Impacts of Central Tire Inflation Systems Application on Forest Transportation – Review
Total Page:16
File Type:pdf, Size:1020Kb
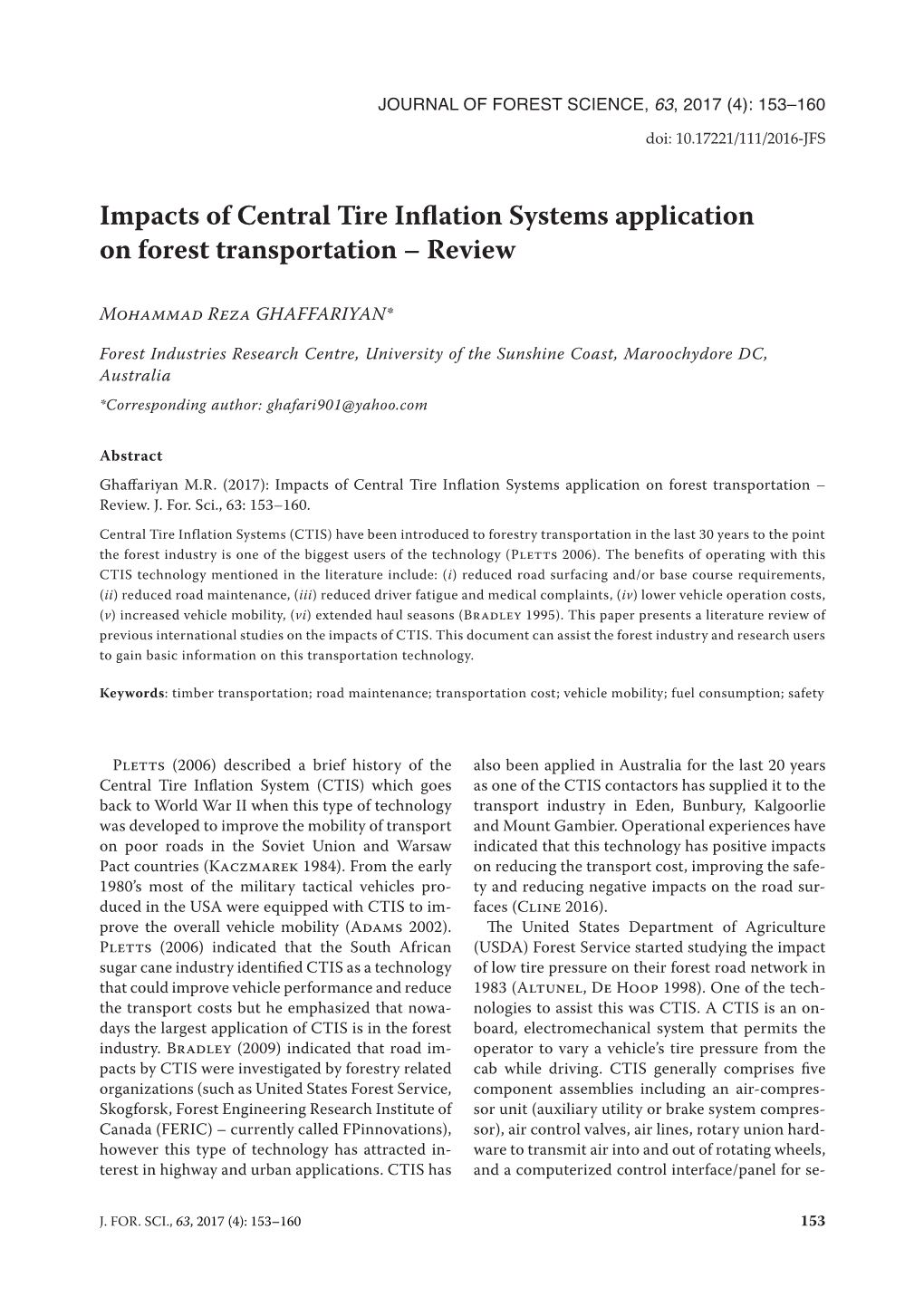
Load more
Recommended publications
-
Nonlinear Finite Element Modeling and Analysis of a Truck Tire
The Pennsylvania State University The Graduate School Intercollege Graduate Program in Materials NONLINEAR FINITE ELEMENT MODELING AND ANALYSIS OF A TRUCK TIRE A Thesis in Materials by Seokyong Chae © 2006 Seokyong Chae Submitted in Partial Fulfillment of the Requirements for the Degree of Doctor of Philosophy August 2006 The thesis of Seokyong Chae was reviewed and approved* by the following: Moustafa El-Gindy Senior Research Associate, Applied Research Laboratory Thesis Co-Advisor Co-Chair of Committee James P. Runt Professor of Materials Science and Engineering Thesis Co-Advisor Co-Chair of Committee Co-Chair of the Intercollege Graduate Program in Materials Charles E. Bakis Professor of Engineering Science and Mechanics Ashok D. Belegundu Professor of Mechanical Engineering *Signatures are on file in the Graduate School. iii ABSTRACT For an efficient full vehicle model simulation, a multi-body system (MBS) simulation is frequently adopted. By conducting the MBS simulations, the dynamic and steady-state responses of the sprung mass can be shortly predicted when the vehicle runs on an irregular road surface such as step curb or pothole. A multi-body vehicle model consists of a sprung mass, simplified tire models, and suspension system to connect them. For the simplified tire model, a rigid ring tire model is mostly used due to its efficiency. The rigid ring tire model consists of a rigid ring representing the tread and the belt, elastic sidewalls, and rigid rim. Several in-plane and out-of-plane parameters need to be determined through tire tests to represent a real pneumatic tire. Physical tire tests are costly and difficult in operations. -
MICHELIN TRUCK TIRE Technical BULLETIN May 19, 2017
MICHELIN TRUCK TIRE technical BULLETIN May 19, 2017 MICHELIN® X® INCITY™ Z SL 305/85R22.5 LRJ (MSPN 62156) MICHELIN® is introducing a new product for Urban Transit buses. The new MICHELIN® X® InCity™ Z SL tire 305/85R22.5 LRJ (MSPN 62156). The new MICHELIN® X® InCity™ Z SL tire is for Single Life (SL) usage only. The tires are marked “Do Not Retread” on both sidewalls; however, they may be regrooved to provide extended life in applications where regrooving is practiced. Additionally, Michelin recommends that Urban Transit buses fitted with 12R22.5 or 305/85R22.5 dimensions only Federal Transit Administration (FTA) testing use the MICHELIN® X® InCity™ Z or X InCity Z SL tires. procedures for buses assume a simulated average passenger weight of 150 pounds. The MICHELIN® X® InCity™ Z range of products is This regulatory standard may underestimate designed specifically to resist the demands of Urban the actual average combined weight of Transit use and provide the following distinctive individual passengers and their personal features: effects. The actual axle loads may exceed the • Reinforced sidewalls with scrub depth indicators Gross Axle Weight Rating of the vehicle and to manage the effects of abrasion from frequent the maximum load capacity of the tires. scrubbing on curbs. • Reinforced bead design to help maintain the Since tire inflation pressures should be set casing integrity from exposure to brake heat from according to actual loads seen at maximum frequent stopping. vehicle occupancy, MICHELIN recommends a • MICHELIN® Durable Technologies™ – patented cold inflation pressure of 120 psi (830 kPa) Matrix™ 3D sipe technology to provide extended for all 12R 22.5 LRH and 305/85R22.5 LRJ traction throughout the life of the tire tread. -
Tire Markings
(FM8) SEMCON JLR OWNER GUIDE VER 1.00 NAS LANGUAGE: english-NAS-en; MARQUE: jaguar; MODEL: XK L Tires TIRETires MARKINGS 1. P indicates that the tire is for passenger 8. US DOT Tire Identification Number (TIN). vehicle use. This begins with the letters DOT and 2. The width of the tire from sidewall edge to indicates that the tire meets all federal sidewall edge in millimetres. standards. The next 2 numbers or letters are the plant code where the tire was 3. The aspect ratio, also known as the profile, manufactured, the last 4 numbers are the gives the sidewall height as a percentage of date of manufacture. For example, if the the tread width. So, if the tread width is number was 3111, the tire was made in the 205 mm, and the aspect ratio is 50, the 31st week of 2011. The other numbers are sidewall height will be 102 mm. marketing codes used at the 4. R indicates that the tire is of Radial ply manufacturer’s discretion. This construction. information can be used to contact 5. The diameter of the wheel rim given in consumers if a tire defect requires a recall. inches. 9. M+S or M/S indicates that the tire has been 6. The load index for the tire. This index is not designed with some capability for mud and always shown. snow. 7. The speed rating denotes the maximum speed at which the tire should be used for extended periods. See 175, SPEED RATINGS. 174 (FM8) SEMCON JLR OWNER GUIDE VER 1.00 NAS LANGUAGE: english-NAS-en; MARQUE: jaguar; MODEL: XK R Tires 10. -
Tire Pressures
R Tires Do not exceed the maximum pressure stated Do not drive the vehicle with a leaking tire. on the sidewall of the tire. Even if the tire appears to be inflated, it could be dangerously under-inflated and will continue to deflate. Replace or contact an Avoid damaging the TPMS sensor when approved repairer. removing a tire from the wheel and fitting a tire to the wheel. All of the vehicle©s tires (including the spare) If the vehicle has been parked in strong should be checked regularly for damage, wear, sunlight, or used in high ambient and distortion. If you are in any doubt about the temperatures, do not reduce the tire condition of a tire, have it checked immediately pressures. Move the vehicle into the shade by a tire repair center or a Dealer/Authorized and allow the tires to cool before rechecking Repairer. the pressures. TIRE PRESSURES Under-inflation also reduces fuel efficiency and tire tread life, and may affect the vehicle's Never drive your vehicle if the tire pressures handling and stopping ability. are incorrect. Under-inflation causes excessive flexing and uneven tire wear. This can lead to sudden tire failure. Over-inflation causes harsh ride, uneven tire wear, and poor handling. Pressure checks should be carried out only when the tires are cold and the vehicle has been stationary for more than 3 hours. A hot tire, at or below the recommended cold inflation pressure, is dangerously under-inflated. A tire information label is located in the driver's All tire pressures, including the spare, should door opening, giving information specific to the be checked regularly using an accurate original wheel and tire equipment fitted to the pressure gauge, when the tires are cold. -
An Evaluation of Existing Tire Pressure Monitoring Systems This Publication Is Distributed by the U.S
US Department of Transportation National Highway Traffic Safety Administration DOT HS 809 297 July 2001 An Evaluation of Existing Tire Pressure Monitoring Systems This publication is distributed by the U.S. Department of Transportation, National Highway Traffic Safety Administration, in the interest of information exchange. The opinions, findings, and conclusions expressed in this publication are those of the author(s) and not necessarily those of the Department of Transportation or the National Highway Traffic Safety Administration. The United States Government assumes no liability for its contents or use thereof. If trade or manufacturers= names or products are mentioned, it is because they are considered essential to the object of the publication and should not be construed as an endorsement. The United States Government does not endorse products or manufacturers. Technical Report Documentation Page 1. Report No. 2. Government Accession No. 3. Recipient's Catalog No. DOT 809 297 4. Title and Subtitle 5. Report Date An Evaluation of Existing Tire Pressure Monitoring Systems July 2001 6. Author(s) 7. Performing Organization Code Paul Grygier, W. Riley Garrott, and Elizabeth N. Mazzae, National Highway Traffic Safety Administration 8. Performing Organization Report No. James D. MacIsaac Jr., Richard L. Hoover, Devin Elsasser, and Thomas A. Ranney, - Transportation Research Center (TRC) Inc. 9. Performing Organization Name and Address 10. Work Unit No. (TRAIS) National Highway Traffic Safety Administration Vehicle Research and Test Center 11. Contract or Grant No. P.O. Box B-37 East Liberty, OH 43319-0337 12. Sponsoring Agency Name and Address 13. Type of Report and Period Covered National Highway Traffic Safety Administration Technical report 400 Seventh Street, S.W. -
2019 Chrysler/Dodge/Jeep/Ram/Fiat/SRT
TABLE OF CONTENTS TIRE INFORMATION SUPPLEMENT ................3 BFGOODRICH TIRES ...........................27 BRIDGESTONE®-FIRESTONE® ................45 CONTINENTALTIRE ............................87 FALKEN TIRE CORPORATION ...................95 GENERALTIRE ...............................115 GOODYEAR DUNLOP TIRES ...................123 HANKOOKTIRES .............................139 KUMHOTIRES.................................145 MICHELIN ....................................159 NEXEN TIRE ..................................187 PIRELLITIRES.................................197 TOYOTIRES–LIMITEDWARRANTY ...........217 YOKOHAMATIRES—LIMITEDWARRANTY .....261 1 2 TIRE INFORMATION SUPPLEMENT TIRES TIRES TireSafetyInformation Tire safety information will cover aspects of the following information: TireMarkings,TireIdentificationNumbersȱǻ Ǽ,TireTerminology andDefi-nitions,TirePressures,andTireLoading. TireMarkings Tire Markings 1USDOTSafetyStandards Code(TIN) 2SizeDesignation 3ServiceDescription Śȱȯȱ¡ȱ śȱȯȱ¡ȱ Ŝȱȯȱ ǰȱȱȱ ȱ NOTE: • P(Passenger)—MetrictiresizingisbasedonUSdesignstandards. P-Metric tires have the letter “P” molded into the sidewall preceding the size designation. Example: P215/65R15 95H. • European — Metric tire sizing is based on European design standards. Tires designed to this standard have the tire size molded into the sidewall beginning with the section width. The letter ЉPЉ is absent from this tire size designation. Example: 215/65R15 96H. 4 TIRES • LT(LightTruck)—MetrictiresizingisbasedonUSdesignstandards. ThesizedesignationforLT-MetrictiresisthesameasforP-Metrictires -
RECREATIONAL VEHICLE TIRE and CARE GUIDE Table of Contents
RECREATIONAL VEHICLE TIRE AND CARE GUIDE TABLE OF CONTENTS Introduction to Goodyear RV Tires ...........................................................................................3 Why Choose Goodyear?................................................................................................................4 Four Great Tires To Keep You Rolling .......................................................................................4 The Big Four of RV Tire Care ........................................................................................................5 Tire Inflation ......................................................................................................................................5 When To Check Your RV or Trailer Tire Pressure ...................................................................5 How To Check Your Tire Pressure ...............................................................................................5 The Effects of Temperature and Atmospheric Pressure ....................................................6 How Much Air is Enough ..............................................................................................................6 Understanding Gross Vehicle Weight and Gross Vehicle Weight Ratings ..................6 Weighing Your Vehicle ...............................................................................................................6-9 Load/Inflation Information .................................................................................................. -
Aircraft Tire Care & Maintenance
Introduction Aircraft Tire Care & Maintenance 1 Revised – 1/20 Introduction The purpose of this manual is to help aircraft owners and maintenance personnel obtain optimum service from their bias and radial aircraft tires. The discussions contained in this part are designed not only to teach how to properly operate and maintain aircraft tires, but also to demonstrate why these techniques and procedures are necessary. Any information in this manual can be overridden by instructions from the tire or aircraft manufacturer. Aircraft operating conditions require a wide variety of tire sizes and constructions. The modern aircraft tire is a highly- engineered composite structure designed to carry heavy loads at high speeds in the smallest and lightest configuration practical. Tires are a multi-component item consisting of three major materials: steel, rubber and fabric. There are different types of fabric and rubber compounds in a tire construction, each with its own special properties designed to successfully complete the task assigned. Goodyear aircraft tire technology utilizes Computer Aided Design and Analysis, as well as the science of compounds and materials applications. Materials and finished tires are subjected to a variety of laboratory, dynamometer, and field evaluations to confirm performance objectives and obtain certification. The manufacturing process requires the precision assembly of tight-tolerance components and a curing process under carefully controlled time, temperature and pressure conditions. Quality assurance procedures help to ensure that individual components and finished tires meet specifications. The Goodyear Innovation Center and all Goodyear Aviation Tire new and retread tire plants are ISO 9001:2000 certified. NOTE: The procedures and standards included in this manual are intended to supplement the specific instructions issued by aircraft and wheel/rim manufacturers. -
Operator's Manual
Operator’s Manual 1 2 OPERATOR’S MANUAL SMARTIRE® TIRE PRESSURE MONITORING SYSTEM BY BENDIX CVS Thank you for purchasing the SmarTire® Tire Pressure Monitoring System (TPMS). With SmarTire® TPMS onboard, your vehicle is equipped with a wireless communication network allowing seamless integration of wireless sensing technology. The SmarTire® TPMS application is an advanced tire pressure monitoring system specifically designed for commercial vehicles. The system constantly monitors the pressure and temperature of each tire on your vehicle in order to provide real-time, on-demand tire status information and to warn the driver of a tire-related problem before it becomes dangerous. SMARTIRE® TPMS: • Extends tire life, • Reduces maintenance costs and time, • Maximizes fuel economy by ensuring tires are properly inflated, • Reduces vehicle downtime, and • Reduces accident risk caused by a tire blowout or tire fire. FEATURES OF SMARTIRE®: • Temperature compensated alert: know when your tires are at risk no matter how long you’ve been driving. • Real-time tire information while you drive. • Tire alerts provide instant visual and optional audible alert of a tire problem. • 3 types of alerts: Pressure Deviation Alert, Critical Low Pressure Alert, and High Temperature Alert. • Can be linked to the J1939 communication network for seamless vehicle integration. IMPORTANT NOTICE: PLEASE READ SmarTire® tire sensors can be broken when mounting and dismounting a tire unless specific instructions are followed. If tire work is done by a non-Bendix authorized facility, please let them know that a tire pressure monitoring system is installed on the vehicle before they remove a tire from a wheel. 3 WARNING! PLEASE READ AND FOLLOW THESE INSTRUCTIONS TO AVOID PERSONAL INJURY OR DEATH: When working on or around a vehicle, the following general precautions should be observed at all times. -
TPMS Glossary of Terms Courtesy of Continental Commercial Vehicles & Aftermarket
TPMS Glossary of Terms Courtesy of Continental Commercial Vehicles & Aftermarket Tire Pressure Monitoring System (TPMS) Tire pressure monitoring systems (TPMS) provide real safety and economic benefits for motorists. By helping drivers to maintain proper tire inflation, TPMS can help improve ride and handling, reduce stopping distances and the potential for hydroplaning, increase MPG and extend tire life. TPMS is designed to monitor the air pressure in a tire and send a warning to the vehicle’s on-board monitoring system when the pressure drops below a preset limit. In addition to the different types of systems and variety of components found in today’s TPMS-equipped vehicles, there are also a wide variety of terms used to describe various TPMS functions and service requirements. This glossary will help you to define and better understand these industry terms. Disclosure: While this TPMS glossary of terms may contain useful reference information for the global TPMS service marketplace, it is specifically intended for the USA, primarily due to legislation references. Glossary of TPMS Terms 2 Glossary of TPMS Terms Term Definition Activate See “LF low frequency trigger (wake) signal” definition. Adjustable valve stem A TPMS sensor valve stem that pivots to accommodate different wheel rim contours and the valve hole angle of the rim. Advanced system Typically a TPMS system with a dashboard display that shows each tire’s pressure by wheel location (left front, right front, etc.). Advanced TPMS systems may also display individual tire air temperatures. Aftermarket sensors Sensors that are available as replacements for the vehicle’s original equipment. Includes OE replacement sensors, cloneable sensors, configurable sensors, multi-application sensors and programmable sensors. -
RP 235A(T) Dft
Recommended Practice Proposed RP 235A (T) VMRS 017 GUIDELINES FOR TIRE INFLATION PRESSURE MAINTENANCE PREFACE The following Recommended Practice is subject to the Disclaimer at the front of TMC’s Recommended Maintenance Practices Manual. Users are urged to read the Disclaimer before considering adoption of any portion of this Recommended Practice. PURPOSE AND SCOPE The purpose of this Recommended Practice (RP) is to demonstrate the importance of inflation pressure and its effect on tires and tire service life. It addresses all aspects of the relationship between inflation pres- sure and tires, and provides equipment users with a practical guide for better understanding the issues Underinflated Correct Overinflated and costs that stem from failing to address this issue Inflation properly in everyday fleet operations. This RP ap- plies to Class 2-8 commercial vehicles in light-, Fig. 1 medium- and heavy-duty service. fatigue and break. Also, excessive heat will develop INTRODUCTION and deteriorate the tires. This RP offers comprehensive guidelines on proper tire inflation pressure maintenance. It covers air Overinflated tires are more vulnerable to tread sur- pressure and its relevance to: face cutting, impact breaks, punctures, and shock • footprint damage. Changes in inflation pressure affect the • irregular wear tire’s footprint, which is the area that contacts the • load road. (See Fig. 1.) • tire temperature • maintenance INFLATION PRESSURE AND IRREGULAR WEAR • sealants Both over and underinflation change a tire’s footprint, • steer axles affecting tire traction and leading to irregular wear • dual assemblies patterns. For example, medium truck tires rotate • equipment about 500 times for every mile travelled. In 100,000 • fuel miles, each part of the tread gets pressed against the • nitrogen pavement about 50 million times. -
Tire Operational and Sustainability Tradeoffs
UMTRI-2013-28 AUGUST 2013 TIRE OPERATIONAL A ND SUSTAINABILITY TRADEOFFS MARION G. POTTINGER TIRE OPERATIONAL AND SUSTAINABILITY TRADEOFFS Marion G. Pottinger The University of Michigan Transportation Research Institute Ann Arbor, Michigan 48109-2150 U.S.A. Report No. UMTRI-2013-28 August 2013 Technical Report Documentation Page 1. Report No. 2. Government Accession No. 3. Recipient’s Catalog No. UMTRI-2013-28 4. Title and Subtitle 5. Report Date Tire Operational and Sustainability Tradeoffs August 2013 6. Performing Organization Code 383818 7. Author(s) 8. Performing Organization Report No. Marion G. Pottinger UMTRI-2013-28 9. Performing Organization Name and Address 10. Work Unit no. (TRAIS) The University of Michigan Transportation Research Institute 11. Contract or Grant No. 2901 Baxter Road Ann Arbor, Michigan 48109-2150 U.S.A. 12. Sponsoring Agency Name and Address 13. Type of Report and Period Covered The University of Michigan Sustainable Worldwide Transportation 14. Sponsoring Agency Code 15. Supplementary Notes Information about Sustainable Worldwide Transportation is available at http://www.umich.edu/~umtriswt. 16. Abstract This report forecasts likely changes in passenger car and light truck fuel economy through 2025 as a result of projected tire evolution with respect to aspect ratio and design inflation pressure. Tire-material evolution over the last decade is expected to continue. Tire aspect ratios from 55 to 85 are examined, along with cold inflation pressures from 35 to 50 psi. The forecast fuel economy change is the primary factor considered in evaluating tire sustainability. The secondary factor considered is the change in raw material usage, which affects tire weight.