ADAMS/Aircraft MSC.ADAMS Industry–Specific Product
Total Page:16
File Type:pdf, Size:1020Kb
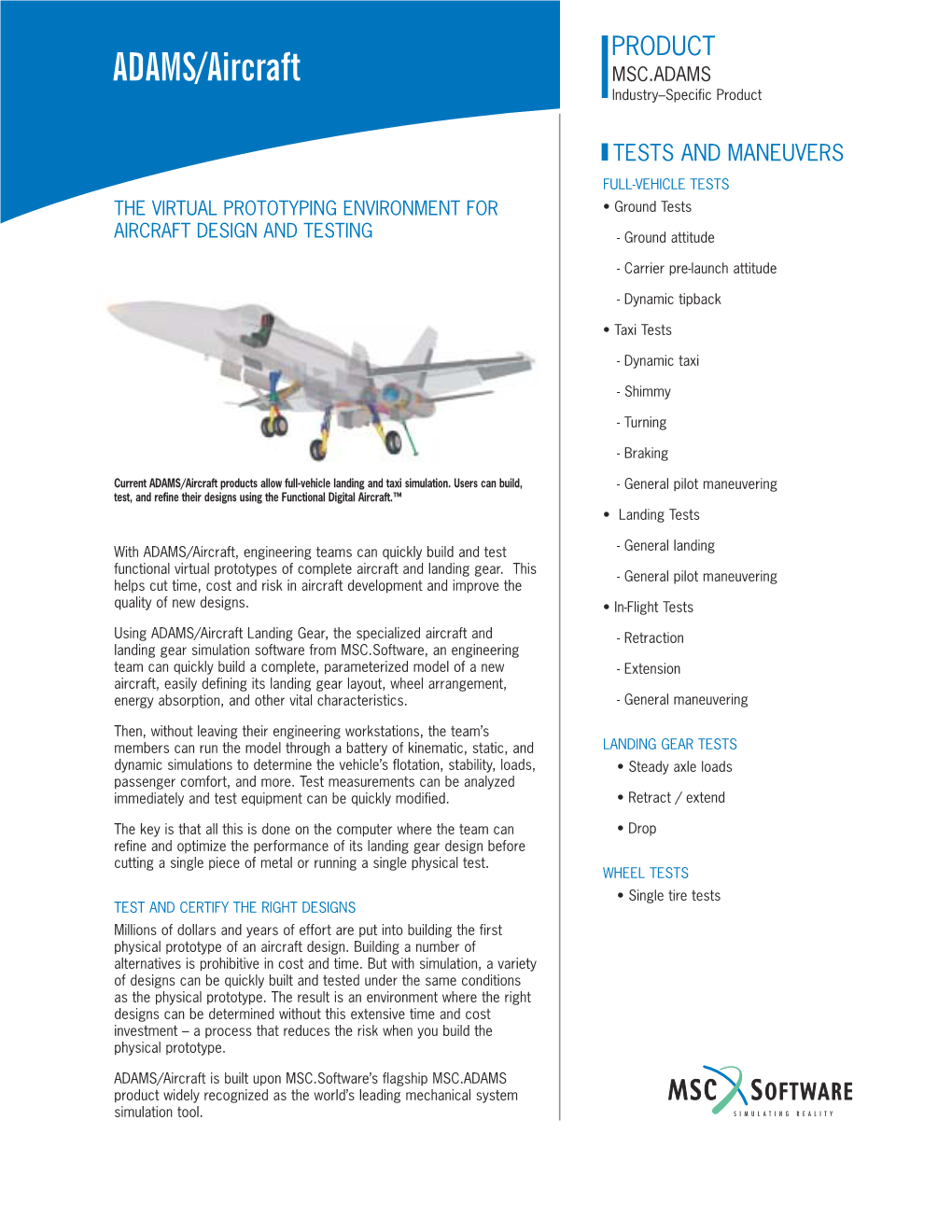
Load more
Recommended publications
-
Bell 429 Product Specifications
BELL 429 SPECIFICATIONS BELL 429 SPECIFICATIONS Publisher’s Notice The information herein is general in nature and may vary with conditions. Individuals using this information must exercise their independent judgment in evaluating product selection and determining product appropriateness for their particular purpose and requirements. For performance data and operating limitations for any specific mission, reference must be made to the approved flight manual. Bell Helicopter Textron Inc. makes no representations or warranties, either expressed or implied, including without limitation any warranties of merchantability or fitness for a particular purpose with respect to the information set forth herein or the product(s) and service(s) to which the information refers. Accordingly, Bell Helicopter Textron Inc. will not be responsible for damages (of any kind or nature, including incidental, direct, indirect, or consequential damages) resulting from the use of or reliance on this information. Bell Helicopter Textron Inc. reserves the right to change product designs and specifications without notice. © 2019 Bell Helicopter Textron Inc. All registered trademarks are the property of their respective owners. FEBRUARY 2019 © 2019 Bell Helicopter Textron Inc. Specifications subject to change without notice. i BELL 429 SPECIFICATIONS Table of Contents Bell 429 ..................................................................................................................................1 Bell 429 Specification Summary (U.S. Units) ........................................................................4 -
Remote ID NPRM Maps out UAS Airspace Integration Plans by Charles Alcock
PUBLICATIONS Vol.49 | No.2 $9.00 FEBRUARY 2020 | ainonline.com « Joby Aviation’s S4 eVTOL aircraft took a leap forward in the race to launch commercial service with a January 15 announcement of $590 million in new investment from a group led by Japanese car maker Toyota. Joby says it will have the piloted S4 flying as part of the Uber Air air taxi network in early adopter cities before the end of 2023, but it will surely take far longer to get clearance for autonomous eVTOL operations. (Full story on page 8) People HAI’s new president takes the reins page 14 Safety 2019 was a bad year for Part 91 page 12 Part 135 FAA has stern words for BlackBird page 22 Remote ID NPRM maps out UAS airspace integration plans by Charles Alcock Stakeholders have until March 2 to com- in planned urban air mobility applications. Read Our SPECIAL REPORT ment on proposed rules intended to provide The final rule resulting from NPRM FAA- a framework for integrating unmanned air- 2019-100 is expected to require remote craft systems (UAS) into the U.S. National identification for the majority of UAS, with Airspace System. On New Year’s Eve, the exceptions to be made for some amateur- EFB Hardware Federal Aviation Administration (FAA) pub- built UAS, aircraft operated by the U.S. gov- When it comes to electronic flight lished its long-awaited notice of proposed ernment, and UAS weighing less than 0.55 bags, (EFBs), most attention focuses on rulemaking (NPRM) for remote identifica- pounds. -
R66 Police Brochure
The R66 POLICE HELICOPTER offers law enforcement a reliable, high-performance TURBINE POLICE turbine helicopter that is economical and easy to maintain. R66 HELICOPTER The four-place R66 Police Helicopter meets the latest FAA crashworthiness regula- tions. Its aerodynamic fuselage optimizes airspeed and fuel economy, allowing the helicopter to remain on station for up to three hours. The R66 Police Helicopter comes turn-key equipped with the latest in navigation and surveillance technology. • Wescam MX-10 Infrared Camera • Garmin G500H 1060 TXi PFD/MFD (compatible with optional autopilot) • Garmin GTN 635 Touchscreen GPS/COM • SX-7 Starsun Searchlight System, 25-30 Million Candlepower Searchlight • Two 6-Channel Audio Controllers • Lithium-ion Battery • Fold-Away Color Monitor • Garmin GTX 335 Transponder A wide variety of upgrades and options are available including: searchlight-to-cam- era slaving system, 5-point shoulder harness system (front seats), P/A speaker and siren, LoJack provisions, moving map systems, Garmin Synthetic Vision Technol- ogy, a selection of UHF, VHF, and 800 MHz police radios, SAS/Autopilot, radar altime- ter, air conditioning, and auxiliary fuel tank. Wescam MX-10 Infrared Camera TURBINE POLICE R66 HELICOPTER SPECIFICATIONS Engine Rolls Royce RR300 turbine Horsepower 300 shp turboshaft; derated to 270 shp for takeoff and 224 shp continuous Maximum Gross Weight 2700 lb (1225 kg) Approximate Empty Weight 1421 lb (644 kg) (including oil, avionics and standard police package) Fuel Capacity (73.6 gal) 493 lb (224 kg) Pilot, Passengers and Cargo 786 lb (357 kg) with Standard Fuel Cruise Speed at Maximum up to 110 kts (127 mph) Gross Weight Maximum Range approx 325 nm (602 km) STANDARD EQUIPMENT (no reserve) • Hydraulic power controls Hover Ceiling IGE over 10,000 ft • Bladder fuel tank at Max. -
Aviation Week & Space Technology Student Edition
Chinese Aviation Revealed Fly by Wire How Quick a Recovery? U.S./UK Hypersonic Thresher for All $14.95 APRIL 6-19, 2020 REMAKING THE U.S. MARINES Aviation Week Workforce Initiative Supported by: The Wings Club Digital Edition Copyright Notice The content contained in this digital edition (“Digital Material”), as well as its selection and arrangement, is owned by Informa. and its affiliated companies, licensors, and suppliers, and is protected by their respective copyright, trademark and other proprietary rights. Upon payment of the subscription price, if applicable, you are hereby authorized to view, download, copy, and print Digital Material solely for your own personal, non-commercial use, provided that by doing any of the foregoing, you acknowledge that (i) you do not and will not acquire any ownership rights of any kind in the Digital Material or any portion thereof, (ii) you must preserve all copyright and other proprietary notices included in any downloaded Digital Material, and (iii) you must comply in all respects with the use restrictions set forth below and in the Informa Privacy Policy and the Informa Terms of Use (the “Use Restrictions”), each of which is hereby incorporated by reference. Any use not in accordance with, and any failure to comply fully with, the Use Restrictions is expressly prohibited by law, and may result in severe civil and criminal penalties. Violators will be prosecuted to the maximum possible extent. You may not modify, publish, license, transmit (including by way of email, facsimile or other electronic means), transfer, sell, reproduce (including by copying or posting on any network computer), create derivative works from, display, store, or in any way exploit, broadcast, disseminate or distribute, in any format or media of any kind, any of the Digital Material, in whole or in part, without the express prior written consent of Informa. -
Instruction Manual
TM WE GET PEOPLE FLYING INSTRUCTION MANUAL • 90% Custom built • Designed by 8-time TOC competitor Mike McConville • Specifically designed for excellence in precision and 3-D aerobatics • Prepainted fiberglass cowl and wheelpants • Plug-in wing and stab • Precovered with genuine Hangar 9™ UltraCote® • IMAC and Giant Scale legal • Instructions include 3-D flying tips from Mike McConville Specifications Wingspan: . 97 in . 2,464 mm Fuselage Length: . 90 in . 2,286 mm Wing Area: . 1,750 sq in . 112.9 dm sq Flight Weight: . 23 to 26 lb . 10.4–11.8 kg Recommended Engines: . 60 to 80 cc – gasoline Table of Contents Introduction ......................................................................................................................................... 3 Warning ............................................................................................................................................... 3 Additional Required Equipment ........................................................................................................... 4 Other Items Needed (not included in the kit) ........................................................................................ 5 Tools and Adhesives Needed (not included in the kit) .......................................................................... 5 Additional Needed Items .......................................................................................................................5 Contents of Kit ......................................................................................................................................6 -
Worldwide Equipment Guide Volume 2: Air and Air Defense Systems
Dec Worldwide Equipment Guide 2016 Worldwide Equipment Guide Volume 2: Air and Air Defense Systems TRADOC G-2 ACE–Threats Integration Ft. Leavenworth, KS Distribution Statement: Approved for public release; distribution is unlimited. 1 UNCLASSIFIED Worldwide Equipment Guide Opposing Force: Worldwide Equipment Guide Chapters Volume 2 Volume 2 Air and Air Defense Systems Volume 2 Signature Letter Volume 2 TOC and Introduction Volume 2 Tier Tables – Fixed Wing, Rotary Wing, UAVs, Air Defense Chapter 1 Fixed Wing Aviation Chapter 2 Rotary Wing Aviation Chapter 3 UAVs Chapter 4 Aviation Countermeasures, Upgrades, Emerging Technology Chapter 5 Unconventional and SPF Arial Systems Chapter 6 Theatre Missiles Chapter 7 Air Defense Systems 2 UNCLASSIFIED Worldwide Equipment Guide Units of Measure The following example symbols and abbreviations are used in this guide. Unit of Measure Parameter (°) degrees (of slope/gradient, elevation, traverse, etc.) GHz gigahertz—frequency (GHz = 1 billion hertz) hp horsepower (kWx1.341 = hp) Hz hertz—unit of frequency kg kilogram(s) (2.2 lb.) kg/cm2 kg per square centimeter—pressure km kilometer(s) km/h km per hour kt knot—speed. 1 kt = 1 nautical mile (nm) per hr. kW kilowatt(s) (1 kW = 1,000 watts) liters liters—liquid measurement (1 gal. = 3.785 liters) m meter(s)—if over 1 meter use meters; if under use mm m3 cubic meter(s) m3/hr cubic meters per hour—earth moving capacity m/hr meters per hour—operating speed (earth moving) MHz megahertz—frequency (MHz = 1 million hertz) mach mach + (factor) —aircraft velocity (average 1062 km/h) mil milliradian, radial measure (360° = 6400 mils, 6000 Russian) min minute(s) mm millimeter(s) m/s meters per second—velocity mt metric ton(s) (mt = 1,000 kg) nm nautical mile = 6076 ft (1.152 miles or 1.86 km) rd/min rounds per minute—rate of fire RHAe rolled homogeneous armor (equivalent) shp shaft horsepower—helicopter engines (kWx1.341 = shp) µm micron/micrometer—wavelength for lasers, etc. -
Defence Annual Report 2002-03 Analysis
Review of Defence Annual Report 2002-03: Analysis of Department of Defence Responses Dr Carlo Kopp, MIEEE, MAIAA, PEng, Defence Analyst and Consulting Engineer Peter A Goon, BEng, FTE (USNTPS) Managing Director, Australian Flight Test Services Pty Ltd January 26, 2004 Submission to the JOINT STANDING COMMITTEE ON FOREIGN AFFAIRS, DEFENCE AND TRADE DEFENCE SUBCOMMITTEE Defence Annual Report 2002-03 Analysis 2 Analysis Findings The Defence Senior Leadership Group does not appear to under- Finding 1: stand the magnitude or the impact of the risk factors arising in the Joint Strike Fighter program. The Defence Senior Leadership Group appears to be confusing the characteristics and design aims of the smaller Joint Strike Fighter Finding 2: with the characteristics and design aims of the larger and more capable F/A-22A fighter. The Defence Senior Leadership Group does not appear to under- stand the respective cost structures of the Joint Strike Fighter and Finding 3: F/A-22A fighter programs, and the export pricing models which apply. The Defence Senior Leadership Group does not appear to under- stand the capabilities in the F-111, especially in terms of the air- Finding 4: craft’s capacity for the carriage and delivery of precision guided munitions which the F-111 has been doing since the early 1980’s. The Defence Senior Leadership Group does not appear to under- stand modern strategic and battlefield strike techniques, especially Finding 5: persistent strike techniques required for the engagement of mobile ground targets. The Defence Senior Leadership Group does not appear to under- Finding 6: stand the operational economics of the existing RAAF force struc- ture, and their proposed RAAF force structures. -
Effects of Stores on Aircraft Structure
Effects of Stores on Aircraft Structure Wolfgang G. LUBER wgl-dynamics 81735 Munich GERMANY +49-172 832 9241 [email protected] ABSTRACT The approach to prove structural integrity of military combat aircraft with external stores focus on the understanding of the fundamental structural dynamics mechanisms involved and the identification of boundaries for all potential store loading up to the design limit of the aircraft. A finite element model is required which will be updated with ground and flight test results. The basic for the analytical investigation can be a coarse grid model which is derived from fine finite element component models, assembled to a complete aircraft model. The advantage of using the fine static grid model as basic model is that in case of refinement all used models can be updated in one step. From selected assumed mode a set of generalized unsteady aerodynamic matrices will be calculated. To analyze real conditions, aerodynamic interference of different surfaces is investigated. The analytical calculations were verified by low speed wind tunnel tests and flight test. The main flight tests are flutter, structural coupling, and vibration and loads survey. Different excitation methods and maneuvers were used to excite the aircraft in a symmetric or antisymmetric case. 1.0 INTRODUCTION The layout of military aircraft structures is strongly influenced by dynamic loads from the early development phase onwards up to final design and clearance phase. Different dynamic loads have to be considered, namely dynamic gust loads, buffet loads on wing, fin, fuselage also buffet loads from airbrakes, cavities and blisters, gunfire loads mainly at attachment frames and panels, Hammershock loads for air intake, bird strike and ammunition impact, acoustic loads for outer air intake and missile bays. -
FSAE Chassis Hardpoint Optimization
FSAE Chassis Hardpoint Optimization Final Design Review 03/19/2021 Chris Soohoo [email protected] Dwarak Reddy [email protected] Ethan Vallivero [email protected] Project Sponsor: Project Advisor: John Fabijanic Mechanical Engineering Department California Polytechnic State University, San Luis Obispo ME 430 Winter 2021 1 Statement of Disclaimer Since this project is a result of a class assignment, it has been graded and accepted as fulfillment of the course requirements. Acceptance does not imply technical accuracy or reliability. Any use of information in this report is done at the risk of the user. These risks may include catastrophic failure of the device or infringement of patent or copyright laws. California Polytechnic State University at San Luis Obispo and its staff cannot be held liable for any use or misuse of the project. 2 Abstract Our team has been tasked with optimizing hardpoints for the Cal Poly Racing team. Hardpoints are the locations on the chassis of a car that are designed to carry both internal and external loads, they are the areas where the engine and suspension connect to the chassis. These points are subject to torsion, shear, bending and pull-out loads. Cal Poly Racing needs more thoroughly analyzed individualized hardpoints that are optimized for weight, strength and specific stiffness, so they can reduce the overall weight and improve the race times of the vehicle while maintaining their strength and stiffness standards. Our team has reviewed past projects, research papers, and test results to gain a strong understanding of hardpoints. Our goal was to design a hardpoint that minimizes weight while maintaining the strength and stiffness standards of Cal Poly FSAE. -
Gallery of Weapons
Gallery of Weapons By Aaron M. U. Church 2017 USAF Almanac B-1 Lancer TSgt. Richard Ebensberger/USAF BOMBER AIRCRAFT 2016. FY17 funds support development of higher ■■ B-2 SPIRIT powered Military Code (M-Code) jam-resistant Brief: Stealthy, long-range nuclear and con- ■■ B-1 LANCER GPS interface. B-1s resumed Pacific presence ventional strike bomber. Brief: Long-range penetrating bomber capable rotations to Guam in 2016. of delivering the largest weapon load of any COMMENTARY aircraft in the Air Force inventory. EXTANT VARIANT(S) The B-2 is a flying wing that combines LO • B-1B. Upgraded production version of the stealth design with high aerodynamic efficiency. COMMENTARY canceled B-1A. Spirit entered combat against Serb targets The B-1A was initially proposed as a replace- Function: Long-range conventional bomber. during Allied Force on March 24, 1999. B-2 ment for the B-52, and four prototypes were Operator: AFGSC, AFMC. production was completed in three successive developed and tested before program cancella- First Flight: Dec. 23, 1974 (B-1A); Oct. 18, blocks and all aircraft were upgraded to Block tion in 1977. The program was revived in 1981 1984 (B-1B). 30 standards with AESA radar. AESA paves the as the B-1B. The vastly upgraded aircraft added Delivered: June 1985-May 1988. way for future advanced weapons integration 74,000 lb of usable payload, improved radar, and IOC: Oct. 1, 1986, Dyess AFB, Texas (B-1B). including Long-Range Standoff (LRSO) mis- reduced radar cross section, but cut speed to Production: 104. sile and B61-12 bomb. -
Extra 330 Manual
TM WE GET PEOPLE FLYING INSTRUCTION MANUAL • 90% custom built • Designed by 7-time TOC competitor Mike McConville • Specifically designed for excellence in precision and 3D aerobatics • Prepainted fiberglass cowl and wheelpants • Plug-in wing and stab • Precovered with genuine Goldberg UltraCote® • IMAC and IMAA legal • Instructions include 3D flying tips from Mike McConville Specifications Wingspan: . 97 in . 2,463.8 mm Fuselage Length: . 88 in . 2,235.2 mm Wing Area: . 1,750 sq in . 112.9 dm2 Flight Weight: . 23.5 to 26.5 lb . 9.98–11.80 kg Recommended Engines: . 60 to 80 cc Table of Contents Introduction ..................................................................................................................................................................................... 2 Warning ..................................................................................................................................................................................... 3 Additional Equipment Required ............................................................................................................................................................ 3 Other Items Needed (not included in the kit) ......................................................................................................................................... 4 Tools and Supplies Needed (not included in the kit) ............................................................................................................................. 4 Contents of Kit -
Afsc 2A3x2 F-16/F-117/Cv-22 Avionic Systems Career Field Education And
DEPARTMENT OF THE AIR FORCE CFETP 2A3X2 Headquarters US Air Force Parts I and II Washington, DC 20330-1030 OCT 97 AFSC 2A3X2 F-16/F-117/CV-22 AVIONIC SYSTEMS CAREER FIELD EDUCATION AND TRAINING PLAN CAREER FIELD EDUCATION AND TRAINING PLAN F-16/F-117/CV-22 AVIONIC SYSTEMS AFSC 2A3X2 Table of Contents PART I Page Number Preface................................................................................................................................. 2 Abbreviations/Terms Explained.......................................................................................... 3 Section A, General Information ....................................................................................... 5 Purpose of the CFETP ................................................................................................. 5 Use of the CFETP........................................................................................................ 5 Coordination and Approval ......................................................................................... 6 Section B, Career Field Progression and Information...................................................... 6 Specialty Descriptions ................................................................................................. 6 2A332/52 ..................................................................................................................... 6 2A372 .......................................................................................................................... 6 2A390