Owner's Manual – C-LINE
Total Page:16
File Type:pdf, Size:1020Kb
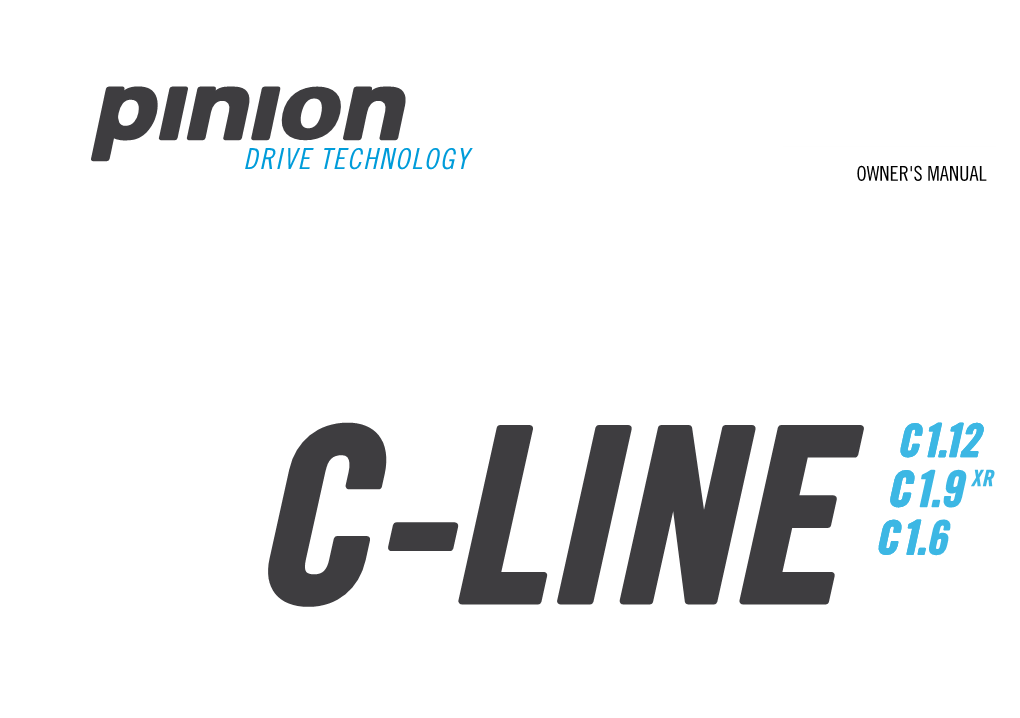
Load more
Recommended publications
-
Design and Development of Open Differential for Transmission System of Quad Bike
International Research Journal of Engineering and Technology (IRJET) e-ISSN: 2395-0056 Volume: 05 Issue: 12 | Dec 2018 www.irjet.net p-ISSN: 2395-0072 Design and Development of Open Differential for Transmission System of Quad Bike Utkarsha Chaudhari1, Prathamesh Sangelkar2, Prajval Vaskar3 1,2,3Department of Mechanical Engineering, Sinhgad Academy of Engineering, Kondhwa ---------------------------------------------------------------------***---------------------------------------------------------------------- Abstract – A differential is an important torque 2. ANALYTICAL CALCULATIONS transmitting device in most of the rear wheel drive vehicles. An ATV is a vehicle which is used to ride in off-road terrains; 2.1 Primary Calculations for Gear Reduction hence continuous application of traction is a vital factor which showcases its performative aspect. The paper describes Input Data: designing and manufacturing an open differential for an off road ATV (Quad Bike) so that the vehicle maneuvers sharp Turning radius of vehicle: - 3m corners without losing traction to the driving wheels. Rear Track width: - 40” Rear tire diameter: - 23” Key Words: Open differential, traction difference, ANSYS, CREO, gear, pinion, centre pin. 1. INTRODUCTION A differential is a gear train with three shafts that has the property that the rotational speed of one shaft is the average of the speeds of the others, or a fixed multiple of that average. In automobiles, the differential allows the outer drive wheel to rotate faster than the inner drive wheel during a turn. This is necessary when the vehicle turns, making the wheel that is travelling around the outside of the turning curve roll farther and faster than the other. The average of the rotational speed of the two driving wheels equals the input rotational speed of the drive shaft. -
Flexible Wheel Chair
GRD Journals- Global Research and Development Journal for Engineering | Volume 1 | Issue 8 | July 2016 ISSN: 2455-5703 Flexible Wheel Chair Mahantesh Tanodi Department of Mechanical Engineering Hirasugar Institute of Technology, Nidasoshi, Karnataka (India) Sujata Huddar S. B. Yapalaparvi Department of Electrical and Electronics Engineering Department of Mechanical Engineering Hirasugar Institute of Technology, Nidasoshi, Karnataka Hirasugar Institute of Technology, Nidasoshi, Karnataka (India) (India) Abstract The wheelchair is one of the most commonly used assistive devices for enhancing personal mobility, which is a precondition for enjoying human rights and living in dignity and assists people with disabilities to become more productive members of their communities. For many people, an appropriate, well-designed and well-fitted wheelchair can be the first step towards inclusion and participation in society. When the need is not met, people with disabilities are isolated and do not have access to the same opportunities as others within their own communities. Providing wheelchairs that are fit for the purpose not only enhances mobility but begins a process of opening up a world of education, work and social life [1]. The development of national policies and increased training opportunities in the design, production and supply of wheelchairs are essential next steps. Every human being need to move from one place another to fulfill his requirements and to accomplish that requirements he will travel from one place to another place by walking which is a basic medium of transportation. But it is exceptional in case of physically disables (Persons don’t have both legs). In order to support and help such a person’s we designed a special manually lever operated wheel chair. -
Chain Drives 759
Chain Drives 759 C H A P T E R 21 Chain Drives 1. Introduction. 2. Advantages and Disadvantages of Chain Drive over Belt or Rope Drive. 3. Terms Used in Chain Drive. 4. Relation Between Pitch and Pitch Circle Diameter. 5. Velocity Ratio of Chain Drives. 6. Length of Chain and Centre Distance. 7. Classification of Chains. 8. Hoisting and Hauling Chains. 9. Conveyor Chains. 10. Power Transmitting Chains. 11. Characteristics of Roller Chains. 12. Factor of Safety for Chain Drives. 21.1 Introduction 13. Permissible Speed of We have seen in previous chapters on belt and rope Smaller Sprocket. 14. Power Transmitted by drives that slipping may occur. In order to avoid slipping, Chains. steel chains are used. The chains are made up of number of 15. Number of Teeth on the rigid links which are hinged together by pin joints in order Smaller or Driving Sprocket or Pinion. to provide the necessary flexibility for wraping round the 16. Maximum Speed for driving and driven wheels. These wheels have projecting Chains. teeth of special profile and fit into the corresponding recesses 17. Principal Dimensions of Tooth Profile. in the links of the chain as shown in Fig. 21.1. The toothed 18. Design Procedure for wheels are known as *sprocket wheels or simply sprockets. Chain Drive. The sprockets and the chain are thus constrained to move together without slipping and ensures perfect velocity ratio. * These wheels resemble to spur gears. 759 760 A Textbook of Machine Design Fig. 21.1. Sprockets and chain. The chains are mostly used to transmit motion and power from one shaft to another, when the centre distance between their shafts is short such as in bicycles, motor cycles, agricultural machinery, conveyors, rolling mills, road rollers etc. -
Worksman Eagle Lite Tricycle Owner's Manual
Worksman Eagle Lite Tricycle Owner’s Manual Worksman Trading Corporation – 94-15 100th Street – Ozone Park, NY 11416 – (718) 322-2000 www.worksmancycles.com Parts list EAG07 Models EAG-FW, EAG-2F, EAG-CB, EAG-3CB Worksman Eagle Lite Tricycle - The Finest Adult Tricycle in the World! Congratulations! You have purchased an American-made Worksman Eagle Lite Tricycle. Before assembling and riding, make certain to read this manual thoroughly. Always follow the rules of safe riding. Always keep your Eagle Lite tricycle in tip-top shape by replacing worn parts as needed with genuine Worksman Cycles parts. (Do not use generic bicycle parts.) With simple maintenance, your Eagle Lite Tricycle will perform reliably day after day, year after year. Your Eagle Lite Tricycle has been hand-made in the USA by our American craftspeople. Our reputation rides along with you, so your ultimate satisfaction is our goal. The Eagle is a light-duty tricycle. It has a recommended maximum capacity of 250 pounds, including the rider. If you are a heavier rider, or intend to use this cycle for heavy industrial use, we recommend our Worksman Business Cycle System of industrial, heavy-duty tricycles. FAILURE TO HAVE A QUALIFIED BICYCLE MECHANIC ASSEMBLE THIS CYCLE COULD RESULT IN SERIOUS INJURY OR DEATH. Worksman Eagle Lite Parts List (For all freewheel, coaster brake and three-speed coaster brake Eagle Lite Tricycles.) Frame, Fork and Related Parts Part # Description Part # Description 3950 Eagle Lite Frame (specify color) 154 Fork (Silver) 3950A Eagle Lite Rear w/ -
Oscillatory Motion Leadscrews • for Applications Requiring Linear Oscillatory Motion Over a Fixed Path
© 1994 by Alexander H. Slocum Precision Machine Design Topic 21 Linear motion actuators Purpose: This lecture provides an introduction to the design issues associated with linear power transmission elements. Major topics: • Error sources • Belt drives • Rack and pinion drives •Friction drives • Leadscrews • Linear electric motors "...screw your courage to the sticking-place, And we'll not fail" Shakespeare 21-1 © 1994 by Alexander H. Slocum Error sources: • There are five principal error sources that affect linear actuator' performance: • Form error in the device components. • Component misalignment. • Backlash. • Friction. • Thermal effects • These systems often have long shafts (e.g., ballscrews). • One must be careful of bending frequencies being excited by rotating motors. 21-2 © 1994 by Alexander H. Slocum Belt drives • Used in printers, semiconductor automated material handling systems, robots, etc. • Timing belts will not slip. • Metal belts have greater stiffness, but stress limits life: σ = Et 2ρ • Timing belts will be the actuator of choice for low cost, low stiffness, low force linear motion until: •Linear electric motor cost comes down. • PC based control boards with self-tuning modular algorithms become more prevalent. • To prevent the belts' edges wearing on pulley flanges: • Use side rollers to guide timing belt to prevent wear caused by flanged sheaves: load Guide roller Belt 21-3 © 1994 by Alexander H. Slocum Rack and pinion drives Motor Pinion Rack • One of the least expensive methods of generating linear motion from rotary motion. • Racks can be placed end to end for as great a distance as one can provide a secure base on which to bolt them. -
Bike Tune Up
Bike Tune Up March 14, 2007 Contents What You Will Need For Tuning Your Bicycle: . 3 What if you get in over your head? . 3 Step 1: Adjust Headset . 4 Step 2: Bottom Bracket Adjustment . 6 Pedals . 7 Step 3: Adjust The Front Wheel Bike Hub . 9 Step 4: Adjust Rear Wheel Hubs . 11 Coaster Brake . 11 Three-Speed Wheels . 11 Derailleur-Equipped and BMX Bicycle Wheels . 11 Overhauling . 12 Freewheels - Overhaul, General Care and Troubleshooting . 12 Step 5: Wheel Truing . 14 Unbending A Bicycle Bent Wheel . 15 Flat Spots . 16 Kinks . 17 Broken Spokes . 17 Step 6: Bike Brake Adjustment . 19 If It Is A Sidepull Or Centerpull Brake: . 21 If It Is A Cantilever Bike Brake: . 21 Replacing A Cable . 22 The Brake Pads . 25 Diagnosing Brake Stickiness . 25 Hand Levers . 25 Step 7: Adjust The Rear Derailleur . 27 Replacing a Cable . 29 Step 8: Adjust The Front Derailleur . 31 Replacing a Cable . 33 Step 9: Finish The Tune-Up . 34 1 2 What You Will Need For Tuning Your Bicycle: • This Presentation • An adjustable wrench or set of wrenches • Tongue and groove pliers, sometimes called ”channellocks” • Bicycle bearing cone wrenches (approx. $8 at bike stores) Figure 1: cone wrench • Oil, grease, and non-flammable, non-toxic cleaning solvent • A couple of screwdrivers • A freewheel remover (maybe) Figure 2: Freewheel Remover • Patience - This is the most important ingredient What if you get in over your head? Ask a friend, or call the mechanic at the local bike shop for advice. In the worst case, you would have to take the bike into the shop and pay for professional help, which would still cost less than a complete tune-up anyway. -
The Effect of Vehicle Electrification on Transmissions and The
MAG 2016 # December The AutomotiveCTI TM, HEV & EV Drives magazine by CTI A New Automatic Trans mission The Effect of Vehicle Approach – a Suitable MT Electrification on Replacement? Transmissions and the Transmission Market Interview with John Juriga Director Powertrain, What Chinese Customer Hyundai America Technical Center is Expecting Innovations in motion Experience the powertrain technology of tomorrow. Be inspired by modern designs that bring together dynamics, comfort and highest effi ciency to offer superior performance. Learn more about our perfect solutions for powertrain systems and discover a whole world of fascinating ideas for the mobility of the future. Visit us at the CTI Symposium in Berlin and meet our experts! www.magna.com CTIMAG Contents 6 The Effect of Vehicle Electrification on 45 Software-based Load and Lifetime Transmissions and the Transmission Monitoring for Automotive Components Market TU Darmstadt & compredict IHS Automotive 49 “Knowledge-Based Data is the Key” 10 What Chinese Customer is Expecting Interview with Prof. Dr-Ing. Stephan Rinderknecht, AVL TU Darmstadt 13 HEV P2 Module Concepts for Different 50 Efficient Development Process from Transmission Architectures Supplier Point of View BorgWarner VOIT Automotive 17 Modular P2–P3 Dedicated Hybrid 53 Synchronisers and Hydraulics Become Transmission for 48V and HV applications Redundant for Hybrid and EV with Oerlikon Graziano Innovative Actuation and Control Methods Vocis 20 eTWINSTER – the First New-Generation Electric Axle System 56 Moving Towards Higher -
Design and Modification of Bicycle by Using Additional Sprockets
Vol-3 Issue-4 2017 IJARIIE-ISSN(O)-2395-4396 DESIGN AND MODIFICATION OF BICYCLE BY USING ADDITIONAL SPROCKETS Sanjeey Reddy K Hudgikar1 S.M.Saleemuddin2 1 Professor, Mechanical Department, Lingaraj Appa Engineering College,Bidar,Karnataka,India 2 Assistant Professor, Mechanical Department, Annamachara Institute of Technology & Sciences,Rajampet,Kadapa,AP. ABSTRACT Biking is increasingly being recognized as a highly sustainable form of transportation. The present work focus on design and development of bi-cycle which can be implemented as an alternative to the two wheelers consuming large amount of fuel and polluting the environment. To overcome these problems, an effort is being made to search some other for the vehicles. Again, it is also not affordable to purchase vehicles (mopeds, scooters or motorcycles) for all the class of society. Keeping this in mind, a search for some way to cater these economically poor people as well as to provide a solution for the environmental pollution was in progress. This work deals with these problems efficiently as energy is generated utilizing the mechanical energy of the rider. Keyword: - Sprockets, Welding, Gear Mechanism 1. INTRODUCTION A bicycle, often called a bike or cycle, is a human-powered, pedal-driven and single-track vehicle having two wheels attached to a frame, one behind the other. A bicycle rider is called a cyclist or bicyclist. Bicycles were introduced in the 19th century in Europe and as of 2003, more than 1 billion have been produced worldwide twice as many as the number of automobiles that have been produced. They are the principal means of transportation in many regions. -
Design and Fabrication of Multi-Speed Bicycle Sprocket on CNC Milling Machine Adib Bin Rashid#1, M.A
SSRG International Journal of Industrial Engineering (SSRG-IJIE) - Volume 7 Issue 2 - May - Aug 2020 Design and Fabrication of Multi-speed Bicycle Sprocket on CNC Milling Machine Adib Bin Rashid#1, M.A. Rashid Tipu*2 #Assistant Professor, Industrial and Production Engineering Department, Military Institute of Science and Technology, Mirpur Cantonment, Dhaka, Bangladesh *Managing Director, Mart Engineering and Consultancy Ltd, Dhaka, Bangladesh Abstract most common. British CEI (Cycle Engineers Institute) Now a day's cycling is a passion for the young thread was adopted as the international standard and generation of Bangladesh. Multi-speed bicycles are is now known as B.S.C. - British Standard Cycle and most preferable to them as it allows gear selection to is a standardized right-hand thread (1.375 x 24 TPI) suit the circumstances: a cyclist could use a high onto which a standard freewheel is screwed. This gear when cycling downhill, a medium gear when allows different brands of freewheels to be mounted cycling on a flat road, and a low gear when cycling on different brands of hubs. uphill. On a Multi-speed bicycle, the cogset or cluster Cassettes are distinguished from freewheels in that a is the set of multiple sprockets that attaches to the cassette has a series of straight splines that form the hub on the rear wheel to provide multiple gear ratios mechanical connection between the sprockets and the to the rider. Manufacturing of sprocket in an cassette compatible hub, called a freehub, which accurate dimension is a challenge to the cycle contains the ratcheting mechanism. The entire manufacturing industry. -
Acrobat Distiller, Job 3
2003-01-3278 A Purely Mechanical Energy Storing Concept for Hybrid Vehicles Latchezar Tchobansky Martin Kozek Gerd Schlager Hanns P. Jörgl Institute for Machine- and Process-Automation, Vienna University of Technology Copyright © 2003 SAE International ABSTRACT necessary for propulsion is not only consumed to overcome the cumulative rolling resistances but a The paper contains the design and simulation of a purely considerable part of energy is required for acceleration. mechanical system for storing energy during vehicle During typical ‘stop-and-go’ stretches this acceleration deceleration, which can be utilized during subsequent energy is dissipated through the main brakes acceleration (regenerative braking). A continuously immediately afterwards. Additionally, the vehicle engine variable transmission (CVT) regulates the energy is almost always operating under sub-optimal working transfer, energy storage is accomplished by means of a conditions leading to high emissions, high wear, and low spiral spring and additional use of a planetary efficiency. transmission. The transmission ratio of the CVT is adapted by a combined feed-forward and feed-back In order to overcome or at least diminish these problems control. A computer simulation for a vehicle with an part of the kinetic energy may be accumulated during overall mass of 1500kg, and an energy storage capacity deceleration phases, stored in a proper device, and used of 30kJ was performed for different driving cycles. In a for a subsequent acceleration. This procedure is also typical urban stop and go situation the proposed device termed as “regenerative braking” since each deceleration will save up to 0.72kg fuel per 100km and the overall event replenishes the stored energy used for efficiency analysis together with simple design, easy acceleration. -
Rear Drive System Largest Largest in a Malfunction
SI-0027B-000-00 General Safety Information Specifications Mounting the shifting lever Connect the inner cable to the derailleur as shown in the illustration. Rear Derailleur WARNING Use a handlebar grip with a maximum Model number RD-C201 outer diameter of 32 mm. • Check that the wheels are fastened securely before riding the bicycle. If the wheels are loose in any way, they may come off the bicycle and serious injury may result. Type MGS • Use neutral detergent to clean the chain. Do not use alkali-based or acid based Total capacity 43T Allen key tightening torque: detergent such as rust cleaners as it may result in damage and/or failure of the chain. 6 - 8 N·m {53 - 69 in. lbs.} • Use the reinforced connecting pin only for connecting the narrow type of chain. Largest sprocket 34T Inner cable • There are two different types of reinforced connecting pins available. Be sure to check Smallest sprocket 11T the table below before selecting which pin to use. If connecting pins other than Front chainwheel tooth difference 20T reinforced connecting pins are used, or if a reinforced connecting pin or tool which is Cutting the outer casing 5 mm Allen key not suitable for the type of chain is used, sufficient connection force may not be When cutting the outer casing, cut the opposite end to the end obtained, which could cause the chain to break or fall off. Cassette sprocket tooth combination with the marking. After cutting the outer casing, make the end Reinforced Model number Sprockets Group name Tooth combination round so that the inside of the hole has a uniform diameter. -
Rexnord BSD Freewheels and Backstops Overview
Rexnord BSD Freewheels and Backstops Overview Rexnord BSD Freewheels and Backstops Freewheels and Backstops Functioning and Application Examples Functioning Clamping Roller Types Freewheels are directional couplings, which means Clamping roller freewheels and backstops are equipped with that the driving part rotates the driven part in one cylindrical rollers as clamping elements. The rollers engage direction, while automatically disengaging from between the contact surface of the outer race and the the driven part when the direction of rotation is clamping surface of the inner hub in one direction of rotation reversed. There are two operational states: blocking this direction. They are free slipping in the opposite • Transmission of torque direction of rotation. Compression springs acting on the clamping rollers by thrust pins ensure the clamping readiness. • Idling (overrunning) • Ball bearings incorporated on both sides center Freewheels are used as: the outer race to the inner hub. • Overrunning Clutch • Ra dial and axial forces are admissible by considering The freewheel automatically disengages when the the capability of the installed bearings. driven part rotates faster than the driving part. • O il lubrication is used as standard. If required, grease • B ackstop filling may be possible for special applications. For gearbox applications, oil mist or spray is recommended. The freewheel allows for rotation in one direction only. The freewheel continuously overruns during operation. At disconnection of the drive, the free- wheel prevents reverse rotation. Centrifugal Releasing Types • F reewheel Clutch / Indexing Clutch Freewheels and backstops with centrifugal releasing wedge (as customized solution) type clamping elements are mostly identical to the clamping The freewheel allows the conversion of a roller design regarding operating principle, dimensions and modular design.