Pioneering Technology
Total Page:16
File Type:pdf, Size:1020Kb
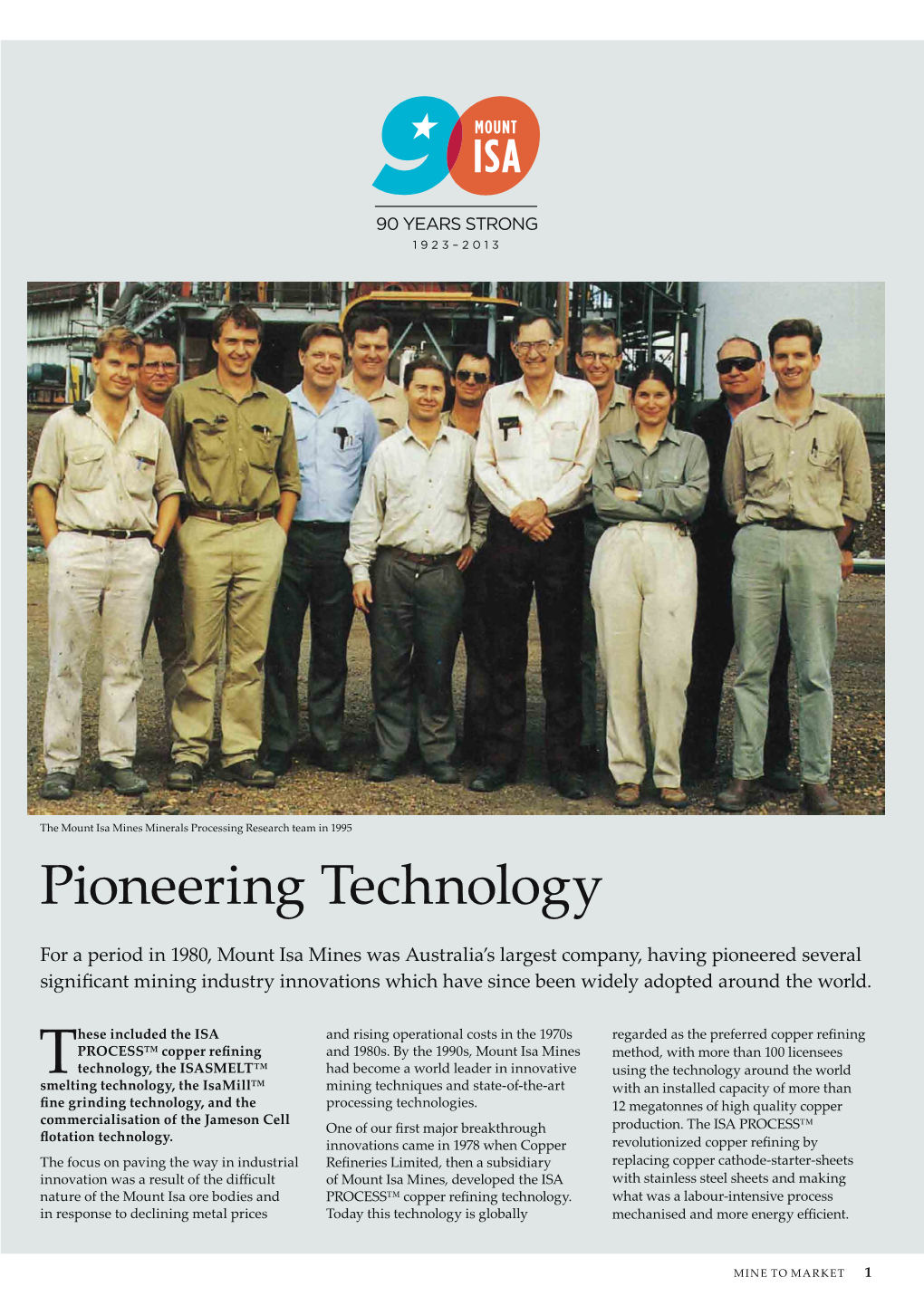
Load more
Recommended publications
-
From Base Metals and Back – Isamills and Their Advantages in African Base Metal Operations
The Southern African Institute of Mining and Metallurgy Base Metals Conference 2013 H. de Waal, K. Barns, and J. Monama From base metals and back – IsaMills and their advantages in African base metal operations H. de Waal, K. Barns, and J. Monama Xstrata IsaMill™ technology was developed from Netzsch Feinmahltechnik GmbH stirred milling technology in the early 1990s to bring about a step change in grinding efficiency that was required to make Xstrata’s fine-grained lead/zinc orebodies economic to process. From small-scale machines suited to ultrafine grinding, the IsaMill™ has developed into technology that is able to treat much larger tonnages, in coarser applications, while still achieving high energy efficiency, suited for coarser more standard regrind and mainstream grinding applications. The unique design of the IsaMillTM, combining high power intensity and effective internal classification, achieves high energy efficiency and tight product distribution which can be effectively scaled from laboratory scale to full-sized models. The use of fine ceramic media also leads to significant benefits in downstream flotation and leaching operations. These benefits are key drivers for the adoption of the technology into processing a diverse range of minerals worldwide, and offer major opportunities for power reduction and improved metallurgy for the African base metal operations. Keywords: IsaMill, regrind, energy efficiency, inert grinding. Introduction The development of the IsaMillTM, by MIM (now GlencoreXstrata) and Netzsch Feinmahltechnik GmbH, was initiated to enable the development of the fine-grained ore deposits at Mt Isa and McArthur River in Northern Australia. To liberate the valuable minerals and so produce a saleable concentrate this ultrafine-grained ore needed to be ground to a P80 of 7 μm. -
Effects of Varied Process Parameters on Froth Flotation Efficiency: a Case Study of Itakpe Iron Ore
Nigerian Journal of Technology (NIJOTECH) Vol. 39, No. 3, July 2020, pp. 807 – 815 Copyright© Faculty of Engineering, University of Nigeria, Nsukka, Print ISSN: 0331-8443, Electronic ISSN: 2467-8821 www.nijotech.com http://dx.doi.org/10.4314/njt.v39i3.21 EFFECTS OF VARIED PROCESS PARAMETERS ON FROTH FLOTATION EFFICIENCY: A CASE STUDY OF ITAKPE IRON ORE S. Akande1, E. O. Ajaka2, O. O. Alabi3 and T. A. Olatunji4,* 1, 2, DEPARTMENT OF MINING ENGINEERING, FEDERAL UNIV. OF TECHNOLOGY, AKURE, ONDO STATE, NIGERIA 3, 4, DEPT. OF MET. & MATERIALS ENGINEERING, FEDERAL UNIV. OF TECHNOLOGY, AKURE, ONDO STATE, NIGERIA Email addresses: 1 [email protected], 2 [email protected], 3 [email protected], 4 [email protected] ABSTRACT The dire need for Itakpe iron ore concentrates of appreciable iron content meets for smelting operation necessitated this study. Core samples of the iron ore sourced from Itakpe, Kogi State, Nigeria were prepared for petrological analysis followed by chemical and particle size analyses. Froth flotation was done using different collectors at varying particle sizes and pH values. Characterization studies carried out revealed that Itakpe iron ore is a lean ore assaying 36.18% Fe2O3 and contains predominantly quartz, sillimanite, and haematite. Its liberation size lies favourably at 75 µm. Processing the ore by froth flotation yielded appreciable enrichment. Optimal recovery (~92%) was achieved using potassium amyl xanthate (PAX) at pH 11 for fine feed sizes (<125 µm) yielding iron concentrate assaying 67.66% Fe2O3. Thus, processing at this set-of- conditions is recommended for the industrial production of more enriched Itakpe iron ore concentrates. -
Orica's Flotation Reagents Increase Copper Recovery Rates, Resulting in a $2M Increase in Gross Revenue
Greater understanding, improved performance Orica’s flotation reagents increase copper recovery rates, resulting in a $2M increase in gross revenue WHO WAS THE CLIENT? combined with sodium isobutyl Xstrata Mount Isa Mines form one xanthate (SIBX). As a result, DSP 330 “The best flotation of the largest underground mining was chosen for plant trial. operations in the world. The plant trial supported the initial performance was The mines, based in North laboratory results, with copper achieved with the Queensland, produce both copper recovery improving by 3%. 50:50 addition ratio and zinc-lead-silver. Established Further laboratory testing and plant in 1924, 5,700 employees and trials conducted by Mount Isa Mines of DSP 330 and contractors today work across found an improvement in overall SIBX, with a copper Xstrata Mount Isa’s twin mining recovery of 3.5%. As a result, and processing streams. DSP 330 was adopted as specialty recovery of 92.4% for collector of choice when treating a head grade of 5.4% WHAT WERE THE CHALLENGES? slow cooled copper slag. Xstrata needed to improve copper and a cut-off copper recovery and called on Orica to WHAT WERE THE KEY grade of 24-25%.” identify and test collectors. OUTCOMES? Orica formulated a collector that would enhance milling and Pengfu Tan, Alberto Galvez, Lucya Yunus– Mount Isa Mines flotation of slow cooled copper slag. Identification of Ultimately, the process needed to achieve superior recovery of copper superior collector at a natural pH over a specific grind fineness. Xstrata’s key requirements were to: Optimised flotation • Identify superior collectors performance • Reduce reagent costs • Optimise flotation performance • Integrate improvements into 3.5% improvement existing operations in copper recovery HOW DID ORICA HELP? Orica developed a laboratory test work program using Xstrata’s current Reduction in performance as a benchmark. -
Softening Behaviour of Lead Sinter and Slag At
Paper Title: THE ISA-YMG LEAD SMELTING PROCESS Paper Presented at: PbZn 2005 Conference, Kyoto, Japan Authors: Bill Errington & Philip Arthur, Xstrata Technology Jikun Wang & Ying Dong, Yunnan Metallurgical Group, Date of Publication: October, 2005 For further information please contact us at [email protected] www.isasmelt.com THE ISA-YMG LEAD SMELTING PROCESS Bill Errington and Philip Arthur Xstrata Technology, Level 4, 307 Queen Street,, Brisbane, Queensland 4000, Australia [email protected] Jikun Wang and Ying Dong Yunnan Metallurgical Group, Kunming,Yunnan, P. R. China ABSTRACT The Yunnan Metallurgical Group (YMG) has constructed a new lead-zinc smelting/refinery complex at Qujing in Yunnan Province, China. The lead smelting process combines an ISASMELT™ smelting furnace with a YMG designed blast furnace. The ISASMELT furnace produces lead bullion plus a high-lead slag that is cast into lump form and fed to the blast furnace. YMG installed a blast furnace in the 1950's to treat high lead slag produced by earlier silver operations. This furnace later treated sinter. For the present project YMG carried out trials at the pilot and commercial scale before deciding on the final blast furnace design. The ISASMELT furnace design was based on the operation of the Lead ISASMELT Plant at Mount Isa. This paper describes the development and the operation of both the ISASMELT furnace and the YMG blast furnace. This combination of new technology and remodelled traditional technology provides an economical solution to achieving an environmentally acceptable lead smelter. Key words: ISASMELT process, lead smelting, lead slag, lead blast furnace www.isasmelt.com 2 INTRODUCTION The new YMG lead smelter forms one part of a new greenfield lead/zinc smelting and refinery complex located at Qujing in Yunnan Province in China. -
Principles of Extractive Metallurgy Lectures Note
PRINCIPLES OF EXTRACTIVE METALLURGY B.TECH, 3RD SEMESTER LECTURES NOTE BY SAGAR NAYAK DR. KALI CHARAN SABAT DEPARTMENT OF METALLURGICAL AND MATERIALS ENGINEERING PARALA MAHARAJA ENGINEERING COLLEGE, BERHAMPUR DISCLAIMER This document does not claim any originality and cannot be used as a substitute for prescribed textbooks. The information presented here is merely a collection by the author for their respective teaching assignments as an additional tool for the teaching-learning process. Various sources as mentioned at the reference of the document as well as freely available material from internet were consulted for preparing this document. The ownership of the information lies with the respective author or institutions. Further, this document is not intended to be used for commercial purpose and the faculty is not accountable for any issues, legal or otherwise, arising out of use of this document. The committee faculty members make no representations or warranties with respect to the accuracy or completeness of the contents of this document and specifically disclaim any implied warranties of merchantability or fitness for a particular purpose. BPUT SYLLABUS PRINCIPLES OF EXTRACTIVE METALLURGY (3-1-0) MODULE I (14 HOURS) Unit processes in Pyro metallurgy: Calcination and roasting, sintering, smelting, converting, reduction, smelting-reduction, Metallothermic and hydrogen reduction; distillation and other physical and chemical refining methods: Fire refining, Zone refining, Liquation and Cupellation. Small problems related to pyro metallurgy. MODULE II (14 HOURS) Unit processes in Hydrometallurgy: Leaching practice: In situ leaching, Dump and heap leaching, Percolation leaching, Agitation leaching, Purification of leach liquor, Kinetics of Leaching; Bio- leaching: Recovery of metals from Leach liquor by Solvent Extraction, Ion exchange , Precipitation and Cementation process. -
Developments in Permanent Stainless Steel Cathodes Within the Copper Industry
DEVELOPMENTS IN PERMANENT STAINLESS STEEL CATHODES WITHIN THE COPPER INDUSTRY K.L. Eastwood and G.W. Whebell Xstrata Technology Hunter Street Townsville, Australia 4811 [email protected] ABSTRACT The ISA PROCESS™ cathode plate is characterised by its copper coated suspension bar, coupled with a blade employing austenitic stainless steel alloy 316L. The blade material has become the mainstay of the technology and has been closely copied by competing cathode designs. Improvement to the cathode plate design remains a key area for research, and ongoing developments by Xstrata Technology’s ISA PROCESS™ have recently been commercialised. Two such developments are the ISA Cathode BR™ and ISA 2000 AB Cathode. The ISA BR cathode is a lower resistance cathode that has proven to enhance operating efficiencies. The AB cathode was designed to improve stripping inefficiencies in the ISA 2000 technology. These developments have now had time to mature and their long term performance will be discussed. Rising material costs and the desire to extend the operating boundaries of the standard 316L cathode plate has triggered a number of significant advances. These involve the use of different stainless steels as alternatives in some operational situations. The technical aspects and results of commercial trials on this development will also be discussed in this paper. INTRODUCTION The introduction of permanent stainless steel cathode technology was pioneered in the copper industry by IJ Perry and colleagues in 1978, with the introduction of the ISA PROCESSTM in the Townsville Copper Refinery, Perry [1]. While a number of parallel processes have emerged since its introduction, ISA Process Technology (IPT) has continued to be the mainstay electrolytic copper process with consistent improvements and superior operational performance. -
Calcium-Looping Performance of Steel and Blast Furnace Slags for Thermochemical Energy Storage in Concentrated Solar Power Plants
View metadata, citation and similar papers at core.ac.uk brought to you by CORE provided by idUS. Depósito de Investigación Universidad de Sevilla Calcium-Looping performance of steel and blast furnace slags for Thermochemical Energy Storage in Concentrated Solar Power plants Jose Manuel Valverde a*, Juan Miranda-Pizarroa,c, Antonio Perejónb,c, Pedro E. Sánchez-Jiménezc, Luis A. Pérez-Maquedac aFacultad de Fisica, Universidad de Sevilla, Avenida Reina Mercedes s/n, 41012 Sevilla, Spain. bDepartamento de Química Inorgánica, Facultad de Química, Universidad de Sevilla, C. Prof. García González 1, Sevilla 41071, Spain. cInstituto de Ciencia de Materiales de Sevilla (C.S.I.C. - Universidad de Sevilla). C. Américo Vespucio 49, Sevilla 41092, Spain. Abstract The Calcium Looping (CaL) process, based on the carbonation/calcination of CaO, has been proposed as a feasible technology for Thermochemical Energy Storage (TCES) in Concentrated Solar Power (CSP) plants. The CaL process usually employs limestone as CaO precursor for its very low cost, non-toxicity, abundance and wide geographical distribution. However, the multicycle activity of limestone derived CaO under relevant CaL conditions for TCES in CSP plants can be severely limited by pore plugging. In this work, the alternative use of calcium-rich steel and blast furnace slags after treatment with acetic acid is investigated. A main observation is that the calcination temperature to regenerate the CaO is significantly reduced as compared to limestone. Furthermore, the multicycle activity of some of the slags tested at relevant CaL conditions for TCES remains high and stable if the treated samples are subjected to filtration. This process serves to remove silica grains, which helps decrease the porosity of the CaO resulting from calcination thus mitigating pore plugging. -
Grained Pyrite in the Mount Isa Copper System
Trace Element Variation of Coarse- Grained Pyrite in the Mount Isa Copper System Thesis submitted in accordance with the requirements of the University of Adelaide for an Honours Degree in Geology Shauna Maguire-Olstad November 2016 Shauna Maguire-Olstad Mt. Isa Coarse-grained Pyrite TRACE ELEMENT VARIATIONOF COARSE-GRAINED PYRITE IN THE MOUNT ISA COPPER SYSTEM MT.ISA COARSE-GRAINED PYRITE ABSTRACT The unique Mount Isa system, northwest Queensland, contains two world class deposits of copper and lead-zinc, which have a complex spatial relationship. The formation of the copper mineralization has long been debated, and occurs in a close spatial and temporal association with silica-dolomite alteration and coarse-grained pyrite (Pyrite 2). The geochemical characteristics of coarse-grained pyrite has not previously been studied and it is believed to hold valuable insight into the fluid evolution of the Mount Isa Copper System. Using LA-ICP-MS analysis, trace element variation of Pyrite 2 was investigated for numerous elements including Ag, As, Ba, Co, Cu, Mo, Ni, Pb and Zn across an explorative transect (drill hole 0406ED2), which passed through the alteration halo of the 1100 orebody. The trace element composition of Pyrite 2 was not consistent throughout the 0406ED2 transect and it does not appear to be controlled by host lithology. The analysis determined the Pyrite 2 grains formed during, or in close association with, the ore-mineral enriched hydrothermal fluid. Pyrite 2 data is consistent with the Mount Isa system having undergone multiple hydrothermal fluid events or from an evolving hydrothermal fluid. The trace element variation of Pyrite 2 is consistent with the currently established paragenesis and is indicative of the concurrent Cu, Pb and Zn mineralising system formed during protracted hydrothermal events. -
Challenges Related to the Processing of Fines in the Recovery of Platinum Group Minerals (Pgms)
minerals Review Challenges Related to the Processing of Fines in the Recovery of Platinum Group Minerals (PGMs) Kirsten C. Corin 1,* , Belinda J. McFadzean 1, Natalie J. Shackleton 2 and Cyril T. O’Connor 1 1 Centre for Minerals Research, Chemical Engineering Department, University of Cape Town, P Bag X3, Rondebosch, Cape Town 7700, South Africa; [email protected] (B.J.M.); [email protected] (C.T.O.) 2 Minerals Expertise Tech Pty Ltd., Germiston 2007, South Africa; [email protected] * Correspondence: [email protected] Abstract: In order to increase the recovery of PGMs by flotation, it is necessary to optimise the liberation of the key minerals in which the platinum group elements (PGEs) are contained which include sulphides, arsenides, tellurides, and ferroalloys among others, while at the same time ensuring the optimal depression of gangue minerals. In order to achieve this, comminution circuits usually consist of two or three stages of milling, in which the first stage is autogeneous, followed by ball milling. Further liberation is achieved in subsequent stages using ultra-fine grinding. Each comminution stage is followed by flotation in the so-called MF2 or MF3 circuits. While this staged process increases overall recoveries, overgrinding may occur, hence creating problems associated with fine particle flotation. This paper presents an overview of the mineralogy of most of the more significant PGM ores processed in South Africa and the various technologies used in comminution circuits. The paper then summarises the methodology used in flotation circuits to optimise recovery Citation: Corin, K.C.; McFadzean, of fine particles in terms of the collectors, depressants, and frothers used. -
Choosing & Using a Milling Machine
CHOOSING & USING A MILLING MACHINE Bench mill vs. Knee mill? There are similarities between ALL small vertical milling Variable machines and the traditional drill press, right: speed drive 1. A vertically-movable quill which encloses the spindle. 2. A drill press lever which propels the quill downward. Head- 3. A quill clamp to lock the quill firmly in position. stock 4. A variable-speed spindle drive system. Quill 5. A headstock that can be moved up or down on a clamp vertical column. Quill Feature (5) applies only to bench mills, but check for Drill Column press this important difference: Many, but not all, bench mills lever have dovetails for headstock height adjustment, not round columns — see next page. Table Every vertical mill is a part-time drill press, but there’s more to it than that. Comparing mills with drill presses, here are the KEY DIFFERENCES: 1. Massive, rigid construction, a lot more cast iron. 4. A mill spindle is designed for both down load (axial, like a 2. Heavy T-slotted movable table on dovetail ways, with ± drill press), and also side load (radial). That is why a mill 0.0005″ position measurement capability (optional 2- or spindle runs in tapered roller bearings (or deep-groove ball 3-axis DRO). bearings) inside the quill. 3. The workpiece doesn’t slide on the mill table: instead it is 5. The spindle isn’t just for drill chucks — use any R8 com- firmly clamped to the table, which moves left-to-right and patible device — end mill holders, collets, slitting saws, etc. -
Minerals and Metallurgical Engineering
Course Structure B. Tech. - Minerals and Metallurgical Engineering Applicable to those admitted through JEE from 2019 onwards Department of Fuel, Minerals and Metallurgical Engineering Indian Institute of Technology (ISM) Dhanbad Dhanbad, Jharkhand, India (September - 2019) Page 1 of 41 Course Structure SEMESTER III S. Subject Subject Name Lecture Tutorial Practical Credit Contact No. ID (L) (T) (P) Hours Hours 1 FMC201 Colloids and interfacial 3 0 0 9 3 phenomena 2 FMC202 Heat and mass transfer 3 0 0 9 3 3 FMC203 Physical separation 3 0 0 9 3 processes for coal and minerals 4 FME221 Particle technology (ESO 3 0 0 9 3 1) 5 E/SO 2 E/SO 3 0 0 9 3 6 FMC251 Particle technology 0 0 2 2 2 laboratory 7 FMC252 Physical separation 0 0 2 2 2 processes laboratory Total Credit 49 19 SEMESTER IV S. Subject Subject Name Lecture Tutorial Practical Credit Contact No. ID (L) (T) (P) Hours Hours 1 FMC204 Electrochemistry and 3 0 0 9 3 corrosion 2 FMC205 Thermodynamics and 3 0 0 9 3 kinetics 3 FMC206 Phase transformation and 3 0 0 9 3 heat treatment 4 FMC207 Fine particle processing for 3 0 0 9 3 coal and minerals 5 FME222 Introduction to fuel 3 0 0 9 3 technology (ESO 3) 6 FMC253 Fine particle processing 0 0 2 2 2 laboratory 7 FMC254 Introduction to fuel 0 0 2 2 2 technology laboratory Total Credit 49 19 Page 2 of 41 SEMESTER V S. Subject Subject Name Lecture Tutorial Practical Credit Contact No. -
Evolution of the Isamill™ Into Magnetite Processing
EVOLUTION OF THE ISAMILL™ INTO MAGNETITE PROCESSING Greg Rasmussen, Xstrata Technology Pty Ltd Tommy Do , Ernest Henry Mining Michael Larson, Xstrata Technology Pty Ltd Katie Barns, Xstrata Technology Pty Ltd Xstrata Technology • Mount Isa Mines (MIM), a large Australian mining company, was acquired by Xstrata in 2003 who then merged with Glencore in 2013 • MIM internal technology group was re-named Xstrata Technology (XT) and became an independent technology developer and supplier to the global minerals industry with 250 staff worldwide • The equipment and processes which are marketed by XT are developed in our own operations • XT offers full-package solutions including: • Equipment and processes • Engineering • Commissioning and Training • Dedicated after-market support IsaMill™ Technology Development ™ • Development of IsaMill driven by inability Broken Hill to efficiently treat fine grained orebodies • Late 1980s, Xstrata required 7µm grind for new Pb/Zn orebodies in Australia • Conventional mining technologies tested (1975-1990), but 0 40 micron − Too high power consumption to achieve target size McArthur River − Ball/tower mills ineffective below 20-30μm − Negative influence of steel grinding on flotation 0 40 micron IsaMill™ Technology Development A technology was found... • Horizontal Bead Mills − Used in industries other than mining (pharmaceuticals, paint, food, etc.) − Small, batch scale − Very expensive and exotic media types • Cross-over into mining required: − Much larger scale − Continuous operation − Ability to use cheap,