Design and Development of Kaplan Turbine Runner Blade
Total Page:16
File Type:pdf, Size:1020Kb
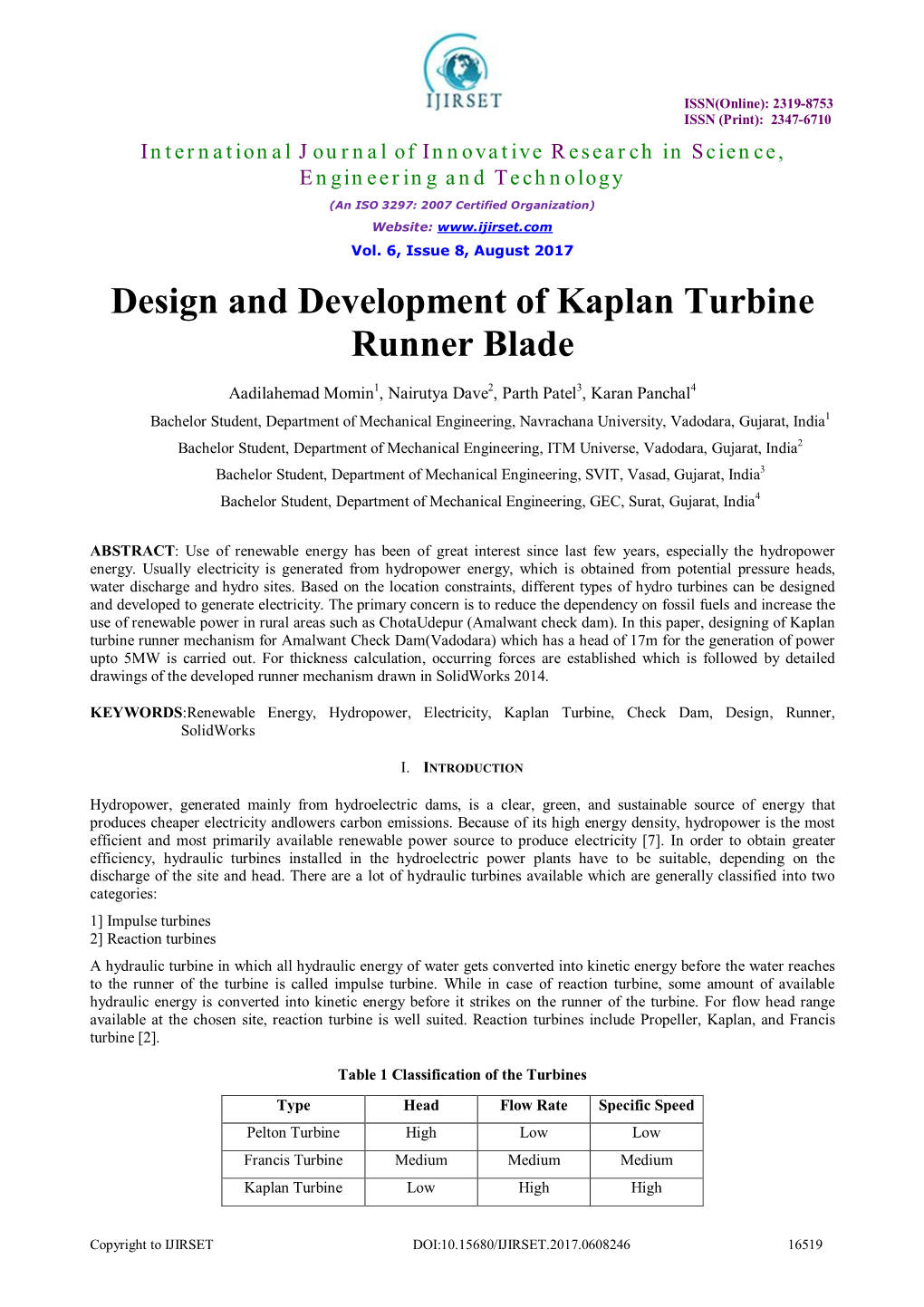
Load more
Recommended publications
-
Design and Analysis of a Kaplan Turbine Runner Wheel
Proceedings of the 3rd World Congress on Mechanical, Chemical, and Material Engineering (MCM'17) Rome, Italy – June 8 – 10, 2017 Paper No. HTFF 151 ISSN: 2369-8136 DOI: 10.11159/htff17.151 Design and Analysis of a Kaplan Turbine Runner Wheel Chamil Abeykoon1, Tobi Hantsch2 1Faculty of Science and Engineering, University of Manchester Oxford Road, M13 9PL, Manchester, UK [email protected] 2Devison of Applied Science, Computing and Engineering, Glyndwr University Mold Road, LL11 2AW, Wrexham, UK Abstract - The demand for renewable energy sources such as hydro, solar and wind has been rapidly growing over the last few decades due to the increasing environmental issues and the predicted scarcity of fossil fuels. Among the renewable energy sources, hydropower generation is one of the primary sources which date back to 1770s. Hydropower turbines are in two types as impulse and reaction where Kaplan turbine is a reaction type which was invented in 1913. The efficiency of a turbine is highly influenced by its runner wheel and this work aims to study the design of a Kaplan turbine runner wheel. First, a theoretical design was performed for determining the main characteristics where it showed an efficiency of 94%. Usually, theoretical equations are generalized and simplified and also they assumed constants of experienced data and hence a theoretical design will only be an approximate. This was confirmed as the same theoretical design showed only 59.98% of efficiency with a computational fluids dynamics (CFD) evaluation. Then, the theoretically proposed design was further analysed where pressure distribution and inlet/outlet tangential velocities of the blades were analysed and corrected with CFD to improve the efficiency of power generation. -
Low Head Hydro Market Assessment Volume 1
Natural Resources Canada Hydraulic Energy Group Renewable Energy Technologies Sustainable Buildings and Communities CANMET Energy Technology Centre (CETC) 580 Booth Street, 13th Floor Ottawa, Ontario K1A 0E4 Low Head Hydro Market Assessment Volume 1 - Main Report Final H-327842 Rev 0 March 2008 Natural Resources Canada - Low Head Hydro Market Assessment Volume 1 - Main Report Volume 2 - Appendices H-327842.201.01, Rev. 0 Low Head Market Assess - Mainreport.Doc © Hatch 2006/03 a Natural Resources Canada - Low Head Hydro Market Assessment Main Report Table of Contents Report and Estimate Disclaimer List of Acronyms/Abbreviations Hydropower Glossary List of Tables List of Figures 1. Introduction ......................................................................................................................................... 1-1 1.1 Background................................................................................................................................. 1-2 2. Small and Low Head Hydro ................................................................................................................. 2-1 2.1 Small Hydro Defined .................................................................................................................. 2-1 2.2 Low Head Hydro Defined........................................................................................................... 2-1 2.3 Run-of-River Defined .................................................................................................................. 2-2 -
Guideline and Manual for Hydropower Development Vol. 2 Small Scale Hydropower
Guideline and Manual for Hydropower Development Vol. 2 Small Scale Hydropower March 2011 Japan International Cooperation Agency Electric Power Development Co., Ltd. JP Design Co., Ltd. IDD JR 11-020 TABLE OF CONTENTS Part 1 Introduction on Small Scale Hydropower for Rural Electrification Chapter 1 Significance of Small Scale Hydropower Development ..................................... 1-1 Chapter 2 Objectives and Scope of Manual ......................................................................... 2-1 Chapter 3 Outline of Hydropower Generation ..................................................................... 3-1 Chapter 4 Rural Electrification Project by Small-Scale Hydropower ................................. 4-1 Part 2 Designation of the Area of Electrification Chapter 5 Selection of the Area of Electrification and Finding of the Site .......................... 5-1 Part 3 Investigation, Planning, Designing and Construction Chapter 6 Social Economic Research .................................................................................. 6-1 Chapter 7 Technical Survey ................................................................................................. 7-1 Chapter 8 Generation Plan ................................................................................................... 8-1 Chapter 9 Design of Civil Structures ................................................................................... 9-1 Chapter 10 Design of Electro-Mechanical Equipment ......................................................... -
Renewable Electricity Generation and Storage Technologies Futures Study
Volume 2 of 4 Renewable Electricity Renewable Electricity Generation and Storage Technologies Futures Study Volume 1 Volume 2 Volume 3 Volume 4 PDF PDF PDF PDF NREL is a national laboratory of the U.S. Department of Energy, Office of Energy Efficiency and Renewable Energy, operated by the Alliance for Sustainable Energy, LLC. Renewable Electricity Futures Study Edited By Hand, M.M. Baldwin, S. DeMeo, E. National Renewable U.S. Department of Renewable Energy Energy Laboratory Energy Consulting Services, Inc. Reilly, J.M. Mai, T. Arent, D. Massachusetts Institute of National Renewable Joint Institute for Strategic Technology Energy Laboratory Energy Analysis Porro, G. Meshek, M. Sandor, D. National Renewable National Renewable National Renewable Energy Laboratory Energy Laboratory Energy Laboratory Suggested Citations Renewable Electricity Futures Study (Entire Report) National Renewable Energy Laboratory. (2012). Renewable Electricity Futures Study. Hand, M.M.; Baldwin, S.; DeMeo, E.; Reilly, J.M.; Mai, T.; Arent, D.; Porro, G.; Meshek, M.; Sandor, D. eds. 4 vols. NREL/TP-6A20-52409. Golden, CO: National Renewable Energy Laboratory. http://www.nrel.gov/analysis/re_futures/. Volume 2: Renewable Electricity Generation and Storage Technologies Augustine, C.; Bain, R.; Chapman, J.; Denholm, P.; Drury, E.; Hall, D.G.; Lantz, E.; Margolis, R.; Thresher, R.; Sandor, D.; Bishop, N.A.; Brown, S.R.; Cada, G.F.; Felker, F.; Fernandez, S.J.; Goodrich, A.C.; Hagerman, G.; Heath, G.; O’Neil, S.; Paquette, J.; Tegen, S.; Young, K. (2012). Renewable Electricity Generation and Storage Technologies. Vol 2. of Renewable Electricity Futures Study. NREL/TP-6A20-52409-2. Golden, CO: National Renewable Energy Laboratory. Chapter 6. -
Hydraulic Turbines and Auxiliary Equipment
BR01B1848 ETDE-BR--0278 Hydraulic Turbines and Auxiliary Equipment Reporter: Mr. Luo Gaorong Deputy Director of International Centre of PCH of ONU in China .. Small Hydro Power in China L The Procedures of Small Hydro Power (SHP) Construction 1. The SHP Planning 1.1. The planning of middle and small rivers. Since all SHP stations are built on middle and small rivers, it is necessary to mnduct river planning before the SHP design, which shall be in accordance with multipurpose water resources utilization and cascade optimal development. To be more specific, river planning should take such purposes into account, namely, flood control, water supply, navigation, power generation, environmental protection, natural scene improvement, improvement of surviving conditions of human being, etc so as to develop water resources fully and rationally. At present, most rivers in China have been planned and the planning can be modified annually according to the social and economic development. The planning can be accomplished by water conse~ancy bureaus (departments) at the provincial, prefectural or county level as the river basin varies. 1.2. The planning of rural grid. Most SHP has been incorporated into the rural grid, so the electricity demand of the grid and load forecasting determine the SHP development. At present, most rural SHP grids face such a contradiction, i.e. abundant electricity during the flood season vs. electricity shortage during dry season, which can be relaxed a little bit by exchanging electricity with the national grid. So constructing SHP stations with yearly regulating reservoir has become a priority, 1.3. The SHP planning. -
Turbine Wheel-A Hydropower Converter for Head Differences
University of Southampton Research Repository ePrints Soton Copyright © and Moral Rights for this thesis are retained by the author and/or other copyright owners. A copy can be downloaded for personal non-commercial research or study, without prior permission or charge. This thesis cannot be reproduced or quoted extensively from without first obtaining permission in writing from the copyright holder/s. The content must not be changed in any way or sold commercially in any format or medium without the formal permission of the copyright holders. When referring to this work, full bibliographic details including the author, title, awarding institution and date of the thesis must be given e.g. AUTHOR (year of submission) "Full thesis title", University of Southampton, name of the University School or Department, PhD Thesis, pagination http://eprints.soton.ac.uk School of Civil Engineering and the Environment Turbine wheel - a hydropower converter for head differences between 2.5 and 5 m Ph.D Thesis Helmizar Supervisors: Dr.Gerald Müller February 2016 2 CONTENTS Academic Thesis: Declaration Of Authorship ......................................................................... 18 Acknowledgments.................................................................................................................... 19 Abstract .................................................................................................................................... 20 Chapter 1 ................................................................................................................................. -
Design and Flow Analysis of Enhanced Kaplan Turbine
DESIGN AND FLOW ANALYSIS OF ENHANCED KAPLAN TURBINE Shri Krishna Gupta1, Anshu Prakash Maurya2, 3 4 Ankit kumar Maurya Priyanka Jhavar 1P G Scholar,deparment of mechanical engineering SSSUTMS, Bhopal (India) 2Assistant Professor, Ashoka Institute of Technology and Management, Varanasi UP (India) 3P G Scholar,deparment of mechanical engineering SSSUTMS, Bhopal (India) 4HOD, SSSUTMS, Bhopal, ABSTRACT This paper presents the study of fluid flow analysis in enhanced Kaplan turbine. By changing the blade design, we consume the more energy even at low pressure of water flow in the Turbine. This turbine works on the principle of Archimedean screw that convert’s the potential energy of water on an upstream level into kinetic energy. Water flows into the turbine and its weight presses down onto the blades of the turbine, which in turn forces the turbine to turn. Water flows freely off the end of the turbine into the river. Also this study focused to found the variations of velocity components and the pressure by average circumferential area (ACA) from inlet to outlet of the blades and used as factors to analyzed the flow inside the blades, the results of this analysis shows a good prediction of the flow behavior inside the blades and this lead to acceptable blade design, which can be used in Kaplan turbine. Blade complex geometry and design have been developed by using the coordinates point system on the blade in PRO-E /CREO software. Based on the flow rate and heads, blade profiles are analyzed using ANSYS software to check and compare the output results for optimization of the blades for improved results which show that by changing blade profile angle and its geometry can be optimized using the computational techniques with changes in CAD models. -
Design and Analysis of a Kaplan Turbine Runner Wheel
The University of Manchester Research Design and Analysis of a Kaplan Turbine Runner Wheel Link to publication record in Manchester Research Explorer Citation for published version (APA): Abeykoon, C., & Hantsch, T. (2017). Design and Analysis of a Kaplan Turbine Runner Wheel. In The 3rd World Congress on Mechanical, Chemical, and Material Engineering (MCM'17) (pp. 1-16). [HTFF151]. Published in: The 3rd World Congress on Mechanical, Chemical, and Material Engineering (MCM'17) Citing this paper Please note that where the full-text provided on Manchester Research Explorer is the Author Accepted Manuscript or Proof version this may differ from the final Published version. If citing, it is advised that you check and use the publisher's definitive version. General rights Copyright and moral rights for the publications made accessible in the Research Explorer are retained by the authors and/or other copyright owners and it is a condition of accessing publications that users recognise and abide by the legal requirements associated with these rights. Takedown policy If you believe that this document breaches copyright please refer to the University of Manchester’s Takedown Procedures [http://man.ac.uk/04Y6Bo] or contact [email protected] providing relevant details, so we can investigate your claim. Download date:09. Oct. 2021 Proceedings of the 3rd World Congress on Mechanical, Chemical, and Material Engineering (MCM'17) Rome, Italy – June 8 – 10, 2017 Paper No. HTFF 151 ISSN: 2369-8136 DOI: 10.11159/htff17.151 Design -
Testimony of Gia D. Schneider Chairman and CEO Natel Energy
Testimony of Gia D. Schneider Chairman and CEO Natel Energy, Inc. Before the Committee on Science and Technology, Subcommittee on Energy and Environment United States House of Representatives “Marine and Hydrokinetic Energy Technology: Finding the Path to Commercialization” December 3, 2009 Introduction Good morning Chairman Gordon, Ranking Member Hall, and members of the Committee and Subcommittee. My name is Gia Schneider and I am a co-founder and the chairman and CEO of Natel Energy, Inc. I greatly appreciate the opportunity to share Natel Energy’s story with the Committee, and to discuss the roles of the federal government and private industry in developing technologies suitable for low head hydropower energy generation. Natel Energy Background Natel Energy, Inc. is a California and Texas-based company that is commercializing a new hydropower technology called the Linear Hydroengine or SLH, which could cut the cost of low-head turbines by as much as 50%. Our mission is to maximize the use of existing water infrastructure in the U.S. to bring on- line cost-effective, distributed, baseload, renewable energy from low head hydropower sources with minimal negative environmental impacts. Indeed, in certain cases, we believe the potential exists to implement projects that both deliver renewable energy and create positive environmental co-benefits. For example, we are evaluating the potential to incorporate renewable energy into low dams in the Midwest whose primary purpose is to create wetlands that trap nutrient pollutants which are a primary cause of the dead zone in the Gulf of Mexico. If we can successfully incorporate low head hydropower generation into some of these projects, we could create an additional revenue source for Midwest farmers, bring new renewable energy onto the grid, and reduce nutrient pollution. -
Learn About Turbines
Learn about Turbines Akashdeep Singh, AEO TURBINES • The word ‘turbine’ was coined by Claude Bourdin in the early 19th century and is derived from the Latin word for 'whirling' or a 'vortex'. • Water under pressure contains energy. • Turbines convert this energy into rotating mechanical energy. • Flowing water is directed onto the Blades of a turbine Runner, creating a force on the blades, thus transferring kinetic energy from the water flow to the turbine. Where are Turbines used • Hydroelectric schemes use the kinetic energy of moving water to produce electricity. This water is put through a turbine, which in turn drives a generator that generates electricity. Types of Hydro-Electric Schemes • Run of the river: Turbine and generator are located at the dam or along its side – e.g. Bhakhra Dam. • Diversion: The supply of water is taken from a dammed river or lake to a remote powerhouse containing the turbine and generator – e.g. Slapper (the dam is at Pandoh, the water flows through two tunnels & a channel to power house at Slapper) . • Pumped storage: This scheme incorporates two reservoirs. At times of low demand, electricity is used to pump the water from lower to upper basin. This extra water is then released to create power at a time when demand is high – e.g. Tehri Hydropower Complex where Tehri dam forms the upper reservoir and Koteshwar dam serves as lower reservoir. Types of Turbines • Water wheel Turbine • Impulse Turbine • Kaplan Turbine • Francis Turbine • Pelton Turbine • Cross flow Turbine WATER WHEEL TURBINE • Have you seen a water wheel in a field? These were very common till a few decades ago to water the fields. -
Power Technologies Energy Data Book Fourth Edition
Power Technologies Energy Data Book Fourth Edition August 2006 • NREL/TP-620-39728 Power Technologies Technical Report NREL/TP-620-39728 Energy Data Book August 2006 Fourth Edition Compiled by J. Aabakken Prepared under Task No. WUA3.1000 National Renewable Energy Laboratory 1617 Cole Boulevard, Golden, Colorado 80401-3393 303-275-3000 • www.nrel.gov Operated for the U.S. Department of Energy Office of Energy Efficiency and Renewable Energy by Midwest Research Institute • Battelle Contract No. DE-AC36-99-GO10337 NOTICE This report was prepared as an account of work sponsored by an agency of the United States government. Neither the United States government nor any agency thereof, nor any of their employees, makes any warranty, express or implied, or assumes any legal liability or responsibility for the accuracy, completeness, or usefulness of any information, apparatus, product, or process disclosed, or represents that its use would not infringe privately owned rights. Reference herein to any specific commercial product, process, or service by trade name, trademark, manufacturer, or otherwise does not necessarily constitute or imply its endorsement, recommendation, or favoring by the United States government or any agency thereof. The views and opinions of authors expressed herein do not necessarily state or reflect those of the United States government or any agency thereof. Available electronically at http://www.osti.gov/bridge Available for a processing fee to U.S. Department of Energy and its contractors, in paper, from: U.S. Department of Energy Office of Scientific and Technical Information P.O. Box 62 Oak Ridge, TN 37831-0062 phone: 865.576.8401 fax: 865.576.5728 email: mailto:[email protected] Available for sale to the public, in paper, from: U.S. -
Design of Hydro Power by Using Turbines Kaplan on the Discharge Channel Paiton 1 and 2
E3S Web of Conferences 42, 01008 (2018) https://doi.org/10.1051/e3sconf/20184201008 ASTECHNOVA 2016 Design of Hydro Power by Using Turbines Kaplan on The Discharge Channel Paiton 1 and 2 Alvin K. Sosilo, Harsono Hadi, and Totok Soehartanto Engineering Physics Dept. Institut Teknologi Sepuluh Nopember, Surabaya, Indonesia Abstract..Condenser water from the discharge channel PJB Paiton discharged to the sea has the potential mechanical energy, because the flow rate of 7.6 m3 / s (if both discharge PJB Paiton function) and the discharge channel reaches a height of 4m. This paper will describe the design of hydro power (in the form of a block diagram) by using Kaplan turbine driven by utilizing the wastewater condenser. Kaplan turbine performance represented in the form of the relationship between the incoming water flow and the pitch angle (the angle between the propellers with a hub) to the torque generated. The simulation results indicate that the turbine torque is proportional to the mechanical power turbine. The greater the torque, the greater the mechanical power, and vice versa. 1 Introduction 2 Basic Theory In the steam power plant contained equipment such as boilers, condensers, turbines, generators, and pumps. The 2.1 Condenser condenser is a heat exchanger, comprising the cooling Condenser at hydroelectric plants is a heat exchanger, water used to cool the steam turbine output. The steam serves to cool the steam turbine output. The water will be condensed into water condensate, and condensate condensation steam turbine output is called condensate water will be fed back into the boiler using a pump water.