Diapositiva 1
Total Page:16
File Type:pdf, Size:1020Kb
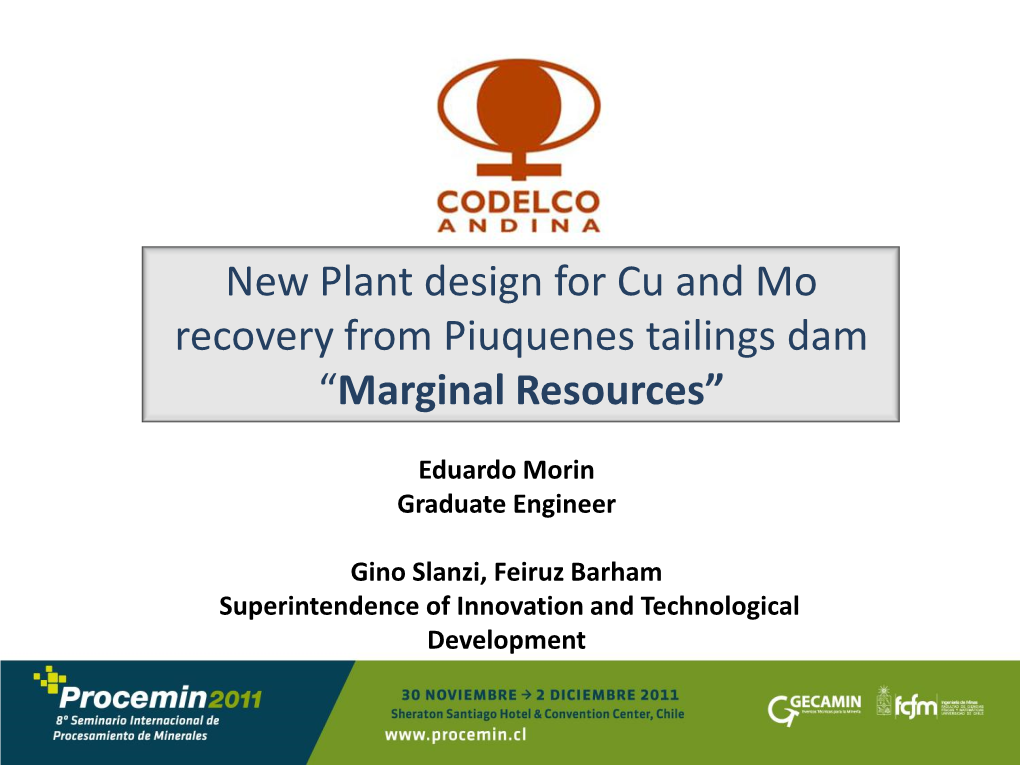
Load more
Recommended publications
-
From Base Metals and Back – Isamills and Their Advantages in African Base Metal Operations
The Southern African Institute of Mining and Metallurgy Base Metals Conference 2013 H. de Waal, K. Barns, and J. Monama From base metals and back – IsaMills and their advantages in African base metal operations H. de Waal, K. Barns, and J. Monama Xstrata IsaMill™ technology was developed from Netzsch Feinmahltechnik GmbH stirred milling technology in the early 1990s to bring about a step change in grinding efficiency that was required to make Xstrata’s fine-grained lead/zinc orebodies economic to process. From small-scale machines suited to ultrafine grinding, the IsaMill™ has developed into technology that is able to treat much larger tonnages, in coarser applications, while still achieving high energy efficiency, suited for coarser more standard regrind and mainstream grinding applications. The unique design of the IsaMillTM, combining high power intensity and effective internal classification, achieves high energy efficiency and tight product distribution which can be effectively scaled from laboratory scale to full-sized models. The use of fine ceramic media also leads to significant benefits in downstream flotation and leaching operations. These benefits are key drivers for the adoption of the technology into processing a diverse range of minerals worldwide, and offer major opportunities for power reduction and improved metallurgy for the African base metal operations. Keywords: IsaMill, regrind, energy efficiency, inert grinding. Introduction The development of the IsaMillTM, by MIM (now GlencoreXstrata) and Netzsch Feinmahltechnik GmbH, was initiated to enable the development of the fine-grained ore deposits at Mt Isa and McArthur River in Northern Australia. To liberate the valuable minerals and so produce a saleable concentrate this ultrafine-grained ore needed to be ground to a P80 of 7 μm. -
Challenges Related to the Processing of Fines in the Recovery of Platinum Group Minerals (Pgms)
minerals Review Challenges Related to the Processing of Fines in the Recovery of Platinum Group Minerals (PGMs) Kirsten C. Corin 1,* , Belinda J. McFadzean 1, Natalie J. Shackleton 2 and Cyril T. O’Connor 1 1 Centre for Minerals Research, Chemical Engineering Department, University of Cape Town, P Bag X3, Rondebosch, Cape Town 7700, South Africa; [email protected] (B.J.M.); [email protected] (C.T.O.) 2 Minerals Expertise Tech Pty Ltd., Germiston 2007, South Africa; [email protected] * Correspondence: [email protected] Abstract: In order to increase the recovery of PGMs by flotation, it is necessary to optimise the liberation of the key minerals in which the platinum group elements (PGEs) are contained which include sulphides, arsenides, tellurides, and ferroalloys among others, while at the same time ensuring the optimal depression of gangue minerals. In order to achieve this, comminution circuits usually consist of two or three stages of milling, in which the first stage is autogeneous, followed by ball milling. Further liberation is achieved in subsequent stages using ultra-fine grinding. Each comminution stage is followed by flotation in the so-called MF2 or MF3 circuits. While this staged process increases overall recoveries, overgrinding may occur, hence creating problems associated with fine particle flotation. This paper presents an overview of the mineralogy of most of the more significant PGM ores processed in South Africa and the various technologies used in comminution circuits. The paper then summarises the methodology used in flotation circuits to optimise recovery Citation: Corin, K.C.; McFadzean, of fine particles in terms of the collectors, depressants, and frothers used. -
Minerals and Metallurgical Engineering
Course Structure B. Tech. - Minerals and Metallurgical Engineering Applicable to those admitted through JEE from 2019 onwards Department of Fuel, Minerals and Metallurgical Engineering Indian Institute of Technology (ISM) Dhanbad Dhanbad, Jharkhand, India (September - 2019) Page 1 of 41 Course Structure SEMESTER III S. Subject Subject Name Lecture Tutorial Practical Credit Contact No. ID (L) (T) (P) Hours Hours 1 FMC201 Colloids and interfacial 3 0 0 9 3 phenomena 2 FMC202 Heat and mass transfer 3 0 0 9 3 3 FMC203 Physical separation 3 0 0 9 3 processes for coal and minerals 4 FME221 Particle technology (ESO 3 0 0 9 3 1) 5 E/SO 2 E/SO 3 0 0 9 3 6 FMC251 Particle technology 0 0 2 2 2 laboratory 7 FMC252 Physical separation 0 0 2 2 2 processes laboratory Total Credit 49 19 SEMESTER IV S. Subject Subject Name Lecture Tutorial Practical Credit Contact No. ID (L) (T) (P) Hours Hours 1 FMC204 Electrochemistry and 3 0 0 9 3 corrosion 2 FMC205 Thermodynamics and 3 0 0 9 3 kinetics 3 FMC206 Phase transformation and 3 0 0 9 3 heat treatment 4 FMC207 Fine particle processing for 3 0 0 9 3 coal and minerals 5 FME222 Introduction to fuel 3 0 0 9 3 technology (ESO 3) 6 FMC253 Fine particle processing 0 0 2 2 2 laboratory 7 FMC254 Introduction to fuel 0 0 2 2 2 technology laboratory Total Credit 49 19 Page 2 of 41 SEMESTER V S. Subject Subject Name Lecture Tutorial Practical Credit Contact No. -
Evolution of the Isamill™ Into Magnetite Processing
EVOLUTION OF THE ISAMILL™ INTO MAGNETITE PROCESSING Greg Rasmussen, Xstrata Technology Pty Ltd Tommy Do , Ernest Henry Mining Michael Larson, Xstrata Technology Pty Ltd Katie Barns, Xstrata Technology Pty Ltd Xstrata Technology • Mount Isa Mines (MIM), a large Australian mining company, was acquired by Xstrata in 2003 who then merged with Glencore in 2013 • MIM internal technology group was re-named Xstrata Technology (XT) and became an independent technology developer and supplier to the global minerals industry with 250 staff worldwide • The equipment and processes which are marketed by XT are developed in our own operations • XT offers full-package solutions including: • Equipment and processes • Engineering • Commissioning and Training • Dedicated after-market support IsaMill™ Technology Development ™ • Development of IsaMill driven by inability Broken Hill to efficiently treat fine grained orebodies • Late 1980s, Xstrata required 7µm grind for new Pb/Zn orebodies in Australia • Conventional mining technologies tested (1975-1990), but 0 40 micron − Too high power consumption to achieve target size McArthur River − Ball/tower mills ineffective below 20-30μm − Negative influence of steel grinding on flotation 0 40 micron IsaMill™ Technology Development A technology was found... • Horizontal Bead Mills − Used in industries other than mining (pharmaceuticals, paint, food, etc.) − Small, batch scale − Very expensive and exotic media types • Cross-over into mining required: − Much larger scale − Continuous operation − Ability to use cheap, -
Regrinding and Fine Grinding Technology - the Facts and Myths
A review of regrinding and fine grinding technology - the facts and myths Dr Alex Jankovic, Metso Minerals Process Technology Asia-Pacific, [email protected] ABSTRACT Stirred milling technology is used extensively for fine grinding in the ceramic, paint and pharmaceutical industrials. It has been recently adopted by the mining industry. Specific conditions in the mining industry require somewhat different operation of this technology. However, the basic principles of operation are the same and the accumulated knowledge and experience developed in these other industries could be used to assist mining operations to get the most benefit from the stirred milling technology. This paper presents some of the important aspects of stirred milling operation discussed in the literature and not commonly known within the mining industry: grinding media motion, active grinding volume, wear of grinding media and energy transfer, stress intensity, scale-up issues and flow limitations. The intention is to introduce a “different perspective” of stirred milling technology, in particular highlighting its potential benefits and limitations. HISTORY Stirred milling technology may be regarded as relatively new in minerals processing, however it is a mature and extensively used technology in the ceramic, paint and pharmaceutical industries. The latest development of this technology is in the area of “Nano-grinding” for grinding down to nano-sizes. One may say that stirred mills used today in mining and minerals processing are equivalent to the early models of stirred mills used in parallel industries. The most commonly used stirred mills in mining and minerals processing are the VERTIMILL®, STIRRED MEDIA DETRITOR (SMD®) and ISAMILL® and a brief history of their development is given below. -
Isamill™ Technology Used in Efficient Grinding Circuits
1 IsaMill™ Technology Used in Efficient Grinding Circuits B.D. Burford1 and L.W. Clark2 High intensity stirred milling is now an industry accepted method to efficiently grind fine and coarse particles. In particular, the IsaMill™, which was invented for, and transformed the fine grinding industry, is now being included in many new comminution circuits in coarser applications. While comminution has always been regarded as important from a processing perspective, the pressure being applied by environmental concerns on all large scale power users, now make highly energy efficient processes more important than ever. The advantages that were developed in fine grinding in the early IsaMill™ installations have been carried over into coarse grinding applications. These advantages include a simple grinding circuit that operates in open circuit with a small footprint, the ability to offer sharp product size classification, as well as the use of inert media in a high energy intensive environment. This paper will examine the use of IsaMill™ technology in fine grinding (P80 below 15 micron), and examine the use of the technology in conventional grinding applications (P80 20 - 150 µm). Recent installations will be examined, including fine and coarse grinding applications, as well as the recent test work that was undertaken using an IsaMill™ in a primary grinding circuit, and the resulting circuit proposal for this site. While comminution has been relatively unchanged for the last century, the need to install energy efficient technology will promote further growth in IsaMill™ installations, and result in one of the biggest challenges to traditional comminution design. 1. Senior Process Engineer, Xstrata Technology, L4, 307 Queen Street, Brisbane 4000, Qld, Australia 2. -
The Effect of Regrinding Chemistry and Particle Breakage Mechanisms on Subsequent Cleaner Flotation Xumeng Chen Beng and Meng in Materials Engineering
The Effect of Regrinding Chemistry and Particle Breakage Mechanisms on Subsequent Cleaner Flotation Xumeng Chen BEng and MEng in Materials Engineering A thesis submitted for the degree of Doctor of Philosophy at The University of Queensland in November 2014 Sustainable Minerals Institute Julius Kruttschnitt Mineral Research Centre Abstract Regrinding rougher flotation concentrates is typically used to liberate valuable minerals from gangue prior to the cleaner separation stage in processing of low grade ores. Compared to the rougher flotation after primary grinding, it is usually more challenging to achieve a satisfactory performance in post-regrind cleaner flotation especially when fine particles are generated. One main factor which results in this reduction in flotation is the unsuitable particle surfaces produced after regrinding. However, this factor is not usually considered when designing and optimizing the regrinding process. Extensive studies have demonstrated that grinding chemistry can influence mineral floatability. However, earlier studies focused on primary grinding and rougher flotation rather than regrinding and cleaner flotation. In addition, different types of regrind mills are used in industry, and these provide different particle breakage mechanisms which may also influence mineral floatability. Therefore, the overall objective of this thesis study is to investigate the effects of regrinding chemistry and particle breakage mechanisms on the cleaner flotation. The implementation of regrinding in the copper and pyrite flotation circuits at Telfer gold mine was taken as a case study and four research areas were addressed with the objective of developing fundamental understanding to provide practical guidance for the plant operation. The four areas investigated are: 1. Effect of regrinding chemistry on copper activation of pyrite and its flotation; 2. -
Telfer Processing Plant Upgrade – the Implementation of Additional
Telfer Processing Plant Upgrade – The Implementation of Additional Cleaning Capacity and the Regrinding of Copper and Pyrite Concentrates D R Seaman1, F Burns2, B Adamson3, B A Seaman4 and P Manton5 ABSTRACT The Telfer concentrator, located in the Great Sandy Desert of Western Australia, consists of a dual train gold/copper operation processing ore from one underground and, currently, two open pit mines with differing mineralogy. The fl otation circuit of each train was designed to operate in several modes depending on the feed mineralogy. The majority of ore mined at Telfer is processed in a sequential mode where copper minerals are fi rst fl oated into a saleable copper concentrate followed by the fl otation of an auriferous pyrite concentrate which is treated in an on-site hydrometallurgical plant (carbon-in-leach (CIL)). Gold is recovered as a gravity product within the primary grinding circuit, to the copper concentrate, and to a lesser extent, the CIL circuit. Since Telfer was re-opened, with a new concentrator, in 2004, the processing plant has struggled with poor copper concentrate grades, partially due to the excessive entrainment of non-sulfi de gangue minerals in the copper fl otation circuit and, more recently, due to composite copper particles produced when processing ore from a supplementary satellite pit that has not previously been processed through the new Telfer concentrator. Gold recoveries in the CIL circuit have also been below industry standard. This paper presents the implementation of recent changes made to the circuit to address these performance issues. The reconfi guration of the circuit has involved the installation of the following major equipment items: two ISAMills™ in ultra-fi ne grinding applications (one in the copper circuit and one in the pyrite circuit), two Jameson Cells to improve fi ne gangue rejection and a bank of 5 × Outotec TC30s to recovery copper and gold from the reground pyrite stream. -
Xstrata Technology Update Edition 13 – April 2012 Building Plants That Work
xstrata technology update Edition 13 – April 2012 Building plants that work You have to get a lot of things it takes another operator to get them right to build a plant that works. right. Someone who has lived through the problems, had to do the maintenance, operated during a midnight power Of course the big picture must be right – doing the right project, in the right place, failure, cleaned up the spill. Someone at the right time. who has “closed the loop” on previous designs; lived with previous decisions After that, the devil is in the detail. You and improved them, over and over. need a sound design, good execution, good commissioning, and ongoing This is why Xstrata Technology provides support after commissioning. You need a technology “package”. Just as a car to operate and maintain your plant in is more than an engine, technology is the long run, long after the construction more than a single piece of equipment. company has left. That’s when all the Technology is a system. All the elements “little” details become important – how of the system have to work with each easy is it to operate, how good is the other and with the people in the plant. maintenance access, what happens in We want our cars designed by people a power failure, where are the spillage who love cars and driving. So should points and how do we clean them our plants be designed by people with up? Are the instruments reliable and experience and passion to make each is the process control strategy robust one work better than the last. -
Certej Updated Definitive Feasibility Study Summary Technical Report
Certej Updated Definitive Feasibility Study Summary Technical Report Authors:- Patrick Forward February 26th 2009 Neil Liddell Tony Jackson Certej Updated Definitive Feasibility Study Summary Technical Report Contents 3. SUMMARY ................................................................................................................................................................... 1 4. INTRODUCTION AND TERMS OF REFERENCE ................................................................................................................ 6 5. RELIANCE ON OTHER EXPERTS ...................................................................................................................................... 7 6. PROPERTY DESCRIPTION AND LOCATION ..................................................................................................................... 8 7. ACCESSIBILITY, CLIMATE, LOCAL RESOURCES, INFRASTRUCTURE, AND PHYSIOGRAPHY ............................................. 10 7.1. ACCESS ............................................................................................................................................................. 10 7.2. CLIMATE ........................................................................................................................................................... 10 7.3. LOCAL RESOURCES AND INFRASTRUCTURE ....................................................................................................... 10 7.4. PHYSIOGRAPHY ............................................................................................................................................... -
Scale-Up in Froth Flotation: a State-Of-The-Art Review
Scale-up in froth flotation: A state-of-the-art review Diego Mesa∗, Pablo R. Brito-Parada Department of Earth Science and Engineering, Royal School of Mines, Imperial College London, South Kensington Campus, London SW7 2AZ, United Kingdom Abstract Froth flotation has been one of the most important and widely used methods to concentrate minerals since its introduction over a hundred years ago. Over the last few decades, in order to process more mineral while reducing capital costs, flotation equipment has become exponentially larger. The increase in tank volume, however, has brought new challenges in the operation and design of industrial flotation tanks. This review analyses the literature on flotation tank scale-up for the first time, contrasting several techniques and approaches used in both historical and state-of- the-art research. The study of flotation scale-up is crucial for the optimisation of industrial plant performance and the maximisation of laboratory-scale research impact. While important advances in our understanding of flotation have been achieved, large flotation tank design and scale-up has, to a large extent, remained in-house know-how of manufacturing companies. This review of the literature relevant to flotation tank scale-up has resulted in a new classification, dividing the scale-up literature into two main areas of study, namely \Kinetic scale-up" and \Machine design scale-up". This review indicates that current scale-up rules governing the design of flotation tanks focus mainly on pulp zone kinetic parameters and neglect the effects on the froth zone, despite the importance of froth stability and mobility in determining flotation performance. -
Extractive Metallurgy of Copper This Page Intentionally Left Blank Extractive Metallurgy of Copper
Extractive Metallurgy of Copper This page intentionally left blank Extractive Metallurgy of Copper Mark E. Schlesinger Matthew J. King Kathryn C. Sole William G. Davenport AMSTERDAM l BOSTON l HEIDELBERG l LONDON NEW YORK l OXFORD l PARIS l SAN DIEGO SAN FRANCISCO l SINGAPORE l SYDNEY l TOKYO Elsevier The Boulevard, Langford Lane, Kidlington, Oxford OX5 1GB, UK Radarweg 29, PO Box 211, 1000 AE Amsterdam, The Netherlands First edition 1976 Second edition 1980 Third edition 1994 Fourth edition 2002 Fifth Edition 2011 Copyright Ó 2011 Elsevier Ltd. All rights reserved. No part of this publication may be reproduced, stored in a retrieval system or transmitted in any form or by any means electronic, mechanical, photocopying, recording or otherwise without the prior written permission of the publisher Permissions may be sought directly from Elsevier’s Science & Technology Rights Department in Oxford, UK: phone (+44) (0) 1865 843830; fax (+44) (0) 1865 853333; email: permissions@ elsevier.com. Alternatively you can submit your request online by visiting the Elsevier web site at http://elsevier.com/locate/permissions, and selecting Obtaining permission to use Elsevier material Notice No responsibility is assumed by the publisher for any injury and/or damage to persons or property as a matter of products liability, negligence or otherwise, or from any use or operation of any methods, products, instructions or ideas contained in the material herein British Library Cataloguing in Publication Data A catalogue record for this book is available from the British Library Library of Congress Cataloging-in-Publication Data A catalog record for this book is available from the Library of Congress ISBN: 978-0-08-096789-9 For information on all Elsevier publications visit our web site at elsevierdirect.com Printed and bound in Great Britain 11 12 13 14 10 9 8 7 6 5 Photo credits: Secondary cover photograph shows anode casting furnace at Palabora Mining Company, South Africa.