Unit 2 Excavation Equipment-11
Total Page:16
File Type:pdf, Size:1020Kb
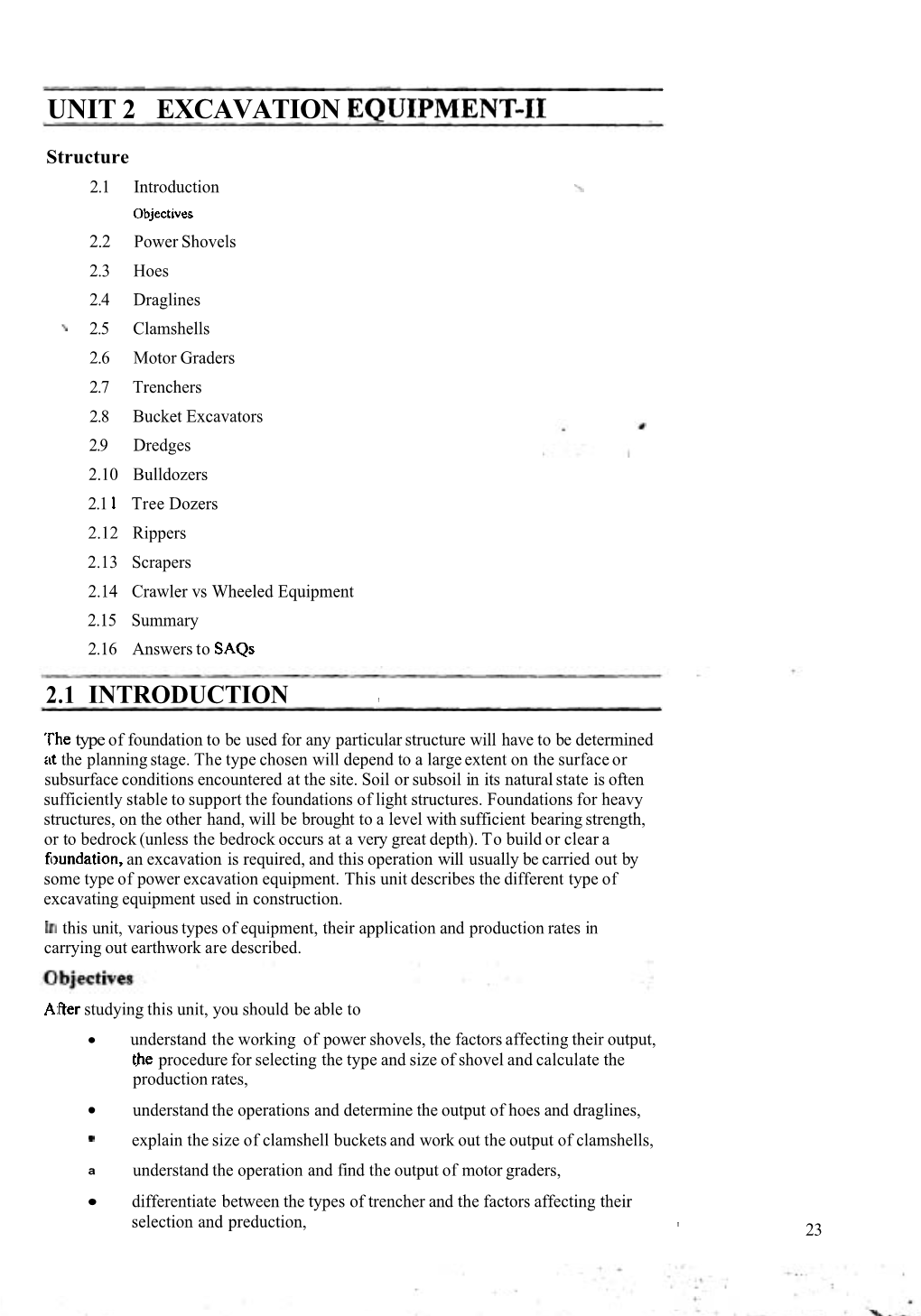
Load more
Recommended publications
-
~ Coal Mining in Canada: a Historical and Comparative Overview
~ Coal Mining in Canada: A Historical and Comparative Overview Delphin A. Muise Robert G. McIntosh Transformation Series Collection Transformation "Transformation," an occasional paper series pub- La collection Transformation, publication en st~~rie du lished by the Collection and Research Branch of the Musee national des sciences et de la technologic parais- National Museum of Science and Technology, is intended sant irregulierement, a pour but de faire connaitre, le to make current research available as quickly and inex- plus vite possible et au moindre cout, les recherches en pensively as possible. The series presents original cours dans certains secteurs. Elle prend la forme de research on science and technology history and issues monographies ou de recueils de courtes etudes accep- in Canada through refereed monographs or collections tes par un comite d'experts et s'alignant sur le thenne cen- of shorter studies, consistent with the Corporate frame- tral de la Societe, v La transformation du CanadaLo . Elle work, "The Transformation of Canada," and curatorial presente les travaux de recherche originaux en histoire subject priorities in agricultural and forestry, communi- des sciences et de la technologic au Canada et, ques- cations and space, transportation, industry, physical tions connexes realises en fonction des priorites de la sciences and energy. Division de la conservation, dans les secteurs de: l'agri- The Transformation series provides access to research culture et des forets, des communications et de 1'cspace, undertaken by staff curators and researchers for develop- des transports, de 1'industrie, des sciences physiques ment of collections, exhibits and programs. Submissions et de 1'energie . -
Department of the Interior
DEPARTMENTOF THE INTERIOR UNITED STATES BUREAU OF MINES JOHNW. FINCH*DIRCC~OFI INFORMATION CIRCULAR - PLACER MINING IN THE WESTERN UNlTED STATES - - PART Ill. DREDGING AND OTHER FORMS OF MECHANICAL. HANDLING OF GRAVEL, AND DRIFT MINING 1 I . .C. 6788. February 1935 Part I11 . .Dredeing and Other Forms of Mechanical Handling of Eravel . and Drift Miniqg CONTENTS Introduction ....................................................................................:..................... Acknowledgments ..................................................................:................................. Excavating by teams or power equipment ...................................................... General statement...................................................................................... Team or traotors...................................................................................... Teams .................................................................................................... Tractors.............................................................................................. Scrapers and hoists.................................................................................. Drag scrapers...... : ............................................................................. Slaokline on oablewags .................................................................. Power shovels and draglines.................................................................. Stationary washing plants........................................................... -
Dragline Dredging Methods
BRITISH COLUMBIA DEPARTMENT OF MINES Hon.HERBERT ANSCOMB, Minister JOHN F. WALKER, Deputy Minister BULLETIN No. 16 DraglineDredging Methods Compiled by STUART S. HOLLAND 1942 This Bulletin is in large part a reprint from United States Bureau of Mines Information Circular 7013 VICTOIIIA, R.C.: Photoaffset by CH~LESF. BANPI~U).Printer to the King's Most Excellent Majsty. 1042. CONTEPJTS Page ' HISTORY AND DEVELOP1IZNT ..................................................................................................................................................................... 1 n LINITATIONS 'OF M~THOD................. 1............................................................... :........................................................................................... ' 5 Values ....................................................................................................... ......................................................................................................... 6 Depth .................................................................. ..... ............................................................................................................................. .. 6 7 Bottom ....................................................................................................................................................................................................................... Character of thegravel ............................................................................................................................................... -
Mines Regulations, 2018, S-15.1 Reg 8
1 MINES, 2018 S-15.1 REG 8 The Mines Regulations, 2018 being Chapter S-15.1 Reg 8 (effective April 6, 2019). NOTE: This consolidation is not official. Amendments have been incorporated for convenience of reference and the original statutes and regulations should be consulted for all purposes of interpretation and application of the law. In order to preserve the integrity of the original statutes and regulations, errors that may have appeared are reproduced in this consolidation. 2 S-15.1 REG 8 MINES, 2018 3 MINES, 2018 S-15.1 REG 8 Table of Contents PART 1 5-15 Report by professional engineer Preliminary Matters 5-16 Information re hazards 1-1 Title 5-17 Controlling movement of strata 1-2 Definitions 5-18 Determination of surface subsidence 1-3 Application of these regulations 5-19 Prevention of inrush 1-4 Application of OHS regulations to mines PART 6 PART 2 Design of mines General Notice Requirements DIVISION 1 2-1 Commencement of work, intended installation General 2-2 Dangerous occurrences 6-1 Change and shower facilities PART 3 6-2 Fixed ladders underground Plans and Records 6-3 Wire rope or chain ladders 3-1 Preparation of plans 6-4 Stairways 3-2 Marking current progress DIVISION 2 3-3 Annual submission of certified copies Underground Mines 3-4 Monthly statistics 6-5 Application of Division 3-5 Electronic log or records 6-6 Design of mine 3-6 Entries in log books, records 6-7 Tailings containing cyanide prohibited 3-7 Record retention 6-8 Exits to surface PART 4 6-9 Exits underground Supervision of Workers 6-10 Marking exits, etc. -
Drilling Tools,Wellhead Tools
矿 业工程专业词汇英语翻2-298 译 钻299-309 井常用对 话 钻 具,井口工具,打捞工310-311 具 石 油钻井业常用专业词312-336 汇 输 出电动钻机词汇表(钻井337-350 机 方面) www.chinatungsten.com 1 矿业工程专业词汇英语翻译 abandoned workings 废巷道 abandonment 废弃 abelite 阿贝立特炸药 abichite 砷铜矿 ability 能力 ability to flow 怜性 ablation 水蚀 ablution 洗净 abnormality 反常 abrasion 磨损 abrasion resistance 抗磨蚀能力 abrasive 磨料 abruption 断层 abscissa 横座标 absite 钍钛铀矿 absolute error 绝对误差 absolute humidity 绝对温度 absorbability 吸收性 www.chinatungsten.com absorbent 吸收剂 absorber 吸收器吸收剂;减震器 absorbing ability 吸收性 absorption 吸收 absorption factor 吸收系数 absorption meter 液体溶气计 absorptivity 吸收性 absortion constant 吸收常数 abstraction of pillars 回采煤柱 abundance 丰富 abundant 富有的 abutment 拱座 abutment area 支承压力带 abutment pressure 支承压力 accelerated motion 加速运动 accelerating agent 速凝剂 acceptance test 验收试验 acceptor charge 被动装药 accessory equipment 补助设备 accessory minerals 副矿物 accidental explosion 意外爆炸 acclivity 上倾 accompanying bed 伴生层 accoustic signal 音响信号 accretion 表土 2 accumulation 蓄积 accumulator 蓄电池 accumulator capacity 蓄电池容量 accumulator lamp 蓄电池灯 accumulator locomotive 蓄电池机车 accuracy 精度 accuracy degree 精确度 acetate 醋酸盐 acetic acid 醋酸 aceton 丙酮 acetonitrile 乙腈 acetyl 乙酰 acetylene 乙炔 acetylene lamp 电石灯 achromatic 消色差的 aciculite 针状矿石 acid 酸 acid mine water 酸性矿水 acid number 酸值 www.chinatungsten.com acid proof 酎酸的 acid resistance 耐酸性 acid resistant 耐酸的 acid resistant steel 耐酸钢 acid resisting steel 耐酸钢 acid rock 酸性岩 acid treatment of a bore hole 钻孔酸处理 acid value 酸值 acidite 酸性岩 acidity 酸度 acidness 酸度 acidproof 耐酸的 actinium 锕 actinolite 阳起石 action radius 酌半径 activate 活化 activated -
Mechanical and Electrical Design of Power Excavators (Paper & Discussion)
DESIGN OF POWER EXCAVATORS. 41 PAPER MECHANICAL AND ELECTRICAL DESIGN OF POWER EXCAVATORS. By T. W. Fairhurst. JUSTIFICATION FOR USE OF POWER EXCAVATORS. The power excavator owes its original existence, and sub- sequent widespread use, to the fairly obvious fact that the great and small earth and mineral moving projects of the world could never be carried out economically by manual la- bour, even if such labour were available in ample quantity. Irrigation and reclamation works, construction of railways, docks, harbours, etc., open-strip mineral mining, quarry work- ing, as well as large and small contracting works have been rendered possible to their present extent only by the power excavator. HISTORY OF POWER EXCAVATION. The detailed history of power excavators is material for several volumes, and it is, therefore proposed to refer to this history only in such a way as to give a sound general impres- sion of the course of development. Prior to 1836 a very crude single steam engined digger was produced by one Otis, of Philadelphia, U.S.A., for work on the first American railroad construction between Albany and Schenectady, in N.Y. State. This . machine, although. crude. clumsy and slow, quite justified its existence and did considerable excavation at much lower cost than equivalent hand labour. Between this time and about 1875 several steam exca- vators were built in America, and, it is believed, one or two were tried in Europe with very indifferent success. The American-built machines, about twelve in number, all did fair work on the Erie Canal and other jobs, but, owing to the high-handed attitude of the manufacturers, few customers were obtained or retained. -
Technical and Economical Optimization Of
Technical and economical optimization of surface mining processes – Development of a data base and a program structure for the computer-based selection and dimensioning of equipment in surface mining operations Dissertation zur Erlangung des Grades eines Doktor-Ingenieurs vorgelegt von M.Sc. Raheb Bagherpour Aus dem Iran Genehmigt von der Fakultät für Energie- und Wirtschaftswissenschaften der Technischen Universität Clausthal Tag der mündlichen Prüfung 17.09.2007 Vorsitzende: Prof.Dr. Heike. Y. Schenk-Mathes Hauptberichterstatter: Prof. Dr.-Ing. habil. H. Tudeshki Berichterstatter: Prof. Dr.-Ing. Oliver Langefeld Contents Contents .........................................................................................................................I Figures List .................................................................................................................. IV Tables List.................................................................................................................... VI 1 Introduction...................................................................................................1 2 Mining Industry Progresses ........................................................................3 2.1 The History of Mining......................................................................................3 2.2 Mining and Mineral Description ......................................................................4 2.3 Mining Technology Progresses.......................................................................5 -
Download at Soneticscorp.Com/Listen-Through-Public-Works
digdifferent.com JULY 2021 DIFFERENTThink outside the bucket digVacuum Excavation DIRECTORY 24 SMART BUSINESS: TIME TO TAKE ADVANTAGE OF LOW-INTEREST BUSINESS LOANS 40 GROWTH SPURT Company’s quick expansion triggered by small hydrovac units 12 SAFETY FIRST: NO CUTTING CORNERS ON TRENCH SAFETY 18 work simple, work safe, work smart safe digging made easy A dedicated brand of hydro and air excavators manufactured by Learn Vactor® Mfg., Inc. with a variety of training, service and support More options available. today TRUVA C.COM ©2021 Vactor Mfg., Inc. All Rights Reserved. IMPROVE SITUATIONAL AWARENESS & STAY ALERT TO POTENTIAL HAZARDS AROUND YOU Get the Sonetics Infographic Download at soneticscorp.com/listen-through-public-works Learn how Listen-Through Technology improves jobsite safety for public works crews. digdifferent.com July 2021 3 Contents Think outside the bucket digDIFFERENT JULY 2021 FOCUS: Vacuum Excavation ON THE COVER: COVER STORY Torovac operator Bruno Cornacchia, left, 12 PROFILE: VACUUM EXCAVATION and Byron Mifsud, crewman, work on a job site Growth Spurt in Pickering, Ontario, where they are exposing for utilities. Torovac Services, based in Toronto, City-suitable trucks, social-media was founded in 2019 by Frank Rotundo and marketing trigger quick expansion Bento Soares and now has six employees and for Toronto company. serves the greater Ontario region. (Photography By Ken Wysocky by Bruce Bell) FEATURES 40 SMART BUSINESS: Look Before You Leap 22 Dig My Rig A low-interest loan can help you We feature Mack Construction expand your business in multiple Services, Sherwood Park, ways, but there are always risks Alberta, Canada. to consider. -
Steam Shovel (Edited from Wikipedia)
Steam Shovel (Edited from Wikipedia) SUMMARY A steam shovel is a large steam-powered excavating machine designed for lifting and moving material such as rock and soil. It is the earliest type of power shovel or excavator. They played a major role in public works in the 19th and early 20th century, being key to the construction of railroads and the Panama Canal. The development of simpler, cheaper diesel-powered shovels caused steam shovels to fall out of favor in the 1930s. HISTORY The steam shovel was invented by William Otis, who received a patent for his design in 1839. Officially the patent drawing is missing but a drawing exists which is said to be the one from the patent and this shows the crane mounted on a railroad car. A load of earth could be lifted by the bucket, raised by the crane and turned to be dumped, such as in railcars. The patent described how a steam engine of a type then in ordinary use, was installed with a power control mechanism for the crane, and a system of pulleys to move its arms and bucket. It could move about 380 cubic meters of earth a day, with its 1.1 cubic meter capacity shovel and 180° slewing wooden jib. It was first used on the Western Railroad in Massachusetts. Otis was born on September 20, 1813, in Pelham, Massachusetts. He was a cousin of Elisha Otis of elevator fame. At an early age, William was interested in earthworks and mechanics. At the age of 22, he had shown an uncommon mechanical ingenuity and created the first steam powered mechanical excavator. -
(MSHA) Was Formed
Visit the Mine Safety and Health Administration website at www.msha.gov Catalog of Training Products for the Mining Industry U. S. Department of Labor Elaine L. Chao Secretary Mine Safety and Health Administration National Mine Health and Safety Academy THIS PAGE INTENTIONALLY LEFT BLANK TABLE OF CONTENTS Information and Products ........................................................... iii Información Y Productos ........................................................... iv Other Sources of Training Materials .................................................. v Multimedia Training Materials....................................................... 1 Computer CDs ................................................................. 2 DVDs ........................................................................ 7 Videotapes (VHS)............................................................... 35 Historical Videos ............................................................... 45 Training Materials................................................................. 53 Historical Training Materials ...................................................... 91 Pocket Cards ..................................................................... 95 NIOSH Materials ................................................................. 101 Index (By Subject) ................................................................ 125 Index (By Title) .................................................................. 137 Índice (Por Título) ............................................................... -
CHAPTER ONE 1. Introduction 1.1 General
CHAPTER ONE 1. Introduction 1.1 General Construction equipment is one of the three major inputs of the building construction process, together with labors and materials. One of the development and use of equipment with construction is, to enable construction activities to be performed which are beyond the limit of human strength, and to achieve high standards, which is required by current construction technologies and design . The second one is to make the construction process more economics . Construction of projects requires heavy equipment or ‘‘big iron’’ to assist many of the work activities. At the start of the 21st century, construction accounted for approximately 10% of the U.S. gross national product and employed approximately 4.5 million people. Heavy construction equipment is one of the primary reasons that construction has reached this status. In fact, the role of heavy construction equipment today is mission critical and indirectly influences the quality of our lives everyday. Heavy construction work typically requires high-volume or high-capacity equipment. These requirements are typically driven by the large amount of work to be done and the amount of time to complete it. This work can further be classified by whether the construction is vertical or horizontal. Vertical construction typically requires less surface work, earth moving, and excavating and more lifting. Horizontal construction typically requires more surface work and limited lifting. 1 Today contractors undertake many types of construction activities that require different types, sizes, and groupings of equipment for earth moving, excavating, and lifting. There is a piece of equipment for practically any work activity, large or small. -
Section 8 Coding Manual
SECTION 8 CODING MANUAL TABLE OF CONTENTS Page SECTION 8. CODING MANUAL 8.1 Introduction ...............................................................................................................................8-1 8.2 Mining Machines.......................................................................................................................8-1 8.3 Trade Names of Equipment.......................................................................................................8-5 8.4 All Mine Occupations .............................................................................................................8-11 All Mine Occupations - Metal/Nonmetal and Coal ................................................................8-12 (Numerical Listing) Coal and Metal/Nonmetal Occupations ................................................8-23 8.5 Degree of Injury ......................................................................................................................8-30 8.5.1 Degree 1 (Fatal)...........................................................................................................8-31 8.5.2 Degree 2 (Permanent-total or partial disability)..........................................................8-31 8.5.3 Degree 3 (Days away from work only).......................................................................8-31 8.5.4 Degree 4 (Days away from work and days of restricted activity)...............................8-32 8.5.5 Degree 5 (Days of restricted work activity only)........................................................8-32