Metallurgy and Mineral Processing
Total Page:16
File Type:pdf, Size:1020Kb
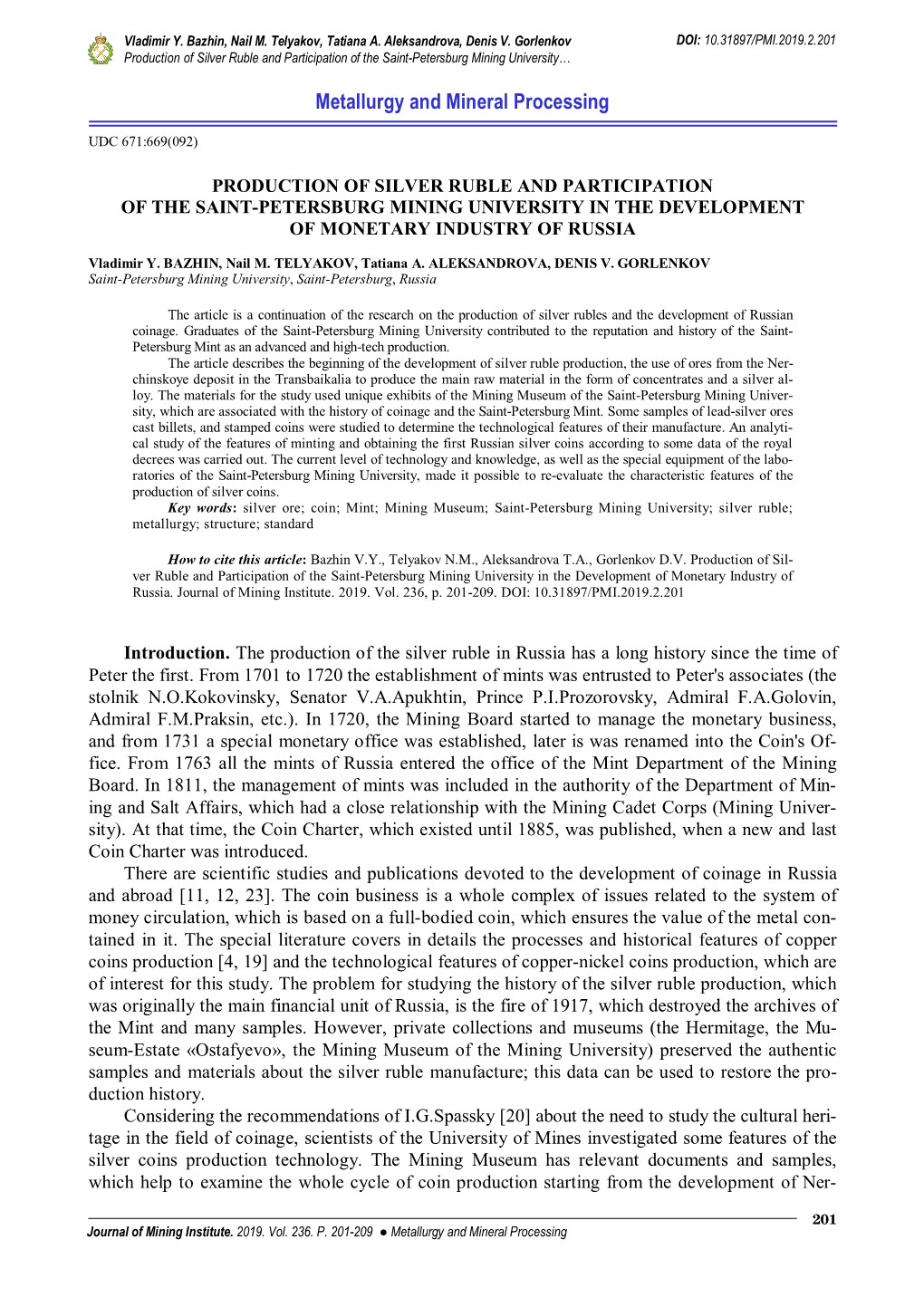
Load more
Recommended publications
-
The Monetary Legacy of the Soviet Union / Patrick Conway
ESSAYS IN INTERNATIONAL FINANCE ESSAYS IN INTERNATIONAL FINANCE are published by the International Finance Section of the Department of Economics of Princeton University. The Section sponsors this series of publications, but the opinions expressed are those of the authors. The Section welcomes the submission of manuscripts for publication in this and its other series. Please see the Notice to Contributors at the back of this Essay. The author of this Essay, Patrick Conway, is Professor of Economics at the University of North Carolina at Chapel Hill. He has written extensively on the subject of structural adjustment in developing and transitional economies, beginning with Economic Shocks and Structural Adjustment: Turkey after 1973 (1987) and continuing, most recently, with “An Atheoretic Evaluation of Success in Structural Adjustment” (1994a). Professor Conway has considerable experience with the economies of the former Soviet Union and has made research visits to each of the republics discussed in this Essay. PETER B. KENEN, Director International Finance Section INTERNATIONAL FINANCE SECTION EDITORIAL STAFF Peter B. Kenen, Director Margaret B. Riccardi, Editor Lillian Spais, Editorial Aide Lalitha H. Chandra, Subscriptions and Orders Library of Congress Cataloging-in-Publication Data Conway, Patrick J. Currency proliferation: the monetary legacy of the Soviet Union / Patrick Conway. p. cm. — (Essays in international finance, ISSN 0071-142X ; no. 197) Includes bibliographical references. ISBN 0-88165-104-4 (pbk.) : $8.00 1. Currency question—Former Soviet republics. 2. Monetary policy—Former Soviet republics. 3. Finance—Former Soviet republics. I. Title. II. Series. HG136.P7 no. 197 [HG1075] 332′.042 s—dc20 [332.4′947] 95-18713 CIP Copyright © 1995 by International Finance Section, Department of Economics, Princeton University. -
Russiske Mynter Russian Coins 1021-1024 Russiske MYNTER / Russian COINS
RUSSISKE MYNTER / ruSSIAN COINS Russiske mynter Russian coins 1021-1024 RUSSISKE MYNTER / ruSSIAN COINS RUSSISKE myntER/RUSSIAn coINS PETER I 1689-1725 1021 Rubel 1704. Red Mint Bitkin 797 1+ 30 000 Peter the Great (ruled 1682–1725) and the first decimal coinage The reign of Peter I (the Great) is generally regarded as a watershed in Russian history, noted for a programme of extensive military, civil and social reforms that transformed Russia from an isolated agricultural society into a major European power. Early in his career, Peter toured Europe (sometimes in disguise) and educated himself in Western culture and science, as well as naval and military techniques. On his return to Russia he set about ‘modernizing’ or ‘westernizing’ the country, as well as extending its boundaries through a number of military campaigns. In 1703, during the Great Northern War with Sweden, Peter captured land on the Baltic Sea, where he founded his new capital, St Petersburg. This modern city, built in Western style, was intended to become the centre of new Russia just as Moscow had been the centre of old. The monetary system of Russia also changed dramatically as part of Peter the Great’s extensive reforms. In 1700 the czar decreed a decimal coinage system for Russia – the first in history – with 100 kopeks equal to one rouble. The first (copper) kopek and (silver) rouble coins under the new system appeared in 1704. As well as introducing a decimal coinage, Peter I also banned the use of foreign coins in Russia. Moreover, in order to ensure a standard size and weight for the new Russian coins, the czar ordered that coins should no longer be minted by hand, but should be machine-struck. -
Russian Ruble, Rub
As of March 16th 2015 RUSSIA - RUSSIAN RUBLE, RUB Country: Russia Currency: Russian Ruble (RUB) Phonetic Spelling: {ru:bil} Country Overview Abbreviation: RUB FOREIGN EXCHANGE Controlled by the Central Bank of Russia (http://www.cbr.ru/eng/) The RUB continues Etymology to be affected by the oil price shock, escalating capital outflows, and damaging The origin of the word “rouble” is derived from the economic sanctions. The Russian ruble (RUB) continued to extend its losses and Russian verb руби́ть (rubit’), which means “to chop, cut, suffered its largest one-day decline on Dec 1st against the US dollar (USD) — less than to hack.” Historically, “ruble” was a piece of a certain a month after allowing the RUB to float freely. The RUB’s slide reflects the fact that weight chopped off a silver oblong block, hence the Russia is among the most exposed to falling oil prices and is particularly vulnerable to name. Another version of the word’s origin comes from the Russian noun рубец, rubets, which translates OPEC’s recent decision to maintain its supply target of 30-million-barrels per day. This to the seam that is left around the coin after casting, combined with the adverse impact of Western sanctions has contributed to the RUB’s therefore, the word ruble means “a cast with a seam” nearly 40% depreciation vis-à-vis the USD since the start of 2014. In this context, the Russian Central Bank will likely hike interest rates at its next meeting on December In English, both the spellings “ruble” and “rouble” are 11th. -
Auction 26 | September 15-17, 2016 | Session D
World Coins Session D Begins on Friday, September 16, 2016 at 14:00 PDT World Coins Europe (continued) 1232. GREAT BRITAIN: Commonwealth and Protectorate, 1649-1660, AR crown, 1658/7, KM-D207, Dav-3773, ESC-240, Spink-3226, Oliver Cromwell Protector issue, original Thomas Simon strike, a couple small reverse rim bumps, one-year type, VF, S $2,000 - 2,200 1227. GIBRALTAR: AE 2 quarts (9.08g), 1802, KM-Tn2.2, payable at R. Keeling, EF-AU $120 - 160 1233. GREAT BRITAIN: Commonwealth and Protectorate, 1649-1660, AE medal, 1658, Eimer-203, 38mm, death medal of Oliver Cromwell in silvered bronze, draped bust left with OLIVARIUS CROMWELL. around and I.DASSIER.F. at bottom / 1228. GIBRALTAR: AE quarto (4.41g), 1813, KM-Tn5, four genii tending monument with ANGLIAE. SCOL ET HIB. payable at Richard Cattons, Goldsmith, EF $120 - 160 PROTECTOR inscribed and NAT. 3. APRIL. 1603. MORT. 3. SEPT. 1658. in exergue, struck on cast planchet, part of Dassier’s Kings and Queens of England series, F-VF $75 - 100 1229. GIBRALTAR: AE 2 quartos (8.34g), 1820, KM-Tn9, payable at James Spittle’s, choice EF-AU $150 - 200 1234. GREAT BRITAIN: Charles II, 1660-1685, AR crown, 1662, KM-417.2, Dav-3774var, ESC-340, Spink-3350B, scarcer variety with striped cloak, central obverse a bit softly struck, old-time toning, VF $500 - 600 1230. GREAT BRITAIN: Elizabeth I, 1558-1603, AR shilling, S-2555, 2nd series, mintmark cross-crosslet (1560-61), VF $80 - 100 1235. GREAT BRITAIN: Anne, 1702-1714, AR ½ crown, 1745/3, KM-584.3, Spink-3695, LIMA under bust, F-VF $125 - 175 1231. -
A Case Study of a Currency Crisis: the Russian Default of 1998
agents attempting to alter their portfolio by buying A Case Study of a another currency with the currency of country A.2 This might occur because investors fear that the Currency Crisis: The government will finance its high prospective deficit through seigniorage (printing money) or attempt to Russian Default of 1998 reduce its nonindexed debt (debt indexed to neither another currency nor inflation) through devaluation. Abbigail J. Chiodo and Michael T. Owyang A devaluation occurs when there is market pres- sure to increase the exchange rate (as measured by currency crisis can be defined as a specula- domestic currency over foreign currency) because tive attack on a country’s currency that can the country either cannot or will not bear the cost A result in a forced devaluation and possible of supporting its currency. In order to maintain a debt default. One example of a currency crisis lower exchange rate peg, the central bank must buy occurred in Russia in 1998 and led to the devaluation up its currency with foreign reserves. If the central of the ruble and the default on public and private bank’s foreign reserves are depleted, the government debt.1 Currency crises such as Russia’s are often must allow the exchange rate to float up—a devalu- thought to emerge from a variety of economic condi- ation of the currency. This causes domestic goods tions, such as large deficits and low foreign reserves. and services to become cheaper relative to foreign They sometimes appear to be triggered by similar goods and services. The devaluation associated with crises nearby, although the spillover from these con- a successful speculative attack can cause a decrease tagious crises does not infect all neighboring econ- in output, possible inflation, and a disruption in omies—only those vulnerable to a crisis themselves. -
The August 2016 ANA Auction Ancient & World Coins Internet Only
The August 2016 ANA Auction Ancient & World Coins Internet Only August 15, 2016 Anaheim, CA An Official Auctioneer of the ANA World’s Fair of Money Stack’s Bowers Galleries Upcoming Auction Schedule Coins and Currency Date Auction Consignment Deadline August 15-17, 2016 Stack’s Bowers and Ponterio – Chinese & Asian Coins & Banknotes Request a Catalog Hong Kong Auction of Chinese and Asian Coins & Currency Hong Kong September 7, 2016 Collectors Choice Online Auction – U.S. Coins August 24, 2016 StacksBowers.com October 5, 2016 Collectors Choice Online Auction – U.S. Coins September 21, 2016 StacksBowers.com November 2-4, 2016 Stack’s Bowers Galleries – U.S. Coins & Currency September 13, 2016 Ocial Auction of the Whitman Coin & Collectibles Baltimore Expo Baltimore, MD December 7, 2016 Collectors Choice Online Auction – U.S. Coins November 23, 2016 StacksBowers.com January 4, 2017 Collectors Choice Online Auction – U.S. Coins December 21, 2016 StacksBowers.com January 6-7, 2017 Stack’s Bowers Galleries – World Coins & Paper Money November 11, 2016 An Ocial Auction of the NYINC New York, NY March 29-31, 2017 Stack’s Bowers Galleries – U.S. Coins & Currency January 31, 2017 Ocial Auction of the Whitman Coin & Collectibles Baltimore Expo Baltimore, MD April 3-5, 2017 Stack’s Bowers and Ponterio – Chinese & Asian Coins & Banknotes January 30, 2017 Hong Kong Auction of Chinese and Asian Coins & Currency Hong Kong Spring 2017 Stack’s Bowers Galleries – U.S. Coins Not Applicable e D. Brent Pogue Collection, Part V Spring 2017 Stack’s Bowers Galleries – U.S. Coins TBD Rarities Auction (Special Terms Apply) June 21-24, 2017 Stack’s Bowers Galleries – U.S. -
Belarus Country Report BTI 2016
BTI 2016 | Belarus Country Report Status Index 1-10 4.27 # 99 of 129 Political Transformation 1-10 3.93 # 91 of 129 Economic Transformation 1-10 4.61 # 90 of 129 Management Index 1-10 3.02 # 115 of 129 scale score rank trend This report is part of the Bertelsmann Stiftung’s Transformation Index (BTI) 2016. It covers the period from 1 February 2013 to 31 January 2015. The BTI assesses the transformation toward democracy and a market economy as well as the quality of political management in 129 countries. More on the BTI at http://www.bti-project.org. Please cite as follows: Bertelsmann Stiftung, BTI 2016 — Belarus Country Report. Gütersloh: Bertelsmann Stiftung, 2016. This work is licensed under a Creative Commons Attribution 4.0 International License. BTI 2016 | Belarus 2 Key Indicators Population M 9.5 HDI 0.786 GDP p.c., PPP $ 18184.9 Pop. growth1 % p.a. 0.0 HDI rank of 187 53 Gini Index 26.0 Life expectancy years 72.5 UN Education Index 0.820 Poverty3 % 0.0 Urban population % 76.3 Gender inequality2 0.152 Aid per capita $ 11.1 Sources (as of October 2015): The World Bank, World Development Indicators 2015 | UNDP, Human Development Report 2014. Footnotes: (1) Average annual growth rate. (2) Gender Inequality Index (GII). (3) Percentage of population living on less than $3.10 a day at 2011 international prices. Executive Summary Summer 2014 marked the 20th anniversary of Aliaksandr Lukashenka’s election as the first, and so far only, president of the Republic of Belarus. -
Currencies of the World
The World Trade Press Guide to Currencies of the World Currency, Sub-Currency & Symbol Tables by Country, Currency, ISO Alpha Code, and ISO Numeric Code € € € € ¥ ¥ ¥ ¥ $ $ $ $ £ £ £ £ Professional Industry Report 2 World Trade Press Currencies and Sub-Currencies Guide to Currencies and Sub-Currencies of the World of the World World Trade Press Ta b l e o f C o n t e n t s 800 Lindberg Lane, Suite 190 Petaluma, California 94952 USA Tel: +1 (707) 778-1124 x 3 Introduction . 3 Fax: +1 (707) 778-1329 Currencies of the World www.WorldTradePress.com BY COUNTRY . 4 [email protected] Currencies of the World Copyright Notice BY CURRENCY . 12 World Trade Press Guide to Currencies and Sub-Currencies Currencies of the World of the World © Copyright 2000-2008 by World Trade Press. BY ISO ALPHA CODE . 20 All Rights Reserved. Reproduction or translation of any part of this work without the express written permission of the Currencies of the World copyright holder is unlawful. Requests for permissions and/or BY ISO NUMERIC CODE . 28 translation or electronic rights should be addressed to “Pub- lisher” at the above address. Additional Copyright Notice(s) All illustrations in this guide were custom developed by, and are proprietary to, World Trade Press. World Trade Press Web URLs www.WorldTradePress.com (main Website: world-class books, maps, reports, and e-con- tent for international trade and logistics) www.BestCountryReports.com (world’s most comprehensive downloadable reports on cul- ture, communications, travel, business, trade, marketing, -
Investment Guide. Belarus 2020
Invest in Belarus Guidebook Investment opportunities, legal and economic environment PREPARED BY In today’s dynamically changing world, each may reckon on when considering prospects of opening and every state’s successin promotion of foreign business in our country. direct investment is largely determined by its ability National Agency of Investment and Privatization to not only perceive present, but also envisage serves as a reliable and competent partner for future needs of businesses and, consequently, act businesses through all stages of investment projects proactively while creating a favorable investment realization in Belarus, employing its long-time climate. experience and expertise while rendering free-of-charge Drawing on its key competitive advantages – professional consultative, communication and unique location, considerable human, industrial and organizational assistance to investors. logistical potential, and forward-looking legislation – This edition encompasses the most up-to-date Belarus today continues to consistently enhance information on the top priority sectors for FDI, conditions for doing business, adequately adjusting opportunities available within various preferential to new realities and successfully implementing regimes, judicial aspects of investments, Belarus’s digital transformation of the national economy. primary avenues of multi-faceted international Stable domestic political situation, high level of cooperation and even more. public security, coherent and constantly improving I am confident, inside You -
BELARUSIAN RUBLE BEJIOPYCCKH:Q Pybjih
On peut d'ores et deja parler du succes des strategies de developpement choisies par differents pays en transition. Par rapport aux pays "reformateurs'', le Belarus a perdu en investissements, en competitivite et en revenus. Les courbes des indices de liberte economique et politique et des indices de rid:formes permettent de constater !'accumulation du retard a cause de reformes ajournees (le Belarus occupe la 151<me place parmi les 161 pays dans "Les indices de liberte economique (2003)"). A.A. 5aiiauH 6r3Y (M~HCK) BELARUSIAN RUBLE BEJIOPYCCKH:Q PYBJih ~eJibiO pa60Thl SlBJISleTCSl llOllhlTK8 Onpep;eJI'HTh p;aJibHeHUI.H.e nep COCKTlflJhi 6eJiopyccKOH BaJIIOTbl. ~Jia aToro npocJie)Kea nyTb «3aH'lH Ka• C MOMeHTa ero BXO)f(,ll;eH'HSl B o6pB.IQCIUIC, npowe,Amero ,ABC ,AeBO MKH~HH, ll.O cerop;asrwaero p;an. Py6Jib xapaKTepa3yeTcH 3KOHOMH <IeCKOH CTa6HJibHOCTbiO Ba.D;HOHaJif>HOH BaJI10Thi B HeHCHOCThiO /l,aJih aefd:mefd: ee cyp;b6hl. Ten years have passed since the Belarus Supreme Court ruled to authorize the Belarusian ruble, issued by the National Bank, as the only legal tender. In the early 1990s, the Russian monetary authorities encouraged the former Soviet Republics to introduce their own currencies. In 1992, Russia introduced its own currency and stopped supplying ex-Soviet Republics with cash. Therefore, Belarus and Ukraine had to issue their own currencies. The Soviet ruble was circulating with the Belarusian ruble. Their correlations were 1 to 10. In other words, one Belarusian ruble cost ten Soviet rubles and common people, as well as cashiers at the shops, become confused with switching from the Soviet to Belarusian rubles. -
Dollarization in Ukraine: 1991 to the Present
Dollarization in Ukraine: 1991 to the Present By Elisabeth S. Curtis, Roy Gardner and Christopher J. Waller* An economy is dollarized when a foreign currency performs the major functions of money alongside a domestic currency. Like many emerging market economies, the Ukrainian economy is dollarized – in fact, its entire period of independence has been marked by dollarization. What makes this situation more striking is that, while Ukraine has witnessed two very different monetary regimes since independence, the extent of dollarization appears to be largely unchanged across the two regimes. We offer an explanation of this phenomenon, highlighting the significant role the shadow economy plays in Ukraine, and we discuss implications for dollarization or euroization in Ukraine’s future. (JEL) An economy is dollarized when a foreign currency (often the US dollar) performs the major functions of money alongside a domestic currency. Like many emerging market economies throughout the world, the economy of Ukraine is dollarized (Antinolfi and Keister, 2001). Indeed, the entire period of independence, starting in August 1991, has been marked by a dollarized Ukrainian economy. What makes this situation even more striking is that, while Ukraine has witnessed two very different monetary regimes * Curtis: Drexel University, Philadelphia, PA 19104; Gardner: Indiana University, Bloomington, IN 47405; Waller: University of Kentucky, Lexington, KY, 40506-0034. Prepared for presentation at the 35th Annual Conference of the Money, Macro and Finance Research Group, September 10-12, 2003, Cambridge, UK. We wish to thank Olexandra Betliy and Olga Manziy for their research assistance. All remaining errors are the responsibility of the authors. Work on this paper commenced while the authors were affiliated with the Economics Education and Research Consortium, National University “Kyiv-Mohyla Academy” in Kyiv, Ukraine. -
Zbwleibniz-Informationszentrum
A Service of Leibniz-Informationszentrum econstor Wirtschaft Leibniz Information Centre Make Your Publications Visible. zbw for Economics Orlowski, Lucjan T. Working Paper — Digitized Version The disintegration of the ruble zone: Driving forces and proposals for policy change Kiel Working Paper, No. 585 Provided in Cooperation with: Kiel Institute for the World Economy (IfW) Suggested Citation: Orlowski, Lucjan T. (1993) : The disintegration of the ruble zone: Driving forces and proposals for policy change, Kiel Working Paper, No. 585, Kiel Institute of World Economics (IfW), Kiel This Version is available at: http://hdl.handle.net/10419/46995 Standard-Nutzungsbedingungen: Terms of use: Die Dokumente auf EconStor dürfen zu eigenen wissenschaftlichen Documents in EconStor may be saved and copied for your Zwecken und zum Privatgebrauch gespeichert und kopiert werden. personal and scholarly purposes. Sie dürfen die Dokumente nicht für öffentliche oder kommerzielle You are not to copy documents for public or commercial Zwecke vervielfältigen, öffentlich ausstellen, öffentlich zugänglich purposes, to exhibit the documents publicly, to make them machen, vertreiben oder anderweitig nutzen. publicly available on the internet, or to distribute or otherwise use the documents in public. Sofern die Verfasser die Dokumente unter Open-Content-Lizenzen (insbesondere CC-Lizenzen) zur Verfügung gestellt haben sollten, If the documents have been made available under an Open gelten abweichend von diesen Nutzungsbedingungen die in der dort Content Licence (especially Creative Commons Licences), you genannten Lizenz gewährten Nutzungsrechte. may exercise further usage rights as specified in the indicated licence. www.econstor.eu KielerArbeitspapiere Kiel Working Papers Kiel Working Paper No. 585 The Disintegration of the Ruble Zone: Driving Forces and Proposals for Policy Change by Lucjan T.