Comparison of Jameson Cell and Jet Diffuser Flotation Column
Total Page:16
File Type:pdf, Size:1020Kb
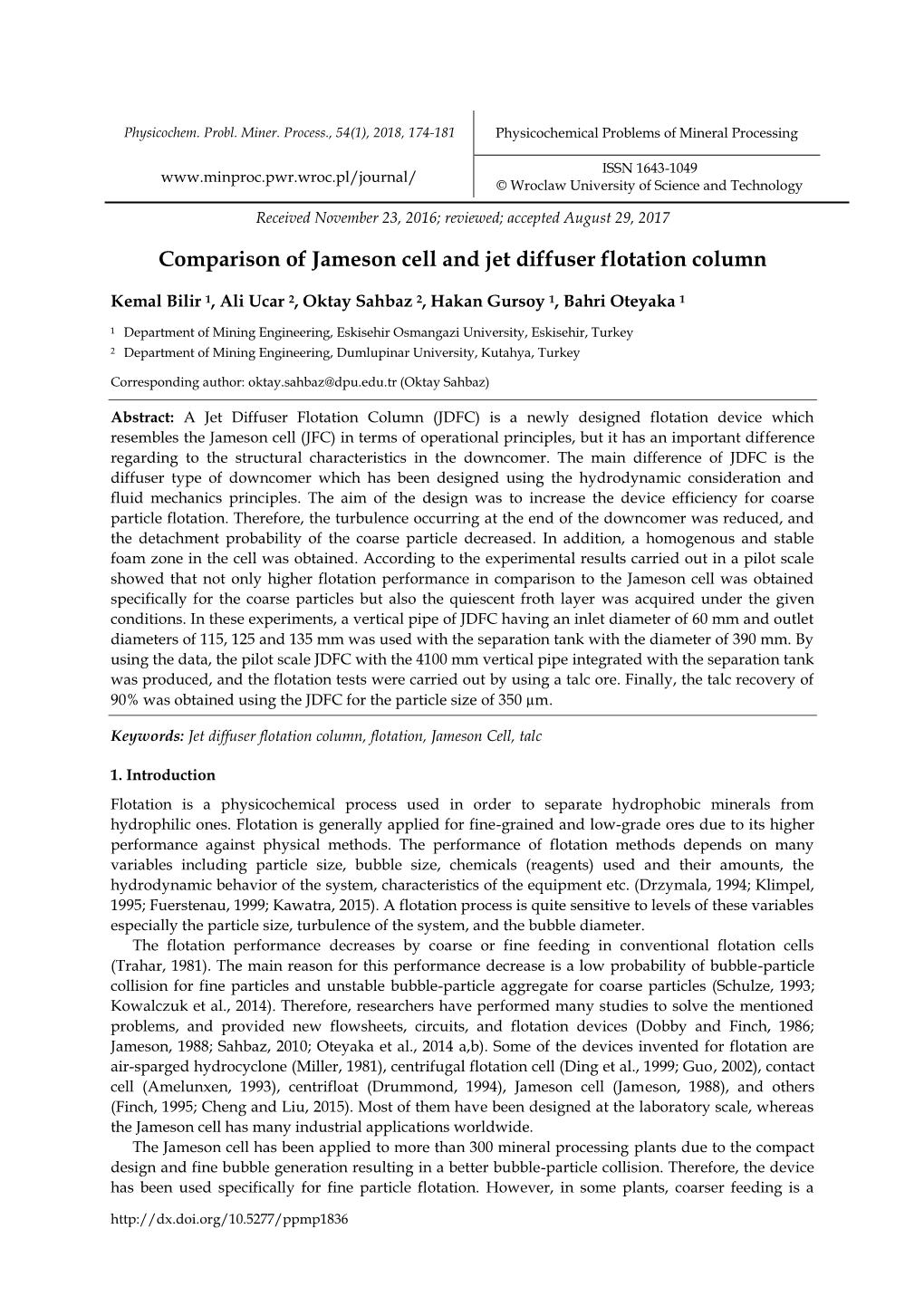
Load more
Recommended publications
-
Minerals and Metallurgical Engineering
Course Structure B. Tech. - Minerals and Metallurgical Engineering Applicable to those admitted through JEE from 2019 onwards Department of Fuel, Minerals and Metallurgical Engineering Indian Institute of Technology (ISM) Dhanbad Dhanbad, Jharkhand, India (September - 2019) Page 1 of 41 Course Structure SEMESTER III S. Subject Subject Name Lecture Tutorial Practical Credit Contact No. ID (L) (T) (P) Hours Hours 1 FMC201 Colloids and interfacial 3 0 0 9 3 phenomena 2 FMC202 Heat and mass transfer 3 0 0 9 3 3 FMC203 Physical separation 3 0 0 9 3 processes for coal and minerals 4 FME221 Particle technology (ESO 3 0 0 9 3 1) 5 E/SO 2 E/SO 3 0 0 9 3 6 FMC251 Particle technology 0 0 2 2 2 laboratory 7 FMC252 Physical separation 0 0 2 2 2 processes laboratory Total Credit 49 19 SEMESTER IV S. Subject Subject Name Lecture Tutorial Practical Credit Contact No. ID (L) (T) (P) Hours Hours 1 FMC204 Electrochemistry and 3 0 0 9 3 corrosion 2 FMC205 Thermodynamics and 3 0 0 9 3 kinetics 3 FMC206 Phase transformation and 3 0 0 9 3 heat treatment 4 FMC207 Fine particle processing for 3 0 0 9 3 coal and minerals 5 FME222 Introduction to fuel 3 0 0 9 3 technology (ESO 3) 6 FMC253 Fine particle processing 0 0 2 2 2 laboratory 7 FMC254 Introduction to fuel 0 0 2 2 2 technology laboratory Total Credit 49 19 Page 2 of 41 SEMESTER V S. Subject Subject Name Lecture Tutorial Practical Credit Contact No. -
Telfer Processing Plant Upgrade – the Implementation of Additional
Telfer Processing Plant Upgrade – The Implementation of Additional Cleaning Capacity and the Regrinding of Copper and Pyrite Concentrates D R Seaman1, F Burns2, B Adamson3, B A Seaman4 and P Manton5 ABSTRACT The Telfer concentrator, located in the Great Sandy Desert of Western Australia, consists of a dual train gold/copper operation processing ore from one underground and, currently, two open pit mines with differing mineralogy. The fl otation circuit of each train was designed to operate in several modes depending on the feed mineralogy. The majority of ore mined at Telfer is processed in a sequential mode where copper minerals are fi rst fl oated into a saleable copper concentrate followed by the fl otation of an auriferous pyrite concentrate which is treated in an on-site hydrometallurgical plant (carbon-in-leach (CIL)). Gold is recovered as a gravity product within the primary grinding circuit, to the copper concentrate, and to a lesser extent, the CIL circuit. Since Telfer was re-opened, with a new concentrator, in 2004, the processing plant has struggled with poor copper concentrate grades, partially due to the excessive entrainment of non-sulfi de gangue minerals in the copper fl otation circuit and, more recently, due to composite copper particles produced when processing ore from a supplementary satellite pit that has not previously been processed through the new Telfer concentrator. Gold recoveries in the CIL circuit have also been below industry standard. This paper presents the implementation of recent changes made to the circuit to address these performance issues. The reconfi guration of the circuit has involved the installation of the following major equipment items: two ISAMills™ in ultra-fi ne grinding applications (one in the copper circuit and one in the pyrite circuit), two Jameson Cells to improve fi ne gangue rejection and a bank of 5 × Outotec TC30s to recovery copper and gold from the reground pyrite stream. -
Xstrata Technology Update Edition 13 – April 2012 Building Plants That Work
xstrata technology update Edition 13 – April 2012 Building plants that work You have to get a lot of things it takes another operator to get them right to build a plant that works. right. Someone who has lived through the problems, had to do the maintenance, operated during a midnight power Of course the big picture must be right – doing the right project, in the right place, failure, cleaned up the spill. Someone at the right time. who has “closed the loop” on previous designs; lived with previous decisions After that, the devil is in the detail. You and improved them, over and over. need a sound design, good execution, good commissioning, and ongoing This is why Xstrata Technology provides support after commissioning. You need a technology “package”. Just as a car to operate and maintain your plant in is more than an engine, technology is the long run, long after the construction more than a single piece of equipment. company has left. That’s when all the Technology is a system. All the elements “little” details become important – how of the system have to work with each easy is it to operate, how good is the other and with the people in the plant. maintenance access, what happens in We want our cars designed by people a power failure, where are the spillage who love cars and driving. So should points and how do we clean them our plants be designed by people with up? Are the instruments reliable and experience and passion to make each is the process control strategy robust one work better than the last. -
Scale-Up in Froth Flotation: a State-Of-The-Art Review
Scale-up in froth flotation: A state-of-the-art review Diego Mesa∗, Pablo R. Brito-Parada Department of Earth Science and Engineering, Royal School of Mines, Imperial College London, South Kensington Campus, London SW7 2AZ, United Kingdom Abstract Froth flotation has been one of the most important and widely used methods to concentrate minerals since its introduction over a hundred years ago. Over the last few decades, in order to process more mineral while reducing capital costs, flotation equipment has become exponentially larger. The increase in tank volume, however, has brought new challenges in the operation and design of industrial flotation tanks. This review analyses the literature on flotation tank scale-up for the first time, contrasting several techniques and approaches used in both historical and state-of- the-art research. The study of flotation scale-up is crucial for the optimisation of industrial plant performance and the maximisation of laboratory-scale research impact. While important advances in our understanding of flotation have been achieved, large flotation tank design and scale-up has, to a large extent, remained in-house know-how of manufacturing companies. This review of the literature relevant to flotation tank scale-up has resulted in a new classification, dividing the scale-up literature into two main areas of study, namely \Kinetic scale-up" and \Machine design scale-up". This review indicates that current scale-up rules governing the design of flotation tanks focus mainly on pulp zone kinetic parameters and neglect the effects on the froth zone, despite the importance of froth stability and mobility in determining flotation performance. -
Extractive Metallurgy of Copper This Page Intentionally Left Blank Extractive Metallurgy of Copper
Extractive Metallurgy of Copper This page intentionally left blank Extractive Metallurgy of Copper Mark E. Schlesinger Matthew J. King Kathryn C. Sole William G. Davenport AMSTERDAM l BOSTON l HEIDELBERG l LONDON NEW YORK l OXFORD l PARIS l SAN DIEGO SAN FRANCISCO l SINGAPORE l SYDNEY l TOKYO Elsevier The Boulevard, Langford Lane, Kidlington, Oxford OX5 1GB, UK Radarweg 29, PO Box 211, 1000 AE Amsterdam, The Netherlands First edition 1976 Second edition 1980 Third edition 1994 Fourth edition 2002 Fifth Edition 2011 Copyright Ó 2011 Elsevier Ltd. All rights reserved. No part of this publication may be reproduced, stored in a retrieval system or transmitted in any form or by any means electronic, mechanical, photocopying, recording or otherwise without the prior written permission of the publisher Permissions may be sought directly from Elsevier’s Science & Technology Rights Department in Oxford, UK: phone (+44) (0) 1865 843830; fax (+44) (0) 1865 853333; email: permissions@ elsevier.com. Alternatively you can submit your request online by visiting the Elsevier web site at http://elsevier.com/locate/permissions, and selecting Obtaining permission to use Elsevier material Notice No responsibility is assumed by the publisher for any injury and/or damage to persons or property as a matter of products liability, negligence or otherwise, or from any use or operation of any methods, products, instructions or ideas contained in the material herein British Library Cataloguing in Publication Data A catalogue record for this book is available from the British Library Library of Congress Cataloging-in-Publication Data A catalog record for this book is available from the Library of Congress ISBN: 978-0-08-096789-9 For information on all Elsevier publications visit our web site at elsevierdirect.com Printed and bound in Great Britain 11 12 13 14 10 9 8 7 6 5 Photo credits: Secondary cover photograph shows anode casting furnace at Palabora Mining Company, South Africa. -
Flotation of Sulphide Ores - HZL Experience
FROTH FLOTATION : RECENT TRENDS @IIME, JAMSHEDPUR, 1998; pp. 18-41 Flotation of Sulphide Ores - HZL Experience V.P. KOHAD Hindustan Zinc Ltd., Zawar Mines, Udaipur - 313 901 ABSTRACT Flotation process, patented in the year 1906, was originally developed for mineral industry to recover values from high grade tailings of gravity separation plants. This technology has acclaimed importance as a versatile process for the beneficiation of vast variety of sulphide minerals. Due to flexibility of the process and remarkable development taken place in flotation technology and its ancillary systems, it has now become possible to recover fine grained sulphide minerals from complex ore deposits, whose processing was earlier considered un- economical. Today, about 400 million tonnes of sulphide ore is treated annually by flotation process worldwide. M/s Hindustan Zinc Ltd. (HZL), a leading lead-zinc mining and smelting company in India has experienced a spectacular growth from the time of its inception. Starting from a single 500 MT per day lead-zinc mine at Zawar, HZL has expanded its mining capacity to about 13,000 MT per day with matching ore beneficiation plants, all adopting froth flotation technology. The phenomenal progress is a result of HZL's emphasis on research and development with an objective to improve the efficiency and to optimize performance, and to seek innovative modern technology and control systems in their flotation plant and processes. This has not only solved metallurgical problems but improved overall plant economics. High grade concentrates produced with reduced deleterious impurities have further enhanced smelting efficiency. The paper covers general principles and aspects of industrial sulphide ore flotation practices in brief and processes adopted in HZL's plants. -
Glencore Technology Overview
COMPANY OVERVIEW GLENCORE TECHNOLOGY Level 10, 160 Ann St Brisbane, Queensland, Australia, 4001 Tel. +61 7 3833 8500 Fax. +61 7 3833 8555 [email protected] www.glencoretechnology.com/ Glencore: Enhancing Processes in the Mining Industry Glencore Technology’s Chief Technology Officer Reinhardt Viljoen discusses the importance of collaboration in the mining industry and opens up about the importance of branding and marketing Written by: Robert Spence Produced by: Vince Kielty GLENCORE MINING ISASMELT and IsaKidd, which are slurry storage and leaching patented processes widely used in tanks that incorporates modular the smelting, electrowinning and components and mechanical joins copper refining industry today. to provide all the benefits of a Additional technologies include traditional welded tank, but with IsaMill, a fine and mainstream lower costs, reduced installation grinding technology, the Jameson times and far greater flexibility. Cell flotation technology and the “The tank is mechanically Albion Process leaching technology. bolted. Anyone with a minimal “We’ve initially developed amount of skill and supervision specific copper processing can bolt it together. Its scalability technology,” said Reinhardt makes it very exciting for clients Viljoen, Glencore Technology’s as it can accommodate most Chief Technology Officer. projects and even be reused for “However, we’re now also involved other projects.” IsaKidd robotic CSM in the broader design of smelters In addition, Glencore Technology and refineries and our technology has developed the HyperSparge™, s one of the largest Glencore Technology. Spawned is applicable to other base metals a proven and cost effective system Acommodity traders and from the merger with Xstrata, like zinc, lead, nickel, etc. -
Economic Recovery and Upgrade of Metals from Middling and Tailing Streams
ECONOMIC RECOVERY AND UPGRADE OF METALS FROM MIDDLING AND TAILING STREAMS *P. Voigt1, M. Hourn1, V. Lawson1, G. Anderson1, and D. Mallah2. 1Glencore Technology 160 Ann St Brisbane, Australia 4000 (*Corresponding author: [email protected]) 2Glencore Zinc PMB 6, Mount Isa Queensland, Australia, 4825 ABSTRACT As mine head grades decline and orebodies become more complex, traditional mineral processing techniques and flowsheets to achieve saleable concentrate become more difficult to design and construct. Mines with lower quality concentrates or concentrates with penalty elements are particular under threat. The economics of these operations are far more susceptible to metal price, concentrate treatment terms and the availability of other, cleaner concentrates. Additional value may be realised for these orebodies through improved recovery by producing a low grade middling concentrate for further processing, in conjunction with a saleable concentrate. The most cost effective way to reduce impurity levels is to do so as early as possible in the mining value chain. Technologies such as fine grinding and fine particle flotation are well established as effective methods for impurity rejection in mineral processing. What is normally overlooked is how a hydrometallurgical process could also be integrated in the overall flowsheet to achieve higher overall recovery at the mill. In the base metals environment, this is mainly because hydrometallurgical processes are associated with production of metal or use of expensive and toxic precipitating agents once the minerals of interest are solubilised. These processes can be very expensive, particularly with rising power costs and poor economies of scale in capital costs associated with low production rates from middling streams. -
Xstrata Technology Newsletter
Edition 10 – March 2009 Focus on the Fundamentals The last 6 months have been tumultuous. But the mining industry This operating know-how and specialisation is Xstrata Technology’s is used to tough times. It knows there are fundamental truths that strength. So is being part of an operating company with access apply in good times and in bad. One of these is controlling cost to full scale installations, and our global network of users keen to – both operating and capital. Improving energy efficiency and share ideas to improve operating efficiency and maintenance for making better product grade and recovery are always good. So mutual benefit. is improving environmental performance. Projects must start up We aim to keep our stable core team through good times and bad. quickly and successfully, and this needs good design, experienced This approach will now serve our clients in the tough times ahead. project management, specialist training, commissioning and Whether it is for new projects, or for improving the efficiency of ongoing support. existing operations, nothing beats experienced operators. There is no shortcut to achieving this. The critical success factor is experience. The best people to design your plant are those who Xstrata Technology: Solutions have managed their own operations and projects to survive tough times. People who specialise in their equipment – who have from Real Operators operated it themselves, and have designed and commissioned Joe Pease, Chief Executive, Xstrata Technology dozens of new installations to constantly improve their designs. [email protected] This results in hundreds of “small” design details that make a huge difference. -
Adsorbing Colloidal Flotation Removing Metals Ions in a Modified Jet Cell
Minerals Engineering 24 (2011) 1010–1015 Contents lists available at ScienceDirect Minerals Engineering journal homepage: www.elsevier.com/locate/mineng Adsorbing colloidal flotation removing metals ions in a modified jet cell ⇑ ⇑ M. Santander a, , L. Valderrama a, M. Guevara a, J. Rubio b, a Departamento de Metalurgia, CRIDESAT, Universidad de Atacama (UDA), Av. Copayapu 485 Copiapó-Atacama, Chile b Laboratório de Tecnologia Mineral e Ambiental, Departamento de Engenharia de Minas, PPG3M, Universidade Federal do Rio Grande do Sul (UFRGS), Av. Bento Gonçalves 9500, Prédio 75, Porto Alegre, RS 91501-970, Brazil article info abstract Article history: The removal of Cu2+,Zn2+ and Ni2+ ions from synthetic wastewater with a modified Jameson cell (MJC) Received 14 January 2011 was studied using adsorption colloidal flotation (ACF). A colloidal dispersion of Fe (OH)3 (formed Accepted 29 April 2011 in situ from FeCl3) at pH 11 was used as an adsorbent colloid to ensure full adsorption and precipitation. The precipitates were flocculated with polyacrylamide and hydrophobised with sodium oleate and pine oil as a frother during the flotation stage. In the modified jet cell, the downcomer was sealed at the bot- Keywords: tom with a diffuser, and the re-flotation of detached flocs and the probability of bubbles/particles capture Jet flotation was enhanced, which improved the recovery rate. As a result, the modified Jameson cell was more effi- Colloid adsorbent cient (higher loaded carrier recoveries) than the conventional jet cell (CJC) in removing heavy metals ions. Ions removal The physico-chemical characteristics, cell design and operating parameters were studied, and the removal efficiency was evaluated by monitoring the final concentration of ions in the treated effluent. -
Recovery Interactions Between the Froth Zone, Pulp Zone and Downcomer Within a Jameson Cell
RECOVERY INTERACTIONS BETWEEN THE FROTH ZONE, PULP ZONE AND DOWNCOMER WITHIN A JAMESON CELL G Harbort(1), J Cowburn(2), E Manalpig(3) (1) University of Queensland (2) Xstrata Technology (3) Julius Kruttschnitt Mineral Research Centre ABSTRACT The work reported in this paper shows that the primary area of coal recovery within the Jameson Cell is the downcomer, where the air and pulp are dispersed into a dense foam of fine bubbles. This creates an intense collection zone for bubble-particle collision and coal collection. Historically, coal recovery in the Jameson Cell has not differentiated between recovery in the downcomer, pulp zone or the froth zone. As such, attempts to optimise the recovery of coal in one zone can result in non-optimum performance of another. A major flotation programme has been undertaken to measure coal recovery in the three zones of the Jameson Cell, separate from each other. The findings from this work should allow, upon completion, recovery in each zone to be individually optimised to give maximum overall coal recovery, from a size by size perspective. INTRODUCTION The Jameson Cell was a joint development between Mount Isa Mines and Prof. Graeme Jameson of the University of Newcastle (Jameson, 1988). Since its invention in 1986 there have been 94 Jameson Cells installed in the coal industry, both in Australia and overseas. Jameson Cell operation The principles of Jameson Cell operation have been discussed by numerous authors, including Jameson et al (1988), Evans et al (1995) and recently by Harbort et al (2002). The Jameson Cell can be divided into three main zones, as described with reference to Fig. -
241.241.435/2571.435/259,435,306 07: 58 Field of Search
USOO5951875A United States Patent (19) 11 Patent Number: 5,951,875 Kanel et al. (45) Date of Patent: *Sep. 14, 1999 54 ADSORPTIVE BUBBLE SEPARATION 5,332,100 7/1994 Jameson. METHODS AND SYSTEMS FOR 5,378,369 1/1995 Rose et al.. COMPONENTS THEREFROM 486999 2/1976 Australia. 487018 2/1976 Australia. 75 Inventors: Jeffrey Scott Kanel, Kingsport, Tenn.; O 523 883 1/1993 European Pat. Off.. Scott Arthur Guelcher, Weirton, Va. O 586 255 3/1994 European Pat. Off.. O 612 725 8/1994 European Pat. Off.. 73 Assignee: Eastman Chemical Company, 2367.705 5/1978 France Kingsport, Tenn 1541 345 2/1979 United Kingdom. s 20224.59 12/1979 United Kingdom. * Notice: This patent is Subject to a terminal dis- OTHER PUBLICATIONS CC. Rose, P.D. et al.; “Cross-flow Ultrafiltration Used in Algal 21 Appl. No.: 08/771,754 High Rate Oxidation Pond Treatment of Saline Organic 9 Effluents with the Recovery of Products of Value"; Water 22 Filed: Dec. 20, 1996 Science and Technology, 1992; Vol. 25, No. 10; pp. 319-327. 3.51 Int. Cl.C ................................210/703; AO1G 7.7100 BO1D2. 1/O2 Smith, P.H. et al., “Froth Flotation for Harvesting Chlorella O X O -- O "210/70,474. 241/. 241/2: 24/301; Algae'; Northwest Science, vol. 42, No. 4, 1968; pp. 241.241.435/2571.435/259,435,306 07: 58 Field of Search ................................. 210/703, 221.2, (List continued on next page.) 210/806, 768, 770; 47/1.4; 241/1, 2,301, 24.11; 435/259, 306.1, 283.1, 257.1 Primary Examiner Thomas M.