Starter Motors Damage Scenarios
Total Page:16
File Type:pdf, Size:1020Kb
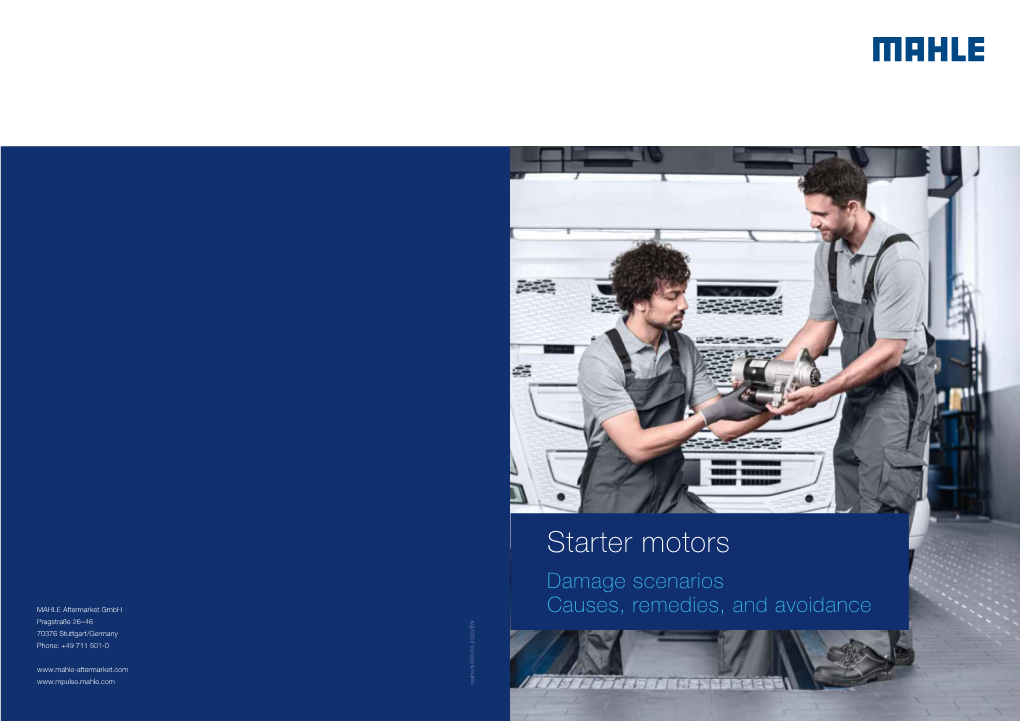
Load more
Recommended publications
-
The Starting System Includes the Battery, Starter Motor, Solenoid, Ignition Switch and in Some Cases, a Starter Relay
UNIT II STARTING SYSTEM &CHARGING SYSTEM The starting system: The starting system includes the battery, starter motor, solenoid, ignition switch and in some cases, a starter relay. An inhibitor or a neutral safety switch is included in the starting system circuit to prevent the vehicle from being started while in gear. When the ignition key is turned to the start position, current flows and energizes the starter's solenoid coil. The energized coil becomes an electromagnet which pulls the plunger into the coil. The plunger closes a set of contacts which allow high current to reach the starter motor. The charging system: The charging system consists of an alternator (generator), drive belt, battery, voltage regulator and the associated wiring. The charging system, like the starting system is a series circuit with the battery wired in parallel. After the engine is started and running, the alternator takes over as the source of power and the battery then becomes part of the load on the charging system. The alternator, which is driven by the belt, consists of a rotating coil of laminated wire called the rotor. Surrounding the rotor are more coils of laminated wire that remain stationary (called stator) just inside the alternator case. When current is passed through the rotor via the slip rings and brushes, the rotor becomes a rotating magnet having a magnetic field. When a magnetic field passes through a conductor (the stator), alternating current (A/C) is generated. This A/C current is rectified, turned into direct current (D/C), by the diodes located within the alternator. -
Design and Development of Open Differential for Transmission System of Quad Bike
International Research Journal of Engineering and Technology (IRJET) e-ISSN: 2395-0056 Volume: 05 Issue: 12 | Dec 2018 www.irjet.net p-ISSN: 2395-0072 Design and Development of Open Differential for Transmission System of Quad Bike Utkarsha Chaudhari1, Prathamesh Sangelkar2, Prajval Vaskar3 1,2,3Department of Mechanical Engineering, Sinhgad Academy of Engineering, Kondhwa ---------------------------------------------------------------------***---------------------------------------------------------------------- Abstract – A differential is an important torque 2. ANALYTICAL CALCULATIONS transmitting device in most of the rear wheel drive vehicles. An ATV is a vehicle which is used to ride in off-road terrains; 2.1 Primary Calculations for Gear Reduction hence continuous application of traction is a vital factor which showcases its performative aspect. The paper describes Input Data: designing and manufacturing an open differential for an off road ATV (Quad Bike) so that the vehicle maneuvers sharp Turning radius of vehicle: - 3m corners without losing traction to the driving wheels. Rear Track width: - 40” Rear tire diameter: - 23” Key Words: Open differential, traction difference, ANSYS, CREO, gear, pinion, centre pin. 1. INTRODUCTION A differential is a gear train with three shafts that has the property that the rotational speed of one shaft is the average of the speeds of the others, or a fixed multiple of that average. In automobiles, the differential allows the outer drive wheel to rotate faster than the inner drive wheel during a turn. This is necessary when the vehicle turns, making the wheel that is travelling around the outside of the turning curve roll farther and faster than the other. The average of the rotational speed of the two driving wheels equals the input rotational speed of the drive shaft. -
Development of Two-Stage Electric Turbocharging System for Automobiles
Mitsubishi Heavy Industries Technical Review Vol. 52 No. 1 (March 2015) 71 Development of Two-stage Electric Turbocharging system for Automobiles BYEONGIL AN*1 NAOMICHI SHIBATA*2 HIROSHI SUZUKI*3 MOTOKI EBISU*1 Engine downsizing using supercharging is progressing to cope with tightening global environmental regulations. In addition, further improvement in fuel consumption is expected with such applications as ultra-high EGR, Miller cycle, and lean combustion. Mitsubishi Heavy Industries, Ltd. (MHI) has developed a two-stage electric turbocharging system to balance better drivability and improved fuel consumption by increasing the turbocharging pressure and improving the transient response. |1. Introduction Engine downsizing/downspeeding through supercharging is progressing to cope with annually enhanced improvement in fuel consumption and exhaust gas. Downsizing through direct injection and supercharging has been developed mainly in European countries where the CO2 regulations are the most stringent, and it has expedited the increase of the turbocharger installation rate in other areas. Diesel vehicles are supposed to satisfy the CO2 and exhaust gas regulation standards in 2021. However, gasoline vehicles are still not able to meet the standards even in the case of low-fuel consumption vehicles with supercharged downsizing, and further measures are required. The adoption of WLTC (Worldwide harmonized Light duty driving Test Cycle) is planned globally in and after 2017, and new regulations taking actual driving conditions into consideration are being discussed. Turbochargers are required to provide a further boost pressure and better response, as well as robust and easy to operate characteristics, for this purpose. Existing turbochargers have a time-lag and EGR response delay, and proper control is difficult. -
DEUTZ Pose Also Implies Compliance with the Con- Original Parts Is Prescribed
Operation Manual 914 Safety guidelines / Accident prevention ● Please read and observe the information given in this Operation Manual. This will ● Unauthorized engine modifications will in- enable you to avoid accidents, preserve the validate any liability claims against the manu- manufacturer’s warranty and maintain the facturer for resultant damage. engine in peak operating condition. Manipulations of the injection and regulating system may also influence the performance ● This engine has been built exclusively for of the engine, and its emissions. Adherence the application specified in the scope of to legislation on pollution cannot be guaran- supply, as described by the equipment manu- teed under such conditions. facturer and is to be used only for the intended purpose. Any use exceeding that ● Do not change, convert or adjust the cooling scope is considered to be contrary to the air intake area to the blower. intended purpose. The manufacturer will The manufacturer shall not be held respon- not assume responsibility for any damage sible for any damage which results from resulting therefrom. The risks involved are such work. to be borne solely by the user. ● When carrying out maintenance/repair op- ● Use in accordance with the intended pur- erations on the engine, the use of DEUTZ pose also implies compliance with the con- original parts is prescribed. These are spe- ditions laid down by the manufacturer for cially designed for your engine and guaran- operation, maintenance and servicing. The tee perfect operation. engine should only be operated by person- Non-compliance results in the expiry of the nel trained in its use and the hazards in- warranty! volved. -
Starters & Alternators
Starters & Alternators Technical Manual www.denso-am.eu n UK & IE n RU n DACH n Eastern Europe n Export n Iberia, France, Italy DENSO Europe B.V. After Market and Industrial Solutions Business Unit Sales Representation European Headquarters Albania Hungary Portugal Weesp, Netherlands Austria Ireland Romania Belarus Israel Russia (Moscow) Belgium Italy Russia (Novosibirsk) Distribution warehouses Bosnia and Herzegovina Kaliningrad Slovakia Bulgaria Kazakhstan Slovenia Gennevilliers, France Cyprus Latvia Spain Leipzig, Germany Czech Republic Lithuania Sweden Madrid, Spain Denmark Luxembourg Switzerland Milton Keynes, UK Estonia Macedonia Turkey Moscow, Russia Finland Moldova United Kingdom Polrino, Italy France Montenegro Ukraine Weesp, Netherlands Georgia Netherlands Germany Norway Greece Poland DENSO Starters & Alternators Table of Content DENSO in Europe > The Aftermarket Originals 04 Introduction > About This Publication 04 > Product Range 05 PART 1 – DENSO Starters PART 2 – DENSO Alternators Characteristics Characteristics > System outline 08 > System outline 42 > How Starters work 09 > How Alternators work 43 Types Types > Pinion Shift Type 11 > Conventional Type 45 > Reduction Type 14 > Type III 46 > Planetary Type 17 > SC Type 47 Wall Chart 21 Wall Chart 53 Stop & Start Technology 22 Replacement Guide 54 Replacement Guide 28 Troubleshooting > Diagnostic Chart 55 Troubleshooting > Inspection 56 > Diagnostic Chart 29 > Q&A 58 > Inspection 30 > Q&A 37 Edition: 1, date of publication: August 2016 All rights reserved by DENSO EUROPE B.V. This document may not be reproduced or copied, in Edition: 2, date of publication: October 2016 whole or in part, without the written permission of the publisher. DENSO EUROPE B.V. reserves Editorial dept, staff: DNEU AMIS Technical Service, K. -
Chain Drives 759
Chain Drives 759 C H A P T E R 21 Chain Drives 1. Introduction. 2. Advantages and Disadvantages of Chain Drive over Belt or Rope Drive. 3. Terms Used in Chain Drive. 4. Relation Between Pitch and Pitch Circle Diameter. 5. Velocity Ratio of Chain Drives. 6. Length of Chain and Centre Distance. 7. Classification of Chains. 8. Hoisting and Hauling Chains. 9. Conveyor Chains. 10. Power Transmitting Chains. 11. Characteristics of Roller Chains. 12. Factor of Safety for Chain Drives. 21.1 Introduction 13. Permissible Speed of We have seen in previous chapters on belt and rope Smaller Sprocket. 14. Power Transmitted by drives that slipping may occur. In order to avoid slipping, Chains. steel chains are used. The chains are made up of number of 15. Number of Teeth on the rigid links which are hinged together by pin joints in order Smaller or Driving Sprocket or Pinion. to provide the necessary flexibility for wraping round the 16. Maximum Speed for driving and driven wheels. These wheels have projecting Chains. teeth of special profile and fit into the corresponding recesses 17. Principal Dimensions of Tooth Profile. in the links of the chain as shown in Fig. 21.1. The toothed 18. Design Procedure for wheels are known as *sprocket wheels or simply sprockets. Chain Drive. The sprockets and the chain are thus constrained to move together without slipping and ensures perfect velocity ratio. * These wheels resemble to spur gears. 759 760 A Textbook of Machine Design Fig. 21.1. Sprockets and chain. The chains are mostly used to transmit motion and power from one shaft to another, when the centre distance between their shafts is short such as in bicycles, motor cycles, agricultural machinery, conveyors, rolling mills, road rollers etc. -
Diesel Engine Starting Systems Are As Follows: a Diesel Engine Needs to Rotate Between 150 and 250 Rpm
chapter 7 DIESEL ENGINE STARTING SYSTEMS LEARNING OBJECTIVES KEY TERMS After reading this chapter, the student should Armature 220 Hold in 240 be able to: Field coil 220 Starter interlock 234 1. Identify all main components of a diesel engine Brushes 220 Starter relay 225 starting system Commutator 223 Disconnect switch 237 2. Describe the similarities and differences Pull in 240 between air, hydraulic, and electric starting systems 3. Identify all main components of an electric starter motor assembly 4. Describe how electrical current flows through an electric starter motor 5. Explain the purpose of starting systems interlocks 6. Identify the main components of a pneumatic starting system 7. Identify the main components of a hydraulic starting system 8. Describe a step-by-step diagnostic procedure for a slow cranking problem 9. Describe a step-by-step diagnostic procedure for a no crank problem 10. Explain how to test for excessive voltage drop in a starter circuit 216 M07_HEAR3623_01_SE_C07.indd 216 07/01/15 8:26 PM INTRODUCTION able to get the job done. Many large diesel engines will use a 24V starting system for even greater cranking power. ● SEE FIGURE 7–2 for a typical arrangement of a heavy-duty electric SAFETY FIRST Some specific safety concerns related to starter on a diesel engine. diesel engine starting systems are as follows: A diesel engine needs to rotate between 150 and 250 rpm ■ Battery explosion risk to start. The purpose of the starting system is to provide the torque needed to achieve the necessary minimum cranking ■ Burns from high current flow through battery cables speed. -
Oscillatory Motion Leadscrews • for Applications Requiring Linear Oscillatory Motion Over a Fixed Path
© 1994 by Alexander H. Slocum Precision Machine Design Topic 21 Linear motion actuators Purpose: This lecture provides an introduction to the design issues associated with linear power transmission elements. Major topics: • Error sources • Belt drives • Rack and pinion drives •Friction drives • Leadscrews • Linear electric motors "...screw your courage to the sticking-place, And we'll not fail" Shakespeare 21-1 © 1994 by Alexander H. Slocum Error sources: • There are five principal error sources that affect linear actuator' performance: • Form error in the device components. • Component misalignment. • Backlash. • Friction. • Thermal effects • These systems often have long shafts (e.g., ballscrews). • One must be careful of bending frequencies being excited by rotating motors. 21-2 © 1994 by Alexander H. Slocum Belt drives • Used in printers, semiconductor automated material handling systems, robots, etc. • Timing belts will not slip. • Metal belts have greater stiffness, but stress limits life: σ = Et 2ρ • Timing belts will be the actuator of choice for low cost, low stiffness, low force linear motion until: •Linear electric motor cost comes down. • PC based control boards with self-tuning modular algorithms become more prevalent. • To prevent the belts' edges wearing on pulley flanges: • Use side rollers to guide timing belt to prevent wear caused by flanged sheaves: load Guide roller Belt 21-3 © 1994 by Alexander H. Slocum Rack and pinion drives Motor Pinion Rack • One of the least expensive methods of generating linear motion from rotary motion. • Racks can be placed end to end for as great a distance as one can provide a secure base on which to bolt them. -
735.5270 Inc D-Of-C TCG250 (N1 Engine Shaft) with Part Numbers (WITH Machine Stand) Current 28.9.17.Pub
TCG 250 Floor Grinder Operation and Maintenance Manual www.trelawnyspt.co.uk OPERATION Foreword Safety that the operators wear personal Thank you for your purchase of the WEAR SAFETY BOOTS, FACE protective equipment [PPE] TRELAWNY TCG250 Floor Grinder. MASK, SHATTERPROOF particularly gloves and clothing to GLASSES, HELMET, GLOVES and keep them warm and dry. This manual contains the necessary any other personal protective Employers should consider setting maintenance information for you to equipment required for the working up a programme of health ensure proper operation and care for conditions. Avoid loose clothing; this surveillance to establish a this machine. may become trapped in moving benchmark for each operator and to parts and cause serious injury. detect early symptoms of vibration See also the manual that is TO AVOID NUISANCE DUST, injury. supplied by the engine connect an industrial vacuum We are not aware of any PPE that manufacturer. cleaner (minimum 3000watts or provides protection against vibration equivalent) to the 50mm (2”) vacuum injury by attenuating vibration It is essential for you to read port situated at the rear of the emissions. through these manuals machine. thoroughly. ENSURE THAT THE WORK PLACE See ‘Specifications’ section for IS WELL VENTILATED. Avoid vibration emission data. In the unlikely event that you operating engine-powered machines experience problems with your in an enclosed area, since engine Further advice is available from our TCG250, please do not hesitate to exhaust gases are poisonous. Technical Department. contact your local Trelawny dealer or BE VERY CAREFUL WITH HOT agent. We always welcome COMPONENTS. The exhaust and We strongly advise you to visit the feedback and comments from our other parts of the engine are hot Health & Safety Executive website valued customers. -
Software Controlled Stepping Valve System for a Modern Car Engine
Available online at www.sciencedirect.com ScienceDirect Procedia Manufacturing 8 ( 2017 ) 525 – 532 14th Global Conference on Sustainable Manufacturing, GCSM 3-5 October 2016, Stellenbosch, South Africa Software Controlled Stepping Valve System for a Modern Car Engine I. Zibania, R. Marumob, J. Chumac and I. Ngebanid.* a,b,dUniversity of Botswana, P/Bag 0022, Gaborone, Botswana cBotswana International University of Science and Technology, P/Bag 16, Palapye, Botswana Abstract To address the problem of a piston-valve collision associated with poppet valve engines, we replaced the conventional poppet valve with a solenoid operated stepping valve whose motion is perpendicular to that of the piston. The valve events are software controlled, giving rise to precise intake/exhaust cycles and improved engine efficiency. Other rotary engine models like the Coates engine suffer from sealing problems and possible valve seizure resulting from excessive frictional forces between valve and seat. The proposed valve on the other hand, is located within the combustion chamber so that the cylinder pressure help seal the valve. To minimize friction, the valve clears its seat before stepping into its next position. The proposed system was successfully simulated using ALTERA’s QUARTUS II Development System. A successful prototype was built using a single piston engine. This is an ongoing project to eventually produce a 4-cylinder engine. ©© 2017 201 6Published The Authors. by Elsevier Published B.V. Thisby Elsevier is an open B.V. access article under the CC BY-NC-ND license (Peerhttp://creativecommons.org/licenses/by-nc-nd/4.0/-review under responsibility of the organizing). committee of the 14th Global Conference on Sustainable Manufacturing. -
009 Automotive Service Technician Course Outline
Apprenticeship and Industry Training Automotive Service Technician Apprenticeship Course Outline 0912 (2012) ALBERTA ADVANCED EDUCATION AND TECHNOLOGY CATALOGUING IN PUBLICATION DATA Alberta. Alberta Advanced Education and Technology. Apprenticeship and Industry Training. Automotive service technician : apprenticeship course outline. ISBN 978-0-7785-9909-8 (Online) Available online: http://www.tradesecrets.gov.ab.ca 1. Automobile mechanics – Vocational guidance – Alberta. 2. Automobiles – Maintenance and repair – Vocational guidance – Alberta. 3. Apprentices – Alberta. 4. Apprenticeship programs – Alberta. 5. Occupational training – Alberta. I. Title. II. Series: Apprenticeship and industry training. HD4885.C2.A23 A333 2012 373.27 ALL RIGHTS RESERVED: © 2012, Her Majesty the Queen in right of the Province of Alberta, as represented by the Minister of Alberta Advanced Education and Technology, 10th floor, Commerce Place, Edmonton, Alberta, Canada, T5J 4L5. All rights reserved. No part of this material may be reproduced in any form or by any means, without the prior written consent of the Minister of Advanced Education and Technology Province of Alberta, Canada. Automotive Service Technician Table of Contents Automotive Service Technician Table of Contents ................................................................................................................. 1 Apprenticeship .......................................................................................................................................................................... -
Martin Machined Gear Rack Brochure
Locations Corporate Offices Sales & Manufacturing USA Arlington, TX 817-258-3000 (FAX 817-258-3333) Regional Manufacturing Plants Albemarle, NC 704-982-9555 (FAX 704-982-9599) Stocked in Steel Atlanta, GA 404-292-8744 (FAX 404-292-7771) Burleson, TX 14½º & 20º PA 817-295-7151 (FAX 817-447-3840) MACHINED Danielsville, PA 610-837-1841 (FAX 610-837-7337) MTO Capabilities Ft. Worth, TX 817-258-3000 (FAX 817-258-3173) Up to 12' long Montpelier, OH GEAR RACK 419-485-5515 (FAX 419-485-3565) Sacramento, CA 916-441-7172 (FAX 916-441-4600) Branch Manufacturing Plants Boston, MA 508-634-3990 (FAX 508-634-3998) Charlotte, NC 704-394-9111 (FAX 704-394-9122) Chicago, IL 847-298-8844 (FAX 847-298-2967) Denver, CO 303-371-8466 (FAX 303-371-7116) Houston, TX 713-849-4330 (FAX 713-849-4807) Kansas City, MO 816-231-5575 (FAX 816-231-1959) Los Angeles, CA 323-728-8117 (FAX 323-722-7526) Minneapolis, MN 952-829-0623 (FAX 952-944-9385) Nashville, TN 615-871-4730 (FAX 615-871-4125) Pittsburgh, PA 724-452-4555 (FAX 724-452-5794) Portland, OR 503-223-7261 (FAX 503-221-0203) Tampa, FL 813-623-1705 (FAX 813-626-8953) Manufacturing Only Abilene, TX • Clarksville, TX Dallas, TX • Mansfield, TX Paragould, AR Cambridge, Ontario 519-621-0546 (FAX 519-621-4413) Edmonton, Alberta 780-450-0888 (FAX 780-465-0079) CANADA Mississauga, Ontario 905-670-1991 (FAX 905-670-2110) Guadalajara, JAL +52 33-3283-1188 (FAX +52 33-3271-8450) Monterrey, N.L.