How to Avoid Severe Incidents at Hydropower Plants
Total Page:16
File Type:pdf, Size:1020Kb
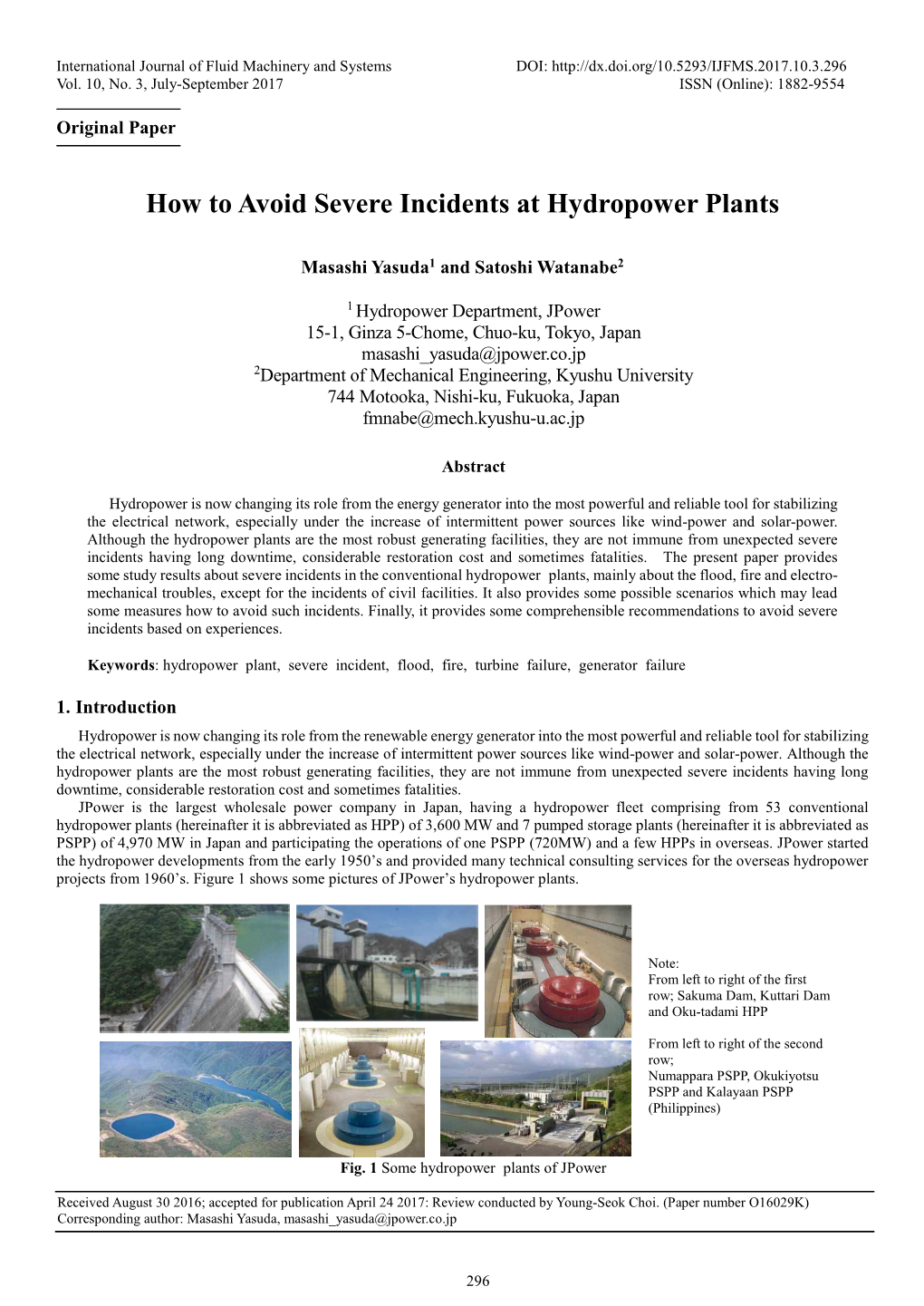
Load more
Recommended publications
-
Vol2 Case History English(1-206)
Renewal & Upgrading of Hydropower Plants IEA Hydro Technical Report _______________________________________ Volume 2: Case Histories Report March 2016 IEA Hydropower Agreement: Annex XI AUSTRALIA USA Table of contents㸦Volume 2㸧 ࠙Japanࠚ Jp. 1 : Houri #2 (Miyazaki Prefecture) P 1 㹼 P 5ۑ Jp. 2 : Kikka (Kumamoto Prefecture) P 6 㹼 P 10ۑ Jp. 3 : Hidaka River System (Hokkaido Electric Power Company) P 11 㹼 P 19ۑ Jp. 4 : Kurobe River System (Kansai Electric Power Company) P 20 㹼 P 28ۑ Jp. 5 : Kiso River System (Kansai Electric Power Company) P 29 㹼 P 37ۑ Jp. 6 : Ontake (Kansai Electric Power Company) P 38 㹼 P 46ۑ Jp. 7 : Shin-Kuronagi (Kansai Electric Power Company) P 47 㹼 P 52ۑ Jp. 8 : Okutataragi (Kansai Electric Power Company) P 53 㹼 P 63ۑ Jp. 9 : Okuyoshino / Asahi Dam (Kansai Electric Power Company) P 64 㹼 P 72ۑ Jp.10 : Shin-Takatsuo (Kansai Electric Power Company) P 73 㹼 P 78ۑ Jp.11 : Yamasubaru , Saigo (Kyushu Electric Power Company) P 79 㹼 P 86ۑ Jp.12 : Nishiyoshino #1,#2(Electric Power Development Company) P 87 㹼 P 99ۑ Jp.13 : Shin-Nogawa (Yamagata Prefecture) P100 㹼 P108ۑ Jp.14 : Shiroyama (Kanagawa Prefecture) P109 㹼 P114ۑ Jp.15 : Toyomi (Tohoku Electric Power Company) P115 㹼 P123ۑ Jp.16 : Tsuchimurokawa (Tokyo Electric Power Company) P124㹼 P129ۑ Jp.17 : Nishikinugawa (Tokyo Electric Power Company) P130 㹼 P138ۑ Jp.18 : Minakata (Chubu Electric Power Company) P139 㹼 P145ۑ Jp.19 : Himekawa #2 (Chubu Electric Power Company) P146 㹼 P154ۑ Jp.20 : Oguchi (Hokuriku Electric Power Company) P155 㹼 P164ۑ Jp.21 : Doi (Chugoku Electric Power Company) -
Electrical Repairman
VIRGINIA DEPARTMENT OF MINES, MINERALS & ENERGY DIVISION OF MINES ELECTRICAL REPAIRMAN MAINTENANCE FOREMAN & CHIEF ELECTRICIAN CERTIFICATION STUDY GUIDE 2011 Copyright 1997 Commonwealth of Virginia Commonwealth of Virginia Department of Mines, Minerals, and Energy Division of Mines P.O. Drawer 900 Big Stone Gap, VA 24219 (276) 523-8100 Repairman, Maintenance Foreman, and Chief Electrician Certification Study Guide INTRODUCTION The purpose of the Electrical Repairman, Maintenance Foreman and Chief Electrician Certification Study Guide is to assist a qualified applicant in obtaining the Underground Electrical Repairman, Maintenance Foreman and/or Chief Electrician certification(s). The Board of Coal Mining Examiners (BCME) may require certification of persons who work in coal mines and persons whose duties and responsibilities in relation to coal mining require competency, skill or knowledge in order to perform consistently with the health and safety of persons and property. The purpose of the electrical repairman’s section is to assist an applicant who possesses one-year electrical experience in underground coal mining in obtaining an Underground Electrical Repairman certification in accordance with the regulations for the BCME’s certification requirements. Applicants may be given six months credit for electrical educational training from a college, technical school, or vocational school. In addition, each applicant shall pass examinations in first aid and gas detection. The purpose of the maintenance foreman’s section is to assist the electrical repairman who possesses three years of electrical experience in underground coal mining in obtaining a Maintenance Foreman certification. Knowledge of the material in the repairman’s and maintenance foreman’s sections is needed to prepare for the examination. -
Assessing Hydraulic Conditions Through Francis Turbines Using an Autonomous Sensor Device
Renewable Energy 99 (2016) 1244e1252 Contents lists available at ScienceDirect Renewable Energy journal homepage: www.elsevier.com/locate/renene Assessing hydraulic conditions through Francis turbines using an autonomous sensor device * Tao Fu, Zhiqun Daniel Deng , Joanne P. Duncan, Daqing Zhou, Thomas J. Carlson, Gary E. Johnson, Hongfei Hou Pacific Northwest National Laboratory, Energy & Environment Directorate, Richland, WA 99352, United States article info abstract Article history: Fish can be injured or killed during turbine passage. This paper reports the first in-situ evaluation of Received 6 February 2016 hydraulic conditions that fish experienced during passage through Francis turbines using an autonomous Accepted 9 August 2016 sensor device at Arrowrock, Cougar, and Detroit Dams. Among different turbine passage regions, most of Available online 19 August 2016 the severe events occurred in the stay vane/wicket gate and the runner regions. In the stay vane/wicket gate region, almost all severe events were collisions. In the runner region, both severe collisions and Keywords: severe shear events occurred. At Cougar Dam, at least 50% fewer releases experienced severe collisions in Francis turbine the runner region operating at peak efficiency than at the minimum and maximum opening, indicating Turbine evaluation Fish-friendly turbine the wicket gate opening could affect hydraulic conditions in the runner region. A higher percentage of Turbine passage releases experienced severe events in the runner region when passing through the Francis turbines than Turbine operations through an advanced hydropower Kaplan turbine (AHT) at Wanapum Dam. The nadir pressures of the three Francis turbines were more than 50% lower than those of the AHT. -
Design and Analysis of a Kaplan Turbine Runner Wheel
Proceedings of the 3rd World Congress on Mechanical, Chemical, and Material Engineering (MCM'17) Rome, Italy – June 8 – 10, 2017 Paper No. HTFF 151 ISSN: 2369-8136 DOI: 10.11159/htff17.151 Design and Analysis of a Kaplan Turbine Runner Wheel Chamil Abeykoon1, Tobi Hantsch2 1Faculty of Science and Engineering, University of Manchester Oxford Road, M13 9PL, Manchester, UK [email protected] 2Devison of Applied Science, Computing and Engineering, Glyndwr University Mold Road, LL11 2AW, Wrexham, UK Abstract - The demand for renewable energy sources such as hydro, solar and wind has been rapidly growing over the last few decades due to the increasing environmental issues and the predicted scarcity of fossil fuels. Among the renewable energy sources, hydropower generation is one of the primary sources which date back to 1770s. Hydropower turbines are in two types as impulse and reaction where Kaplan turbine is a reaction type which was invented in 1913. The efficiency of a turbine is highly influenced by its runner wheel and this work aims to study the design of a Kaplan turbine runner wheel. First, a theoretical design was performed for determining the main characteristics where it showed an efficiency of 94%. Usually, theoretical equations are generalized and simplified and also they assumed constants of experienced data and hence a theoretical design will only be an approximate. This was confirmed as the same theoretical design showed only 59.98% of efficiency with a computational fluids dynamics (CFD) evaluation. Then, the theoretically proposed design was further analysed where pressure distribution and inlet/outlet tangential velocities of the blades were analysed and corrected with CFD to improve the efficiency of power generation. -
Hydropower Technologies Program — Harnessing America’S Abundant Natural Resources for Clean Power Generation
U.S. Department of Energy — Energy Efficiency and Renewable Energy Wind & Hydropower Technologies Program — Harnessing America’s abundant natural resources for clean power generation. Contents Hydropower Today ......................................... 1 Enhancing Generation and Environmental Performance ......... 6 Large Turbine Field-Testing ............................... 9 Providing Safe Passage for Fish ........................... 9 Improving Mitigation Practices .......................... 11 From the Laboratories to the Hydropower Communities ..... 12 Hydropower Tomorrow .................................... 14 Developing the Next Generation of Hydropower ............ 15 Integrating Wind and Hydropower Technologies ............ 16 Optimizing Project Operations ........................... 17 The Federal Wind and Hydropower Technologies Program ..... 19 Mission and Goals ...................................... 20 2003 Hydropower Research Highlights Alden Research Center completes prototype turbine tests at their facility in Holden, MA . 9 Laboratories form partnerships to develop and test new sensor arrays and computer models . 10 DOE hosts Workshop on Turbulence at Hydroelectric Power Plants in Atlanta . 11 New retrofit aeration system designed to increase the dissolved oxygen content of water discharged from the turbines of the Osage Project in Missouri . 11 Low head/low power resource assessments completed for conventional turbines, unconventional systems, and micro hydropower . 15 Wind and hydropower integration activities in 2003 aim to identify potential sites and partners . 17 Cover photo: To harness undeveloped hydropower resources without using a dam as part of the system that produces electricity, researchers are developing technologies that extract energy from free flowing water sources like this stream in West Virginia. ii HYDROPOWER TODAY Water power — it can cut deep canyons, chisel majestic mountains, quench parched lands, and transport tons — and it can generate enough electricity to light up millions of homes and businesses around the world. -
Low Head Hydro Market Assessment Volume 1
Natural Resources Canada Hydraulic Energy Group Renewable Energy Technologies Sustainable Buildings and Communities CANMET Energy Technology Centre (CETC) 580 Booth Street, 13th Floor Ottawa, Ontario K1A 0E4 Low Head Hydro Market Assessment Volume 1 - Main Report Final H-327842 Rev 0 March 2008 Natural Resources Canada - Low Head Hydro Market Assessment Volume 1 - Main Report Volume 2 - Appendices H-327842.201.01, Rev. 0 Low Head Market Assess - Mainreport.Doc © Hatch 2006/03 a Natural Resources Canada - Low Head Hydro Market Assessment Main Report Table of Contents Report and Estimate Disclaimer List of Acronyms/Abbreviations Hydropower Glossary List of Tables List of Figures 1. Introduction ......................................................................................................................................... 1-1 1.1 Background................................................................................................................................. 1-2 2. Small and Low Head Hydro ................................................................................................................. 2-1 2.1 Small Hydro Defined .................................................................................................................. 2-1 2.2 Low Head Hydro Defined........................................................................................................... 2-1 2.3 Run-of-River Defined .................................................................................................................. 2-2 -
Understanding the Grounding Continuity Test the “Understanding the Product Safety Tests” Series
Weekly Whitepaper Week #533 -23-18 Understanding the Grounding Continuity Test The “Understanding the Product Safety Tests” Series The Grounding Continuity Test (aka Earthing Continuity Test) is one of the most common product safety tests. It is performed on products that have a ground (earth) connection by Certification labs as part of the product Certification and by electrical product manufacturers on 100% of production. Let’s review the elements of this test. Key Definitions: a) Grounding vs. Earthing: Grounding & Earthing are interchangeable terms with identical meaning. In the US & Canada, the term “grounding” is used, while most other countries use the term “earthing”. Accordingly, UL & CSA standards use the term “grounding” while IEC & EN standards use the term “earthing”. This whitepaper uses the term “grounding” which can be replaced throughout with the term “earthing”. b) Protective Current Rating: Some standards specify using a test current level that is based on the “protective current rating”. The protective current rating is the current rating for the device that provides “branch-circuit overcurrent protection”. It is the rating of a circuit breaker or cartridge fuse = this device can be part of the product, but it is usually part of the building electrical system (i.e. the circuit breaker in the breaker panel). • Branch circuit rated circuit breakers and fuses can handle high short-circuit current and are therefore much larger than “supplementary” protectors = the types of circuit breakers and fuses included in many products do not provide branch circuit protection and therefore are not considered when identifying the protective current rating. c) Protective Earth Terminal (P.E.): The P.E. -
7 CONTROL and PROTECTION of HYDRO ELECTRIC STATION 7.1 Introduction 7.1.1 Control System the Main Control And
CHAPTER –7 CONTROL AND PROTECTION OF HYDRO ELECTRIC STATION 7.1 Introduction 7.1.1 Control System The main control and automation system in a hydroelectric power plant are associated with start and stop sequence for the unit and optimum running control of power (real and reactive), voltage and frequency. Data acquisition and retrieval is used to cover such operations as relaying plant operating status, instantaneous system efficiency, or monthly plant factor, to the operators and managers. Type of control equipment and levels of control to be applied to a hydro plant are affected by such factors as number, size and type of turbine and generator. The control equipment for a hydro power plant include control circuits/logic, control devices, indication, instrumentation, protection and annunciation at the main control board and at the unit control board for generation, conversion and transmission operation including grid interconnected operation of hydro stations including small hydro stations. These features are necessary to provide operators with the facilities required for the control and supervision of the station’s major and auxiliary equipment. In the design of these features consideration must be given to the size and importance of the station with respect to other stations in the power system, location of the main control room with respect to the equipments to be controlled and all other station features which influence the control system. The control system of a power station plays an important role in the station’s rendering reliable service; this function should be kept in mind in the design of all control features. -
TURBOMACHINE NOTES 15ME53 TURBO MACHINES Subject Code
TURBOMACHINE NOTES 15ME53 TURBO MACHINES Subject Code: 15ME53 IA Marks: 20 Hours/Week: 05 Exam Hours: 03 Total Hours: 50 Exam Marks: 80 Module - I Introduction: Definition of turbo machine, parts of turbo machines, Comparison with positive displacement machines, Classification, Dimensionless parameters and their significance, Effect of Reynolds number, Unit and specific quantities, model studies. (Note: Since dimensional analysis is covered in Fluid Mechanics subject, questions on dimensional analysis may not be given. However, dimensional parameters and model studies may be given more weightage.) Thermodynamics of fluid flow: Application of first and second law of thermodynamics to turbo machines, Efficiencies of turbo machines, Static and Stagnation states, Incompressible fluids and perfect gases, overall isentropic efficiency, stage efficiency (their comparison) and polytropic efficiency for both compression and expansion processes. Reheat factor for expansion process. 10 Hours expansion process Module –II Energy exchange in Turbo machines: Euler’s turbine equation, Alternate form of Euler’s turbine equation, Velocity triangles for different values of degree of reaction, Components of energy transfer, Degree of Reaction, utilization factor, Relation between degree of reaction and Utilization factor, Problems. General Analysis of Turbo machines: Radial flow compressors and pumps – general analysis, Expression for degree of reaction, velocity triangles, Effect of blade discharge angle on energy transfer and degree of reaction, Effect of blade discharge angle on performance, Theoretical head – capacity relationship, General analysis of axial flow pumps and compressors, degree of reaction, velocity triangles, Problems. 10 Hours Module –III Steam Turbines: Classification, Single stage impulse turbine, condition for maximum blade efficiency, stage efficiency, Need and methods of compounding, Multi-stage impulse turbine, expression for maximum utilization factor. -
Electric Motor-Driven Mine Equipment and Accessories and High-Voltage Longwall Equipment Standards for Underground Coal Mines; Final Rule
Monday, March 11, 2002 Part II Department of Labor Mine Safety and Health Administration 30 CFR Parts 18 and 75 Electric Motor-Driven Mine Equipment and Accessories and High-Voltage Longwall Equipment Standards for Underground Coal Mines; Final Rule VerDate 11<MAY>2000 12:47 Mar 08, 2002 Jkt 197001 PO 00000 Frm 00001 Fmt 4717 Sfmt 4717 E:\FR\FM\11MRR2.SGM pfrm01 PsN: 11MRR2 10972 Federal Register / Vol. 67, No. 47 / Monday, March 11, 2002 / Rules and Regulations DEPARTMENT OF LABOR underground coal mines and allowed the industry’s need for higher voltages the use of high-voltage longwall and the marked improvement in the Mine Safety and Health Administration equipment. However, it did not design and manufacturing technology of specifically focus on the safety issues high-voltage components, MSHA 30 CFR Parts 18 and 75 related to the use of high-voltage developed rules that establish RIN 1219–AA75 longwall equipment. The Agency requirements for safe high-voltage published a new proposed rule (57 FR electric equipment use. This rule Electric Motor-Driven Mine Equipment 39036) on August 27, 1992, related provides improved design requirements and Accessories and High-Voltage specifically to the safe use of high- for longwall equipment, consistent with Longwall Equipment Standards for voltage longwall equipment in existing requirements in 30 CFR part 18, Underground Coal Mines underground coal mines. These rules and contains provisions that also specifically addressed approval accommodate new design technology, AGENCY: Mine Safety and Health requirements for high-voltage electrical are practical, and lessen burdens on the Administration (MSHA), Labor. -
Guideline and Manual for Hydropower Development Vol. 2 Small Scale Hydropower
Guideline and Manual for Hydropower Development Vol. 2 Small Scale Hydropower March 2011 Japan International Cooperation Agency Electric Power Development Co., Ltd. JP Design Co., Ltd. IDD JR 11-020 TABLE OF CONTENTS Part 1 Introduction on Small Scale Hydropower for Rural Electrification Chapter 1 Significance of Small Scale Hydropower Development ..................................... 1-1 Chapter 2 Objectives and Scope of Manual ......................................................................... 2-1 Chapter 3 Outline of Hydropower Generation ..................................................................... 3-1 Chapter 4 Rural Electrification Project by Small-Scale Hydropower ................................. 4-1 Part 2 Designation of the Area of Electrification Chapter 5 Selection of the Area of Electrification and Finding of the Site .......................... 5-1 Part 3 Investigation, Planning, Designing and Construction Chapter 6 Social Economic Research .................................................................................. 6-1 Chapter 7 Technical Survey ................................................................................................. 7-1 Chapter 8 Generation Plan ................................................................................................... 8-1 Chapter 9 Design of Civil Structures ................................................................................... 9-1 Chapter 10 Design of Electro-Mechanical Equipment ......................................................... -
Transfer Switches
POWER SYSTEMS TOPICS 112 Understanding the Withstand and Close-On Ratings for TRANSFER SWITCHES AUTHOR INTRODUCTION MIKE LITTLE Principal Engineer Numerous short circuit current ratings and references exist for transfer Kohler Co. switches that are often confusing and seemingly contradictory. This paper Power Systems Division provides some explanation and clarification to help engineers specify the proper equipment to meet local and national regulations. For an electrical system to operate safely, the design should consider a variety of scenarios where things do not go as planned. One of those scenarios is when a short circuit occurs in the system and causes extremely high currents. An electrical system needs to be designed to safely react to these extreme conditions and, ideally, to continue to function afterwards. This article looks at automatic transfer switches (ATS) which are integral pieces of the power distribution system that help ensure power for home, office, factory or process, when served by an emergency or standby generator in addition to the local utility. This paper also aims to help engineers understand what the withstand and close-on ratings (WCR) means and provide background information to allow the proper sizing and selection of the transfer switch. Two key abilities of the transfer switch are tested under the WCR: the quantified ability to withstand fault currents for a specified period of time while maintaining functionality; and the ability to close into a fault current and continue to operate. Both abilities are critical to allow the electrical system to sustain a fault current with minimal impact. SELECTING AN ATS I. UNDERSTAND DAMAGES CAUSED BY HIGH II.