The Abrasiveness of Sheer Overlay Fabrics Used in Textile Conservation
Total Page:16
File Type:pdf, Size:1020Kb
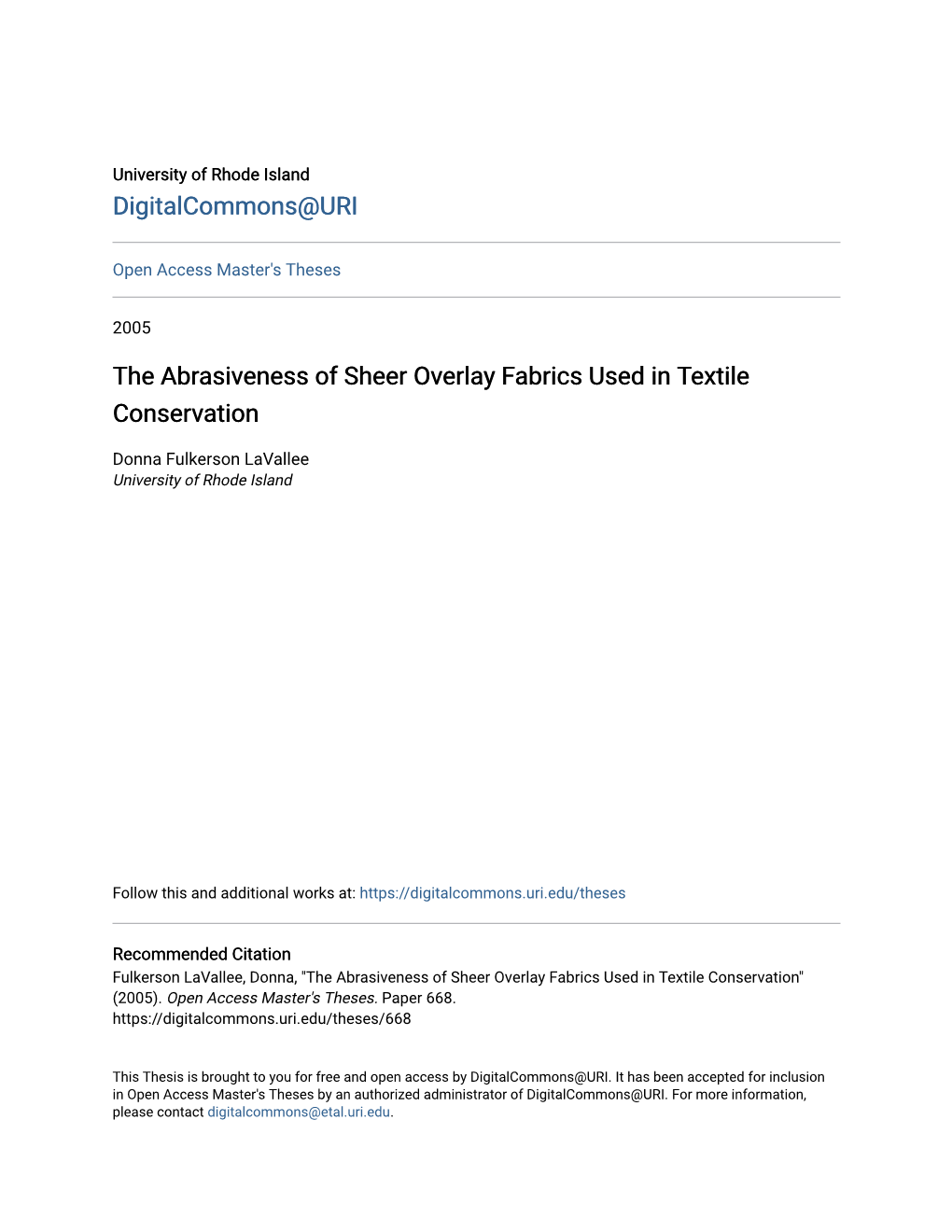
Load more
Recommended publications
-
Clothing of Kansas Women, 1854-1870
CLOTHING OF KANSAS WOMEN 1854 - 1870 by BARBARA M. FARGO B. A., Washburn University, 1956 A MASTER'S THESIS submitted in partial fulfillment of the requirements for the degree MASTER OF SCIENCE Department of Clothing, Textiles and Interior Design KANSAS STATE UNIVERSITY Manhattan, Kansas 1969 )ved by Major Professor ACKNOWLEDGMENTS The author wishes to express sincere appreciation to her adviser, Dr. Jessie A. Warden, for her assistance and guidance during the writing of this thesis. Grateful acknowledgment also is expressed to Dr. Dorothy Harrison and Mrs. Helen Brockman, members of the thesis committee. The author is indebted to the staff of the Kansas State Historical Society for their assistance. TABLE OP CONTENTS PAGE ACKNOWLEDGMENT ii INTRODUCTION AND PROCEDURE 1 REVIEW OF LITERATURE 3 CLOTHING OF KANSAS WOMEN 1854 - 1870 12 Wardrobe planning 17 Fabric used and produced in the pioneer homes 18 Style and fashion 21 Full petticoats 22 Bonnets 25 Innovations in acquisition of clothing 31 Laundry procedures 35 Overcoming obstacles to fashion 40 Fashions from 1856 44 Clothing for special occasions 59 Bridal clothes 66 SUMMARY AND CONCLUSIONS 72 REFERENCES 74 LIST OF PLATES PLATE PAGE 1. Bloomer dress 15 2. Pioneer woman and child's dress 24 3. Slat bonnet 30 4. Interior of a sod house 33 5. Children's clothing 37 6. A fashionable dress of 1858 42 7. Typical dress of the 1860's 47 8. Black silk dress 50 9. Cape and bonnet worn during the 1860's 53 10. Shawls 55 11. Interior of a home of the late 1860's 58 12. -
“Al-Tally” Ascension Journey from an Egyptian Folk Art to International Fashion Trend
مجمة العمارة والفنون العدد العاشر “Al-tally” ascension journey from an Egyptian folk art to international fashion trend Dr. Noha Fawzy Abdel Wahab Lecturer at fashion department -The Higher Institute of Applied Arts Introduction: Tally is a netting fabric embroidered with metal. The embroidery is done by threading wide needles with flat strips of metal about 1/8” wide. The metal may be nickel silver, copper or brass. The netting is made of cotton or linen. The fabric is also called tulle-bi-telli. The patterns formed by this metal embroidery include geometric figures as well as plants, birds, people and camels. Tally has been made in the Asyut region of Upper Egypt since the late 19th century, although the concept of metal embroidery dates to ancient Egypt, as well as other areas of the Middle East, Asia, India and Europe. A very sheer fabric is shown in Ancient Egyptian tomb paintings. The fabric was first imported to the U.S. for the 1893 Chicago. The geometric motifs were well suited to the Art Deco style of the time. Tally is generally black, white or ecru. It is found most often in the form of a shawl, but also seen in small squares, large pieces used as bed canopies and even traditional Egyptian dresses. Tally shawls were made into garments by purchasers, particularly during the 1920s. ملخص البحث: التمي ىو نوع من انواع االتطريز عمى اقمشة منسوجة ويتم ىذا النوع من التطريز عن طريق لضم ابر عريضة بخيوط معدنية مسطحة بسمك 1/8" تصنع ىذه الخيوط من النيكل او الفضة او النحاس.واﻻقمشة المستخدمة في صناعة التمي تكون مصنوعة اما من القطن او الكتان. -
Curtains and Draperies
Extension Bulletin 264 June 1951 BULLErJN HU()fvt liBRARY, Uf\WERC:ITY Fi>.P.M Selecting and Making CURTAINS AND DRAPERIES planning ideas buying guides construction aids Jfelen Jf. )Uatfteis WitcH Vou Select eurtnifiS and Vraperies ODAY'S homemaker has a world of new ideas and new prod T ucts to choose from when she plans window treatments for her home. She finds tremendous stress placed on the number, size, shape, and placement of windows in rooms in order that they may serve a number of purposes. Among these are, of course, the basic functions of windows-light, air, and vision. In addition windows often are the focal point, or gathering place for people in a room. All these points must be considered when planning windows and window decor. Whatever your light, air, vision, or by the store display of suggested room activity problems, remember that good settings. window treatment will be restful, it In addition, successful shopping calls will harmonize with the room, and lend for accurate information about your ·distinction to the furnishings used room requirements. You supply this by there. This means that good window carrying with you a sketch of your treatment will take its place as a sat room, preferably with wall and floor isfying part of the room furnishings and space indicated in %-inch scale. will also allow flowers, books,' works Salespeople count on this when they of art, and hobby interests of the family prepare merchandise for your selec to accent the character of furnishings tion. They must know about the archi in the room. -
Specialized Sewing Machine Operator
PARTICIPANT HANDBOOK Language: Apparel English Specialized Sewing Machine Operator Fruits and VegetablesSpecialized Processing Sewing Machine Operator SPECIALIZED SEWING MACHINE OPERATOR औ फल और ल र और र र ल फल और , और र फल और फ र र र र औ फल , और ल र , और , फ र, और फ ल - फल , र , र , र और ल ___________________________________________________________________________ ल ___ 1 1 फल फ र र और ल ल र र र और र र और और र र 12 Fruits and VegetablesSpecialized Processing Sewing Machine Operator Table of Contents Sr. No. Chapter Name Page No. 1. Introductio t Stitchi pparel Sector 4-13 2. Carry t fferent ypes of titches usin pecializ 14-108 Sewin achine 3. Different ypes f titches i pecialize ewi 109-167 machine 4. Achiev uality i ewi Work 168-218 5. Maintai Work re, Tools n Machines 219-244 औ 6. Maintai Healthy, afety a ecurity t Workplace 245-281 फल और ल र और र र ल फल और , और र फल और फ र र र र औ फल , और ल र , और , फ र, और फ ल - फल , र , र , र और ल ___________________________________________________________________________ ल ___ 2 2 फल फ र र और ल ल र र र और र र और और र र 12 Fruits and VegetablesSpecialized Processing Sewing Machine Operator Chapter 1 Introduction to Stitching and Apparel Sector औ फल और ल र और र र ल फल और , और र फल और फ र र र र औ फल , और ल र , और , फ र, और फ ल - फल , र , र , र और ल ___________________________________________________________________________ ल ___ 3 3 फल फ र र और ल ल र र र और र र और और र र 12 Fruits and VegetablesSpecialized Processing Sewing Machine Operator Learning Outcome: After attendin he ession, trainees oul be able o: Understa th titchin an pparel ndustry n ndi Lear about h different oles f ewi achin perator Pre Session Activity This ctivity he form f ―Flash Card‖ session. -
House Dresses
L'iJA1 HJ - r a ,iwfw; . t. ,. mmmmmmmtms ' i ,1 ""."' . .,1.., j rtriiMn lis .u'.. 77ie Stere C7e5 Mjm .isriwww V7'v.tiiiz T Daily at 5 k M. Extra Trousers, $9.75 CLOTHIER double anniversary price. Smi STRAWBR1DGE & Werth this w will be the first day of our summer Suits of fine-twi- ll serge, with two pairs of roey shopping schedule. Beginning And until further notice the Stere will open at 9.00 M. and will close 6 P. M. dally. Sale A. at Anniversary years special at $1.25. H Incidentally the morning hours are the best Strawbrldee fc Clothier Second Floer, Filbert Street, Eatt K for' shopping, as they are the coolest. Thursday i: Announcements for Tomorrow w MBM m ' ' New Summer Frecks Much Wi These Wonder-Value-s in Women's. Coats and Capes Under Price in the Sale Canten Crepe Frecks, $32.50 Draped, plaited and straight-lin- e models, $15.00 $18.00 beaded and embroidered. Navy blue, black, Serges and wool veleurs. Tan Belivia weaves, wool veleurs beaver, gray, rust and white. and medium blue in Coats; tan, and tan cloaking, in loose-lin- e navy blue and black in Capes. Ceat3.. Capes of wool velour Fine Cotten Frecks, $17.50 Beautifully tailored and lined and twills nearly all lined Embroidered Dotted Swiss in navy blue, throughout. throughout. Copenhagen blue, brown, orchid and green. Im- 3& Strawbrldte Clothier Second Floer. Centre ported ginghams in blue, red, green and orchid trimmed in white. Dimities and Ginghams, $15 Dimity and fine ginghams, in tangerine, black, Misses' Dresses Under Price lavender and green. -
Headwear How Do YOU Get Ahead? the TRICK to GETTING Ahead in TODAY’S VAST SEA of RETAIL IS to CAST a WIDE NET in ORDER to GATHER up ALL CUSTOMERS WHO ENTER YOUR SHOP
Headwear How do YOU get Ahead? THE TRICK TO GETTING Ahead IN TODAY’S VAST SEA OF RETAIL IS TO CAST A WIDE NET IN ORDER TO GATHER UP ALL CUSTOMERS WHO ENTER YOUR SHOP. OUR ALTERNATIVE GRAPHICS AND KNACK FOR PAIRING UP THE RIGHT ORNAMENTATION TECHNIQUE FOR EACH PIECE, SATISFIES CUSTOMERS OF ALL AGES AND TASTES. BAIT YOUR SHOPPERS WITH Ahead’s GREAT STYLING, MODERN FABRICS, AND ON TREND COLORS TO KEEP THOSE DOLLARS FROM SWIMMING AWAY. Ahead HAS BEEN SUCCESSFULLY FISHING IN THESE WATERS FOR OVER 20 YEARS... join us! Felt Appliqué Chain Stitch Direct Embroidery Printed Rubber Appliqué Bounce Stitch Printed Vintage Label Twill Patch Vintage Label w/Embroidery What drives Us to be Ahead? New Bedford Heritage: It’s in the Water & Soil! Farmers will tell you that the best tasting crops owe it to the water and soil. They discount, or perhaps don’t even realize, the know-how and work ethic that they inherited from those before them. The crew at Ahead is very similar. Hard work comes naturally to our staff as a result of the industries that their New Bedford ancestors pioneered. Today, the city’s thriving arts community helps to drive creativity within Ahead’s walls. In the 1800s, whale oil was After whaling, Textile mills After The Great Depression, used for lamps, candles, & boomed, & skilled workers 2/3s of New Bedford’s mills household items. The tireless from around the world mi- closed. Decades later, artists sailors of New Bedford’s grated to the area. By 1905, began gravitating to the whaling ships landed enough about 80% of the residents impoverished city in search Leviathans to make the city had arrived from Portugal, of inexpensive lofts. -
3D Weaving Process : Development of Near Net Shape Preforms and Verification of Mechanical Properties
Vol. 34, No. 2, 96-100 (2021) DOI: http://dx.doi.org/10.7234/composres.2021.34.2.096 ISSN 2288-2103(Print), ISSN 2288-2111(Online) Paper 3D Weaving Process : Development of Near Net Shape Preforms and Verification of Mechanical Properties Vinzenz Klapper*,**,***, Kwang-Hoon Jo*, Joon-Hyung Byun*, Jung-Il Song**, Chee-Ryong Joe**† ABSTRACT: The lightweight industry continuously demands reliable near-net-shape fabrication where the preform just out-of-machine is close to the final shape. In this study, different half-finished preforms are made π-beams. Then the preforms are unfolded to make a 3D shape with integrated structure of fibers, providing easier handling in the further processing of composites. Several 3D textile preforms are made using weaving technique and are examined after resin infusion for mechanical properties such as inter-laminar shear strength, compressive strength and tensile strength. Considering that the time and labor are important parameters in modern production, 3D weaving technique reduces the manufacturing steps and therefore the costs, such as hand-lay up of textile layers, cutting, and converting into preform shape. Hence this 3D weaving technique offers many possibilities for new applications with efficient composite production. Key Words: 3D weaving, weave pattern, π-beam, T-joint 1. INTRODUCTION connection in position and length by the warp yarn is offering many possibilities to create 3D textile preforms. With 3D To reduce the product weight and material cost, the light- weaving techniques, many integrated structural solutions such weight industry is continuously demanding a preform that is as different beam types and stiffeners can be produced [4]. -
An Empirical Assessment of the Relationship Of
An International Multidisciplinary Journal, Ethiopia Vol. 7 (2), Serial No. 29, April, 2013:350-370 ISSN 1994-9057 (Print) ISSN 2070--0083 (Online) DOI: http://dx.doi.org/10.4314/afrrev.7i2.22 Adire in South-western Nigeria: Geography of the Centres Areo, Margaret Olugbemisola- Department of Fine and Applied Arts, Ladoke Akintola University of Technology, P. M. B 4000, Ogbomoso, Nigeria E-mail; [email protected] & Kalilu, Razaq Olatunde Rom - Department of Fine and Applied Arts, Ladoke Akintola University of Technology, P. M. B 4000, Ogbomoso, Nigeria E-mail; [email protected] Abstract Adire, the patterned dyed cloth is extant and is practiced in almost all Yoruba towns in Southwestern Nigeria. The art tradition is however preponderant in a few Yoruba towns to the extent that the names of these towns are traditionally inseparable with the Adire art tradition. With Western education, introduction of foreign religions, influence from other cultures, technique and technology, there is a shift in the producers of Adire, the training pattern, and even an evolution in the production centre. While Western education resulted in a shift from the hitherto traditional Copyright© IAARR 2013: www.afrrevjo.net 350 Indexed African Journals Online: www.ajol.info Vol. 7 (2) Serial No. 29, April, 2013 Pp.350-370 apprenticeship method to the study of the art in schools, unemployment gave birth to the introduction of training drives by government and non governmental parastatals. This study, a field research, is an appraisal of the factors that contributed to the vibrancy of the traditionally renowned centres, and how the newly evolved centres have in contemporary times contributed to the sustainability of the Adire art tradition. -
Custom Digital Print
Digital Print Custom Capabilities What Will You Design? From digitally printed wallcovering, upholstery, 1. CHOOSE A DESIGN drapery and panel fabrics, our Digital Print Have an original design you want to see come to life? We can Custom Capabilities program has you covered. help make it a reality. Need some inspiration? Many of our KnollTextiles patterns can be translated to digital print designs Create truly one-of-a-kind textiles, combining for different applications or we can create a unique, ground-up modern technology with artful design, with our design for you. simple and cost-effective process. 2. SELECT A BASECLOTH Plus, with lower minimums and shorter lead We have a wide range of basecloths to choose from including times, customization has never been easier. a selection of proprietary textiles from our standard line. If you don’t see something that suits your needs, we can source a Questions? solution for you. Please contact your KnollTextiles Sales Representative for more information about 3. MAKE A STATEMENT Digital Print Custom Capabilities. Digital printing is the perfect solution for adding a touch of original design to your project, while balancing the challenges of budget and time. Let us help realize your vision. Digital Print Custom Capabilities Below are examples of one-of-a-kind digitally printed projects designed in collaboration with the KnollTextiles Customs team. From digitally printed wallcovering, upholstery, drapery and panel fabrics, our Digital Print Custom Capabilities program has you covered. For additional information, please contact your local Sales Representative. April 2021 | ©2021 KnollTextiles, Inc. All rights reserved. knolltextiles.com Digital Print Custom Capabilities Basecloth Options Choose from 16 basecloth options for upholstery, drapery, panel, wallcovering and pillow projects. -
YOUNIQUE TOUCH Pressed Powder Foundation
Fact Sheet YOUNIQUE TOUCH Pressed Powder Foundation New shades. New formula. Meet your match. We’ve got you covered with YOUNIQUE TOUCH pressed powder foundation. Our new formula goes on silky smooth to create a flawless, airbrushed finish with buildable, medium-to-full coverage. With brand-new shade options (in addition to our classic shades of TOUCH MINERAL pressed powder foundation), we’re sure you’ll be able to find your perfect match. TELL ME MORE APPLICATION TIPS USE WITH • Smooth and easy application with 1. Swirl the YOUNIQUE™ powder • Included foundation sponge a velvety soft feel puff brush or YOUNIQUE™ • YOUNIQUE™ • Shine control with matte finish powder/concealer brush in powder/concealer brush or • New skin-flattering shades: product, tapping away excess. YOUNIQUE™ powder • Crepe • Damask You can also swipe foundation puff brush • Camlet • Dupioni onto the included • TOUCH MINERAL skin • Poplin • Twill foundation sponge. perfecting concealer • Jacquard • Sable 2. Apply from center of face • Tweed • Percale towards outer edges. • Gingham • Brocade 3. Continue to build for • Voile desired coverage. Price for 8 g / 0.28 oz: $32 USD | $39 CAD | $46 AUD | $45 NZD | £25 GBP | $560 MXN | 34,50 € EUR | HK$248 ABOUT YOUNIQUE Nature + Love + Science. Since its inception in 2012, Younique has been committed to developing beauty products that combine innovative science with the best ingredients nature has to offer. Younique, famous for its best-selling MOODSTRUCK 3D FIBER LASHES+™ lash enhancer, is the first direct-selling company to pioneer the social media-based business model. Founded by a brother-sister team—Derek Maxfield and Melanie Huscroft—Younique offers women the opportunity to look and feel great while helping advance the brand’s mission to uplift, empower, and validate women around the world. -
USA Net Price List (Prices Not Applicable for Markets Outside USA) Carnegiefabrics.Com 800.727.6770
USA Net Price List (Prices not applicable for markets outside USA) carnegiefabrics.com 800.727.6770 USA Net Price List Effective January 6, 2021 TABLE OF CONTENTS GENERAL INFORMATION ................................................................................ 3 FABRIC FINISHES ............................................................................................. 8 PRICE LIST, ALPHABETICAL ........................................................................... 13 A | B | C | D | E | F | G | H | I | J | K | L | M N | O | P | Q | R | S | T | U | V | W | Z PRICE LIST, NUMERICAL ................................................................................ 46 2000 | 4000 | 5000 | 6000 | 7000 | 8000 | 30000 | 100000 Net Pricelist January 2021 2 carnegiefabrics.com 800.727.6770 General Information PRICES Prices shown are the net wholesale costs per linear yard F.O.B Rockville Centre, N.Y. Prices are not applicable for markets outside USA. Please see carnegiefabrics.com for listings of our International Distribution Partners. These prices are subject to change without notice. We therefore suggest that before concluding a transaction you confirm prices with our Rockville Centre office or your local sales representative. SALES SERVICES To place orders, request samples or for other general information, please contact Carnegie Sales Services, Monday through Thursday, 8:30am - 5:30pm. Friday, 8:30am - 5:00pm, Eastern time. Carnegie 110 North Centre Avenue Rockville Centre, New York 11570 Tel. (800)727-6770 Tel. (516)678-6770 Fax (516)307-3765 [email protected] TERMS OF SALE Terms are net 30 days for customers with open accounts. You may apply for an open account by sending us the names, addresses, and fax numbers of four trade credit references and your bank with your account number. INSPECTION All orders are carefully inspected before shipment for pattern, color, quality and yardage. -
Ifbanefield & Co.
WEW-YORK DAILY TRIBUNE, SUNDAY, FEBRUARY 19. 1005. 9 NOT WASH SALKS THEY SAY s.lir.l) LIFE WITH TEETH. TO SAVE CITY $1,000,000. BY MUXROBS. Women on hunaway Airship Bit Six Cent Verdict for Man Whose I & CO. STATEMENT\u25a0 FBANEFIELD :.r__ Hole in Balloon. Property Was Damaged by Rain. IMPORTERS. JEWELERS. IBV TKLKGRAPH ' - Bought TO THE TBIBL'N'E.] Tlie Corporation 'oun \u25a0< i are now I'>i"atr<l $c (la, to •Ssn Francisco. Offset the Loxcmoh Scare, Feb. IS.—With broken cables days' trial, obtained .1 vprdicl ywsterdaj which will 1. Altmatt dans;";;;i(: and r.ith Mis. <;r Helton, in ilnirbuilding, 1 v Oi8 W. wife save tho city ov«»r The was Ks Inventor, f1.W0.000. actioo They Declare. of as Its freisht. the airship California brought by Henry Bundhelmer to recover dfti Messenger suddenly sprang upward f,,, 1 ST., two thousand from tlip.i|;v InjuricK Ii \u25a0 it 38 34TU Tr« f'ft done nn.ii.ru WEST stn-k brokerage firm of klunroe & Uunroe ovft- Idord Turk- 'iMs'-aftornbbn;' There M«med i»;Ptli-st.. in the rainstorm Augu I 19 I. when who came Into \v*]| no hop. of between lii'th Aye. an<l Herald Square Street promlnet-Cce about' two for its .K-rnpsnt. >but the woman Hi-- In 'I'h. Bninx wo I" , the gas Millbrook sewer unable months as<r when !»r>*ciilatlve movement in bit a bole in the bag and the machine plunged carry orf thr- water, and Bundhfimer'f pr< >Tc»r.tr-*l an.l Boston Ptock collapsed, and whore earthward, to hud lightly in Host Berkley.