Method of Improving Lateral Stability by Using Additional Yaw Moment of Semi-Trailer
Total Page:16
File Type:pdf, Size:1020Kb
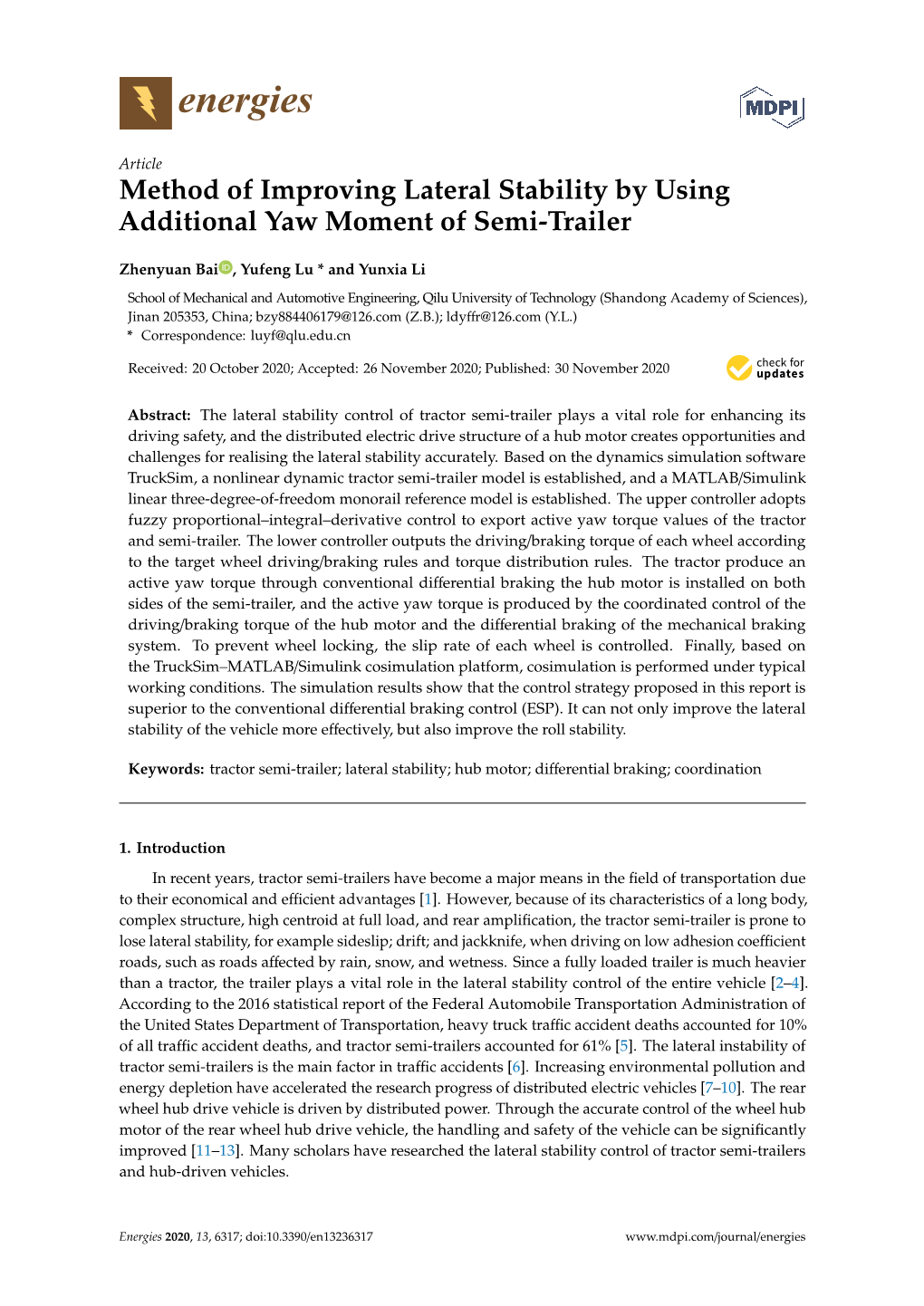
Load more
Recommended publications
-
A Comprehensive Study of Key Electric Vehicle (EV) Components, Technologies, Challenges, Impacts, and Future Direction of Development
Review A Comprehensive Study of Key Electric Vehicle (EV) Components, Technologies, Challenges, Impacts, and Future Direction of Development Fuad Un-Noor 1, Sanjeevikumar Padmanaban 2,*, Lucian Mihet-Popa 3, Mohammad Nurunnabi Mollah 1 and Eklas Hossain 4,* 1 Department of Electrical and Electronic Engineering, Khulna University of Engineering and Technology, Khulna 9203, Bangladesh; [email protected] (F.U.-N.); [email protected] (M.N.M.) 2 Department of Electrical and Electronics Engineering, University of Johannesburg, Auckland Park 2006, South Africa 3 Faculty of Engineering, Østfold University College, Kobberslagerstredet 5, 1671 Kråkeroy-Fredrikstad, Norway; [email protected] 4 Department of Electrical Engineering & Renewable Energy, Oregon Tech, Klamath Falls, OR 97601, USA * Correspondence: [email protected] (S.P.); [email protected] (E.H.); Tel.: +27-79-219-9845 (S.P.); +1-541-885-1516 (E.H.) Academic Editor: Sergio Saponara Received: 8 May 2017; Accepted: 21 July 2017; Published: 17 August 2017 Abstract: Electric vehicles (EV), including Battery Electric Vehicle (BEV), Hybrid Electric Vehicle (HEV), Plug-in Hybrid Electric Vehicle (PHEV), Fuel Cell Electric Vehicle (FCEV), are becoming more commonplace in the transportation sector in recent times. As the present trend suggests, this mode of transport is likely to replace internal combustion engine (ICE) vehicles in the near future. Each of the main EV components has a number of technologies that are currently in use or can become prominent in the future. EVs can cause significant impacts on the environment, power system, and other related sectors. The present power system could face huge instabilities with enough EV penetration, but with proper management and coordination, EVs can be turned into a major contributor to the successful implementation of the smart grid concept. -
Individual Drive-Wheel Energy Management for Rear-Traction Electric Vehicles with In-Wheel Motors
applied sciences Article Individual Drive-Wheel Energy Management for Rear-Traction Electric Vehicles with In-Wheel Motors Jose del C. Julio-Rodríguez * , Alfredo Santana-Díaz. * and Ricardo A. Ramirez-Mendoza * School of Engineering and Sciences, Tecnologico de Monterrey, Toluca 50110, Mexico * Correspondence: [email protected] (J.d.C.J.-R.); [email protected] (A.S.-D.); [email protected] (R.A.R.-M.) Abstract: In-wheel motor technology has reduced the number of components required in a vehicle’s power train system, but it has also led to several additional technological challenges. According to kinematic laws, during the turning maneuvers of a vehicle, the tires must turn at adequate rotational speeds to provide an instantaneous center of rotation. An Electronic Differential System (EDS) controlling these speeds is necessary to ensure speeds on the rear axle wheels, always guaranteeing a tractive effort to move the vehicle with the least possible energy. In this work, we present an EDS developed, implemented, and tested in a virtual environment using MATLAB™, with the proposed developments then implemented in a test car. Exhaustive experimental testing demonstrated that the proposed EDS design significantly improves the test vehicle’s longitudinal dynamics and energy consumption. This paper’s main contribution consists of designing an EDS for an in-wheel motor electric vehicle (IWMEV), with motors directly connected to the rear axle. The design demonstrated effective energy management, with savings of up to 21.4% over a vehicle without EDS, while at the same time improving longitudinal dynamic performance. Citation: Julio-Rodríguez, J.d.C.; Keywords: electric vehicles; electromobility; in-wheel motors; electronic differential; wheel-speed Santana-Díaz., A.; Ramirez-Mendoza, control; powertrain; energy consumption; automotive control; vehicle dynamics control R.A. -
Embedded System Design and Implementation of an Intelligent Electronic Differential System for Electric Vehicles
(IJACSA) International Journal of Advanced Computer Science and Applications, Vol. 8, No. 9, 2017 Embedded System Design and Implementation of an Intelligent Electronic Differential System for Electric Vehicles Ali UYSAL Emel SOYLU Technology Faculty, Department of Mechatronics Technology Faculty, Department of Mechatronics Engineering, Karabük University Engineering, Karabük University Karabük, TURKEY Karabük, TURKEY Abstract—This paper presents an experimental study of the mechanical differential, torque is not limited by the least- electronic differential system with four-wheel, dual-rear in wheel wheeled wheel, fast response time, accurate information on motor independently driven an electric vehicle. It is worth torque per wheel [2]. bearing in mind that the electronic differential is a new technology used in electric vehicle technology and provides better In this work, the intelligent supervised EDS for electric balancing in curved paths. In addition, it is more lightweight vehicles is designed and realized. There are studies in this issue than the mechanical differential and can be controlled by a single in the literature. This technology has many applications and controller. In this study, intelligently supervised electronic vehicle performance has been improved with successful differential design and control is carried out for electric vehicles. applications. The movement of this earthmoving truck is Embedded system is used to provide motor control with a fuzzy provided by an electric drive system consisting of two logic controller. High accuracy is obtained from experimental independent electric motors. Providing a maximum power of study. 2700 kW, these engines are controlled to adjust their speed when cornering, thereby increasing traction and reducing tire Keywords—Electronic differential; electric vehicle; embedded wear. -
Electronic Differential in Electric Vehicles
International Journal of Scientific & Engineering Research, Volume 4, Issue 11, November-2013 1322 ISSN 2229-5518 Electronic differential in electric vehicles Akshay aggarwal Abstract - Electronic differential is advancement in electric vehicles technology along with the more traction control. The electronic differential provides the required torque for each driving wheel and allows different wheel speeds electronically. It is used in place of the mechanical differential in multi-drive systems. When cornering the inner and outer wheels rotate at different speeds, because the inner wheels describe a smaller turning radius. The electronic differential uses the steering wheel command signal, throttle position signals and the motor speed signals to control the power to each wheel so that all wheels are supplied with the torque they need. The proposed control structure is based on the PID control for each wheel motor. PID Control system is then evaluated in the Matlab/Simulink environment. Electronic differential have the advantages of replacing loosely, heavy and inefficient mechanical transmission and mechanical differential with a more efficient, light and small electric motors directly coupled to the wheels using a single gear reduction or an in-wheel motor. Index terms PID controller, electric vehicle, controller area network, electronic control unit, electronic differential —————————— —————————— 1 Introduction trajectory or a lane change each wheel is controlled The heavy body including the structure and materials through an ED in order to satisfy the motion used in Electric Vehicle hasIJSER always been a field of requirements. interest to designers. Their continuous research work to reduce the weight of the body has interested many 3 Electric Vehicle Mechanical Load people worldwide. -
Status of Pure Electric Vehicle Power Train Technology and Future Prospects
Review Status of Pure Electric Vehicle Power Train Technology and Future Prospects Abhisek Karki 1,2,* , Sudip Phuyal 3,4,* , Daniel Tuladhar 1, Subarna Basnet 5 and Bim Prasad Shrestha 1 1 Department of Mechanical Engineering, Kathmandu University, Dhulikhel 45200, Nepal; [email protected] (D.T.); [email protected] (B.P.S.) 2 Aviyanta ko Karmashala Pvt. Ltd., Bhaktapur 44800, Nepal 3 Department of Electrical and Electronics Engineering, Kathmandu University, Dhulikhel 45200, Nepal 4 Institute of Himalayan Risk Reduction, Lalitpur 44700, Nepal 5 International Design Center, Massachusetts Institute of Technology, Cambridge, MA 02139, USA; [email protected] * Correspondence: [email protected] (A.K.); [email protected] (S.P.) Received: 14 July 2020; Accepted: 10 August 2020; Published: 17 August 2020 Abstract: Electric vehicles (EV) are becoming more common mobility in the transportation sector in recent times. The dependence on oil as the source of energy for passenger vehicles has economic and political implications, and the crisis will take over as the oil reserves of the world diminish. As concerns of oil depletion and security of the oil supply remain as severe as ever, and faced with the consequences of climate change due to greenhouse gas emissions from the tail pipes of vehicles, the world today is increasingly looking at alternatives to traditional road transport technologies. EVs are seen as a promising green technology which could lead to the decarbonization of the passenger vehicle fleet and to independence from oil. There are possibilities of immense environmental benefits as well, as EVs have zero tail pipe emission and therefore are capable of curbing the pollution problems created by vehicle emission in an efficient way so they can extensively reduce the greenhouse gas emissions produced by the transportation sector as pure electric vehicles are the only vehicles with zero-emission potential. -
Multi-Objective Optimisation for Battery Electric Vehicle Powertrain Topologies
Original Article Proc IMechE Part D: J Automobile Engineering 1–20 Multi-objective optimisation for Ó IMechE 2016 Reprints and permissions: sagepub.co.uk/journalsPermissions.nav battery electric vehicle powertrain DOI: 10.1177/0954407016671275 topologies pid.sagepub.com Pongpun Othaganont1, Francis Assadian2 and Daniel J Auger1 Abstract Electric vehicles are becoming more popular in the market. To be competitive, manufacturers need to produce vehicles with a low energy consumption, a good range and an acceptable driving performance. These are dependent on the choice of components and the topology in which they are used. In a conventional gasoline vehicle, the powertrain topol- ogy is constrained to a few well-understood layouts; these typically consist of a single engine driving one axle or both axles through a multi-ratio gearbox. With electric vehicles, there is more flexibility, and the design space is relatively unexplored. In this paper, we evaluate several different topologies as follows: a traditional topology using a single electric motor driving a single axle with a fixed gear ratio; a topology using separate motors for the front axle and the rear axle, each with its own fixed gear ratio; a topology using in-wheel motors on a single axle; a four-wheel-drive topology using in-wheel motors on both axes. Multi-objective optimisation techniques are used to find the optimal component sizing for a given requirement set and to investigate the trade-offs between the energy consumption, the powertrain cost and the acceleration performance. The paper concludes with a discussion of the relative merits of the different topologies and their applicability to real-world passenger cars. -
SCCA Fastrack News January 2021 Page 1 Solo
Solo SOLO EVENTS BOARD | November 25th The Solo Events Board met by conference call November 25th. Attending were SEB members Mark Labbancz, Bob Davis, Zack Barnes, Keith Brown, Mark Scroggs, and Marshall Grice; Charlie Davis and Steve Strickland of the BOD. These minutes are presented in topical order rather than the order discussed. Comments regarding items published herein should be directed via the website www.soloeventsboard.com. Member Advisories Street Modified Category #29086 #28658 feedback - manufacturer specific engine blocks The SMAC thanks you for your input. #29130 #28658 Delete the cross-make engine weight penalty - feedback The SMAC thanks you for your input. #29258 In support of #28658 to remove cross-manufacturer penalty The SMAC thanks you for your input. #29307, 29308, 29310, 29313 Feedback on #28407 Aftermarket gauge clusters (various) The SMAC thanks you for your input. #29335 28407 Feedback The SMAC thanks you for your input. Prepared Category #29371 Front Air Damn Vertical means perpendicular to horizontal. Front spoilers/air dams are covered in 17.2.O, which "allows a vertical air dam/spoiler above a horizontal splitter." As per 1.c in Appendix A, X Prepared, the splitter has a +/- 3 degree allowance from horizontal. The PAC strongly cautions against tortured interpretations of the rules. #29735 Bodywork modifications Per the PAC, if bodywork is in excess of the allowances of section 17.2 of the Solo Rules, but is compliant with the Club Racing General Competition Rules (GCR) GT rule set, and is of a car listed in Appendix A of the Solo Rule Book for CP (I.E. -
Acronimos Automotriz
ACRONIMOS AUTOMOTRIZ 0LEV 1AX 1BBL 1BC 1DOF 1HP 1MR 1OHC 1SR 1STR 1TT 1WD 1ZYL 12HOS 2AT 2AV 2AX 2BBL 2BC 2CAM 2CE 2CEO 2CO 2CT 2CV 2CVC 2CW 2DFB 2DH 2DOF 2DP 2DR 2DS 2DV 2DW 2F2F 2GR 2K1 2LH 2LR 2MH 2MHEV 2NH 2OHC 2OHV 2RA 2RM 2RV 2SE 2SF 2SLB 2SO 2SPD 2SR 2SRB 2STR 2TBO 2TP 2TT 2VPC 2WB 2WD 2WLTL 2WS 2WTL 2WV 2ZYL 24HLM 24HN 24HOD 24HRS 3AV 3AX 3BL 3CC 3CE 3CV 3DCC 3DD 3DHB 3DOF 3DR 3DS 3DV 3DW 3GR 3GT 3LH 3LR 3MA 3PB 3PH 3PSB 3PT 3SK 3ST 3STR 3TBO 3VPC 3WC 3WCC 3WD 3WEV 3WH 3WP 3WS 3WT 3WV 3ZYL 4ABS 4ADT 4AT 4AV 4AX 4BBL 4CE 4CL 4CLT 4CV 4DC 4DH 4DR 4DS 4DSC 4DV 4DW 4EAT 4ECT 4ETC 4ETS 4EW 4FV 4GA 4GR 4HLC 4LF 4LH 4LLC 4LR 4LS 4MT 4RA 4RD 4RM 4RT 4SE 4SLB 4SPD 4SRB 4SS 4ST 4STR 4TB 4VPC 4WA 4WABS 4WAL 4WAS 4WB 4WC 4WD 4WDA 4WDB 4WDC 4WDO 4WDR 4WIS 4WOTY 4WS 4WV 4WW 4X2 4X4 4ZYL 5AT 5DHB 5DR 5DS 5DSB 5DV 5DW 5GA 5GR 5MAN 5MT 5SS 5ST 5STR 5VPC 5WC 5WD 5WH 5ZYL 6AT 6CE 6CL 6CM 6DOF 6DR 6GA 6HSP 6MAN 6MT 6RDS 6SS 6ST 6STR 6WD 6WH 6WV 6X6 6ZYL 7SS 7STR 8CL 8CLT 8CM 8CTF 8WD 8X8 8ZYL 9STR A&E A&F A&J A1GP A4K A4WD A5K A7C AAA AAAA AAAFTS AAAM AAAS AAB AABC AABS AAC AACA AACC AACET AACF AACN AAD AADA AADF AADT AADTT AAE AAF AAFEA AAFLS AAFRSR AAG AAGT AAHF AAI AAIA AAITF AAIW AAK AAL AALA AALM AAM AAMA AAMVA AAN AAOL AAP AAPAC AAPC AAPEC AAPEX AAPS AAPTS AAR AARA AARDA AARN AARS AAS AASA AASHTO AASP AASRV AAT AATA AATC AAV AAV8 AAW AAWDC AAWF AAWT AAZ ABA ABAG ABAN ABARS ABB ABC ABCA ABCV ABD ABDC ABE ABEIVA ABFD ABG ABH ABHP ABI ABIAUTO ABK ABL ABLS ABM ABN ABO ABOT ABP ABPV ABR ABRAVE ABRN ABRS ABS ABSA ABSBSC ABSL ABSS ABSSL ABSV ABT ABTT -
Traction Control of an Electric Vehicle with Four In-Wheel Motors
Traction Control of an Electric Vehicle with Four In-Wheel Motors by Amin Hajihosseinlu A thesis submitted to the Faculty of Graduate Studies of The University of Manitoba in partial fulfillment of the requirements for the degree of MASTER OF SCIENCE Department of Electrical and Computer Engineering University of Manitoba Winnipeg, MB, Canada Copyright c August 2014 by Amin Hajihosseinlu i Abstract This thesis evaluates an electric vehicle with four independently-controlled in-wheel electric motors. The electric vehicle investigated in this work requires a main con- troller that not only coordinates with each individual motor drive controller, but is also needed to distribute torque and power to each in-wheel motor. The controller adjusts the speed of each motor to the driving conditions according to the require- ments and emulates the behavior of a mechanical differential. Then, in addition to the electronic differential controller, a simple yet robust control strategy for maximiz- ing traction force between tire and road is developed and presented. Moreover, the controller continuously senses the yaw rate and prevents over- and under-steering by adjusting the torque on the right or left wheels. Simulation and experimental results validate the proposed strategy. ii Acknowledgements First and foremost, I would like to express my sincere gratitude to my academic advisor, Dr. Shaahin Filizadeh for giving me the opportunity to work here on a project that I am enthusiastic about and for his continual support and guidance. Without his support and the facilities that he provided, this dissertation would not have been possible. I want to thank my parents for their support. -
Graduation Project Report Torque Vectoring
Scource: http://mercedesbenzblogphotodb.wordpress.com/2009/04/20/20042009-mercedes-benz-at-auto-shanghai-2009/torque-vectoring-brake/ (03-08-2011) Scource: http://mercedesbenzblogphotodb.wordpress.com/2009/04/20/20042009-mercedes-benz-at-auto-shanghai-2009/torque-vectoring-brake/ (03-08-2011) Enhanced Improvement Of Vehicle Dynamic Enhanced Improvement Of Vehicle Dynamic Behaviour By Applying Torque Vectoring BehaviourViewed From The By Vehicle Applying Dynamic And Torque Powertrains Vectoring Perspective Viewed From The Vehicle Dynamic And Powertrains Perspective Enhanced Improvement Of Vehicle Dynamic Behaviour By Applying Torque Vectoring Viewed From The Vehicle Dynamic And Powertrains Perspective Source: [40] 10/01/2012| Graduation Project | S.J. Koster (Joost) & S. Nada (Shady) Graduation Project Report Hogeschool van Arnhem en Nijmegen HTS-Autotechniek Contact Information Placement company: Educational institution: TNO Automotive HAN University of Applied Sciences Steenovenweg 1 HTS Autotechniek 5708 HN Helmond Ruitenberglaan 29 T 088 866 57 29 6826 CC Arnhem F 088 866 88 62 T(024) 353 05 00E [email protected] [email protected] Company supervisors; Ir. S.T.H. Jansen Ir. L.J.M. van Eeuwijk T +31 (0)88 866 57 43 T +31 (0)88 866 09 13 M +31 (0)65 388 94 82 M +31 (0)6 - [email protected] [email protected] Educational supervisors: Ir. A.J. van Breugel Ing. I. de Gijsel T +31 (0)26 384 93 47 T +31 (0)26 384 93 39 M +31 (0)63 626 25 64 M +31 (0)61 489 85 87 [email protected] [email protected] Graduates: S.J. -
Model-Based Powertrain Design and Control System Development for the Ideal All-Wheel Drive Electric Vehicle Haotian Wu Purdue University
Purdue University Purdue e-Pubs Open Access Dissertations Theses and Dissertations Fall 2014 Model-based powertrain design and control system development for the ideal all-wheel drive electric vehicle Haotian Wu Purdue University Follow this and additional works at: https://docs.lib.purdue.edu/open_access_dissertations Part of the Mechanical Engineering Commons Recommended Citation Wu, Haotian, "Model-based powertrain design and control system development for the ideal all-wheel drive electric vehicle" (2014). Open Access Dissertations. 392. https://docs.lib.purdue.edu/open_access_dissertations/392 This document has been made available through Purdue e-Pubs, a service of the Purdue University Libraries. Please contact [email protected] for additional information. *UDGXDWH6FKRRO)RUP30 5HYLVHG 0814 PURDUE UNIVERSITY GRADUATE SCHOOL Thesis/Dissertation Acceptance 7KLVLVWRFHUWLI\WKDWWKHWKHVLVGLVVHUWDWLRQSUHSDUHG %\ Haotian Wu (QWLWOHG MODEL-BASED POWERTRAIN DESIGN AND CONTROL SYSTEM DEVELOPMENT FOR THE IDEAL ALL-WHEEL DRIVE ELECTRIC VEHICLE Doctor of Philosophy )RUWKHGHJUHHRI ,VDSSURYHGE\WKHILQDOH[DPLQLQJFRPPLWWHH Richard M. French Haiyan H. Zhang Qingyou Han Ayhan Ince To the best of my knowledge and as understood by the student in the Thesis/Dissertation Agreement, Publication Delay, and Certification/Disclaimer (Graduate School Form 32), this thesis/dissertation adheres to the provisions of Purdue University’s “Policy on Integrity in Research” and the use of copyrighted material. Haiyan H. Zhang $SSURYHGE\0DMRU3URIHVVRU V BBBBBBBBBBBBBBBBBBBBBBBBBBBBBBBBBBBB -
Electronic Stability Control: Review of Research and Regulations
ELECTRONIC STABILITY CONTROL: REVIEW OF RESEARCH AND REGULATIONS Prepared by Michael Paine Vehicle Design and Research Pty Limited for ROADS AND TRAFFIC AUTHORITY OF NSW June 2005 Vehicle Design & Research REPORT DOCUMENTATION PAGE Report No. Report Date Pages G248 2 June 2005 30 Title and Subtitle Electronic Stability Control: Review of Research and Regulations Authors Michael Paine Performing Organisation Vehicle Design and Research Pty Limited 10 Lanai Place, Beacon Hill NSW Australia 2100 Sponsoring Organisation Roads and Traffic Authority of New South Wales. Harry Vertsonis, Road Environment and Light Vehicle Standards 280 Elizabeth St, Surry Hills, NSW Abstract Recent analysis of real world accidents in the USA suggest that Electronic Stability Control (ESC) can be remarkably effective at preventing loss-of-control accidents. Regulatory authorities and consumer test organisations around the world are therefore actively researching test methods that can be used to assess the performance of ESC. Researchers in the USA, Canada, Europe, Japan and Australia were contacted to establish the status of research and to obtain comments on ways in which ESC can be assessed and encouraged. Strategies range from "regulation by definition" and defining functional requirements for ESC, to the performance of comparative dynamic tests. At this stage there is no performance-based test and assessment protocol that is suitable for use by the Australian New Car Assessment Program or in regulations. However, consideration should be given to regulating functional requirements to ensure there are no unintended adverse effects from ESC. To complement the global research it is recommended that a small research program be undertaken in Australia to evaluate the ability of an Australian- developed test procedure to assess ESC performance.