05-123 Empty Passenger Train 4356, Overrun of Conditional Stop Board
Total Page:16
File Type:pdf, Size:1020Kb
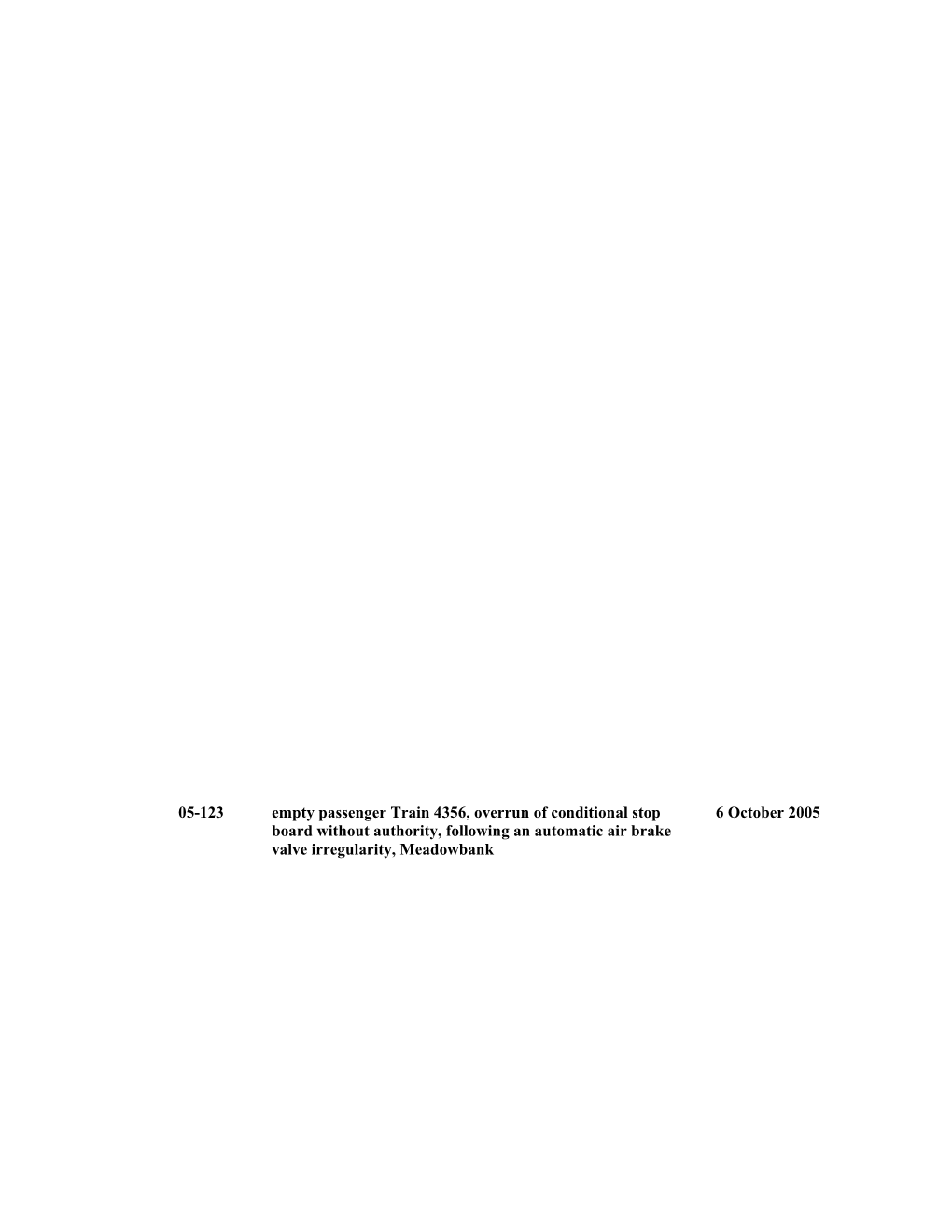
Load more
Recommended publications
-
NZ TRANSPORT AGENCY NATIONAL OFFICE WAKA KOTAHI 50 Victoria Street Private Bag 6995 Wellington 6141 New Zealand T 64 4 894 5400 F 64 4 894 6100
NZ TRANSPORT AGENCY NATIONAL OFFICE WAKA KOTAHI 50 Victoria Street Private Bag 6995 Wellington 6141 New Zealand T 64 4 894 5400 F 64 4 894 6100 www.nzta.govt.nz 9 November 2015 Tony Randle [email protected] Dear Tony Request made under the Official Information Act 1982 Thank you for your email of 9 October 2015 requesting the following information under the Official Information Act 1982: a. the source document for the cost estimate of $2.3Million to be provided to the GWRC to "improve the Wairarapa Line" (although you stated it was actually for improving the Hutt Line). b. a description of the work that the $2.3Million was to support (I understand the GWRC claimed the funding is to "go toward replacing corroded rail and rolling out more powerful DFB diesel locomotives" but that NZTA is only funding track replacement). c. the funding memo notes that poor track causes an average loss of travel time of 10 minutes generates negative travel time benefits of approximately $5 million per annum, based on an average travel time value of $5 per hour (combined peak and off peak values), delay of ten minutes and 6,382,000 passenger trips on the Hutt Valley Line" for all commuters. A copy of the source that outlines the 10 minutes estimate for travel time loss currently affecting 6,382,000 passenger trips on the Hutt Valley Line that will be address by this funding investment to be provided. d. any meeting notes or correspondence associated with the $2,290,000 investment by the NZTA to the GWRC to "bring forward and substantially address the deferred maintenance" as outlined in the NZTA Memo. -
Evaluation of Occupational Noise Exposure Levels on the Wellington Suburban Tranz Metro Rail Service
Evaluation of occupational noise exposure levels on the Wellington Suburban Tranz Metro Rail Service 1 Ka’isa Beech and 2 Stuart J McLaren 1 Advanced student at Massey University and Wellington Suburban On-board Staff Member, KiwiRail, Wellington 2 School of Public Health, Massey University, Wellington 2 Email: [email protected] Abstract An occupational noise evaluation study was carried out by Massey University students on locomotive engineers and on-board staff on the two main train sets operating on the Wellington Rail Suburban Network. All measurement results conducted as part of the study show full compliance with the criteria for workplace noise exposure prescribed within the Health and Safety in Employment Regulations 1995. The health and safety noise criterion level permits a maximum dose of 100% which is equivalent to 85 dB LAeq for a normalised 8 hour working day. The highest measured sound exposure was 13% of the total permitted exposure. All occupational noise measurements were observed and written accounts were taken by the three person investigation team. Observations revealed atypical behaviour of one participant which likely compromised one set of readings. This atypical result was removed from the analysis and therefore did not alter the study conclusions. Regardless, such observed behaviour from the study team, reinforces the value of observed real time field monitoring during collection of data. Original peer-reviewed student paper 1. Introduction and purpose of About Ka’isa Beech assessment Age 23, is training to be a The Tranz Metro Rail Passenger Service is operated by Train Traffic Controller KiwiRail and funded by the Greater Wellington Regional with KiwiRail. -
Restoration of the Rimutaka Incline Railway Development Proposal
Restoration of the Rimutaka Incline Railway Development Proposal and Environment Management Plan: Maymorn to Summit Executive Summary Rimutaka Incline Railway Heritage Trust November 2011. Photo: S class locomotive and train at Summit circa 1880. William Williams, Alexander Turnbull Library Page 1 of 46 Development Proposal and Environment Management Plan v2 Preface This document is an Executive Summary form of the Development Proposal and Assessment of Environmental Effects, which canvasses the issues which are considered to be important in relation to deciding whether approval should be given to reinstating the Rimutaka Incline Railway. This document provides a summary, via answers to key questions, concerning elements of the proposal and the main environmental, planning, design and construction issues. Information shown on maps and plans in this document are indicative only. Reference should be made to detailed maps and plans where referenced. Page 2 of 46 Development Proposal and Environment Management Plan v2 Contents Restoration of the Rimutaka Incline Railway .................................................................................. 1 Development Proposal and Environment Management Plan: Maymorn to Summit ....................... 1 Executive Summary ......................................................................................................................... 1 Preface ......................................................................................................................................... 2 Contents -
Report 99-104 Train 1613 Passenger Safety Incident Featherston 3 April
Report 99-104 Train 1613 passenger safety incident Featherston 3 April 1999 Abstract On Saturday 3 April 1999, Train 1613, the southbound Masterton to Wellington passenger service, departed from Featherston while a scout party and an adult passenger were still loading their gear into the van. Three scouts were left on the platform and a fourth scout and the adult travelled to Upper Hutt in the unlit van. The scouts were at risk as they either alighted from, or attempted to board, the moving train during departure. The guard was unaware of the scouts’ presence in the van. The incident occurred due to a failure to ensure passenger safety prior to the departure of the train. A safety issue identified was the lack of adequate procedures to ensure passenger safety prior to giving right of way. One safety recommendation was made to the operator. The Transport Accident Investigation Commission is an independent Crown entity established to determine the circumstances and causes of accidents and incidents with a view to avoiding similar occurrences in the future. Accordingly it is inappropriate that reports should be used to assign fault or blame or determine liability, since neither the investigation nor the reporting process has been undertaken for that purpose. The Commission may make recommendations to improve transport safety. The cost of implementing any recommendation must always be balanced against its benefits. Such analysis is a matter for the regulator and the industry. These reports may be reprinted in whole or in part without charge, providing acknowledgement is made to the Transport Accident Investigation Commission. -
Rail in Auckland
Overview and Turnaround Plan Kimberley Brady, Communications Manager Recent rail history NZ RAILWAYS NZ RAILWAYS 1982 CORPORATION Limited liability company under Government 1990 NZ RAIL LTD ownership Privatised; outsourced: Mechanical Services to 1993 TRANZ RAIL HOLDINGS United Group and Track Operations to Transfield Services 2003 TOLL HOLDINGS LTD Bought business Government purchased infrastructure arm; in- 2004 ONTRACK sourced maintenance Government purchased operations businesses; 2008 KIWIRAIL reintegration of industry The KiwiRail structure Jim Quinn Chief Executive David Walsh Karen Paterson Graeme Docherty Nicola Brown Chief Financial Officer General Manager Chief Information General Manager Legal & Governance Officer Human Resources Iain Hill Thomas Davis Lloyd Major Dr Deborah Hume Rick van Barneveld General Manager General Manager General Manager General Manager General Manager KiwiRail Freight KiwiRail Interislander Mechanical KiwiRail Passenger KiwiRail Network Each week, train control operations manage the movement of: • 900 freight trains • 52 inter-city passenger trains • Approximately 2,200 suburban passenger services in Wellington • Approximately 1,490 suburban passenger services in Auckland In a year, the Interislander manages 5,500 sailings carrying: • 859,000 passengers • 59,000 rail wagons • 56,000 trucks • 223,000 cars Traffic volumes Freight Nett Nett Ferry Carried Tonnes Tonnes % Passengers 891,234 Bulk 8,026,424 56% Export 4,420,040 31% Vehicle 221,857 Domestic 1,965,536 14% Rail LM 819,262 Total 14,412,000 100% -
Tranz Metro Communications
Tranz Metro Communications Customer Communications review for the Johnsonville Line 1. Purpose The purpose of this document is 2. Background “-Services on the JVL are experiencing delays of approximately 10 minutes due to slippery track conditions. Updates to follow.” This is an all too familiar text to Johnsonville Line passengers over the past year and a half. 1 M:\National Passenger\Planning and Performance\... • During a slip disruption, RTI boards said shuttle between Ngaio and Johnsonville and buses between Ngaio and Wellington. The word shuttle is confusing. Also, RTI boards not clear on whether or not buses or trains are running. Below are some of the suggestions we have received from passengers about how we can communicate to them better and more efficiently. • It could be grateful if you could run an audit to ensure that all delays are going into the system. • Many of the delays were put on the Tranz Metro text system as "operational reasons", but when he asked train staff why they were late, the answer was slippery tracks. In our view, the information given to passengers needs to be as accurate and consistent as possible. • Surely if the system temporarily cannot show the correct information it would be better switched off. • It would be better if you said "train" instead of "shuttle", because it is not clear whether a "shuttle" means a bus or a train, In fact, everybody went to wait at the bus stop and we only made it because the driver saw us and happened to pick us up. 4. Proposal To try and minimise the effect that delays have on the on time performance of the Johnsonville Line, KiwiRail and Greater Wellington Regional Council trialled a new morning and afternoon peak timetable last October that proved successful. -
Auckland Metro Rail Network Electrification
AUCKLAND METRO RAIL NETWORK ELECTRIFICATION Heritage Assessment Table of Contents 1.0 Executive Summary 3 2.0 Introduction 4 3.0 Heritage Significance 6 4.0 Western Line (Newmarket–Swanson) 12 5.0 Britomart–Penrose–Onehunga 18 6.0 Penrose–Papakura (including Manukau Branch) 26 7.0 Eastern Diversion (Britomart–Westfield) 32 8.0 Conclusion 35 9.0 Appendices APPENDIX 1: Identification of Groups / 37 Individuals / Stakeholders for Consultation APPENDIX 2: Historical Chronology 38 APPENDIX 3: Policy for Government 66 Departments’ Management of Historic Heritage APPENDIX 4: Draft Areas of Visual Sensitivity 75 for Discussion APPENDIX 5: Map of Study Area 89 APPENDIX 6: Map of Railway Lines 90 APPENDIX 7: Items of Potential Significance (P*) 91 to be Altered or Demolished AUCKLAND METRO-RAIL ELECTRIFICATION: Heritage Assessment Page 2 of 92 1.0 Executive Summary This heritage assessment has been prepared to identify the built rail heritage in the Auckland Metro Rail network and to understand the heritage issues associated with the electrification of the network. It is supported and underpinned by the Policy for Government Departments’ Management of Historic Heritage 2004. The overall heritage significance of the various lines is discussed and the study further identifies 59 heritage ‘items’ including stations and associated structures on a 3 tiered scale according to their identified (I), potential (P) and adjacent significance (A), (see Section 3.0) Based on the historical chronology, (see APPENDIX 2), the assessment follows in consecutive order along the rail lines as they developed historically, section 4.0 Western Line, section 5.0 Britomart-Penrose- Onehunga, section 6.0 Penrose-Papakura (including Manukau Branch), and section 7.0 Eastern Diversion (Britomart-Westfield). -
Annual Report 2013-2014
F.18a 2014 ANNUAL REPORT KiwiRail Overview From 1 January 2013, railway business activities were separated from rail land holdings as a result of a Government restructure carried out to put the business on a more commercial footing. The former parent, New Zealand Railways Corporation (NZRC), continued to hold the 18,000 hectares of rail network land, from which no financial return is expected. The business activities were transferred to a new State Owned Enterprise, KiwiRail Holdings Ltd. NZRC is managed by KiwiRail Holdings Ltd under a long-term nominal fee management agreement, and therefore has limited operational activities. We conduct business in the following areas: Whangarei Logistics: We are a logistics provider to customers who use Dargaville our rail freight and ferry services. Each week, approximately 900 freight trains operate on the KiwiRail network. They carry AUCKLAND bulk freight such as coal and milk, containerised import or export freight to and from ports and full container loads for Hamilton Tauranga Kawerau New Zealand freight forwarders. Three ferries provide the inter- Te Kuiti Kinleith island supply chain link with more than 4000 sailings a year. New Plymouth Taumarunui Shipping: We are an owner and operator of shipping services Stratford Napier operating under the Interislander brand. Of our three ferries, Waiouru Wanganui two are owned and one is chartered. Dannevirke Palmerston North Otaki Tourism Experiences: We provide tourism experiences by Masterton Featherston rail and sea. Three long-distance rail passenger trains - the Picton WELLINGTON Blenheim TranzAlpine, Coastal Pacific and Northern Explorer - provide Westport daily, tri-weekly or seasonal services. Train charters provide Reefton specific rail experiences and service the cruise market. -
We Move People and Freight
F.18a ANNUAL INTEGRATED We move people REPORT 2016 and freight Rose Pettigrew, Terminal Manager Operations and Emma–Jane Wells, Rail Operator 2 | KIWIRAIL ANNUAL INTEGRATED REPORT 2016 Contents Overview of our business Management review Business review At a glance 4 Our first annual integrated Performance of our report 8 business units 16 Who we are and what we do 6 Integrated reporting concept: Value creation process 9 Chairman’s message to stakeholders 10 Our progress 2010–2016 12 Chief Executive’s report 14 Capitals review Governance review Statutory review How KiwiRail creates value 18 The KiwiRail Board 42 Financial statements 48 Helping to grow our exports 20 The KiwiRail Executive Team 44 Independent Auditor’s report 82 Financial 21 How we are governed 46 Key Performance Indicators 84 Increasing the value Vote Transport 86 of tourism 23 Employee remuneration 87 People 24 Directory 88 High Performance High Engagement 27 Assets 28 Inland ports and freight hubs 30 Know–how 31 eProtect: Innovative safety initiative helps save lives 33 Relationships 34 Working with communities to deliver results 36 Environmental 37 Delivering cost and energy savings 39 Outlook 41 KIWIRAIL ANNUAL INTEGRATED REPORT 2016 | 3 Overview of our business: At a glance Highlights from FY16 Awards Relationships • Chartered Institute of Logistics • 11% growth in import and export markets, and Transport “Most Innovative underpinned by strong relationships with ports Public Transport project” for and customers electrification and re–signalling of Financial the Auckland -
A Lowering Carbon Pilot – Summary Report
The Kapiti Coast Day Out A lowering carbon pilot August 2009 Summary Report prepared by the Hikurangi Foundation In cooperation with south- 1 CONTENTS Introduction: The story of Carbon and Tourism Page 2 Background: The Kapiti Coast Day Out Pilot Page 3 Let the Day Begin Page 4 Sharing Stories Page 5-8 Conclusions: What we now know Page 9 Did it Work? Page 10 Now what? Next steps. Page 11 Contacts Page 12 This report is a summary. A full technical report is available at www.hikurangi.org.nz SUPPORTED BY Nyco Chocolates, Paraparaumu Visitor Information Centre, Lembas Café, Waterfront Bar & Kitchen, Coastlands, Lindale Farm Walk. The Hikurangi Foundation is made possible by funding from the Tindall Foundation and The Todd Foundation. 2 Introduction: The story of carbon and tourism This is a modest but important story from a lovely part of Aotearoa – the Kapiti Coast – an hour north of Wellington, and an Tourism contributes $20 billion every year in economic activity. hour south-west from Palmerston North. This story has the But tourism is responsible for 6% of total carbon emissions (not potential to benefit every New Zealander and it goes like this; counting those from international aviation), and, it’s the fastest smart action can deliver great holidays, strong local economies, growing sector in terms of emissions in New Zealand. Not many and less carbon emissions. people know that three quarters of the carbon footprint of tour- ism here is from Kiwis on holiday, not international tourists. In The story of carbon and tourism turn, three quarters of that is from the transport we use (mainly cars and domestic planes). -
Wellington Region Rail Programme
Greater Wellington Regional Council and KiwiRail (ONTRACK and Tranz Metro) Wellington are working closely Region Rail together to bring passengers more Programme reliable and frequent train services. ellington ohnsonville apiti For more information go to: www.ontrack.govt.nz www.gw.govt.nz We’re improving the Wellington railway system to provide more reliable and frequent passenger services. Wellington Station Entry Region Rail We are adding another main line into Wellington Railway Station Programme to reduce congestion. Currently there is a bottleneck Introducing a fleet of new electric trains – the where the multiple tracks Matangi trains. These will begin to arrive in 2010. reduce down to just two main Making tunnels on the Johnsonville line larger lines in the rail yards. We will so the new trains can use the line. This work is install a third line which will now largely complete. carry trains into the station in Extending electrification and double tracked the morning and out in the lines to take commuter services to Waikanae. evening. Adding another line into Wellington Railway Station to reduce delays. February – June 2009 – Dig foundation holes Installing new power supply equipment and – Erect steel traction poles to carry overhead wires railway signalling to accommodate the new trains. – Begin building a retaining wall near the Aotea Quay overbridge Improving a number of platforms and station – Install drains for the new tracks facilities. Building additional train storage and upgrading From July 2009 WELLINGTON STATION ENTRY – Start laying new tracks maintenance facilities. North – Install new signalling Current Situation The trains have been ordered and will start arriving from 2010. -
Final Report RO-2016-101: Signal Passed at Danger Leading to Near Collision, Wellington Railway Station, 28 May 2016
Final report RO-2016-101: Signal passed at danger leading to near collision, Wellington Railway Station, 28 May 2016 The Transport Accident Investigation Commission is an independent Crown entity established to determine the circumstances and causes of accidents and incidents with a view to avoiding similar occurrences in the future. Accordingly it is inappropriate that reports should be used to assign fault or blame or determine liability, since neither the investigation nor the reporting process has been undertaken for that purpose. The Commission may make recommendations to improve transport safety. The cost of implementing any recommendation must always be balanced against its benefits. Such analysis is a matter for the regulator and the industry. These reports may be reprinted in whole or in part without charge, providing acknowledgement is made to the Transport Accident Investigation Commission. Final Report Rail inquiry RO-2016-101 Signal passed at danger leading to near collision Wellington Railway Station 28 May 2016 Approved for publication: December 2017 Transport Accident Investigation Commission About the Transport Accident Investigation Commission The Transport Accident Investigation Commission (the Commission) is a standing Commission of inquiry and an independent Crown entity responsible for inquiring into maritime, aviation and rail accidents and incidents for New Zealand, and co-ordinating and co-operating with other accident investigation organisations overseas. The principal purpose of its inquiries is to determine the circumstances and causes of occurrences with a view to avoiding similar occurrences in the future. Its purpose is not to ascribe blame to any person or agency or to pursue (or to assist an agency to pursue) criminal, civil or regulatory action against a person or agency.