Equilibrium Analysis of Masonry Domes
Total Page:16
File Type:pdf, Size:1020Kb
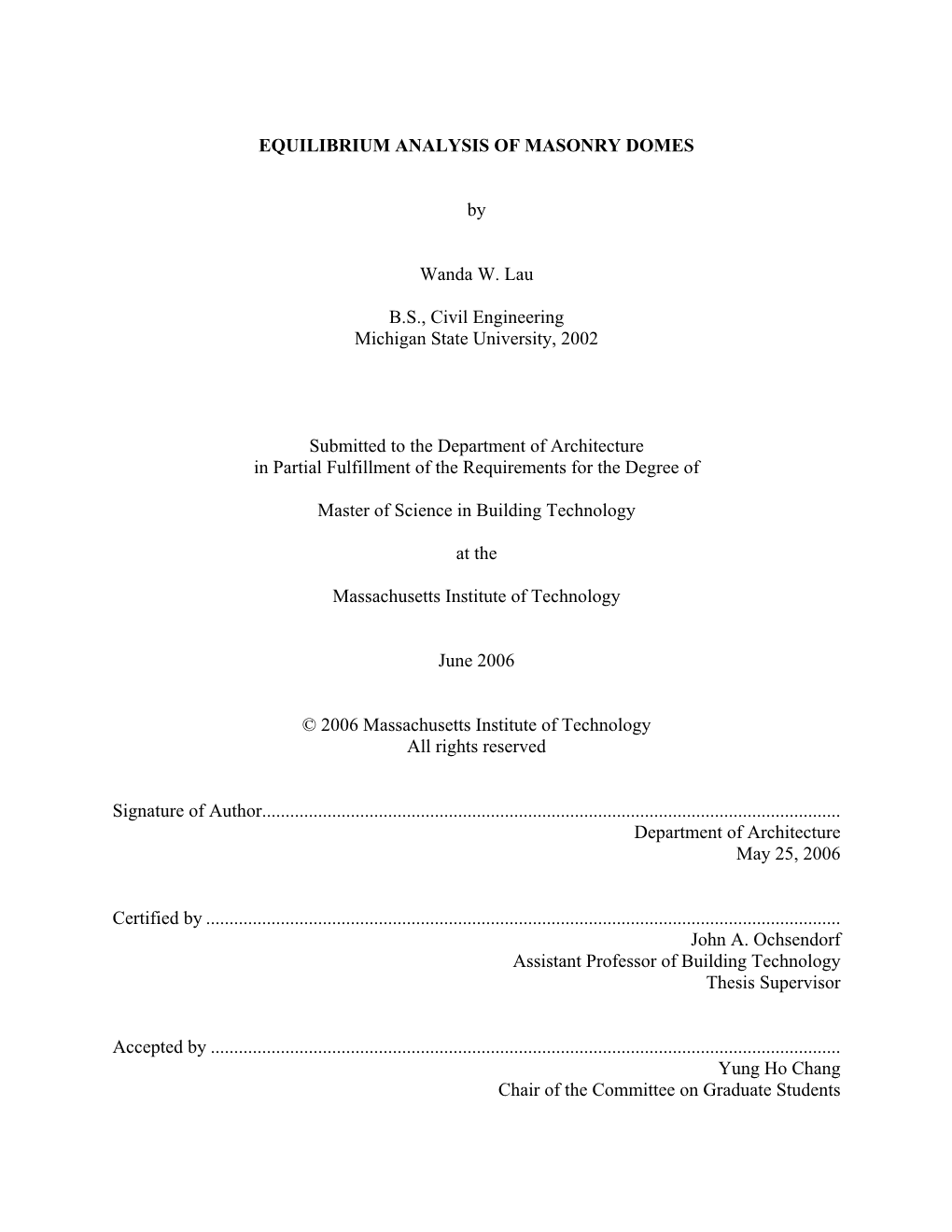
Load more
Recommended publications
-
Advancements in Arch Analysis and Design During the Age of Enlightenment
ADVANCEMENTS IN ARCH ANALYSIS AND DESIGN DURING THE AGE OF ENLIGHTENMENT by EMILY GARRISON B.S., Kansas State University, 2016 A REPORT submitted in partial fulfillment of the requirements for the degree MASTER OF SCIENCE Department of Architectural Engineering and Construction Science and Management College of Engineering KANSAS STATE UNIVERSITY Manhattan, Kansas 2016 Approved by: Major Professor Kimberly Waggle Kramer, PE, SE Copyright Emily Garrison 2016. Abstract Prior to the Age of Enlightenment, arches were designed by empirical rules based off of previous successes or failures. The Age of Enlightenment brought about the emergence of statics and mechanics, which scholars promptly applied to masonry arch analysis and design. Masonry was assumed to be infinitely strong, so the scholars concerned themselves mainly with arch stability. Early Age of Enlightenment scholars defined the path of the compression force in the arch, or the shape of the true arch, as a catenary, while most scholars studying arches used statics with some mechanics to idealize the behavior of arches. These scholars can be broken into two categories, those who neglected friction and those who included it. The scholars of the first half of the 18th century understood the presence of friction, but it was not able to be quantified until the second half of the century. The advancements made during the Age of Enlightenment were the foundation for structural engineering as it is known today. The statics and mechanics used by the 17th and 18th century scholars are the same used by structural engineers today with changes only in the assumptions made in order to idealize an arch. -
The Story of Architecture
A/ft CORNELL UNIVERSITY LIBRARY FINE ARTS LIBRARY CORNELL UNIVERSITY LIBRARY 924 062 545 193 Production Note Cornell University Library pro- duced this volume to replace the irreparably deteriorated original. It was scanned using Xerox soft- ware and equipment at 600 dots per inch resolution and com- pressed prior to storage using CCITT Group 4 compression. The digital data were used to create Cornell's replacement volume on paper that meets the ANSI Stand- ard Z39. 48-1984. The production of this volume was supported in part by the Commission on Pres- ervation and Access and the Xerox Corporation. Digital file copy- right by Cornell University Library 1992. Cornell University Library The original of this book is in the Cornell University Library. There are no known copyright restrictions in the United States on the use of the text. http://www.archive.org/cletails/cu31924062545193 o o I I < y 5 o < A. O u < 3 w s H > ua: S O Q J H HE STORY OF ARCHITECTURE: AN OUTLINE OF THE STYLES IN T ALL COUNTRIES • « « * BY CHARLES THOMPSON MATHEWS, M. A. FELLOW OF THE AMERICAN INSTITUTE OF ARCHITECTS AUTHOR OF THE RENAISSANCE UNDER THE VALOIS NEW YORK D. APPLETON AND COMPANY 1896 Copyright, 1896, By D. APPLETON AND COMPANY. INTRODUCTORY. Architecture, like philosophy, dates from the morning of the mind's history. Primitive man found Nature beautiful to look at, wet and uncomfortable to live in; a shelter became the first desideratum; and hence arose " the most useful of the fine arts, and the finest of the useful arts." Its history, however, does not begin until the thought of beauty had insinuated itself into the mind of the builder. -
Hana Taragan HISTORICAL REFERENCE in MEDIEVAL ISLAMIC ARCHITECTURE: BAYBARS's BUILDINGS in PALESTINE
the israeli academic center in cairo ¯È‰˜· Èχ¯˘È‰ ÈÓ„˜‡‰ ÊίӉ Hana Taragan HISTORICAL REFERENCE IN MEDIEVAL ISLAMIC ARCHITECTURE: BAYBARS’S BUILDINGS IN PALESTINE Hana Taragan is a lecturer in Islamic art at Tel Aviv University, where she received her Ph.D. in 1992. Her current research concerns Umayyad and Mamluk architecture in Eretz Israel in the medieval period. She is the author of Art and Patronage in the Umayyad Palace in Jericho (in Hebrew) and of numerous articles in the field of Islamic art. In the year 1274, al-Malik al-Zahir also changed a structure’s function Baybars, the first Mamluk ruler of from church to mosque, as he did Palestine (1260–1277), ordered the in Qaqun.5 addition of a riwaq (porch) to the Baybars’s choice of Yavne may tomb of Abu Hurayra in Yavne.1 be explained by the ruin of the The riwaq, featuring a tripartite coastal towns, or by Yavne’s loca- portal and six tiny domes, had two tion on the main road from Cairo arches decorated with cushion to Damascus. However, it seems to voussoirs and one with a zigzag me that above and beyond any frieze (Figure 1). Baybars also strategic and administrative con- installed a dedicatory inscription siderations, Baybars focused on naming himself as builder of the this site in an attempt to exploit riwaq.2 The addition of a portal to Abu Hurayra’s tomb as a means of the existing tomb structure typifies institutionalizing the power of the Baybars’s building policy in Pales- Mamluk dynasty in general and tine. -
The Aesthetics of Islamic Architecture & the Exuberance of Mamluk Design
The Aesthetics of Islamic Architecture & The Exuberance of Mamluk Design Tarek A. El-Akkad Dipòsit Legal: B. 17657-2013 ADVERTIMENT. La consulta d’aquesta tesi queda condicionada a l’acceptació de les següents condicions d'ús: La difusió d’aquesta tesi per mitjà del servei TDX (www.tesisenxarxa.net) ha estat autoritzada pels titulars dels drets de propietat intel·lectual únicament per a usos privats emmarcats en activitats d’investigació i docència. No s’autoritza la seva reproducció amb finalitats de lucre ni la seva difusió i posada a disposició des d’un lloc aliè al servei TDX. No s’autoritza la presentació del s eu contingut en una finestra o marc aliè a TDX (framing). Aquesta reserva de drets afecta tant al resum de presentació de la tesi com als seus continguts. En la utilització o cita de parts de la tesi és obligat indicar el nom de la persona autora. ADVERTENCIA. La consulta de esta tesis queda condicionada a la aceptación de las siguientes condiciones de uso: La difusión de esta tesis por medio del servicio TDR (www.tesisenred.net) ha sido autorizada por los titulares de los derechos de propiedad intelectual únicamente para usos privados enmarcados en actividades de investigación y docencia. No se autoriza su reproducción con finalidades de lucro ni su difusión y puesta a disposición desde un sitio ajeno al servicio TDR. No se autoriza la presentación de su contenido en una ventana o marco ajeno a TDR (framing). Esta reserva de derechos afecta tanto al resumen de presentación de la tesis como a sus contenidos. -
Graphical and Analytical Quantitative Comparison in the Domes Assessment: the Case of San Francesco Di Paola
applied sciences Article Graphical and Analytical Quantitative Comparison in the Domes Assessment: The Case of San Francesco di Paola Concetta Cusano 1,*,†, Andrea Montanino 2,† , Carlo Olivieri 3,† , Vittorio Paris 4,† and Claudia Cennamo 1,† 1 Department of Architecture and Industrial Design, Universitá degli Studi della Campania “Luigi Vanvitelli”, Abbazia di San Lorenzo in Septimum, 81031 Aversa (CE), Italy; [email protected] 2 Department of Structures for Engineering and Architecture, Università degli Studi di Napoli “Federico II”, Via Claudio 21, 80143 Napoli (NA), Italy; [email protected] 3 Department of Civil Engineering, DICIV, Università degli Studi di Salerno, Via Giovanni Paolo II 132, 84084 Fisciano (SA), Italy; [email protected] 4 Department of Engineering and Applied Sciences, Università degli Studi di Bergamo, Via G. Marconi 5, 24044 Dalmine (BG), Italy; [email protected] * Correspondence: [email protected] † These authors contributed equally to this work. Abstract: (1) Methods for checking the condition of monumental masonry structures can still be considered understudied. Among the different approaches available in the literature, the graphical ones have a special role, due to their simplicity and effectiveness. (2) In this work, a 2D method (Thrust Line Analysis (TLA)), the Modified Thrust Line Method (MTLM), and the 3D Membrane Equilibrium Analysis (MEA) method are compared. All methods have the same starting concept: no tensile strength, no sliding between the stone blocks, infinite compressive strength. (3) The methods are compared in terms of stress distribution (for the same—or similar—thrust line), and in terms Citation: Cusano, C.; Montanino, A.; Olivieri, C.; Paris, V.; Cennamo, C. -
The Structural Development of Masonry Domes in India
Proceedings of the First International Congress on Construction History, Madrid, 20th-24th January 2003, ed. S. Huerta, Madrid: I. Juan de Herrera, SEdHC, ETSAM, A. E. Benvenuto, COAM, F. Dragados, 2003. The structural development of masonry domes in India Stuart Tappin This paper researches the origins, structural which still generally relies on non-mechanised development and construction of masonry domes in methods of building and documented practice in India. It investigates where the structural engineering Europe during the period under study. knowledge of the original builders carne from and how successfully that knowledge was applied. We will also look at the choices that had to be made with ISLAMIC PROTOTYPES materials and methods of construction. The period under review covers Islamic rule over In Syria the classical Roman temples and mausolea northern and central India fram the late 12th century became the model for builders who created churches to the mid 18th century. New types of buildings or memorial s to house the body or relics of Christian and structural forms carne with the new rulers in saints or biblical character, or to mark a particular particular, for this study, the domed tambo How event (Hillenbrand 1984, 254). These were generally Hindu masons, experienced only in trabe ate small in scale and used a variety of plan-forms; construction, responded to these new structural forms square, cruciform, polygonal or circular. The small is a key part the synthesis of sty les that created a size meant that the structura] stability of the dome wholly new and original architecture. could be achieved by copying existing buildings. -
Reflection of Technology on the Inherited Conceptual Design of Mosques
Ain Shams University Faculty of Engineering Department of Architecture REFLECTION OF TECHNOLOGY ON THE INHERITED CONCEPTUAL DESIGN OF MOSQUES A thesis submitted to the Faculty of Engineering - Ain Shams University in partial fulfillment of the requirements for Master of Science Degree in Architecture By Radwa Ahmed Omar Abuel Seoud B.Sc. Architecture-Ain Shams University, 2006 Under the supervision of Prof. Dr. Khaled Dewidar Professor - Department of Architecture Faculty of Engineering - Ain Shams University Prof. Dr. Shaimaa Kamel Professor - Department of Architecture Faculty of Engineering - Ain Shams University Dr. Somaya Bahy Eldin Lecturer - Department of Architecture Faculty of Engineering - Ain Shams University 2013 Statement I hereby declare that all information in this document has been obtained and presented in accordance with academic rules and ethical conduct. I also declare that, as required by these rules and conduct, I have fully cited and referenced all material and results that are not original to this work. Name: Radwa Ahmed Omar Abuel Seoud Signature: Date: Ain Shams University Faculty of Engineering Department of Architecture Submitted by: Radwa Ahmed Omar Abuel Seoud Thesis Title: Reflection of Technology on the Inherited Conceptual Design of Mosques Supervising Committee: Signature Prof. Dr. Khaled Dewidar Professor - Department of Architecture Faculty of Engineering - Ain Shams University Prof. Dr. Shaimaa Kamel Professor - Department of Architecture Faculty of Engineering - Ain Shams University Dr. Somaya Bahy -
Oval Domes: History, Geometry and Mechanics
Santiago Huerta Research E. T.S. de Arquitectura Oval Domes: Universidad Politécnica de Madrid Avda. Juan de Herrera, 4 History, Geometry and Mechanics 28040 Madrid SPAIN Abstract. An oval dome may be defined as a dome whose [email protected] plan or profile (or both) has an oval form. The word “oval” Keywords: oval domes, history of comes from the Latin ovum, egg. The present paper contains engineering, history of an outline of the origin and application of the oval in construction, structural design historical architecture; a discussion of the spatial geometry of oval domes, that is, the different methods employed to lay them out; a brief exposition of the mechanics of oval arches and domes; and a final discussion of the role of geometry in oval arch and dome design. Introduction An oval dome may be defined as a dome whose plan or profile (or both) has an oval form. The word Aoval@ comes from the Latin ovum, egg. Thus, an oval dome is egg-shaped. The first buildings with oval plans were built without a predetermined form, just trying to enclose a space in the most economical form. Eventually, the geometry was defined by using circular arcs with common tangents at the points of change of curvature. Later the oval acquired a more regular form with two axes of symmetry. Therefore, an “oval” may be defined as an egg-shaped form, doubly symmetric, constructed with circular arcs; an oval needs a minimum of four centres, but it is possible also to build ovals with multiple centres. The preceding definition corresponds with the origin and the use of oval forms in building and may be applied without problem up to, say, the eighteenth century. -
Dictionary of Islamic Architecture
DICTIONARY OF ISLAMIC ARCHITECTURE DICTIONARY OF ISLAMIC ARCHITECTURE Andrew Petersen London and New York First published 1996 by Routledge 11 New Fetter Lane, London EC4P 4EE This edition published in the Taylor & Francis e-Library, 2002. Simultaneously published in the USA and Canada by Routledge 29 West 35th Street, New York, NY 10001 First published in paperback 1999 © 1996 Andrew Petersen All rights reserved. No part of this book may be reprinted or reproduced or utilized in any form or by any electronic, mechanical, or other means, now known or hereafter invented, including photocopying and recording, or in any information storage or retrieval system, without permission in writing from the publishers. British Library Cataloguing in Publication Data A catalogue record for this book is available from the British Library Library of Congress Cataloging in Publication Data A catalogue record for this book is available from the Library of Congress ISBN 0-415-06084-2 (hbk) ISBN 0-415-21332-0 (pbk) ISBN 0-203-20387-9 Master e-book ISBN ISBN 0-203-20390-9 (Glassbook Format) Contents Preface vii Acknowledgements ix Entries 1 Appendix The Mediterranean World showing principal historic cities and sites 320 The Middle East and Central Asia showing principal historic cities and sites 321 Dedication This book is dedicated to my friend Jamie Cameron (1962–95) historian of James V of Scotland. Preface In one of the quarters of the city is the Muhammadan town, where the Muslims have their cathedral, mosque, hospice and bazar. They have also a qadi and a shaykh, for in every one of the cities of China there must always be a shaykh al- Islam, to whom all matters concerning Muslims are referred. -
Etruscan 700-300 Bc Classical Greece 750-146 Bc Early Christain 100-800 Ad
EARLY CHRISTAIN : key characteristics -baptistery MINOAN ETRUSCAN -mausoleum 3100-1100 BC 700-300 BC -martyria MINOAN : Knossos, Crete key characteristics EARLY -inverted columns* -space haphazardly -no city walls on flat -fasces; strength, -voussoir arch; underground -tuscan order* -fresco wall paintings CHRISTAIN organized around land DARK AGES power, unity sewage -clerestory windows 100-800 AD courtyard 1100-750 BC -pictio/proto writing ETRUSCAN : NE of Italy -modeled after roman floor & ceiling treatments -monarchies basillica, apse, altar, & nave -gypsum & limestone (floors) city characteristics -plaster & frescos (ceilings) -city states -plaster, fresco, marble facings -grid layouts (walls) -interior staircases -post & lintel -minotaur and the -steep hilltops -related to megaron below lightwells construction labyrinth -wood & adobe brick -high stone base -wide overhanging eves -stairs at front -3 room cella -addition of transept with nave, altar, &apse -climate change -ionic order* ROMAN EMPIRE : acroteriae entablature tympanum -roads -Pantheon cornice frieze -warrior aristocracy -corbel arches to -trusses to span -city walls; rubble, ashlar, & -barrel vault span space space cyclopian masonry -volcanic eruption architrave -groin vault -steep hills -doric order* -corinthian order* -bridges & roman temple : composite columns aqueducts columns*, engaged columns*, high platform base with stairs at front CLASSICAL stylobate -hypocaust MYCENEAN : Greece & Crete GREECE -king agamenmnon -tsunami 750-146 BC city characteristics -invasions -
Landmarks Manual Table of Contents I
Landmark Manual Ray Gindroz, Jungle Road , 1993 , Palm Beach, FL. Jane S. Day Town of Palm Beach, Florida Landmarks Preservation Commission And The Preservation Foundation of Palm Beach 2009 Effects of Landmarking Landmarking Does: Landmarking Does NOT: Preserve important buildings in the Change any existing zoning community Prohibit redevelopment Preserve property values by discouraging redevelopment and increases in density Lead to declines in property value Stabilize and improve property values based Usurp individual rights because all on appraisal information construction goes to either the Landmarks or Architectural Commission Require Landmarks Commission review of exterior alterations and new construction Affect interior changes Require exterior only review Create an extra municipal hurdle for the Landmark’s owner Substitute Landmarks Commission review for Architectural Commission review Require restoration Offer restoration and rehabilitation Restrict normal maintenance information to property owners Prevent modernizing a building Allow normal maintenance without review by the Landmarks Commission Require a building to be open to the public or to have a historic sign Provide a mechanism for quick administrative approval, usually for minor changes ($2,000 or Lead to a listing on a tourism map less) such as security lighting, driveways, etc. Encourage historic research and community pride Preserve the historic and cultural integrity of Palm Beach Acknowledgements The Town of Palm Beach would like to thank the following for their gracious help in the publication and production of the Landmark Manual : The Preservation Foundation of Palm Beach The Preservation Foundation of Palm Beach is a private, non-profit membership organization dedicated to the preservation of the historic, architectural, and cultural heritage of Palm Beach, Florida. -
Exotic Revival, 1900-1980
LOS ANGELES CITYWIDE HISTORIC CONTEXT STATEMENT Context: ARCHITECTURE AND ENGINEERING Theme: Exotic Revival, 1900-1980 Prepared for: City of Los Angeles Department of City Planning Office of Historic Resources DECEMBER 2015 SurveyLA Citywide Historic Context Statement Context: Architecture and Engineering; Theme: Exotic Revival, 1900-1980 TABLE OF CONTENTS PREFACE 3 CONTRIBUTORS 3 INTRODUCTION 3 HISTORIC CONTEXT 5 Sub-theme: Mayan Revival, 1910-1950 10 Sub-theme: Egyptian Revival, 1920-1940 15 Sub-theme: Byzantine Revival, 1926-1965 19 Sub-theme: Moorish Revival, 1895-1940 23 Sub-theme: East Asian Eclectic, 1920-1980 28 Sub-theme: Tiki/Polynesian, 1940-1960 30 SELECTED BIBLIOGRAPHY 34 Page | 2 SurveyLA Citywide Historic Context Statement Context: Architecture and Engineering; Theme: Exotic Revival, 1900-1980 PREFACE This theme is a component of Los Angeles’ citywide historic context statement and provides guidance to field surveyors in identifying and evaluating potential historic resources relating to Exotic Revival architecture. Refer to www.HistoricPlacesLA.org for information on designated resources associated with this theme as well as those identified through SurveyLA and other surveys. CONTRIBUTORS Teresa Grimes and Amanda Yoder, GPA Consulting. Ms. Grimes is a Principal Architectural Historian at GPA Consulting. She earned her Master of Arts degree in Architecture from the University of California, Los Angeles and has over twenty-five years of experience in the field. Ms. Yoder is an Architectural Historian at GPA Consulting; she earned her Bachelor of Fine Arts degree in Historic Preservation from the Savannah College of Art and Design, and has been practicing in the field since 2011. INTRODUCTION The theme of “Exotic Revival, 1900-1980” examines a collection of six sub-themes: Mayan Revival, Egyptian Revival, Byzantine Revival, Moorish Revival, East Asian Eclectic, and Tiki/Polynesian.