Iron Foundries in Denmark and in Aalborg Before Henning Smith
Total Page:16
File Type:pdf, Size:1020Kb
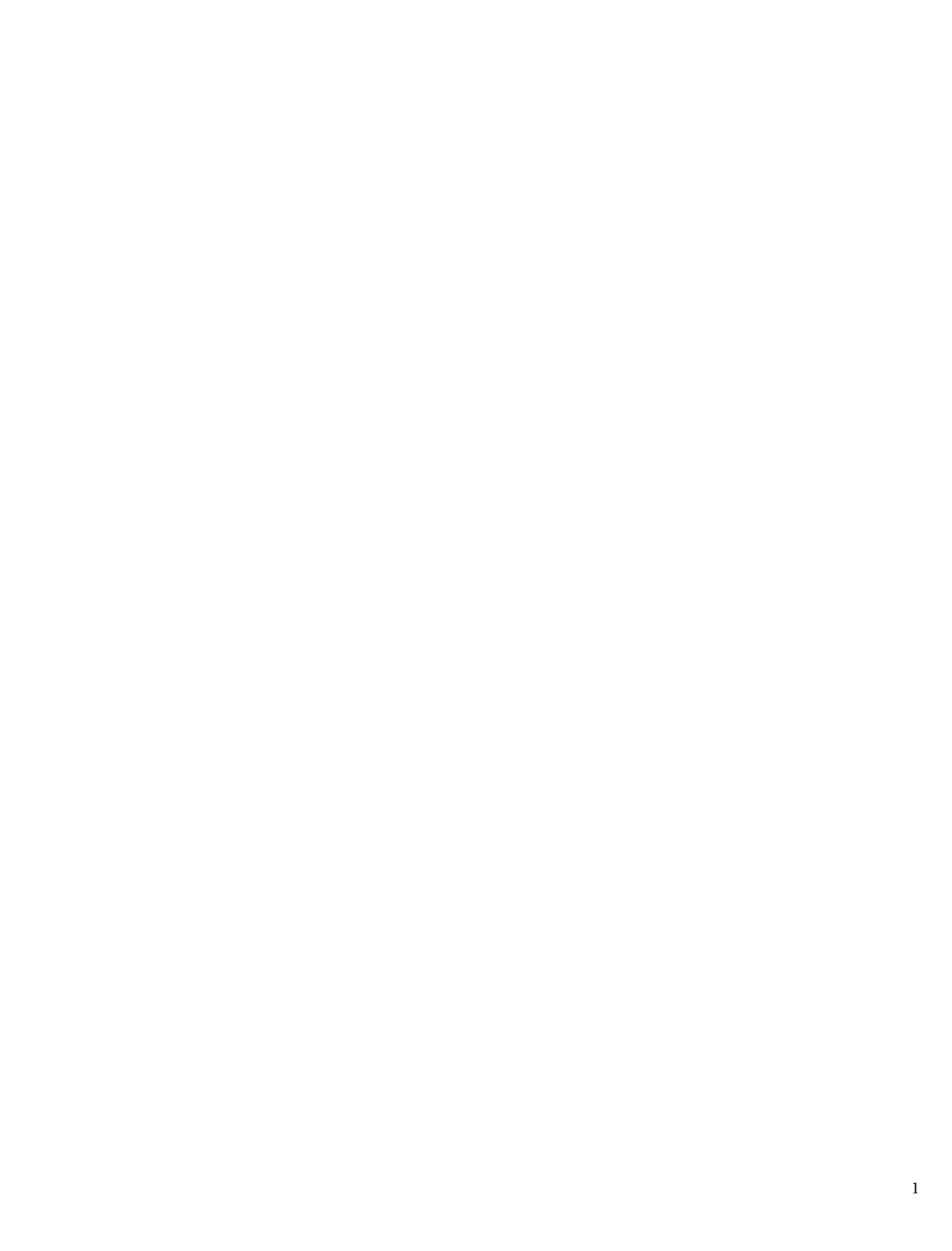
Load more
Recommended publications
-
Henriksen, Sune Ribergaard Page 1 of 1 12-05-2010
Page 1 of 1 Henriksen, Sune Ribergaard Fra: Brøndum, Jette på vegne af AAR - Aarhus hovedpostkasse Sendt: 28. april 2010 11:20 Til: Brøndum, Jette Cc: Henriksen, Sune Ribergaard Emne: VS: Kommentar vedrørende flytning af risteperron ved Lindholm Station Fra: Jørgen Harbøll [mailto:[email protected]] Sendt: 28. april 2010 08:45 Til: AAR - Aarhus hovedpostkasse Emne: Kommentar vedrørende flytning af risteperron ved Lindholm Station Ved flytning af denne perron de 350 meter nordpå, vil det så ikke bare betyde, at I flytter problemet ud i Kolonihavehusområdet? Hvad med at vente lidt – og så arbejde ihærdigt på, at endestationen skal være ved Lufthavnen? Venlig Hilsen Jørgen Harbøll 12-05-2010 05-05-10 Vedr. ”Forlængelse af spor 0 og flytning af risteperron ved Lindholm Station” Kommentar til oplægget om flytning. Jeg kan forstå man ønsker at flytte det nuværende anlæg længere nordpå og som følge af det forslag vil vi komme forholdsvis tæt på. Der er vel ca 40 m over fra vores have og til det nuværende banelegeme. Hvis anlægget bliver flyttet herud og man placerer det vest for banelegemet så vil vi komme til at få det nærmere. Hvordan det vil komme til at påvirke os er svært at sige, men på baggrund af de gener vi af og til oplever fra virksomheder der ligger på Voerbjergvej nordøst for os små 100 m væk er det lydt nok. For et par år siden standsede man også med Skagens banen, tror jeg det var, med at køre godstog. De år de kørte fik man lært at stå tidligt op når det kom forbi om morgenen klokken 5 med 50 godsvogne eller mere. -
Systematic Professional Services
Systematic Professional Services Together we achieve the best 2 l SITAWARE Enhancing your expertise Planning, installing and maintaining a Command & Control (C2) system is no small task. Hardware and software need to be considered, as do legacy systems, doctrine, operational procedures and interoperability. Everything must be efficiently integrated if the new system is to provide your armed forces with the valuable benefits expected from a modern C2 system Managing such a complex assignment alone advice for particular phases, the amount of knowledge can be daunting. This is where Systematic gained by our specialists is impressive. Professional Services can help you to avoid You can take full benefit from our vast experience costly mistakes, pitfalls and difficulties and all the knowledge we have gained along the way. throughout the entire lifecycle of the project Systematic Professional Services can provide you with full support. Our range of services complements Proven ability, practical know-how our off-the-shelf SitaWare C2 and IRIS interoperability For over 25 years Systematic experts have worked with software suites, and has been created to embrace armies, navies and air forces in over 40 countries to the entire lifecycle of a C2 system: from initial design, provide specialist consultancy regarding C2 systems. installation and adaptation to familiarisation, operation From directing entire projects, to providing specific and through life capability management. Systematic Professional Services l 3 “I meet with the customer... ...where ever they are. I analyse and tailor the right solution to fit the customer’s needs. It’s my job to work with them and anticipate possible issues, whether it be with deployment for the end-users or integration with existing third party software. -
Arne Jensen , En Vejgaard Dreng Fortæller
Arne Jensen. En Vejgaard dreng fortæller om sin tid i Vejgaard Fra 1934 – 1951. 1 En Vejgaard dreng fortæller. Arne Jensens beretning om hans tid i Vejgaard. Det hele begyndte i 1934. Onsdag før påske den 28. marts nedkom min mor, Signe Marie Jensen (født Poulsen) med mig. Klokken var 12.30 og til at bistå med fødslen var, foruden jordemoderen, fru Jensen, som boede i stueetagen. Fødslen var en hjemmefødsel og foregik i mine bedsteforældres hjem på Østervangsvej 29 i Vejgaard, som dengang var en selvstændig forstadskommune til Aalborg. Min far, Erhard Johan Wittrup Jensen, var ikke til stede ved fødselstidspunktet, idet han stadig sejlede som søfyrbøder og først afmønstrede 2 måneder senere og ifølge min mor medbragte en fin barnevogn. Senere fremstillede han både en barneseng til mig og en kommode til mit tøj for far var en dygtig håndværker. Min far og mor fik den første tid bolig i et værelse hos mormor og morfar, og mens de boede der, blev jeg døbt den 21. maj 1934 og fik navnet Arne Jensen. Min barnedåb den 21. maj 1934 2 Vejgaard – Frederikshavn Tur/retur Birthes fødsel Far havde intet arbejde og da han var fra Frederikshavn, søgte han og fik arbejde på Frederikshavn Skibsværft hen på sommeren 1934 så vi flyttede til Frederikshavn, hvor vi den første tid boede til leje hos en af fars ungdomskammerater. Her boede vi en kort tid, indtil far fandt en lejlighed på Emilievej og senere på Ingeborgvej. I september 1935 kom der familie forøgelse. Den 9. september fødtes min lillesøster, som kom til at hedde Birthe og hun blev ligesom min far Frederikshavner. -
Nye Byroller I Kommuneplanen - Kort Fortalt
NYE BYROLLER I KOMMUNEPLANEN - kort fortalt godt i gang med Kommuneplan 2009 Nye byrollerMiljøministeriet i kommuneplanen | Realdania Forord Aalborg Kommune byder på et bredt udvalg af spændende og attraktive oplandsbyer og enestående naturkva- liteter. Udviklingsmulighederne i den enkelte oplandsby bestemmes ikke mindst af evnen til at udnytte egne styrker og muligheder i det regionale bynetværk. Bystrukturen består udover Aalborg, af en række mellemstore byer som Nibe, Svenstrup, Storvorde, Hals og Vodskov samt mange mindre byer og landsbyer. Kommunalreformen har skabt anledning til at se nærmere på de mange oplandsbyer for at kunne udvikle byer, der tager udgangspunkt i dets befolkning, relationer, styrker og forskelligheder. Til det arbejde har Aalborg Kommune har modtaget støtte af Realdania til at udvikle et nyt bykoncept, der erstatter det tidligere bymønster i amtets og de 4 sammenlægningskommuners planlægning. Resultatet vil i Kommuneplan 2009 for Aalborg Kommune, der snart offentliggøres. Dette hæfte samler ”kort fortalt” op på nogle af de spændende resultater projektet ’Nye byroller i kommu- neplanlægningen’ har resulteret i. Projektet er udarbejdet i perioden 2007-09 og for mere information kan henvises til: Plan09’s hjemmeside www.plan09.dk/Aalborg Aalborg kommunes hjemmeside www.aalborgkommune.dk Ny byroller i kommuneplanen - kort fortalt Udgivet af | Aalborg Kommune med støtte fra Plan09 Styregruppe | Peter Mikkelsen, Jens-Erik Qourtrup, Jørn Hviid Carlsen og Mette Kristoffersen, Aalborg Kommune Arbejdegruppe | Jesper Schultz, -
Storvorde-Sejlflod Fattigkommission 1803 Mødet På Klarupgaard 15. December 1803 Mødtes En Gruppe Mænd På Herregården Klaru
Storvorde-Sejlflod fattigkommission 1803 Mødet på Klarupgaard 15. december 1803 mødtes en gruppe mænd på herregården Klarupgaard. Nærmere bestemt drejede det sig om gårdmændene Niels Poulsen og Christen Nielsen fra Storvorde sogn, mens Sejlflod sogn var repræsenteret ved Christen Callesen og Lars Sørensen. Til stede var desuden Klarupgaards ejer, proprietær Werner Christensen (1759-1819) og præsten i Storvorde og Sejlflod Rudolf Frederich Lassen (1760-1811). Endelig var der Hornum-Fleskums herreds dommer og politimester, herredsfoged Niels Bassesen, der havde taget turen fra Nibe til Klarupgaard. Anledningen til mødet var det ”Reglement for Fattigvæsnets Indretning og Bestyrelse paa Landet i Danmark”, der var blevet udstedt 5. juli 1803. Det var regeringens hensigt, at det nye reglement for første gang siden 1708 skulle reformere, organisere og effektivisere uddelingen af hjælpen til de mennesker, der levede på landet og som ikke ved egne kræfter og på lovlig vis kunne forsørge sig selv. Til det formål skulle der nu i hvert pastorat oprettes en fattigkommission til varetagelse af dette arbejde. Selvskrevne til at få sæde i fattigkommissionen var sognets største lodsejer, præsten og den lokale politimester. Eftersom Storvorde og Sejlflod havde fælles præst, repræsenterede Lassen begge sogne. Hver fattigkommission var ansvarlig overfor først den lokale amtmand og herredsprovst samt kongen i København. De tre faste medlemmer skulle som deres første embedshandling i fællesskab udpege tre-fire mænd fra sognet til at bistå dem i arbejdet med reglementets gennemførelse. Christensen, Lassen og Bassesen var i den forbindelse blevet enige om at vælge to mænd fra hvert af de to sogne, så det er i den forbindelse at vi også træffer Niels Poulsen, Christen Nielsen, Christen Callesen og Lars Sørensen på Klarupgaard den dag i december. -
Report of AIS EWG 5/2003
HELSINKI COMMISSION – Baltic Marine Environment Protection Commission Expert Working Group for Mutual Exchange and AIS EWG 5/2003 Deliveries of AIS data (AIS EWG) Document No. 1/Rev. 1 Fifth Meeting 29 April 2003 Copenhagen, Denmark 29-30 April 2003 REPORT OF THE FIFTH MEETING OF THE EXPERT WORKING GROUP FOR MUTUAL EXCHANGE AND DELIVERIES OF AIS DATA (AIS EWG) OF THE HELSINKI COMMISSION 1. The fifth meeting of the Expert Working Group for Mutual Exchange and Deliveries of AIS data (AIS EWG) was held in Copenhagen, Denmark, on 29-30 April 2003, on the basis of the report of the fourth meeting of the Expert Working Group (AIS EWG 4/2003, document no. 4/Rev.1). 2. The meeting was attended by delegations from Denmark, Estonia, Finland, Germany, Latvia, Lithuania, Poland, Russia and Sweden. Mr. Terje Alling and Mr. Kjell Arne Aarmo from the Norwegian National Coastal Administration participated as invited guests. The list of participants is attached as Annex 1. 3. Mr. Benny Pettersson from Sweden, Chairman of the Expert Working Group, chaired the meeting. Ms. Serpil Pedersen, Assistant at the Royal Danish Administration of Navigation and Hydrography, acted as Secretary of the meeting. 4. The agenda for the meeting is attached as Annex 2. 5. In his opening remarks the Chairman referred to the last meeting in Finland and to the accomplishments made during this meeting. The Chairman further informed that Sweden will update the AIS Network SW in the middle of May and will be able to deliver data in IEC format hereafter. The Chairman also stated that the action plan and time schedule adopted at the last meeting should be reconsidered during the fifth meeting in order to assess whether or not these can be fulfilled. -
'Accentuate the Positive': Getting the Most out of ERASMUS+
AEC Annual Meeting for International Relations Coordinators, 26-28 September 2014, Aalborg th th Aalborg, 26 -28 September 2014 The Royal Academy of Music Aarhus/Aalborg Denmark 'Accentuate the Positive': getting the most out of ERASMUS+ 1 AEC Annual Meeting for International Relations Coordinators, 26-28 September 2014, Aalborg Thanks to our sponsors: www.earmaster.com www.asimut.com The AEC team would like to express special thanks to the Director of the Royal Academy of Music in Aarhus/Aalborg Thomas Winther, and his team, in particular Martin Granum, Charlotte Pilgaard Andersen and Keld Hosbond for their wonderful support in organizing the AEC Annual Meeting for IRCs 2014 in Aalborg 2 AEC Annual Meeting for International Relations Coordinators, 26-28 September 2014, Aalborg Contents Introduction: 'Accentuate the Positive': getting the most out of ERASMUS+ .................................................. 4 Programme ........................................................................................................................................................ 6 Special Features ............................................................................................................................................... 10 Session for First Time Delegates .................................................................................................................. 10 New AEC Website Helpdesk ........................................................................................................................ 10 Bar Camp -
We Want You Magazine.Pdf
We Want You 2 City of Aalborg - We Want You City of Aalborg - We Want You 3 We Want You Some cities are huge, dynamic metropolises. Some towns are small and quaint. Others, like Aalborg, are exactly like in the story of Goldi- locks and the Three Bears: just right. In Aalborg, it is truly our expe- in population and workforce, as rience that one size fits all. From thousands of new students and our huge shopping centres to our workers join us every year, result- peaceful harbour front, from our ing in a demographic trend that is pulsating night life to the stillness rendering Aalborg younger of our parks, from our buzzing air- and younger. port to our safe, clean and attrac- tive residential areas - Aalborg has This development is influencing a place to suit any mood. many aspects of life in Aalborg and almost every part of the city Why the sales pitch? Because we where building sites are the visible want you to join our workforce. proof; industrial sites are trans- Your talents and skills are needed formed into homes and offices for in our vibrant business com- knowledge based businesses. munity, in our many public and private companies and organisa- Welcome to our rapidly growing tions. Whatever your profession, city. Whether you’re one of the we’re sure that you’re just right many new citizens in Aalborg or for Aalborg. just considering moving here, know that you are very welcome Judging by Aalborg’s demo- and that you have much to look graphic evolution, you would think forward to. -
1.2 Comparison of Aalborg and Jönköping
METROBUSSYSTEMER Synopsis I Aalborg blev metrobussystemet introduceret i april 2004, som følge af et faldende passagertal i den kollektive trafik. Inspirationen kom fra Jönköping i Titel: Metrobussystemer Sverige, hvor indførelsen af et stambusnet efter princippet ”Tænk sporvogn - kør bus” har vendt passagernedgang til passagerfremgang. Tema: Afgangsprojekt Dette projekt er den første evaluering af metrobussystemet i Aalborg, og har til Projektperiode: 1. februar - 13. juni 2008 formål at fastlægge, om omlægningen af den kollektive trafik i 2004 har opnået den ønskede effekt. Evalueringen er foretaget på baggrund af en række Deltagere: Majken Andersen passagertællinger, kundeundersøgelser og GPS-data, som udgør evalueringens primære datagrundlag. Vejleder: Niels Melchior Jensen Som metrobussystemet ser ud i dag, har omlægningen af den kollektive trafik Oplagstal: 3 ikke ændret væsentligt på kvaliteten af trafiktilbuddet. Frekvensen er, efter nedskæringer, på samme niveau som før omlægningen, og fremkommeligheden Sideantal: 147 for busserne er forringet. Dette kommer også til udtryk i kommunens samlede passagertal, der over perioden er faldet ca. 11 %. På metrobusnettet har kun metrobus 2 haft fremgang, mens de øvrige linjer har mistet passagerer. En sammenligning af metrobussystemet i Aalborg med stambussystemet i Jönköping har endvidere belyst, hvorfor Aalborg ikke har kunnet opnå samme positive resultater som Jönköping. Først og fremmest har kompromis fra politisk side medført nedskæringer, der har forringet kvaliteten væsentligt. Ydermere har de økonomiske begrænsninger, ikke gjort det muligt at forbedre fremkommeligheden for busserne på samme niveau, som det er gjort i Jönköping. Majken Andersen Odense står i dag i samme situation, som Aalborg gjorde før omlægningen i 2004. Det ønskes derfor at introducere et metrobussystem med det formål at vende den negative passagerudvikling. -
Welcome to Aalborg Psychiatric Summer School 2021 Contents
Welcome to Aalborg Psychiatric Summer School 2021 According to New York Times, Aalborg was the 8th best place to visit in 2019 Contents Welcome to Aalborg Psychiatric Summer School 2021 .................................................................................... 1 Arriving in Aalborg ............................................................................................................................................. 2 Arriving by plane ............................................................................................................................................ 2 Arriving by bus/train ...................................................................................................................................... 2 Accommodation in Aalborg ............................................................................................................................... 3 Hotels ............................................................................................................................................................. 3 Other types of accommodation .................................................................................................................... 3 What to see and do ........................................................................................................................................... 5 Practical information ......................................................................................................................................... 5 Venue ................................................................................................................................................................ -
Fugleskydning 2016
VI MØDES ATTER PÅ BAKKEN TAG MED TIL POKAL- SKYDNING I HADERSLEV BAKKEFOLKET • NR. 63 DET BRODERLIGE SKYDESELSKAB DET BRODERLIGE SKYDESELSKAB BAKKEFOLKET NR. 63 • AUGUST 2016 BAKKEFOLKET NR. 63 • AUGUST 2016 INDHOLD VELKOMMEN TIL FUGLESKYDNING 2016 INDHOLDSFORTEGNELSE ARTIKLER OG ANNONCER Igen i år vil Brødrene samles på Bakken til fugleskydning. Alle Brødre kan bruge Bakkefolket Kolofon ..................................................................... 2 Det vil ske i godt samsæde og med respekt for temaet om at som talerør, dog ikke til politiske eller Leder ......................................................................... 3 gavne og fornøje. Blandt de herligste stunder er gensynene religiøse indlæg, men gerne til løst Selskabets bestyrelse .............................................. 4 med de mange gode Brødre fra vore venskabsgilder fra nær og fast om Selskabet og livet blandt Program for fugleskydning 2016 ............................... 4 Brødre på Bakken og andre steder. og fjern. Det er med vemod, jeg tænker på, at der er et par Formandens beretning på generalforsamlingen ........ 5 Brødre, som vi aldrig mere vil se. Men vi har været der, og Brodergolf i Aarhus ................................................... 9 Ansvarshavende redaktør deltaget på deres sidste rejse. Og for de gamle som faldt …! Damernes udflugt i Flensborg ................................ 10 Hans Jørgen Jensen véd vi, at der er nye på vej. Højtidsfest i Lund .................................................... 11 Vivaldisvej 117, Frejlev, 9200 Aalborg -
STUDENT HANDBOOK 2018 Dear Freshman! CONTENTS Welcome to Aalborg, Welcome to University, and Welcome to This Year’S Student Handbook
STUDENTERSAMFUNDETS STUDENT HANDBOOK 2018 Dear freshman! CONTENTS Welcome to Aalborg, welcome to university, and welcome to this year’s Student Handbook. 4-21 Welcome to Aalborg University The Student Handbook is written for you as a freshman, and hopefully you will find the handbook useful. In the section “Aalborg University” you can find practical advice on your 6-7 Welcome by rector, Per Michael Johansen first day of study, on the PBL model and on Aalborg University’s IT systems. In “Life as a 8-11 Study-start party 2018 student” you can read about topics such as your chance to get influence on the university, 12-15 PBL-model volunteering, study techniques, events and leisure activities. Finally, in the “Aalborg” section, 16-17 Studying abroad you can read more about the city where you will be studying and about local sights, as well as find maps of Aalborg. 18-21 IT-guide I wish you a pleasant start of term and a pleasant time at Aalborg University! Best regards 22-53 Study life Marianne Roed Abrahamsen Editor-in-chief, Student Handbook 2018 24-25 Welcome by the chairman of the student society 26-27 Students’ politics 28-29 The bars Editor Text 30-31 Study technique Marianne Roed Abrahamsen, student Alexander Kokkedal, student 34-35 Opinion start of term [email protected] Majken Ravnkilde, student 36-37 Intro event UniRun’18 Dianna Korshøj, student Layout Emil Njor, student 40-43 Voluntary work Emil Kongsgaard Guldager, student Mie Louise Nielsen, student 46-49 Student’s influence [email protected] Malene Gadegaard,