Archetroceedings T.Ab
Total Page:16
File Type:pdf, Size:1020Kb
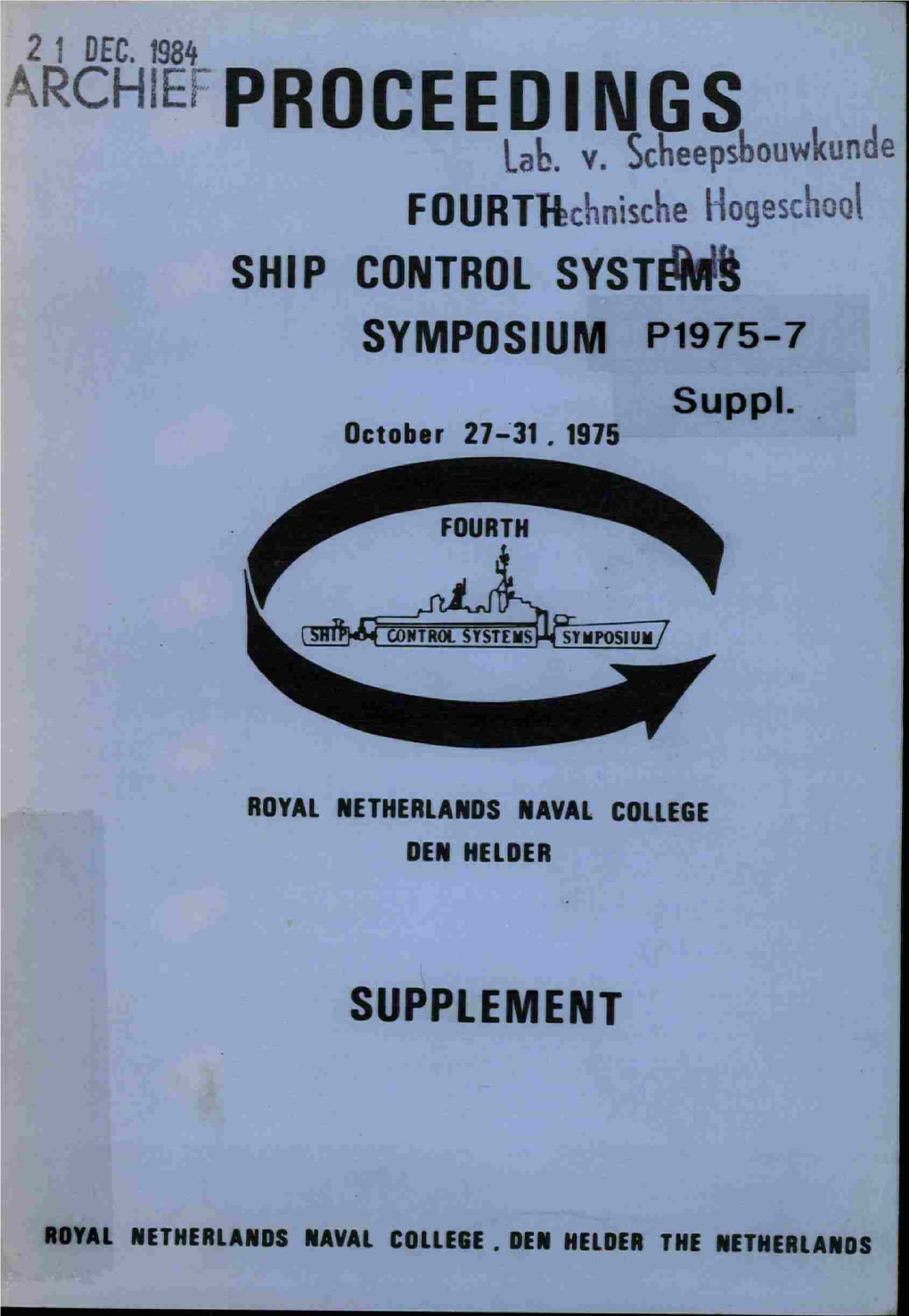
Load more
Recommended publications
-
Reginald James Morry's Memoirs of WWII
THE MORRY FAMILY WEBSITE -- HTTP://WEB.NCF.CA/fr307/ World War II Memoirs of Reginald James Morry Including an eyewitness account of the sinking of the German battleship “Bismarck”. Reginald James Morry 10/6/2007 Edited by C. J. Morry Following long standing Newfoundland maritime tradition, when hostilities broke out at the beginning of WWII, Reginald James Morry chose to serve in the “Senior Service”, the Royal Navy. This is his personal account of those momentous years, including one of the most crucial naval battles of the war, the sinking of the German battleship “Bismarck”. © Reginald James Morry; Edmonton, Alberta, Canada; 2007 World War II Memoirs of Reginald James Morry (then Able Seaman R. Morry P/SSX 31753) Including an eyewitness account of the sinking of the German battleship “Bismarck”. Newfoundland’s Military Legacy Newfoundland participated in both World Wars. Even though the province is small, it produced a famous Regiment of Infantry that fought in Gallipolis and from there to France. They lost quite a few men in Turkey and were decimated twice in France, once in Beaumont Hamel and again at Arras and other areas on the Somme. Total casualties (fatal) were 1305, and at sea 179 lost their lives. Of those that returned, many died of wounds, stress, and worn out hearts. They were given the title “Royal” for their role in the defence of Masnieres (the Battle for Cambrai) by King George VI, the reigning Monarch of the time. World War II is practically dead history, especially since some anti-Royals disbanded the regiment in 2002, as it's territorial section, according to the present army regime in HQ Ottawa, did not measure up!! During WWII the British changed the regiment over to Artillery so they became known as The Royal Newfoundland Light Artillery to lessen the chances of heavy losses. -
Thanks a Million, Tornado
Aug 11 Issue 39 desthe magazine for defenceider equipment and support Thanks a million, Tornado Fast jets in focus − Typhoon and Tornado impress See inside Welcome Warrior Goliath’s The future Warfare goes Voyager returns to war giant task is now on screen lockheedmartin.com/f35 NOT JUSTAN AIRCRAFT, THE UK’SAIRCRAFT The F-35 Lightning II isn’t just a cutting-edge aircraft. It also demonstrates the power of collaboration. Today, a host of UK companies are playing their part in developing and building this next-generation F-35 fi ghter. The F-35 programme is creating thousands of jobs throughout the country, as well as contributing LIGHTNINGLIGHTNING IIII to UK industrial and economic development. It’s enhancing the UK’s ability to compete in the global technology marketplace. F-35 Lightning II. Delivering prosperity and security. UNITED KINGDOM THE F-35 LIGHTNING II TEAM NORTHROP GRUMMAN BAE SYSTEMS PRATT & WHITNEY LOCKHEED MARTIN 301-61505_NotJust_Desider.indd 1 7/14/11 2:12 PM FRONTISPIECE 3 lockheedmartin.com/f35 Jackal helps keep the peace JACKAL CUTS a dash on Highway 1 between Kabul and Kandahar, one of the most important routes in Afghanistan. Soldiers from the 9th/12th Royal Lancers have been helping to keep open a section of the road which locals use to transport anything from camels to cars. The men from the Lancers have the tough task of keeping the highway open along with members of 2 Kandak of the Afghan National Army, who man checkpoints along the road. NOT JUSTAN AIRCRAFT, Picture: Sergeant Alison Baskerville, Royal Logistic Corps THE UK’SAIRCRAFT The F-35 Lightning II isn’t just a cutting-edge aircraft. -
The American Legion [Volume 116, No. 5 (May 1984)]
one pair WHEN YOU PAIRS ORDER SHOES ANY FOR Yes! Wear them, try them, test one pair any way you wish before you decide to keep your order. Because Haband, the mail order people from Paterson, New Jersey, believe you can't tell a shoe by its cover! you must be sure they look as great, feel as great, and wear every bit as great as promised or pack them up and fire them back for full refund of the $29.95! HABAND RE-INVENTS THE SHOE!! No other product known to man can so immediately mpact your minute to minute personal comfort as your shoes! Yet who can afford the current outrageous $50 or $100 a pair? That's why Haband invented a whole New Factory Approach, just as cataclysmic as the reorganization of General Motors! You get a better product! Better Looks! and FAR MORE COMFORT! You get beautiful lustrous kid grained man-made uppers that, keep a soft natural lustre, & never need a shine! You get sure footed extra cushion crepe rubber heel & sole! Special built-in support shank in the arch! Long wear shape / holding heel counters. Loafers have built-in elastic gore. Oxfords have strong braided laces. In short, you get ALL YOU EVER WANTED in BEWARE THE RETURN OF INFLATION! Look Carefully and Act Fast! Shoe prices are at the edge of the springboard and on the way up! Do not miss this extraordinary chance RIGHT NOW to Haband 100% man-made ^\^\qc seize the LOWEST p 95 SHOE PRICE FOR executive Q hTs 5>Q THE REST S QUALITY SHOES V WtJ OF YOUR 4 for 39.50 ALL 5 for 08.95 LIFE! HABAND 265 IN. -
For Veterans, by Veterans
RECRUITERS ‘MADE IT HAPPEN’ IN 2019 O?PLP:LABG@MHGCENTENNIAL SERVING VETERANS FOR 100YEARS WOUNDED VETS INSPIRE & MOTIVATE VFW FOSTERS FIRST ALL-GIRL BOY SCOUT TROOP Mesothelioma Victims While bravely serving this country, many military veterans were exposed to asbestos – the dangerous mineral that causes the cancer, mesothelioma. 5 Important Facts: 1. Asbestos-containing products and equipment were widely used across every branch of the military between 1930 and the late 1970s. 2. 44% of all Sokolove Law mesothelioma cases are U.S. Veterans – representing nearly every state in the U.S. 3. Symptoms of mesothelioma can take 20-50 years to appear. 4. An estimated $30 Billion in court-ordered trusts has been set aside to provide funds for victims and families. 5. Pursuing an asbestos legal claim does not affect VA LiiwÌÃÀ pensions. We bring claims against the manufacturers – not the U.S. government or military. Most mesothelioma claims are settled out of court, easing the stress and burden on families. If you or a loved one has been diagnosed with mesothelioma, or any other asbestos-related cancer, you may be eligible for compensation – without ever w}>>ÜÃÕÌÀiÛi}}ÌVÕÀ̰ Call us today. Our team is available 24/7, every day. Call 800-721-1960 This is an advertisement. Sokolove Law, LLC (LLP in certain states), 1330 Boylston St, Chestnut Hill/MA. Ricky LeBlanc admitted in MA only. Members: Hardy Croxton, Rogers/AR, Rich Grabow, 970 Farmington Ave West Hartford/CT (860) 904-7789, Paul J. Morgan, Winter Park/ FL, Nick Nighswander, Florence/KY, Michael Breaux, Gonzales, admitted LA, Gregg Hobbie, NJ, Matt Christian, 1007 East Washington Street, Greenville SC. -
The Navy Is Here!
CONTACT ! The Newsletter of the former RAF Defford Reunion Association, now merged with the DEFFORD AIRFIELD HERITAGE GROUP in partnership with THE NATIONAL TRUST, CROOME http://deffordairfieldheritagegroup.wordpress.com Editor: Bob Shaw Distribution: Ann Sterry Number 124, February 2019 THE NAVY IS HERE! Photo: Geoff Shaw Royal Navy Corsair comes in fast and low. There were at least four Corsairs at Defford from 1944, for trials with the Royal Naval section at Defford. In this edition of ‘Contact!’ we tell the story of Lt Cdr ‘Loopy’ Dunworth DSC, who was Officer Commanding the Naval Section at Defford 1951-1953. A popular and eccentric figure, he stayed on at Defford as a test pilot with Boulton Paul (see ‘Contact!’ no. 123, January 2019), at Defford after leaving the Navy. .2. Lt Cdr Geoffrey “Loopy” Dunworth DSC OC Naval Section, RAF Defford 1951-53. BPA Pilot 1953-1961 By Les Whitehouse, with additional material from Dennis Williams and overall editing by the editor Born in Manchester 5/8/1921 Geoff Dunworth qualified as a Research Chemist for ICI but in Sept 1940 he volunteered to be aircrew with the Fleet Air Arm of the Royal Navy, as an Observer. From RNAS Arbroath, he was posted to 817 Squadron aboard HMS Victorious, August 1941, which was part of the replacements for aircraft losses over Petsamo and Kirkenes, Norway in July. Escort of the Arctic convoys to Archangel (Operation Dervish) and then the escort of HMS Argus returning from Murmansk followed. Victorious launched air attacks, on targets in Norway, through to October 1941. L/A Geoff Dunworth along with gunner L/A Davies were teamed up with S/L Raymond. -
The American Legion [Volume 135, No. 3 (September 1993)]
I THE AMERICAN \ %%>^^ Legiom^ FOR GOD AND COUNTRY September 1993 Two Dollars HOME SCHflOUHB, Going To School By Staying Home It's Warm, it's Hefty, it's Handsome and it's 100% Acrylic Easy Care! Grey Use this coupon and grab yourself a couple today! Cardigan Sweater Q5 2 for 49.50 3 for 74.00 HAB 24 4 for 98.50 lOOFainiew HABAND COMPANY Prospect Park 100 Fairview Ave., Prospect Park, N J 07530 Send 07530 I Regular Sizes: S(34-36) M{38-40) L(42-44) XL(46-4£ sweaters, *Big Men Sizes: Add $4 each for cable knit I Handsome have enclosed 2XL(50-52) 3XL(54-56) 4XL(58-60) both front and back WHAT HOW is an expensive fealLir purchase price plus $3.50 7A7-72C SIZE? MANY? an amazing low pi le Burgundy postage and handling. A ECRU Check Enclosed B GREY D BURGUNDY 1 CARD # Name . Mail Addr ;ss ' Apt. # City 1 State Zip The Magazine for a Strong America Vol. 135, No. 3 ARTICLES September 1993 RETiraNG GRADUALLY By Gordon Williams 18 VA RESEARCH: WE ALL SeiEHT AWxnt^ VA research has improvedAmericans' health, budget cuts now threaten thisprogram. By Ken Schamberg 22 TO SCHOOL BY STAYING AT I More and more parents believe they can succeed at home where schools havefailed. By Deidre Sullivan 25 To dramatize the dangers, activists have been playingfast and loose with the numbers. By Steve Salerno 28 THE GHOST PLANE FROM MINDANAO You may have the information to help solve this WWII mystery. FAMILY TIES: LONGER UVES Centenarians reveal the secret oftheir long and healthy lives. -
Hornblower's Ships
Names of Ships from the Hornblower Books. Introduction Hornblower’s biographer, C S Forester, wrote eleven books covering the most active and dramatic episodes of the life of his subject. In addition, he also wrote a Hornblower “Companion” and the so called three “lost” short stories. There were some years and activities in Hornblower’s life that were not written about before the biographer’s death and therefore not recorded. However, the books and stories that were published describe not only what Hornblower did and thought about his life and career but also mentioned in varying levels of detail the people and the ships that he encountered. Hornblower of course served on many ships but also fought with and against them, captured them, sank them or protected them besides just being aware of them. Of all the ships mentioned, a handful of them would have been highly significant for him. The Indefatigable was the ship on which Midshipman and then Acting Lieutenant Hornblower mostly learnt and developed his skills as a seaman and as a fighting man. This learning continued with his experiences on the Renown as a lieutenant. His first commands, apart from prizes taken, were on the Hotspur and the Atropos. Later as a full captain, he took the Lydia round the Horn to the Pacific coast of South America and his first and only captaincy of a ship of the line was on the Sutherland. He first flew his own flag on the Nonsuch and sailed to the Baltic on her. In later years his ships were smaller as befitted the nature of the tasks that fell to him. -
Disposal Services Agency Annual Report and Accounts 2006-2007
Annual Report & Accounts 2006-2007 DisposalSMART 1 What is the Disposal Services Agency? The Disposal Services Agency (DSA) is the sole authority for the disposal process of all surplus defence equipment, with the exception of nuclear, land and buildings. The Agency targets potential markets particularly in developing countries in a pro-active manner; to enable them to procure formally used British defence equipment instead of equipment from other countries. The principal activity of the Agency is the provision of disposal and sales services to MoD and other parts of the public sector. These services include Government-to-Government Sales, Asset Realisation, Inventory Disposals, Site Clearances, Repayment Sales, Waste Management and Consultancy and Valuation Services. DSA’s Aim: To secure the best nancial return from the sale of surplus equipment and stores; to minimise the cost of sales and to operate as an intelligent contracting organisation with various agreements with British Industry and Commerce. DSA’s Mission: To provide Defence and other users with an agreed, effective and ef cient disposals and sales service in order to support UK Defence capability. DSA’s Vision: To be the best government Disposals organisation in the world. DisposalSMART Annual Report & Accounts 2006-2007 A Defence Agency of the Ministry of Defence Annual Report and Accounts 2006-2007 Presented to the House of Commons pursuant to section 7 of the Government Resources and Accounts Act 2000 Ordered by the House of Commons to be printed 23rd July 2007 HC 705 -
Trouble Ahead: Risks and Rising Costs in the UK Nuclear Weapons
TROUBLE AHEAD RISKS AND RISING COSTS IN THE UK NUCLEAR WEAPONS PROGRAMME TROUBLE AHEAD RISKS AND RISING COSTS IN THE UK NUCLEAR WEAPONS PROGRAMME David Cullen Nuclear Information Service April 2019 1 A note on terminology The National Audit Ofce (NAO) uses the term The terms ‘project’ and ‘programme’ are both used ‘Defence Nuclear Enterprise’. This refers to all of within government in diferent contexts to describe the elements in the programme but also includes the same thing. Although referred to as ‘projects’ elements which are technically and bureaucratically in the annual data produced by the government’s intertwined with it as part of the Astute submarine Infrastructure and Projects Authority (IPA), the programme. The term has also been adopted by the large MOD projects discussed in this report refer to MOD in recent publications. This report will also themselves as ‘programmes’ in their titles, and contain employ the term with the same meaning, usually within them major streams of work which are no doubt preferring the shorter ‘the Enterprise’. managed as separate projects in their own right. This report also uses the NATO shorthand ‘SSBN’ to As a general rule, this report aims to use the terms refer to submarines which are nuclear powered and project and programme to mean diferent things – a nuclear-armed and ‘SSN’ to refer to submarines which project being a relatively streamlined body of work are nuclear powered but not nuclear-armed. with a single purpose, and a programme being a larger-scale endeavour potentially encompassing A full glossary of terms and acronyms can be found at several bodies of work which may themselves be the end of the report on page 53. -
Missouri Veteran Stories, Collection, 2007-2010, (C4089)
C Missouri Veteran Stories, Collection, 2007-2010 4089 934 DVDs, 230 DAT tapes This collection is available at The State Historical Society of Missouri. If you would like more information, please contact us at [email protected]. INTRODUCTION The collection contains interviews with Missouri veterans on DVDs and DAT tapes. DONOR INFORMATION The records were transferred to the State Historical Society of Missouri by the Missouri Office of Administration on 24 June 2011 (Accession No. CA6288). ORGANIZATIONAL SKETCH Missouri Veterans Stories, a company hired by the Lt. Governor’s Office, collected these stories from Missouri veterans and hosted them online for the benefit of veterans and the general public. The program was open to all men and women currently residing in Missouri who had served in any branch of the United States military. SCOPE AND CONTENT NOTE The records have been arranged into the following three series: Individual Interviews Group and Miscellaneous Interviews DAT Tapes The Individual Interviews series contains hundreds of DVDs with Missouri veterans sharing stories about their military service. This series is arranged alphabetically by last name. The Group and Miscellaneous Interviews series contains group interviews and interview compilations. The DAT Tapes series consists of hundreds of digital recorded tapes and is arranged chronologically by date. C4089 Missouri Veteran Stories Collection, 2007-2010 Page 2 AUDIO VIDEO LIST Individual Interviews Series DVD Name Branch Rank/Assignment Service War/Conflict 1 VACANT 2 Second Class Carpenters Absher, Thomas F. Navy Mate, 63rd Naval Seabees 1942-1945 WWII 3 Ackmann, Harry Navy First Class Seaman, PC 597 1944-1946 4 Adair, Ronald Navy 1951-1955 Korea 5 Sergeant First Class, 25th Adams, James H. -
The Seven Seas Tattler Issue 4.3 – August 2020
The Seven Seas Tattler Issue 4.3 – August 2020 Good Day fellow members and welcome to the August edition of Tattler. As always, your comments, contributions and critique are welcome - Send to me at [email protected] Chairman's Report The Committee has not been idle during this lockdown and is managing issues of the Club virtually to determine the way forward when the Club reopens for business. The Committee is highly appreciative of Ancient Mariners and Honorary members who have forfeited their privilege of no subs, to make a donation for this financial year to assist the Club tackle the financial predicament it finds itself in during this lockdown period. The same appreciation goes towards the 100 club winners who have donated their winnings back to the Club. BZ. The Club is still fortunate to be able to remunerate its staff during this period with the exception of the Club Manager who has refused to take a salary and donated it back to the Club. This, once again, is highly appreciated. The good intentions of the above is soured a bit by certain members who have yet to pay their annual subscription. I urge those members to settle their accounts as soon as possible. Jonathan Golding is putting an auction together during this lockdown period to generate funding for the Club. It would appreciated if members support this endeavor as much as possible. Looking forward to seeing you all at the Club, sooner rather than later. Be safe. Birthdays in August The Club wishes the following members a very happy birthday and hopes that year ahead will be very kind to each of you! Capt. -
The Navy Vol 78 No 2 Apr 2016
WWW.NAVYLEAGUE.ORG.AU • @NAVYLEAGUEAUST • APR-JUN 2016 VOLUME 78 No.2 THE MAGAZINE OF THE NAVY LEAGUE OF AUSTRALIA ASIA’S RESTLESS F-35S FOR THE GIANTS CANBERRA CLASS LHDS BEFORE YOU STRIKE THE SILVER PHANTOM HARD AND FAST… HMS AURORA $5.95 INC.GST AUSTRALIA’S LEADING NAVAL MAGAZINE SINCE 1938 is the tailoring of purpose-built logistic solutions which deliver the most effective, efficient and sustainable outcomes for our clients. Our engineered approach is built on STRANG’s 90 years of experience, expertise, dedication and innovation. STRANG engineers world-leading solutions encompassing Supply Line Logistics, Project Freight Forwarding, Advisory Services and Port and Terminal Operations. We Engineer these Logistic Solutions globally, for example at Port Ehoala Madagascar depicted above, where we provide cargo handling, logistics, stevedoring and port services. Contact us www.stxgroup.com.au +61 2 9669 1099 Volume 78 No.2 THE MAGAZINE OF THE NAVY LEAGUE OF AUSTRALIA FEDERAL COUNCIL SOUTH AUSTRALIA DIVISION President: Graham M Harris, RFD (Incl. Northern Territory) 06 ASIA’S RESTLESS GIANTS: Senior Vice-President: Patron: His Excellency, John Jeremy, AM The Governor of South Australia. THE CHALLENGES TO ASIA’S Vice-Presidents: President: Dean Watson, RFD LCDR Roger Blythman, RFD, Hon. Secretary: Miss J E Gill MARITIME COMMONS Mark Schweikert PO Box 3008, Unley, SA 5061 By Michael Wesley Hon. Secretary: Philip Corboy Telephone: (08) 8272 6435 PO Box 128, Clayfield, Qld 4011 Mob: 0421 280 481 WESTERN AUSTRALIA DIVISION Email: [email protected] 11 F-35s FOR THE CANBERRA Patron: Her Excellency, The Governor of Western Australia. CLASS LHDs: CHOOSING AN NEW SOUTH WALES DIVISION President: Peter Jarvis (Incl.