Precision Motion Control Application & Selection Guide
Total Page:16
File Type:pdf, Size:1020Kb
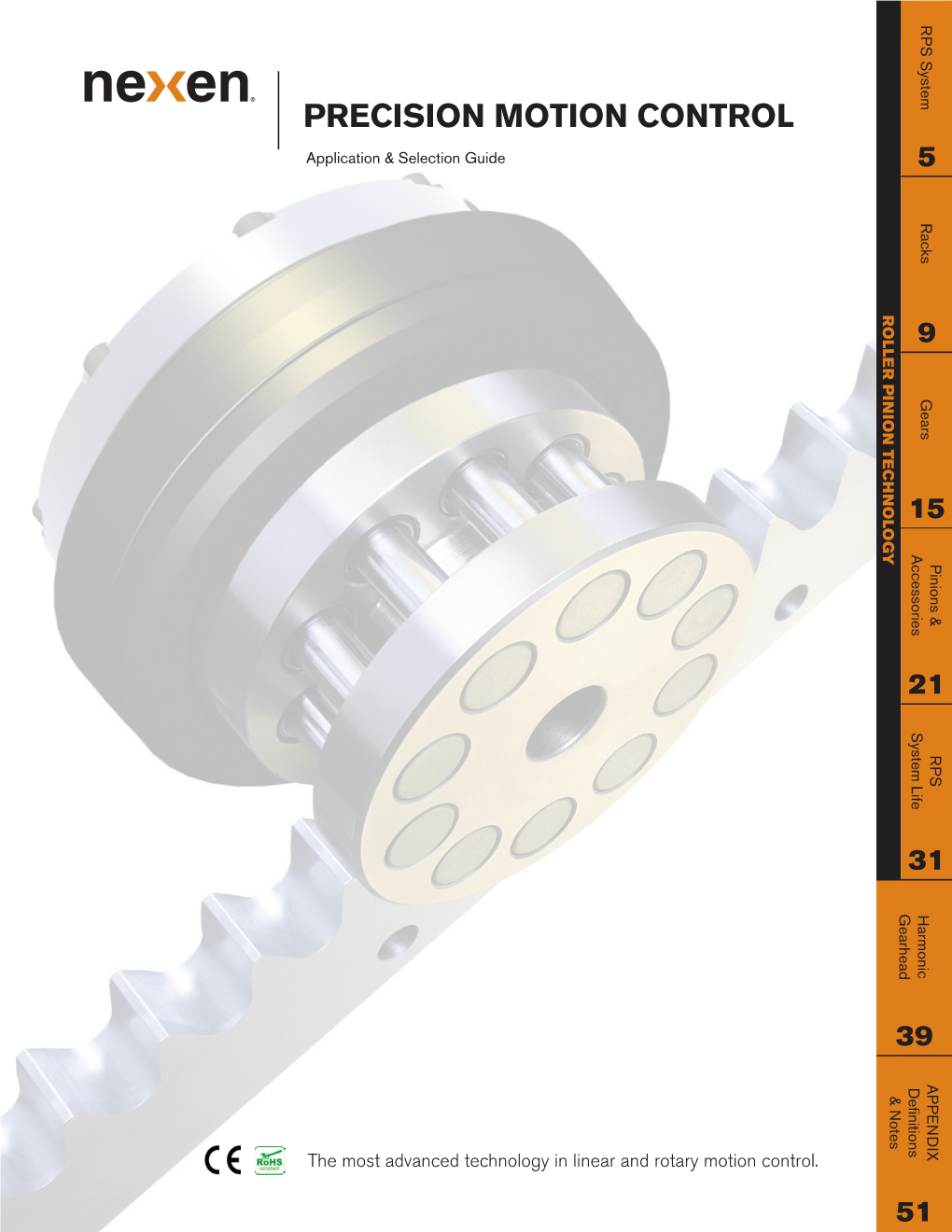
Load more
Recommended publications
-
Design and Development of Open Differential for Transmission System of Quad Bike
International Research Journal of Engineering and Technology (IRJET) e-ISSN: 2395-0056 Volume: 05 Issue: 12 | Dec 2018 www.irjet.net p-ISSN: 2395-0072 Design and Development of Open Differential for Transmission System of Quad Bike Utkarsha Chaudhari1, Prathamesh Sangelkar2, Prajval Vaskar3 1,2,3Department of Mechanical Engineering, Sinhgad Academy of Engineering, Kondhwa ---------------------------------------------------------------------***---------------------------------------------------------------------- Abstract – A differential is an important torque 2. ANALYTICAL CALCULATIONS transmitting device in most of the rear wheel drive vehicles. An ATV is a vehicle which is used to ride in off-road terrains; 2.1 Primary Calculations for Gear Reduction hence continuous application of traction is a vital factor which showcases its performative aspect. The paper describes Input Data: designing and manufacturing an open differential for an off road ATV (Quad Bike) so that the vehicle maneuvers sharp Turning radius of vehicle: - 3m corners without losing traction to the driving wheels. Rear Track width: - 40” Rear tire diameter: - 23” Key Words: Open differential, traction difference, ANSYS, CREO, gear, pinion, centre pin. 1. INTRODUCTION A differential is a gear train with three shafts that has the property that the rotational speed of one shaft is the average of the speeds of the others, or a fixed multiple of that average. In automobiles, the differential allows the outer drive wheel to rotate faster than the inner drive wheel during a turn. This is necessary when the vehicle turns, making the wheel that is travelling around the outside of the turning curve roll farther and faster than the other. The average of the rotational speed of the two driving wheels equals the input rotational speed of the drive shaft. -
Chain Drives 759
Chain Drives 759 C H A P T E R 21 Chain Drives 1. Introduction. 2. Advantages and Disadvantages of Chain Drive over Belt or Rope Drive. 3. Terms Used in Chain Drive. 4. Relation Between Pitch and Pitch Circle Diameter. 5. Velocity Ratio of Chain Drives. 6. Length of Chain and Centre Distance. 7. Classification of Chains. 8. Hoisting and Hauling Chains. 9. Conveyor Chains. 10. Power Transmitting Chains. 11. Characteristics of Roller Chains. 12. Factor of Safety for Chain Drives. 21.1 Introduction 13. Permissible Speed of We have seen in previous chapters on belt and rope Smaller Sprocket. 14. Power Transmitted by drives that slipping may occur. In order to avoid slipping, Chains. steel chains are used. The chains are made up of number of 15. Number of Teeth on the rigid links which are hinged together by pin joints in order Smaller or Driving Sprocket or Pinion. to provide the necessary flexibility for wraping round the 16. Maximum Speed for driving and driven wheels. These wheels have projecting Chains. teeth of special profile and fit into the corresponding recesses 17. Principal Dimensions of Tooth Profile. in the links of the chain as shown in Fig. 21.1. The toothed 18. Design Procedure for wheels are known as *sprocket wheels or simply sprockets. Chain Drive. The sprockets and the chain are thus constrained to move together without slipping and ensures perfect velocity ratio. * These wheels resemble to spur gears. 759 760 A Textbook of Machine Design Fig. 21.1. Sprockets and chain. The chains are mostly used to transmit motion and power from one shaft to another, when the centre distance between their shafts is short such as in bicycles, motor cycles, agricultural machinery, conveyors, rolling mills, road rollers etc. -
Oscillatory Motion Leadscrews • for Applications Requiring Linear Oscillatory Motion Over a Fixed Path
© 1994 by Alexander H. Slocum Precision Machine Design Topic 21 Linear motion actuators Purpose: This lecture provides an introduction to the design issues associated with linear power transmission elements. Major topics: • Error sources • Belt drives • Rack and pinion drives •Friction drives • Leadscrews • Linear electric motors "...screw your courage to the sticking-place, And we'll not fail" Shakespeare 21-1 © 1994 by Alexander H. Slocum Error sources: • There are five principal error sources that affect linear actuator' performance: • Form error in the device components. • Component misalignment. • Backlash. • Friction. • Thermal effects • These systems often have long shafts (e.g., ballscrews). • One must be careful of bending frequencies being excited by rotating motors. 21-2 © 1994 by Alexander H. Slocum Belt drives • Used in printers, semiconductor automated material handling systems, robots, etc. • Timing belts will not slip. • Metal belts have greater stiffness, but stress limits life: σ = Et 2ρ • Timing belts will be the actuator of choice for low cost, low stiffness, low force linear motion until: •Linear electric motor cost comes down. • PC based control boards with self-tuning modular algorithms become more prevalent. • To prevent the belts' edges wearing on pulley flanges: • Use side rollers to guide timing belt to prevent wear caused by flanged sheaves: load Guide roller Belt 21-3 © 1994 by Alexander H. Slocum Rack and pinion drives Motor Pinion Rack • One of the least expensive methods of generating linear motion from rotary motion. • Racks can be placed end to end for as great a distance as one can provide a secure base on which to bolt them. -
Martin Machined Gear Rack Brochure
Locations Corporate Offices Sales & Manufacturing USA Arlington, TX 817-258-3000 (FAX 817-258-3333) Regional Manufacturing Plants Albemarle, NC 704-982-9555 (FAX 704-982-9599) Stocked in Steel Atlanta, GA 404-292-8744 (FAX 404-292-7771) Burleson, TX 14½º & 20º PA 817-295-7151 (FAX 817-447-3840) MACHINED Danielsville, PA 610-837-1841 (FAX 610-837-7337) MTO Capabilities Ft. Worth, TX 817-258-3000 (FAX 817-258-3173) Up to 12' long Montpelier, OH GEAR RACK 419-485-5515 (FAX 419-485-3565) Sacramento, CA 916-441-7172 (FAX 916-441-4600) Branch Manufacturing Plants Boston, MA 508-634-3990 (FAX 508-634-3998) Charlotte, NC 704-394-9111 (FAX 704-394-9122) Chicago, IL 847-298-8844 (FAX 847-298-2967) Denver, CO 303-371-8466 (FAX 303-371-7116) Houston, TX 713-849-4330 (FAX 713-849-4807) Kansas City, MO 816-231-5575 (FAX 816-231-1959) Los Angeles, CA 323-728-8117 (FAX 323-722-7526) Minneapolis, MN 952-829-0623 (FAX 952-944-9385) Nashville, TN 615-871-4730 (FAX 615-871-4125) Pittsburgh, PA 724-452-4555 (FAX 724-452-5794) Portland, OR 503-223-7261 (FAX 503-221-0203) Tampa, FL 813-623-1705 (FAX 813-626-8953) Manufacturing Only Abilene, TX • Clarksville, TX Dallas, TX • Mansfield, TX Paragould, AR Cambridge, Ontario 519-621-0546 (FAX 519-621-4413) Edmonton, Alberta 780-450-0888 (FAX 780-465-0079) CANADA Mississauga, Ontario 905-670-1991 (FAX 905-670-2110) Guadalajara, JAL +52 33-3283-1188 (FAX +52 33-3271-8450) Monterrey, N.L. -
Basic Fundamentals of Gear Drives
Basic Fundamentals of Gear Drives Course No: M06-031 Credit: 6 PDH A. Bhatia Continuing Education and Development, Inc. 22 Stonewall Court Woodcliff Lake, NJ 07677 P: (877) 322-5800 [email protected] BASIC FUNDAMENTALS OF GEAR DRIVES A gear is a toothed wheel that engages another toothed mechanism to change speed or the direction of transmitted motion. Gears are generally used for one of four different reasons: 1. To increase or decrease the speed of rotation; 2. To change the amount of force or torque; 3. To move rotational motion to a different axis (i.e. parallel, right angles, rotating, linear etc.); and 4. To reverse the direction of rotation. Gears are compact, positive-engagement, power transmission elements capable of changing the amount of force or torque. Sports cars go fast (have speed) but cannot pull any weight. Big trucks can pull heavy loads (have power) but cannot go fast. Gears cause this. Gears are generally selected and manufactured using standards established by American Gear Manufacturers Association (AGMA) and American National Standards Institute (ANSI). This course provides an outline of gear fundamentals and is beneficial to readers who want to acquire knowledge about mechanics of gears. The course is divided into 6 sections: Section -1 Gear Types, Characteristics and Applications Section -2 Gears Fundamentals Section -3 Power Transmission Fundamentals Section -4 Gear Trains Section -5 Gear Failure and Reliability Analysis Section -6 How to Specify and Select Gear Drives SECTION -1 GEAR TYPES, CHARACTERISTICS & APPLICATIONS The gears can be classified according to: 1. the position of shaft axes 2. -
General Notes on Pinion Transmission Systems
GENERAL NOTES ON PINION TRANSMISSION SYSTEMS The running of a Pinion transmission gets better and better during the first 1000 km. Also, the running-in period may be significantly shorter depending on the type of rider. The surfaces of various parts become smooth and all components adjust to one another ideally. A transmission always has the basic property of giving the impression that it runs less smoothly in the high RUNNING IN THE gears. This is due to the transmission ratio in the transmission, and it is just a perceived effect. In actual fact, a Pinion transmission runs with silky smoothness in all gears. TRANSMISSION A slight difference in the smooth-running properties between individual gears depends on the particular seal friction. The seal friction varies, firstly, as a result of production and, secondly, depending on the formation of the lubrication film. However, during riding, this minimum level of friction can be disregarded. Clean your transmission from the outside using soap solution and a moist cloth. Bicycle care products or protection sprays can also be used. If you use high-pressure cleaners, please keep a TRANSMISSION CARE minimum distance of 50 cm from the transmission. From time to time, grease the inside of the gear shift box with lubricating grease that does not have any gumming properties. IMPORTANT: never retighten the special screws on the housing. These have been screwed in at the factory to the correct torque and then locked. This is the only way to guarantee that the transmission will remain leak-tight on a continuous basis. RANGE OF Pinion transmissions are used all over the world – under almost any conditions, no matter how challenging. -
AN EXPERIMENTAL INVESTIGATION of CHURNING POWER LOSSES of a GEARBOX THESIS Presented in Partial Fulfillment of the Requirements
AN EXPERIMENTAL INVESTIGATION OF CHURNING POWER LOSSES OF A GEARBOX THESIS Presented in Partial Fulfillment of the Requirements for The Degree of Master of Science in the Graduate School of the Ohio State University By Joseph H. Polly, B.S. Graduate Program in Mechanical Engineering ***** The Ohio State University 2013 Thesis Committee: Dr. Ahmet Kahraman, Advisor Dr. Donald Houser © Copyright by: Joseph H. Polly 2013 ABSTRACT In this study, load-independent (spin) power losses of a gearbox operating under dip-lubrication conditions are investigated experimentally. A family of final drive helical gear pairs from an automotive transmission is considered as the example for this investigation. A dedicated gearbox is designed and fabricated to operate a single gear or a gear pair under given speed conditions. The test gearbox is incorporated with a high- speed test bed with power loss measurement capability. A test matrix that consists of sets of tests with (i) single spur, helical gears, or disks with no teeth, and (ii) helical gear pairs of varying gear ratios is executed with three different transmission fluids at various temperatures and immersion depths. Power losses from single gear and gear pair tests at identical operating conditions are compared to break down the total spin loss to its main components, namely gear drag loss, gear mesh pocketing loss, and bearing/seal loss. In addition, the space around the gears within the gearbox will be altered to quantify any influences of enclosures and peripheral shrouds on the spin losses of a rotating gear. ii Dedicated to my family: past, present, and future iii ACKNOWLEDGEMENTS I would like to offer the highest level of gratitude to my advisor, Dr. -
Topic 6 Power Transmission Elements II
FUNdaMENTALS of Design Topic 6 Power Transmission Elements II © 2008 Alexander Slocum 6-0 1/1/2008 Power Transmission Elements II were scaled to create accurate gears for industry and this also helped power the industrial revolution. Screws & gears are transmission elements that warrant a special place in power transmission systems We may never know who the great minds were because of the huge range of power levels at which they who actually had the moment of brilliance to invent are applied and the very high transmission ratios they screws and gears, but we salute these great minds; for can achieve. without screws and gears, which still serve us today, society would grind to a halt, and industry would be The first screws were used perhaps by threaded! Archimedes in 200 BC as pumps to lift water from a river to a field. It is not known when the first power By considering FUNdaMENTAL principles, you screw for lifting a solid load was invented, but it was will better be able to separate marketing hype from likely over a thousand years ago. Like many technolo- engineering reality. Remember Maudslay’s Maxims, gies, the military was a powerful catalyst for develop- and apply them in the context of: ment. One could imagine designers wondering how they could convert rotary motion into linear motion, or • Kinematics: motion, accuracy, space how they could amplify force or torque. With gunpow- • Dynamics: forces, speeds, life der came the need for the manufacture of better gun bar- • Economics: design, build, maintain rels which propelled the fledgling machine tool industry. -
PRECISION MOTION CONTROL the ROLLER PINION System
PRECISION MOTION CONTROL ThE Roller Pinion System Application and Selection Guide ii Index Introducing Innovative, High-Performance, Motion Control Technology ......................................................................................................... 1 The Nexen RPS Advantage .......................................................................................................................................................................... 2 How the RPS Technology Works .............................................................................................................................................................. 3 Applications ................................................................................................................................................................................................... 4 RPS Linear Drive Selection Process .................................................................................................................................................................................. 5 Models, Sizes and Specifications ..................................................................................................................................................... 7 Dimensions and Product Numbers ..................................................................................................................................................... 8 RPG Rotary Drive Selection Process ................................................................................................................................................................................ -
Design and Analysis of Differential Gear Box Used in Heavy Vehicle
Vol.2, No.1 ISSN Number (online): 2454-9614 Proceedings of International Conference on Recent Trends in Mechanical Engineering-2K15(NECICRTME-2K15), 20th – 21st November,2015 DESIGN AND ANALYSIS OF DIFFERENTIAL GEAR BOX USED IN HEAVY VEHICLE N.Vijayababu#1, Ch.Sekhar#2 Narasaraopeta Engineering College, JNT University, Kakinada., [email protected] [email protected] Abstract common use is in motor vehicles, where the transmission adapts the output of the internal Differential is used when a vehicle takes a turn, combustion engine to the drive wheels. Such engines the outer wheel on a longer radius than the inner need to operate at a relatively high rotational speed, wheel. The outer wheel turns faster than the inner which is inappropriate for starting, stopping, and wheel that is when there is a relative movement slower travel. The transmission reduces the higher between the two rear wheels. If the two rear engine speed to the slower wheel speed, increasing wheels are rigidly fixed to a rear axle the inner torque in the process. Transmissions are also used on wheel will slip which cause rapid tire wear, pedal bicycles, fixed machines, and anywhere else steering difficulties and poor load holding. rotational speed and torque needs to be adapted. Differential is a part of inner axle 1.1 DIFFERENTIAL GEAR BOX housing assembly, which includes the differential rear axles, wheels and bearings. The differential A differential is a device, usually but not necessarily consists of a system of gears arranged in such a employing gears, capable of transmitting torque and way that connects the propeller shaft with the rear rotation through three shafts, almost always used in axles. -
Handbook for Chain Engineering Design and Construction / Examples of Calculation
Version 2010 Handbook for chain engineering Design and construction / Examples of calculation www.iwis.com Tel: +49 89 76909-1500 Fax: +49 89 76909-1198 [email protected] www.iwis.com Power transmission chain A Chain wheels B Joh. Winklhofer Beteiligungs GmbH & Co. KG Company Headquarters, Parent of the independent subsidiary companies, Management Organisation of the Internationally operating companies iwis motorsysteme iwis antriebssysteme iwis antriebssysteme iwis agrisystems chain drives chain GmbH & Co. KG GmbH & Co. KG GmbH (Div.) Layout of Subsidiary for the automotive Subsidiary for the industrial A distribution and service Competence centre for the sector, for example chain drives sector, high precision chains and company within the chain iwis agricultural chain program for C and mass balance drives as well drive systems for a wide range drive industry combines and maize harvesting as oil pump drives and gear of applications box chains chain drives chain General information München (DE) München (DE) Wilnsdorf (DE) Sontra (DE) Landsberg (DE) Indianapolis (US) Indianapolis (US) Indianapolis (US) D Indianapolis (US) Langley (CA) Langley (CA) Langley (CA) Pune (IN) Johannesburg (ZA) Johannesburg (ZA) Johannesburg (ZA) São Paulo (BR) Meyzieu (FR) Meyzieu (FR) Meyzieu (FR) Seoul (KR) Othmarsingen (CH) Othmarsingen (CH) Othmarsingen (CH) Shanghai (CN) Porto Alegre (BR) Porto Alegre (BR) Porto Alegre (BR) Shanghai (CN) Shanghai (CN) Shanghai (CN) Strakonice (CZ) Tipton (UK) Tipton (UK) Tipton (UK) Chains for industrial use E Together, we -
Design and Analysis of Crown Pinion of a Differential Gear Box for Reduced Number of Teeth to Improve Torque Transmitted
Int. J. Mech. Eng. & Rob. Res. 2014 Santosh S Bagewadi et al., 2014 ISSN 2278 – 0149 www.ijmerr.com Vol. 3, No. 4, October, 2014 © 2014 IJMERR. All Rights Reserved Research Paper DESIGN AND ANALYSIS OF CROWN PINION OF A DIFFERENTIAL GEAR BOX FOR REDUCED NUMBER OF TEETH TO IMPROVE TORQUE TRANSMITTED Santosh S Bagewadi1*, I G Bhavi2 and S N Kurbet3 *Corresponding Author: Santosh S Bagewadi [email protected] Bevel gears are widely used because of their suitability towards transferring power between nonparallel shafts at almost any angle or speed. Spiral bevel gears, in comparison to straight or zerol bevel gears, have additional overlapping tooth action which creates a smoother gear mesh. This smooth transmission of power along the gear teeth helps to reduce noise and vibration that increases exponentially at higher speeds. Currently the bolero pickup vehicle of Mahindra Company is running with a pinion present in the differential gear box having 11 numbers of teeth. By reducing number of teeth on pinion, we can increase the torque. So we carried out this work to design a new pinion suitable to fit in the bolero pickup vehicle. Only the number of teeth are reduced by keeping all other dimensions same to fit the new pinion in the same housing. Keywords: Spiral bevel gear, Pinion, Differential gear box INTRODUCTION time it should keep the speed of all the wheels When the car is taking a turn, the outer same when going straight ahead. Such a wheels will have to travel greater speed device which serves the above function is distance as compared to the inner wheels in called a Differential.