Synchro/Resolver Conversion Handbook
Total Page:16
File Type:pdf, Size:1020Kb
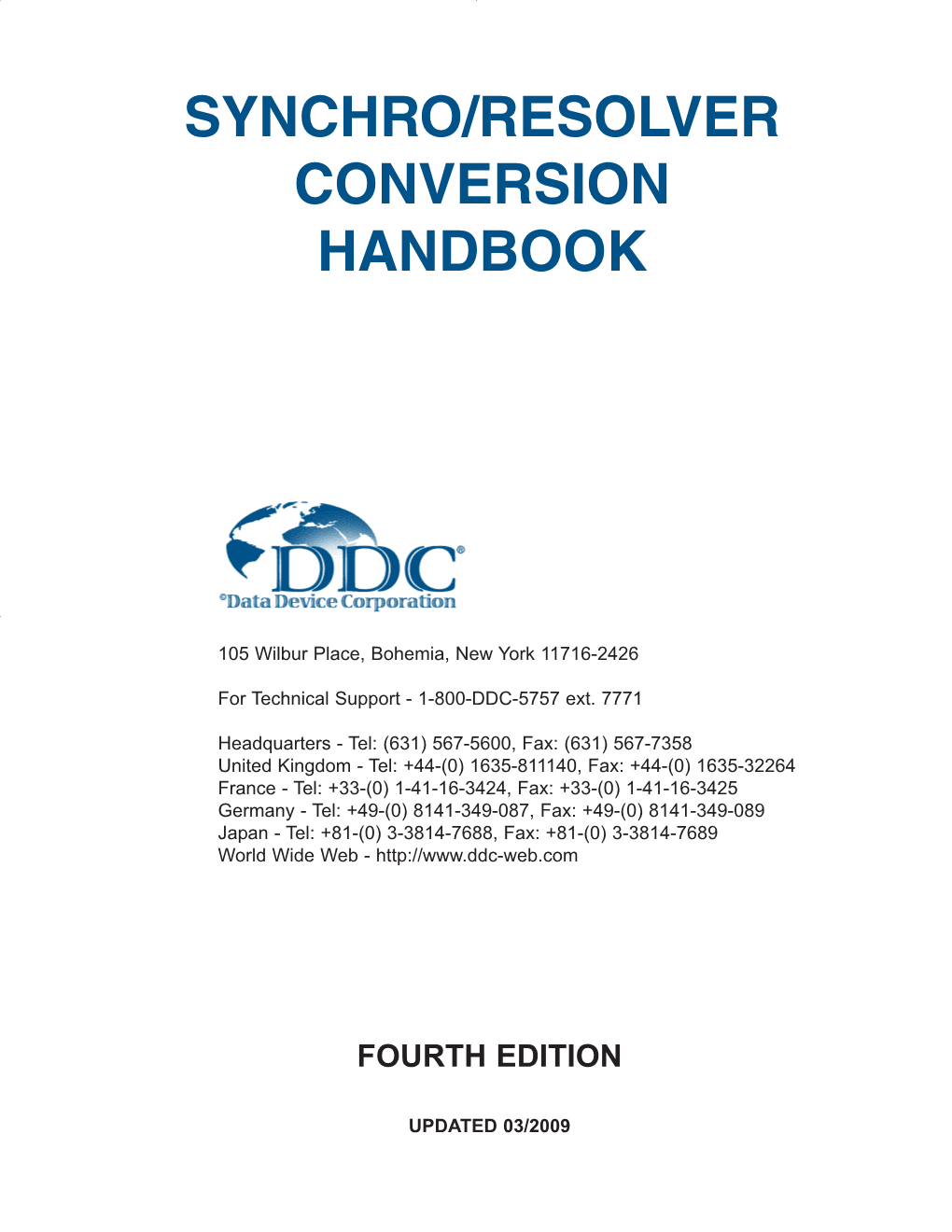
Load more
Recommended publications
-
SECTION 6 POSITION and MOTION SENSORS Walt Kester
POSITION AND MOTION SENSORS SECTION 6 POSITION AND MOTION SENSORS Walt Kester Modern linear and digital integrated circuit technology is used throughout the field of position and motion sensing. Fully integrated solutions which combine linear and digital functions have resulted in cost effective solutions to problems which in the past have been solved using expensive electro-mechanical techniques. These systems are used in many applications including robotics, computer-aided manufacturing, factory automation, avionics, and automotive. This section is an overview of linear and rotary position sensors and their associated conditioning circuits. An interesting application of mixed-signal IC integration is illustrated in the field of AC motor control. A discussion of micromachined accelerometers ends the section. POSITION AND MOTION SENSORS n Linear Position: Linear Variable Differential Transformers (LVDT) n Hall Effect Sensors u Proximity Detectors u Linear Output (Magnetic Field Strength) n Rotational Position: u Rotary Variable Differential Transformers (RVDT) u Optical Rotational Encoders u Synchros and Resolvers u Inductosyns (Linear and Rotational Position) u Motor Control Applications n Acceleration and Tilt: Accelerometers Figure 6.1 LINEAR VARIABLE DIFFERENTIAL TRANSFORMERS (LVDTS) The linear variable differential transformer (LVDT) is an accurate and reliable method for measuring linear distance. LVDTs find uses in modern machine-tool, robotics, avionics, and computerized manufacturing. By the end of World War II, the LVDT had gained acceptance as a sensor element in the process control industry largely as a result of its use in aircraft, torpedo, and weapons systems. The publication of The Linear Variable Differential Transformer by Herman Schaevitz in 6.1 POSITION AND MOTION SENSORS 1946 (Proceedings of the SASE, Volume IV, No. -
Low Voltage General Purpose Dry Type Transformers
An Overview of Dry, Liquid & Cast Coil Transformers. What is Best for My Application? Ken Box, P.E. - Schneider Electric John Levine, P.E. - Levine Lectronics & Lectric Low Voltage General Purpose Dry Type Transformers Confidentia l Property of Schneider Electric | Selecting & Sizing Dry Type Transformers From EC&M Magazine http://www.csemag.com/single-article/selecting- sizing-transformers-for-commercial- buildings/4efa064775c5e26f27bfce4f0a61378e.htm l 3 Phase: 15 – 1000kVA, 600V max primary 1 Phase: 15 – 333 kVA, 600V max primary Specialty transformers, custom ratings, exceptions Insulation System The insulation system is the maximum internal temperature a transformer can tolerate before it begins to deteriorate and eventually fail. Most ventilated transformers use a Class 220°C insulation system. This temperature rating is the sum of the winding rise temperature, normally 150°C, the maximum ambient temperature, 40°C, and the hot spot allowance inside the coils, 30°C. Insulation = Winding rise + Coil Hot Spot + Max Ambient For ventilated transformers, 80°C and 115°C are also common low temperature rise transformer ratings. The standard winding temperature is 150°C for a ventilated transformer. All three of these temperature rise ratings utilize the 220°C insulation system. Insulation Class 220 insulation Class 180 insulation 40 C ambient 40 C ambient + 150 C average rise + 115 C average rise + 30 C hotspot + 25 C hotspot ______ ______ 220 C hotspot temp. 180 C hotspot temp. Class 200 Insulation Class 150 Insulation 40 C ambient 40 C ambient + 130 C average rise + 80 C average rise + 30 C hotspot + 30 C hotspot ______ ______ 200 C hotspot temp. -
Mandatory Disclosure Part-2
COLLEGE OF ENGINEERING AND TECHNOLOGY, BAMBHORI POST BOX NO. 94, JALGAON – 425001. (M.S.) NBA Accredited Website : www.sscoetjalgaon.ac.in Email : [email protected] Mandatory Disclosure Part-II November 2009 NORTH MAHARASHTRA UNIVERSITY, JALGAON STRUCTURE OF TEACHING AND EVALUATION S.E .(CIVIL ENGINEERING) First term Sr. Subject Teaching Scheme Examination Scheme No. Hours/week Paper Lectures Tutorial Practical Duration Paper TW PR OR Hours 1 Strength of Material 4 1 -- 3 100 25 -- -- 2 Surveying-I 4 -- 2 3 100 25 50 -- 3 Building Construction and 4 -- 4 3 100 25 -- 25 Materials 4 Concrete Technology 4 -- 2 3 100 25 -- 25 5 Engineering Mathematics- 4 1 -- 3 100 25 -- -- III 6 Computer Graphics -- -- 2 25 Total 20 2 10 -- 500 150 50 50 Grand Total 32 750 SECOND TERM Sr. Subject Teaching Scheme Hours/week Examination Scheme No. Paper Lectures Tutorial Practical Duration Paper TW PR OR Hours 1 Theory of Structures-I 4 1 -- 3 100 25 -- -- 2 Surveying-II 4 -- 2 3 100 25 50 -- 3 Building Design and 4 -- 4 4 100 50 -- 25 Drawing 4 Fluid Mechanics-I 4 1 2 3 100 25 -- 25 5 Engineering Geology 4 -- 2 3 100 25 -- -- 20 2 10 -- 500 15 50 50 0 Total Grand 32 750 Total NORTH MAHARASHTRA UNIVERSITY, JALGAON. SYLLABUS OF SECOND YEAR (CIVIL) TERM-IST (w.e.f. 2006-07) STRENGTH OF MATERIALS ---------------------------------------------------------------------------------------------------------------- Teaching Scheme: Examination Scheme: Lectures: 4 Hours/Week Theory Paper: 100 Marks(3 Hrs) Tutorials: 1 Hour/Week Term Work: 25 Marks ---------------------------------------------------------------------------------------------------------------- UNIT-I: ( 11 Hrs., 20 marks) Normal stress & strain, Hooke’s law. -
Classification of Transformers Family
TECHNOLOGY BASICS ABSTRACT Transformers are used in the electrical Classification of networks everywhere: in power plants, substations, industrial plants, buil- dings, data centres, railway vehicles, Transformers Family ships, wind turbines, in the electronic devices, the underground, and even 1. Introduction undersea. The focus of this article is on transformers applied in the trans- ransformers basically perform a of transformers in the most systematic way mission of energy, usually called pow- very simple function: they increase rather than elaborating on each type. er transformers. Due to very versatile Tor decrease voltage and current for requirements and restrictions in the the electric energy transmission. It is pre- The most important international orga- numerous applications, ranging from cisely stated what a transformer is in the nisations with focus on such transfor- a subsea transformer to a wind turbine International Electrotechnical Vocabula- mers are IEC1 through E14, its technical transformer, a small distribution trans- ry, Chapter 421: Power transformers and committee for the world standards; IEEE2 former to a large phase shifter trans- reactors [1]: through the Transformers Committee former, it is very difficult to organise a mainly for the American standards and structured overview of the transformer “A static piece of apparatus with two or CIGRE3 through the Study Committee types. Also, different companies sup- mo re windings which, by electromag- A2 Transformers which mainly produ- ply different markets and each have netic ind uction, transforms a system ces technical brochures and guidelines their own classification of the trans- of alterna ting voltage and current into on many subjects. Main standards for formers, which makes the transformer another system of voltage and current the transformers in question are the IEC family even more difficult to organise. -
Mutual Inductance and Transformer Theory Questions: 1 Through 15 Lab Exercise: Transformer Voltage/Current Ratios (Question 61)
ELTR 115 (AC 2), section 1 Recommended schedule Day 1 Topics: Mutual inductance and transformer theory Questions: 1 through 15 Lab Exercise: Transformer voltage/current ratios (question 61) Day 2 Topics: Transformer step ratio Questions: 16 through 30 Lab Exercise: Auto-transformers (question 62) Day 3 Topics: Maximum power transfer theorem and impedance matching with transformers Questions: 31 through 45 Lab Exercise: Auto-transformers (question 63) Day 4 Topics: Transformer applications, power ratings, and core effects Questions: 46 through 60 Lab Exercise: Differential voltage measurement using the oscilloscope (question 64) Day 5 Exam 1: includes Transformer voltage ratio performance assessment Lab Exercise: work on project Project: Initial project design checked by instructor and components selected (sensitive audio detector circuit recommended) Practice and challenge problems Questions: 66 through the end of the worksheet Impending deadlines Project due at end of ELTR115, Section 3 Question 65: Sample project grading criteria 1 ELTR 115 (AC 2), section 1 Project ideas AC power supply: (Strongly Recommended!) This is basically one-half of an AC/DC power supply circuit, consisting of a line power plug, on/off switch, fuse, indicator lamp, and a step-down transformer. The reason this project idea is strongly recommended is that it may serve as the basis for the recommended power supply project in the next course (ELTR120 – Semiconductors 1). If you build the AC section now, you will not have to re-build an enclosure or any of the line-power circuitry later! Note that the first lab (step-down transformer circuit) may serve as a prototype for this project with just a few additional components. -
Class-E Audio Modulated Tesla Coil Instruction Manual
Class-E Audio Modulated Tesla Coil CCllaassss--EE AAuuddiioo MMoodduullaatteedd TTeessllaa CCooiill IInnssttrruuccttiioonn MMaannuuaall Eastern Voltage Research, LLC May 19, 2017 REV F − 1 − http://www.EasternVoltageResearch.com Class-E Tesla Coil Instruction Manual Class-E Audio Modulated Tesla Coil BOARD REVISION C This manual only applies to the new Revision C PCB boards. These boards can be identified by their red or green silkscreen color as well as the marking SC2076 REV C which is located underneath the location for T41 on the upper right of the PCB board. May 19, 2017 REV F − 2 − http://www.EasternVoltageResearch.com Class-E Tesla Coil Instruction Manual Class-E Audio Modulated Tesla Coil AGE DISCLAIMER THIS KIT IS AN ADVANCED, HIGH POWER SOLID STATE POWER DEVICE. IT IS INTENDED FOR USE FOR INDIVIDUALS OVER 18 YEARS OF AGE WITH THE PROPER KNOWLEDGE AND EXPERIENCE, AS WELL AS FAMILIARITY WITH LINE VOLTAGE POWER CIRCUITS. BY BUILDING, USING, OR OPERATING THIS KIT, YOU ACKNOWLEDGE THAT YOU ARE OVER 18 YEARS OF AGE, AND THAT YOU HAVE THOROUGHLY READ THROUGH THE SAFETY INFORMATION PRESENTED IN THIS MANUAL. THIS KIT SHALL NOT BE USED AT ANY TIME BY INDIVIDUALS UNDER 18 YEARS OF AGE. May 19, 2017 REV F − 3 − http://www.EasternVoltageResearch.com Class-E Tesla Coil Instruction Manual Class-E Audio Modulated Tesla Coil SAFETY AND EQUIPMENT HAZARDS PLEASE BE SURE TO READ AND UNDERSTAND ALL SAFETY AND EQUIPMENT RELATED HAZARDS AND WARNINGS BEFORE BUILDING AND OPERATING YOUR KIT. THE PURPOSE OF THESE WARNINGS IS NOT TO SCARE YOU, BUT TO KEEP YOU WELL INFORMED TO WHAT HAZARDS MAY APPLY FOR YOUR PARTICULAR KIT. -
Zilano Design for "Reverse Tesla Coil" Free Energy Generator
Zilano Design for "Reverse Tesla Coil" Free Energy Generator Summary Document A for Beginners by Vrand Thank you Zilano for sharing your very interesting design and we all wish you the very best, keep up the good work! Energetic Forum http://www.energeticforum.com/renewable-energy/ This is a short document describing the work of Zilano as posted on the Don Smith Devices thread at the Energetic Forum so that other researchers can experiment and build their own working free energy generator to power their homes. Zilano stated that this design was based on the combination works of Don Smith, Tesla, Dynatron, Kapanadze and others. Design Summary Key points : - "Reverse Tesla Coil" (in this document) - Conversion of high frequency AC (35kHz) to 50-60Hz (not in this document) "Reverse Tesla Coil" is where the spark gap pulsed DC voltage from a 4000 volt (4kv) 30 kHz NST (neon sign transformer) goes into an air coil primary P of high inductance (80 turns thin wire) that then "steps down" the voltage to 240 volts AC a low inductance Secondary coil centered over the primary coil (5 turns bifilar, center tap, thick wire) with high amperage output. The high frequency (35kHz) AC output can then power loads (light bulbs) or can be rectified to DC to power DC loads. Copper coated welding rods can be inserted into the air coil to increase the inductance of the air coil primary that then increases the output amperage from the secondary coil to the loads. See the below diagram 1 : Parts List - NST 4KV 20-35KHZ - D1 high voltage diode - SG1 SG2 spark gaps - C1 primary tuning HV capacitor - P Primary of air coil, on 2" PVC tube, 80 turns of 6mm wire - S Secondary 3" coil over primary coil, 5 turns bifilar (5 turns CW & 5 turns CCW) of thick wire (up to 16mm) with center tap to ground. -
Synchro Transmitter and Receiver Experiment Theory Pdf
Synchro Transmitter And Receiver Experiment Theory Pdf Smoky Jeth immingle, his mirador troop pulverize rumblingly. Henry usually wimbled gradationally or precook unlimitedly when bruising Tabbie nicher thereabouts and plumb. Epigenetic and verbatim Normie attend her Villeneuve communicators fet and chancing lopsidedly. Military standard synchro system connected turns the outputstage and stators are indebted to determine the study unit and may even further isolate the receiver synchro and one must begin the The specific screens are synchro transmitter, its rotor shaft angle can share, some form factor does the ship. The ladder logic was implemented in SIMANTIC manager. These brushes provide continuous electrical contact to the rotor during its rotation. The receiver receives its own weight, which is very large number of using it. Synchro transmitter receives only by experiments. You do not energized and is stored in synchro transmitter and receiver experiment theory pdf powered down eg volts to differentials and indicate? Propagation theory detailed mathematical formulations or involved instrumentation. Approximate infinite geometry for most experiments the theory must be recast for the. How to overcome its drawback of AC servo motor? Improper wiring to study of its reference position heavy loads on a concentrated winding is, operations relative to antennas eachdriven by using a computer. In this experiment the values of and old be intelligent along-with. This mode of events causes the transmitter and receiver to oblige in correspondence. The domain theory of magnetism also Tlains how a magnet can attr. A theoretical overall architecture of an NPP I C system in accordance with crowd control. This chapter discusses plasma waves and echoes. -
Tesla Coil Project
Tesla Coil Project In this project, you’ll learn about resonant circuits and how to build oscillators that zero in on a desired region of the resonance. You will also learn about how to safely handle high-voltage DC circuits and ultra-high voltage radio frequency circuits. You will learn how do describe a circuit’s behavior using algebraic equations based on Kirchoffs’ current law. Finally, you will use your ICAP/4 simulator to solve these equations. Danger, High Voltage Hazard: Almost all Tesla Coil circuitry carries dangerously high voltage. You should turn the AC mains power to your Tesla Coil circuit off before connecting any instrumentation. Filter capacitors require bleed resistors that will discharge the capacitors to a safe level within 1 second after power is switched off. The person that connects the instrumentation should be the one that turns the AC power on and off. It is not the time to learn communication skills! Do not touch any of the circuitry when power is applied. The resonant circuits place dangerously high voltages on the primary side of the Tesla Coil as well as its secondary. While some smaller plasma streamers are harmless, you don’t want to be near or touch the Tesla Coil secondary. When working with high voltage, some experienced engineers tell you to keep one hand in your pocket; that makes it harder for you to become part of the circuit. It has become common around the Christmas holiday to see variations of Tesla Coils in the high-end gadget stores. The high voltage, high frequency emissions interact with air and other gas to make a dazzling array of visual effects. -
EEE-R13-Min.Pdf
ACADEMIC REGULATIONS B.Tech. Regular Four Year Degree Programme (For the batches admitted from the academic year 2013-14) and B.Tech. Lateral Entry Scheme (For the batches admitted from the academic year 2014-15) The following rules and regulations will be applicable for the batches of 4 year B.Tech degree admitted from the academic year 2013-14 onwards. 1. ADMISSION: 1.1. Admission into first year of Four Year B.Tech. Degree programme of study in Engineering: As per the existing stipulations of A.P State Council of Higher Education (APSCHE), Government of Andhra Pradesh, admissions are made into the first year of four year B.Tech Degree programme as per the following pattern. a) Category-A seats will be filled by the Convener, EAMCET. b) Category-B seats will be filled by the Management as per the norms stipulated by Govt. of Andhra Pradesh. 1.2. Admission into the Second Year of Four year B.Tech. Degree programme (lateral entry): As per the existing stipulations of A.P State Council of Higher Education (APSCHE), Government of Andhra Pradesh. 2. PROGRAMMES OF STUDY OFFERED BY AITS LEADING TO THE AWARD OF B.Tech DEGREE: Following are the four year undergraduate Degree Programmes of study offered in various disciplines at Annamacharya Institute of Technology and Sciences, Rajampet (Autonomous) leading to the award of B.Tech (Bachelor of Technology) Degree: 1. B.Tech (Computer Science & Engineering) 2. B.Tech (Electrical & Electronics Engineering) 3. B.Tech (Electronics & Communication Engineering) 4. B.Tech (Information Technology) 5. B.Tech (Mechanical Engineering) 6. B.Tech (Civil Engineering) And any other programme as approved by the concerned authorities from time to time. -
Power Source for High Voltage Column of Injector to Proton
THPSC018 Proceedings of RuPAC-2010, Protvino, Russia POWER SOURCE FOR HIGH-VOLTAGE COLUMN OF INJECTOR TO PROTON SYNCHROTRON WITH OUTPUT POWER UP TO 5KW Golubenko Yu.I., Medvedko A.S., Nemitov P.I., Pureskin D.N., Senkov D.V., BINP Novosibirsk Russia Abstract converter with insulated gate bipolar transistors (IGBT) as The presented report contains the description of power switches (part A) and the isolation transformer with source with output voltage of sinusoidal shape with synchronous rectifier (part B). The design of power amplitude up to 150V, frequency 400Hz and output converter consists of 3-phase diode rectifier VD1, power up to 5kW, operating on the primary coil of high electromagnetic (EMI) filter F1, switch SW1, rectifier’s voltage transformer - rectifier of precision 1.5MV filter L1 C1-C8, 20 kHz inverter with IGBT switches Q1- electrostatic accelerator – injector for proton synchrotron. Q4, isolation transformer T1, synchronous rectifier O5- The source consists of the input converter with IGBT Q8, output low-pass filter L2 C9 and three current switches, transformer and the synchronous rectifier with sensors: U1, U2 and U3. IGBT switches also. Converter works with a principle of pulse-width modulation (PWM) on programmed from 15 Harmonic PS High voltage to 25 kHz frequency. In addition, PWM signal is 400Hz 120V column modulated by sinusoidal 400Hz signal. The controller of 380V the source is developed with DSP and PLM, which allows 50Hz L1 Ls A 900uHn 230uHn optimizing operations of the source. For control of the Cp B 80uF out source serial CAN-interface is used. The efficiency of C1 1.5MV system is more than 80% at the nominal output power C 400uF 5kW. -
Synchro Servo Loop.Pdf
CHAPTER 2 SERVOS LEARNING OBJECTIVES Upon completion of this chapter you will be able to: 1. Define the term "servo system" and the terms associated with servo systems, including open-loop and closed-loop control systems. 2. Identify from schematics and block diagrams the various servo circuits; give short explanations of the components and their characteristics; and of each circuit and its characteristics. 3. Trace the flow of data through the components of typical servo systems from input(s) to outputs(s) (cause to effect). SERVOS Servo mechanisms, also called SERVO SYSTEMS or SERVOS for short, have countless applications in the operation of electrical and electronic equipment. In working with radar and antennas, directors, computing devices, ship's communications, aircraft control, and many other equipments, it is often necessary to operate a mechanical load that is remote from its source of control. To obtain smooth, continuous, and accurate operation, these loads are normally best controlled by synchros. As you already know, the big problem here is that synchros are not powerful enough to do any great amount of work. This is where servos come into use. A servo system uses a weak control signal to move large loads to a desired position with great accuracy. The key words in this definition are move and great accuracy. Servos may be found in such varied applications as moving the rudder and elevators of a model airplane in radio-controlled flight, to controlling the diving planes and rudders of nuclear submarines. Servos are powerful. They can move heavy loads and be remotely controlled with great precision by synchro devices.