Design and Implementation of a Low-Power Low-Cost Digital
Total Page:16
File Type:pdf, Size:1020Kb
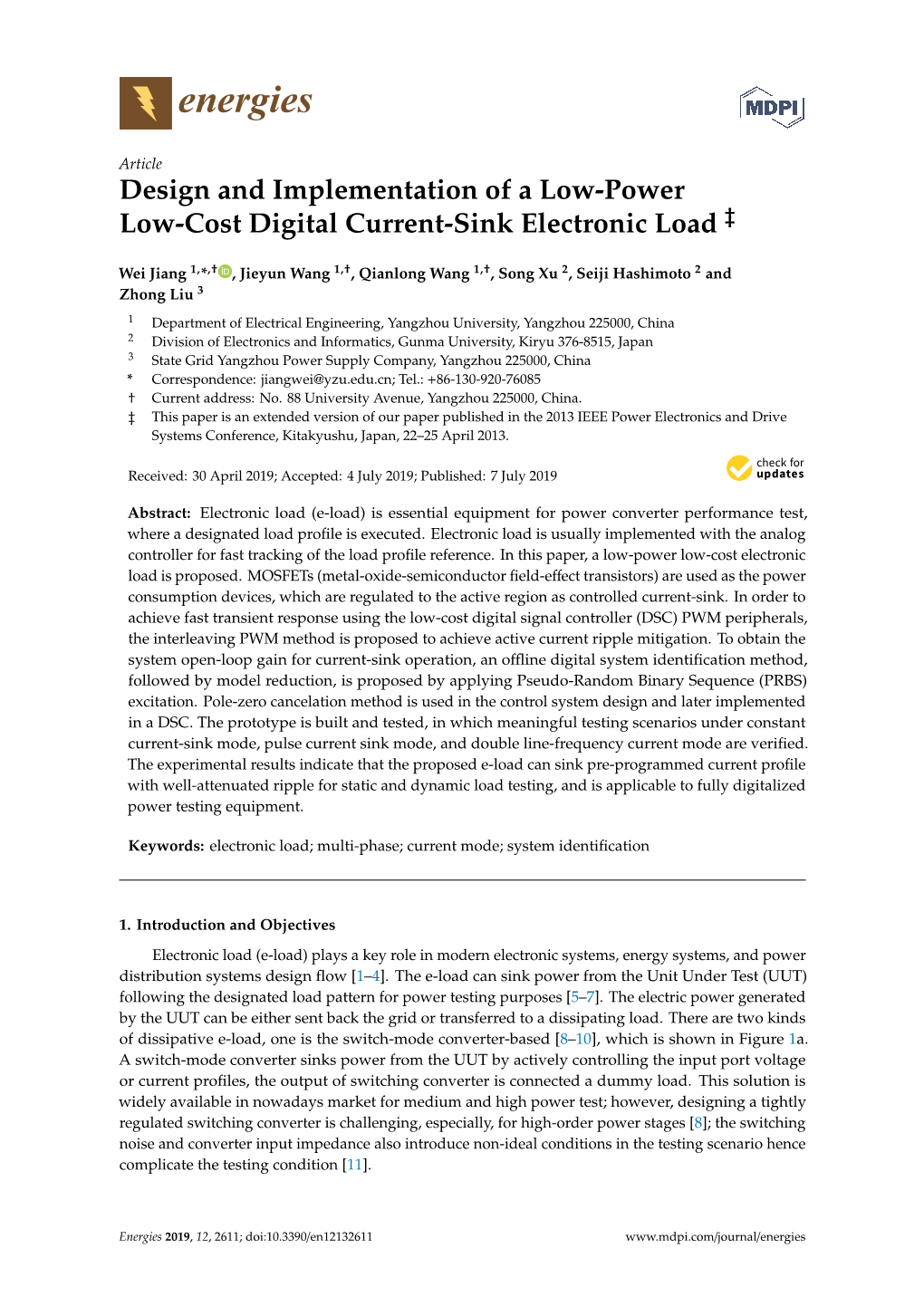
Load more
Recommended publications
-
Ultracapacitors for Port Crane Applications: Sizing and Techno-Economic Analysis
energies Article Ultracapacitors for Port Crane Applications: Sizing and Techno-Economic Analysis Mostafa Kermani 1,*, Giuseppe Parise 1, Ben Chavdarian 2 and Luigi Martirano 1 1 Department of Astronautical, Electrical and Energy Engineering (DIAEE), Sapienza University of Rome, 00184 Rome, Italy; [email protected] (G.P.); [email protected] (L.M.) 2 P2S, Inc., Long Beach, CA 90815, USA; [email protected] * Correspondence: [email protected] Received: 2 March 2020; Accepted: 7 April 2020; Published: 22 April 2020 Abstract: The use of energy storage with high power density and fast response time at container terminals (CTs) with a power demand of tens of megawatts is one of the most critical factors for peak reduction and economic benefits. Peak shaving can balance the load demand and facilitate the participation of small power units in generation based on renewable energies. Therefore, in this paper, the economic efficiency of peak demand reduction in ship to shore (STS) cranes based on the ultracapacitor (UC) energy storage sizing has been investigated. The results show the UC energy storage significantly reduce the peak demand, increasing the load factor, load leveling, and most importantly, an outstanding reduction in power and energy cost. In fact, the suggested approach is the start point to improve reliability and reduce peak demand energy consumption. Keywords: ultracapacitor sizing; techno-economic analysis; energy storage system (ESS); ship to shore (STS) crane; peak shaving; energy cost 1. Introduction It is well known that large-scale commodity (and people) transport uses the sea as a crucial and optimal route. In maritime transportation ports and harbors with power demands of tens of megawatts based on some vast consumers with a high peak level (such as giant cranes, cold ironing, etc.) require a unique power system. -
Introduction to Power Quality
CHAPTER 1 INTRODUCTION TO POWER QUALITY 1.1 INTRODUCTION This chapter reviews the power quality definition, standards, causes and effects of harmonic distortion in a power system. 1.2 DEFINITION OF ELECTRIC POWER QUALITY In recent years, there has been an increased emphasis and concern for the quality of power delivered to factories, commercial establishments, and residences. This is due to the increasing usage of harmonic-creating non linear loads such as adjustable-speed drives, switched mode power supplies, arc furnaces, electronic fluorescent lamp ballasts etc.[1]. Power quality loosely defined, as the study of powering and grounding electronic systems so as to maintain the integrity of the power supplied to the system. IEEE Standard 1159 defines power quality as [2]: The concept of powering and grounding sensitive equipment in a manner that is suitable for the operation of that equipment. In the IEEE 100 Authoritative Dictionary of IEEE Standard Terms, Power quality is defined as ([1], p. 855): The concept of powering and grounding electronic equipment in a manner that is suitable to the operation of that equipment and compatible with the premise wiring system and other connected equipment. Good power quality, however, is not easy to define because what is good power quality to a refrigerator motor may not be good enough for today‟s personal computers and other sensitive loads. 1.3 DESCRIPTIONS OF SOME POOR POWER QUALITY EVENTS The following are some examples and descriptions of poor power quality “events.” Fig. 1.1 Typical power disturbances [2]. ■ A voltage sag/dip is a brief decrease in the r.m.s line-voltage of 10 to 90 percent of the nominal line-voltage. -
Wireless Power Transmission
International Journal of Scientific & Engineering Research, Volume 5, Issue 10, October-2014 125 ISSN 2229-5518 Wireless Power Transmission Mystica Augustine Michael Duke Final year student, Mechanical Engineering, CEG, Anna university, Chennai, Tamilnadu, India [email protected] ABSTRACT- The technology for wireless power transfer (WPT) is a varied and a complex process. The demand for electricity is much higher than the amount being produced. Generally, the power generated is transmitted through wires. To reduce transmission and distribution losses, researchers have drifted towards wireless energy transmission. The present paper discusses about the history, evolution, types, research and advantages of wireless power transmission. There are separate methods proposed for shorter and longer distance power transmission; Inductive coupling, Resonant inductive coupling and air ionization for short distances; Microwave and Laser transmission for longer distances. The pioneer of the field, Tesla attempted to create a powerful, wireless electric transmitter more than a century ago which has now seen an exponential growth. This paper as a whole illuminates all the efficient methods proposed for transmitting power without wires. —————————— —————————— INTRODUCTION Wireless power transfer involves the transmission of power from a power source to an electrical load without connectors, across an air gap. The basis of a wireless power system involves essentially two coils – a transmitter and receiver coil. The transmitter coil is energized by alternating current to generate a magnetic field, which in turn induces a current in the receiver coil (Ref 1). The basics of wireless power transfer involves the inductive transmission of energy from a transmitter to a receiver via an oscillating magnetic field. -
The Basics of Electricity and Vehicle Lighting the Basics of Electricity and Lighting
$200.00 USD Series of Self-Study Guides from Grote Industries The Basics of Electricity and Vehicle Lighting The Basics of Electricity and Lighting How To Use This Book This self-study guide is divided into six sec- down to expose the first line of the second tions that cover topics from basic theory of question. The answer to the first question is electricity to choosing the right equipment. shown at the far right. Compare your answer It presents the information in text form sup- to the answer key. ported by illustrations, diagrams charts and Choose an answer to the second question. other graphics that highlight and explain key Slide the cover sheet down to expose the first points. Each section also includes a short quiz line of the third question and compare your to give the you a measure of your comprehen- answer to the answer key. sion. At the end of the guide is a final test that In the same manner, answer the balance of is designed to measure the learner’s overall the quiz questions. comprehension of the material. The final exam at the end of this guide To get the most value from this study guide, presents a second test of your knowledge of carefully read the text and study the illustra- the material. Be certain to use the quizzes and tions in each section. In some cases, you may final exam. In the case of the final exam, fold want to underline or highlight key information the answer sheet as directed, and mail to the for easier review and study later. -
POWER QUALITY Energy Efficiency Reference Guide DISCLAIMER: Neither CEA Technologies Inc
POWER QUALITY Energy Efficiency Reference Guide DISCLAIMER: Neither CEA Technologies Inc. (CEATI), the authors, nor any of the organizations providing funding support for this work (including any persons acting on the behalf of the aforementioned) assume any liability or responsibility for any dam- ages arising or resulting from the use of any information, equip- ment, product, method or any other process whatsoever disclosed or contained in this guide. The use of certified practitioners for the application of the informa- tion contained herein is strongly recommended. This guide was prepared by Energy @ Work for the CEA Technologies Inc. (CEATI) Customer Energy Solutions Interest Group (CESIG) with the sponsorship of the following utility consortium participants: © 2007 CEA Technologies Inc. (CEATI) All rights reserved. Appreciation to Ontario Hydro, Ontario Power Generation and others who have contributed material that has been used in preparing this guide. Table of Contents Chapter Page Foreword 5 Power Quality Guide Format 5 1.0 The Scope of Power Quality 9 1.1 Definition of Power Quality 9 1.3 Why Knowledge of Power Quality is Important 13 1.4 Major Factors Contributing to Power Quality Issues 14 1.5 Supply vs. End Use Issues 15 1.6 Countering the Top 5 PQ Myths 16 1.7 Financial and Life Cycle Costs 19 2.0 Understanding Power Quality Concepts 23 2.1 The Electrical Distribution System 23 2.2 Basic Power Quality Concepts 28 3.0 Power Quality Problems 33 3.1 How Power Quality Problems Develop 33 3.2 Power Quality Disturbances 35 3.3 -
Short-Circuit Current Calculations
Short-Circuit Current Calculations Basic Point-to-Point Calculation Procedure At some distance from the terminals, depending upon wire size, the L-N fault Step 1. Determine the transformer full load amps (F.L.A.) from current is lower than the L-L fault current. The 1.5 multiplier is an approximation and will theoretically vary from 1.33 to 1.67. These figures are based on change in turns ratio between primary and secondary, infinite source available, zero feet from terminals of transformer, and 1.2 x %X and 1.5 x %R for L-N vs. L-L resistance and reactance values. Begin L-N calculations at transformer secondary terminals, then proceed point-to-point. Step 5. Calculate "M" (multiplier) or take from Table 2. either the nameplate, the following formulas or Table 1: M = 1 1 + f Multiplier = 100 *%Z transformer Step 6. Calculate the available short circuit symmetrical RMS current at the point of fault. Add motor contribution, if Step 2. Find the transformer multiplier. See Notes 1 and 2 applicable. * Note 1. Get %Z from nameplate or Table 1. Transformer impedance (Z) helps to IS.C. sym. RMS = IS.C. x M determine what the short circuit current will be at the transformer secondary. Transformer impedance is determined as follows: The transformer secondary is short Step 6A. Motor short circuit contribution, if significant, may be circuited. Voltage is increased on the primary until full load current flows in the added at all fault locations throughout the system. A secondary. This applied voltage divided by the rated primary voltage (times 100) is the practical estimate of motor short circuit contribution is to impedance of the transformer. -
A Review on the Selected Applications of Battery-Supercapacitor Hybrid Energy Storage Systems for Microgrids
energies Review A Review on the Selected Applications of Battery-Supercapacitor Hybrid Energy Storage Systems for Microgrids Muhammad Khalid 1,2 1 Electrical Engineering Department, King Fahd University of Petroleum and Minerals, Dhahran 31261, Saudi Arabia; [email protected]; Tel.: +966-13-860-8076 2 K A CARE Energy Research & Innovation Center, Dhahran 31261, Saudi Arabia · · Received: 23 October 2019; Accepted: 20 November 2019; Published: 29 November 2019 Abstract: This paper presents a comprehensive categorical review of the recent advances and past research development of the hybrid storage paradigm over the last two decades. The main intent of the study is to provide an application-focused survey where every category and sub-category herein is thoroughly and independently investigated. Implementation of energy storage systems is one of the most interestingly effective options for further progression in the field of alternative energy technology. Apart from a meticulous garnering of the energy resources regulated by the energy storage, the main concern is to optimize the characteristic integrity of the storage devices to achieve a practically techno-economic size and operation. In this paper, hybrid energy storage consisting of batteries and supercapacitors is studied. The fact that the characteristic of batteries is mostly complementary to that of supercapacitors, hybridizing these storage systems enhances their scope of application in various fields. Therefore, the objective of this paper is to present an inclusive review of these applications. Specifically, the application domain includes: (1) regulation of renewable energy sources, (2) contributions to grid regulation (voltage and frequency compensation, contribution to power system inertia), (3) energy storage enhancements (life cycle improvement, and size reduction), (4) regenerative braking in electric vehicles, (5) improvement in wireless power transfer technology. -
The Seven Types of Power Problems
The Seven Types of Power Problems White Paper 18 Revision 1 by Joseph Seymour Contents > Executive summary Click on a section to jump to it Introduction 2 Many of the mysteries of equipment failure, downtime, software and data corruption, are the result of a prob- Transients 4 lematic supply of power. There is also a common problem with describing power problems in a standard Interruptions 8 way. This white paper will describe the most common types of power disturbances, what can cause them, Sag / undervoltage 9 what they can do to your critical equipment, and how to Swell / overvoltage 10 safeguard your equipment, using the IEEE standards for describing power quality problems. Waveform distortion 11 Voltage fluctuations 15 Frequency variations 15 Conclusion 18 Resources 19 Appendix 20 RATE THIS PAPER white papers are now part of the Schneider Electric white paper library produced by Schneider Electric’s Data Center Science Center [email protected] The Seven Types of Power Problems Introduction Our technological world has become deeply dependent upon the continuous availability of electrical power. In most countries, commercial power is made available via nationwide grids, interconnecting numerous generating stations to the loads. The grid must supply basic national needs of residential, lighting, heating, refrigeration, air conditioning, and transporta- tion as well as critical supply to governmental, industrial, financial, commercial, medical and communications communities. Commercial power literally enables today’s modern world to function at its busy pace. Sophisticated technology has reached deeply into our homes and careers, and with the advent of e-commerce is continually changing the way we interact with the rest of the world. -
POWER up TERMS for AC Power Management
POWER UP TERMS for AC Power Management AC Receptacles (15 amp versus 20 amp) = In order to prevent a mismatch between power loads and electric power sources, various styles of AC receptacles are designated for specific applications. There are many receptacle configurations, each designed for a specific voltage, current load or single or three phase application. Those configurations most commonly encountered in residential and light commercial installations are the NEMA 5-15 and NEMA 5-20. The suffix “P” following the NEMA designation indicates the connector is a plug (male). The suffix “R” indicates a receptacle (female). The NEMA 5-15 is rated for a maximum current load of fifteen amps, and is the type of wall outlet commonly found in a home. It has two parallel blades, one for hot and one for neutral. The NEMA 5-20 is rated at twenty amps and has one blade at a right angle to the other. “Hybrid” receptacles which are rated at 20 amps but have a “T” shaped slot to allow use with either a fifteen amp or twenty amp plug are often also called NEMA 5-20. Other, less frequently encountered AC power connectors are the locking or “twist-lock” variety indicated with a prefix “L” (e.g. L5-20R) and a range of thirty amp connectors (e.g. L5-30R). Note, almost always a thirty amp connector will be the locking variety. Alternating Current (AC) = The flow of electricity changes direction on a systematic basis. For US power utilities this direction change occurs sixty times per second (60 Hz) which is referred to as its frequency. -
Supercapacitors Serving As Power Supply in Tiny Sport Sensors Field Testing Through Heart Rate Monitoring in Endurance Trail Runs
Supercapacitors Serving as Power Supply in Tiny Sport Sensors Field Testing Through Heart Rate Monitoring in Endurance Trail Runs Hans Weghorn BW Cooperative State University, Kronenstrasse 53A, 70174 Stuttgart, Germany Keywords: Body Sensor, Heart Rate Monitor, Endurance Training, ANT+, Bluetooth LE. Abstract: In professional and in non-elite sport activities, people today are using various electronic monitoring tools quite commonly. Sportspersons often are embedded into a personal body sensor network, which traces different parameters of their physiological activity. Especially heart rate sensors are used broadly, but often all kinds of meters, e.g., for counting foot steps and pedal turning, are also utilized in parallel. As technical construction, it has commonly established that these sensor devices are autonomously operated as very tiny computer systems from built-in lithium battery cells. Replacing such sensor batteries from time to time is expensive, the mechanical handling of this process is not very easy due to the small sensor housings, and it has to be reminded that use of throwaway batteries represents a waste of resources. In this work, an alternative power supply for sports sensors is investigated, which bases on the use of so-called supercapacitors. Construction concepts, advantages of the approach related to handling and manufacturing, and the possible application ranges are thoroughly discussed, while the study is complemented with practical experiments from endurance running sports. 1 INTRODUCTION and recording. Fig. 1 shows three different HR devices, two of them communicate through the so- Improving health by controlled physical activities called Bluetooth LE standard (Bluetooth SIG, 2017), plays an important role in our modern and aging while the third unit (device S) broadcasts its societies. -
Transformer Theory
Tyco Electronics Corporation Crompton Instruments 1610 Cobb International Parkway, Unit #4 Kennesaw, GA 30152 Tel. 770-425-8903 Fax. 770-423-7194 TRANSFORMERS INTRODUCTION A transformer is a device that transfers electrical energy from one circuit to another by electromagnetic induction (also called transformer action). It is most often used to step up or step down voltage. Occasionally, it is used as an isolating device to eliminate a direct mechanical electrical connection between the power source and the loads. The electrical energy is always transferred without a change in frequency but may involve changes in the effective value of voltage and current. Because a transformer works on the principle of electromagnetic induction, it must be used with an input source that varies in amplitude. Examining a very unusual transformer will show power is transferred through the use of electromagnetic induction. This direct current transformer will demonstrate the actions of a step-up transformer and provide stop-action analysis of the moving magnetic field. Figure 8-1 shows a one-line diagram of the primary and secondary automobile ignition system. The primary circuit, or power source side, includes the battery positive terminal, the ignition switch, the primary winding to the ignition points, and the battery negative terminal. The secondary circuit starts with the secondary winding wire and connects the distributor rotor and the spark plug. When both the ignition switch and the points are closed, there is a complete circuit through the 12-volt battery terminals and the primary windings. As a current initially moves through the conductor, an expanding magnetic field is created. -
Guide for Use of Supercapacitors in the Marine and Offshore Industries
Guide for Use of Supercapacitors in the Marine and Offshore Industries GUIDE FOR USE OF SUPERCAPACITORS IN THE MARINE AND OFFSHORE INDUSTRIES DECEMBER 2017 American Bureau of Shipping Incorporated by Act of Legislature of the State of New York 1862 2017 American Bureau of Shipping. All rights reserved. ABS Plaza 16855 Northchase Drive Houston, TX 77060 USA Foreword Foreword Hybrid electric power applications are increasing in the marine and offshore industries. ABS recognizes the application of supercapacitor technology in support of the hybrid initiatives and its benefits for improving energy efficiency of the onboard power plant. Supercapacitors, as a commercialized energy storage device, exhibit beneficial characteristics such as high power density, a fast charging/discharging process, no thermal runaway characteristics, and wide operating-temperature range. The operating environment typical in the marine and offshore industries may differ from those considered when a supercapacitor system was originally designed and so necessitates a review of the environmental and operational aspects prior to adoption. ABS has produced this Guide to provide requirements and reference standards to facilitate effective installation and operation of on-board supercapacitor systems. The purpose of this Guide is to establish safety guidelines for owners, operators, shipyard builders, designers, and manufacturers. The supercapacitors covered by this Guide are also referred as Electrical Double Layer Capacitors (EDLC), Electrochemical Capacitors, or Ultracapacitors. Requirements applicable to conventional electrolytic capacitors used for power factor correction or harmonic filtering are contained in Part 4 of the ABS Rules for Building and Classing Steel Vessels. Supercapacitor technology is continuously evolving with respect to materials and design.