An Overview of Standard Cell Based Digital VLSI Design
Total Page:16
File Type:pdf, Size:1020Kb
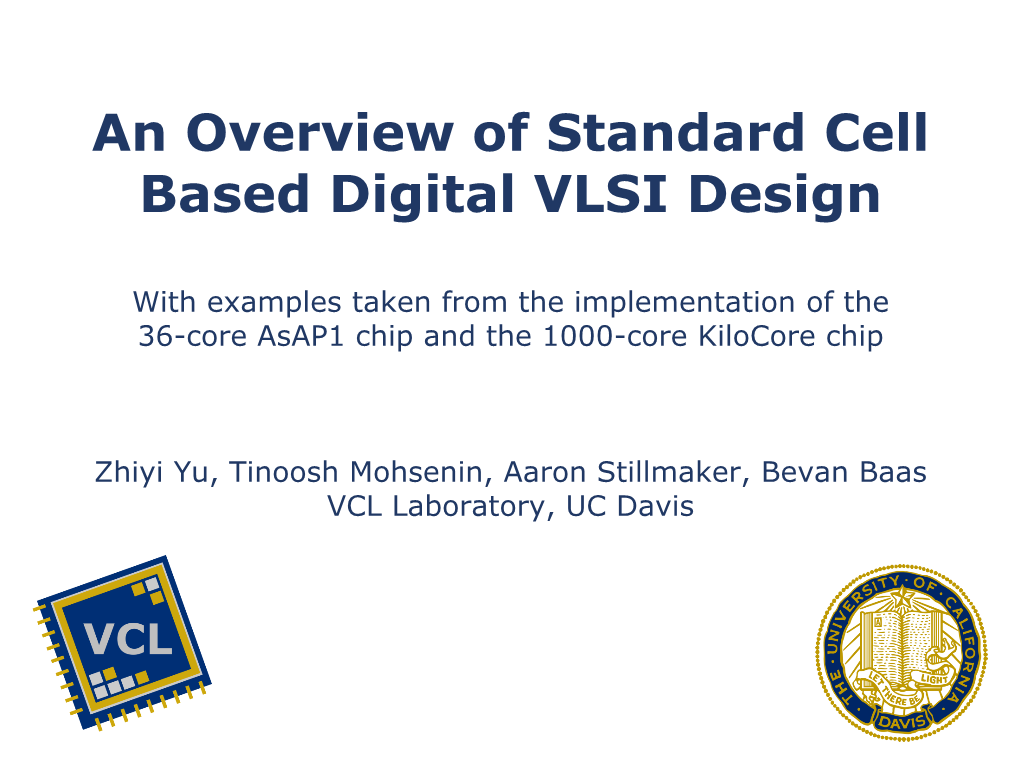
Load more
Recommended publications
-
Section 3. ASIC Industry Trends
3 ASIC INDUSTRY TRENDS ASSPs AND ASICs The term ASIC (Application Specific IC) has been a misnomer from the very beginning. ASICs, as now known in the IC industry, are really customer specific ICs. In other words, the gate array or standard cell device is specifically made for one customer. ASIC, if taken literally, would mean the device was created for one particular type of system (e.g., a disk-drive), even if this device is sold to numerous customers and/or is put in the IC manufacturer’s catalog. Currently, a device type that is sold to more than one user, even if it is produced using ASIC tech- nology, is considered a standard IC or ASSP (Application Specific Standard Product). Thus, we are left with the following nomenclature guidelines (Figure 3-1). ASIC: A device produced for only one customer. PLDs are included as ASICs because the customer “programs” that device for its needs only. CSIC: What ASICs should have been called from the beginning. Some companies differentiate an ASIC from a CSIC by who completes or is responsible for the majority of the IC design effort. If it is the IC producer, the part is labeled a CSIC, if it is the end-user, the device is called an ASIC. This term is not currently used very often in the IC industry. ASSP: A relatively new term for ICs targeting specific types of systems. In many cases the IC will be manufactured using ASIC technology (e.g., gate or linear array or standard cell techniques) but will ultimately be sold as a standard device type to numerous users (i.e., put into a product catolog). -
Introduction to ASIC Design
’14EC770 : ASIC DESIGN’ An Introduction Application - Specific Integrated Circuit Dr.K.Kalyani AP, ECE, TCE. 1 VLSI COMPANIES IN INDIA • Motorola India – IC design center • Texas Instruments – IC design center in Bangalore • VLSI India – ASIC design and FPGA services • VLSI Software – Design of electronic design automation tools • Microchip Technology – Offers VLSI CMOS semiconductor components for embedded systems • Delsoft – Electronic design automation, digital video technology and VLSI design services • Horizon Semiconductors – ASIC, VLSI and IC design training • Bit Mapper – Design, development & training • Calorex Institute of Technology – Courses in VLSI chip design, DSP and Verilog HDL • ControlNet India – VLSI design, network monitoring products and services • E Infochips – ASIC chip design, embedded systems and software development • EDAIndia – Resource on VLSI design centres and tutorials • Cypress Semiconductor – US semiconductor major Cypress has set up a VLSI development center in Bangalore • VDAT 2000 – Info on VLSI design and test workshops 2 VLSI COMPANIES IN INDIA • Sandeepani – VLSI design training courses • Sanyo LSI Technology – Semiconductor design centre of Sanyo Electronics • Semiconductor Complex – Manufacturer of microelectronics equipment like VLSIs & VLSI based systems & sub systems • Sequence Design – Provider of electronic design automation tools • Trident Techlabs – Power systems analysis software and electrical machine design services • VEDA IIT – Offers courses & training in VLSI design & development • Zensonet Technologies – VLSI IC design firm eg3.com – Useful links for the design engineer • Analog Devices India Product Development Center – Designs DSPs in Bangalore • CG-CoreEl Programmable Solutions – Design services in telecommunications, networking and DSP 3 Physical Design, CAD Tools. • SiCore Systems Pvt. Ltd. 161, Greams Road, ... • Silicon Automation Systems (India) Pvt. Ltd. ( SASI) ... • Tata Elxsi Ltd. -
ICS904/EN2 : Design of Digital Integrated Circuits
ICS904/EN2 : Design of Digital Integrated Circuits L5 : Design automation : The "liberty" file format Yves MATHIEU [email protected] Standard Cell characterization "Liberty" files Give all necessary informations to the synthesis and P&R tools A de-facto standard : "Liberty" files from "Synopsys" company. For each cell : • Logic behavior • Area • Power Consumption • Timing But also, for a whole library : • Characterization conditions (Process, Supply Voltage , Temperature) • Characterization conditions (Max rising time, Max capacitances,...) • Statistical capacitance model for wiring... 3/35 ICS904-EN2-L5 Yves MATHIEU An example library Nangate 45nm Open Cell Library Nangate is company creating characterization tools for standard cell libraries. Library distributed by Si2 (Silicon Integration Initiative) an association of electronic design automation companies. No way to process any true circuit, but usable for research and teaching purposes. Based on the NCSU (North Carolina State University) FreePDK45 process kit. FreePDK45 : An open source fictitious, non manufacturable process. 4/35 ICS904-EN2-L5 Yves MATHIEU Nangate 45nm Open Cell Library Units for measurements /* Units Attributes */ voltage_unit : "1V"; current_unit : "1mA"; pulling_resistance_unit : "1kohm"; capacitive_load_unit (1,ff); All measurements use defined units. 6/35 ICS904-EN2-L5 Yves MATHIEU Nangate 45nm Open Cell Library Characterization conditions /* Operation Conditions */ nom_process : 1.00; nom_temperature : 25.00; nom_voltage : 1.10; voltage_map (VDD,1.10); -
Full-Custom Ics Standard-Cell-Based
Full-Custom ICs Design a chip from scratch. Engineers design some or all of the logic cells, circuits, and the chip layout specifi- cally for a full-custom IC. Custom mask layers are created in order to fabricate a full-custom IC. Advantages: complete flexibility, high degree of optimization in performance and area. Disadvantages: large amount of design effort, expensive. 1 Standard-Cell-Based ICs Use predesigned, pretested and precharacterized logic cells from standard-cell li- brary as building blocks. The chip layout (defining the location of the building blocks and wiring between them) is customized. As in full-custom design, all mask layers need to be customized to fabricate a new chip. Advantages: save design time and money, reduce risk compared to full-custom design. Disadvantages: still incurs high non-recurring-engineering (NRE) cost and long manufacture time. 2 D A B C A B B D C D A A B B Cell A Cell B Cell C Cell D Feedthrough Cell Standard-cell-based IC design. 3 Gate-Array Parts of the chip are pre-fabricated, and other parts are custom fabricated for a particular customer’s circuit. Idential base cells are pre-fabricated in the form of a 2-D array on a gate-array (this partially finished chip is called gate-array template). The wires between the transistors inside the cells and between the cells are custom fabricated for each customer. Custom masks are made for the wiring only. Advantages: cost saving (fabrication cost of a large number of identical template wafers is amortized over different customers), shorter manufacture lead time. -
Standard Cell Library Design and Optimization with CDM for Deeply Scaled Finfet Devices
Standard Cell Library Design and Optimization with CDM for Deeply Scaled FinFET Devices. by Ashish Joshi, B.E A Thesis In Electrical Engineering Submitted to the Graduate Faculty of Texas Tech University in Partial Fulfillment of the Requirements for the Degree of MASTER OF SCIENCES IN ELECTRICAL ENGINEERING Approved Dr. Tooraj Nikoubin Chair of Committee Dr. Brian Nutter Dr. Stephen Bayne Mark Sheridan Dean of the Graduate School May, 2016 © Ashish Joshi, 2016 Texas Tech University, Ashish Joshi, May 2016 ACKNOWLEDGEMENTS I would like to sincerely thank my supervisor Dr. Nikoubin for providing me the opportunity to pursue my thesis under his guidance. He has been a commendable support and guidance throughout the journey and his thoughtful ideas for problems faced really been the tremendous help. His immense knowledge in VLSI designs constitute the rich source that I have been sampling since the beginning of my research. I am especially indebted to my thesis committee members Dr. Bayne and Dr. Nutter. They have been very gracious and generous with their time, ideas and support. I appreciate Dr. Nutter’s insights in discussing my ideas and depth to which he forces me to think. I would like to thank Texas Instruments and my colleagues Mayank Garg, Jun, Alex, Amber, William, Wenxiao, Shyam, Toshio, Suchi at Texas Instruments for providing me the opportunity to do summer internship with them. I continue to be inspired by their hard work and innovative thinking. I learnt a lot during that tenure and it helped me identifying my field of interest. Internship not only helped me with the technical aspects but also build the confidence to accept the challenges and come up with the innovative solutions. -
Development and Verification of a Small CMOS Digital Standard Cell Library Based on SMIC 130Nm Process
4th International Conference on Mechatronics, Materials, Chemistry and Computer Engineering (ICMMCCE 2015) Development and Verification of A Small CMOS Digital Standard Cell Library Based on SMIC 130nm Process Yiwen Wang1,a,*, Hang Su1,a, Mingjiang Wang1,a, Jipan Huang2,b, Hao Chen2,b 1School of Electronic and Information Engineering, Harbin Institute of Technology Shenzhen Graduate School, Shenzhen, China 2School of Electronic and Computer Engineering, Peking University Shenzhen Graduate School, Shenzhen, China [email protected], [email protected] Keywords: Standard cell library; Full adder; Optimization; Verification; P&R Abstract. Nowadays, Semi-custom design based on the standard cells is the mainstream design method for digital IC chip. In this thesis, the standard cell library is built and verified based on the SMIC 130nm technology, especially the optimization of a 1-bit full adder cell, during which the structure and layout of the full adder in the SMIC library is analyzed. As a result, the structure and size of the adder cell are improved better, which is simulated by H-spice. The comparison shows that the optimized adder is not only smaller in area, with width decreased by 0.82μm, but also have advantages in power consumption and timing, with energy delay product reduced by 7.7% .In the end, the s298 circuit in ISCAS Benchmark89 is used as the benchmark to complete the verification method of the standard cell library. Introduction Standard cell library is the basis of gate-level module based circuit design, and it has a direct impact on the performance[1,2], power consumption, size and yield of the final flowing out circuits. -
Eg, Nangate 15 Nm Standard Cell Library
Nanosystem Design Kit (NDK): Transforming Emerging Technologies into Physical Designs of VLSI Systems G. Hills, M. Shulaker, C.-S. Lee, H.-S. P. Wong, S. Mitra Stanford Massachusetts University Institute of Technology Abundant-Data Explosion “Swimming in sensors, drowning in data” Wide variety & complexity Unstructured data 0 40K 0 ExaB (Billionsof GB) 2006 Year 2020 Mine, search, analyze data in near real-time Data centers, mobile phones, robots 2 Abundant-Data Applications Huge memory wall: processors, accelerators Energy Measurements Genomics classification Natural language processing 5% 18 % 0% 0% … 95 82 % % Compute Memory Intel performance counter monitors 2 CPUs, 8-cores/CPU + 128GB DRAM 3 US National Academy of Sciences (2011) 4 Computing Today 2-Dimensional 5 3-Dimensional Nanosystems Computation immersed in memory 6 3-Dimensional Nanosystems Computation immersed in memory Increased functionality Fine-grained, Memory ultra-dense 3D Computing logic Impossible with today’s technologies 7 Enabling Technologies 3D Resistive RAM Massive storage No TSV 1D CNFET, 2D FET Compute, RAM access thermal STT MRAM Ultra-dense, Quick access fine-grained 1D CNFET, 2D FET vias Compute, RAM access thermal 1D CNFET, 2D FET Silicon Compute, Power, Clock compatible thermal 8 Nanosystems: Compact Models Essential 3D Resistive RAM nanohub Massive storage 1D CNFET, 2D FET Compute, RAM access thermal STT MRAM Quick access m-Cell 1D CNFET, 2D FET Compute, RAM access thermal 1D CNFET, 2D FET Compute, Power, Clock thermal 9 Compact Models: Insufficient Alone Design for Realistic Systems Wire parasitics Inter-module interface circuits Routing congestion Application-dependent workloads Multiple clock domains Cache architecture Memory access patterns Processor vs. -
Standard Cell Library Design with Transistor Folding Using
STANDARD CELL LIBRARY DESIGN WITH TRANSISTOR FOLDING USING 65NM TECHNOLOGY BY GLOBAL FOUNDRIES by Vibhav Kumarswami Salimath APPROVED BY SUPERVISORY COMMITTEE: ___________________________________________ Dr. Carl M. Sechen, Chair ___________________________________________ Dr. William Swartz ___________________________________________ Dr. Benjamin Carrion Schaefer Copyright 2018 Vibhav Kumarswami Salimath All Rights Reserved To my family and my teachers STANDARD CELL LIBRARY DESIGN WITH TRANSISTOR FOLDING USING 65NM TECHNOLOGY BY GLOBAL FOUNDRIES by VIBHAV KUMARSWAMI SALIMATH, B.E. THESIS Presented to the Faculty of The University of Texas at Dallas in Partial Fulfillment of the Requirements for the Degree of MASTER OF SCIENCE IN ELECTRICAL ENGINEERING THE UNIVERSITY OF TEXAS AT DALLAS May 2018 ACKNOWLEDGMENTS I want to thank my advisor, Dr. Carl Sechen, for his continuous supervision and guidance. I took Dr. Sechen’s course during my first semester in the master’s degree program. I loved the way he taught and came away from the course with a clear idea of my research interests. Working at the Nanometer Design Lab has been an incredible experience and I am most grateful for this opportunity. Thank you to my friends at Nanometer Design Lab for their valuable input, especially Xiangyu Xu and Qiongdan Huang (Olivia). I wish to specially thank Dr. William Swartz Jr. for providing me with timely help and support. Thank you to Dr. William Swartz Jr. and Dr. Benjamin Carrion Schaefer for serving as the committee members for my defense and providing me with their support and advice. I am extremely grateful to my family and friends for their encouragement, which has motivated me to do my best academically. -
Introduction • ASIC Is an Acronym for Application Specific Integrated Circuit
Introduction • ASIC is an acronym for Application Specific Integrated Circuit. • As the name indicates, ASIC is a non- standard integrated circuit that is designed for a specific use or application. • Generally an ASIC design will be undertaken for a product that will have a large production run , and the ASIC may contain a very large part of the electronics needed on a single integrated circuit. SCRIET(CCS University Meerut) 1 Contd. • Examples for ASIC Ics are : a chip for a toy bear that talks; a chip for a satellite; a chip designed to handle the interface between memory and a microprocessor for a workstation CPU; and a chip containing a microprocessor as a cell together with other logic. SCRIET(CCS University Meerut) 2 Contd. • Two ICs that might or might not be considered as ASICs are, a controller chip for a PC and a chip for a modem. Both of these examples are specific to an application (shades of an ASIC) but are sold to many different system vendors (shades of a standard part). ASICs such as these are sometimes called application- specific standard products ( ASSPs ). SCRIET(CCS University Meerut) 3 Types of • The classificationASICs of ASICs is shown below SCRIET(CCS University Meerut) 4 Full-Custom ASICs • A Full custom ASIC is one which includes some (possibly all) logic cells that are customized and all mask layers that are customized. • A microprocessor is an example of a full-custom IC . Designers spend many hours squeezing the most out of every last square micron of microprocessor chip space by hand. -
Standard Cell Library Design and Optimization Methodology for ASAP7
Standard Cell Library Design and Optimization Methodology for ASAP7 PDK (Invited Paper) Xiaoqing Xu1, Nishi Shah1, Andrew Evans1, Saurabh Sinha1,BrianCline1,andGregYeric1 1ARM Inc., Austin, TX, USA xiaoqing.xu,nishi.shah,andrew.evans,saurabh.sinha,brian.cline,greg.yeric @arm.com { } ABSTRACT explore the impact of lithography design rules and SC archi- Standard cell libraries are the foundation for the entire back- tectures [2,7–9]. However, very few SC design and optimiza- end design and optimization flow in modern application-specific tion techniques are discussed for complex logic/sequential integrated circuit designs. At 7nm technology node and be- cells. More importantly, none of them are publicly available, yond, standard cell library design and optimization is becom- which prevents academic researchers from exploring novel SC ing increasingly difficult due to extremely complex design design and optimization techniques. constraints, as described in the ASAP7 process design kit Therefore, this study proposes a set of design and opti- (PDK). Notable complexities include discrete transistor siz- mization techniques to create publicly-available SC libraries ing due to FinFETs, complicated design rules from lithogra- with ASAP7 PDK [10–12]. We first discuss exhaustive tran- phy and restrictive layout space from modern standard cell ar- sistor sizing for cell timing optimization taking advantage of chitectures. The design methodology presented in this paper the discrete transistor sizing for a FinFET-based SC design. enables efficient and high-quality standard cell library design Generalized Euler path theory [13] is adopted to generate and optimization with the ASAP7 PDK. The key techniques high-quality transistor placement results. The generalized include exhaustive transistor sizing for cell timing optimiza- Euler paths lead to a much larger solution space than that of tion, transistor placement with generalized Euler paths and conventional Euler path theory, while accommodating pin ac- back-end design prototyping for library-level explorations. -
Mathematical Methods for Physical Layout of Printed Circuit Boards: an Overview
Takustraße 7 Konrad-Zuse-Zentrum D-14195 Berlin-Dahlem fur¨ Informationstechnik Berlin Germany NADINE ABBOUD MARTIN GRO¨ TSCHEL THORSTEN KOCH Mathematical Methods for Physical Layout of Printed Circuit Boards: An Overview Work supported the DFG Research Center Mathematics for key technologies: Modelling, simulation, and optimization of real-world processes (MATHEON) ZIB-Report 06-29 (Dec 2006) Abstract This article surveys mathematical models and methods used for the physical layout of printed circuit boards, in particular component placement and wire routing. The main concepts are briefly described together with relevant references. Mathematics Subject Classification (2000): 90C90 90-02 68R05 1 Introduction Printed circuit boards (PCBs), see Figures 2 and 3 for an example, are ubiquituous. PCBs are the backbones of almost every electronic device, and therefore, PCB design and manufacturing are extremly important components of many industrial production processes. Before a PCB can serve its task it evolves through three main steps. The first one is the logic design, which defines the components to be used and their interconnections. The second step is the physical layout of the PCB where the geometric positions of the components and their physical connections are decided. The final step is the industrial production of the PCB. In this article we give an overview on the mathematical models and methods used in the second step, the physical design of the board. The two major issues here are component placement and wire routing as depicted in Figure 1. Step 1 Step 2 Step 3 Logical Design Physical Layout PCB Production Determine form factor and number of layers Component placement Pin assignment Layer assignment Wire routing Via minimization Figure 1: Tasks in PCB design A digital logic circuit consists of a collection of interconnected parts. -
Standard Cell Design Standard Cell Libraries Standard Cell Libraries Are
Advanced VLSI Design Standard Cell Design CMPE 641 Standard Cell Libraries Standard cell libraries are required by almost all CAD tools for chip design Standard cell libraries contain primitive cells required for digital design However, more complex cells that have been specially optimized can also be included The main purpose of the CAD tools is to implement the so called RTL-to-GDS flow The input to the design process, in most cases, is the circuit description at the register- transfer level (RTL) The final output from the design process is the full chip layout, mostly in the GDSII (gds2) format To produce a functionally correct design that meets all the specifications and constraints, requires a combination of different tools in the design flows These tools require specific information in different formats for each of the cells in the stan- dard cell library provided to them for the design 1 Advanced VLSI Design Standard Cell Design CMPE 641 Standard Cell Library Formats The formats explained here are for Cadence tools, howerver similar information is required for other tool suites. Physical Layout (gdsII, Virtuoso Layout Editor) Should follow specific design standards eg. constant height, offsets etc. Logical View (verilog description or TLF or LIB) Verilog is required for dynamic simulation. Place and route tools usually can use TLF. Verilog description should preferably support back annotation of timing information. Abstract View (Cadence Abstract Generator, LEF) LEF: Contains information about each cell as well as technology information Timing, power and parasitics (TLF or LIB) Transistor and interconnect parasitics are extracted using Cadence or other extraction tools.