SHAPING CNC-CUT PLYWOOD STRUCTURES Design Principles for CNC-Milled Panel Wood Connections in a Safe Spanning Structure
Total Page:16
File Type:pdf, Size:1020Kb
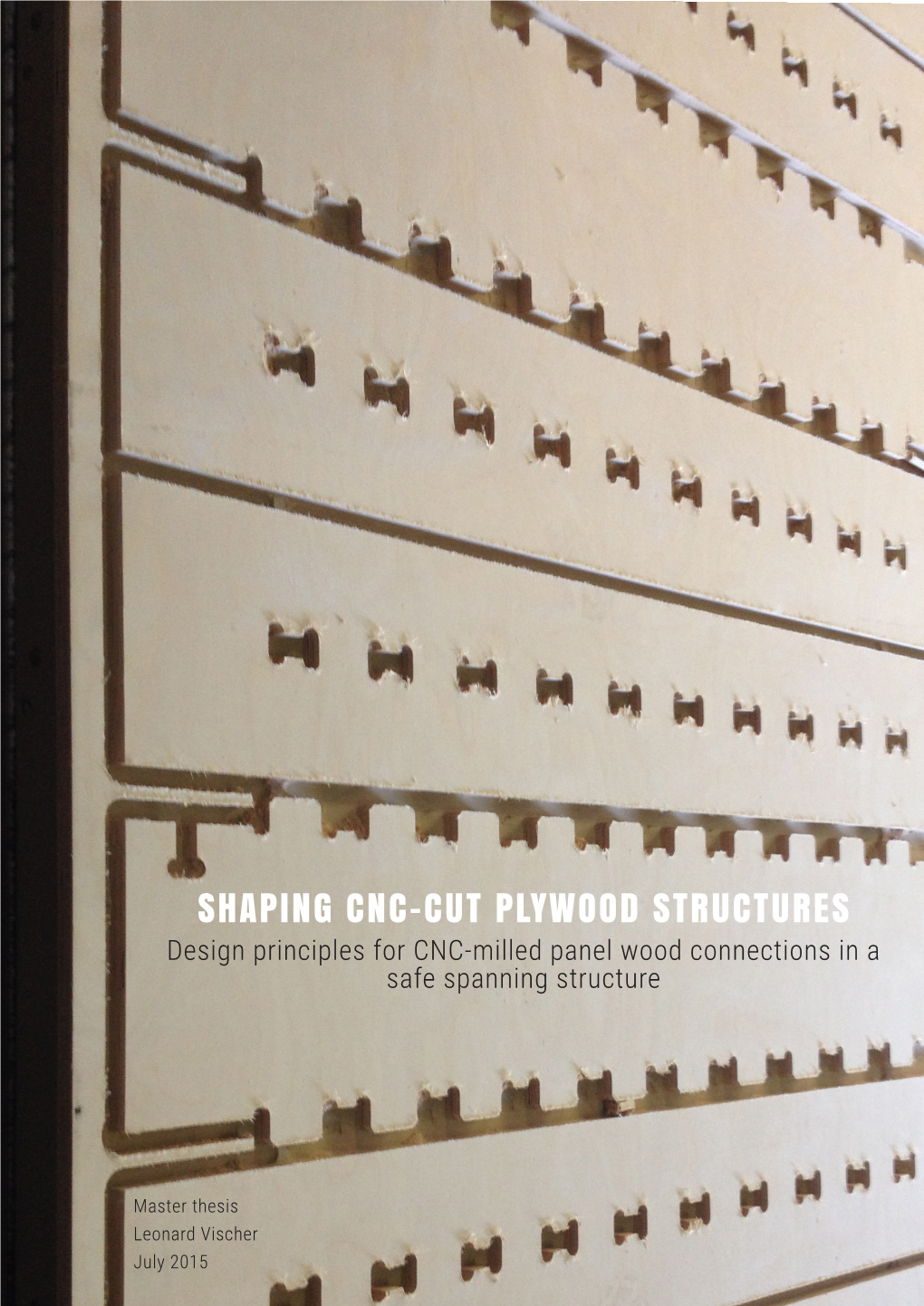
Load more
Recommended publications
-
In 2017, the Château of Chambord Is Replanting Its 18Th-Century French Formal Gardens
TABLE OF CONTENTS INTRODUCTION ................................................................................................................................ 3 I - HISTORY .......................................................................................................................................... 4 1 - The Château’s Surroundings in the 16th Century ........................................................................ 4 2 - The Major Projects of the 17th Century ........................................................................................ 4 3 - Completion of the Parterre in the 18th Century ........................................................................... 5 4 - The Steady Disappearance of the Garden .................................................................................. 7 II – SCIENTIFIC APPROACH ........................................................................................................... 8 1 - A Methodical and Scientific Investigation .................................................................................. 8 2 - Historical Research (2003–2014) .................................................................................................. 8 3 - Archaeological and Geophysical Surface Surveys (2013–2014) .................................................. 8 4 - Planned Archaeological Digs (2016) ............................................................................................ 9 III – COMPOSITION OF FRENCH FORMAL GARDENS ........................................................ -
Patching Old Floorboards
Patching Old Floorboards SPAB Technical Advice Note Philip Hughes BSc, MRICS (Chartered Building Surveyor) and SPAB Scholar The Society for the Protection of Ancient Buildings 37 Spital Square London E1 6DY 020 7377 1644 [email protected] www.spab.org.uk Contents An old floor of wide boards – scrubbed or polished for generations and uneven from wear – adds considerable richness to any room in an old building. A floor is one of the principal surfaces of a room, yet ancient boards are often badly abused. Bodged attempts to replace boards are common. Even when replacement is completed satisfactorily, the result will not always be visually acceptable. In addition, replacement of floors in their entirety often takes place unnecessarily. This Technical Advice Note aims to alleviate the problem by suggesting a number of methods by which old boards may be patched or repaired. 1 Introduction ....................... 3 2 Deterioration ....................... 3 3 Lifting floorboards ....................... 3 4 Undulations and gaps ....................... 5 5 Reducing unevenness ....................... 6 6 Repairing a split board ....................... 6 7 Repairing a broken edge ....................... 7 8 Strengthening a weak board ....................... 8 9 Splicing a broken end ....................... 8 10 Relaying old boards ....................... 8 11 Surface treatment ....................... 9 12 Conclusion ....................... 9 13 References ....................... 9 14 Other advice ....................... 9 Cover image: Warmth and richness of a well-repaired old floor. Photo: Philip Hughes 2 SPAB Patching Old Floorboards 1 Introduction 3 Lifting This Technical Advice Note explains common reasons why floorboards deteriorate (section 2) floorboards and a range of methods by which they can be repaired (sections 4 to 9). It also discusses It is extremely easy to cause serious damage techniques for successfully lifting floorboards, to floorboards by attempting to lift them – where it is necessary to take them up, and offers particularly when the board is decayed. -
Idaho's Monarch Butterfly Connection by Beth Waterbury, Wildlife Biologist, Idaho Department of Fish and Game, Salmon Region
Vol. 39 No. 1 March 2017 Newsletter of the Idaho Native Plant Society Promoting Interest in Idaho’s Native Flora Idaho's Monarch Butterfly Connection By Beth Waterbury, Wildlife Biologist, Idaho Department of Fish and Game, Salmon Region Few species spark people's wonder and pas- little was known about milkweed and breeding sion like the monarch butterfly. With its fiery- monarch distribution in the West. This was cer- orange and black pattern and large wingspan, the tainly the case for Idaho, where as recently as monarch is among the most recognized insects in 2014, only a handful of monarch and milkweed North America. Its life cycle is a complex marvel records existed for the entire state. involving a lengthy migration completed relay- style by several generations in a single year. Dur- Federal grant helps to leverage monarch ing their summer wanderings, female monarchs work in Idaho and Washington lay their eggs on the leaves of milkweeds—the sole Through a grant from the U.S. Fish and Wild- food source for their striking yellow, white, and life Service, Idaho Department of Fish and Game black-striped caterpillars. Milkweeds are the es- (IDFG), Washington Department of Fish and sential links of the chain that connect monarch Wildlife (WDFW), and the Xerces Society for In- breeding populations across North America. vertebrate Conservation partnered on a multi- Monarch butterflies have made their mark on faceted project to address monarch and milkweed Idaho as the official state insect. Idaho is one of 11 data gaps in Idaho and Washington. Starting in western states that contribute to the western mon- 2016, partners worked to compile monarch and arch population. -
Woodworking Glossary, a Comprehensive List of Woodworking Terms and Their Definitions That Will Help You Understand More About Woodworking
Welcome to the Woodworking Glossary, a comprehensive list of woodworking terms and their definitions that will help you understand more about woodworking. Each word has a complete definition, and several have links to other pages that further explain the term. Enjoy. Woodworking Glossary A | B | C | D | E | F | G | H | I | J | K | L | M | N | O | P | Q | R | S | T | U | V | W | X | Y | Z | #'s | A | A-Frame This is a common and strong building and construction shape where you place two side pieces in the orientation of the legs of a letter "A" shape, and then cross brace the middle. This is useful on project ends, and bases where strength is needed. Abrasive Abrasive is a term use to describe sandpaper typically. This is a material that grinds or abrades material, most commonly wood, to change the surface texture. Using Abrasive papers means using sandpaper in most cases, and you can use it on wood, or on a finish in between coats or for leveling. Absolute Humidity The absolute humidity of the air is a measurement of the amount of water that is in the air. This is without regard to the temperature, and is a measure of how much water vapor is being held in the surrounding air. Acetone Acetone is a solvent that you can use to clean parts, or remove grease. Acetone is useful for removing and cutting grease on a wooden bench top that has become contaminated with oil. Across the Grain When looking at the grain of a piece of wood, if you were to scratch the piece perpendicular to the direction of the grain, this would be an across the grain scratch. -
Download This Issue As
A A Wednesday, June 27, 2018 • Vol. 12 Issue 9 July 4th in Orinda! JULY 8 a.m. Haley’s Fun Run for a Reason Independent, locally 9 a.m. Book Sale 26,000 copies owned and operated! delivered biweekly to 10 a.m. Lamorinda homes & Best Hometown businesses 2018 Parade! 925-377-0977 www.lamorindaweekly.com 11:30 Party in the Park FREE Local newspaper delivered to Lafayette,Family fun Moraga for all ages! and Orinda Visit OrindaParade.com Presented by The Orinda Association since 1984 JULY 2018 A ConFire firefighter drops a lit sparkler in a nearby field. The vegetation was ablaze five seconds later. Photos Nick Marnell This happened in five seconds By Nick Marnell apt. David Woods dropped a lit sparkler to the ground If you try this at home, you will likely not be immedi- cause hundreds of fires, taking off the street firefighters who during a June 19 Contra Costa County Fire Protec- ately surrounded by professional emergency personnel. could answer other emergency calls. Laing recommends that Ction District training session and in five seconds, the “Sparklers burn at 1,200 to 2,000 degrees. They can very you enjoy the aerial firework displays licensed and regulated vegetation was completely ablaze. The exercise occurred in easily start fires, they are not safe and they are illegal,” said by the fire districts, like the Fourth of July fireworks show a confined, regulated space, with dozens of firefighters read- Capt. George Laing. put on by the town of Moraga. ily available. With the dry grasses in the area, illegal fireworks can “We do not need any more ignition sources,” Laing said. -
NPRC) VIP List, 2009
Description of document: National Archives National Personnel Records Center (NPRC) VIP list, 2009 Requested date: December 2007 Released date: March 2008 Posted date: 04-January-2010 Source of document: National Personnel Records Center Military Personnel Records 9700 Page Avenue St. Louis, MO 63132-5100 Note: NPRC staff has compiled a list of prominent persons whose military records files they hold. They call this their VIP Listing. You can ask for a copy of any of these files simply by submitting a Freedom of Information Act request to the address above. The governmentattic.org web site (“the site”) is noncommercial and free to the public. The site and materials made available on the site, such as this file, are for reference only. The governmentattic.org web site and its principals have made every effort to make this information as complete and as accurate as possible, however, there may be mistakes and omissions, both typographical and in content. The governmentattic.org web site and its principals shall have neither liability nor responsibility to any person or entity with respect to any loss or damage caused, or alleged to have been caused, directly or indirectly, by the information provided on the governmentattic.org web site or in this file. The public records published on the site were obtained from government agencies using proper legal channels. Each document is identified as to the source. Any concerns about the contents of the site should be directed to the agency originating the document in question. GovernmentAttic.org is not responsible for the contents of documents published on the website. -
Complete Instructions and Setup for Clincher Fence Machinetm and Smartfence
INCLUDES COLLECTION OF SIXTY, 16” long TEMPLATES and FULL SIZE PLANS FOR MAKING: • Box joints • Double-Double Box joints • Half-Blind Dovetails • Double Dovetails • Through & Double Through Dovetails • Jointech’s exclusive BoxtailsTM FULLY ILLUSTRATED WITH OVER • Plus 18 Scales for repetitive cutting 1 7 DETAILED ULL COLOR Cutting intervals range from /8” up to /8”. 200 F - DRAWINGS AND PHOTOS, PLUS NUMEROUS SHOP TIPS AND TECHNIQUES. Complete Instructions and Setup for MADE IN THE U.S.A. Manufactured by: TM ® Clincher Fence Machine and SmartFence . Jointech, Inc. SETUPS for CABINET MAKING OPERATIONS P.O. Box 790727 San Antonio, TX 78279 • Edge Jointing • Frames • Raised Panels Customer Svc : (210) 524-9104 Facsimile: (210) 377-1282 email:[email protected] Introduction CLINCHER FENCE MACHINE.....................................................................................2 Templates and scales Fence Machine Systems Warranty OPTIONAL ACCESSORIES.........................................................................................3 Setting Up SYSTEM SETUP and ASSEMBLY...............................................................................4 Mounting CLINCHER Mounting Fence Dust Collection Attachment Vertical Push Fixture assembly X-Y Stop Block operation Cutting Profile Inserts Cabinet Making EDGE JOINTING......... ................................................................................................6 Operations SHAPING OPERATIONS .............................................................................................7 -
MONARCH Summary Brochure.Art 31/10/01 9:45 Am Page 1
MONARCH Summary brochure.art 31/10/01 9:45 am Page 1 All photographs used by permission Climate Change and Paul Sterry, Nature Photographers Ltd (NPL) E Thompson (NPL) front cover: rocky shore, page 11: azure damselfly page 6: large heath butterfly, Nature Conservation page 8: trailing azalea, British Trust for Ornithology page 9: spanish catchfly, page 1: red-throated diver, page 12: capercaillie, page 7: dunlin, in Britain and Ireland page 14: salt marsh, sea purslane, page 12: nuthatch, page 17: mountain ringlet page 15: oystercatcher MONARCH - Modelling Natural Resource Andrew Cleave (NPL) English Nature front cover: mudflats, page 8: globe flower, Responses to Climate Change page 10: peat bog, page 9: beech trees, page 15: sabellaria alveolata page 11: female natterjack toad S.Bisserot (NPL) Duchas, The Heritage Service, Ireland page 13: stalagmites page 13: Burren national park Sverre Stølen, Norway page 9: Norwegian mugwort The UK Climate Impacts Programme (UKCIP) UKCIP was established by the UK Government in 1997, with the aim of providing a framework for the integrated assessment of climate change impacts. Researchers for MONARCH used the UKCIP98 climate scenarios and data sets, as well as the statistical techniques and several computer models. They also considered their findings in the light of other research undertaken under the UKCIP umbrella, particularly the DEFRA Conservation Policy Review and regional scoping studies. These earlier studies were based on expert opinion and literature reviews, but the modelling in MONARCH -
The Effects of the Butterfly Joints on Failure Loads and Fatigue Performance of Composite Structures
©Freund Publishing House Ltd. Science and Engineering of Composite Materials 17, 199-212 (2010) The Effects of the Butterfly Joints on Failure Loads and Fatigue Performance of Composite Structures G rkan Altan*, Muzaffer Τορφυ, Hasan Qalhoglu Faculty of Engineering, Department of Mechanical Engineering, Pamnkkale University, Kinikli 20070 Denizli, Turkey ABSTRACT The present study was designed to examine experimentally the effects of butterfly fitting clearances and different adhesives on the load carrying abilities of the composite structures joined via a butterfly-shaped joining component and the fatigue performance of the specimens joined by the best joint style obtained. Experiment specimens and butterfly- shaped locking components were cut from a composite plate by means of water jet. Fatigue experiments were conducted at the constant load ratio and at different maximum fatigue loads. To compare the fatigue performance, the fatigue experiments of the butt joints were also carried out. According to the experiment results obtained, it was determined that fatigue strengths of adhesively-bonded butterfly joints have a longer life span than those of the bonded butt joints under the same circumstances. The present study has made it possible that with the use of butterfly joining component, the earliest damage should occur on the butterfly and should have a longer service life with the repairs of the butterfly joining component. Keywords: Butterfly joint; Composite; Fatigue life; Failure load. 1. INTRODUCTION Composite materials are especially preferred in the aviation, navigation and automobile industries for their lightness. Large structures made from composite materials are generally used under static and dynamic loading conditions. Each large composite structure consists of one or more joints because of their production and design circumstances. -
Table Top and Base Collection
Table Top and Base Collection Laminate and Veneer Solid Wood Specialty Tables Bases 877.747.7638 | softtouchfurniture.com WHAT MAKES US DIFFERENT With a nod to the past, an eye on the future, and a clear focus on our customer’s present needs, Soft Touch Furniture has carved out a distinct space in the restaurant and hospitality furniture industry. In business for more than 40 years, we have a long history of innovative design and quality workmanship that have delighted both customers and their patrons. Our job is to make you look good, and it’s one we take very seriously. WE ARE THE MANUFACTURER We’re a complete commercial furniture manufacturer capable of filling just about any need you may have. We work with all types of clients, from designers, architects, national chains and single owner operators of any size, on Table of Content: any size order. Laminate and Veneer 4–13 Metal & Powder Coating 29 Wood Styles & Species 14–19 Seating Capacity 30 You can get exactly what you want. We have a large Specialty Tables 20–23 Table Heights 31 stock, ready for your choice of color, fabrics, and finishes. Live Edge Tables 24–25 Table Bases 32–37 But if you want custom, we’ll work with you and design Drop Leaf Tables 26–27 Table Options 38–39 something that fits your space. We are the manufacturer, Technology 28 and because of that, there are no middlemen. We offer American-made quality, in the styles and finishes you want, at competitive prices. Delivery and installation are never a problem, as we handle those as well. -
Interactive Construction
Interactive Construction: Interactive Fabrication of Functional Mechanical Devices Stefanie Mueller, Pedro Lopes, and Patrick Baudisch Hasso Plattner Institute, Potsdam, Germany {stefanie..mueller, pedro..lopes, patrick. baudisch}@hpi.u.ni-potsdam.de ABSTRACT Personal fabrication tools, such as laser cutters and 3D printers allow users to create precise objects quickly. How- ever, working through a CAD system removes users from the workpiece. Recent interactive fabrication tools reintro- duce this directness, but at the expense of precision. In this paper, we introduce constructable, an interactive drafting table that produces precise physical output in every step. Users interact by drafting directly on the workpiece using a hand-held laser pointer. The system tracks the pointer, beautifies its path, and implements its effect by cutting the workpiece using a fast high-powered laser cutter. Constructable achieves precision through tool-specific constraints, user-defined sketch lines, and by using the laser cutter itself for all visual feedback, rather than using a screen or projection. We demonstrate how Constructable allows creating simple but functional devices, including a simple gearbox, that cannot be created with traditional Figure 1: (a) Constructable users interact by drafting interactive fabrication tools. directly on the workpiece with hand-held lasers. (b) Here the user sketches a finger joint across two Author Keywords: interactive fabrication; laser cutting; objects (c) The system responds by cutting the desired rapid prototyping; sketching; construction; mechanics. joint using the cutting laser. (d) Constructable allows ACM Classification Keywords: H5.2 [Information inter- creating precise & functional mechanical objects, faces and presentation]: User Interfaces. - Graphical user such as this simple motorized vehicle. -
Kentucky Unwanted Plants
Chapter 6 A Brief Guide to Kentucky’s Non-Native, Invasive Species, Common Weeds, and Other Unwanted Plants A publication of the Louisville Water Company Wellhead Protection Plan, Phase III Source Reduction Grant # X9-96479407-0 Chapter 6 A Brief Guide to Kentucky’s Non-native, Invasive Species, Common Weeds and Other Unwanted Plants What is an invasive exotic plant? A plant is considered exotic, (alien, foreign, non- indigenous, non-native), when it has been introduced by humans to a location outside its native or natural range. Most invasive, exotic plants have escaped cultivation or have spread from its origin and have become a problem or a potential problem in natural biological communities. For example, black locust, a tree that is native to the southern Appalachian region and portions of Indiana, Illinois, and Missouri, was planted throughout the U.S. for living fences, erosion control, and other uses for many years. Black locust is considered exotic outside its natural native range because it got to these places Kudzu is an invasive exotic plant that has spread by human introduction rather than by natural from Japan and China to become a large problem in dispersion. It has become invasive, displacing native much of the US. Local, state, and the federal species and adversely impacting ecosystems and governments spend millions of dollars per year to several endangered native bird species that depend on control the spread of kudzu. Even yearly control other plants for food, as well as several endangered may not be enough to successfully remove kudzu. Seeds can remain dormant in the plant species.