengman Shen School of Metallurgy, Northeastern University, Shenyang 110819, China; [email protected] (G.D.); [email protected] (H.G.); [email protected] (F.S.) * Correspondence: [email protected] (X.J.); [email protected] (Q.G.); Tel.: +86-24-83681506 (X.J.); +86-24-83691266 (Q.G.) Received: 19 October 2018; Accepted: 21 November 2018; Published: 27 November 2018 Abstract: Recently, increasing attention has been paid to alternative ironmaking processes due to the desire for sustainable development. Aiming to develop a new direct reduction technology, the paired straight hearth (PSH) furnace process, the carbothermic reduction of ore-coal composite pellets in a tall pellets bed was investigated at the lab-scale in the present work. The experimental results show that, under the present experimental conditions, when the height of the pellets bed is 80 mm (16–18 mm each layer, and 5 layers), the optimal amount of carbon to add is C/O = 0.95. Addition of either more or less carbon does not benefit the production of high quality direct reduced iron (DRI). The longer reduction time (60 min) may result in more molten slag in the top layer of DRI, which does not benefit the actual operation. At 50 min, the metallization degree could be up to 85.24%. When the experiment was performed using 5 layers of pellets (about 80 mm in height) and at 50 min duration, the productivity of metallic iron could reach 55.41 kg-MFe/m2·h (or 75.26 kg-DRI/m2·h). -
Standard Muffle Furnace FO Series
Standard Muffle Furnace FO Series Operating o Temp. control Internal 1.5L 3.75L 7.5L 9L 11.3L 17.5L 23.6L 30L 100~1150 C ±2°C (at 1150°C) temp. range accuracy capacity (FO100CR/110CR) (FO200CR/210CR) (FO300CR/310CR) (FO410CR) (FO510CR) (FO610CR) (FO710CR) (FO810CR) Wide selection of space-saving compact units with maximum inner capacity Easy to use controller Excellent heat tightness with a firmly sealed chamber door High temperature accuracy at ±2.0°C Program operation of maximum of 6 patterns: 30 steps x 1 pattern, 15 steps x 2 patterns or 10 steps x 3 patterns Safety features include self-diagnostic functions, calibration off-set, lock function, auto-recovery after power failure, earth leakage breaker and automatic overheat prevention device Selectable options include exhaust system 1.5L 9L 11.3L 30L unit, N2 gas loading device (with flow meter), FO110CR FO410CR FO510CR FO810CR temperature output terminal, time up / alarm output terminal and sample tray Upgraded with long life R-thermocouple sensors Designed with communication port Specifications Model FO100CR/110CR FO200CR/210CR FO300CR/310CR FO410CR FO510CR FO610CR FO710CR FO810CR Operating temp. range 100~1150oC Temp. control accuracy ±2oC (at 1150oC) Max. temp. reaching time ~60min. ~70min. ~80min. Exterior material Cold rolled steel plate with baked-on melamine resin finish Internal material Ceramic fiber Sensor R-thermocouple Heater Iron-chrome wire 1kW 1.5kW 2kW 2.2kW 2.5kW 3kW 3.5kW 4kW Exhaust port ø20mm (top) Cooling Fan Type Axial fan motor Temp. controller PID controll by microprocessor Temp. setting/display method Digital setting by▲/▼ keys / Digital display Operation function Fixed temperature, quick auto stop, auto stop, auto start, program (maximum 6 patterns: 30 steps x 1 pattern, 15 steps x 2 patterns or 10 steps x 3 patterns) Additional function Calibration offset, power failure compensation, lock, RS485 communication interface Timer 1 min. -
Transactions
52-5 TRANSACTIONS OF THE AMERICAN INSTITUTE OF MINING ENGINEERS. VOL. IV. MAY, 1875, TO FEBRUARY, 1876. EASTON, PA.: PUBLISHED BY THE INSTITUTE, AT THE OFFICE OF THE SECRETARY, LAFAYETTE COLLEGE. PHILADELPHIA: SHERMAN & CO., PRINTERS. CONTENTS. PAGE OFFICERS AND MEMBERS,.......................................................................v-xx RULES, ................................................................................................... xxi DOVER MEETING, May, 1875,........................................................................3 CLEVELAND MEETING, October, 1875,........................................................... 9 WASHINGTON MEETING, February, 1876....................................................... 1 8 DOVER MEETING. Repairing the Upper Part of a Furnace Lining, without Blowing Out. By FRANK FIRMSTONE, ....................................................................29 On the Use of Natural Gas for Puddling and Heating, at Leechburg, Penn- sylvania. By A. L. HOLLEY, C.E.,...................................................... 32 The Swansea Silver Smelting arid Refining Works of Chicago. By .J. L. JERNEGAN, JR., M.E., ...........................................................................35 Fires in Mines. Their Causes and the Means of Extinguishing Them. By RlCHARD P. ROTHWELL, M.E.........................................................................54 CLEVELAND MEETING. Some Pressing Needs of Our Iron and Steel Manufacture. By A. L HOL- LEY,C.E.,...........................................................................................................