Vertical Axis Wind Turbine 1
Total Page:16
File Type:pdf, Size:1020Kb
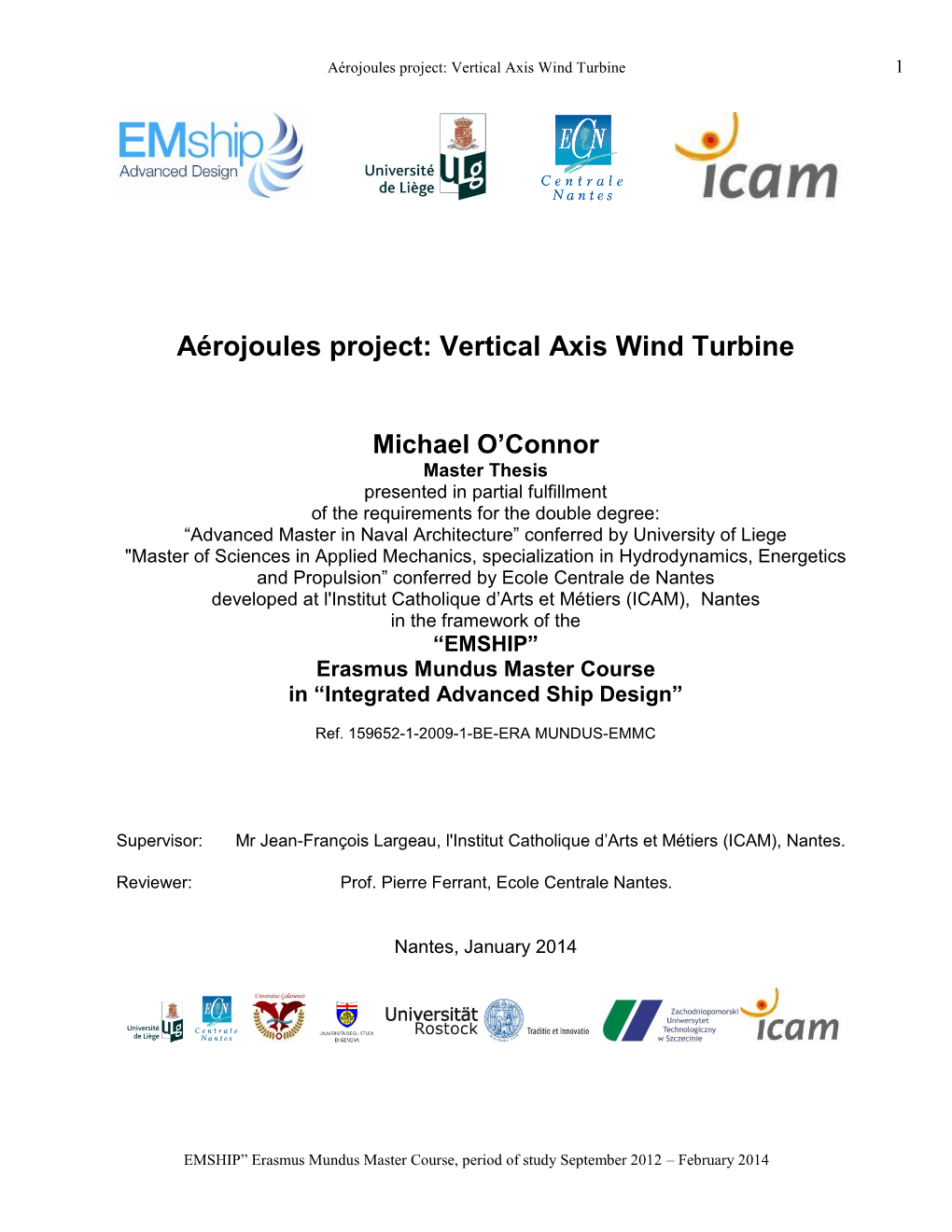
Load more
Recommended publications
-
Implementation and Validation of an Advanced Wind Energy Controller in Aero-Servo-Elastic Simulations Using the Lifting Line Free Vortex Wake Model
energies Article Implementation and Validation of an Advanced Wind Energy Controller in Aero-Servo-Elastic Simulations Using the Lifting Line Free Vortex Wake Model Sebastian Perez-Becker *, David Marten, Christian Navid Nayeri and Christian Oliver Paschereit Chair of Fluid Dynamics, Hermann Föttinger Institute, Technische Universität Berlin, Müller-Breslau-Str. 8, 10623 Berlin, Germany; [email protected] (D.M.); [email protected] (C.N.N.); [email protected] (C.O.P.) * Correspondence: [email protected] Abstract: Accurate and reproducible aeroelastic load calculations are indispensable for designing modern multi-MW wind turbines. They are also essential for assessing the load reduction capabilities of advanced wind turbine control strategies. In this paper, we contribute to this topic by introducing the TUB Controller, an advanced open-source wind turbine controller capable of performing full load calculations. It is compatible with the aeroelastic software QBlade, which features a lifting line free vortex wake aerodynamic model. The paper describes in detail the controller and includes a validation study against an established open-source controller from the literature. Both controllers show comparable performance with our chosen metrics. Furthermore, we analyze the advanced load reduction capabilities of the individual pitch control strategy included in the TUB Controller. Turbulent wind simulations with the DTU 10 MW Reference Wind Turbine featuring the individual pitch control strategy show a decrease in the out-of-plane and torsional blade root bending moment fatigue loads of 14% and 9.4% respectively compared to a baseline controller. Citation: Perez-Becker, S.; Marten, D.; Nayeri, C.N.; Paschereit, C.O. -
Investigation of Different Airfoils on Outer Sections of Large Rotor Blades
School of Innovation, Design and Engineering Bachelor Thesis in Aeronautical Engineering 15 credits, Basic level 300 Investigation of Different Airfoils on Outer Sections of Large Rotor Blades Authors: Torstein Hiorth Soland and Sebastian Thuné Report code: MDH.IDT.FLYG.0254.2012.GN300.15HP.Ae Sammanfattning Vindkraft står för ca 3 % av jordens produktion av elektricitet. I jakten på grönare kraft, så ligger mycket av uppmärksamheten på att få mer elektricitet från vindens kinetiska energi med hjälp av vindturbiner. Vindturbiner har använts för elektricitetsproduktion sedan 1887 och sedan dess så har turbinerna blivit signifikant större och med högre verkningsgrad. Driftsförhållandena förändras avsevärt över en rotors längd. Inre delen är oftast utsatt för mer komplexa driftsförhållanden än den yttre delen. Den yttre delen har emellertid mycket större inverkan på kraft och lastalstring. Här är efterfrågan på god aerodynamisk prestanda mycket stor. Vingprofiler för mitten/yttersektionen har undersökts för att passa till en 7.0 MW rotor med diametern 165 meter. Kriterier för bladprestanda ställdes upp och sensitivitetsanalys gjordes. Med hjälp av programmen XFLR5 (XFoil) och Qblade så sattes ett blad ihop av varierande vingprofiler som sedan testades med bladelement momentum teorin. Huvuduppgiften var att göra en simulering av rotorn med en aero-elastisk kod som gav information beträffande driftsbelastningar på rotorbladet för olika vingprofiler. Dessa resultat validerades i ett professionellt program för aeroelasticitet (Flex5) som simulerar steady state, turbulent och wind shear. De bästa vingprofilerna från denna rapportens profilkatalog är NACA 63-6XX och NACA 64-6XX. Genom att implementera dessa vingprofiler på blad design 2 och 3 så erhölls en mycket hög prestanda jämfört med stora kommersiella HAWT rotorer. -
Wind Field Simulation in a Wind Farm Using Openfoam and Actuator Line Model
ParCFD'2019 31st International Conference on Parallel Computational Fluid Dynamics May-14-17 2019, Antalya TURKEY WIND FIELD SIMULATION IN A WIND FARM USING OPENFOAM AND ACTUATOR LINE MODEL Huseyin Can Onel∗ & Dr. Ismail H. Tuncery ∗ Middle East Technical University (METU) Department of Aerospace Engineering 06800 Ankara, TURKEY e-mail: [email protected] yMiddle East Technical University (METU) Department of Aerospace Engineering 06800 Ankara, TURKEY e-mail: [email protected] - Web page: http://www.ae.metu.edu.tr/tuncer/ Key words: Aerospace applications, Wind turbine, HAWT, Actuator Line Model, Wake calculation Abstract. In this study, a horizontal axis wind turbine (HAWT) is modeled using so called Actuator Line Model (ALM), where full resolution of boundary layer over turbine blades is not needed and hence computation is cheaper. Results are validated against other numerical and experimental studies as well as panel method (XFOIL) and Blade Element Momentum Theory (BEMT) results which are still widely employed in today's wind energy industry. Important simulation and operation parameters and their effects on accuracy are discussed. It is concluded that within a certain range of tip speed ratios, ALM gives acceptable results and is a promising model for full-scale wind farm simulations to estimate energy production. 1 INTRODUCTION Market share of renewable energy grows at ever highest rates and wind turbine and wind farm design processes becomes more sophisticated with the advancements in computation technologies. There are two main design problems in wind energy: • Design of an individual wind turbine at its ideal operation conditions, where classical methods like 2D airfoil theory, potential flow theory and Blade Element Momentum Theory (BEMT) are still widely used, • Design of a complete wind farm, in which statistical meteorological data is used for macro-siting and simple analytical or empirical methods are used for micro-siting. -
Design and Simulation of Small Wind Turbine Blades in Q-Blade
© 2017 IJEDR | Volume 5, Issue 4 | ISSN: 2321-9939 Design and Simulation of Small Wind Turbine Blades in Q-Blade 1Veeksha Rao Ponakala, 2Dr G Anil Kumar 1PG Student, 2Assistant Professor School of Renewable Energy and Environment, Institute of Science and Technology, JNTUK, Kakinada, India Abstract- Electrical energy demand has been continuously increasing. Power generation using wind turbines is becoming viable solution as there is demand for cleaner energy sources. Wind power generators are usually located away from human dwellings for higher power generation. In any other case, turbines placed at lower altitudes, are subjected to low wind speeds and non optimal wind flow conditions. Vertical axis wind turbines (VAWTs) are more efficient than the horizontal axis wind turbines (HAWTs) for low wind speed applications because of their ability to capture wind flowing from any direction. Therefore, VAWT systems are more suitable for residential and urban applications as they are universally adaptable. Major limitation observed in VAWT is high drag and turbulent force produced by the blade. This paper presents the VAWT rotor blade design to overcome the limitations. By considering the parameters required for design of blade geometry, National Advisory Committee of Aeronautics (NACA) series 0016- 64 can be utilised for optimum aerodynamic performance. NACA 0018 airfoil is selected and analysed within the required range of Reynolds numbers and wind speeds in Q-Blade software. With the proper airfoil design optimal for low wind speed conditions, the turbine efficiency can be increased in addition to maximisation of the power produced. Index Terms- VAWT, Rotor Blades, Airfoil, Lift Force, Drag Force, Q-Blade. -
Qblade Guidelines V0.6
QBlade Guidelines v0.6 David Marten Juliane Wendler January 18, 2013 Contact: david.marten(at)tu-berlin.de Contents 1 Introduction 5 1.1 Blade design and simulation in the wind turbine industry . 5 1.2 The software project . 7 2 Software implementation 9 2.1 Code limitations . 9 2.2 Code structure . 9 2.3 Plotting results / Graph controls . 11 3 TUTORIAL: How to create simulations in QBlade 13 4 XFOIL and XFLR/QFLR 29 5 The QBlade 360◦ extrapolation module 30 5.0.1 Basics . 30 5.0.2 Montgomery extrapolation . 31 5.0.3 Viterna-Corrigan post stall model . 32 6 The QBlade HAWT module 33 6.1 Basics . 33 6.1.1 The Blade Element Momentum Method . 33 6.1.2 Iteration procedure . 33 6.2 The blade design and optimization submodule . 34 6.2.1 Blade optimization . 36 6.2.2 Blade scaling . 37 6.2.3 Advanced design . 38 6.3 The rotor simulation submodule . 39 6.4 The multi parameter simulation submodule . 40 6.5 The turbine definition and simulation submodule . 41 6.6 Simulation settings . 43 6.6.1 Simulation Parameters . 43 6.6.2 Corrections . 47 6.7 Simulation results . 52 6.7.1 Data storage and visualization . 52 6.7.2 Variable listings . 53 3 Contents 7 The QBlade VAWT Module 56 7.1 Basics . 56 7.1.1 Method of operation . 56 7.1.2 The Double-Multiple Streamtube Model . 57 7.1.3 Velocities . 59 7.1.4 Iteration procedure . 59 7.1.5 Limitations . 60 7.2 The blade design and optimization submodule . -
Performance Analysis of a Small Capacity Horizontal Axis Wind Turbine Using Qblade
International Journal of Recent Technology and Engineering (IJRTE) ISSN: 2277-3878, Volume-7, Issue-6S, March 2019 Performance Analysis of a Small Capacity Horizontal Axis Wind Turbine using QBlade Ali Said, Mazharul Islam, Mohiuddin A.K.M, Moumen Idres Abstract--- In recent times, wind energy has become one of the In this article, selected prospective airfoils have been leading renewable energy sources for generating electricity in identified and analyzed with the help of Qblade software. prospective regions around the globe. Nowadays, researchers are Results for a 3kW HAWT have also been validated with conducting different research activities to develop and optimize existing experimental results from Anderson et al [3]. The the existing designs of wind turbines through experimental and diversified computational techniques. Among the computational current research outcomes are expected to help the techniques, one of the popular choices is Computational Fluid prospective researchers to design optimized smaller-capacity Dynamics (CFD). However, CFD techniques are hardware HAWT for different prospective locations. intensive and computationally expensive. On the other hand, freely available simple tools like QBlade is computationally inexpensive and it can be used for performance and design analyses of horizontal and vertical axis wind turbines. In the present research, an attempt has been made to use QBlade for performance analyses of a smaller capacity horizontal axis wind turbine using selected prospective airfoils. In this study, four airfoils (namely, NACA 4412, SG6043, SD7062 and S833) have been selected and investigated in QBlade. It has been found that the overall power coefficients (CP) of NACA 4412 at different tip speed ratios are superior to the other three airfoils. -
Book of Abstracts
Book of abstracts 9th PhD Seminar on Wind Energy in Europe September 18-20, 2013 Uppsala University Campus Gotland, Sweden Campus Gotland WIND ENERGY Book of abstracts of 9th PhD Seminar on Wind Energy in Europe Uppsala University Campus Gotland, Sweden Campus Gotland, Wind Energy 621 67 Visby PREFACE The wind energy field is becoming more and more important in relation with future challenges of switching the world energy system to renewables. Therefore it is of high importance that tomorrow’s researchers in the field from all over the word meet and discuss future challenges. The 9th annual EAWE PhD seminar is in 2013 organized by Uppsala University Campus Gotland. This is a very suitable place for this event since it combines a unique historical environment with a sustainable profile and a long tradition of wind energy. Today about 45% of the energy consumption is locally produced by wind energy. Uppsala University Campus Gotland also has more than 10 years experience of teaching and research in the field with a focus on wind power project development. The aim with this seminar is to improve the international communication and information sharing of ongoing activities as well as simplify contact building between young researchers. It is also a perfect opportunity for PhD students to practice and improve their presentation and discussion skills. Associate Professor Stefan Ivanell Director, Wind Energy Uppsala University, Campus Gotland Book of abstracts of 9th PhD Seminar on Wind Energy in Europe September 18-20, 2013, Uppsala University Campus Gotland, Sweden TABLE OF CONTENTS ROTOR & WAKE AERODYNAMICS UNDERSTANDING THE WIND TURBINE BREAKDOWN MECHANISM WITH CFD M. -
Numerical Simulations of a Large Offshore Wind Turbine Exposed to Turbulent Inflow Conditions
9th European Seminar OWEMES 2017 Numerical simulations of a large offshore wind turbine exposed to turbulent inflow conditions Galih Bangga, Giorgia Guma, Thorsten Lutz and Ewald Krämer Institute of Aerodynamics and Gas Dynamics (IAG),University of Stuttgart, Germany [email protected] Abstract – The present works are intended to investigate the aerodynamic responses of a large generic 10MW offshore wind turbine under turbulent inflow conditions. The non-linear Lifting Line Free Vortex Wake Simulations approach is employed for this purpose computed using the QBlade code. In these studies, the effects of a three-dimensional (3D) correction model for the airfoil polars were studied in advance. For this purpose, the Blade Element Momentum computations employing the corrected polars are performed and compared to Computational Fluid Dynamics (CFD) simulations, and a good agreement is obtained between both employed approaches. Background turbulence is then imposed in the QLLT simulations with the turbulence intensities ranging from low to high turbulence levels (3% - 15%). Furthermore, the impact of wind shear from different locations (offshore and onshore) is investigated in the present works. 1. Introduction A fundamental issue in accurate estimation of the power output has been noted with the continuous increase of the offshore wind farm size which is partly contributed by difficulties in flow and wake modeling [1]. This is particularly caused by the complexity of the wake downstream of the turbine and their relationship with atmospheric variables such as the variability of wind speed, direction, turbulence and atmospheric stability that is not yet fully understood [2]. Further understanding of the relationships between these variables is required to improve the current state of the art wind farm and wake models. -
Master Index 2004-05 to 2017-18
BHARATI VIDYAPEETH DEEMED UNIVERSITY COLLEGE OF ENGINEERING, PUNE 411043 RESEARCH PUBLICATION ACADEMIC YEAR 2012-13 to 2017-18 SUMMARY OF LIST OF PUBLICATIONS No. of Research Papers Published in Sr. Academic Journal Conference Total No. Year International National International National 1. 229 03 27 01 260 2017-18 2. 249 02 20 04 267 2016-17 3. 263 00 16 02 236 2015-16 4. 2014-15 206 05 28 03 218 5. 171 07 27 01 199 2013-14 1118 17 118 11 1180 Total Academic Year 2017-18 International Journal Sr. No. Author (s) Complete Title of the Journal Volume & Page Month ISSN Impact List List List Title of the Issue Nos. and Factor ed ed ed Article Number Year of In In In Publicati Sco Web Goo on pus of gle Scie Scho nce lar 1. BVDUC Pallavi C. Synthesis International Journal Volume pp: July 2017 ISSN: 0.34 N N Y OE/2017- Kale, and of Chemtech 10, 477- 0974- 18/IJ01/ Prashant L. Characterizat Research Issue 486 4290 Chem. Chaudhari ion of Nano 9 Zinc Peroxide Photocatalyst for the Removal of Brilliant Green Dye from Textile Waste Water. 2. BVDUC Satyajeet S. Isobaric Journal of Chemical Volume 62 pp: July 2017 ISSN: 2.196 Y Y Y OE/2017- Yadav, Nilesh Vapor−Liqui and Engineering 2436- 0021- 18/IJ02/ A. Mali, Sunil d Data 2442 9568 Chem. S. Joshi, and Equilibrium Prakash V. Data for the Chavan Binary Systems of Dimethyl Carbonate with Xylene Isomers at 93.13 kPa 3. BVDUC Manisha Cauliflower Bioprocess and Volume: pp: October ISSN: 2.139 Y Y Y OE/2017- A.Khedkar , Waste Biosystems 40, 1493- 2017 1615- 18/IJ03/ Pranhita Utilization Engineering Issue: 10 1506 7591 Chem. -
Template COBEM 2007
XXVI Congresso Nacional de Estudantes de Engenharia Mecânica, CREEM 2019 19 a 23 de agosto de 2019, Ilhéus, BA, Brasil ANÁLISE DO COMPORTAMENTO MECÂNICO DA PÁ DE TURBINA EÓLICA DE 5 MW POR MEIO DE SOFTWARE LIVRE BASEADO NO MÉTODO DE ELEMENTOS FINITOS Renata Silva Lins, [email protected] Augusto Salomão Bornschlegell, [email protected] 1Universidade Federal da Grande Dourados, Rodovia Dourados/Itahum, Km 12 - Unidade II Resumo. Objetivo deste trabalho é analisar a influência da aceleração gravitacional e centrífuga em uma pá de turbina eólica de 5MW desenvolvida pela National Renewable Energy Laboratory (NREL), em seu limite de operação, convertendo a velocidade de corte em pressão dinâmica em sua superfície. Será observado os casos em que ela se encontra de modo estático e rotacional, avaliando os campos de tensões principais, tensão de von Mises e os deslocamentos. Para os carregamentos avaliados, os níveis de tensões da estrutura estão abaixo dos limites de escoamento do material. Palavras chave: Pás eólicas. FEA. Salome-Meca. Análise estrutural. 1. INTRODUÇÃO A transição energética se faz necessária para cumprir as metas climáticas, colaborar com a preservação do meio ambiente e a redução da emissão de gases poluentes provenientes de combustíveis fósseis. Devido a estes fatores, energias renováveis estão sendo consumidas cada vez mais pelos países desenvolvidos e em desenvolvimento, não apenas por questões ambientais, mas pelos recursos inesgotáveis que auxiliam também na economia destes. O vento é um desses recursos, sendo o principal elemento na geração de energia eólica. A potência extraída deste recurso pode ocorrer em fazendas eólicas instaladas tanto em meio terrestre (onshore) quanto marítimo (offshore). -
Page De Garde
-PET- Vol. 57 ISSN : 1737-9934 Advanced techniques on control & signal processing Proceedings of Engineering & Technology -PET- Editor : Dr. Ahmed Rhif (Tunisia) International Centre for Innovation & Development –ICID– ISSN: 1737-9334 -PET- Vol. 57 ICID International Centre for Innovation & Development Proceedings of Engineering & Technology -PET- Advanced techniques on control & signal processing Editor: Dr. Ahmed Rhif (Tunisia) International Centre for Innovation & Development ICID – – Editor in Chief: Lijie Jiang, China Dr. Ahmed Rhif (Tunisia) Mohammed Sidki, Morocco [email protected] Dean of International Centre for Natheer K.Gharaibeh, Jordan Innovation & Development (ICID) O. Begovich Mendoza, Mexico Editorial board: Özlem Senvar, Turkey Janset Kuvulmaz Dasdemir, Turkey Qing Zhu, USA Mohsen Guizani, USA Ved Ram Singh, India Quanmin Zhu, UK Beisenbia Mamirbek, Kazakhstan Muhammad Sarfraz, Kuwait Claudia Fernanda Yasar, Turkey Minyar Sassi, Tunisia Habib Hamdi, Tunisia Seref Naci Engin, Turkey Laura Giarré, Italy Victoria Lopez, Spain Lamamra Kheireddine, Algeria Yue Ma, China Maria Letizia Corradini, Italy Zhengjie Wang, China Ozlem Defterli, Turkey Amer Zerek, Libya Abdel Aziz Zaidi, Tunisia Abdulrahman A. A. Emhemed, Libya Brahim Berbaoui, Algeria Abdelouahid Lyhyaoui, Morocco Jalel Ghabi, Tunisia Ali Haddi, Morocco Yar M. Mughal, Estonia Hedi Dhouibi, Tunisia Syedah Sadaf Zehra, Pakistan Jalel Chebil, Tunisia Ali Mohammad-Djafari, France Tahar Bahi, Algeria Greg Ditzler, USA Youcef Soufi, Algeria Fatma Sbiaa, Tunisia Ahmad Tahar Azar, Egypt Kenz A.Bozed, Libya Sundarapandian Vaidyanathan, India Lucia Nacinovic Prskalo, Croatia Ahmed El Oualkadi, Morocco Mostafa Ezziyyani, Morocco Chalee Vorakulpipat, Thailand Nilay Papila, Turkey Faisal A. Mohamed Elabdli, Libya Rahmita Wirza, Malaysia Feng Qiao, UK Summary Comparative of Data Acquisition Using Wired and Wireless Communication System Based Page 1 on Arduino and nRF24L01. -
Effects of Airfoil's Polar Data in the Stall Region on The
David Marten Chair of Fluid Dynamics, Hermann-F€ottinger-Institut, Technische Universit€at Berlin, M€uller-Breslau-Str. 8, Berlin 10623, Germany e-mail: [email protected] Downloaded from https://asmedigitalcollection.asme.org/gasturbinespower/article-pdf/139/2/022606/6175472/gtp_139_02_022606.pdf by Tu Berlin Universitaetsbibl.im Volkswagen-haus user on 20 December 2019 Alessandro Bianchini Department of Industrial Engineering, University of Florence, Via di Santa Marta 3, Firenze 50139, Italy Effects of Airfoil’s Polar Data e-mail: [email protected]fi.it Georgios Pechlivanoglou in the Stall Region on the Chair of Fluid Dynamics, Hermann-F€ottinger-Institut, Estimation of Darrieus Wind Technische Universit€at Berlin, M€uller-Breslau-Str. 8, Berlin 10623, Germany Turbine Performance e-mail: [email protected] Interest in vertical-axis wind turbines (VAWTs) is experiencing a renaissance after most Francesco Balduzzi major research projects came to a standstill in the mid 1990s, in favor of conventional Department of Industrial Engineering, horizontal-axis turbines (HAWTs). Nowadays, the inherent advantages of the VAWT con- University of Florence, cept, especially in the Darrieus configuration, may outweigh their disadvantages in spe- Via di Santa Marta 3, cific applications, like the urban context or floating platforms. To enable these concepts Firenze 50139, Italy further, efficient, accurate, and robust aerodynamic prediction tools and design guide- e-mail: [email protected]fi.it lines are needed for VAWTs, for which low-order simulation methods have not reached yet a maturity comparable to that of the blade element momentum theory for HAWTs’ Christian Navid Nayeri applications. The two computationally efficient methods that are presently capable of Chair of Fluid Dynamics, capturing the unsteady aerodynamics of Darrieus turbines are the double multiple Hermann-F€ottinger-Institut, streamtubes (DMS) theory, based on momentum balances, and the lifting line theory Technische Universit€at Berlin, (LLT) coupled to a free vortex wake model.