The Joule-Thomson Process in Cryogenic Refrigeration Systems
Total Page:16
File Type:pdf, Size:1020Kb
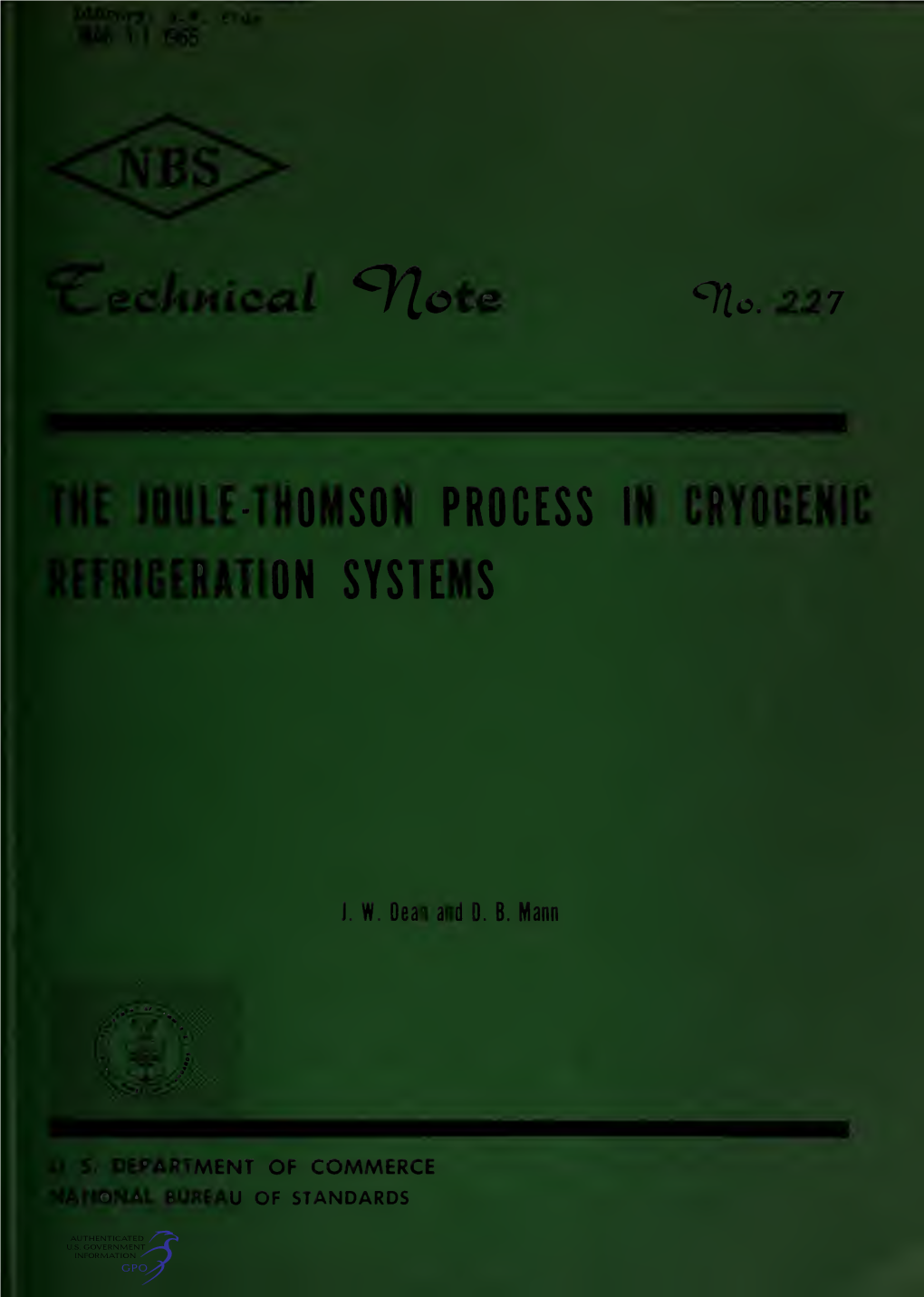
Load more
Recommended publications
-
Joule-Thomson Expansion of Charged Ads Black Holes
Joule-Thomson Expansion of Charged AdS Black Holes Ozg¨ur¨ Okc¨u¨ ∗ and Ekrem Aydınery Department of Physics, Faculty of Science, Istanbul_ University, Istanbul,_ 34134, Turkey (Dated: January 24, 2017) In this paper, we study Joule-Thomson effects for charged AdS black holes. We obtain inversion temperatures and curves. We investigate similarities and differences between van der Waals fluids and charged AdS black holes for the expansion. We obtain isenthalpic curves for both systems in T − P plane and determine the cooling-heating regions. I. INTRODUCTION Variable cosmological constant notion has some nice features such as phase transition, heat cycles and com- It is well known that black holes as thermodynamic pressibility of black holes [41]. Applicabilities of these systems have many interesting consequences. It sets deep thermodynamic phenomena to black holes encourage us and fundamental connections between the laws of clas- to consider Joule-Thomson expansion of charged AdS sical general relativity, thermodynamics, and quantum black holes. In this letter, we study the Joule-Thompson mechanics. Since it has a key feature to understand expansion for chraged AdS black holes. We find sim- quantum gravity, much attention has been paid to the ilarities and differences with van der Waals fluids. In topic. The properties of black hole thermodynamics have Joule-Thomson expansion, gas at a high pressure passes been investigated since the first studies of Bekenstein and through a porous plug to a section with a low pressure Hawking [1{6]. When Hawking discovered that black and during the expansion enthalpy is constant. With holes radiate, black holes are considered as thermody- the Joule-Thomson expansion, one can consider heating- namic systems. -
Chapter 3 Non-Ideal Gases
Chapter 3 Non-ideal Gases This chapter is devoted to considering systems where the interactions be- tween particles can no longer be ignored. We note that in the previous chapter we did indeed consider, albeit briefly, the effects of interactions in fermion and in boson gases. This chapter is concerned more with a system- atic treatment of interatomic interactions. Here the quantum aspect is but a complication and most of the discussions will thus take place within the context of a classical description. 3.1 Statistical Mechanics of Interacting Par- ticles 3.1.1 The partition function We are now considering gases where the interactions between the particles cannot be ignored. Our starting point is that everything can be found from the partition function. We will work, initially, in the classical framework where the energy function of the system is p2 H (p , q ) = i + U (q , q ) . (3.1.1) i i 2m i j i i<j X X Because of the interaction term U (qi, qj) the partition function can no longer be factorised into the product of single-particle partition functions. The many-body partition function is 1 p2/2m+ U(q ,q ) kT 3N 3N Z = e− ( i i i<j i j )/ d p d q (3.1.2) N!h3N Z P P 133 134 CHAPTER 3. NON-IDEAL GASES where the factor 1/N! is used to account for the particles being indistinguish- able. While the partition function cannot be factorised into the product of single-particle partition functions, we can factor out the partition function for the non-interacting case since the energy is a sum of a momentum-dependent term (kinetic energy) and a coordinate-dependent term (potential energy). -
Thermodynamics and Statistical Mechanics
Thermodynamics and Statistical Mechanics Richard Fitzpatrick Professor of Physics The University of Texas at Austin Contents 1 Introduction 7 1.1 IntendedAudience.................................. 7 1.2 MajorSources.................................... 7 1.3 Why Study Thermodynamics? ........................... 7 1.4 AtomicTheoryofMatter.............................. 7 1.5 What is Thermodynamics? . ........................... 8 1.6 NeedforStatisticalApproach............................ 8 1.7 MicroscopicandMacroscopicSystems....................... 10 1.8 Classical and Statistical Thermodynamics . .................... 10 1.9 ClassicalandQuantumApproaches......................... 11 2 Probability Theory 13 2.1 Introduction . .................................. 13 2.2 What is Probability? . ........................... 13 2.3 Combining Probabilities . ........................... 13 2.4 Two-StateSystem.................................. 15 2.5 CombinatorialAnalysis............................... 16 2.6 Binomial Probability Distribution . .................... 17 2.7 Mean,Variance,andStandardDeviation...................... 18 2.8 Application to Binomial Probability Distribution . ................ 19 2.9 Gaussian Probability Distribution . .................... 22 2.10 CentralLimitTheorem............................... 25 Exercises ....................................... 26 3 Statistical Mechanics 29 3.1 Introduction . .................................. 29 3.2 SpecificationofStateofMany-ParticleSystem................... 29 2 CONTENTS 3.3 Principle -
An Important Practical Question Is What Happens When a Gas Is Expanded Into Vacuum Or a Very Low Pressure (Against “Zero External Pressure”)
An important practical question is what happens when a gas is expanded into vacuum or a very low pressure (against “zero external pressure”). We saw already that W=0. And in a fundamental sense, it helps us to further illustrate the (usefulness of the) concept of enthalpy. Does the T decrease, as is typical when it is expanded adiabatically? Should it, if no work is done? (Remember that the adiabatic expansion curve on the P-v diagram is steeper than that of isothermal expansion!) Initial experiments (done by Joule in the 19th century) showed that, when the gas can be considered ideal, heat is neither evolved nor absorbed. Thus both heat and work are zero, which means that the internal energy remains constant: ∂U =0 ∂V T In fact, this condition is a complementary definition of an ideal gas, because Joule and Thomson -- two of the leading 'fathers' of thermodynamics, the latter immortalized as lord Kelvin -- subsequently showed that this is not true in general (for non-ideal or real gases). In fact, the ability to predict the so called Joule-Thomson inversion temperature (see relevant figures in the textbook) is often used as a litmus test for an equation of state. So the concept and the quantification of the Joule-Thomson coefficient is an essential topic in an introductory thermo course: ∂T ≡ μ ∂P H It turns out that the assumption Q=0 is more reasonable than the assumption W=0, because of the need to overcome the attractive (or repulsive!) forces between molecules. In other words, no ‘external’ work is done (by compressing the surroundings), but some ‘internal’ work is done.. -
Intro-Propulsion-Lect-19
19 1 Lect-19 In this lecture ... • Helmholtz and Gibb’s functions • Legendre transformations • Thermodynamic potentials • The Maxwell relations • The ideal gas equation of state • Compressibility factor • Other equations of state • Joule-Thomson coefficient 2 Prof. Bhaskar Roy, Prof. A M Pradeep, Department of Aerospace, IIT Bombay Lect-19 Helmholtz and Gibbs functions • We have already discussed about a combination property, enthalpy, h. • We now introduce two new combination properties, Helmholtz function, a and the Gibbs function, g. • Helmholtz function, a: indicates the maximum work that can be obtained from a system. It is expressed as: a = u – Ts 3 Prof. Bhaskar Roy, Prof. A M Pradeep, Department of Aerospace, IIT Bombay Lect-19 Helmholtz and Gibbs functions • It can be seen that this is less than the internal energy, u, and the product Ts is a measure of the unavailable energy. • Gibbs function, g: indicates the maximum useful work that can be obtained from a system. It is expressed as: g = h – Ts • This is less than the enthalpy. 4 Prof. Bhaskar Roy, Prof. A M Pradeep, Department of Aerospace, IIT Bombay Lect-19 Helmholtz and Gibbs functions • Two of the Gibbs equations that were derived earlier (Tds relations) are: du = Tds – Pdv dh = Tds + vdP • The other two Gibbs equations are: a = u – Ts g = h – Ts • Differentiating, da = du – Tds – sdT dg = dh – Tds – sdT 5 Prof. Bhaskar Roy, Prof. A M Pradeep, Department of Aerospace, IIT Bombay Lect-19 Legendre transformations • A simple compressible system is characterized completely by its energy, u (or entropy, s) and volume, v: u = u(s,v) ⇒ du = Tds − Pdv ∂u ∂u such that T = P = ∂s v ∂v s Alternatively, in the entropy representation, s = s(u,v) ⇒ Tds = du + Pdv 1 ∂s P ∂s such that = = T ∂u v T ∂v u 6 Prof. -
Joule-Thomson Inversion Curves and Related Coefficients for Several Simple Fluids
https://ntrs.nasa.gov/search.jsp?R=19720020315 2020-03-23T11:57:09+00:00Z I NASA TECHNICAL NOTE ni 0 h I 0 a0 Y -- = LOAN COPY: REhiw z AFWL (DOE= c i KIRTLAND AFE~ZS 4 - 2 c/) L 4 - a JOULE-THOMSON INVERSION CURVES AND RELATED COEFFICIENTS FOR SEVERAL SIMPLE FLUIDS by Robert C. Hendricks, Ildiko C, Peller, dnd Anne K. Baron Lewis Research Center Cleveland, Ohio 44135 .. NATIONAL AERONAUTICS AND SPACE ADMINISTRATION WASHINGTON, D. C. JULY 1972 - -. 1. Report No. 2. Government Accession No. 3. Recipient's Catalog No. NASA TN D -68 07 I 4. Title and Subtitle 5. Report Date JOULE-THOMSON INVERSION CURVES AND RELATED July 1972 7. Author(s) 8. Performing Organization Report No. Robert C. Hendricks, lldiko C. Peller, and Anne K. Baron E- 6786 ~~ -10. Work Unit No. 9. Performing Organization Name and Address 113-31 Lewis Research Center 11. Contract or Grant No. National Aeronautics and Space Administration Cleveland, Ohio 44135 13. Type of Report and Period Covered '2. Sponsoring Agency Name and Address ITechnical Note National Aeronautics and Space Administration 14. Sponsoring Agency Code Washington, D. C. 20546 I 5. Supplementary Notes -~ . .. 6. Abstract The equations of state (PVT relations) for methane, oxygen, argon, carbon dioxide, carbon monoxide, neon, hydrogen, and helium were used to establish Joule-Thomson inversion curves for each fluid. The principle of corresponding states was applied to the inversion curves, and a generalized inversion curve for fluids with small acentric factors was developed. The quan tum fluids (neon, hydrogen, and helium) were excluded from the generalization, but available data for the fluids xenon and krypton were included. -
Statistical Physics Problem Set 8: Thermodynamics of Real Gases
Statistical Physics xford hysics Second year physics course Dr A. A. Schekochihin and Prof. A. Boothroyd (with thanks to Prof. S. J. Blundell) Problem Set 8: Thermodynamics of Real Gases and Phase Equilibria ++ Statistical Mechanics Revision Questions (vacation work) Some useful constants −23 −1 Boltzmann's constant kB 1:3807 × 10 JK Stefan{Boltzmann constant σ 5:67 × 10−8 Wm−2K−4 23 −1 Avogadro's number NA 6:022 × 10 mol Standard molar volume 22:414 × 10−3 m3 mol−1 Molar gas constant R 8:315 J mol−1 K−1 1 pascal (Pa) 1 N m−2 1 standard atmosphere 1:0132 × 105 Pa (N m−2) 1 bar (= 1000 mbar) 105 N m−2 PROBLEM SET 8: Real Gases, Expansions and Phase Equilibria Problem set 8 can be covered in 1 tutorial. The relevant material will be done in lectures by the end of week 8 of Hilary Term. Starred questions (*) are harder. Revision questions are designed to build on the understanding of Statistical Mechanics developed in the two previous problem sets. Real gases 8.1 A gas obeys the equation p(V −b) = RT and has CV independent of temperature. Show that (a) the internal energy is a function of temperature only, (b) the ratio γ = Cp=CV is independent of temperature and pressure, (c) the equation of an adiabatic change has the form p(V − b)γ = constant. 8.2 Dieterici's equation of state for 1 mole is p(V − b) = RT e−a=RT V : (1) (a) Show that the critical point is specified by 2 2 Tc = a=4Rb; Vc = 2b; pc = a=4e b : (b) Show that equation (1) obeys a law of corresponding states, i.e. -
Prediction of Differential Joule-Thomson Inversion Curves for Cryogens Using Equations of State
PREDICTION OF DIFFERENTIAL JOULE-THOMSON INVERSION CURVES FOR CRYOGENS USING EQUATIONS OF STATE Nupura Ravishankar1, P.M. Ardhapurkar2, M.D. Atrey3 1Sardar Vallabhbhai National Institute of Technology, Surat – 395 007 2S.S.G.M. College of Engineering, Shegaon – 444 203 3Indian Institute of Technology Bombay, Mumbai – 400 076 In many cryogenic applications, Joule–Thomson (J–T) effect is used to produce low temperatures. The isenthalpic expansion of gas results in lowering of temperature only if the initial temperature of the working fluid is below its characteristic temperature, called the inversion temperature. Inversion curves are helpful in studying the inversion temperatures. The prediction of inversion curves solely depends on the equation of state (EOS) for the working fluid. In the present work, various EOS are explored in order to predict the Joule–Thomson differential inversion curve for various commonly used cryogens viz. nitrogen, argon, carbon dioxide, helium, hydrogen and neon. The widely accepted EOS such as Van der Waals, Redlich–Kwong and Peng–Robinson EOS are used for this purpose. Key words: Inversion curve, Joule Thomson Effect, Van der Waal, Redlich Kwong, Peng Robinson INTRODUCTION Joule–Thomson coefficient, µJT and is given as, The Joule-Thomson (J-T) effect has been widely investigated because of its 흏푻 흁푱푻 = ( ) (1) importance for theoretical and practical 흏푷 푯 purposes. It has many cryogenic applications and is widely used in gas The locus of points for which μJT =0 is liquefaction. The effect describes called the differential inversion curve. The the temperature change of a gas or liquid inversion curve divides the p-T plane into when it is forced through a valve or porous two zones as shown in Figure 1. -
Joule-Thomson Inversion Curves and Related Coefficients for Several Simple Fluids
I NASA TECHNICAL NOTE ni 0 h I 0 a0 Y -- = LOAN COPY: REhiw z AFWL (DOE= c i KIRTLAND AFE~ZS 4 - 2 c/) L 4 - a JOULE-THOMSON INVERSION CURVES AND RELATED COEFFICIENTS FOR SEVERAL SIMPLE FLUIDS by Robert C. Hendricks, Ildiko C, Peller, dnd Anne K. Baron Lewis Research Center Cleveland, Ohio 44135 .. NATIONAL AERONAUTICS AND SPACE ADMINISTRATION WASHINGTON, D. C. JULY 1972 - -. 1. Report No. 2. Government Accession No. 3. Recipient's Catalog No. NASA TN D -68 07 I 4. Title and Subtitle 5. Report Date JOULE-THOMSON INVERSION CURVES AND RELATED July 1972 7. Author(s) 8. Performing Organization Report No. Robert C. Hendricks, lldiko C. Peller, and Anne K. Baron E- 6786 ~~ -10. Work Unit No. 9. Performing Organization Name and Address 113-31 Lewis Research Center 11. Contract or Grant No. National Aeronautics and Space Administration Cleveland, Ohio 44135 13. Type of Report and Period Covered '2. Sponsoring Agency Name and Address ITechnical Note National Aeronautics and Space Administration 14. Sponsoring Agency Code Washington, D. C. 20546 I 5. Supplementary Notes -~ . .. 6. Abstract The equations of state (PVT relations) for methane, oxygen, argon, carbon dioxide, carbon monoxide, neon, hydrogen, and helium were used to establish Joule-Thomson inversion curves for each fluid. The principle of corresponding states was applied to the inversion curves, and a generalized inversion curve for fluids with small acentric factors was developed. The quan tum fluids (neon, hydrogen, and helium) were excluded from the generalization, but available data for the fluids xenon and krypton were included. The critical isenthalpic Joule-Thomson coefficient pc was determined; and a simplified approximation pc 3 Tc/6Pc was found adequate, where Tc and Pc are the temperature and pressure at the thermodynamic critical point. -
Physical Chemistry- III (Classical Thermodynamics, Non-Equilibrium Thermodynamics, Surface Chemistry, Fast Kinetics) Module No and Title 5, Joule Thomson Effect
Subject Chemistry Paper No and Title 10, Physical Chemistry- III (Classical Thermodynamics, Non-Equilibrium Thermodynamics, Surface chemistry, Fast kinetics) Module No and Title 5, Joule Thomson effect Module Tag CHE_P10_M5 CHEMISTRY Paper No. 10: Physical Chemistry- III (Classical Thermodynamics, Non-Equilibrium Thermodynamics, Surface chemistry, Fast kinetics) Module No. 5: Joule Thomson effect TABLE OF CONTENTS 1. Learning Outcomes 2. Introduction 3. Joule-Thomson effect 4. Joule Thomson coefficient 4.1 Joule Thomson coefficient for an ideal gas 4.2 Joule Thomson coefficient for a real gas 5. Derivation of Joule Thomson coefficient and Inversion temperature 6. Summary CHEMISTRY Paper No. 10: Physical Chemistry- III (Classical Thermodynamics, Non-Equilibrium Thermodynamics, Surface chemistry, Fast kinetics) Module No. 5: Joule Thomson effect 1. Learning Outcomes After studying this module you shall be able to: Know about Throttling process Learn why Joule Thomson effect is known as isenthalpic process Differentiate between Joule Thomson coefficient of an ideal gas and Joule Thomson coefficient of real gas. Derive Joule Thomson coefficient 2. Introduction In thermodynamics, the effect called Joule Thomson effect was discovered in 1852. This effect was named after two physicists James Prescott Joule (1818-1889) and William Thomson (1824-1907). This effect describes the change in temperature of a real gas or liquid when it is forced to pass through porous plug or valve while it is kept insulated so that exchange of heat with the environment is not possible. This process is called throttling process or Joule Thomson effect. This effect is mainly used in thermal machines such as refrigerators, heat pumps and air conditioners. -
Joule-Thomson Inversion Curves Calculation by Using Equation of State
Asian Journal of Chemistry; Vol. 24, No. 2 (2012), 533-537 Joule-Thomson Inversion Curves Calculation by Using Equation of State 1,* 2 BEHZAD HAGHIGHI and MOHAMMAD REZA BOZORGMEHR 1Thermophysical Properties Research Laboratory, Department of Chemistry, Faculty of Science, Birjand University, 97175-615, Birjand, Iran 2Department of Chemistry, Faculty of Science, Mashhad Branch, Islamic Azad University of Mashhad, Mashhad, Iran *Corresponding author: E-mail: haghighi.behzad@gmail. com; behzadhaghighi_chem@yahoo. com (Received: 14 January 2011; Accepted: 3 October 2011) AJC-10475 Since the prediction of the Joule-Thomson inversion curve is known as a sever test of the equations of state (EoS). Some cubic equations of state (CEoS) can eventually have inadequate prediction for checking their ability to calculate the Joule-Thomson inversion curve. In this paper the Joule-Thomson inversion curve has been used to test the predictive capabilities of some recent equations of state. This enables us to judge the accuracy of the results obtained from different equations of state. These five equations of state are: Wang- Gmehling (WG) equations of state, modified Peng-Robinson by Twu-Coon-Cunningham (PR-TCC) equations of state, Riazi-Mansoori (RM) equations of state, Geana equations of state and modified Peng- Robinson-Stryjek-Vera proposed by Samir I. Abu-Eishah (PRSV2) equations of state. All of these equations of state are modified van der Waals (vdW) equations of state recommended in the literature for estimating volumetric properties of relevant compounds. As a corollary to the present study, we have perceived that the investigated equations of state give good prediction of the low-temperature branch of the inversion curve, except for Riazi-Mansoori and Geana equations of state. -
Liquefaction of Helium
REFRIGERATION U. Wagner CERN, Geneva, Switzerland Abstract This introduction to cryogenic refrigeration is written in the frame of the CERN Accelerator School (CAS) Course on Superconductivity and Cryogenics. It consequently concerns refrigeration for cooling of superconductive devices with emphasis of liquid helium refrigeration. Following a general reminder of the thermodynamics involved, i.e. principally the first and second laws, the different thermodynamic cycles used to produce low temperatures are presented. Refrigerators working according to the different cycles are explained starting with the low capacity range covered by cryocoolers and then concentrating on Claude-cycle refrigerators. The different thermodynamic and technological elements of a Claude-cycle refrigerator are discussed and an example for a large refrigerator used in an accelerator equipped with superconducting magnets is presented. 1. INTRODUCTION The cryogenic temperature range has been defined as from -150 ˚C (-123 K) down to absolute zero (-273 ˚C or 0 K), the temperature at which molecular motion comes as close as theoretically possible to ceasing completely [1]. The application of cryogenics can roughly be separated into five major domains: i) Liquefaction and separation of gases ii) Storage and transport of gases iii) Altering material and fluid properties by reduced temperature iv) Biological and medical applications v) Superconductivity With the exception of the quest to get closer and closer to the absolute zero, in all the cases listed above cryogenics is a utility enabling the desired application or function. Since the first liquefaction of helium by Heike Kammerlingh Onnes in 1908, cryogenics has evolved in an engineering science combining different technologies in a "best compromise" to achieve a given goal.