Fuel Saving by Gradual Climb Procedure
Total Page:16
File Type:pdf, Size:1020Kb
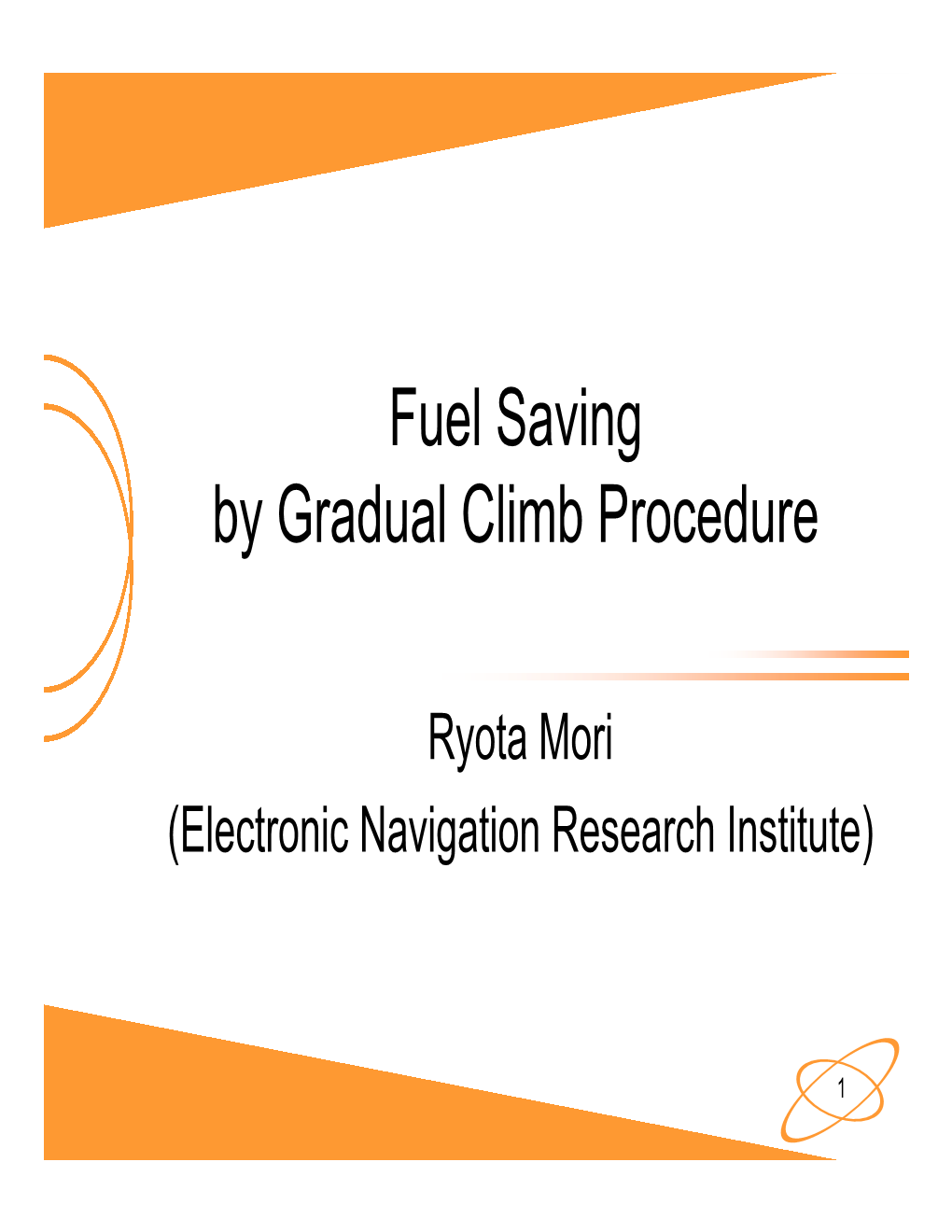
Load more
Recommended publications
-
CRUISE FLIGHT OPTIMIZATION of a COMMERCIAL AIRCRAFT with WINDS a Thesis Presented To
CRUISE FLIGHT OPTIMIZATION OF A COMMERCIAL AIRCRAFT WITH WINDS _______________________________________ A Thesis presented to the Faculty of the Graduate School at the University of Missouri-Columbia _______________________________________________________ In Partial Fulfillment of the Requirements for the Degree Master of Science _____________________________________________________ by STEPHEN ANSBERRY Dr. Craig Kluever, Thesis Supervisor MAY 2015 The undersigned, appointed by the dean of the Graduate School, have examined the thesis entitled CRUISE FLIGHT OPTMIZATION OF A COMMERCIAL AIRCRAFT WITH WINDS presented by Stephen Ansberry, a candidate for the degree of Master of Science, and hereby certify that, in their opinion, it is worthy of acceptance. Professor Craig Kluever Professor Roger Fales Professor Carmen Chicone ACKNOWLEDGEMENTS I would like to thank Dr. Kluever for his help and guidance through this thesis. I would like to thank my other panel professors, Dr. Chicone and Dr. Fales for their support. I would also like to thank Steve Nagel for his assistance with the engine theory and Tyler Shinn for his assistance with the computer program. ii TABLE OF CONTENTS ACKNOWLEDGEMENTS………………………………...………………………………………………ii LIST OF FIGURES………………………………………………………………………………………..iv LIST OF TABLES…………………………………………………………………………………….……v SYMBOLS....................................................................................................................................................vi ABSTRACT……………………………………………………………………………………………...viii 1. INTRODUCTION.....................................................................................................................................1 -
Predictability of Top of Descent Location for Operational Idle-Thrust Descents
Predictability of Top of Descent Location for Operational Idle-thrust Descents Laurel L. Stell∗ NASA Ames Research Center, Moffett Field, CA 94035 To enable arriving aircraft to fly optimized descents computed by the flight management system (FMS) in congested airspace, ground automation must accurately predict descent trajectories. To support development of the trajectory predictor and its uncertainty mod- els, commercial flights executed idle-thrust descents at a specified descent speed, and the recorded data included the specified descent speed profile, aircraft weight, and the winds entered into the FMS as well as the radar data. The FMS computed the intended descent path assuming idle thrust after top of descent (TOD), and the controllers and pilots then endeavored to allow the FMS to fly the descent to the meter fix with minimal human intervention. The horizontal flight path, cruise and meter fix altitudes, and actual TOD location were extracted from the radar data. Using approximately 70 descents each in Boeing 757 and Airbus 319/320 aircraft, multiple regression estimated TOD location as a linear function of the available predictive factors. The cruise and meter fix altitudes, descent speed, and wind clearly improve goodness of fit. The aircraft weight improves fit for the Airbus descents but not for the B757. Except for a few statistical outliers, the residuals have absolute value less than 5 nmi. Thus, these predictive factors adequately explain the TOD location, which indicates the data do not include excessive noise. Nomenclature b Least -
Prediction of Top of Descent Location for Idle-Thrust Descents
Ninth USA/Europe Air Traffic Management Research and Development Seminar (ATM2011) Prediction of Top of Descent Location for Idle-thrust Descents Laurel Stell Aviation Systems Division NASA Ames Research Center Moffett Field, CA, USA [email protected] Abstract—To enable arriving aircraft to fly optimized descents enabling continuous descents is being pursued by several re- computed by the flight management system (FMS) in congested search groups. Most of the previous research has focused on airspace, ground automation must accurately predict descent tra- prediction of arrival time at a waypoint. While this helps with jectories. Development and assessment of the trajectory predictor lateral separation, accurate prediction of the vertical profile is and the concept of operations requires models of the prediction also essential to ensure vertical separation from aircraft at dif- error due to various error sources. Polynomial approximations ferent altitudes, including crossing traffic. In fact, error in pre- of the along-track distance of the top of descent (TOD) from the diction of the vertical profile is likely to have more impact than meter fix are given in terms of the inputs to the equations of mo- tion. Polynomials with three different levels of complexity are pre- along-track prediction error on procedures and data exchange sented, with the simplest being linear. These approximations were necessary to enable more fuel-efficient descents in congested obtained by analyzing output from one predictor. While this pre- airspace. Only the TOD location is analyzed in this paper, dictor’s thrust and drag models do not seem to agree well with which is the first step in understanding the entire vertical pro- those used by the FMS, both laboratory and operational data us- file. -
Cessna Model 150M Performance- Cessna Specifications Model 150M Performance - Specifications
PILOT'S OPERATING HANDBOOK ssna 1977 150 Commuter CESSNA MODEL 150M PERFORMANCE- CESSNA SPECIFICATIONS MODEL 150M PERFORMANCE - SPECIFICATIONS SPEED: Maximum at Sea Level 109 KNOTS Cruise, 75% Power at 7000 Ft 106 KNOTS CRUISE: Recommended Lean Mixture with fuel allowance for engine start, taxi, takeoff, climb and 45 minutes reserve at 45% power. 75% Power at 7000 Ft Range 340 NM 22.5 Gallons Usable Fuel Time 3.3 HRS 75% Power at 7000 Ft Range 580 NM 35 Gallons Usable Fuel Time 5. 5 HRS Maximum Range at 10,000 Ft Range 420 NM 22. 5 Gallons Usable Fuel Time 4.9 HRS Maximum Range at 10,000 Ft Range 735 NM 35 Gallons Usable Fuel Time 8. 5 HRS RATE OF CLIMB AT SEA LEVEL 670 FPM SERVICE CEILING 14, 000 FT TAKEOFF PERFORMANCE: Ground Roll 735 FT Total Distance Over 50-Ft Obstacle 1385 FT LANDING PERFORMANCE: Ground Roll 445 FT Total Distance Over 50-Ft Obstacle 107 5 FT STALL SPEED (CAS): Flaps Up, Power Off 48 KNOTS Flaps Down, Power Off 42 KNOTS MAXIMUM WEIGHT 1600 LBS STANDARD EMPTY WEIGHT: Commuter 1111 LBS Commuter II 1129 LBS MAXIMUM USEFUL LOAD: Commuter 489 LBS Commuter II 471 LBS BAGGAGE ALLOWANCE 120 LBS WING LOADING: Pounds/Sq Ft 10.0 POWER LOADING: Pounds/HP 16.0 FUEL CAPACITY: Total Standard Tanks 26 GAL. Long; Range Tanks 38 GAL. OIL CAPACITY 6 QTS ENGINE: Teledyne Continental O-200-A 100 BHP at 2750 RPM PROPELLER: Fixed Pitch, Diameter 69 IN. D1080-13-RPC-6,000-12/77 PILOT'S OPERATING HANDBOOK Cessna 150 COMMUTER 1977 MODEL 150M Serial No. -
Optimal Top of Descent Analysis in Respect to Wind Prediction Errors and Guidance Strategies*
Trans. JSASS Aerospace Tech. Japan Vol. 15, No. APISAT-2016, pp. a45-a51, 2017 Optimal Top of Descent Analysis in Respect to Wind Prediction Errors and Guidance Strategies* By Adriana ANDREEVA-MORI and Tsuneharu UEMURA (5mm) Aeronautical Technology Directorate, Japan Aerospace Exploration Agency, Tokyo, Japan (Received January 31st, 2017) Modern airliners use the profiles calculated by the onboard flight management system (FMS) to execute safe and efficient descents. Since the wind often varies greatly between the cruising altitude and the end-of-descent altitude, the FMS uses both predicted and measured wind to determine the descent profile. Even so, the actual wind encountered along the descent changes the profile. When a constant descent speed is maintained at idling thrust, the aircraft deviates from its path and needs to either fly an additional steady level flight segment to the metering fix or deflect speed brakes to ensure the speed constraints at the metering fix are met. This research analyses the optimal top of descent in respect to such wind prediction error and fuel burn. Numerical simulations for the Boeing 767-300 are done and it is shown that an early descent of 0.5 nm would save, on average, 0.9 lb of fuel for an idling descent from 30,000 ft to 10,000 ft and at a constant speed of 280 kt, and decrease the number of cases where the necessary deceleration could not be achieved due to lack of enough lateral distance by 77%, thus improving safety and easing operations. Key Words: Top of Descent, Flight Management System, VNAV-SPEED, Wind Disturbances, Fuel Optimal 1. -
C-130J Super Hercules Whatever the Situation, We'll Be There
C-130J Super Hercules Whatever the Situation, We’ll Be There Table of Contents Introduction INTRODUCTION 1 Note: In general this document and its contents refer RECENT CAPABILITY/PERFORMANCE UPGRADES 4 to the C-130J-30, the stretched/advanced version of the Hercules. SURVIVABILITY OPTIONS 5 GENERAL ARRANGEMENT 6 GENERAL CHARACTERISTICS 7 TECHNOLOGY IMPROVEMENTS 8 COMPETITIVE COMPARISON 9 CARGO COMPARTMENT 10 CROSS SECTIONS 11 CARGO ARRANGEMENT 12 CAPACITY AND LOADS 13 ENHANCED CARGO HANDLING SYSTEM 15 COMBAT TROOP SEATING 17 Paratroop Seating 18 Litters 19 GROUND SERVICING POINTS 20 GROUND OPERATIONS 21 The C-130 Hercules is the standard against which FLIGHT STATION LAYOUTS 22 military transport aircraft are measured. Versatility, Instrument Panel 22 reliability, and ruggedness make it the military Overhead Panel 23 transport of choice for more than 60 nations on six Center Console 24 continents. More than 2,300 of these aircraft have USAF AVIONICS CONFIGURATION 25 been delivered by Lockheed Martin Aeronautics MAJOR SYSTEMS 26 Company since it entered production in 1956. Electrical 26 During the past five decades, Lockheed Martin and its subcontractors have upgraded virtually every Environmental Control System 27 system, component, and structural part of the Fuel System 27 aircraft to make it more durable, easier to maintain, Hydraulic Systems 28 and less expensive to operate. In addition to the Enhanced Cargo Handling System 29 tactical airlift mission, versions of the C-130 serve Defensive Systems 29 as aerial tanker and ground refuelers, weather PERFORMANCE 30 reconnaissance, command and control, gunships, Maximum Effort Takeoff Roll 30 firefighters, electronic recon, search and rescue, Normal Takeoff Distance (Over 50 Feet) 30 and flying hospitals. -
(VL for Attrid
ECCAIRS Aviation 1.3.0.12 Data Definition Standard English Attribute Values ECCAIRS Aviation 1.3.0.12 VL for AttrID: 391 - Event Phases Powered Fixed-wing aircraft. (Powered Fixed-wing aircraft) 10000 This section covers flight phases specifically adopted for the operation of a powered fixed-wing aircraft. Standing. (Standing) 10100 The phase of flight prior to pushback or taxi, or after arrival, at the gate, ramp, or parking area, while the aircraft is stationary. Standing : Engine(s) Not Operating. (Standing : Engine(s) Not Operating) 10101 The phase of flight, while the aircraft is standing and during which no aircraft engine is running. Standing : Engine(s) Start-up. (Standing : Engine(s) Start-up) 10102 The phase of flight, while the aircraft is parked during which the first engine is started. Standing : Engine(s) Run-up. (Standing : Engine(s) Run-up) 990899 The phase of flight after start-up, during which power is applied to engines, for a pre-flight engine performance test. Standing : Engine(s) Operating. (Standing : Engine(s) Operating) 10103 The phase of flight following engine start-up, or after post-flight arrival at the destination. Standing : Engine(s) Shut Down. (Standing : Engine(s) Shut Down) 10104 Engine shutdown is from the start of the shutdown sequence until the engine(s) cease rotation. Standing : Other. (Standing : Other) 10198 An event involving any standing phase of flight other than one of the above. Taxi. (Taxi) 10200 The phase of flight in which movement of an aircraft on the surface of an aerodrome under its own power occurs, excluding take- off and landing. -
B767 FMS Step Climb Predictions
Page 1 BOEING 767 B767 FMS STEP CLIMB Step climb calculations depend upon prior calculation of the required profile for the current cruise altitude and the active route. This profile is based on scheduled speeds and cost index, beginning with current gross weight. If no wind or temperature forecast is entered, it is based on still air and zero ISA deviation prior to takeoff. In flight, the currently measured ISA deviation is extrapolated to all waypoints in the flight plan through the end of the flight. The actual wind is resolved into a headwind or tailwind component which is washed out to half its value in 200 NM during cruise or in 5000 ft during climb or descent. Beyond these points it continues to wash out exponentially. Entering wind forecasts will make the active flight plan profile prediction more precise. This can be done in two ways; An overall average wind entered on the PERF INIT page will be treated as a forecast of cruise wind. A wind forecast entered opposite a cruise waypoint on the RTE DATA page overrides the overall wind forecast from that waypoint on. In fact, it is retained for the remainder of the cruise segment until the next waypoint with a wind forecast entry. Therefore, wind forecasts can be precisely reflected in the FMC by entering winds opposite the cruise waypoints they take effect. They need not be entered at each waypoint, only those where there is a significant change in the forecast. These entries affect only the active or provisional route fuel/cost predictions. -
Cessna 172SP
CESSNA INTRODUCTION MODEL 172S NOTICE AT THE TIME OF ISSUANCE, THIS INFORMATION MANUAL WAS AN EXACT DUPLICATE OF THE OFFICIAL PILOT'S OPERATING HANDBOOK AND FAA APPROVED AIRPLANE FLIGHT MANUAL AND IS TO BE USED FOR GENERAL PURPOSES ONLY. IT WILL NOT BE KEPT CURRENT AND, THEREFORE, CANNOT BE USED AS A SUBSTITUTE FOR THE OFFICIAL PILOT'S OPERATING HANDBOOK AND FAA APPROVED AIRPLANE FLIGHT MANUAL INTENDED FOR OPERATION OF THE AIRPLANE. THE PILOT'S OPERATING HANDBOOK MUST BE CARRIED IN THE AIRPLANE AND AVAILABLE TO THE PILOT AT ALL TIMES. Cessna Aircraft Company Original Issue - 8 July 1998 Revision 5 - 19 July 2004 I Revision 5 U.S. INTRODUCTION CESSNA MODEL 172S PERFORMANCE - SPECIFICATIONS *SPEED: Maximum at Sea Level ......................... 126 KNOTS Cruise, 75% Power at 8500 Feet. ................. 124 KNOTS CRUISE: Recommended lean mixture with fuel allowance for engine start, taxi, takeoff, climb and 45 minutes reserve. 75% Power at 8500 Feet ..................... Range - 518 NM 53 Gallons Usable Fuel. .................... Time - 4.26 HRS Range at 10,000 Feet, 45% Power ............. Range - 638 NM 53 Gallons Usable Fuel. .................... Time - 6.72 HRS RATE-OF-CLIMB AT SEA LEVEL ...................... 730 FPM SERVICE CEILING ............................. 14,000 FEET TAKEOFF PERFORMANCE: Ground Roll .................................... 960 FEET Total Distance Over 50 Foot Obstacle ............... 1630 FEET LANDING PERFORMANCE: Ground Roll .................................... 575 FEET Total Distance Over 50 Foot Obstacle ............... 1335 FEET STALL SPEED: Flaps Up, Power Off ..............................53 KCAS Flaps Down, Power Off ........................... .48 KCAS MAXIMUM WEIGHT: Ramp ..................................... 2558 POUNDS Takeoff .................................... 2550 POUNDS Landing ................................... 2550 POUNDS STANDARD EMPTY WEIGHT .................... 1663 POUNDS MAXIMUM USEFUL LOAD ....................... 895 POUNDS BAGGAGE ALLOWANCE ........................ 120 POUNDS (Continued Next Page) I ii U.S. -
CO2 EMISSIONS from COMMERCIAL AVIATION: 2013, 2018, and 2019 Down from Nearly 19% in 2013
OCTOBER 2020 CO2 EMISSIONS FROM COMMERCIAL AVIATION 2013, 2018, AND 2019 BRANDON GRAVER, PH.D., DAN RUTHERFORD, PH.D., AND SOLA ZHENG ACKNOWLEDGMENTS The authors thank Jennifer Callahan and Dale Hall (ICCT), Tim Johnson (Aviation Environment Federation), and Andrew Murphy (Transport & Environment) for their review. This work was conducted with generous support from the Aspen Global Change Institute. SUPPLEMENTAL DATA Additional country-specific operations and CO2 emissions data for 2013, 2018, and 2019 can be found on the ICCT website. International Council on Clean Transportation 1500 K Street NW, Suite 650, Washington, DC 20005 [email protected] | www.theicct.org | @TheICCT © 2020 International Council on Clean Transportation EXECUTIVE SUMMARY Last year, the International Council on Clean Transportation (ICCT) developed a bottom-up, global aviation inventory to better understand carbon dioxide (CO2) emissions from commercial aviation in 2018. This report updates the operations and emissions analyses for calendar year 2018 based on improved source data, and includes new analyses for 2013 and 2019. In 2013, the International Civil Aviation Organization (ICAO) requested its technical experts develop a global CO2 emissions standard for aircraft, and states began to submit voluntary action plans to reduce CO2 emissions from aviation. This paper details a global, transparent, and geographically allocated CO2 inventory for three years of commercial aviation, using operations data from OAG Aviation Worldwide Limited, ICAO, individual airlines, and the Piano aircraft emissions modeling software. Our Global Aviation Carbon Assessment (GACA) model estimated CO2 emissions from global passenger and cargo operations on par with totals reported by industry (Figure ES-1). In all three analyzed years, passenger flights were responsible for approximately 85% of commercial aviation CO2 emissions. -
Climb, Cruise and Descent Speed Reduction for Airborne Delay
Climb, Cruise and Descent Speed Reduction for Airborne Delay without Extra Fuel Yan Xu1 Ramon Dalmau2 and Xavier Prats3 Technical University of Catalonia, Castelldefels 08860, Barcelona, Spain I. Introduction In the majority of the situations, Air Traffic Flow Management (ATFM) regulations are issued due to weather related capacity reductions. Considering the uncertainties in weather prediction and other unforeseen factors, ATFM decisions are typically conservative and the planned regulations may last longer than actually needed [1, 2]. At present, ground delay is more preferable than airborne delay (holding) from a safety, environmental and operating cost points of view. However, when regulations are canceled before their initial planned ending time, as occur often [3, 4], the already accomplished delay on ground cannot be recovered, or can be partially recovered by increasing speed, leading to extra fuel consumption. In order to overcome this issue, a speed reduction (SR) strategy was proposed in [5], which aimed at partially absorbing ATFM delays airborne. Ground delayed aircraft were enabled to fly at the minimum fuel consumption speed (typically slower than nominal cruise speed initially chosen by the airline) performing in this way some airborne delay. At the same time, part of the fuel was saved with respect to the nominal flight. This strategy was further explored in [6], where aircraft were allowed to cruise at the lowest possible speed in such a way the specific range (i.e., the distance flown per unit of fuel consumption) remained the same as initially planned. In this situation, if regulations were canceled, aircraft already airborne and flying slower, could increase their cruise 1 Ph.D. -
The Perceived Importance and Utilization of "Party Line" Information by Air Carrier Flight Crews Was Investigated Through Pilot Surveys and a Flight Simulation Study
Preprint : Fifth International Conference On Human-Machine Interaction And Artificial Intelligence In Aerospace Toulouse, France, September 27-29, 1995 'PARTY LINE' INFORMATION USE STUDIES AND IMPLICATIONS FOR ATC DATALINK COMMUNICATIONS R. John Hansman, Amy Pritchett & Alan Midkiff MIT International Center for Air Transportation MIT Aeronautical Systems Laboratory Room 33-113, 77 Mass. Ave Cambridge, MA 02139 Tel: 617 253 2271 Fax: 617 253 4196 Emaii: [email protected] ABSTRACT The perceived importance and utilization of "party line" information by air carrier flight crews was investigated through pilot surveys and a flight simulation study. The Importance, Availability, and Accuracy of party line information elements were explored through surveys of pilots of several operational types. The survey identified numerous traffic and weather party line information elements which were considered important. These elements were scripted into a full-mission flight simulation which examined the utilization of party line information by studying subject responses to specific information element stimuli. Tae awareness of the different Party Line elements varied, and awareness was also affected by pilot workload. In addition, pilots were aware of some traffic information elements, but were reluctant to act on Par_y Line Information alone. Finally, the results of both the survey and the simulation indicated that the importance of party line information appeared to be greatest for operations near or on the airport. This indicates that caution should be exercised when implementing datalink communications in tower and close-in terminal control sectors. 1. INTRODUCTION Current communications between aircraft and Air Traffic Control (ATC) use shared voice VHF frequencies. Aircraft on a common frequency can monitor all transmissions on that frequency.