Possibilities of Automatic Inspection on Mounted Wheel Sets with Hollow Axle on Slovene Railways
Total Page:16
File Type:pdf, Size:1020Kb
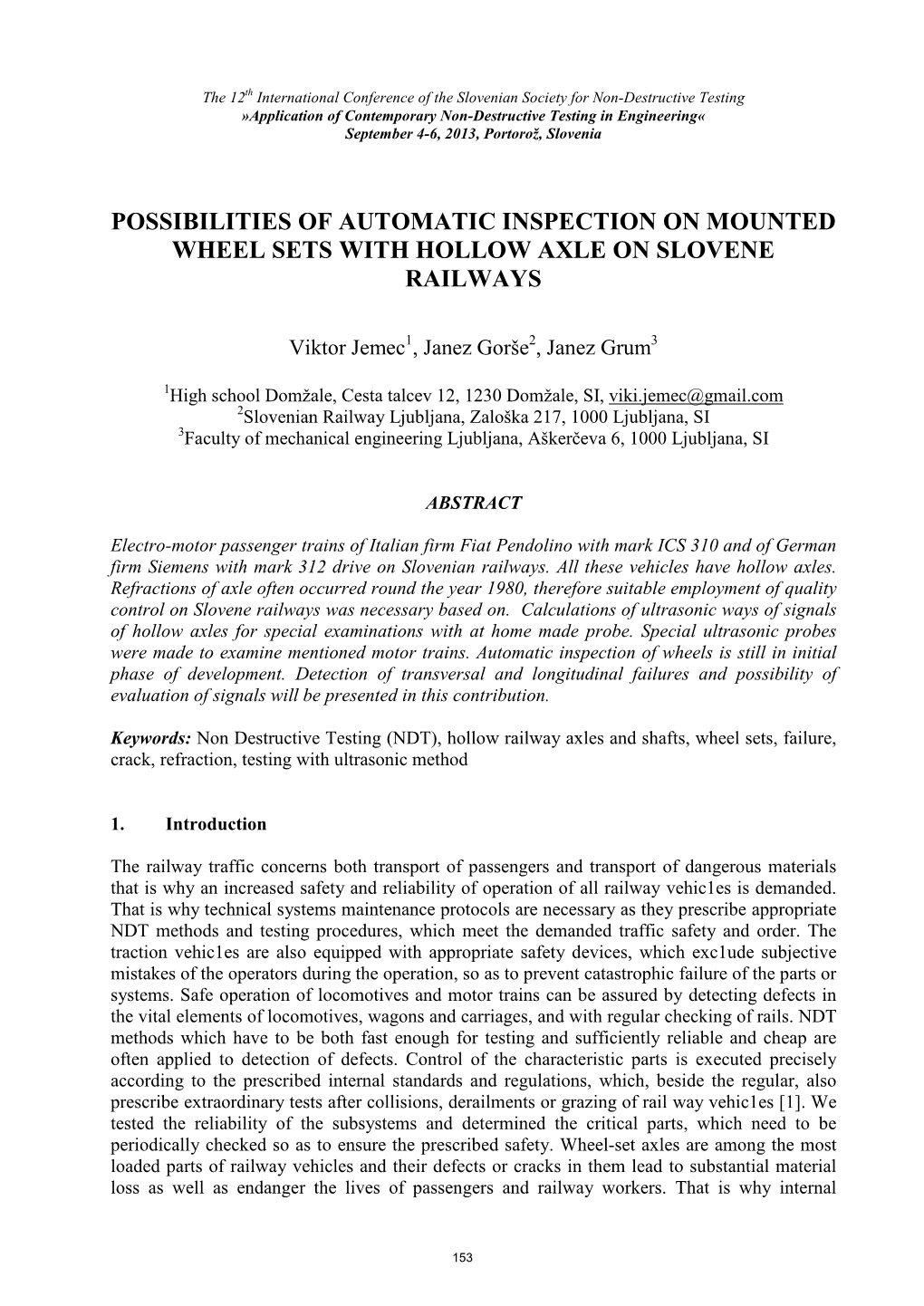
Load more
Recommended publications
-
Peter Verlič Transport & Logistics Conference 2018 Brussels, 22 March 2018
Potential of regional railway cooperation and infrastructure investment „View of Slovenian Railways“ Dr. Peter Verlič Transport & Logistics Conference 2018 Brussels, 22 March 2018 1 Slovenian Railways – At the Crossroads of European Corridors (1) Baltic-Adriatic Corridor RFC 5 Mediterranean Corridor RFC 6 Amber Corridor RFC 11 XPC Corridor (future RFC 10 – Alpine- Western Balkan Rail Freight Corridor) in establishment 2 Slovenian Railways – At the Crossroads of European Corridors (2) • Line length of Rail Freight Corridors on SŽ rail network: Corridor RFC 5 337 km Corridor RFC 6 395 km Corridor XPC 186 km (future RFC 10) Corridor RFC 11 382 km • Planned rail investments on RFCs: Infrastructure upgrades to facilitate interoperability on RFCs (ETCS, double-track lines, remote control traffic management system …) Baltic – Adriatic Mediterranean Alpine – Western Balkan Amber 3 Slovenian Railways – Key Facts of SŽ Rail Network Line length: Total 1,207 km Double-track 333 km Single-track 874 km Electrified 610 km Number of: Rail Freight Stations 105 Rail Passenger Stations 115 Railroad Crossings 745 double track single track 4 Slovenian Railways – Planned Increases of Line Capacity (in %) Track sections where the increase of throughput capacity (number of trains per day) is necessary: up to 20% 20% - 40% more than 40% adequate throughput capacity 5 Slovenian Railways – ERTMS deployment on SŽ Rail Network Entered into service in 2017: . ETCS Level 1 installed on the Koper/Sežana- Hodoš line (ETCS fully deployed on this line – 412 km) . GSM-R installed on the entire Slovenian rail network Future challenges: . ETCS Level 1 deployment currently in progress on the Pragersko-Šentilj-State border line and Zidani Most-Dobova-State border line (total length of 90 km, works completed in 2023) . -
“Naslov Projekta”
Institute of Traffic and Transport Ljubljana l.l.c. your R&D partner in Slovenia, EU Ljubljana, 2012 Prometni institut Ljubljana d.o.o. - Slovenia - EU Institute of Traffic and Transport Ljubljana l.l.c. 22. januar 2013 "Naslov projekta" 2 Company info The Traffic Institute Ljubljana l.l.c. is a research organisation founded by Slovenian Railways. The company with over 40 years of tradition and innovative solutions conducts research and development projects in all traffic modes applied to the domestic and foreign market. The institute is a member of the Slovenian Chamber of Engineers and is registered as a research organisation by the Slovenian research agency. The company specialises in research and development of transport technology, infrastructure, transport economics and law, transport related IT&T as well as in elaboration of investment documentation. 22. januar 2013 "Naslov projekta" 3 Activities TRAFFIC • Railway and road traffic studies (infrastructure capacity analyses, rational organization of TECHNOLOGY technological processes, traffic organization and management, …) • Preparation of construction documents, implementation of UIC leaflets, railway lines TRAFFIC INFRASTRUCTURE condition measurements, traffic infrastructure maintenance optimization, spatial solutions, GIS TRAFFIC IT&T • Modelling and automation of traffic management processes, traffic data-base modelling and implementation, SW development, support and elaboration of ICT pilot projects RESEARCH IN • Transport development analyses, analyses of traffic management system, traffic flows TRANSPORT analyses and estimations, expertise in management and organisation of traffic regulation, ECONOMICS AND LAW analyses of traffic processes efficiency, empirical research in transport INVESTMENT • Investment documentation in the field of transport infrastructure, municipal infrastructure, DOCUMENTATION health and social care, methodology elements for preparation and evaluation of investment projects for public railway infrastructure, expert opinions and reviews 22. -
Slovenian Railways Magazine – Special Edition June, 2014
Slovenian Railways Magazine – Special Edition June, 2014 4th –7 th June, 2014 Across Europe at attractive prices WithInterRail ticket for all generations to 30 countries! Additional infomation available at www.slo-zeleznice.si, [email protected] and on telephone number 1999 (network provider charges appy) Slovenian Railways Magazine – Special edition, June, 2014 Nova proga is published by the Slovenian Railways Group SI-1506 Ljubljana, Kolodvorska 11, Telephone: 00386 1 29 14327, Fax: 00386 1 29 14809 Email: [email protected] Editor-in-chief: Janez Krivec Photography: Miško Kranjec, except where stated otherwise Janez Krivec Print: SŽ- Železniška tiskarna Ljubljana, d. d. Editor-in-chief After months of preparation The Days of Slovenian Railways, an event dedicated to the promotion of rail in Slovenia and abroad, finally began. Slovenian Railways hosted numerous events throughout Slovenia to which we invited our passengers, railway enthusiasts and business partners. In this special issue of Nova proga magazine we give you an insight into the events taking place in June on the first ever Days of Slovenian Railways. Railways are an important part of everyday life for many Slovenians. That is why we prepared a very diverse and engaging programme. The Days of Slovenian Railways were a great opportunity to display to the public various activities our company is undertaking and to discuss the challenges the railways sector currently faces. Special attention was also given to business with a conference which formally opened The Days of Slovenian Railways. The Slovenian Railways Group continually enhances business performance and output. At the conference we proved to the public and our business partners that we are fully equipped to provide the best logistical services and follow their needs. -
ARGE Korridor X Goals and Tasks
ARGE Korridor X Goals and Tasks www.arge-kx.com Version: June 2008 ATTRACTING MORE TRAFFIC TO CORRIDOR X Preface Our Vision Our vision is to enhance the attractiveness and quality of the transport routes that connect people and markets from Central Europe to South Eastern Europe and the Asian continent. Our Mission We connect and strengthen our regions by selective market and research projects to ensure that people and goods in Europe, which is growing together, can be transported safely, economically and quickly to their destinations. ATTRACTING MORE TRAFFIC TO CORRIDOR X 2 The Purpose of ARGE Korridor X ARGE Korridor X (AKX) was founded • in the year 2001 • as an Austrian co-operation constituted under civil law (international railway joint venture group) • in order to push railway subjects on the Pan-European Corridor X in close co-operation between the railway organisations from Greece to Germany • in order to generate and carry out research projects with the knowledge of 8 railways • in order to attract more traffic on Corridor X ATTRACTING MORE TRAFFIC TO CORRIDOR X 3 ARGE Korridor X Members • Foundation Partners OSE Hellenic Railways MZ Macedonian Railways NRIC Bulgarian Railways ZS Serbian Railways HZ Croatian Railways SZ Slovenian Railways ÖBB Austrian Federal Railways DB AG German Railways • Admitted Members (since foundation) GKB Graz-Köflacher-Bahn (2003) ROeEE Raaberbahn (2004) • Observers Since foundation: PEC X Steering Committee of Pan-European Corridor X Since 2006: TCDD Turkish State Railways ZFBH Railways of the Federation -
Connect2ce – “Improving Rail Connections and Smart Mobility in Central Europe” Final Publication
CONNECT2CE – “IMPROVING RAIL CONNECTIONS AND SMART MOBILITY IN CENTRAL EUROPE” FINAL PUBLICATION CONTENTS Introduction ........................................................................................................... 4 Pilot actions ........................................................................................................... 5 Pilot action 1 – Assessment and testing of the extended cross-border passenger railway connection .......................................................................................................... 6 Pilot action 2 – Elaboration of a cross-border Public Service Obligation between Slovenia and Croatia .............................................................................................................. 8 Pilot action 3 – Harmonisation of bus and train timetables in the Hungarian border area .......... 10 Pilot action 4 – Concept for the design of a cross-border public transport service between Austria and Hungary (two bus lines) .................................................................................... 12 Pilot action 5 – Development of new services and offers for cross-border public transport ........ 14 Pilot action 6 – Cross-border integrated ticket Italy-Slovenia ............................................ 16 Pilot action 7 – Info-mobility tool to enhance multimodal public transport options in the Pilsen region ............................................................................................................... 18 Pilot action 8 – Testing a multi-lingual -
Messe-Guide Messe-Guide
TRANSPORT LOGISTIC 12. BIS 15. MAI 2009 MESSE MÜNCH E N verkehrs RUNDSCHAU Messe-GuideMesse-Guide transporttransport logisticlogistic 1 mit großem Ausstellerverzeichnis You drive, we care. Zeigen Sie uns Ihre grüne Seite Eco Performance Award sucht wieder Vorbilder Sie setzen sich im Tagesgeschäft vor- bildlich auf Nachhaltigkeit und bleiben trotzdem effizient? Dann zögern Sie nicht: Ab sofort können sich Transpor- teure für den in zwei Kategorien mit je 10.000 Euro dotierten Eco Performance Award 2010 bewerben. Zum dritten Mal wird der vom DKV Euro Service initi- ierte und gestiftete Preis vergeben. Der Begriff „Eco“ steht sowohl für Ökonomie (Economy) als auch Ökologie (Ecology). „Eco Performance“ beschreibt die unternehmerische Leistung unter wirtschaftlichen, nachhaltigen und sozialen Aspekten. Dabei können Firmen punkten, die Ökologie und Ökonomie in ihrer Unternehmensphi- losophie verankern. Unter wissenschaftlicher Leitung von Prof. Dr. Wolfgang Stölzle, Lehrstuhl für Logistikmanagement an der Schweizer Universität St. Gallen, werden die Bewerberkonzepte anhand eines eigens entwickelten Verfahrens bewer- tet und die besten Eco Performer ermittelt. Die Eco Performance-Broschüre sowie die Bewerbungsunterlagen gibt’s im Internet: www.dkv-euroservice.com/eco-performance oder www.logistik.unisg.ch/eco_performance_award 2 www.dkv-euroservice.com editorial Für manche ist sie das Fest der Spediteure, für andere die Leit- messe der Logistikbranche. In jedem Fall zählt die transport logistic zu den Pflichtterminen der Branche. Wer sich über Trends und Technologien, Produkte und Services, Märkte und Unternehmen informieren oder einfach nur Kontakte knüpfen und Netzwerke pflegen will, ist hier richtig. Über 1700 Aussteller aus 55 Ländern präsentieren die ganze Bandbreite der Logistik – vom Güterverkehr auf Straße, Schiene, Wasser und in der Luft über Telematik und Intralogistik. -
Finished Vehicle Logistics by Rail in Europe
Finished Vehicle Logistics by Rail in Europe Version 3 December 2017 This publication was prepared by Oleh Shchuryk, Research & Projects Manager, ECG – the Association of European Vehicle Logistics. Foreword The project to produce this book on ‘Finished Vehicle Logistics by Rail in Europe’ was initiated during the ECG Land Transport Working Group meeting in January 2014, Frankfurt am Main. Initially, it was suggested by the members of the group that Oleh Shchuryk prepares a short briefing paper about the current status quo of rail transport and FVLs by rail in Europe. It was to be a concise document explaining the complex nature of rail, its difficulties and challenges, main players, and their roles and responsibilities to be used by ECG’s members. However, it rapidly grew way beyond these simple objectives as you will see. The first draft of the project was presented at the following Land Transport WG meeting which took place in May 2014, Frankfurt am Main. It received further support from the group and in order to gain more knowledge on specific rail technical issues it was decided that ECG should organise site visits with rail technical experts of ECG member companies at their railway operations sites. These were held with DB Schenker Rail Automotive in Frankfurt am Main, BLG Automotive in Bremerhaven, ARS Altmann in Wolnzach, and STVA in Valenton and Paris. As a result of these collaborations, and continuous research on various rail issues, the document was extensively enlarged. The document consists of several parts, namely a historical section that covers railway development in Europe and specific EU countries; a technical section that discusses the different technical issues of the railway (gauges, electrification, controlling and signalling systems, etc.); a section on the liberalisation process in Europe; a section on the key rail players, and a section on logistics services provided by rail. -
1St Edition, Dezember 2010
EUROPEAN RAILWAY AGENCY INTEROPERABILITY UNIT DIRECTORY OF PASSENGER CODE LISTS FOR THE ERA TECHNICAL DOCUMENTS USED IN TAP TSI REFERENCE: ERA/TD/2009-14/INT DOCUMENT REFERENCE FILE TYPE: VERSION: 1.1.1 FINAL TAP TSI DATE: 08.03.2012 PAGE 1 OF 77 European Railway Agency ERA/TD/2009-14/INT: PASSENGER CODE LIST TO TAP TSI AMENDMENT RECORD Version Date Section Modification/description number 1.1 05.05.2011 All sections First release 1.1.1 27.09.2011 Code list New values added B.4.7009, code list B.5.308 ERA_TAP_Passenger_Code_List.doc Version 1.1.1 FINAL Page 2/77 European Railway Agency ERA/TD/2009-14/INT: PASSENGER CODE LIST TO TAP TSI Introduction The present document belongs to the set of Technical Documents described in Annex III „List of Technical Documents referenced in this TSI‟ of the COMMISSION REGULATION (EU) No 454/2011. ERA_TAP_Passenger_Code_List.doc Version 1.1.1 FINAL Page 3/77 European Railway Agency ERA/TD/2009-14/INT: PASSENGER CODE LIST TO TAP TSI Code List ERA_TAP_Passenger_Code_List.doc Version 1.1.1 FINAL Page 4/77 European Railway Agency ERA/TD/2009-14/INT: PASSENGER CODE LIST TO TAP TSI Application : With effect from 08 March 2012. All actors of the European Union falling under the provisions of the TAP TSI. ERA_TAP_Passenger_Code_List.doc Version 1.1.1 FINAL Page 5/77 European Railway Agency ERA/TD/2009-14/INT: PASSENGER CODE LIST TO TAP TSI Contents AMENDMENT RECORD ....................................................................................................................................................... -
Special Event Newsletter Transport Logistic 2019
Special event Cargo newsletter Transport Logistic SŽ News 2019 Comprehensive Rail Freight and Logistics Services in the Heart of Europe Business Results 2018 Exceeding Plans as the Basis for Further Growth E-Freight Transport Using E-Business for Comprehensive Services SŽ-Tovorni promet as the Regional Integrator New and Overhauled Locomotives – Better Services for our Customers SŽ Cargo News DEAR BUSINESS PARTNERS, COLLEAGUES, VISITORS! I am very glad that my colleagues and myself are again able In the two years since the last Transport Logistic, at SŽ- to welcome you at the occasion of the Transport Logistic Tovorni promet we have been putting great efforts into exhibition. Once more, at SŽ Cargo, together with our sister developing our services in Slovenia, as well the services company SŽ-VIT, we are prepared to showcase our rich with our own traction in Austria and Croatia. At the same experience and the wide range of services, tailor-made for time, we have been the driving force behind much of the every individual customer. At the same time, we would like integration of rail cargo carriers in the wider region. The to make you aware of the advantages of doing business Sava Express product, a competitive connection of EU with with the Slovenian Railways Group. Cargo and passenger Slovenia, Croatia, Serbia and neighbouring countries, is one rail and road transports, freight forwarding, infrastructure example of our initiative. With our long-time partners and management, rolling stock maintenance and repairs, with our own traction we will continue strengthening our transport-related research and development, security and presence in the region. -
Handbuch CIM/SMGS
GLV-CIM/SMGS CIM/SMGS Consignment Note Manual (GLV CIM/SMGS) of 1 September 2006 Amendment 28 dated 1st July 2018 This amendment contains: - replacement pages 1/2 - replacement pages 1/2 and 3/4 to Appendix 1 - replacement pages 1/2, 5/6 and 15/16 to Appendix 2 - replacement pages 1/2 and 3/4 to Appendix 3 - replacement page 3 to Appendix 8 - Appendices 4 and 9 are available on www.cit-rail.org Appendix 4 Appendix 9 The CIT General Assembly on 5 November 2009 decided that new documents and amend- ments to existing documents would only be distributed electronically. As a consequence of this decision, we would be grateful if you yourself were to print the copies you require for your inter- nal use. The modifications are marked in the margin. ************************************ Edition 1 July 2018 CIM/SMGS Consignment Note Manual (GLV-CIM/SMGS) Applicable with effect from 1 September 2006 GLV-CIM/SMGS 2018-07-01 This document may be shared with the public In accordance with point 2.5 a) of the CIT Statutes, this document is a recommendation and only binds members to the extent that members adopt it (opting-in principle). © 2006 International Rail Transport Committee (CIT) www.cit-rail.org Organisation for Co-operation between Railways (OSJD) www.osjd.org Amendment No Applicable with effect from Amendment No Applicable with effect from 1 2007-07-01 18 2014-07-01 2 2008-01-01 19 2014-10-24 3/4 2008-07-01 20 2015-07-01 5 2009-01-01 21 2016-01-01 6 2009-07-01 22 2016-07-01 7 2010-01-01 23 2016-07-01 8 2010-02-09 24 2017-01-01 9 2010-05-01 25 2017-05-10 10 2010-07-01 26 2017-07-01 11 2011-07-01 27 2017-08-01 12 2012-01-01 28 2018-07-01 13 2012-07-01 14 2013-02-15 15 2013-03-15 16 2013-07-01 17 2014-02-01 - 2 - 2018-07-01 GLV-CIM/SMGS/Appendix 1 Appendix 1 (see points 4, 25 and 26 of this manual) List of the CIT members and SMGS participants which apply this manual and the traffic axes to which it applies 1 CIT members 2 SMGS participants Azerbaijan Railways CJSCo. -
Austria Belgium Bulgaria Czech Republic France
Participant Company, City Austria Ralf-Charley Schultze GEFCO, Vienna Julia Baumgartner GEFCO, Vienna Klaus Lippstreu Schenker & Co. AG, Vienna Alfred Wolfram Schenker & Co. AG, Vienna Christian Prosser Transpetrol Austria GmbH, Vienna Belgium Vitali Vengrynovych Inter Ferry Boats SA, Antwerp Bulgaria Dr. Ivan Petrov FIATA / Transexpess, Sofia Czech Republic Radim Prochazka Spedi-Trans, Praha France Guenther J. Ferk UIC-Xrail, Paris Claude Bouley Geodis Global Solutions, Clichy Gustav Manding UIC, Paris Oliver Sellnick UIC, Paris Participant Company, City France Christian Biteau Fret SNCF, Paris Fanny Remenyi Fret SNCF, Paris Mr. Negre STVA, Jerome Le Gavrian Touax S.A.S, Puteaux Germany Andreas F. Rudolphi CTL Logistics GmbH, Düsseldorf Ernst-Stefan Bruns ESB Consult, Maxdorf Dirk Baerbock Schenker Automotive RailNet GmbH, Hannover Mrs Yeliz Yildiz TRANSFESA, Cologne Daniel Wiegand Schenker AG, Essen Heiner Rogge FIATA, Bonn Mr. Riedl Kombi Verkehr, Mr. Rainer Goedde Kuehne + Nagel, Bernhard Hoffmann DB Schenke Rail, Mainz Geneviève Rogge FIATA, Bonn Hungary Laszlo Jakab GYSEV, Sopron Participant Company, City Hungary Mr. Szekely GYSEV, Zoltan Potvorskzki Raabersped Kft., Budapest Iran Mohammad Satei Niroo Rail Transport Company, Teheran Amir Hossein Pak TransRail, Teheran Italy Fabio Consolo Trenitalia SpA, Rome Dr Francesco Parisi Francesco Parisi Casa di Spedizioni SpA, Trieste Lithuania Tomas Kersis Lithuanian Railways, Vilnius Skirmante Aliukoniene Ministry of Foreign Affairs of Lithuania, Vilnius Jolanda Kriskovieciene Embassy of the Republic of Lithuania, Ankara Romania Mrs Andra Bozga Ansett - Logistics, Bucharest Mr Alexandru Nicolae Ansett - Logistics, Bucharest Participant Company, City Slovenia Mirjam Kastelič Slovenian Railways, Switzerland Erik Evitmov CIT, Berne Alberto Grisone Hupac Intermodal, Chiasso Tufan Khalaji InterRail AG, St. Gallen Robert Hediger Farnair Rail, Basle Tommaso Di Benedetto MEV Schweiz AG, Basle Sascha Bötte MEV Schweiz AG, Basle René Zimmermann FIATA, Zurich Turkey Ms Nezahat Kanbak Terra Intern. -
Transport & Logistics in Slovenia
TRANSPORT & LOGISTICS IN SLOVENIA FLANDERS INVESTMENT & TRADE MARKET SURVEY Market study ////////////////////////////////////////////////////////////////////////////////////////////////////////////////////////////// TRANSPORT & LOGISTICS IN SLOVENIA ////////////////////////////////////////////////////////////////////////////////////////////////////////////////////////////// FLANDERS INVESTMENT & TRADE c/o Embassy of Belgium Kuzmiceva 9 | 1000 Ljubljana | Slovenia T: +386 31 61 95 08 | [email protected] www.flandersinvestmentandtrade.com TABLE OF CONTENT 1. Introduction: Slovenia – a macro-economic survey ......................................................................................... 3 1.1 Economic development in recent years ................................................................................................................................................ 3 1.2 GDP growth ............................................................................................................................................................................................................ 3 1.3 Inflation and consumer price index (‘CPI’) ........................................................................................................................................... 3 1.4 Unemployment and labour market ......................................................................................................................................................... 3 1.5 Foreign trade and government budget ...............................................................................................................................................