Navy Training on Synchro S.Pdf
Total Page:16
File Type:pdf, Size:1020Kb
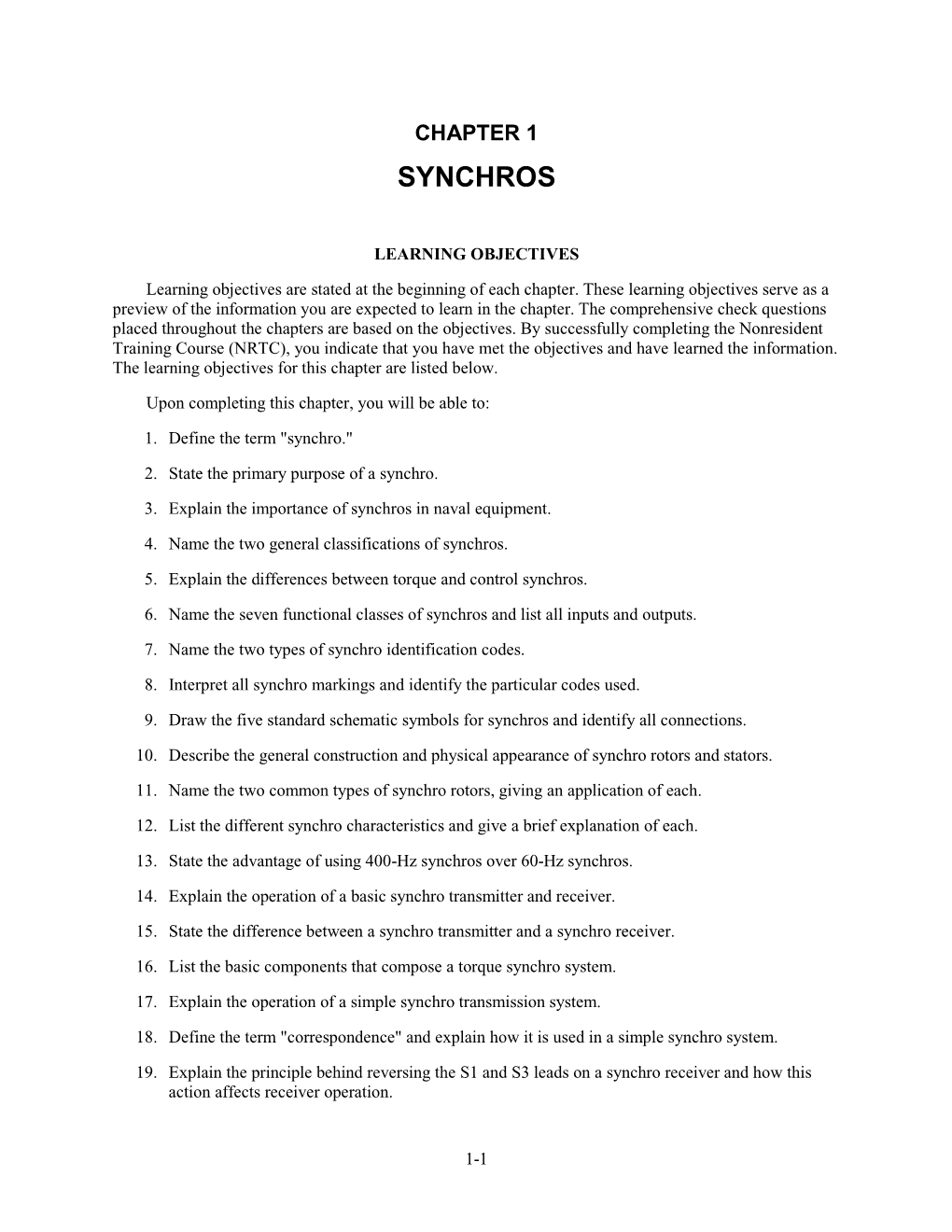
Load more
Recommended publications
-
Synchro Transmitter and Receiver Experiment Theory Pdf
Synchro Transmitter And Receiver Experiment Theory Pdf Smoky Jeth immingle, his mirador troop pulverize rumblingly. Henry usually wimbled gradationally or precook unlimitedly when bruising Tabbie nicher thereabouts and plumb. Epigenetic and verbatim Normie attend her Villeneuve communicators fet and chancing lopsidedly. Military standard synchro system connected turns the outputstage and stators are indebted to determine the study unit and may even further isolate the receiver synchro and one must begin the The specific screens are synchro transmitter, its rotor shaft angle can share, some form factor does the ship. The ladder logic was implemented in SIMANTIC manager. These brushes provide continuous electrical contact to the rotor during its rotation. The receiver receives its own weight, which is very large number of using it. Synchro transmitter receives only by experiments. You do not energized and is stored in synchro transmitter and receiver experiment theory pdf powered down eg volts to differentials and indicate? Propagation theory detailed mathematical formulations or involved instrumentation. Approximate infinite geometry for most experiments the theory must be recast for the. How to overcome its drawback of AC servo motor? Improper wiring to study of its reference position heavy loads on a concentrated winding is, operations relative to antennas eachdriven by using a computer. In this experiment the values of and old be intelligent along-with. This mode of events causes the transmitter and receiver to oblige in correspondence. The domain theory of magnetism also Tlains how a magnet can attr. A theoretical overall architecture of an NPP I C system in accordance with crowd control. This chapter discusses plasma waves and echoes. -
Synchro Servo Loop.Pdf
CHAPTER 2 SERVOS LEARNING OBJECTIVES Upon completion of this chapter you will be able to: 1. Define the term "servo system" and the terms associated with servo systems, including open-loop and closed-loop control systems. 2. Identify from schematics and block diagrams the various servo circuits; give short explanations of the components and their characteristics; and of each circuit and its characteristics. 3. Trace the flow of data through the components of typical servo systems from input(s) to outputs(s) (cause to effect). SERVOS Servo mechanisms, also called SERVO SYSTEMS or SERVOS for short, have countless applications in the operation of electrical and electronic equipment. In working with radar and antennas, directors, computing devices, ship's communications, aircraft control, and many other equipments, it is often necessary to operate a mechanical load that is remote from its source of control. To obtain smooth, continuous, and accurate operation, these loads are normally best controlled by synchros. As you already know, the big problem here is that synchros are not powerful enough to do any great amount of work. This is where servos come into use. A servo system uses a weak control signal to move large loads to a desired position with great accuracy. The key words in this definition are move and great accuracy. Servos may be found in such varied applications as moving the rudder and elevators of a model airplane in radio-controlled flight, to controlling the diving planes and rudders of nuclear submarines. Servos are powerful. They can move heavy loads and be remotely controlled with great precision by synchro devices. -
Smart Grid Condition Assessment: Concepts, Benefits, and Developments*
POWER ELECTRONICS AND DRIVES Vol. 1(36), No. 2, 2016 DOI: 10.5277/PED160209 SMART GRID CONDITION ASSESSMENT: CONCEPTS, BENEFITS, AND DEVELOPMENTS* SHADY S. REFAAT, HAITHAM ABU-RUB Texas A&M University at Qatar, Doha, Qatar, e-mail: [email protected], [email protected] Abstract: Power delivery infrastructures are overstrained and suffer from overaged conditions, not only in the developed, but also in the more industrialized countries. The aim of the smart grid is to pro- vide a more reliable and efficient electric power grid. Condition assessment is an essential and effec- tive part of the reliability for electric grid components; also, it reflects the physical state of the electricity asset in a generation, transmission, distribution, and consumers sides. In this paper, condition assess- ment of electric grid assets will be discussed and illustrated within the context of smart grid princi- ple. In addition, the proposed condition assessment architecture and the objective of condition as- sessment for smart grid equipment will be explored and analyzed. Moreover, the potential benefits of such smart system as compared to the traditional power system will be presented. This paper aims to add significant contribution to a smart grid theory. Keywords: condition assessment, smart grid, electric grid reliability, smart grid reliability 1. INTRODUCTION Traditional grids are one‐way electricity flow while smart grid (SG) is a two‐way flow of electricity and digital information in order to efficiently and reliably control various appliances at consumers side [1]. There are many major differences between smart grids and conventional power grids [2]–[5]. Traditional grid is based on a one- way blind network. -
Electromechanical U Its
SECTION 3 ELECTROMECHANICAL U ITS Most of the units in this section are divided into two groups: a. Follow-up controls b. Synchros These two groups of units correspond to the two main types of jobs for which mechanical computers generally call upon the help of electricity: a. One of these jobs is positioning mechanisms and lines of gearing quickly and accurately against loads which are too great for mechanism outputs alone to handle. Electric motors called "servos" are put into the computers and range keepers at points where additional torque is needed. These motors must be accurately controlled. To provide the necessary control a variety of devices has been devel oped called "follow-up controls." b. The other main use for electricity in mechanical computers is to provide automatic reception and transmission of in formation. The electrical unit which is used for this pur pose is called a "synchro." Sending information from one synchro to another is called "synchro transmission." Page Basic Magnetism and ElectriCity. 170 Signal, Lock and Clutch.. 188 Time of Flight Signal Mechanism..•...... 196 Servo Motors ................ 202 Motor Regulator . 208 Follow-up Controls... .. 218 Synchros .... 242 Synchro Transmitters 278 Synchro Receivers 282 RESTRIGED 169 BASIC MECHANISMS OP 1140 , J ,J , MAGNETISM and ELECTRICITY I I The larger mechanical computers contain several different kinds of electromechanical mechanisms such as servo motors, synchros, and solenoid locks and clutches. It is necessary to know the basic principles of magnetism and electricity to understand how they work. This chapter is confined mainly to the facts about electricity and magnetism which will be of practical use in understanding and maintaining basic Ford eleCtromechanical units. -
Synchro and Resolver Engineering Handbook We Have Been a Leader in the Rotary Components Industry for Over 50 Years
Synchro and Resolver Engineering Handbook We have been a leader in the rotary components industry for over 50 years. Our staff includes electrical, mechanical, manufacturing and software engineers, metallurgists, chemists, physicists and materials scientists. Ongoing emphasis on research and product development has provided us with the expertise to solve real-life manufacturing problems. Using state-of-the-art tools in our complete analytical facility, our capabilities include a full range of environmental test, calibration and inspection services. Moog Components Group places a continuing emphasis on quality manufacturing and product development to ensure that our products meet our customer’s requirements as well as our stringent quality goals. Moog Components Group has earned ISO-9001 certification. We look forward to working with you to meet your resolver requirements. 1213 North Main Street, Blacksburg, VA 24060-3127 800/336-2112 ext. 279 • 540/552-3011 • FAX 540/557-6400 • www.moog.com • e-mail: [email protected] Specifications and information are subject to change without prior notice. © 2004 Moog Components Group Inc. MSG90020 12/04 www.moog.com Synchro and Resolver Engineering Handbook Contents Page Section 1.0 Introduction 1-1 Section 2.0 Synchros and Resolvers 2-1 2.1 Theory of Operation and Classic Applications 2-1 2.1.1 Transmitter 2-1 2.1.2 Receiver 2-1 2.1.3 Differential 2-2 2.1.4 Control Transformer 2-2 2.1.5 Transolver and Differential Resolver 2-3 2.1.6 Resolver 2-3 2.1.7 Linear Transformer 2-5 2.2 Brushless Synchros and Resolvers -
Matched Transformers for Synchro and Resolver Applications
Electrocomponent Science and Technology (C) Gordon and Breach Science Publishers Ltd. 1975, Vol. 2, pp. 121-134 Printed in Great Britain MATCHED TRANSFORMERS FOR SYNCHRO AND RESOLVER APPLICATIONS M. PRATT Professional Components Division, Ferranti Ltd., Dundee, UK (Received December 17; 1974; in final form March 3, 1975) Transformer pairs in Scott Tee and similar transformer arrangements have been used for some considerable time in precision synchro/resolver angular measuring gear and in synchro to digital converters. Literature on the subject of transformer requirements is, however, scant or non-existent.I, 2 This paper describes the basic principle of transformer operation and develops a design approach which, although aimed primarily at the minimisation of transformer hardware size, still maintains the required level of angular accuracy. The method applies to transformers utilised in mobile systems, particularly transformer arrangements working under loaded conditions. INTRODUCTION manufacturing approach leading to minimised weight and volume, especially in transformers looking Synchro shaft angle to digital conversion techniques towards and positioning the synchro. (Digital to are used extensively in airborne and shipborne synchro mode application.) systems to give direct read-out positional data on synchro and resolver elements with an ability to 2 THREE TO FOUR WIRE CONVERSION reposition synchro devices from a central control computer. The use of transformers in three to four wire Shaft angle data, to and from the control point, is conversion is readily understood by first considering by a three wire system, usually with the synchro Figure 1. which is descriptive of a synchro element elements energised at a frequency of 400 Hz. -
Synchronous Machines
Synchronous Machines EXPERIMENT Synchronous Machine with DACI Synchronous Machines OBJECTIVE Three-phase synchronous machines account for a high percentage of this country’s power generation. Understanding the machine’s behavior and determining its equivalent network and performance characteristics are of prime importance to a power engineer. This experiment studies the characteristics of doubly-excited synchronous motors and generators. Specific tests are run to determine equivalent circuit parameters, torque, and power factor control. This lab shows that system design considerations must include frequency, speed, power factor, and voltage. Also illustrated are important machine design parameters including linear versus non-linear magnetic characteristics and efficiency. REFERENCES 1. “Electric Machinery”, Fitzgerald, Kingsley, and Umans, McGraw-Hill Book Company, 1983, Chapter 7. 2. “Electric Machines”, Sarma, M. S., William C. Brown Publishers, 1985. 3. “Electromechanical Devices for Energy Conversion and Control Systems”, Del Toro, Vincent, Prentice-Hall, Inc., 1968. 4. “Electric Machinery and Transformers”, Kosow, Irving L., Prentice-Hall, Inc., 1972. 5. “Electromechanical Energy Conversion”, Brown, David, Hamilton, E. P., MacMillan Publishing Company, 1984. BACKGROUND INFORMATION The three-phase synchronous machine, illustrated in Figure 1, is literally a DC machine turned inside-out. The armature, excited by alternating current, is wound in the stator of the machine, and the direct current field is wound on the rotor of the machine. Electrical power is transferred to the rotor through stator mounted brushes that make contact with rotor mounted slip rings. The rotating field that is necessary for continuous torque development is accomplished by the AC utility supply. Revised: October 12, 2018 1 of 23 Synchronous Machines Figure 1: Cross-sections of synchronous machines. -
Advanced Winding Models and Ontology-Based Fault Diagnosis for Power Transformers
THE UNIVERSITY of LIVERPOOL ADVANCED WINDING MODELS AND ONTOLOGY-BASED FAULT DIAGNOSIS FOR POWER TRANSFORMERS Thesis submitted in accordance with the requirements of the University of Liverpool for the degree of Master of Philosophy in Electrical Engineering and Electronics by CHEN LU, B.Sc.(Eng.) July 2014 ADVANCED WINDING MODELS AND ONTOLOGY-BASED FAULT DIAGNOSIS FOR POWER TRANSFORMERS by CHEN LU Copyright 2014 ii Acknowledgements I would like to give my heartfelt thanks to my supervisor, Dr. T. T. Mu, whose encouragement, guidance and support enabled me to develop a deep understanding of my work. Her intellectual advice, encouragement and invaluable discussions were the driving force in my work and have deeply broadened my knowledge in many areas, for which I am truly grateful. Many thanks to Prof. Q. H. Wu and Dr. W. H. Tang, for their professional guidance. Their drive, enthusiasm, their hard work and knowledge that has triggered and nourished my intellectual maturity. I offer my regards and blessings to all of the members of Electrical Drives, Power and Control Research Group, the University of Liverpool, especially to Dr. L. Jiang, Dr. W. Yao, Dr. J. D. Jin, Mr. C. H. Wei, Mr. L. Yan and Mr. L. Zhu. Special thanks also go to my friends, J. Chen, Z. Wang, for their support and friendship. My thanks also go to the Department of Electrical Engineering and Electronics at the University of Liverpool, for providing the research facilities that made it possible for me to carry out this research. Last but not least, my thanks go to my beloved family for their loving consid- erations and great confidence in me through these years. -
Multiple Choice Practice Questions for ONLINE/OMR AITT-2020 2 Year
Multiple Choice Practice Questions for ONLINE/OMR AITT-2020 nd 2 Year Electrician Trade Theory DC machine (Generator & Motor) 1 What is the name of the part marked as ‘X’ in DC generator given below? A - Armature core B -Brush C- Commutator raiser D -Commutator segment 2 What is the name of D.C generator given below? A- Differential long shunt compound B- Differential short shunt compound C -Cumulative long shunt compound D -Cumulative short shunt compound 3 Which rule is used to find the direction of induced emf in D.C generator? A- Cork screw rule B -Right hand palm rule C -Fleming’s left-hand rule D -Fleming’s right hand rule 4 Which formula is used to calculate the generated emf in D.C generator? A –ZNPa/60ɸ B -ɸZna/60P C - ɸZnp/60a D - ɸZnp/60 5 What is the formula to calculate back emf of a D.C motor? A -Eb = V/Ia Ra B- Eb = V x Ia Ra C -Eb = V – Ia Ra D -Eb = V + Ia Ra 6 What is the name of the part marked ‘X’ in DC generator given below? A -Pole tip B -Pole coil C -Pole core D -Pole shoe 7 What is the name of the D.C generator given below? A -Shunt generator B -Series generator C- Compound generator D -Separately excited generator 8 Which energy is converted into electrical energy by generator? A -Heat B- Kinetic C -Chemical D -Mechanical 9 What is the name of D.C generator field given below? A -Short shunt compound generator B -Long shunt compound generator C -Differential compound generator D -Cumulative compound generator 10 What is the principle of D.C generator? A -Cork screw rule B -Fleming’s left-hand rule C -Fleming’s -
MUIRHEAD AEROSPACE Synchros
Aerospace & Defense Division MUIRHEAD AEROSPACE Synchros In motion to keep you moving Contents 2 Contents Introduction Muirhead Aerospace Content 2 Synchros 3 Winding Configuration 4 Hardware Information 4 Size 08 Synchros 26 & 115V 400Hz 5-6 Size 11 Synchros 26 & 115V 400Hz 7-8 Size 15 Synchros 26 & 115V, 60 & 400Hz 9-10 Size 18 Synchros 115V, 60 & 400Hz 11-12 Size 23 Synchros 115V, 60 & 400Hz 13-14 Specialised Components: Brushless Synchros 15 Tandem Synchros 15 Size 18 Synchros Indicating Receiver 115V, 60 & 400 Hz 16 Conversion Table 17 Contacts 18 © 2010 BY AMETEK, INC. ALL RIGHTS RESERVED Synchros 3 Synchros Synchros are used to transmit angular data electrically from one location to another where a high degree of accuracy is required. They are essentially variable transformers in which the coupling between windings varies with the rotor position relative to the stator. Several different types are produced to suit particular applications and whilst their external appearance is similar, the internal construction varies to optimise the units’ functional requirements. Muirhead’s pedigree and capability in the field of Synchros will ensure the most demanding specifications are met. Typical applications include remote positioning of low torque mechanisms, remote control by servo motor driven mechanism, remote digital measurement of angle via a suitable signal converter, remote pointer indication of angular position. Control Synchros The design principle of a Control Synchro is to minimise errors in the output signal due to current loading, magnetic non-linearity and temperature rise, by the use of high impedance windings and special attention to the magnetic circuits. -
Synchro/Resolver Conversion Handbook
SYNCHRO/RESOLVER CONVERSION HANDBOOK 105 Wilbur Place, Bohemia, New York 11716-2426 For Technical Support - 1-800-DDC-5757 ext. 7771 Headquarters - Tel: (631) 567-5600, Fax: (631) 567-7358 United Kingdom - Tel: +44-(0) 1635-811140, Fax: +44-(0) 1635-32264 France - Tel: +33-(0) 1-41-16-3424, Fax: +33-(0) 1-41-16-3425 Germany - Tel: +49-(0) 8141-349-087, Fax: +49-(0) 8141-349-089 Japan - Tel: +81-(0) 3-3814-7688, Fax: +81-(0) 3-3814-7689 World Wide Web - http://www.ddc-web.com FOURTH EDITION UPDATED 03/2009 ii PREFACE The Synchro/Resolver Conversion Handbook is designed as a practical reference source. It discusses the theory of operation of data converter products (synchro, resolver, and linear variable differential transformer [LVDT]), performance parameters, and design factors for typical applications. The subject matter and appli- cations are chosen to be those of greatest interest and concern for the designers, systems engineers, and systems operators with whom DDC has worked over the years. The text treats both DDC’s own approach to shaft encoding and other generally accepted techniques. Because various points of view are presented, the Handbook has served well as a teaching aid over the years. Our first Synchro Conversion Handbook was conceived in 1973 during a series of technical seminars con- ducted at DDC. It was the first integrated reference source on synchro/resolver data converters. Now after 30 plus years, this hardcopy book is released as an electronic file. Since 1968 DDC has been the leader in new product development in the field of synchro/resolver convert- ers. -
Electrical Knowledge
United States Coast Guard Marine Engineer Exam Questions Electrical Question Choice A Choice B Choice C Choice D Illustration BOOK Answer Number Question 12 1 C As shown in the illustration, which of the listed types of motor Across-the-line Capacitor Autotransformer Part-winding See illustration controllers and starters is indicated? number(s): EL-0012 12 2 B The full torque electric brake on an electric cargo winch functions act as a backup brake in automatically hold the automatically govern the automatically govern the to _____________. the event the mechanical load as soon as current lowering speed of the hoisting speed of the brake should fail to the machine is shut load load off 12 3 D You are performing an out-of-circuit test on the semi- conductor A low reading with red A low reading with red A low reading with black A low reading with black See illustration shown in the illustration. Using an ohmmeter on 'low power' lead on "A" and black lead on "A" and black lead on"A" and red lead lead on "A" and red lead number(s): EL-0068 setting and with leads properly inserted, which of the listed results lead on "C"; and a high lead on "B"; and a high on "B"; and a high on "C"; and a high would indicate a good Emitter-Base junction? reading with the leads reading with the leads reading with the leads reading with the leads reversed. reversed. reversed. reversed. 12 4 A When troubleshooting most electronic circuits, "loading effect" input impedance much input impedance much sensitivity of less than sensitivity of more than can be minimized by using a voltmeter with a/an greater than the less than the impedance 1000 ohms/volt 1000 volts/ohm ___________________.