Canadian Space Robotics in 2016
Total Page:16
File Type:pdf, Size:1020Kb
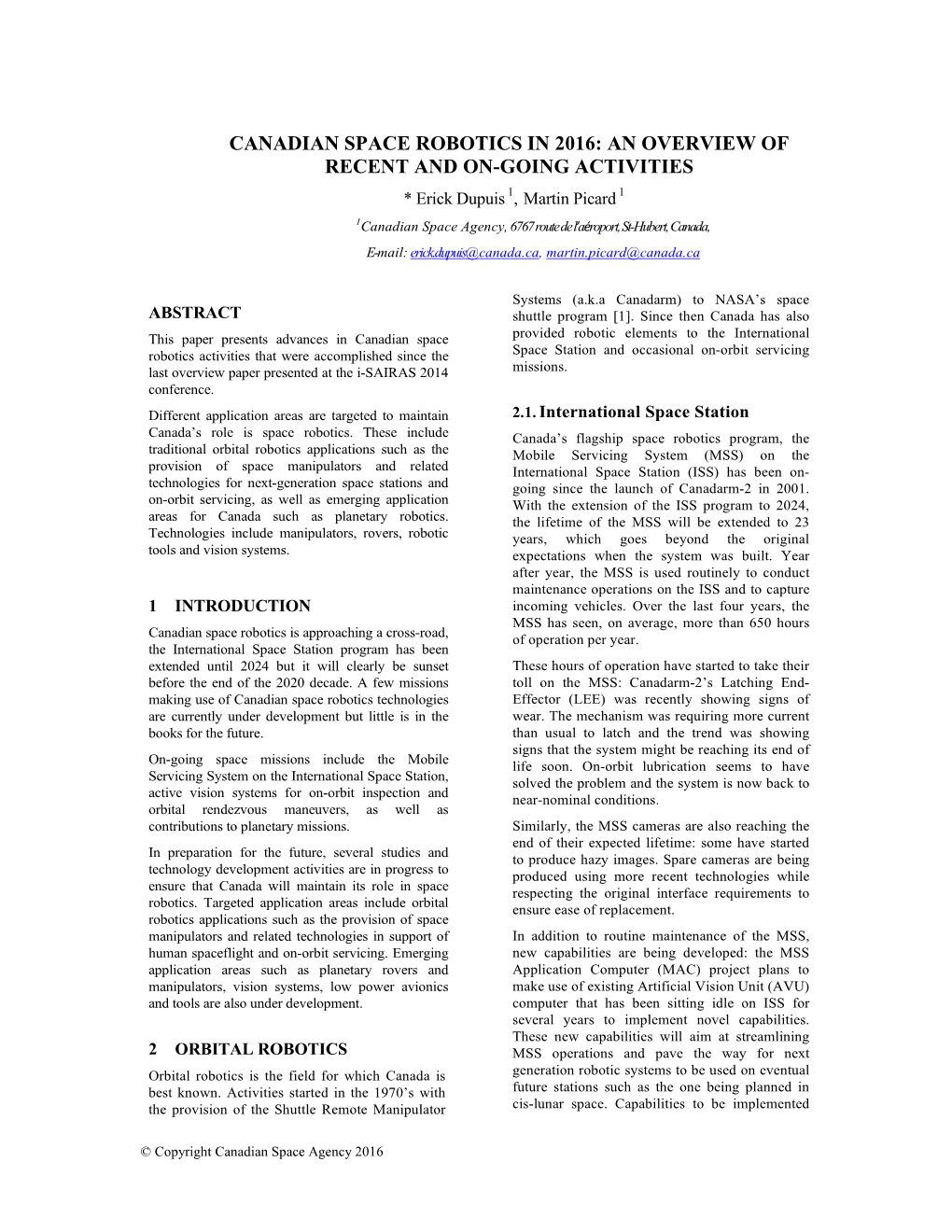
Load more
Recommended publications
-
NASA) Memoranda and Reports Concerning the Decommissioning of the International Space Station (ISS), 2010-2016
Description of document: Unpublished National Aeronautics and Space Administration (NASA) memoranda and reports concerning the decommissioning of the International Space Station (ISS), 2010-2016 Requested date: 28-July-2016 Released date: 05-April-2017 Posted date: 21-May-2018 Source of document: NASA Headquarters 300 E Street, SW Room 5Q16 Washington, DC 20546 Fax: (202) 358-4332 Email: [email protected] The governmentattic.org web site (“the site”) is noncommercial and free to the public. The site and materials made available on the site, such as this file, are for reference only. The governmentattic.org web site and its principals have made every effort to make this information as complete and as accurate as possible, however, there may be mistakes and omissions, both typographical and in content. The governmentattic.org web site and its principals shall have neither liability nor responsibility to any person or entity with respect to any loss or damage caused, or alleged to have been caused, directly or indirectly, by the information provided on the governmentattic.org web site or in this file. The public records published on the site were obtained from government agencies using proper legal channels. Each document is identified as to the source. Any concerns about the contents of the site should be directed to the agency originating the document in question. GovernmentAttic.org is not responsible for the contents of documents published on the website. National Aeronautics and Space Administration Lyndon B. Johnson Space Center 2101 NASA Parkway Houston, Texas 77058-3696 April 5, 2017 Replytoattn.of AD91 l/JSC FOIA Office REF: 16-JSC-F-00829 - Final Release Thank you for your Freedom oflnformation Act (FOIA) request dated and received in the NASA Headquarters FOIA Office on July 28, 2016. -
Relative Navigation Light Detection and Ranging (LIDAR) Sensor Development Test Objective (DTO) Performance Verification
NASA/TM2013-217992 NESC-RP-11-00753 Relative Navigation Light Detection and Ranging (LIDAR) Sensor Development Test Objective (DTO) Performance Verification Cornelius J. Dennehy/NESC Langley Research Center, Hampton, Virginia May 2013 NASA STI Program . in Profile Since its founding, NASA has been dedicated to the CONFERENCE PUBLICATION. advancement of aeronautics and space science. The Collected papers from scientific and NASA scientific and technical information (STI) technical conferences, symposia, seminars, program plays a key part in helping NASA maintain or other meetings sponsored or co- this important role. sponsored by NASA. The NASA STI program operates under the SPECIAL PUBLICATION. Scientific, auspices of the Agency Chief Information Officer. technical, or historical information from It collects, organizes, provides for archiving, and NASA programs, projects, and missions, disseminates NASA’s STI. The NASA STI often concerned with subjects having program provides access to the NASA Aeronautics substantial public interest. and Space Database and its public interface, the NASA Technical Report Server, thus providing one TECHNICAL TRANSLATION. of the largest collections of aeronautical and space English-language translations of foreign science STI in the world. Results are published in scientific and technical material pertinent to both non-NASA channels and by NASA in the NASA’s mission. NASA STI Report Series, which includes the following report types: Specialized services also include organizing and publishing research results, distributing specialized research announcements and feeds, TECHNICAL PUBLICATION. Reports of providing information desk and personal search completed research or a major significant phase support, and enabling data exchange services. of research that present the results of NASA Programs and include extensive data or For more information about the NASA STI theoretical analysis. -
Baikonur-International Space Station : International Approach to Lunar Exploration
ICEUM4, 10-15 July 2000, ESTEC, Noordwijk, The Netherlands Baikonur-International Space Station : International Approach to Lunar Exploration Gulnara Omarova, National Aerospace Agency; Chinghis Omarov, ISU Summer Session '98 alumni On 20th November 1998 our aircraft made soft landing at the Baikonur airport. I was among onboard passengers - officials from Kazakhstan Space, press and diplomats. We all were invited to attend the launch of the International Space Station (ISS) first component (the Russian-made Zarya or Functional Cargo Module FGB) by Proton launch-vehicle at the Baikonur spaceport. Two hours before ISS first module launch we joined the official delegations from NASA, Russian Space Agency (RSA), ESA, Canadian Space Agency (CSA) and NASDA to see the modified facilities of both "Energiya" Corp. and Khrunichev's Proton assembly-and- test building. Mr. Yuri Koptev, Chief of RSA and Mr. Dan Goldin, NASA Administrator actively were drinking russian tea and talking about crucial issues of the International Space Station and the future of Space Exploration. In fact, Cold War is over and the world's top space powers accomplishments are stunning: • The first human flight in space in 1961; • Human space flight initiatives to ascertain if and how long a human could survive in space; • Project Gemini (flights during 1965-1966) to practice space operations, especially rendezvous and docking of spacecraft and extravehicular activity; • Project Apollo (flights during 1968-1972) to explore the Moon; • Space Shuttle's flights (1981 - present); • Satellite programs; • A permanently occupied space station "Mir" (during 1976-1999); • A permanently occupied International Space Station presently underway. We and a few people approached them to learn much more particulars of their talking and to ask them most interesting questions. -
Final Report of the International Space Station Independent Safety
I Contents Executive Summary........................................................................................ 1 Principal Observations ..................................................................................... 3 Principal Recommendations ............................................................................. 3 1. Introduction..................................................................................................... 5 Charter/Scope ................................................................................................... 5 Approach........................................................................................................... 5 Report Organization ......................................................................................... 5 2. The International Space Station Program.................................................... 7 International Space Station Characteristics..................................................... 8 3. International Space Station Crosscutting Management Functions............ 12 Robust On-Orbit Systems.................................................................................. 12 The Design ........................................................................................................ 12 Verification Requirements ................................................................................ 12 Physical (Fit) Verification ................................................................................ 13 Multi-element Integrated Test.......................................................................... -
Robotic Arm.Indd
Ages: 8-12 Topic: Engineering design and teamwork Standards: This activity is aligned to national standards in science, technology, health and mathematics. Mission X: Train Like an Astronaut Next Generation: 3-5-ETS1-2. Generate and compare multiple possible solutions to a problem based on how well each is likely A Robotic Arm to meet the criteria and constraints of the problem. 3-5-ETS1-3. Plan and carry out fair tests in which variables are controlled and failure points are considered to identify aspects of a model or prototype that can be EDUCATOR SECTION (PAGES 1-7) improved. STUDENT SECTION (PAGES 8-15) Background Why do we need robotic arms when working in space? As an example, try holding a book in your hands straight out in front of you and not moving them for one or two minutes. After a while, do your hands start to shake or move around? Imagine how hard it would be to hold your hands steady for many days in a row, or to lift something really heavy. Wouldn’t it be nice to have a really long arm that never gets tired? Well, to help out in space, scientists have designed and used robotic arms for years. On Earth, scientists have designed robotic arms for everything from moving heavy equipment to performing delicate surgery. Robotic arms are important machines that help people work on Earth as well as in space. Astronaut attached to a robotic arm on the ISS. Look at your arms once again. Your arms are covered in skin for protection. -
International Space Station Program Mobile Servicing System (MSS) To
SSP 42004 Revision E Mobile Servicing System (MSS) to User (Generic) Interface Control Document Part I International Space Station Program Revision E, May 22, 1997 Type 1 Approved by NASA National Aeronautics and Space Administration International Space Station Program Johnson Space Center Houston, Texas Contract No. NAS15–10000 SSP 42004, Part 1, Revision E May 22, 1997 REVISION AND HISTORY PAGE REV. DESCRIPTION PUB. DATE C Totally revised Space Station Freedom Document into an International Space Station Alpha Document 03–14–94 D Revision D reference PIRNs 42004–CS–0004A, 42004–NA–0002, 42004–NA–0003, TBD 42004–NA–0004, 42004–NA–0007D, 42004–NA–0008A, 42004–NA–0009C, 42004–NA–0010B, 42004–NA–0013A SSP 42004, Part 1, Revision E May 22, 1997 INTERNATIONAL SPACE STATION PROGRAM MOBILE SERVICING SYSTEM TO USER (GENERIC) INTERFACE CONTROL DOCUMENT MAY 22, 1997 CONCURRENCE PREPARED BY: PRINT NAME ORGN SIGNATURE DATE CHECKED BY: PRINT NAME ORGN SIGNATURE DATE SUPERVISED BY (BOEING): PRINT NAME ORGN SIGNATURE DATE SUPERVISED BY (NASA): PRINT NAME ORGN SIGNATURE DATE DQA: PRINT NAME ORGN SIGNATURE DATE i SSP 42004, Part 1, Revision E May 22, 1997 NASA/CSA INTERNATIONAL SPACE STATION PROGRAM MOBILE SERVICING SYSTEM (MSS) TO USER INTERFACE CONTROL DOCUMENT MAY 22, 1997 Print Name For NASA DATE Print Name For CSA DATE ii SSP 42004, Part 1, Revision E May 22, 1997 PREFACE SSP 42004, Mobile Servicing System (MSS) to User Interface Control Document (ICD) Part I shall be implemented on all new Program contractual and internal activities and shall be included in any existing contracts through contract changes. -
IADC Space Debris Mitigation Guidelines
IADC-02-01 Revision 2 Mar 2020 IADC Space Debris Mitigation Guidelines Issued by IADC Steering Group and Working Group 4 Table of Contents Table of Contents .................................................................................................................. 1 Revision History .................................................................................................................... 2 List of Abbreviations .............................................................................................................. 3 1 Scope ............................................................................................................................. 6 2 Application ...................................................................................................................... 6 3 Terms and definitions ..................................................................................................... 6 3.1 Space Debris ........................................................................................................... 6 3.2 Spacecraft, Launch Vehicles, and Orbital Stages .................................................... 6 3.3 Orbits and Protected Regions ................................................................................. 7 3.4 Mitigation Measures and Related Terms ................................................................. 8 3.5 Operational Phases ................................................................................................. 8 4 General Guidance ......................................................................................................... -
Treaties and Other International Acts Series 94-1115 ______
TREATIES AND OTHER INTERNATIONAL ACTS SERIES 94-1115 ________________________________________________________________________ SPACE Cooperation Memorandum of Understanding Between the UNITED STATES OF AMERICA and CANADA Signed at Washington November 15, 1994 with Appendix NOTE BY THE DEPARTMENT OF STATE Pursuant to Public Law 89—497, approved July 8, 1966 (80 Stat. 271; 1 U.S.C. 113)— “. .the Treaties and Other International Acts Series issued under the authority of the Secretary of State shall be competent evidence . of the treaties, international agreements other than treaties, and proclamations by the President of such treaties and international agreements other than treaties, as the case may be, therein contained, in all the courts of law and equity and of maritime jurisdiction, and in all the tribunals and public offices of the United States, and of the several States, without any further proof or authentication thereof.” CANADA Space: Cooperation Memorandum of Understanding signed at Washington November 15, 1994; Entered into force November 15, 1994. With appendix. MEMORANDUM OF UNDERSTANDING between the UNITED STATES NATIONAL AERONAUTICS AND SPACE ADMINISTRATION and the CANADIAN SPACE AGENCY concerning COOPERATION IN THE FLIGHT OF THE MEASUREMENTS OF POLLUTION IN THE TROPOSPHERE (MOPITT) INSTRUMENT ON THE NASA POLAR ORBITING PLATFORM AND RELATED SUPPORT FOR AN INTERNATIONAL EARTH OBSERVING SYSTEM 2 The United States National Aeronautics and Space Administration (hereinafter "NASA") and the Canadian Space Agency (hereinafter "CSA") -
International Space Exploration Coordination Group (ISECG) Provides an Overview of ISECG Activities, Products and Accomplishments in the Past Year
Annual Report 2012 of the International Space Exploration Coordination Group INTERNATIONAL SPACE EXPLORATION COORDINATION GROUP ISECG Secretariat Keplerlaan 1, PO Box 299, NL-2200 AG Noordwijk, The Netherlands +31 (0) 71 565 3325 [email protected] ISECG publications can be found on: http://www.globalspaceexploration.org/ 2 Table of Contents 1. Introduction 4 2. Executive Summary 4 3. Background 5 4. Activities 4.1. Overview 7 4.2. Activities on ISECG Level 7 4.3. Working Group Activities 8 4.3.1. Exploration Roadmap Working Group (ERWG) 8 4.3.2. International Architecture Working Group (IAWG) 9 4.3.3. International Objectives Working Group (IOWG) 10 4.3.4. Strategic Communications Working Group (SCWG) 10 Annex: Space Exploration Highlights of ISECG Member Agencies 12 1. Agenzia Spaziale Italiana (ASI), Italy 13 2. Centre National d’Etudes Spatiales (CNES), France 15 3. Canadian Space Agency (CSA), Canada 17 4. Deutsches Zentrum für Luft- und Raumfahrt e.V. (DLR), Germany 21 5. European Space Agency (ESA) 23 6. Japan Aerospace Exploration Agency (JAXA), Japan 28 7. Korea Aerospace Research Institute (KARI), Republic of Korea 30 8. National Aeronautics and Space Administration (NASA), USA 31 9. State Space Agency of Ukraine (SSAU), Ukraine 33 10. UK Space Agency (UKSA), United Kingdom 35 3 1 Introduction The 2012 Annual Report of the International Space Exploration Coordination Group (ISECG) provides an overview of ISECG activities, products and accomplishments in the past year. In the annex many of the ISECG participating agencies report on national space exploration highlights in 2012. 2 Executive Summary ISECG was established in response to the “The Global Exploration Strategy: The Framework for Coordination” (GES) developed by 14 space agencies1 and released in May 2007. -
Canadian Space Agency
Canadian Space Agency ERIC LALIBERTÉ DIRECTOR GENERAL, SPACE UTILIZATION Outline • Mandate & Objectives • International Collaboration • Key Activities • Flagship Missions • Scientific Activities • Social and Economic Benefits • Strategic Implications 2 Outline Mandate Promote the peaceful use and development of space, to advance the knowledge of space through science and to ensure that space science and technology provide social and economic benefits for Canadians Departmental Results Space Space Canada's research and Canadians information and investments in development engage with technologies space benefit the advances space improve the lives Canadian science and of Canadians economy technology 3 International Collaboration • All space-faring countries rely on international collaboration • Canada a critical contributor to the US; entrusted with critical components • 21 international MOUs that provide a framework for project level collaboration with X countries • Only non-European Cooperating Member of the European Space Agency (ESA) • Key partner on the International Space Station • Founding member of the International Charter on Space and Major Disasters 4 Key Activities Exploration – Leads Canada’s participation in the International Space Station (ISS), planetary exploration missions and astronomy missions Satellites – Leads the implementation of the earth observation/science satellites to ensure GoC needs are met for high quality space data, applications and services essential for the provision of services to Canadians Technology -
STS-135: the Final Mission Dedicated to the Courageous Men and Women Who Have Devoted Their Lives to the Space Shuttle Program and the Pursuit of Space Exploration
National Aeronautics and Space Administration STS-135: The Final Mission Dedicated to the courageous men and women who have devoted their lives to the Space Shuttle Program and the pursuit of space exploration PRESS KIT/JULY 2011 www.nasa.gov 2 011 2009 2008 2007 2003 2002 2001 1999 1998 1996 1994 1992 1991 1990 1989 STS-1: The First Mission 1985 1981 CONTENTS Section Page SPACE SHUTTLE HISTORY ...................................................................................................... 1 INTRODUCTION ................................................................................................................................... 1 SPACE SHUTTLE CONCEPT AND DEVELOPMENT ................................................................................... 2 THE SPACE SHUTTLE ERA BEGINS ....................................................................................................... 7 NASA REBOUNDS INTO SPACE ............................................................................................................ 14 FROM MIR TO THE INTERNATIONAL SPACE STATION .......................................................................... 20 STATION ASSEMBLY COMPLETED AFTER COLUMBIA ........................................................................... 25 MISSION CONTROL ROSES EXPRESS THANKS, SUPPORT .................................................................... 30 SPACE SHUTTLE PROGRAM’S KEY STATISTICS (THRU STS-134) ........................................................ 32 THE ORBITER FLEET ............................................................................................................................ -
Nanoracks External Cubesat Deployer (NRCSD-E) Interface Definition Document (IDD) 08/31/2018
NanoRacks External CubeSat Deployer (NRCSD-E) Interface Definition Document (IDD) 08/31/2018 Doc No: NR-NRCSD-S0004 Revision: - THIS DOCUMENT HAS NOT BEEN APPROVED FOR PUBLIC RELEASE BY THE UNITED STATES DEPARTMENT OF DEFENSE. NANORACKS PROPRIETARY RIGHTS ARE INCLUDED HEREIN. RECIPIENT AGREES THAT NEITHER THIS DOCUMENT NOR THE INFORMATION DISCUSSED HEREIN NOR ANY PART THEREOF SHALL BE REPRODUCED OR DISCLOSED TO OTHERS. NanoRacks External CubeSat Deployer IDD NRCSD External Doc No: NR-NRCSD-S0004 Rev: - NanoRacks External CubeSat Deployer Interface Definition Document (IDD) Prepared by Nathan Daniels; Mission Manager; Date Reviewed by Henry Martin; Senior Mission Manager; Date Reviewed by Conor Brown; External Payloads Manager; Date Reviewed by Troy Guy; Avionics Manager; Date Reviewed by Teresa Freund; Safety Engineer; Date Approved by Mike Lewis; Chief Technology Officer; Date NanoRacks External CubeSat Deployer IDD NRCSD External Doc No: NR-NRCSD-S0004 Rev: - List of Revisions Revision Revision Date Revised By Revision Description - 8/31/2018 N. Daniels Initial Release NanoRacks External CubeSat Deployer IDD NRCSD External Doc No: NR-NRCSD-S0004 Rev: - Table of Contents 1 Introduction 1 1.1 Purpose 1 1.1.1 Scope 1 1.2 Usage 1 1.3 Exceptions 1 2 Acronyms, Definitions, and Applicable Documents 2 3 NanoRacks External CubeSat Deployer System Overview 5 3.1 NRCSD-E Overview and Payload Capacity 5 3.2 NRCSD-E Coordinate System 5 3.3 NRCSD-E Design Features 6 3.4 NRCSD-E Operations Overview 7 3.4.1 Schedule 7 3.4.2 Ground Operations 8 3.4.3