Helical Turbine and Fish Safety
Total Page:16
File Type:pdf, Size:1020Kb
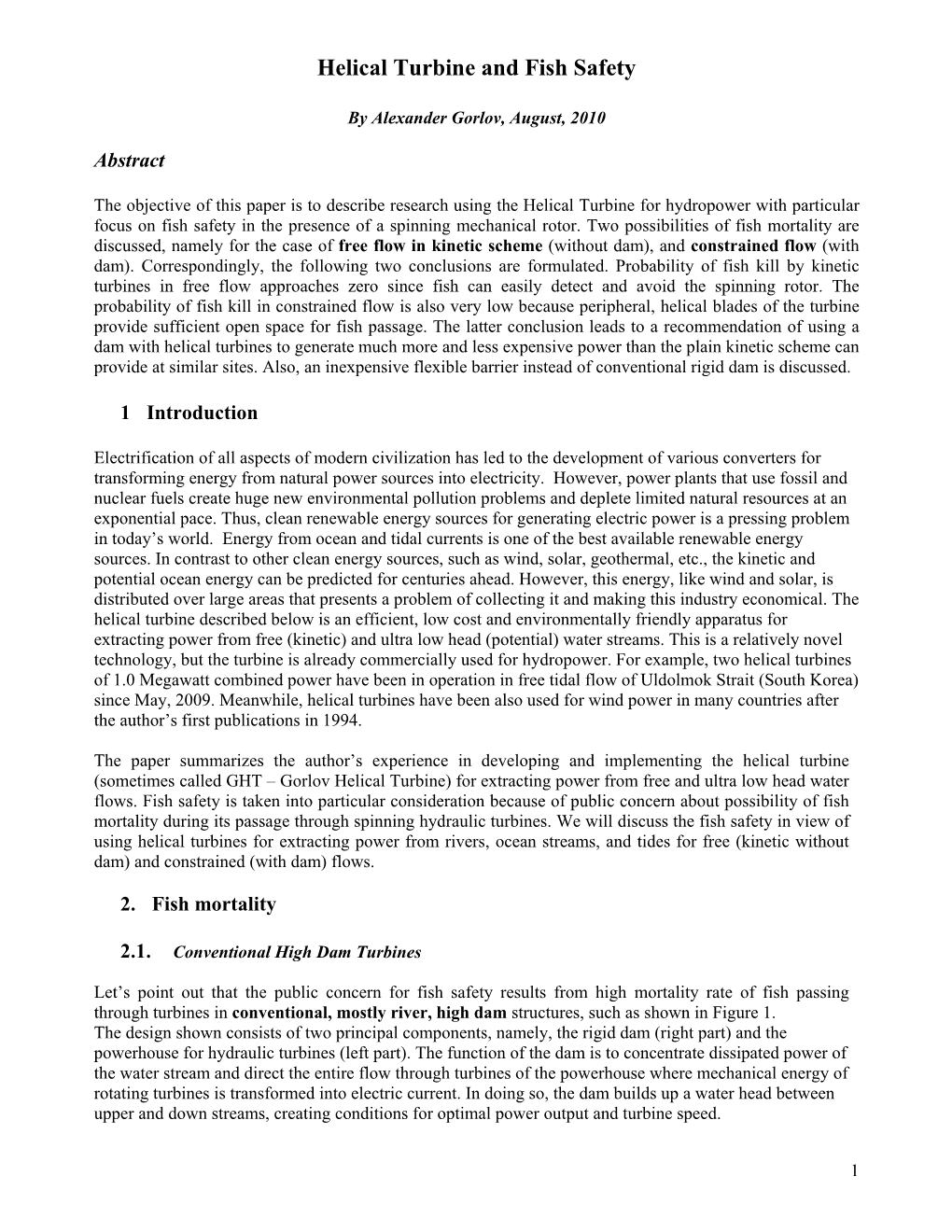
Load more
Recommended publications
-
A SOPAC Desktop Study of Ocean-Based, Renewable Energy
A SOPAC Desktop Study of Ocean-Based RENEWABLE ENERGY TECHNOLOGIES SOPAC Miscellaneous Report 701 A technical publication produced by the SOPAC Community Lifelines Programme Acknowledgements Information presented in this publication has been sourced mainly from the internet and from publications produced by the International Energy Agency (IEA). The compiler would like to thank the following for reviewing and contributing to this publication: • Dr. Luis Vega • Anthony Derrick of IT Power, UK • Guillaume Dréau of Société de Recherche du Pacifique (SRP), New Caledonia • Professor Young-Ho Lee of Korea Maritime University, Korea • Professor Chul H. (Joe) Jo of Inha University, Korea • Luke Gowing and Garry Venus of Argo Environmental Ltd, New Zealand SOPAC Miscellaneous Report 701 Pacific Islands Applied Geoscience Commission (SOPAC), Fiji • Paul Fairbairn – Manager Community Lifelines Programme • Rupeni Mario – Senior Energy Adviser • Arieta Gonelevu – Senior Energy Project Officer • Frank Vukikimoala – Energy Project Officer • Koin Etuati – Energy Project Officer • Reshika Singh – Energy Resource Economist • Atishma Vandana Lal – Energy Support Officer • Mereseini (Lala) Bukarau – Senior Adviser Technical Publications Ivan Krishna • Sailesh Kumar Sen – Graphic Arts Officer Compiler First Edition October 2009 Cover Photo Source: HTTP://WALLPAPERS.FREE-REVIEW.NET/42__BIG_WAVE.HTM Back Cover Photo: Raj Singh A SOPAC Desktop Study of Ocean-Based Renewable Energy Technologies SOPAC Miscellaneous Report 701 Ivan Krishna Compiler First Edition -
OMNI Magazine Interview, July 1992)
ALIEN CITY ON MARS? TiTil W i^ -A Im; SCENES Lji U *' Ul EDITOR IN CHIEF & DESIGN DIRECTOR: BOB GUCCIONE PRESIDENT a C.O.O.: KATHY KEETON VP/EDITOR' KEITH FERRELL EXECUTIVE VP/GBAPHICS DIRECTOR- FRANK DEVINO MANAGING EDITOR: CAROLINE DARK ART DIRECTOR: CATHRYN MEZZO First Word Continuum By Dana Rohrabacher 42 Fighting for Opening the X-Files U.S. patent rights By David Bischoff S Mulder and Scully know Communications something is m out there—and so do their Funds many fans. A behind- By Linda Marsa the-scenes lool< at this fas- Cashing in on collectibles cinating and m increasingly popular Electronic Universe new show. By Grsgg Keizer ArchiTreIc Medicine Designing Generations By Anita Bartholomew By Herman Zimmerman m and Philip Thomas Edgerly .Sounds Boldly going where By Steve Nadis few. production designers Sounds of the silent have gone before: 22 designing the Star Trek Eanii By Melanie Menagh Choices Fiction: S.4 Dying Virtual Realities [Vlichael IVlarshall Smith By Tom Dworetzl<y 7^ 23 Cartoon Feature Artificial Intelligence . By Steve Nadis Interview: 32 Richard hioa gland Mind By Steve Nadis By Steve Nadis A close-up lool< at the Hallucinations, man behind delusions, the face on Mars and schizophrenia SS 33 Tsuneo Sanda's cover painting, On Patrol, made possible by Antimatter the PI" I p Edge ly Age cy n a'^sar qt on witi ZD^sgn Copyrght Pa amount PcturesCorporaticn Games (Additional art rred t"^ page 110) By bi, iff Morris SR1''6ril7'iBn FIRST UUORD INVENTING AMERICA: Patent laws and the protection of individual rights By Dana Rohrabacher merica's greatest asset side. -
A Numerical Approach for Estimating the Aerodynamic Characteristics of a Two Bladed Vertical Darrieus Wind Turbine Ervin Amet, Christian Pellone, Thierry Maître
A numerical approach for estimating the aerodynamic characteristics of a two bladed vertical Darrieus wind turbine Ervin Amet, Christian Pellone, Thierry Maître To cite this version: Ervin Amet, Christian Pellone, Thierry Maître. A numerical approach for estimating the aerodynamic characteristics of a two bladed vertical Darrieus wind turbine. 2nd Workshop on Vortex dominated flows, Jul 2006, Bucarest, Romania. hal-00232721 HAL Id: hal-00232721 https://hal.archives-ouvertes.fr/hal-00232721 Submitted on 27 Mar 2020 HAL is a multi-disciplinary open access L’archive ouverte pluridisciplinaire HAL, est archive for the deposit and dissemination of sci- destinée au dépôt et à la diffusion de documents entific research documents, whether they are pub- scientifiques de niveau recherche, publiés ou non, lished or not. The documents may come from émanant des établissements d’enseignement et de teaching and research institutions in France or recherche français ou étrangers, des laboratoires abroad, or from public or private research centers. publics ou privés. Distributed under a Creative Commons Attribution| 4.0 International License Scientific Bulletin of the 2nd Workshop on Politehnica University of Timisoara Vortex Dominated Flows Transactions on Mechanics Bucharest, Romania Special issue June 30 – July 1, 2006 A NUMERICAL APPROACH FOR ESTIMATING THE AERODYNAMIC CHARACTERISTICS OF A 2 BLADED VERTICAL DARRIEUS WIND TURBINE Ervin AMET, Phd. Student* Christian PELLONE, Scientist Researcher CNRS Laboratory of Geophysical and Industrial Fluid Laboratory -
Helical Turbine for Hydropower
Tidewalker Engineering / Optimization of GHT Production Marine and Hydrokinetic Technology Readiness Advancement Initiative Funding Opportunity Announcement Number: DE-FOA-0000293 CFDA Number: 81.087 PROJECT NARRATIVE Tidewalker Engineering Trescott, Maine Title: Optimization of Gorlov Helical Turbine Production June 2010 Table of Contents: SUBJECT PAGE NUMBER Introduction: Project Narrative 2 Project Objectives 3 Merit Review Criteria Discussion 7 Project Timetable 13 Relevance and Outcomes / Impacts 14 Role of Participants 14 Facilities and Other Resources 15 Equipment 15 Bibliography and References 16 Appendix- A / Letter of Commitment 17 Appendix – B / Velocity Measurements 18 Appendix – C / GHT Applications 19 Appendix – D / Cost Sharing Grant 32 1 Tidewalker Engineering / Optimization of GHT Production Project Narrative: Under this proposal Tidewalker Engineering with the assistance of Dr. Alexander Gorlov and other specialists will investigate the feasibility of placing a hydro-kinetic device into a flexible dam system to generate electricity from tidal flows at sites with a substantial tidal range (average value of 18’). The study will also include the design of a turbo-generator unit which optimizes electrical production from this proposed mode of operation. Environmental issues associated with the placement of a flexible dam into a tidal flow will be analyzed in terms of regulatory licensing requirements. The applicability of this proposed mode of operation will be addressed as part of expected project benefits from the development potential of this concept. The eligibility standard as expressed in published responses within the Federal Connect network for this grant application directly addressed the issue of diversionary structures as excerpted below: DOE will not consider any application under this FOA for the development of a technology that would require blocking or severely altering existing tidal or river flows, as this would be considered a dam or diversionary structure. -
Friday July 14, 1995
7±14±95 Friday Vol. 60 No. 135 July 14, 1995 Pages 36203±36338 Briefings on How To Use the Federal Register For information on briefing in Washington, DC, see announcement on the inside cover of this issue. federal register 1 II Federal Register / Vol. 60, No. 135 / Friday, July 14, 1995 SUBSCRIPTIONS AND COPIES PUBLIC Subscriptions: Paper or fiche 202±512±1800 FEDERAL REGISTER Published daily, Monday through Friday, Assistance with public subscriptions 512±1806 (not published on Saturdays, Sundays, or on official holidays), by Online: the Office of the Federal Register, National Archives and Records Telnet swais.access.gpo.gov, login as newuser <enter>, no Administration, Washington, DC 20408, under the Federal Register > Act (49 Stat. 500, as amended; 44 U.S.C. Ch. 15) and the password <enter ; or use a modem to call (202) 512±1661, login as swais, no password <enter>, at the second login as regulations of the Administrative Committee of the Federal Register > > (1 CFR Ch. I). Distribution is made only by the Superintendent of newuser <enter , no password <enter . Documents, U.S. Government Printing Office, Washington, DC Assistance with online subscriptions 202±512±1530 20402. Single copies/back copies: The Federal Register provides a uniform system for making Paper or fiche 512±1800 available to the public regulations and legal notices issued by Assistance with public single copies 512±1803 Federal agencies. These include Presidential proclamations and Executive Orders and Federal agency documents having general FEDERAL AGENCIES applicability and legal effect, documents required to be published Subscriptions: by act of Congress and other Federal agency documents of public interest. -
The Inventory of the Richard Lourie Collection #1355
The Inventory of the Richard Lourie Collection #1355 Howard Gotlieb Archival Research Center lourie.r LOURIE, RICHARD 194O- 241C Deposit January 1988 OUTLINE OF INVENTORY 7 Boxes I. MANUSCRIPTS 1973, 1985-1987. A. Novels B. Translations c. Short Fiction D. Poetry E. Film Script F. Essay G. Translated Short Prose II. PRINTED REVIEWS, 1973-1986. III. CORRESPONDENCE, 1979-1988. IV. FINANCIAL STATEMENTS, 1986-1987. 1 LOURIE, RICHARD Deposit from Author June 1987, January 1988 I. MANUSCRIPTS 1973, 1985-1987 A. Novels, 1973, 1985, 1987 Box 1 1. FIRST LOYALTY. Harcourt Brace Jovanovich, 1985. a. Holograph on legal notepads (7), ca. 275 p. (#1) b. Draft. Under title STOLAT. Typescript with holo. corr., ca. 400 p. (#2) Box 1/2 c. Setting copy. Typescript with holo. corr., ca. 540 p. including front matter. (Box 1, #3; Box 2, #1) Box 2 d. Misc. draft pages. Typescript with holo. corr., 6 p. (#2) e. Outline. Holograph, 7 p. on 6 leaves. (#2) 2. SAGITTARIUS IN WARSAW. Vanguard Press, 1973. a. Setting copy. Typescript photocopy and typescript, both with holo. corr. 164 p. including front matter. (#3) b. Galley proofs. (#4) 3. ZERO GRAVITY. Harcourt Brace Jovanovich, 1987. a. Outlines and draft pages. 5 legal notepads, holograph, 141 p. (#5 - 6) b. Miscellaneous draft pages and notes. Typescript with holo. corr. and holograph, ca. 55 p. (#7) Box 3 c. Miscellaneous draft pages. Typescript with holo. corr. and holograph, ca. 65 p. (#1) d. Miscellaneous draft pages. Typescript with holo. corr., photocopy of typescript with holo. corr., and holograph, ca. 400 p. (#2) e. -
Hydroelectric Power Generator
HYDROELECTRIC POWER GENERATOR MIME 1501 Technical Design Report Hydroelectric Power Generator Project #SP02 Final Report Design Advisor: Prof. Gorlov Design Team Anthony Chesna, Tony DiBella, Tim Hutchins, Saralyn Kropf, Jeff Lesica, Jim Mahoney May 29, 2002 Department of Mechanical, Industrial and Manufacturing Engineering College of Engineering, Northeastern University Boston, MA 02115 5 HYDROELECTRIC POWER GENERATOR FOR SMALL VESSELS AND REMOTE STATIONS LOCATED NEAR WATER Design Team Anthony Chesna, Tony Dibella, Timothy Hutchins Saralyn Kropf, Jeff Lesica, James Mahoney Design Advisor Prof. A. M. Gorlov Abstract The objective of this Northeastern University Capstone Design project is to design a hydroelectric power generator to charge batteries on small water vessels. This product will replace devices using non- renewable fossil fuels by utilizing the Gorlov Helical turbine to capture kinetic energy from moving water. Power consumption of a sailing vessel could be 250 Watts or higher. Sailing vessels currently use their engines to recharge on-board batteries, which supply the sailing vessel with electrical power. A renewable electrical production device would allow sailing vessels to recharge on board batteries without having to continually restock fuel and burn fossil fuels. The use of the Gorlov Helical Turbine provides the means to harness the power of moving water with an efficiency of 30 percent or greater. The increased efficiency of the turbine is a direct result of the helical arrangement of the airfoil blades, which eliminates the vibration problems of its predecessor, the Darrieus Turbine. Eliminating vibration increases the life of the turbine by decreasing fatigue and creating a steady flow of electrical current. The design consists of an electrical generator, a transmission system, a supporting structure and the Gorlov Helical Turbine. -
Experimental Investigation of Helical Cross-Flow Axis Hydrokinetic Turbines, Including Effects of Waves and Turbulence
University of New Hampshire University of New Hampshire Scholars' Repository Master's Theses and Capstones Student Scholarship Fall 2011 Experimental investigation of helical cross-flow axis hydrokinetic turbines, including effects of waves and turbulence Peter Bachant University of New Hampshire, Durham Follow this and additional works at: https://scholars.unh.edu/thesis Recommended Citation Bachant, Peter, "Experimental investigation of helical cross-flow axis hydrokinetic turbines, including effects of waves and turbulence" (2011). Master's Theses and Capstones. 649. https://scholars.unh.edu/thesis/649 This Thesis is brought to you for free and open access by the Student Scholarship at University of New Hampshire Scholars' Repository. It has been accepted for inclusion in Master's Theses and Capstones by an authorized administrator of University of New Hampshire Scholars' Repository. For more information, please contact [email protected]. EXPERIMENTAL INVESTIGATION OF HELICAL CROSS-FLOW AXIS HYDROKINETIC TURBINES, INCLUDING EFFECTS OF WAVES AND TURBULENCE BY PETER BACHANT BSME, University of Massachusetts Dartmouth, 2008 THESIS Submitted to the University of New Hampshire in Partial Fulfillment of the Requirements for the Degree of Master of Science in Mechanical Engineering September, 2011 UMI Number: 1504939 All rights reserved INFORMATION TO ALL USERS The quality of this reproduction is dependent upon the quality of the copy submitted. In the unlikely event that the author did not send a complete manuscript and there are missing pages, these will be noted. Also, if material had to be removed, a note will indicate the deletion. UMI Dissertation Publishing UMI 1504939 Copyright 2011 by ProQuest LLC. All rights reserved. -
Ocean Energy Task Force Final Report, 2009
Final Report of the Ocean Energy Task Force to Governor John E. Baldacci December 2009 Photo credits (clockwise from top center): Solberg/Statoil; Maine Coastal Program; Ocean Renewable Power Company; Principle Power; Blue H. Center photo: Global Marine Systems, Ltd. Final Report of the Ocean Energy Task Force to Governor John E. Baldacci December 2009 Financial assistance for this document was provided by a grant from the Maine Coastal Program at the Maine State Planning Office, through funding provided by the U.S. Department of Commerce, Office of Ocean and Coastal Resource Management under the Coastal Zone Management Act of 1972, as amended. Additional financial assistance was provided by the Efficiency Maine Trust (Efficiency Maine Trust is a statewide effort to promote the more efficient use of electricity, help Maine residents and businesses reduce energy costs, and improve Maine’s environment), and by the American Recovery and Reinvestment Act of 2009. This publication was produced under appropriation number 020-07B-008205 Final Report of the Ocean Energy Task Force TABLE OF CONTENTS Acknowledgements.....................................................................................................................................ii Executive Summary ...................................................................................................................................iii Summary of Recommendations..............................................................................................................vii Overview -
Cal Poly Nano Hydro
Cal Poly Nano Hydro By Brandon N. Fujio Alex J. Sobel Andrew F. Del Prete Mechanical Engineering Department California Polytechnic State University San Luis Obispo 2013 Statement of Disclaimer Since this project is a result of a class assignment, it has been graded and accepted as fulfillment of the course requirements. Acceptance does not imply technical accuracy or reliability. Any use of information in this report is done at the risk of the user. These risks may include catastrophic failure of the device or infringement of patent or copyright laws. California Polytechnic State University at San Luis Obispo and its staff cannot be held liable for any use or misuse of the project. Table of Contents Executive Summary ....................................................................................................................................... 1 Chapter 1: Introduction ................................................................................................................................ 5 1.1 Background and Needs ....................................................................................................................... 5 1.2 Problem Definition .............................................................................................................................. 6 1.3 Objective/Specification Development ................................................................................................ 6 1.4 Project Management ......................................................................................................................... -
Annual Report 2009-2010 Department Administration and Committees3 Highlights6 Department of Mechanical Engineering Faculty Awards13
An Report 2008-2009 D College of Engineering Annual Report 2009-2010 Department Administration and Committees3 Highlights6 Department of Mechanical Engineering Faculty Awards13 Faculty16 Adjunct, Re- search, Visiting and Associated Faculty19 Staff20 New Faculty and Staff20 Enrollment 22 Degrees Award- ed23 Courses Of- fered24 Objectives and Outcomes 26 Student Awards27 Student Organizations28 Senior Design Projects31 Recruitment36 Enrollment by Program37 Teaching Fellows and Research Assistants38 C O N T E N T S MESSAGE FROM THE CHAIR OVERVIEW 2 Highlights 6 Faculty Awards FACULTY AND STAFF 9 Faculty 12 New Faculty 13 Secondary Faculty 13 Staff UNDERGRADUATE PROGRAMS 15 Objectives and Outcomes 16 Enrollment 16 Degrees Awarded 17 Undergraduate Courses Offered 19 Student Awards 20 Student Organizations 23 Senior Design Projects GRADUATE PROGRAMS 28 Enrollment by Degree Program 29 Graduate Student Awards 30 Degrees Awarded 31 Graduate Courses Offered 32 MS Theses and PhD Dissertations 33 Distance Learning RESEARCH 37 Research Funding 45 Faculty Publications 65 Research Laboratories 70 Affiliated Research Centers 72 Seminars 74 Merril L. Ebner Fund 2 www.bu.edu/me/ At the graduate level, the department offers the PhD in ME as well MESSAGE FROM THE CHAIR as MS degrees in both ME and MFG. Both thesis and non-thesis op- tions are available, and interested students can choose to pursue the MS in manufacturing via distance learning, as part of an international partnership with a consortium of German institutions, or even as a dual MS/MBA degree offered jointly with the School of Management. This programmatic diversity is a direct consequence of the merger, and positions the ME department to respond to new challenges and opportunities in both education and research. -
University of Kwazulu-Natal Design of a Novel Hydrokinetic Turbine for Ocean Current Power Generation
UNIVERSITY OF KWAZULU-NATAL COLLEGE OF AGRICULTURE, ENGINEERING AND SCIENCE DESIGN OF A NOVEL HYDROKINETIC TURBINE FOR OCEAN CURRENT POWER GENERATION Kumaresan Cunden Dissertation submitted in fulfilment of the academic requirements for the degree of Master of Science in Mechanical Engineering Supervisor: Dr Freddie L. Inambao October 2014 “As the candidate’s Supervisor I agree/do not agree to the submission of this dissertation”. The supervisor must sign all copies after deleting which is not applicable. Dr Freddie L. Inambao NAME OF SUPERVISOR SIGNATURE I Form EX1-5 COLLEGE OF AGRICULTURE, ENGINEERING AND SCIENCE DECLARATION 1 - PLAGIARISM I, Kumaresan Cunden, declare that: 1. The research reported in this dissertation, except where otherwise indicated, is my original research. 2. This dissertation has not been submitted for any degree or examination at any other university. 3. This dissertation does not contain other persons’ data, pictures, graphs or other information, unless specifically acknowledged as being sourced from other persons. 4. This dissertation does not contain other persons' writing, unless specifically acknowledged as being sourced from other researchers. Where other written sources have been quoted, then: a. Their words have been re-written but the general information attributed to them has been referenced. b. Where their exact words have been used, then their writing has been placed in italics and inside quotation marks, and referenced. 5. This dissertation does not contain text, graphics or tables copied and pasted