The Effects of Ph on Alkaline Sizing of Bleached Hardwood Pulps with Aquapel
Total Page:16
File Type:pdf, Size:1020Kb
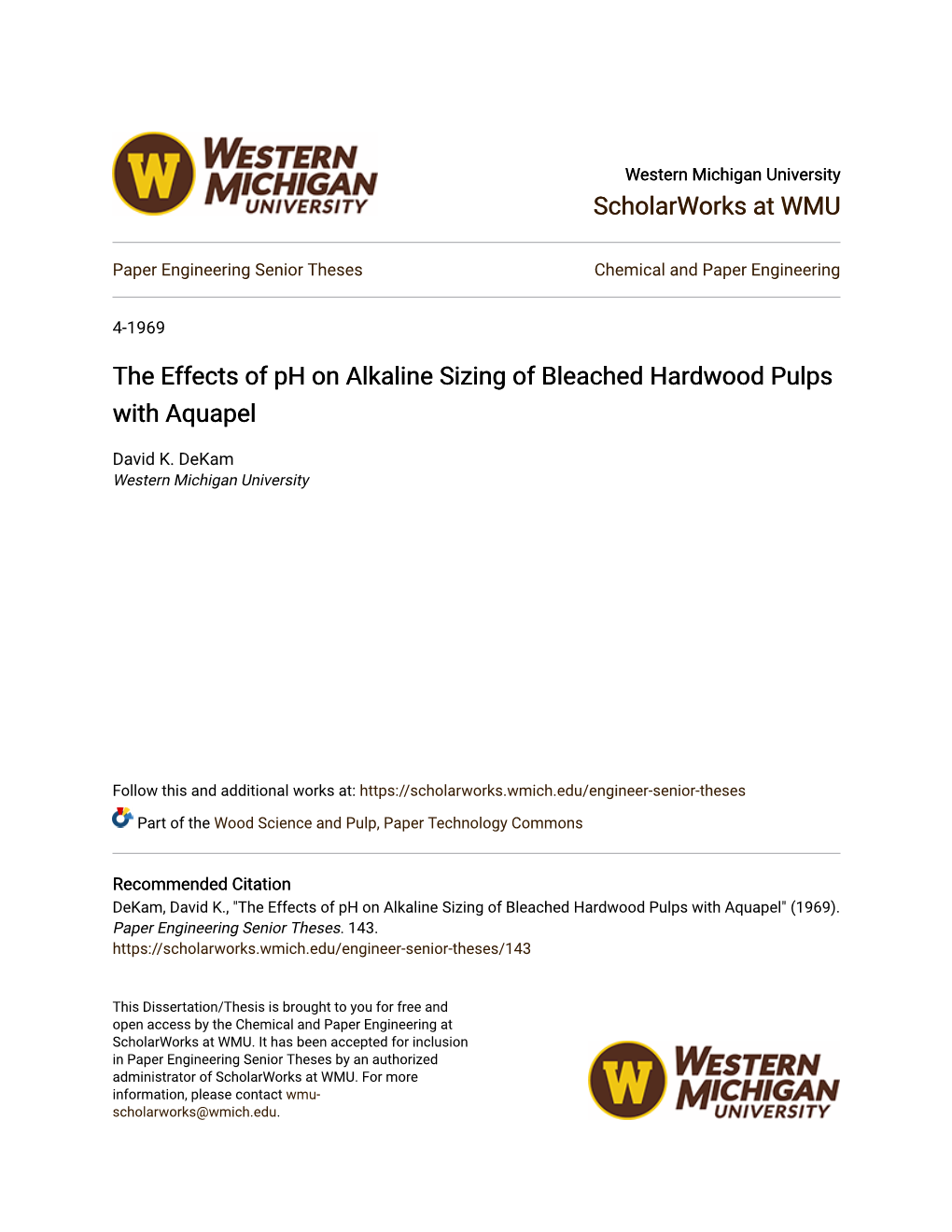
Load more
Recommended publications
-
What Happens to Cellulosic Fibers During Papermaking and Recycling? a Review
PEER-REVIEWED REVIEW ARTICLE ncsu.edu/bioresources WHAT HAPPENS TO CELLULOSIC FIBERS DURING PAPERMAKING AND RECYCLING? A REVIEW Martin A. Hubbe,* Richard A. Venditti, and Orlando J. Rojas Both reversible and irreversible changes take place as cellulosic fibers are manufactured into paper products one or more times. This review considers both physical and chemical changes. It is proposed that by understanding these changes one can make better use of cellulosic fibers at various stages of their life cycles, achieving a broad range of paper performance characteristics. Some of the changes that occur as a result of recycling are inherent to the fibers themselves. Other changes may result from the presence of various contaminants associated with the fibers as a result of manufacturing processes and uses. The former category includes an expected loss of swelling ability and decreased wet-flexibility, especially after kraft fibers are dried. The latter category includes effects of inks, de-inking agents, stickies, and additives used during previous cycles of papermaking. Keywords: Paper recycling, Drying, Deinking, Hornification, Inter-fiber bonding, Refining, Fines, Fiber length, Conformability Contact information: Department of Forest Biomaterials Science and Engineering, Box 8005, North Carolina State University, Raleigh, NC 27695-8005, USA; *Corresponding author: [email protected] INTRODUCTION Cellulosic fibers can change significantly when formed into a wet web of paper and subsequently subjected to such processes as pressing, drying, printing, storage, repulping, and deinking. Some of the changes can be subtle. Often it is possible to substitute recovered fibers in place of virgin fibers used for the production of paper or paperboard. On the other hand, characteristic differences between recycled fibers and virgin fibers (fresh from pulping wood, not recycled) can be expected; many of these can be attributed to drying. -
TECHNICAL REPORT – PATENT ANALYSIS Enhancing Productivity in the Indian Paper and Pulp Sector
TECHNICAL REPORT – PATENT ANALYSIS Enhancing Productivity in the Indian Paper and Pulp Sector 2018 TABLE OF contEnts ACKNOWLEDGEMENTS 10 EXECUTIVE SUMMARY 11 1 INTRODUCTION 13 2 OVERVIEW OF THE PULP AND PAPER SECTOR 15 2.1. Status of the Indian Paper Industry 15 2.2. Overview of the Pulp and Papermaking Process 20 2.3. Patenting in the Paper and Pulp Industry: A Historical Perspective 22 2.4. Environmental Impact of the Pulp and Paper Industry 25 3 METHODOLOGY 27 3.1. Search Strategy 27 4 ANALYSIS OF PATENT DOCUMENTS USING GPI 31 4.1. Papermaking; Production of Cellulose (IPC or CPC class D21) 31 4.2. Analysis of Patenting Activity in Different Technology Areas using GPI 38 5 ANALYSIS OF THE INDIAN PATENT SCENARIO WITHIN THE CONTEXT OF THIS REPORT 81 5.1. Analysis of Patents Filed in India 81 6 CONCLUDING REMARKS 91 REFERENCES 93 ANNEXURE 94 Annexure 1. Technologies related to paper manufacturing 94 Annexure 2. Sustainable/green technologies related to pulp and paper sector 119 Annexure 3. Emerging Technology Areas 127 List OF FIGURES Figure 2.1: Geographical Spread of Figure 4.11: (d) Applicant vs. Date of Indian Paper Mills .................................16 Priority Graph: Paper-Making Machines Figure 2.2: Share of Different Segments and Methods ........................................42 in Total Paper Production .......................19 Figure 4.11: (e) Applicant vs. Date of Figure 2.3: Variety Wise Production of Priority Graph: Calendars and Accessories ..43 Paper from Different Raw Materials ........19 Figure 4.11: (f) Applicant vs. Date of Figure 2.4: Different Varieties of Paper Priority Graph: Pulp or Paper Comprising Made from Various Raw Materials ..........19 Synthetic Cellulose or Non-Cellulose Fibres ..43 Figure 2.5: Diagram of a Process Block Figure 4.11: (g) Applicant vs. -
Pfass and Alternatives in Food Packaging (Paper and Paperboard): Report on the Commercial Availability and Current Uses
PFASs and alternatives in food packaging (paper and paperboard): Report on the commercial availability and current uses Series on Risk Management No. 58 1 Series on Risk Management 0 No. 58 PFASs and Alternatives in Food Packaging (Paper and Paperboard) Report on the Commercial Availability and Current Uses PUBE Please cite this publication as: OECD (2020), PFASs and Alternatives in Food Packaging (Paper and Paperboard) Report on the Commercial Availability and Current Uses, OECD Series on Risk Management, No. 58, Environment, Health and Safety, Environment Directorate, OECD. Acknowledgements: The OECD would like to acknowledge the drafting of a consultancy report by Steve Hollins of Exponent International Ltd. upon which this report is based. It was prepared under the framework of the OECD/UNEP Global PFC Group and included the contribution of information by several organisations (see Annex A). The report is published under the responsibility of the OECD Joint Meeting of the Chemicals Committee and the Working Party on Chemicals, Pesticides and Biotechnology. © Photo credits: Cover: Yuriy Golub/Shutterstock.com © OECD 2020 Applications for permission to reproduce or translate all or part of this material should be made to: Head of Publications Service, [email protected], OECD, 2 rue André-Pascal, 75775 Paris Cedex 16, France ABOUT THE OECD 3 About the OECD The Organisation for Economic Co-operation and Development (OECD) is an intergovernmental organisation in which representatives of 36 industrialised countries in North and South America, Europe and the Asia and Pacific region, as well as the European Commission, meet to co-ordinate and harmonise policies, discuss issues of mutual concern, and work together to respond to international problems. -
The Institute of Paper Science and Technology
The Institute of Paper Science and Technology Atlanta, Georgia Doctoral Dissertation Reprint AN INVESTIGATION OF THE MECHANISM OF ALKALINE SIZING WITH ALKENYL SUCCINIC ANHYDRIDE A thesis submitted by William R. McCarthy B.S. 1982, State University of New York, College of Environmental Science and Forestry, Syracuse, New York M.S. 1984, Lawrence University in partial fulfillment of the requirements of The Institute of Paper Chemistry for the degree of Doctor of Philosophy from Lawrence University Appleton, Wisconsin Publication rights reserved by The Institute of Paper Chemistry June, 1987 TABLE OF CONTENTS Page ABSTRACT 1 INTRODUCTION 3 Chemical Bonding 3 Internal Sizing 4 The Rosin-Alum System 5 Alkaline Sizing 6 Reasons for Use 7 Common Alkaline Sizes 7 Preparation and Theoretical Mechanism 8 Other Chemicals and Considerations 9 Anhydride Chemistry 12 AKD: Literature Review of the Reaction with Cellulose 14 and the Mechanism Summary of the AKD Literature 26 ASA: Literature Review of Factors Affecting Sizing 27 Reactions of Materials Related to ASA 28 Infrared and Diffuse Reflectance Infrared Spectrometry 28 PRESENTATION OF THE PROBLEM AND THESIS OBJECTIVES 31 APPROACH 32 The System 32 Materials 32 Analysis and Testing 33 Experimentation 34 EXPERIMENTAL MATERIALS, EQUIPMENT, AND PROCEDURES 36 Materials 36 Equipment 36 ii Procedures 37 Reaction of ASA in N,N-dimethylformamide with Cotton Linters 37 Handsheet Production 38 Hydrolysis Product Sheets 39 Conditioning and Sample Treatment 40 Hercules Size Tests 40 Spectrometric Techniques 41 -
CHAPTER 18 the GUM BICHROMATE PROCESS Fig: 18 -1 Here, Christopher James, Alicia in Gum #2, 2012 (Gum) OVERVIEW & EXPECTATIO
CHAPTER 18 THE GUM BICHROMATE PROCESS Fig: 18 -1 here, Christopher James, Alicia in Gum #2, 2012 (gum) OVERVIEW & EXPECTATIONS Here’s the truth… in the gum bichromate process there are very few absolutely correct ways to do anything. Here’s another nugget of dependable veracity… in my experience, gum bichromate printers are the most passionate and hard-headed of all alternative process artists when it comes to their particular way of performing the process. I can just imagine so many of my friends reading that last sentence and saying, "I just know he’s talking about me!" © Christopher James, The Book of Alternative Photographic Processes: 3rd Edition, 2015 When the gum bichromate process is broken down into its three component steps, and explained in the most elementary way possible, it appears to be amazingly uncomplicated. However, to nearly every one of my students who has been taken with the process, and for those artists who are dedicated to it for life, gum bichromate slowly reveals itself to be one of the most complex in the alternative process genre. The gum bichromate process is ridiculously seductive. This is primarily due to its very limited chemistry, oh-so-simple water development, unlimited color palette using the watercolors of the artist’s choice, and very flexible ability to be coupled with a wide range of other alternative and graphic arts techniques such as platinum / palladium, cyanotype, all forms of printmaking and artist’s books. I think of gum as the photographic ambassador to the fine arts. Because of its pigment and substrate options, and brush application, gum bichromate printing is one of the few photographic processes capable of achieving that wonderful element I refer to as gesture - gesture being the evidence of the artist’s hand in the creation of an expressive and graphic mark. -
Enzyme Applications in Pulp and Paper Industry
Enzyme Applications in Pulp and Paper: An Introduction to Applications Dr. Richard Venditti Associate Professor - Director of Graduate Programs Department of Wood and Paper Science Biltmore Hall Room 1204 Raleigh NC 27695-8005 Tel. (919) 515-6185 Fax. (919) 515-6302 Email: [email protected] Slides courtesy of Phil Hoekstra. Endo-Beta 1,4 Xylanase Enzymes • Are proteins that catalyze chemical reactions • Biological cells need enzymes to perform needed functions • The starting molecules that enzymes process are called substrates and these are converted to products Endo-Beta 1,4 Xylanase Cellulase enzyme which acts on cellulose substrate to make product of glucose. Endo-Beta 1,4 Xylanase Enzymes • Are extremely selective for specific substrates • Activity affected by inhibitors, pH, temperature, concentration of substrate • Commercial enzyme products are typically mixtures of different enzymes, the enzymes often complement the activity of one another Endo-Beta 1,4 Xylanase Types of Enzymes in Pulp and Paper and Respective Substrates • Amylase --- starch • Cellulase --- cellulose fibers • Protease --- proteins • Hemicellulases(Xylanase) ---hemicellulose • Lipase --- glycerol backbone, pitch • Esterase --- esters, stickies • Pectinase --- pectins Endo-Beta 1,4 Xylanase Enzyme Applications in Pulp and Paper • Treat starches for paper applications • Enhanced bleaching • Treatment for pitch • Enhanced deinking • Treatment for stickies in paper recycling • Removal of fines • Reduce refining energy • Cleans white water systems • Improve -
Enzymatic Deinking and Alkaline Sizing for Recycled Fiber
Enzymatic Deinking and Alkaline Sizing for Recycled Fiber Sharma Kumar Arvind, Sharma Anurag, S.K.Thapar and M.G.Panth Anmol Polymers Pvt. Ltd., New Delhi The use of de-inked pulp is essential from the Environment's point to conserve Forest and other resources. De-inking of Waste Paper is must to recycle the paper for producing quality Papers. Compared to the conventional chemical de-inking process, Biode-inking is a novel concept through which impact on environment is a bare minimum, due to less amount of chemicals used, it also results in cost savings. The savings in cost with Enzymatic De-inking can vary from Rs 150 to Rs.300.per metric ton of fiber. When mills started making Writing and Printing Papers with de- inked Pulps with imported waste paper furnishes, the major problem encountered by mills was due to its inherent filler quality i.e. Calcium Carbonate. It caused several problems during sizing process i.e fluctuations in pH conditions, from mixing chest to Head box. as pH of the stock was widely varying. A temporary solace was to carry out size addition near to Head box and to use dispersed rosin size, which was not a permanent solution. AKD /ASA Sizing, is the only an ultimate solution to overcome these problems. Calcium carbonate filler used has a great impact upon sizing depending upon whether filler is Ground Calcium Carbonate or Precipitated Calcium Carbonate. Precipitated Calcium Carbonate results in more problems as compared to Ground Calcium Carbonate during sizing process.. INTRODUCTION more than the brightness of unprinted paper prior to In a conventional de-inking process, Waste Paper is printing. -
Handmade Gampi
Table of Contents Introduction ........................................................................ 2 About Us & Ordering Terms ............................................ 3 History of Washi ................................................................ 4 Japanese Papermaking .................................................... 5 Differences Between Washi and Western Paper ................... 7 Where our Washi Comes From ...................................... 8 Paper Specifications ........................................................ 11 Pricelist ............................................................................... 16 Fine Art and Conservation Handmade Papers ............................................. 20 Machinemade Papers ....................................... 26 Gampi Papers ..................................................... 29 Large Size Papers .............................................. 31 Small Size/ Specialty Papers .......................... 34 Rolls 100% Kozo Rolls ................................................ 36 Kozo Mix Rolls ................................................... 38 100% Sulphite Pulp Rolls ................................. 38 Inkjet Coated Rolls ........................................... 39 Gampi Rolls ........................................................ 39 Rayon Rolls ......................................................... 40 Decorative Rolls ................................................ 40 Decorative ........................................................................ -
PRINTING PAPERS: SIZING and ITS ROLE Manisha S
Journal of Engineering Research and Studies E-ISSN 0976-7916 Review Article PRINTING PAPERS: SIZING AND ITS ROLE Manisha S. Deshpande Address for Correspondence M.E. (Printing) Third Semester, Pune University E Mail [email protected] Guided by- Prof R. G. Kaduskar, P. V. G’s College of Engineering and Technology, Pune ABSTRACT This document gives information about water resistant property of paper i.e. sizing. It gives details of sizing materials and requirement of properties for different printing methods. KEYWORDS Sizing, Printing Methods, Balanced sizing I. INTRODUCTION conventional practice to add the sizing agent to the paper It is considered that printing; has fostered communication furnish and thereafter add a precipitating agent which aids and propagated the knowledge, has done more to develop in setting the size of the papermaking fibres. The civilization. It has been so only because of use of paper. precipitating agents used are water-soluble polyvalent The forerunner of paper (c. 2600 BC) was papyrus, a metal salts, such as alum or aluminum chloride. Use of the material made out of the papyrus plant, which grows in aforesaid combination of sizing agent and precipitating Africa. The actual invention of paper produced from plant agent can be accomplished in conventional papermaking fibres such as bamboo fibres or cambric grass dates back to machines without the aid of any special apparatus. about AD 105; recent literature refers to paper production Moreover, the materials used are of low cost and are actually dating much further back. Tsai Lun from China is generally quite effective in imparting to paper the ability to accredited as the inventor. -
The Effects of Alum at Different Ph Levels on ASA Sizing
Western Michigan University ScholarWorks at WMU Paper Engineering Senior Theses Chemical and Paper Engineering 4-1986 The Effects of Alum at Different pH Levels on ASA Sizing James A. Farrand Western Michigan University Follow this and additional works at: https://scholarworks.wmich.edu/engineer-senior-theses Part of the Wood Science and Pulp, Paper Technology Commons Recommended Citation Farrand, James A., "The Effects of Alum at Different pH Levels on ASA Sizing" (1986). Paper Engineering Senior Theses. 123. https://scholarworks.wmich.edu/engineer-senior-theses/123 This Dissertation/Thesis is brought to you for free and open access by the Chemical and Paper Engineering at ScholarWorks at WMU. It has been accepted for inclusion in Paper Engineering Senior Theses by an authorized administrator of ScholarWorks at WMU. For more information, please contact wmu- [email protected]. THEJFFECTS OF ALUM AT DIFFERENT pH LEVELS ON ASA SIZING By: James A. Farrand A thesis submitted in partial fulfillment of the course requirements for the Bachelor of Science Degree Western Michigan University Kalamazoo, Michigan April, 1986 Or. Raymond Janes, Advisor ABSTRACT Alkenyl succinic anhydride (ASA) is a cellulose reactive size used in neutral to alkaline sizing. ASA is emulsified in cationic starch to help retain the ASA on the fiber and to protect the ASA from hydrolysis. The stabil ity of the ASA emulsion is largely dependent· upon temperature, pH, and shear. While one of the advantages of alkaline papermaking is the elimination of aluminum from the process water, the addition of small amounts of alum has proven beneficial to some mills running ASA size. -
The Effects of Repulping Variables on Deinking of Flexographic Inks
Western Michigan University ScholarWorks at WMU Master's Theses Graduate College 6-1995 The Effects of Repulping Variables on Deinking of Flexographic Inks Sylvia Ciampa Follow this and additional works at: https://scholarworks.wmich.edu/masters_theses Part of the Wood Science and Pulp, Paper Technology Commons Recommended Citation Ciampa, Sylvia, "The Effects of Repulping Variables on Deinking of Flexographic Inks" (1995). Master's Theses. 4916. https://scholarworks.wmich.edu/masters_theses/4916 This Masters Thesis-Open Access is brought to you for free and open access by the Graduate College at ScholarWorks at WMU. It has been accepted for inclusion in Master's Theses by an authorized administrator of ScholarWorks at WMU. For more information, please contact [email protected]. THE EFFECTS OF REPULPING VARIABLES ON DEINKING OF FLEXOGRAPHIC INKS by Sylvia Ciampa A Thesis Submitted to the Faculty of The Graduate College in partial fulfillment of the requirements for the Degree of Master of Science Department of Paper and Printing Science and Engineering Western Michigan University Kalamazoo, Michigan June 1995 ACKNOWLEDGEMENTS I would like to express my sincere gratitude to Dr. Raymond L. Janes. Without his valuable suggestions, advice and guidance this study would not have been completed. I also would like to thank Dr. John Crowell for his valuable statistics assistance, Dr. Ellsworth Shriver and Dr. Raja Aravamuthan for their constant encouragement, and John Serafano for his help. Finally I would like to thank my parents for their great support and love. Sylvia Ciampa 11 THE EFFECTS OF REPULPING VARIABLES ON DEINKING OF FLEXOGRAPHIC INKS Sylvia Ciampa, M.S. -
Measurement of the Degree of Sizing of Paper
DEPARTMENT OF COMMERCE . BUREAU OF STANDARDS George K. Burgess, Director TECHNOLOGIC PAPERS OF THE BUREAU OF STANDARDS, No. 326 [Part of Vol. 20] MEASUREMENT OF THE DEGREE OF SIZING OF PAPER BY F. T. CARSON, Assistant Physicist Bureau of Standards September 11, 1926 PRICE IS CENTS $1.25 Per Volume on Subscription Sold only by the Superintendent of Documents, Government Printing Office Washington, D. C. WASHINGTON GOVERNMENT PRINTING OFFICE 1926 T326 MEASUREMENT OF THE DEGREE OF SIZING OF PAPER By F. T. Carson ABSTRACT The attempt to obtain a satisfactory means of measuring the degree of sizing of paper or its resistance to permeation by aqueous liquids has resulted in the proposal of no less than 38 sizing tests. For the first time in a single publication these have been described, critically discussed, and the most important ones compared experimentally. Stress is laid on the essential difference in the capillary flow in the direction of the length of the fibers and in the direction normal to their length, and a recommendation made that degree of surface sizing and degree of internal sizing be recognized as separate properties. In general, the various tests are entirely contradictory in their results. This is found to be due largely to the effects of selective adsorption from solution and of an extraneous resistivity. Tests of rate of penetration of water are considered the most logical and the type most indicative of degree of internal sizing. Two methods of this type have been developed at the Bureau of Standards—the curl method and a new test using a dry indicator on one surface of the paper.