SURVEY REPORT of the SURVEILLANCE and PROTECTION
Total Page:16
File Type:pdf, Size:1020Kb
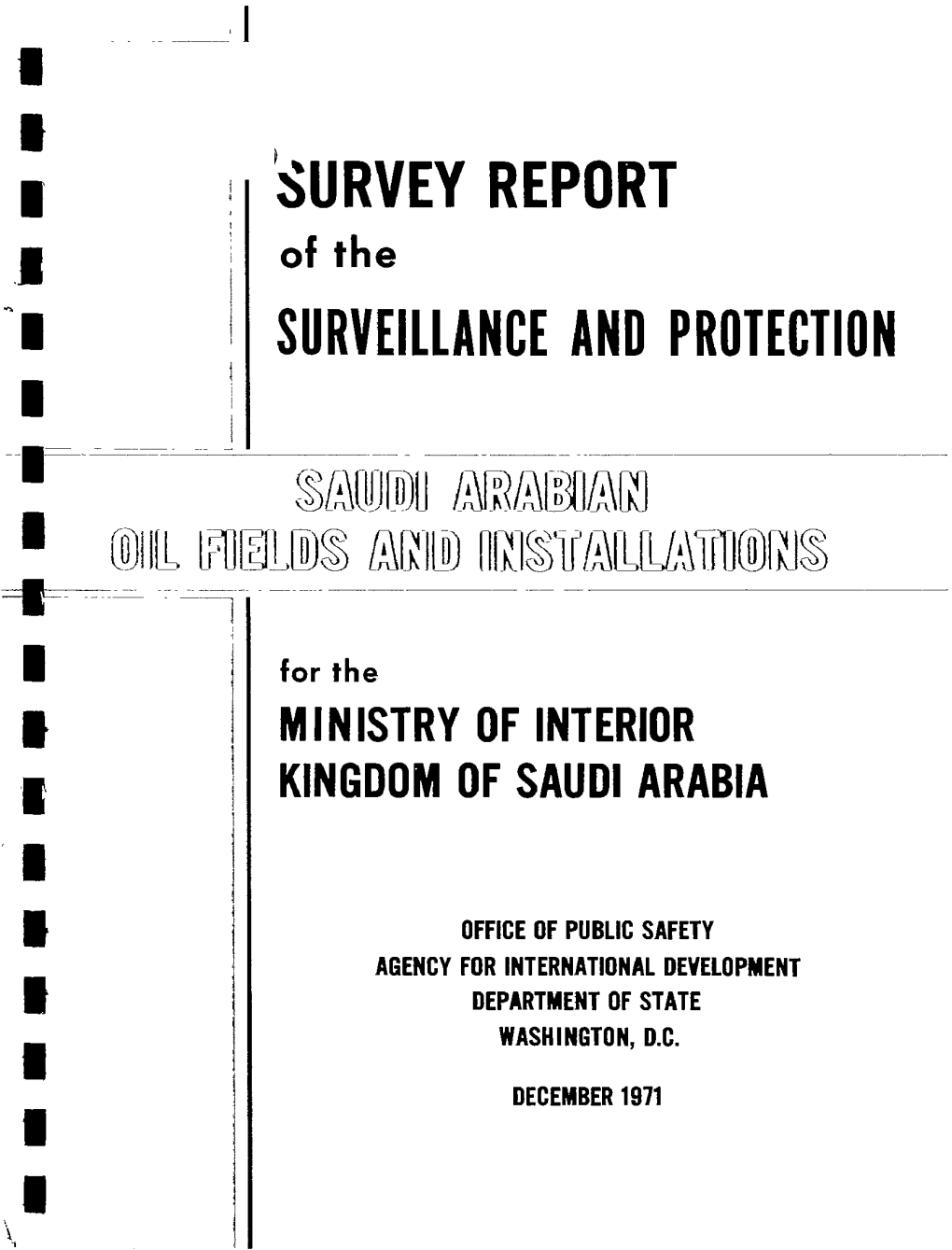
Load more
Recommended publications
-
EPSE PROFILE-19Th Edition
Electrical Power Systems Establishment PROFILE 19th EDITION May, 2019 www.eps-est.com TABLE OF CONTENTS 1.0 INTRODUCTION 2.0 ORGANIZATION INFORMATION 3.0 MESSAGES 3.1 MISSION 3.2 VISION 3.3 COMMITMENT STATEMENT 3.4 QA/QC STATEMENT 3.5 SAFETY STATMENT 4.0 ORGANIZATION CHART 5.0 AFFILIATIONS 6.0 RESOURCES LISTING 6.1 MANPOWER 6.2 CONSTRUCTION EQUIPMENT & TOOLS 6.3 TESTING EQUIPMENT 7.0 BRIEF BUSINESS EXPOSURE 7.1 EQUIPMENT EXPERTISE 7.2 SERVICES 7.3 MAIN CUSTOMERS LIST 8.0 PROJECT LISTING 8.1 ON GOING JOBS 8.2 COMPLETED JOBS Electrical Power Systems Est. Profile 19th Edition May, 2019 PAGE 2 OF 33 1.0 INTRODUCTION Electrical Power Systems Est., (EPSE) was founded in 1989 under the name of Electronics Systems Est. (ESE). Established primarily to provide general services in instrumentation, calibration and personal computer trade, it then revolutionized its interests to the more technical field of Control and Monitoring Systems primarily for the Electric Power utilities. Within a short period of time in this new field of interest, it has achieved a remarkable and outstanding performance that gained the appreciation and acknowledgment of fine clients such as ABB, which from thence entrusted sensitive related jobs to the Establishment. Realizing the soaring demand for services in this specialized field and where only few Saudi firms have ventured, the management was prompted to enhance and confine ESE activities within the bounds of Electric Power Control and Monitoring Systems. In late 1998, Electronics Systems Est. (ESE) was renamed Electrical Power Systems Establishment (EPSE) to appropriately symbolize its specialized activities in the field of Electricity. -
Economic Development Prospects for the Eastern Province
Economic Development Prospects for the Eastern Province Economic Development Prospects for the Eastern Province www.chamber.org.sa Eastern Province in Brief 02 Section One: 04 Eastern Province’s Key Economic Development Section Two: 06 Industrial Activity in Eastern Province Contents Section Three: 15 Infrastructure Development in Eastern Province Section Four: 18 Tourism Activity in Eastern Province Section Five: 22 Population in Eastern Province Section Six: 24 Work Force in Eastern Province Section Seven: 26 Housing Units in Eastern Province Section Eight: 28 Hospital & Beds in Eastern Province Section Nine: 32 Agriculture & Livestock Resources in Eastern Province Section Ten: 38 Water Production in Eastern Province Conclusion and References 42-45 Eastern Province in Brief ASH SHARQIYAH Eastern Province The Eastern Province of Saudi Arabia is the place where Kingdom’s first oil was extracted in 1938 and subsequently this region has become the center of world-class oil, gas and petrochemical industries with the presence of global giants in these sectors. Today, the Eastern Province is dubbed “The Industrial Capital of the Entire Gulf” for its enormous industrial activities. And it is evident when this region has become the biggest recipient of industrial capital investments of the Kingdom. 22 Economic Development Prospects for the Eastern Province With the support from the recently launched “Saudi Vision 2030”, the Eastern Province has taken a key role in the Kingdom’s drive to diversify its income away from oil. Most of the manufacturing industries such as petrochemicals, chemicals, steel, cement, aluminum and plastics are located in the region. These industries are mainly based in the Dammam-I, II and III industrial estates, Al Ahsa-I and II industrial estates, Hafr Al-Batin industrial estate and Jubail-I and II industrial cities. -
Arabian Sun 2 Company News JHAH Awarded ‘Gold’ Person-Centered Care Certification Johns Hopkins Aramco Healthcare Nabeel A
January 13, 2021 Vol. LXXVI, No. 2 a weekly Aramco publication for employees More than just a pretty place Aramco’s new a natural wondersee pages 6 and 7 January 13, 2021 the arabian sun 2 company news JHAH Awarded ‘Gold’ Person-Centered Care Certification Johns Hopkins Aramco Healthcare Nabeel A. (JHAH) has been accredited as one of Al-Jama’, JHAH only four organizations in the Kingdom chairman of the with Gold certification. Person-Cen- Board and tered Care is an international standard senior vice As of today, JHAH is established by Planetree International president of HR and Corporate for quality in health care, where staff, Services, officially the gold patients, and families have their needs delivers and desires heard and addressed. celebratory standard for person- remarks to The Gold Award was celebrated at a attendees after centered care in Saudi being ceremony Jan. 3 in Dhahran. Nabeel A. introduced by Arabia. Together, you Al-Jama’, senior vice president of Hu- Dr. Amar Sattar, man Resources and Corporate Services co-chairman of have built a JHAH and JHAH chairman of the Board, and the Person- Dr. Susan Frampton, president of Plane- Centered Care culture that puts Council. tree International, joined the ceremony virtually to celebrate with JHAH leader- people and their needs ship, including Dr. Michael Walsh, chief right at the front and executive of JHAH; Salem Al-Shehry, and their families who’ve come with congratulations.” COO and Person-Centered Care advo- us on this journey. Together, you have center of everything cate; and JHAH employees. built a JHAH culture that puts people The Gold certification was achieved and their needs right at the front and after a weeklong validation visit by in- we do. -
Karam Restaurant
All Restaurants Top Oers Login Register Now ﻋﺮﺑﻲ Home > Al Khobar > Al Jawaharah > Karam Restaurant Karam Restaurant Your order Arabian Food Minimum order SR 70.0 Delivery time Karam Restaurant Delivery to Al Khobar - Al Jawaharah Delivery fee SR 0.0 Food temperature Customer service Delivery fee: Info Reviews Menu Total : 0 SR Daily Dish General Request Saturday SR 38.0 Add Dawod basha with green salad Restaurant Delivery Sunday SR 38.0 Add Next Chicken Kbsa with green salad Monday SR 38.0 Add Chicken inverted With green salad Tuesday SR 38.0 Add Chicken Biryani with milk salad with cucumber Wednesday SR 40.0 Add Beef kbsa with green salad Thursday SR 40.0 Add Beef biryani with cucumber salad Friday SR 40.0 Add Fish sayadiya with green salad Soups Karam Seafood Soup SR 20.0 Add Cooked with our own style Lentil Soup SR 12.0 Add Rich with protein Mushroom Cream Soup SR 15.0 Add Tasty mushroom pieces with fresh cream Chicken Cream soup SR 15.0 Add Tasty mushroom pieces with fresh cream Cold Appetizers Green Salad SR 12.0 Add Special mix of fresh vegetables Hummus SR 12.0 Add Original Arabic mixture Hummus Beirouty SR 15.0 Add Muttabal SR 12.0 Add Grilled eggplant with tahini sauce Lebanese Tabbouleh SR 13.0 Add Shami Fattoush SR 13.0 Add Fresh vegetable pieces with crispy bread Baba Ghannoug SR 12.0 Add Eggplant mix with onions, tomatoes, olive oil and spices Vine Leaves SR 14.0 Add Stued with special mixture Corn Salad SR 12.0 Add Swiss Salad SR 12.0 Add Russian Salad SR 12.0 Add Vegetables, boiled potatoes and mayonnaise Olives Salad -
[email protected]
Contents Al-Jeel Al-Thalith and its Subsidiaries Subsidiary: Electricity Metering Est. for Contracting Al-Jeel Al-Thalith Introduction……………………………………………………….……………02 Services…………………………………………………………………………………………………………..03 Corporate Information…………………………………………………………………………………06 Health & Safety Policy………………………………………………………………………………….07 Quality Assurance & Quality Control…………………………………………………………10 Facilities…………………………………………………………………………………………………………..12 Manpower Details…………………………………………………………………………………………13 Equipment Details…………………………………………………………………………………………16 Completed Projects……………………………………………………………………………………...20 Ongoing Projects…………………………………………………………………………………………..33 DOCUMENT TITLE Company Profile Glimpses of Projects…………………………………………………………………………………….35 COMPILED BY Legal Documents……………………………………………………………………………….…………56 Khalid Rehman CONTACT T. +966-13-8994747 F. +966-13-8994949 [email protected] Company Profile Introduction Al-Jeel Al-Thalith Contracting Company Ltd & Electricity Metering Establishment For Contracting are 100% Saudi collective company established in the year 1996 and is located in Al-Khobar, Saudi Arabia. Both Companies are well represented in the Kingdom and has participated in some of the SEC and Saudi ARAMCO construction and services projects as well as oth- er agencies. We are proud to say that “successful projects completion” has always re- ceived our highest priority. Our relative success as a construction and services contractor has been due to our ability to maintain a stable and skilled workforce, including management and our -
SN Date Regd. Company Detail Manpower
SN Date Regd. company detail manpower Damakhin Establishment for Maintenance and Operation Synnet International Pvt. Ltd. 1 17-Jul-2019 076/77/1 Riyadh Kathmandu CR No 1010538264 Lic No: 206 Damakin Contracting Est. Synnet International Pvt. Ltd. 2 17-Jul-2019 076/77/2 riyadh Kathmandu CR No 1010375231 Lic No: 206 Taj Renad Contracting Est Synnet International Pvt. Ltd. 3 17-Jul-2019 076/77/3 Riyadh Kathmandu CR No 1010529103 Lic No: 206 Thatwe Golden Lion Restaurant SMP Overseas Pvt. Ltd. 4 17-Jul-2019 076/77/4 Riyadh Kathmandu CR No 1010499662 Lic No: 817 5 17-Jul-2019 076/77/5 Kathmandu CR No 1129004036 Lic No: Sun Shine World Est. White Pigeon Job Placement Pvt. Ltd. 6 17-Jul-2019 076/77/6 Dammam Kathmandu CR No 2063605975 Lic No: 1369 Al Amjad Company for Education and Training Osho Recruiting Agency Pvt. Ltd. 7 17-Jul-2019 076/77/7 Riyadh Kathmandu CR No 1010191787 Lic No: 795 Al Amjad Company for Education and Training Osho Recruiting Agency Pvt. Ltd. 8 17-Jul-2019 076/77/8 Riyadh Kathmandu CR No 1010191787 Lic No: 795 Remal Assawahel Contracting & Maintenance Co. Apple Overseas Pvt. Ltd. 9 17-Jul-2019 076/77/9 Riyadh Kathmandu CR No 1010042569 Lic No: 876 Muntaha Al Azhar Company for contractting Ishan Overseas Pvt. Ltd. 10 17-Jul-2019 076/77/10 Riyadh Kathmandu CR No 1010519298 Lic No: 532 Abhor Contracting Est. Al Harmain HR Pvt. Ltd. 11 17-Jul-2019 076/77/11 Riyadh Kathmandu CR No 4030328887 Lic No: 1160 Remal Assawahel Contracting & Maintenance Co. -
Arabian Bemco Contracting Co. Ltd Qassim Power Plant Iii-RO 100M3/D Qassim BWRO 100 M3/D 30-04-11
Type of Plant Customer's Name Project Name Site Description Capacity Order-date BWRO Arabian Bemco Contracting Co. Ltd Qassim power plant iii-RO 100m3/d Qassim BWRO 100 m3/d 30-04-11 JSC ARCELOR MITTAL TEMIRTAU BWRO 4x100m3/h, Metal Steel Kazaksthan BWRO 4x1000 m3/d 25-Jan-2011 Group-11 - 100 Bed Psychology Health Allatifia Trading & Contracting Hospital Arar, Al Jouf,Quriat BWRO 2x130 m3/d 8-Dec-2010 AL SUWAIKET TRAD&CONTR.CO-KBR Al khobar lake Al Khobar BWRO 1300 m3/d 19-Oct-2010 Turaif,Hafral Batin, Al Rashid Trading & Contracting Co. RTCC BORDER SECURITY Arar, Aueqliah,Rafha- BWRO 2x300 m3/d 13-Jun-2010 Samama Co For Oper & Maint Qassim Military Hospital - MODA Qassim BWRO 1000 m3/d 12-Jun-2010 Swayeh Co BUSAITHAH WTP AL JOUF Al Jouf BWRO 35000 m3/d 12-Apr-2010 Nasrallah Othman Est./Marina Hafar Al-Batin Hafar Al-Batin BWRO 2x300 m3/d 4-Apr-2010 Aujan Soft Drink Industries Aujan Soft Drink BWRO 2x600m3/d Dammam BWRO 2x600 m3/d 29-Mar-2010 Industrial Cities Development andOperating Co. ICDOC Reject WTP for JIC Jeddah BWRO 2000 m3/d 17-Sep-2009 Enterprise Des Travaux Publics Souterrains ETPS Maakni Ourgla RO (Army) Algeria BWRO 100 m3/d 17-Sep-2009 AFS - ALGERIA FILTRING SYSTEMS JGC Algeria BWRO 120 m3/d 29-Jul-2009 Gulf Egyptian Est. - GEEMCO (MOW) Nayeria Expansion WTP No. 5 Nayreia BWRO-Nano 750 m3/d 16-Jul-2009 850+850+400 Jazan Devlopment Co. New Bottling Plant Jazan-Al Zabiah BWRO-Bottling+Remin m3/d 7-Jul-2009 Egyptian European Co. -
Matching the Performance of Saudi Arabian Oil Fields with an Electrical Model
Matching the Performance of Saudi Arabian Oil Fields With an Electrical Model W. L. WAHL L. D. MULLINS SOCONY MOBIL OIL CO., INC. R. H. BARHAM DALLAS, TEX. MEMBERS AIME W. R. BARTlETT ARABIAN AMERICAN OIL CO. MEMBER AIME DHAHRAN, SAUDI ARABIA ABSTRACT devices, output devices, central control and a resistance Downloaded from http://onepetro.org/JPT/article-pdf/14/11/1275/2214599/spe-414-pa.pdf by guest on 02 October 2021 capacitance (RC) network. At times, the RC network This paper describes an electrical model and its appli alone is referred to as the "model". However, it should be cation to the analysis of four reservoirs in Saudi Arabia. evident from the text which meaning is attached to the The model has 2,501 mesh points and represents 35,000 word "model". A discussion of the equipment follows. sq miles of the Arab-D member. Details of modeling such as mesh size, control problems and standards of perfor THE RESISTANCE·CAPACITANCE NETWORK mance in matching reservoir history are discussed. The The RC network consists of 2,501 capacitance decades particular performance match achieved for the Arab-D interconnected through 4,900 resistance decades. The com member is presented. Details such as permeability barriers, ponents are arranged to form a rectangular network of aquifer depletion and interference between oil fields are 2,501 mesh points in a 41- X 61-mesh array. Imposing given. The performance match realized in the Abqaiq the mesh grid system on the continuous reservoir system pool is presented in detail. divides the reservoir into discrete areal segments. -
Energy to the World: the Story of Saudi Aramco Volume 2
ENERGY TO THE WORLD: TO ENERGY ENERGY TO THE WORLD: THE STORY OF SAUDI ARAMCO OF SAUDI THE STORY THE STORY OF SAUDI ARAMCO VOLUME 2 VOLUME 2 VOLUME www.saudiaramco.com J ENERGY TO THE WORLD : VOLUME ONE TITLE K VOLUME TWO Energy to the World The Story of Saudi Aramco II ENERGY TO THE WORLD : VOLUME ONE VOLUME TWO Energy to the World The Story of Saudi Aramco Supertankers load crude oil at Ras Tanura Sea Island Terminal in 2003. Contents Copyright First Edition Volume One Volume Two © 2011 by Aramco Services Company Printed in 2011 Preface xi Illustration: Saudi Arabia viii ISBN All rights reserved. No part of this book Illustration: Saudi Arabia xiv 1 National Resources 1 978-1-882771-23-0 may be reproduced, stored in a retrieval system or transmitted in any form or 1 Prospects 1 2 Boom Time 27 Library of Congress by any means, electronic, mechanical, 2 Negotiations 33 3 Transformation 67 Control Number photocopying, recording or otherwise, 200922694 without the written permission of 3 Reading the Rocks 59 4 Rising to the Challenge 99 Aramco Services Company, except by 4 The War Years 93 5 Achieving the Vision 131 Written by a reviewer, who may quote a brief Scott McMurray passage for review. 5 Expansion 123 Appendix 168 6 Growing Pains 153 A. Upstream 170 Produced by The History Factory 7 Balancing Act 189 B. Downstream 184 Chantilly, Virginia, USA List of Abbreviations 215 C. Operations Data 194 Project Coordinators Notes on Sources 216 Company Leadership 204 Theodore J. Brockish, Kyle L. -
An Alternative Pipeline Strategy in the Persian Gulf
An Alternative Pipeline Strategy in the Persian Gulf M. Webster Ewell, Jr. Center for Naval Analysis Dagobert Brito Department of Economics, Rice University And John Noer Center for Naval Analysis This research was sponsored by the James A. Baker III Institute for Public Policy at Rice University, the Center for International Political Economy, and the Office of the Secretary of Defense. The research and views expressed in this paper are those of he individual researchers, and do not necessarily represent the views of the Baker Institute or other sponsors of the research. Executive Summary This paper examines the idea of increasing the capacity of the trans-Saudi pipeline system by using second-generation drag reduction agent (DRA) technology, so that in the event of a Strait of Hormuz (SoH) closure1, most of the oil2, which currently flows through the Strait could be rerouted through the Red Sea. We find that it should be technologically feasible to upgrade the pipeline system to a capacity of 11 MBD for a cost of $600 million. This capacity assumes the use of both the IPSA and Petroline pipelines; we also present several lower capacity, lower cost options. The upgrades will take at least 18 months to install, so they cannot be implemented in response to a crisis. DRA technology thus represents an opportunity to buy strategic insurance at bargain rates. The pipeline upgrade has several important strategic benefits. It can enhance the Saudi reputation as a stable, reliable oil producer, because it will allow Saudi oil to reach world markets even during a SoH crisis. -
You Must Read the Following Notice Before Continuing
IMPORTANT NOTICE NOT FOR DISTRIBUTION TO ANY U.S. PERSON OR TO ANY PERSON OR ADDRESS IN THE UNITED STATES IMPORTANT: You must read the following notice before continuing. The following notice applies to the attached prospectus following this page (the Prospectus), whether received by email, accessed from an internet page or otherwise received as a result of electronic communication, and you are therefore advised to read this notice carefully before reading, accessing or making any other use of the Prospectus. In reading, accessing or making any other use of the Prospectus, you agree to be bound by the following terms and conditions and each of the restrictions set out in the Prospectus, including any modifications made to them from time to time, each time you receive any information from Saudi Electricity Global SUKUK Company 5 (the Issuer) or Saudi Electricity Company (SEC) as a result of such access. RESTRICTIONS: NOTHING IN THIS ELECTRONIC TRANSMISSION CONSTITUTES AN OFFER TO SELL OR A SOLICITATION OF AN OFFER TO BUY THE CERTIFICATES IN ANY JURISDICTION. ANY CERTIFICATE TO BE ISSUED HAS NOT BEEN AND WILL NOT BE REGISTERED UNDER THE UNITED STATES SECURITIES ACT OF 1933, AS AMENDED (THE SECURITIES ACT), OR WITH ANY SECURITIES REGULATORY AUTHORITY OF ANY STATE OF THE UNITED STATES OR OTHER JURISDICTION. THE CERTIFICATES MAY NOT BE OFFERED, SOLD, PLEDGED OR OTHERWISE TRANSFERRED DIRECTLY OR INDIRECTLY WITHIN THE UNITED STATES OR TO, OR FOR THE ACCOUNT OR BENEFIT OF, U.S. PERSONS (AS DEFINED IN REGULATION S UNDER THE SECURITIES ACT), EXCEPT PURSUANT TO AN EXEMPTION FROM, OR IN A TRANSACTION NOT SUBJECT TO, THE REGISTRATION REQUIREMENTS OF THE SECURITIES ACT AND APPLICABLE STATE OR LOCAL SECURITIES LAWS. -
Annual Review 2017: Unmatched Opportunity
2 inside this review board upstream of directors operations page 06 page 18 chairman's downstream message operations page 08 page 30 president's securing foreword the future page 09 page 42 our enabling operations excellence page 10 page 52 our citizenship in our business communities page 12 page 64 our our performance company in 2017 page 16 page 76 King Salman ibn ‘Abd His Royal Highness Prince Al-‘Aziz Al Sa‘ud Mohammed ibn Salman ibn ‘Abd Al-‘Aziz Al Sa‘ud The Custodian of the Two Holy Mosques Crown Prince, Deputy Premier, and Minister of Defense 6 7 board of directors HE Khalid A. HE Dr. Ibrahim HE Mohammed HE Mohammed HE Yasir O. Al-Falih A. Al-Assaf A. Al-Jadaan M. Al-Tuwaijri Al-Rumayyan HE Khalid A. Al-Falih has been HE Dr. Ibrahim A. Al-Assaf is Minister HE Mohammed A. Al-Jadaan is currently HE Mohammed M. Al-Tuwaijri is currently HE Yasir O. Al-Rumayyan currently serves Chairman of the Board of Saudi of State and a member of the Council Minister of Finance for Saudi Arabia. He the Minister of Economy and Planning for as the Managing Director and Secretary Aramco since April 2015. of Ministers, having previously been the also serves as Chairman of the Board of Saudi Arabia. In addition to other roles, General of the Board of the Saudi Arabian Minister of Finance of Saudi Arabia. He is Directors of the General Authority of he serves as Chairman of the National Public Investment Fund. He is also Advisor He is Minister of Energy, Industry and the Governor of the Islamic Development Zakat and Tax, Chairman of the Fiscal Center of Privatization, Chairman of the to the Saudi Council of Ministers.