Basic Survey for Joint Implementation, Etc. Basic Feasibility Study On
Total Page:16
File Type:pdf, Size:1020Kb
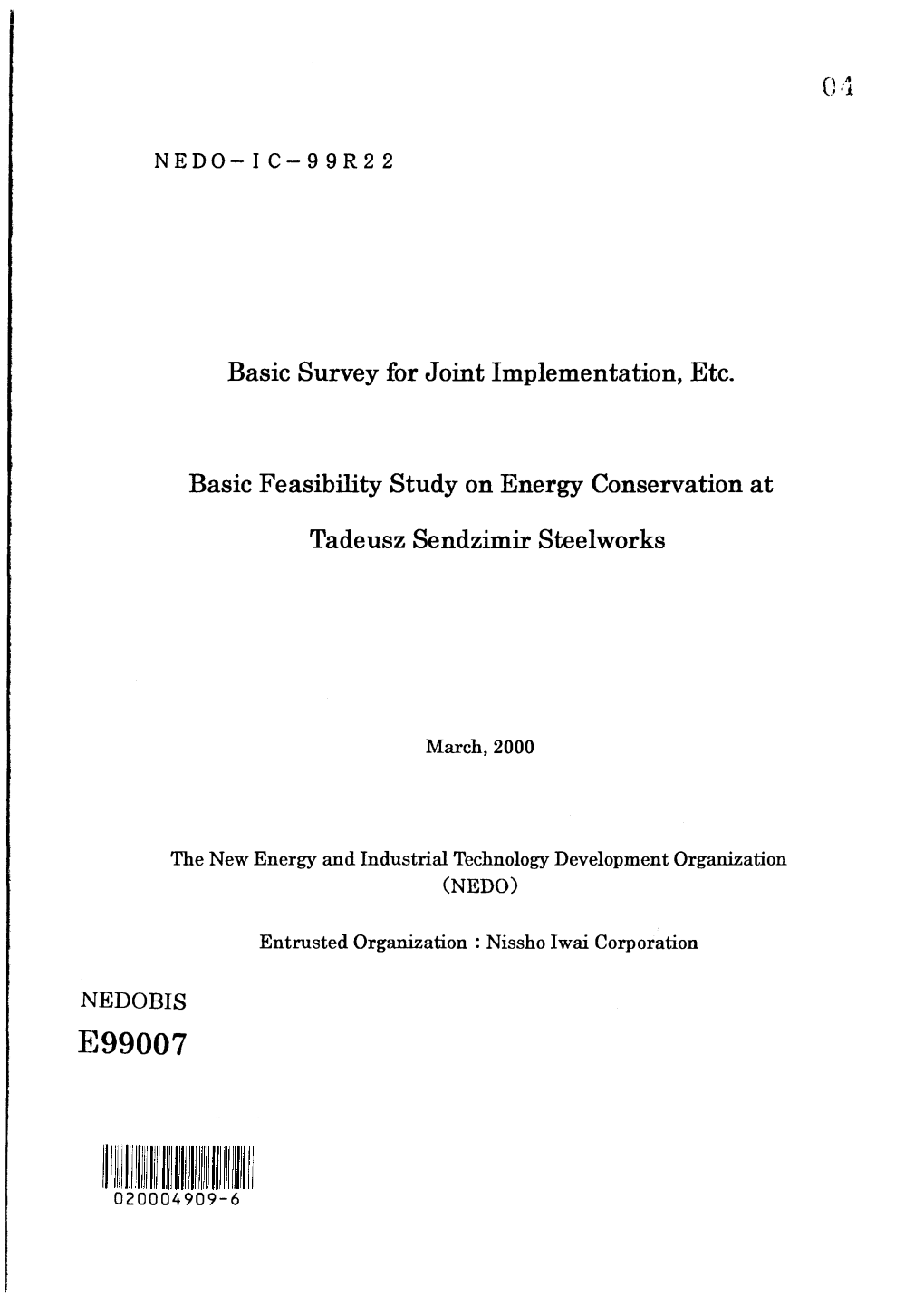
Load more
Recommended publications
-
{PDF} a Concise History of Poland Ebook Free Download
A CONCISE HISTORY OF POLAND PDF, EPUB, EBOOK Jerzy Lukowski,Hubert Zawadzki | 408 pages | 31 Jul 2006 | CAMBRIDGE UNIVERSITY PRESS | 9780521618571 | English | Cambridge, United Kingdom A Concise History of Poland PDF Book On one hand, there's no doubt about the fact that it is a concise book which presents events throughout the country's history in an accessible manner. Showing May 23, Afina rated it it was amazing. Doesn't hold a candle to Norman Davies' 'God's Playground', though that's not to say this isn't a good concise survey of Polish history which is fascinating. Jagiellonian Poland I ended up feeling a bit ambivalent about this presumption. Jerzy Lukowski , Hubert Zawadzki. Error rating book. There are fascinating facts that one does not come across in any of the other histories which add to the general background and it is written in a eminently readable fashion. Lindsay Freed rated it liked it Nov 12, Poland to 1. You have added ' ' to the following students:. Herodotus: Histories Book V. Learn More About the App Got it! Want to Read saving…. Jun 29, Wendy Jackson rated it liked it. Piast Poland? Susie rated it really liked it Jun 27, Published November 12th by Cambridge University Press first published Escape the Present with These 24 Historical Romances. A Concise History of Poland. Lukowski is a very familiar name amongst students of Polish History - his account of the Partitions is a classic and the partnership with Zawadzki This is beyond a doubt the best history of Poland I have read so far and I run a website on Polish History. -
The Public Library Service Provision to the Polish Community Living in Sheffield
The Public Library Service Provision to the Polish Community Living in Sheffield A study submitted in partial fulfilment of the requirements for the degree of Master of Arts in Librarianship at THE UNIVERSITY OF SHEFFIELD by Anna Listwon September 2007 ABSTRACT This dissertation intends to examine the public library service provision to the Polish community in Sheffield. Its main aim is to establish the library needs of the newly arrived Polish people and examine their opinion of the service provision. It also considers the needs and views of the established elderly Polish community on the library services and the opinions of library personnel with regard to their services and awareness of the newly arrived Polish people. The topics covered in the interviews and questionnaire were based on the subjects found in the literature relative to the subject, which has so far made sparse references to the Polish communities living in Great Britain. This study is qualitative and therefore the following methods were implemented: in-depth interviews with librarians and elderly Poles, and questionnaires with open-ended questions distributed to the young Poles in order to develop thorough understanding of the issues in question. The data gathered indicated that the Polish collection and Polish materials are of great significance to the Polish community. The Poles would like to be involved in the selection process and have more Polish books in their collection. The librarians had little knowledge of the scope of the demand for Polish books but were open to gaining more knowledge of the newly arrived Polish people. As a result of this research it is concluded that materials in the Polish language and having books in Polish by Polish authors are essential for the Polish community. -
Poland Country Assistance Review (In Two Volumes) Volume I: Main Report
Report No. Poland Country Assistance Review (In Two Volumes) Volume I: Main Report April 14, 1997 ________________________________________________________________________ Operations Evaluation Department Document of the World Bank Abbreviations and Acronyms ARPP Annual Review of Portfolio Performance ASAL Agriculture Sector Adjustment Loan ATF Agricultural Task Force BAS Budget Accounting System BGZ Polish Bank of Food Economy CAR Country Assistance Review CAS Country Assessment Strategy CEE Central and Eastern Europe CEM Country Economic Memorandum CMEA/COMECON Council of Mutual Economic Assistance COS Cost Accounting System CSIR Country Strategy Implementation Review CSP Country Strategy Paper DDSR Debt and Debt Service Reduction DHE District Heating Enterprises EAA European Association Agreement EBRD European Bank for Reconstruction and Development EC-PHARE European Commission Poland and Hungary Assistance in Restructuring Economies EC European Commission EU European Union ECA Europe and Central Asian Region ECU European Currency Unit (now called the Euro) EDI Economic Development Institute EFF Extended Fund Facility(IMF) EFSAL Enterprise and Financial Sector Adjustment Loan EIB European Investment Bank EP Employment Promotion Project EPSP Employment Promotion Service Project ERG Energy Restructuring Group ERR Economic Rate of Return Director-General, Operations Evaluation : Mr. Robert Picciotto Acting Director, Operations Evaluation Dept. : Mr. Roger Slade Acting Division Chief : Mr. Luis Ramirez Task Manager : Mr. Luis Landau Abbreviations -
Download (15MB)
https://theses.gla.ac.uk/ Theses Digitisation: https://www.gla.ac.uk/myglasgow/research/enlighten/theses/digitisation/ This is a digitised version of the original print thesis. Copyright and moral rights for this work are retained by the author A copy can be downloaded for personal non-commercial research or study, without prior permission or charge This work cannot be reproduced or quoted extensively from without first obtaining permission in writing from the author The content must not be changed in any way or sold commercially in any format or medium without the formal permission of the author When referring to this work, full bibliographic details including the author, title, awarding institution and date of the thesis must be given Enlighten: Theses https://theses.gla.ac.uk/ [email protected] Polish Foreign Policy Between East and West, 1989-2004 Ay§e Artun Submitted in fulfilment of the requirements for the degree of Doctor of Philosophy (Ph.D.) in the Department of Central and East European Studies University of Glasgow March 2007 Ay§e Artun, 2007 ProQuest Number: 10390705 All rights reserved INFORMATION TO ALL USERS The quality of this reproduction is dependent upon the quality of the copy submitted. In the unlikely event that the author did not send a com plete manuscript and there are missing pages, these will be noted. Also, if material had to be removed, a note will indicate the deletion. uest ProQuest 10390705 Published by ProQuest LLO (2017). Copyright of the Dissertation is held by the Author. All rights reserved. This work is protected against unauthorized copying under Title 17, United States C ode Microform Edition © ProQuest LLO. -
Ground Floor Ground Floor First
GROUND FLOOR FIRST FLOOR 8 6 5 wc 7 4 9 2 5 13 2 11 12 10 3 MAIN ENTRANCE 1 GROUND FLOOR decades long interest in the language and its status in rela- similar in both cases. In the situation after the collapse of European countries we can observe emerging political reli- 8. ODILE BERNARD SCHRÖDER, tion to reality. In works created in the 70s and 80s as a result the socialist project in Eastern Europe and a deep crisis of gions of the extreme right, deeply rooted in local, neopagan works from the series Revolution-Revelation (2017-2018) 1. MARIA TOBOŁA, Schadenfreude (2017-2018) of the observations of censorship language and the newspe- the American project, such an action has in equal measure traditions and promoting Euroscepticism. They all use similar Courtesy of the Pola Magnetyczne gallery ak of the Polish People’s Republic, the artist pondered the archaeological and utopian dimensions. logic in constructing the past, which can be summarised in In an iconic television game show of the late 90s., Idź na phenomenon of language as a means of communication. In the part of the installation involving the found footage, the slogan “make … great again”. The starting point for the works of Odile Bernard Schröder całość (Polish version of Let’s Make a Deal), one of the Through the use of words he reclaimed public space, and he two screens are displaying material edited from pieces of (b. 1962) are visual materials from the French presidential consolation prizes was a yearly stock of a Monosodium glu- deconstructed and problematised relationships between the Hollywood movies and social realist productions: social campaign of 2017. -
December 2020 Nato & the Ceec Pg
commemorating poland’s independence day Pg. 2 ■ commemoration of poland's independence in nj Pg. 3 ■ important info from pac – wisconsin division Pg. 4 ■ December 2020 nato & the ceec Pg. 5 ■ led by god’s providence Pg. 6 ■ polish news bytes Pg. 7 ■ polish american heritage month in erie county Pg. 8 ■ ignacy jan paderewski Pg. 9 ■ explore our polish heritage Pg. 10 ■ the breaking of the oplatek Pg. 13 ■ paaos virtual event Pg. 14 ■ from the bookshelf Pg. 15 Polish American Congress Volume 7, Number 6 Your in America!Voice DEADLINES FOR SUBMISSIONS Future PAC Newsletters will be sent out: Deadline for submission Publication date Friday, February 5, 2021 Friday, February 12, 2021 Friday, April 2, 2021 Friday, April 9, 2021 Friday, June 4, 2021 Friday, June 11, 2021 “Your Voice in America” is a bimonthly newsletter published by the Polish American Congress. The purpose of the newsletter is to offer PAC National Directors and PAC Executive Committee members the opportunity to share Dear Directors of the Polish American Congress, news and information about their state divisions and offices. The newsletter does not receive funds from any external I would like to wish you and your loved ones a Merry and source. The editor is Dr. Mark Pienkos. Healthy Christmas Holiday. This year has given us more challenges than we ever imagined. Let’s hope for a better 2021! Articles should be between 100 and 400 words. Some editing will be done to match our style guidelines and spatial constraints, As part of the New Year, I would like us all to bolster our as well as correcting grammatical errors. -
PDF File Generated From
OCCASION This publication has been made available to the public on the occasion of the 50th anniversary of the United Nations Industrial Development Organisation. DISCLAIMER This document has been produced without formal United Nations editing. The designations employed and the presentation of the material in this document do not imply the expression of any opinion whatsoever on the part of the Secretariat of the United Nations Industrial Development Organization (UNIDO) concerning the legal status of any country, territory, city or area or of its authorities, or concerning the delimitation of its frontiers or boundaries, or its economic system or degree of development. Designations such as “developed”, “industrialized” and “developing” are intended for statistical convenience and do not necessarily express a judgment about the stage reached by a particular country or area in the development process. Mention of firm names or commercial products does not constitute an endorsement by UNIDO. FAIR USE POLICY Any part of this publication may be quoted and referenced for educational and research purposes without additional permission from UNIDO. However, those who make use of quoting and referencing this publication are requested to follow the Fair Use Policy of giving due credit to UNIDO. CONTACT Please contact [email protected] for further information concerning UNIDO publications. For more information about UNIDO, please visit us at www.unido.org UNITED NATIONS INDUSTRIAL DEVELOPMENT ORGANIZATION Vienna International Centre, P.O. Box -
The Depiction of Poland and Poles in the Daily Telegraph, 2007-2010
The Depiction of Poland and Poles in The Daily Telegraph, 2007-2010 The Depiction of Poland and Poles in The Daily Telegraph, 2007-2010 By Dorota Kokowicz The Depiction of Poland and Poles in The Daily Telegraph, 2007-2010 By Dorota Kokowicz Reviewers: Prof. nadzw. dr hab. Leszek Pułka Prof. zw. dr hab. Kazimierz Wolny-Zmorzyński Prof. zw. dr hab. Andrzej Zawada Translated from Polish into English: Mathias Foit This book first published 2018 Cambridge Scholars Publishing Lady Stephenson Library, Newcastle upon Tyne, NE6 2PA, UK British Library Cataloguing in Publication Data A catalogue record for this book is available from the British Library Copyright © 2018 by Dorota Kokowicz All rights for this book reserved. No part of this book may be reproduced, stored in a retrieval system, or transmitted, in any form or by any means, electronic, mechanical, photocopying, recording or otherwise, without the prior permission of the copyright owner. ISBN (10): 1-5275-1124-3 ISBN (13): 978-1-5275-1124-8 TABLE OF CONTENTS List of Charts ............................................................................................. vii List of Tables .............................................................................................. ix Translator’s Note ......................................................................................... x Introduction ................................................................................................. 1 Part I: Public Relations – Theoretical Framework Chapter I ................................................................................................... -
The Polska Brand As a Challenge for Polish Cultural Diplomacy. Old Determinants, New Strategies1
Dorota Jurkiewicz-Eckert* The Polska Brand as a Challenge for Polish Cultural Diplomacy. Old Determinants, New Strategies1 Abstract: This paper analyses the evolution of the strategy employed by Polish cultural diplomacy for the promotion of a positive image of Poland in the context of a long-term strategy for developing the Polska brand in the world. The analysis takes the form of a case study and concerns selected aspects of the activity of the Adam Mickiewicz Institute – currently the most infl uential governmental institution responsible for promoting Poland in the world through culture. The paper presents the main determinants and challenges in shaping a coherent message about Poland and their infl uence on the current strategy for promoting the Polska brand through cultural diplomacy. The critical analysis places the Institute’s activities in the context of the priorities of Polish foreign policy and puts forward a thesis on the growing infl uence of the Institute on the development of Polish culture, Polish cultural diplomacy, and nation branding in Poland. Keywords: cultural diplomacy, public diplomacy, Polska brand, Polish foreign policy, nation branding, EU enlargement * Dorota Jurkiewicz-Eckert, MA – Centre for Europe, University of Warsaw. This article is the effect of research conducted by the author at the Centre for Europe between 2011 and 2014 and is a much extended version of the text published in: Poland and Tur- key on Europe – social, economic and political experiences and challenges, A. Adamczyk and P. Dubel (eds.), Warsaw 2014. 1 The remuneration for the Author was fi nanced by the Association of Copyright Collective Administration for Authors of Scientifi c and Technical Works (KOPIPOL), having its seat in Kielce, from fees collected under Article 20 and 201 of the Polish Act on Copyright and Neighbouring Rights. -
Łódzkie Studia Etnograficzne
THE CULINARIES ŁÓDZKIE STUDIA ETNOGRAFICZNE TOM LIV THE CULINARIES Polskie towarzystwo Ludoznawcze Wrocław – Łódź 2015 Editor-in-chief: Grażyna Ewa Karpińska Managing editors: Grażyna Ewa Karpińska, Aleksandra Krupa-Ławrynowicz Language editor (Polish): Krystyna Kossakowska-Jarosz Language editor (English): Robert Lindsay Hodgart Editorial secretary: Aleksandra Krupa-Ławrynowicz Editors: Anna Weronika Brzezińska, Małgorzata Chelińska Editorial board: Maja Godina Golja (Slovenska akademija znanosti in umetnosti, Ljubljana), Božidar Jezernik (Univerza v Ljubljani, Ljubljana), Katarzyna Kaniowska (Uniwersytet Łódzki, Łódź), Padraic Kenney (Indiana University, Bloomington), Bronisława Kopczyńska-Jaworska (Uniwersytet Łódzki, Łódź), Katarzyna Łeńska- Bąk (Uniwersytet Opolski, Opole), Ewa Nowina-Sroczyńska (Uniwersytet Łódzki, Łódź), Katarzyna Orszulak-Dudkowska (Uniwersytet Łódzki, Łódź), Peter Salner (Slovenska akademia vied, Bratyslava), Marta Songin-Mokrzan (Akademia Górniczo- Hutnicza, Kraków), Jan Święch (Uniwersytet Jagielloński, Kraków), Andrzej Paweł Wejland (Uniwersytet Łódzki, Łódź) Translators: Julita Mastalerz, Klaudyna Michałowicz Reviewers: Anna Weronika Brzezińska, Róża Godula-Węcławowicz, Piotr Grochowski, Janina Hajduk-Nijakowska, Renata Hryciuk, Iwona Kabzińska, Katarzyna Kaniowska, Krystyna Kossakowska-Jarosz, Izabella Main, Krystyna Piątkowska, Adam Pomieciński, Agata Stanisz, Andrzej Paweł Wejland Cover and title pages design: Michał Urbański Typesetting: HAPAX Kamil Sobczak The on-line version of the “Łódzkie Studia Etnograficzne” -
Government Capacity to Assure High Quality Regulation Analyses the Institutional Set-Up and Use of Policy Instruments in Poland
2(&'5(9,(:62)5(*8/$725<5()250 5(*8/$725<5()250,132/$1' )52075$16,7,21721(:5(*8/$725<&+$//(1*(6 *29(510(17&$3$&,7<72$6685( +,*+48$/,7<5(*8/$7,21 25*$1,6$7,21)25(&2120,&&223(5$7,21$1''(9(/230(17 ORGANISATION FOR ECONOMIC CO-OPERATION AND DEVELOPMENT Pursuant to Article 1 of the Convention signed in Paris on 14th December 1960, and which came into force on 30th September 1961, the Organisation for Economic Co-operation and Development (OECD) shall promote policies designed: -to achieve the highest sustainable economic growth and employment and a rising standard of living in Member countries, while maintaining financial stability, and thus to contribute to the development of the world economy; -to contribute to sound economic expansion in Member as well as non-member countries in the process of economic development; and -to contribute to the expansion of world trade on a multilateral, non-discriminatory basis in accordance with international obligations. The original Member countries of the OECD are Austria, Belgium, Canada, Denmark, France, Germany, Greece, Iceland, Ireland, Italy, Luxembourg, the Netherlands, Norway, Portugal, Spain, Sweden, Switzerland, Turkey, the United Kingdom and the United States. The following countries became Members subsequently through accession at the dates indicated hereafter: Japan (28th April 1964), Finland (28th January 1969), Australia (7th June 1971), New Zealand (29th May 1973), Mexico (18th May 1994), the Czech Republic (21st December 1995), Hungary (7th May 1996), Poland (22nd November 1996), Korea (12th December 1996) and the Slovak Republic (14th December 2000). -
Qr. 4. 2018 No. 7 ISSN 2543-9839 Warsaw, Poland, November 8, 2018
qr. 4. 2018 no. 7 ISSN 2543-9839 WARSAW, POLAND, NOVEMBER 8, 2018. POLISH PRIME MINISTER MATEUSZ MORAWIECKI (R) AND US SECRETARY OF ENERGY RICK PERRY (L) DURING A MEETING IN WARSAW. ON THE SAME DAY, A LONG-TERM CONTRACT FOR THE PURCHASE OF LIQUEFIED NATURAL GAS (LNG) WAS SIGNED BETWEEN THE STATE-OWNED POLISH OIL AND GAS COMPANY (PGNIG SA) AND THE AMERICAN CHENIERE MARKETING INTERNATIONAL LLP. THIS CONTRACT SPANS A LENGTH OF 24 YEARS AND COVERS AROUND 40 BILLION CUBIC METERS OF GAS. THIS IS YET ANOTHER STEP FOR POLAND TO DIVERSIFY GAS SUppLIES AND DEEPEN COOPERATION WITH THE UNITED STATES IN THE FIELD OF ENERGY SECURITY. © Paweł Supernak (PAP) Editorial Dear Readers, he collapse of communism and the restoration of the states previously locked behind the Iron Curtain formed a new geopolitical constellation in Central Europe. One successful attempt to take advantage of the Tsituation in the region was the launch of a new political initiative, which was expressed through an act of will to cooperate by the leaders of three countries: Czechoslovakia, Hungary, and Poland. In the framework of the Visegrad Group, these states, which are naturally related by a parallel historical background, cultural commonality, and geographic location, have further been consolidated by shared objectives for the future, the most noteworthy of which is the convergence of interests in foreign policy, and the emerging cooperation in terms of economy, transport, ecology, and science. Although the most vital tasks, including the entry of the V4 countries into the structures of the North Atlantic Alliance, and then into the European Union, have been accomplished, effective teamwork has made it possible to inaugurate a sense of local community alongside each state’s own coherent cultural and social identities.