Concept Design of Hybrid Crane Vessel Feasibility Study of Utilizing Electric Energy Storage Technology
Total Page:16
File Type:pdf, Size:1020Kb
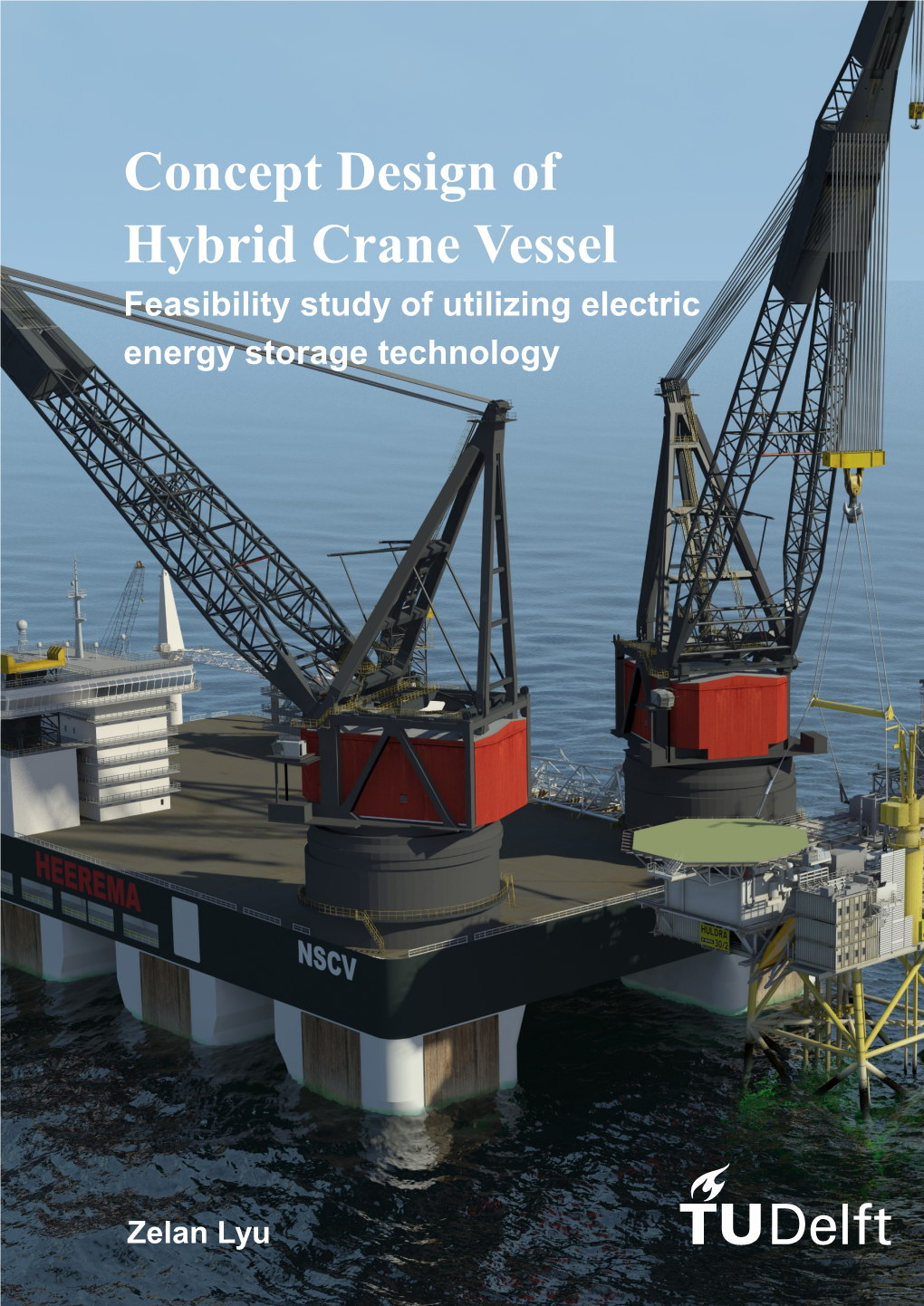
Load more
Recommended publications
-
Det Norske Veritas
DET NORSKE VERITAS Report Heavy fuel in the Arctic (Phase 1) PAME-Skrifstofan á Íslandi Report No./DNV Reg No.: 2011-0053/ 12RJ7IW-4 Rev 00, 2011-01-18 DET NORSKE VERITAS Report for PAME-Skrifstofan á Íslandi Heavy fuel in the Arctic (Phase 1) MANAGING RISK Table of Contents SUMMARY............................................................................................................................... 1 1 INTRODUCTION ............................................................................................................. 3 2 PHASE 1 OBJECTIVE..................................................................................................... 3 3 METHODOLOGY ............................................................................................................ 3 3.1 General ....................................................................................................................... 3 3.2 Arctic waters delimitation .......................................................................................... 3 3.3 Heavy fuel oil definition and fuel descriptions .......................................................... 4 3.4 Application of AIS data.............................................................................................. 5 3.5 Identifying the vessels within the Arctic.................................................................... 6 3.6 Identifying the vessels using HFO as fuel.................................................................. 7 4 TECHNICAL AND PRACTICAL ASPECTS OF USING HFO -
Assessment of Vessel Requirements for the U.S. Offshore Wind Sector
Assessment of Vessel Requirements for the U.S. Offshore Wind Sector Prepared for the Department of Energy as subtopic 5.2 of the U.S. Offshore Wind: Removing Market Barriers Grant Opportunity 24th September 2013 Disclaimer This Report is being disseminated by the Department of Energy. As such, the document was prepared in compliance with Section 515 of the Treasury and General Government Appropriations Act for Fiscal Year 2001 (Public Law 106-554) and information quality guidelines issued by the Department of Energy. Though this Report does not constitute “influential” information, as that term is defined in DOE’s information quality guidelines or the Office of Management and Budget's Information Quality Bulletin for Peer Review (Bulletin), the study was reviewed both internally and externally prior to publication. For purposes of external review, the study and this final Report benefited from the advice and comments of offshore wind industry stakeholders. A series of project-specific workshops at which study findings were presented for critical review included qualified representatives from private corporations, national laboratories, and universities. Acknowledgements Preparing a report of this scope represented a year-long effort with the assistance of many people from government, the consulting sector, the offshore wind industry and our own consortium members. We would like to thank our friends and colleagues at Navigant and Garrad Hassan for their collaboration and input into our thinking and modeling. We would especially like to thank the team at the National Renewable Energy Laboratory (NREL) who prepared many of the detailed, technical analyses which underpinned much of our own subsequent modeling. -
Guidelines for the Selection and Operation of Jack-Ups in the Marine Renewable Energy Industry
www.RenewableUK.com Guidelines for the Selection and Operation of Jack-ups in the Marine Renewable Energy Industry Issue 2: 2013 RUK13-019-02 2 Industry guidance aimed at jack-up owners operators, developers and contractors engaged in site-investigation, construction, operation and maintenance of offshore wind and marine energy installations. Acknowledgements RenewableUK acknowledges the time, effort, experience and expertise of all those who have contributed to this document. This Issue 2 of these guidelines was prepared for RenewableUK by London Offshore Consultants. This was in consultation with key consultees listed at the end of this document, RenewableUK members and key industry stakeholders. Status of this Document RenewableUK Health and Safety Guidelines are intended to provide information on particular technical, legal or policy issues relevant to the core membership base of RenewableUK. Their objective is to provide industry-specific guidance, for example where current information could be considered absent or incomplete. Health and Safety Guidelines are likely to be subject to review and updating, and so the latest version of the guidelines must be referred to. Attention is also drawn to the disclaimer below. Disclaimer The contents of these guidelines are intended for information and general guidance only, and do not constitute advice, are not exhaustive and do not indicate any specific course of action. Detailed professional advice should be obtained before taking or refraining from action in relation to any of the contents of this guide, or the relevance or applicability of the information herein. RenewableUK is not responsible for the content of external websites included in these guidelines and, where applicable, the inclusion of a link to an external website should not be understood to be an endorsement of that website or the site’s owners (or its products/services). -
Part I - Updated Estimate Of
Part I - Updated Estimate of Fair Market Value of the S.S. Keewatin in September 2018 05 October 2018 Part I INDEX PART I S.S. KEEWATIN – ESTIMATE OF FAIR MARKET VALUE SEPTEMBER 2018 SCHEDULE A – UPDATED MUSEUM SHIPS SCHEDULE B – UPDATED COMPASS MARITIME SERVICES DESKTOP VALUATION CERTIFICATE SCHEDULE C – UPDATED VALUATION REPORT ON MACHINERY, EQUIPMENT AND RELATED ASSETS SCHEDULE D – LETTER FROM BELLEHOLME MANAGEMENT INC. PART II S.S. KEEWATIN – ESTIMATE OF FAIR MARKET VALUE NOVEMBER 2017 SCHEDULE 1 – SHIPS LAUNCHED IN 1907 SCHEDULE 2 – MUSEUM SHIPS APPENDIX 1 – JUSTIFICATION FOR OUTSTANDING SIGNIFICANCE & NATIONAL IMPORTANCE OF S.S. KEEWATIN 1907 APPENDIX 2 – THE NORTH AMERICAN MARINE, INC. REPORT OF INSPECTION APPENDIX 3 – COMPASS MARITIME SERVICES INDEPENDENT VALUATION REPORT APPENDIX 4 – CULTURAL PERSONAL PROPERTY VALUATION REPORT APPENDIX 5 – BELLEHOME MANAGEMENT INC. 5 October 2018 The RJ and Diane Peterson Keewatin Foundation 311 Talbot Street PO Box 189 Port McNicoll, ON L0K 1R0 Ladies & Gentlemen We are pleased to enclose an Updated Valuation Report, setting out, at September 2018, our Estimate of Fair Market Value of the Museum Ship S.S. Keewatin, which its owner, Skyline (Port McNicoll) Development Inc., intends to donate to the RJ and Diane Peterson Keewatin Foundation (the “Foundation”). It is prepared to accompany an application by the Foundation for the Canadian Cultural Property Export Review Board. This Updated Valuation Report, for the reasons set out in it, estimates the Fair Market Value of a proposed donation of the S.S. Keewatin to the Foundation at FORTY-EIGHT MILLION FOUR HUNDRED AND SEVENTY-FIVE THOUSAND DOLLARS ($48,475,000) and the effective date is the date of this Report. -
Prevalence of Heavy Fuel Oil and Black Carbon in Arctic Shipping, 2015 to 2025
Prevalence of heavy fuel oil and black carbon in Arctic shipping, 2015 to 2025 BRYAN COMER, NAYA OLMER, XIAOLI MAO, BISWAJOY ROY, DAN RUTHERFORD MAY 2017 www.theicct.org [email protected] BEIJING | BERLIN | BRUSSELS | SAN FRANCISCO | WASHINGTON ACKNOWLEDGMENTS The authors thank James J. Winebrake for his critical review and advice, along with our colleagues Joe Schultz, Jen Fela, and Fanta Kamakaté for their review and support. The authors would like to acknowledge exactEarth for providing satellite Automatic Identification System data and for data processing support. The authors sincerely thank the ClimateWorks Foundation for funding this study. For additional information: International Council on Clean Transportation 1225 I Street NW, Suite 900, Washington DC 20005 [email protected] | www.theicct.org | @TheICCT © 2017 International Council on Clean Transportation TABLE OF CONTENTS Executive Summary ................................................................................................................. iv 1. Introduction and Background ............................................................................................1 1.1 Heavy fuel oil ................................................................................................................................... 2 1.2 Black carbon .................................................................................................................................... 3 1.3 Policy context ..................................................................................................................................4 -
Customs Bulletin Weekly, Vol. 53, December 11, 2019, No. 45
U.S. Customs and Border Protection ◆ CUSTOMS BROKER USER FEE PAYMENT FOR 2020 AGENCY: U.S. Customs and Border Protection, Department of Homeland Security. ACTION: General notice. SUMMARY: This document provides notice to customs brokers that the annual user fee that is assessed for each permit held by a broker, whether it may be an individual, partnership, association, or corpo- ration, is due by January 31, 2020. Pursuant to fee adjustments required by the Fixing America’s Surface Transportation Act (FAST ACT) and U.S. Customs and Border Protection (CBP) regulations, the annual user fee payable for calendar year 2020 will be $147.89. DATES: Payment of the 2020 Customs Broker User Fee is due by January 31, 2020. FOR FURTHER INFORMATION CONTACT: Melba Hubbard, Broker Management Branch, Office of Trade, (202) 325–6986, or [email protected]. SUPPLEMENTARY INFORMATION: Background Pursuant to section 111.96 of title 19 of the Code of Federal Regu- lations (19 CFR 111.96(c)), U.S. Customs and Border Protection (CBP) assesses an annual user fee for each customs broker district and national permit held by an individual, partnership, association, or corporation. CBP regulations provide that this fee is payable for each calendar year in each broker district where the broker was issued a permit to do business by the due date. See 19 CFR 24.22(h) and (i)(9). Broker districts are defined in the General Notice entitled, ‘‘Geographic Boundaries of Customs Brokerage, Cartage and Light- erage Districts,’’ published in the Federal Register on March 15, 2000 (65 FR 14011), and corrected, with minor changes, on March 23, 2000 (65 FR 15686) and on April 6, 2000 (65 FR 18151). -
Rules for the Classification and Construction of Sea-Going Ships
RUSSIAN MARITIME REGISTER OF SHIPPING RULES FOR THE CLASSIFICATION AND CONSTRUCTION OF SEA-GOING SHIPS PART I CLASSIFICATION Saint-Petersburg Edition 2019 Rules for the Classification and Construction of Sea-Going Ships of Russian Maritime Register of Shipping have been approved in accordance with the established approval procedure and come into force on 1 January 2019. The present edition of the Rules is based on the 2018 edition taking into account the amendments developed immediately before publication. The unified requirements, interpretations and recommendations of the International Association of Classification Societies (IACS) and the relevant resolutions of the International Maritime Organization (IMO) have been taken into consideration. The Rules are published in the following parts: Part I "Classification"; Part II "Hull"; Part III "Equipment, Arrangements and Outfit"; Part IV "Stability"; Part V "Subdivision"; Part VI "Fire Protection"; Part VII "Machinery Installations"; Part VIII "Systems and Piping"; Part IX "Machinery"; Part X "Boilers, Heat Exchangers and Pressure Vessels"; Part XI "Electrical Equipment"; Part XII "Refrigerating Plants"; Part XIII "Materials"; Part XIV "Welding"; Part XV "Automation"; Part XVI "Structure and Strength of Fiber-Reinforced Plastic Ships"; Part XVII "Distinguishing Marks and Descriptive Notations in the Class Notation Specifying Structural and Operational Particulars of Ships"; Part XVIII "Common Structural Rules for Bulk Carriers and Oil Tankers". The text of the Part is identical to that of the IACS Common Structural Rules; Part XIX "Additional Requirements for Structures of Container Ships and Ships, Dedicated Primarily to Carry their Load in Containers". The text of the Part is identical to IACS UR S11A "Longitudinal Strength Standard for Container Ships" (June 2015) and S34 "Functional Requirements on Load Cases for Strength Assessment of Container Ships by Finite Element Analysis" (May 2015). -
Crane and S-Lay Vessel Huisman Product Brochure 5000Mt Crane and S-Lay Vessel
5000MT CRANE AND S-LAY VESSEL HUISMAN PRODUCT BROCHURE 5000MT CRANE AND S-LAY VESSEL TABLE OF CONTENTS 01 DESCRIPTION 03 1.1 Vessel General 03 1.2 5000mt Offshore Mast Crane 04 1.3 600mt S-lay System 05 1.4 Design Options 06 1.5 Variable Draft Concept 07 1.6 Anti Heeling Systems 08 1.7 Accomodation 08 1.8 Power Generation and Propulsion 08 02 TECHNICAL SPECIFICATIONS 09 2.1 Vessel General 09 2.2 5000mt Offshore Mast Crane 10 2.3 600mt S-lay System 11 Before upgrade After upgrade 2 5000MT CRANE AND S-LAY VESSEL 1. DESCRIPTION 1.1 Vessel general The fully diesel electric, dynamically positioned (DP3) crane approx. 13000mt (approx. 10000mt after the S-lay System is vessel is equipped with a 5000mt Huisman Offshore Mast installed). Crane (OMC) and optionally a 600mt S-lay System. The crane and vessel are capable of fully revolving with 5000mt load. The vessel design is based on a variable draft concept. At The vessel is optimized for long transits at high speed up the transit draft the breadth of the vessel is limited which to 15 knots. The vessel is suitable for operating world-wide allows sailing at high speed and good motion characteristics including the following areas: China, Brazil, Gulf of Mexico, in waves. The pipe-laying operations and light lifts can be West of Africa, the North Sea, etc. also performed at this draft. For heavy lifts the vessel draft is increased. This increases the breadth of the water line in order The crane vessel is designed for multipurpose hoist- and- to provide sufficient stability for heavy lift operations. -
IHMA and UKHO PORT INFORMATION PROJECT
After a call for action during a IHMA congress in 2006 by the shipping industry, the IHMA and the UKHO have been working hard to come up with a structure for port information. IHMA and UKHO PORT INFORMATION PROJECT: FUNCTIONAL DEFINITIONS FOR NAUTICAL PORT INFORMATION TABLE OF CONTENTS INTRODUCTION ........................................................................................................................... 6 Background ............................................................................................................................................. 6 How this guide is organised:................................................................................................................ 7 Location Identifiers: ............................................................................................................................. 8 INDIVIDUAL PORT SECTIONS .................................................................................................................. 9 Port ...................................................................................................................................................... 9 Roads ................................................................................................................................................... 9 Deep Water Route .............................................................................................................................. 9 Traffic Separation Scheme ................................................................................................................. -
Dynamic Positioning During Heavy Lift Operations
Dynamic Positioning during Heavy Lift Operations Using fuzzy control techniques, Nonlinear Observer and H-Infinity Method Separately to Obtain Stable DP Systems for Heavy Lift Operations J. Ye Thesis for the degree of MSc in Marine Technology in the specialization of DPO – Marine Engineering Dynamic Positioning during Heavy Lift Operations By Jun Ye Performed at RH Marine This thesis (SDPO.16.007.m.) is classified as confidential in accordance with the general conditions for projects performed by the TUDelft. 31.03.2016 Company supervisor Responsible supervisor: E. El Amam Daily Supervisor(s): E. El Amam E-mail: [email protected] Thesis exam committee Chair/Responsible Professor: Prof. ir. J.J. Hopman Staff Member: Dr M. Godjevac Staff Member: Dr. R.R. Negenborn Company Member: E. El Amam Author Details Studynumber: 4274830 Author contact e-mail: [email protected] Summary Dynamic positioning has been developed for over half a century and is now widely used on board. However, the existing dynamic positioning system is not specially made with heavy lift vessels. This report is to solve the dynamic positioning problem during heavy lift operations. To fulfill this goal, the robustness and stability of the solutions are also considered. The solutions mentioned in this report are based on the RH Marine vessel model and the RH Marine dynamic positioning system. First the crane vessel model is reviewed and checked. Then the solutions are chosen and applied. At last the results are presented and analyzed. The stability of each solution is approached and the robustness of each solution is tested in Simulink. -
DNVGL-RU-SHIP-Pt5ch10 Vessels for Special Operations
RULES FOR CLASSIFICATION Ships Edition October 2015 Part 5 Ship types Chapter 10 Vessels for special operations The content of this service document is the subject of intellectual property rights reserved by DNV GL AS ("DNV GL"). The user accepts that it is prohibited by anyone else but DNV GL and/or its licensees to offer and/or perform classification, certification and/or verification services, including the issuance of certificates and/or declarations of conformity, wholly or partly, on the basis of and/or pursuant to this document whether free of charge or chargeable, without DNV GL's prior written consent. DNV GL is not responsible for the consequences arising from any use of this document by others. The electronic pdf version of this document, available free of charge from http://www.dnvgl.com, is the officially binding version. DNV GL AS FOREWORD DNV GL rules for classification contain procedural and technical requirements related to obtaining and retaining a class certificate. The rules represent all requirements adopted by the Society as basis for classification. © DNV GL AS October 2015 Any comments may be sent by e-mail to [email protected] If any person suffers loss or damage which is proved to have been caused by any negligent act or omission of DNV GL, then DNV GL shall pay compensation to such person for his proved direct loss or damage. However, the compensation shall not exceed an amount equal to ten times the fee charged for the service in question, provided that the maximum compensation shall never exceed USD 2 million. -
Greenhouse Gas Emissions from Global Shipping, 2013–2015 (Olmer Et Al., 2017)
Greenhouse gas emissions from global shipping, 2013-2015 Detailed methodology By: Naya Olmer Bryan Comer Biswajoy Roy Xiaoli Mao Dan Rutherford October 2017 Acknowledgments The authors thank Jen Fela and Joe Schultz for their review and support. The authors would like to acknowledge exactEarth for providing satellite Automatic Identification System data and processing support and Global Fishing Watch and IHS Fairplay for contributing vessel characteristics data. This study was funded through the generous support of the ClimateWorks Foundation. For additional information: International Council on Clean Transportation 1225 I Street NW, Suite 900 Washington DC 20005 USA © 2017 International Council on Clean Transportation ii Table of Contents 1 Introduction ........................................................................................................................... 1 2 Detailed methodology ........................................................................................................... 1 2.1 IHS data preprocessing .................................................................................................................1 2.2 AIS data preprocessing .................................................................................................................4 2.3 Matching AIS data with IHS data and GFW data ........................................................................7 2.4 Estimating ship emissions ..........................................................................................................11