The Investigation of Derailments.Pmd
Total Page:16
File Type:pdf, Size:1020Kb
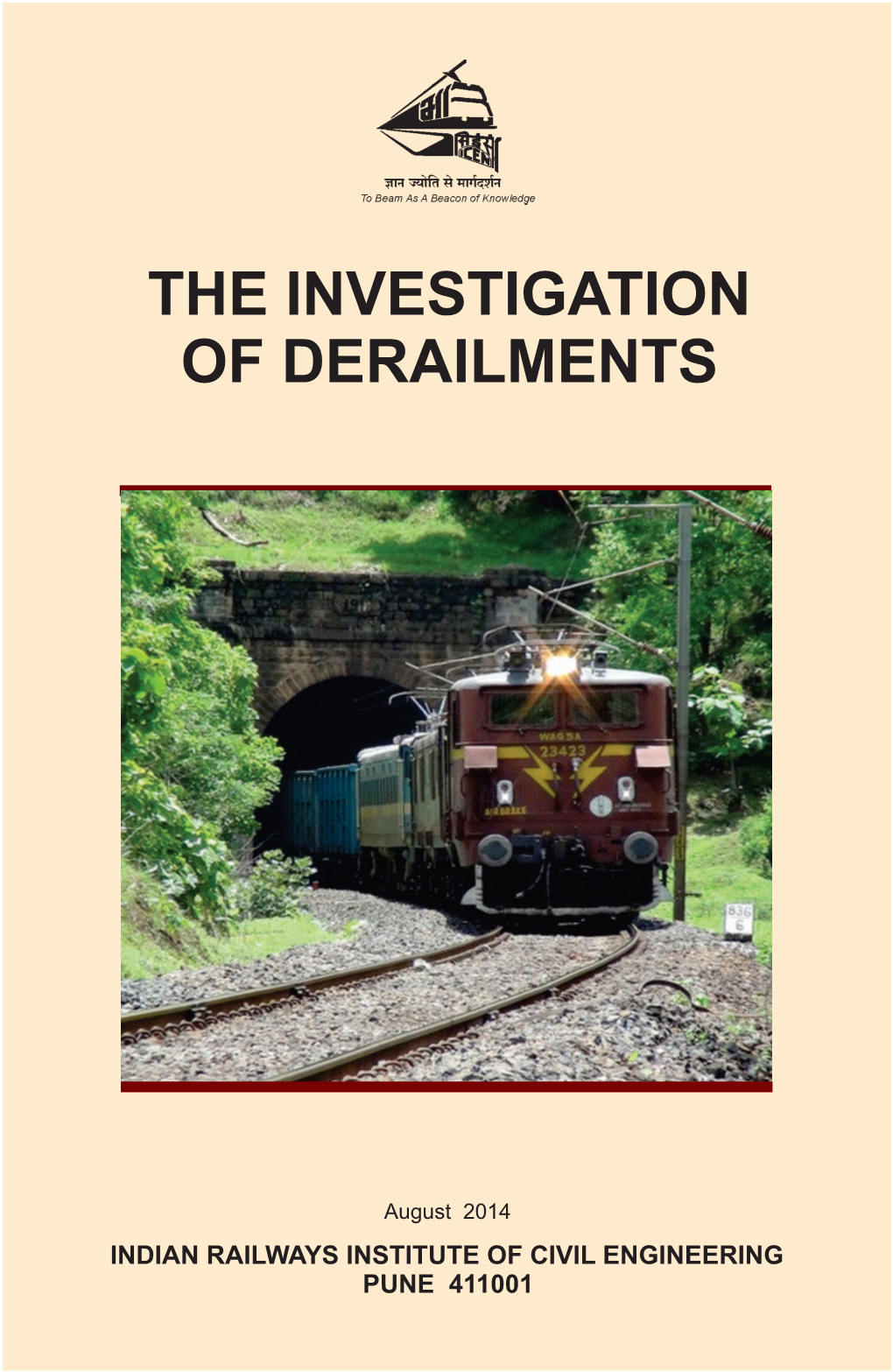
Load more
Recommended publications
-
My,M~Lflijltl~Ffdu \'------
A Review of Rail Behavior u.s. Department Under Wheel/flail Impact Of Transportation Federal Railroad Administration Load ing ,/mY,M~lflijltl~ffDU \'------------- Office of Research and Development Washington DC 20590 D. R. Ahlbeck Batelle Columbus. Laboratories 505 King Avenue Columbus. Ohio 43201-2693 DOT -FRA-ORO-86-01 April 1986 This document IS avaliableto the DOT -TSC-FRA-85-5 Final Report Public through the National Technical Information Service, Springfield, Virginia 22161. RfPROOUCED BY NA Tl.ONAL TECHNICAL INFORMATION SERVICE u.s. DEPARTMENT OF COMMERCE SPRINGFiElD, VA. 22161 NOTICE This document is disseminated under the sponsorship of the Department of Transportation in the interest of information exchange. The United States Government assumes no liability for its contents or use thereof. NOTICE The United States Government does not endorse products of manufacturers. Trade of manufacturers'names appear herein solely because they are con sidered essential to the object of this report. a... - Technical Report Documentation Page I. Repo"No~---------------------r~2~.~G~0-v-.-r"-m-e-n-t~A-c-c-e'-I~io-n~N-o.~---------r~3-.~R~e-c~iP-i-en-t~·'~C-ot-o~lo-g-N--0.---------------, DOT-FRA-ORO-86-0l 4. Till. and Subtitle s. Reporr Dale April 1986 A REVIEW OF RAIL BEHAVIOR UNDER WHEEL/RAIL 6. Perform,ng Orgoni zalian Caoe IMPACT LOADING TSC/DTS-73 r-:;--:-7""~:----------------------------------------------------~ 8. P .rformi ng Orgoni zation Repo,' No. 7. Author'.) / D.R. Ahlbeck _pOT-~SC-FRA-85-5 9. P .,forming_ O,gani &a'ion Nom. and Addr.ss 10. Worlo Unit No, (TRAIS) Batelle Columbus Laboratories RR6l9/R6654 505 King Avenue 11. -
The Locomotives of the Great Northern Railway, 1847-1910
[OCOMOTIVES of tl^e 11 Ix. C^ jtA. I North ern I LWAY ]^ J tmmtmmmmimmam i ¥Bwm \ inm miiminuviNH i m <i m mnmm THE UNIVERSITY OF ILLINOIS LIBRARY ie\0 OAK ST. HDSF THE LOCOMOTIVES OF THE GREAT NORTHERN RAILWAY. ¥ < ^ .r^ : j tP f. Mr. H. A. IVATT, M.i.Mech.E. Locomotive Engineer, Great Northern Railway. The Locomotives of The Great Northern Railway^ 1847^1910^ BY GEO. FREDK. BIRD. NEW AND REVISED EDITION, With 8 Full-page Illustrations and 121 Illustrations in the Text by the Author. ^I-I^- Published by the Locomotive Publishing Co., Ltd. 3, Amen Corner, London, E.G. I 9 I o . PRINTED BY PERCY LUND, HUMPHRIES AND CO., LTD., BRADFORD AND LONDON, FOR THE LOCOMOTIVE PUBLISHING CO., LTD., 3, AMEN CORNER, LONDON, E.C. Ok- PREFACE. V — CL> T N presenting a history of the various types of locomo- I tives have been constructed for the j which Great Northern the is aware of ,^^ Railway, compiler many .^ deficiencies in the work. So far from this being a history ^ of the line, the following pages cannot claim to comprise 1 more than a somewhat brief of loco- 1 anything catalogue J motives, many of which have earned fame in the annals of L railway development. To have dealt with them as fully as ^^ might be is not in the power of the compiler, and equally ?. beyond the limits of space allowable in a publication of this 'S' character. The utmost that can be urged is that, principally ^owing to the disinterested assistance of many kind friends, 0--the writer has been enabled to produce what is, so far as he ^ is aware, the first approximately complete list of the ^locomotives built for the Great Northern Railway from 'Oits opening as a small branch line in Lincolnshire until ^. -
The Evolution of the Steam Locomotive, 1803 to 1898 (1899)
> g s J> ° "^ Q as : F7 lA-dh-**^) THE EVOLUTION OF THE STEAM LOCOMOTIVE (1803 to 1898.) BY Q. A. SEKON, Editor of the "Railway Magazine" and "Hallway Year Book, Author of "A History of the Great Western Railway," *•., 4*. SECOND EDITION (Enlarged). £on&on THE RAILWAY PUBLISHING CO., Ltd., 79 and 80, Temple Chambers, Temple Avenue, E.C. 1899. T3 in PKEFACE TO SECOND EDITION. When, ten days ago, the first copy of the " Evolution of the Steam Locomotive" was ready for sale, I did not expect to be called upon to write a preface for a new edition before 240 hours had expired. The author cannot but be gratified to know that the whole of the extremely large first edition was exhausted practically upon publication, and since many would-be readers are still unsupplied, the demand for another edition is pressing. Under these circumstances but slight modifications have been made in the original text, although additional particulars and illustrations have been inserted in the new edition. The new matter relates to the locomotives of the North Staffordshire, London., Tilbury, and Southend, Great Western, and London and North Western Railways. I sincerely thank the many correspondents who, in the few days that have elapsed since the publication: of the "Evolution of the , Steam Locomotive," have so readily assured me of - their hearty appreciation of the book. rj .;! G. A. SEKON. -! January, 1899. PREFACE TO FIRST EDITION. In connection with the marvellous growth of our railway system there is nothing of so paramount importance and interest as the evolution of the locomotive steam engine. -
Derailment of a Passenger Train Near Clogwyn Y Gwin South Foot Crossing, Welsh Highland Railway, 10 June 2018 Important Safety Message
Derailment of a passenger train near Clogwyn y Gwin South foot crossing, Welsh Highland Railway, 10 June 2018 Important Safety Message This derailment demonstrates the importance of heritage railways ensuring that specific and appropriate inspections and checks are built into the vehicle maintenance and overhaul regimes to monitor the integrity of all safety critical components which could cause derailment in the event of failure, and also to ensure that such components are reassembled correctly after overhaul. This is of particular importance on narrow gauge lines and railways that operate in mountainous areas. Summary of the accident At approximately 12:15 hrs on 10 June 2018, a passenger train, travelling from Porthmadog to Caernarfon on the Welsh Highland Railway, became derailed close to Clogwyn y Gwin South footpath crossing. The crossing is approximately 0.75 miles (1.2 km) north of Rhyd Ddu station. The train was travelling at around the maximum permitted speed at this location of 10 mph (16 km/h). The leading wheelset of the locomotive derailed on a right-hand curve. The driver immediately applied the train’s brake and the train came to a stop in a distance of about 30 metres. The train was hauled by a ‘Garratt’ steam locomotive, number 143, and comprised nine coaches. There were 74 passengers and 7 members of staff on board the train. Rail Accident Investigation Branch Safety digest 06/2018: Clogwyn y Gwin Locomotive 143 at Rhyd Ddu station travelling in same direction (right to left of photograph) as at the time of derailment No injuries were reported amongst the passengers or crew. -
Modeling China's — and Now Iowa's — Mighty QJ 2-10-2'S
February 2007, Volume 75, Number 9 Modeling China’s — and now Iowa’s — mighty QJ 2-10-2’s After being replaced by diesels in their home country of China, a few of these modern, heavy-duty steamers have found their way to the American Heartland / Robert D. Turner ntil the end of 2005 one last place remained on Earth where big steam locomotives in substantial numbers were running in regular freight and passenger service on a year- round basis. That place was northern China, and in particular the autonomous region U of Inner Mongolia, to the northwest of Beijing. There, on the JiTong Railway, (often written Ji-tong) a stable of rugged 2-10-2’s—coal-fired and fire breathing—were still racking up ton- miles every day in an uncompromising display of first-class railroading. These impressive machines were China’s QJ class locomotives. QJ is short for Qian Jin, or “Advancing.” It comes from the Chinese revolutionary slogan, “revolution is the locomotive pushing human history forward.” Revolutionary rhetoric aside, which I am sure loses something in the translation, it is fair to say that in years to come the QJ will be remembered as one of the most interesting and important types of steam locomotives developed in the 20th century. In fact, two now reside in North America, having been imported by Railroad Development Corporation in June of 2006. They were moved to the Iowa Interstate Railroad soon after their arrival and were operated on its rails over the weekend of September 14-17, 2006. I met my first QJ early in 2001 on China Rail just before they were retired, and then began to explore the JiTong Railway, where QJ’s were in abundance. -
15Th May 2017
£1.00 15th May 2017 Station Studio, 6 Summerleys Road, Princes Risborough, Bucks, HP27 9DT Tel: 01844 345158 Fax: 01844 274352 Email: [email protected] Web: www.grsuk.com Narrow Gauge Electric Locomotive Kits Prototype Locomotive kits Manufactured by GRS for both 45mm and 32mm gauges Tasmanian K class Beyer-Garratt 0-4-0+0-4-0 The first two Beyer-Garratt’s to be designed and built in Manchester in 1909 for the North -East Dundas Tramway line in Tasmania. They were unique amongst Garratts in being of the Compound type, a system not recommended by their designer, and having cylinders mounted at the inboard end of the power bogies. At the end of it’s service life, in 1947, K1 was repatriated to Gorton works where it was preserved until Beyer-Peacock closed the works in 1965. Now owned by the Ffestiniog railway and returned to service after an extensive restoration in 2004, K1 can now be seen at work on the Welsh Highland line. The kit is designed to be easy to build and comprises largely of a cast resin superstructure complemented by brass etches, sitting on top of two powered chassis of steel frames and brass stretchers which screw together with the addition of steel and Nickel-Silver valve gear. Length 512mm, Width 110mm, Height 175mm CMR250 K1 Beyer-Garratt loco kit 45mm Gauge CMR251 K1 Beyer-Garratt loco kit 32mm Gauge Campbeltown & Machrianish 0-6-2T Locomotive Andrew Barclay produced two of these locos in 1906/07 for the tourist passenger traffic on the remote Kintyre Peninsula railway. -
Rigging Terms
Appendices 209 Appendix (i) Personal safety equipment and first aid Riggers often have to wear helmets, gloves, eye protection, face masks and respirators and steel capped boots to protect themselves from injury. It is the responsibility of your employer to provide the necessary protective equipment. It is the responsibility of riggers to wear and use the equipment properly and where and when necessary. Safety helmets Safety helmets with chin straps must be worn wherever there is a risk of objects falling from above and on any work site where the hard hat sign is displayed. Helmets should comply with AS 1801 Industrial safety helmets. Gloves Riggers should wear close fitting pigskin gloves to protect hands from: • heat and abrasion • molten metal • sharp edges. Special purpose gloves may be required for protection against chemicals including acids, alkalis, solvents, fats and oils. Eye protection Wear eye protection that conforms to AS 1337 Eye protectors for industrial applications if you are likely to be exposed to: • physical damage caused by – flying particles, dust, molten metal • chemical damage caused by – toxic liquids, gases and vapours dusts • radiation damage caused by – sunlight, visible light, infra red, laser. Respiratory protection Riggers should wear a face mask that conforms to AS 1716 Respiratory protective devices if you are likely to be exposed to: • toxic gases and vapours • irritating dusts, such as silica. Inhalation of some chemical vapours and gases can cause death or a wide range of unpleasant symptoms including narcosis and headaches. Common dusts such as silica can cause lung disease later in life and is found wherever there is excavation, ie building sites, road works, tunnelling and mining. -
Mechanical Track Deterioration Due Tolateral Geometry Irregularities
THESIS FOR THE DEGREE OF LICENTIATE OF ENGINEERING IN SOLID AND STRUCTURAL MECHANICS Mechanical track deterioration due to lateral geometry irregularities KALLE KARTTUNEN Department of Applied Mechanics CHALMERS UNIVERSITY OF TECHNOLOGY G¨oteborg, Sweden 2012 Mechanical track deterioration due to lateral geometry irregularities KALLE KARTTUNEN c KALLE KARTTUNEN, 2012 Thesis for the degree of Licentiate of Engineering 2013:02 ISSN 1652-8565 Department of Applied Mechanics Chalmers University of Technology SE-412 96 G¨oteborg Sweden Telephone: +46 (0)31-772 1000 Cover: Predicted response of the outer wheel on the leading axle of a freight wagon with Y25- bogies negotiating a 438 metre radius curve. The solid line indicates predicted RCF damage (scale on the left axis) and the dotted line lateral position of wheel/rail contact point (scale on the right axis). Grey areas indicate predicted RCF (positive on the left vertical axis) or wear (negative) according to a wear number based criterion. Chalmers Reproservice G¨oteborg, Sweden 2012 Mechanical track deterioration due to lateral geometry irregularities Thesis for the degree of Licentiate of Engineering in Solid and Structural Mechanics KALLE KARTTUNEN Department of Applied Mechanics Chalmers University of Technology Abstract This thesis deals with how a degraded track geometry influences further degradation of the geometry and the formation of rolling contact fatigue (RCF) and wear of rails. The overall objective is optimisation of railway maintenance. For this, further understanding and quantification of the deterioration of track components are needed. Dynamic multibody simulations have been performed featuring different wagons, and a track with different curve radii and different levels of track geometry degradation. -
Eksploatacja I Niezawodnosc – Maintenance and Reliability
Eksploatacja i Niezawodnosc – Maintenance and Reliability Volume 23 (2021), Issue 1 journal homepage: http://www.ein.org.pl Article citation info: Konowrocki R, Kalinowski D, Szolc T, Marczewski A. Identification of safety hazards and operating conditions of the low-floor tram with independently rotating wheels with various drive control algorithms. Eksploatacja i Niezawodnosc – Maintenance and Reliability 2021; 23 (1): 21–33, http://dx.doi.org/10.17531/ein.2021.1.3. Identification of safety hazards and operating conditions of the Indexed by: low-floor tram with independently rotating wheels with various drive control algorithms Robert Konowrockia,*, Dariusz Kalinowskia,b, Tomasz Szolca, Artur Marczewskib aInstitute of Fundamental Technological Research, Polish Academy of Sciences, ul. Pawińskiego 5b, 02-106 Warsaw, Poland bPESA Bydgoszcz SA, ul. Zygmunta Augusta 11, 85-082 Bydgoszcz, Poland Highlights Abstract • Bogies with independently rotating wheels in- The aim of the article is to develop a method for the analysis of tram dynamics related to crease travel comfort. safety during operation. To achieve this, a mathematical model of the vehicle represented by a multibody simulation MBS system is used. Models of tram with a classic and innova- • System of independently rotating wheels (IRW) tive drive, based on a system of independently rotating wheels on crank axles are analyzed. reducing the value of wheel-rail forces. A new configuration of an innovative drive control of the considered vehicle with the use • Higher efficiency of tram drive control through of braking of independent wheels is proposed. A new geometry of test track is presented. additional braking. During numerical investigation the values of ‘Y’ leading forces of tram wheels with the con- • New geometry of simulational test track for light sidered innovative drive proved to be lower than in the corresponding vehicle with standard rail vehicles (LRVs). -
On the Influence of Rail Vehicle Parameters on the Derailment Process and Its Consequences
DAN BRABIE on the Derailment Parameters Vehicle On the Influence of Rail and its Consequences Process TRITA AVE 2005:17 ISSN 1651-7660 ISBN 91-7283-806-X On the Influence of Rail Vehicle Parameters on the Derailment Process and its Consequences DAN BRABIE Licentiate Thesis in Railway Technology KTH 2005 KTH Stockholm, Sweden 2005 www.kth.se On the Influence of Rail Vehicle Parameters on the Derailment Process and its Consequences by Dan Brabie Licentiate Thesis TRITA AVE 2005:17 ISSN 1651-7660 ISBN 91-7283-806-X Postal Address Visiting address Telephone E-mail Royal Institute of Technology Teknikringen 8 +46 8 790 84 76 [email protected] Aeronautical and Vehicle Engineering Stockholm Fax Railway Technology +46 8 790 76 29 SE-100 44 Stockholm . Contents Contents.............................................................................................................................i Preface and acknowledgements.................................................................................... iii Abstract ............................................................................................................................v 1 Introduction.................................................................................................................1 1.1 Background information......................................................................................1 1.2 Previous research.................................................................................................1 1.3 Scope, structure and contribution of this thesis...................................................3 -
Locomotive Engine Driving
.UMWr '• .;.'.«.• .•.^•>.riiMfe|il^^^SHfr^ Pi 1 •iri^ p Eli I ^' . •-'• -*L - ,'5't.-- > / A* ,' Ss.^> ' rX t.*V **: '-^- ', i.4:. 4. •* 'j.jsefe' A v\ (aj o X \\ ."'eS' ^. ^>; .-'--^^ Loiid0n:Crost7-Iidfekwoo<i&C? ZSratioDers HaHCoiirt. LOCOMOTIVE ENGINE DRIVING A PRACTICAL MANUAL FOR ENGINEERS IN CHARGE OF LOCOMOTIVE ENGINES By MICHAEL EEYKOLDS MEMBER OF THE SOCIETY OF EXOIXEERS, FOUMERLY LOCOMOTIVE INSPECTOR LONDON, BRIGHTON, AND SODTH COAST RAILWAY EIGHTH EDITION COMPRISING, BESIDES OTHER ADDITIONAL MATTER A KEY TO THE LOCOMOTIVE ENGINE SSEith nttmcrotts lUustratimts gpiol];u. LONDON CROSBY LOCKWOOD AND SON 7, STATIONERS' HALL COURT, LTJDGATE HILL 1888 \_All rights reserved'] 1 J :i TO THE ENGINEMEN AND FIREMEN OF LOCOMOTIVE ENGINES THEOUGHOUT THE UNITED KINGDOM THIS WOEK IS AS A TRIBUTE OF EEGARD AND RESPECT BY THEIR SERVANT THE AUTHOB rrxv^^ PEEFACE. I AM ambitious to extend and improve the social condition of locomotive drivers by placing within their reach a standard test of capacity that will be unaffected by local or temporary prejudices, fancies, fashions, or accidental connections. It appears to me that our enginemen of to-day will be to those of the next century what " Puffing Billy " in 1825 is to the " Monarch of Speed " in 1877. I hold a very strong opinion that our enginemen may be stripped of old habits and customs by self-help and self-reliance, and developed into a high state of efficiency. In carrying out such a measure of progress, difficulties, no doubt, which usually attend the work of reformation, will crop up ; and many disappointments await the pioneer. The engine is ahead of the engineman—all the hard scheming, comparatively speaking, is done ; but the engineman remains where he was in George Stephenson's time, and his stationary condi- tion jars with his surroundings. -
Tng 84 Summer 1979
NARROW GAUGI RAlllAY SOCIITY Serving the narrow gauge world since 1951 SECRETARY MEMBERSHIP SECRETARY P.A. Slater, The Hole in The Wall, Bradley, Ashbourne, Derbys. TREASURER J.H. Steele, 32 Thistley Hough, Penkhull, Stoke-on-Trent, ST4 5HU. The Society was founded in 1951 to encourage interest in all forms of narrow gauge rail transport. Members interests cover every aspect of the construction, operation, history and modelling of narrow gauge railways throughout the world. Society members receive this magazine and Narrow Gauge News, a bi-monthly review of current events on the narrow gauge scene. An extensive library, locomotive records, and modelling information service are available to members. Meetings and visits are arranged by local areas based in Leeds, Leicester, London, Malvern, Stoke-on-Trent and Warrington. Annual subscription £4.50 due 1 st April. THI NARROW GAUGI ISSN 0142-5587 EDITOR M. Swift, 47 Birchington Avenue, Birchencliffe, Huddersfield, HD3 3RD. ASSISTANT EDITORS R.N. Redman, A. Neale. BACK NUMBER SALES Published quarterly by the Narrow Gauge Railway Society to record the history and development of narrow gauge rail transport. Our intention is to present a balanced, well illustrated publication, and the Editor welcomes original articles, photographs and drawings for consideration. Articles should preferably be written or typed with double spacing on one side of the paper only. The Editor appreciates a stamped addressed envelope if a reply is required. A range of back numbers, and binders for eight issues are available from the address above. Copyright of all material in this magazine remains vested in the authors and publisher.