Enhancement of EM Pump Performance Through Modeling and Testing
Total Page:16
File Type:pdf, Size:1020Kb
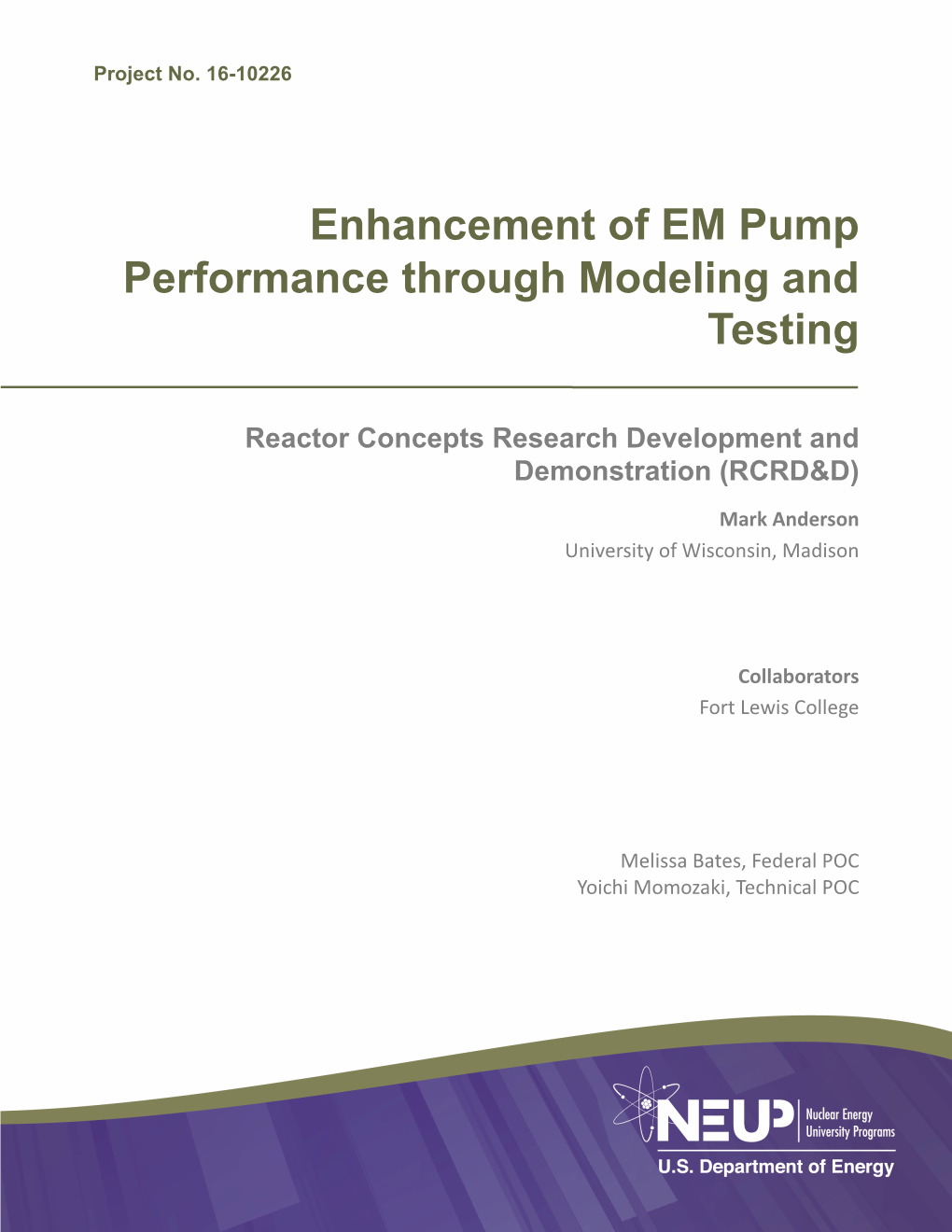
Load more
Recommended publications
-
MHD Interaction in an Electromagnetic Pump for High Flow Rate Loop Of
MHD interaction in an Electromagnetic Pump for high flow rate loop of ASTRID Sodium Fast Reactor secondary circuit -performances S Letout, Y Duterrail, Y Fautrelle, M Medina, F Rey, G Laffont To cite this version: S Letout, Y Duterrail, Y Fautrelle, M Medina, F Rey, et al.. MHD interaction in an Electromagnetic Pump for high flow rate loop of ASTRID Sodium Fast Reactor secondary circuit -performances. 8th International Conference on Electromagnetic Processing of Materials, Oct 2015, Cannes, France. hal- 01336384 HAL Id: hal-01336384 https://hal.archives-ouvertes.fr/hal-01336384 Submitted on 23 Jun 2016 HAL is a multi-disciplinary open access L’archive ouverte pluridisciplinaire HAL, est archive for the deposit and dissemination of sci- destinée au dépôt et à la diffusion de documents entific research documents, whether they are pub- scientifiques de niveau recherche, publiés ou non, lished or not. The documents may come from émanant des établissements d’enseignement et de teaching and research institutions in France or recherche français ou étrangers, des laboratoires abroad, or from public or private research centers. publics ou privés. MHD interaction in an Electromagnetic Pump for high flow rate loop of ASTRID Sodium Fast Reactor secondary circuit - performances 1 1 1 1 2 2 S. Letout , Y. Duterrail , Y. Fautrelle , M. Medina , F. Rey and G. Laffont 1Grenoble Institute of Technology/CNRS, SIMAP-EPM laboratory, 38402 Saint Martin d’Hères, France 2Commissariat à l’Energie Atomique et aux Energies Alternatives, 13108 Saint Paul Lez Durance, France Corresponding author: [email protected] Abstract The present paper deals with the analysis of the performances of a very large Annular Linear Induction Pumps (ALIP) for liquid sodium. -
Formation of a Stationary State of Striations in a Vertically Inhomogeneous Ionosphere
FORMATION OF A STATIONARY STATE OF STRIATIONS IN A VERTICALLY INHOMOGENEOUS IONOSPHERE N.D.Borisov Institute of Terrestrial Magnetism, Ionosphere and Radio Waves Propagation, (IZMIRAN), 142190 Troitsk, Moscow region, Russia, [email protected] Abstract A new theory of a stationary state of striations is presented. Striations are treated as slowly varying with the height wave- guides that trap upper-hybrid resonance (UHR) oscillations. Modes with different discrete eigennumbers are retained in striations. Each mode interacts with a pump wave within a restricted range of heights. Thus the vertical ionospheric inhomogeneity determines the amplification of UHR oscillations. Anomalous absorption of the pump wave associated with the excitation of UHR oscillations in striations is calculated. Typical transversal scales and increase of the electron temperature in striations are estimated. INTRODUCTION One of the most interesting physical phenomena associated with the HF heating of the ionosphere is the formation of striations - elongated plasma depletions [1]. According to the theory striations are created as a result of conversion of the EM pump wave into UHR oscillations on small scale plasma irregularities [2]. UHR oscillations are trapped in striations and increase their amplitude due to the resonance (thermal parametric) instability. The mechanism of amplification of UHR oscillations and the formation of the stationary state of striations is a complicated theoretical problem. The existing modern theories treat this problem taking into account only the transversal plasma inhomogeneity [3, 4]. At the same time it is well-known that the longitudinal inhomogeneity of plasma changes the process of the waves interaction. The instability instead of absolute becomes of a convective type thus restricting the amplitude of the growing waves. -
Study of MHD Instabilities in High Flowrate Induction Electromagnetic Pumps of Annular Linear Design Elena Martin Lopez
Study of MHD instabilities in high flowrate induction electromagnetic pumps of annular linear design Elena Martin Lopez To cite this version: Elena Martin Lopez. Study of MHD instabilities in high flowrate induction electromagnetic pumps of annular linear design. Mechanics of materials [physics.class-ph]. Université Grenoble Alpes, 2018. English. NNT : 2018GREAI090. tel-02055466 HAL Id: tel-02055466 https://tel.archives-ouvertes.fr/tel-02055466 Submitted on 4 Mar 2019 HAL is a multi-disciplinary open access L’archive ouverte pluridisciplinaire HAL, est archive for the deposit and dissemination of sci- destinée au dépôt et à la diffusion de documents entific research documents, whether they are pub- scientifiques de niveau recherche, publiés ou non, lished or not. The documents may come from émanant des établissements d’enseignement et de teaching and research institutions in France or recherche français ou étrangers, des laboratoires abroad, or from public or private research centers. publics ou privés. THÈSE Pour obtenir le grade de DOCTEUR DE LA COMMUNAUTE UNIVERSITE GRENOBLE ALPES Spécialité : IMEP2 / MECANIQUE DES FLUIDES, PROCEDES, ENERGETIQUE Arrêté ministériel : 25 mai 2016 Présentée par « Elena MARTIN LOPEZ » Thèse dirigée par Yves DELANNOY codirigée par Fabrice BENOIT préparée au sein du SIMAP/EPM dans IMEP2 / MECANIQUE DES FLUIDES, PROCEDES, ENERGETIQUE Etude des instabilités Magnétohydrodynamiques dans les Pompes Electromagnétiques à induction annulaire à fort débit Thèse soutenue publiquement le « 29/11/2018 », devant le jury composé de : Mr. Alain JARDY Professeur, Ecole des Mines de Nancy, Président du jury et Rapporteur Mr. Thierry ALBOUSSIERE Directeur de Recherche, CNRS à Lyon, Rapporteur Mr. Christophe GISSINGER Maître de Conférence, Ecole Normale Supérieure de Paris, Membre Mr. -
European Patent Bulletin 1983/30
6 1983/30 •p*- 27.07.1983 Lîbl '.; y BibUofr,-, i 0 084 021 - 0 084 527 2 9. JULJ ,:.J ISSN 0170-9305 EPA-EPO-OE8 R^SSHHTRI "'»"»wffro -trz 'iurri, Europäisches European Bulletin européen Patentblatt Patent Bulletin des brevets Inhalt Contents Sommaire I Veröffentlichte Anmeldungen 2 I Published Applications 3 I Demandes publiées 3 1.1 Geordnet nach der Internationalen 1.1 Arranged in accordance with the 1.1 Classées selon la classification Patentklassifikation 8 International Patent internationale des brevets 8 1.2 Geordnet nach PCT-Veröffent- Classification 8 1.2 Classées selon les numéros de lichungsnummern 70 1.2 Arranged by PCT publication publication PCT 70 1.3(1) Geordnet nach Veröffentlichungs- number 70 13(1) Classées selon les numéros de nummern 71 1-3(1) Arranged by publication publication 71 1.3 (2) Geordnet nach Anmelde- number 71 1-3(2) Classées selon les numéros des nummern 75 1.3 (2) Arranged by application demandes 75 1.4 Geordnet nach Namen der number 75 1.4 Classées selon les noms des Anmelder 80 1.4 Arranged by nîme of demandeurs 80 1.5 Geordnet nach benannten applicant 80 1.5 Classées selon les Etats Vertragsstaaten 88 1.5 Arranged by designated contractants désignés 88 1.6 (1) Nach Erstellung des europäischen Contracting State 88 1-6(1) Documents découverts après Recherchenberichts ermittelte neue 1.6 (1) Documents discovered after comple- l'établissement du rapport de Schriftstücke — tion of the European search recherche européenne — 1.6 (2) Gesonderte Veröffentlichung des report — 1.6 (2) Publication séparée du -
A Magnetohydrodynamic Study of Behavior in an Electrolyte Fluid Using Numerical and Experimental Solutions
Ciência/Science A MAGNETOHYDRODYNAMIC STUDY OF BEHAVIOR IN AN ELECTROLYTE FLUID USING NUMERICAL AND EXPERIMENTAL SOLUTIONS L. P. Aoki, ABSTRACT M. G. Maunsell, This article examines a rectangular closed circuit filled with an electrolyte and H. E. Schulz fluid, known as macro pumps, where a permanent magnet generates a magnetic field and electrodes generate the electric field in the flow. The fluid conductor moves inside the circuit under magnetohydrodynamic effect (MHD). The MHD model has been derived from the Navier Stokes equation and coupled with the Maxwell equations for Newtonian incompressible Universidade de São Paulo fluid. Electric and magnetic components engaged in the test chamber assist Escola de Engenharia de São Carlos in creating the propulsion of the electrolyte fluid. The electromagnetic Departamento de Engenharia Mecânica forces that arise are due to the cross product between the vector density of induced current and the vector density of magnetic field applied. This is the Parque Arnold Schimidt Lorentz force. Results are present of 3D numerical MHD simulation for CP. 13566-590, São Carlos, São Paulo, Brasil newtonian fluid as well as experimental data. The goal is to relate the [email protected] magnetic field with the electric field and the amounts of movement produced, and calculate de current density and fluid velocity. An u-shaped and m-shaped velocity profile is expected in the flows. The flow analysis is performed with the magnetic field fixed, while the electric field is changed. Observing the interaction between the fields strengths, and density of the electrolyte fluid, an optimal configuration for the flow velocity is determined and compared with others publications. -
Electromagnetic Pumps for Liquid Metals
Calhoun: The NPS Institutional Archive Theses and Dissertations Thesis Collection 1965 Electromagnetic pumps for liquid metals Gutierrez, Alejandro U. Monterey, California. Naval Postgraduate School http://hdl.handle.net/10945/12091 NPS ARCHIVE 1965 GUTIERREZ, A. ELECTROMAGNETIC \>\M?$ FOR LIQUID METALS ALEJANDRO U. GUTIERREZ CLAIR E. HECKATHORN \m H Hi »»»»»i iL^LlllJAhUiA:. •y iduatt; DUDLEY KNOX LIBRARY ifornia ELECTROMAGNETIC PUMPS FOR LIQUID METALS ***** Alejandro U. Gutierrez and Clair E. Heckathorn ELECTROMAGNETIC PUMPS FOR LIQUID METALS by Alejandro U. Gutierrez Lieutenant Junior Grade, Chilean Navy and Clair E. Heckathom Lieutenant, United States Navy Submitted in partial fulfillment of the requirements for the degree of MASTER OF SCIENCE IN ELECTRICAL ENGINEERING United States Naval Postgraduate School Monterey, California 19 6 5 ELECTRON GNETIC PUMPS FOR LIQUID METALS by Alejandro U. Gutierrez and Clair E. Heckathorn This work is accepted as fulfilling the thesis requirements for the degree of MASTER OF SCIENCE IN ELECTRICAL ENGINEERING from the United States Naval Postgraduate School ABSTRACT This thesis is the result of a literary research on the subject of electromagnetic pumps for liquid metals. The research was conducted at the U. S. Naval Postgraduate School to educate the authors in the field oi" electromagnetic pimps and to fulfill requirements for a Master of Science Degree i n Electrical Engineering. This thesis which is a synopsis or' information obtained from various technical publications is designed to give the reader information on the theory and design of electromagnetic pumps in general. Included are: (I) Description of operation of all types of conduction and induction pumps (?) The development of the DC conduction pump from the equivalent circuit. -
Electromagnetic Pump
Acta Scientific Applied Physics Volume 2 Issue 3 August 2021 Review Article Electromagnetic Pump Bahman Zohuri* Received: June 19, 2021 Galaxy Advanced Engineering, Chief Executive Officer (CEO), Albuquerque, New Published: July 09, 2021 Mexico, USA Bahman Zohuri. *Corresponding Author: Bahman Zohuri, Galaxy Advanced Engineering, Chief © All rights are reserved by Executive Officer (CEO), Albuquerque, New Mexico, USA. Abstract An electromagnetic pump is a pump that moves liquid in form of metal in particular, any electrically conductive liquid using electromagnetism phenomena. By law of physics of electromagnetic, a magnetic field can be defined as a set at right angles to the direction the liquid moves in, while a current is passing through it as well. This events, induce an electromagnetic force for the movements of the liquid. Applications of electromagnetic pump is including pumping liquid metal through any cooling system that areKeywords: installed inside of liquid metal container in particular. Electromagnetic; Pump; Liquid; Heat Transfer; Neutronic; Electric Current; Pumping Liquid Metal Introduction Electromagnetic Pumps are passive pump system and have Sodium is used as a coolant in fast breeder reactors because of a fairly good conductor of electricity also and this has led to de- - its excellent neutronic and heat transfer characteristics. Sodium is - velopment of many electromagnetic sensors and devices for use in been integrated in use for pumping liquid sodium in auxiliary cool ing circuits such as fill and drain from the container of such metal - lic liquid, and purification circuits of sodium cooled fast breeder liquid sodium. One such device is the electromagnetic pump which nuclear reactors, such as Liquid Metal Fast Breeder Reactor (LMF is used to pump liquid sodium in auxiliary circuits of a fast reactor BR). -
An MHD Study of the Behavior of an Electrolyte Solution Using3d
An MHD Study of the Behavior of an Electrolyte Solution using3D Numerical Simulation and Experimental results Luciano Pires Aoki*1, Harry Edmar Schulz1, Michael George Maunsell1 1University of São Paulo – School of Engineering at São Carlos, São Paulo, Brazil *Corresponding author: Av. Trabalhador São Carlense 400 (São Carlos, S.P.), Brazil, 13566-590 [email protected] Abstract: This article considers a closed water The electromagnetic pumping (EMP) of an circuit with square cross section filled with an electrically conductive fluid described in the electrolyte fluid. The conductor fluid was moved present study uses a direct current (DC) MHD using a so called electromagnetic pump, or EMP, device. Williams [2] described this concept in in which a permanent magnet generates a 1930, applying it to pump liquid metals in a magnetic field and electrodes generate the channel. In the DC EMP used in this study, a electric field in the flow. Thus, the movement is direct current was applied across a rectangular a consequence of the magnetohydrodynamic (or section of the closed channel filled with salt MHD) effect. The model adopted here was water, and submitted to a non-uniform magnetic derived from the Navier-Stokes equations for field perpendicular to the current. The Newtonian incompressible fluid using the k- interactions between current and magnetic fields ε turbulence model and coupled with the produced electromagnetic forces or Lorentz Maxwell equations. The equations were solved forces, driving the fluid through the channel. The using COMSOL Multiphysics® version 3.5a EMP is of growing interest in many industrial (2008). The 3D numerical simulations allowed applications, requiring precise flow controls, obtaining realistic predictions of the Lorentz enabling to induce flow deviations without forces, the current densities, and the movement mechanical moving parts or devices [3]. -
The Optimum Design Analysis of the Small DC Electromagnetic Pump with Loop-Supported Type
Transactions of the Korean Nuclear Society Autumn Meeting Pyeongchang, Korea, October 30-31, 2014 The Optimum Design Analysis of the Small DC Electromagnetic Pump with Loop-Supported Type Geun Hyeong Lee* and Hee Reyoung Kim Ulsan National Institute of Science and Technology, Ulsan 689-798, Republic of Korea *Corresponding author: [email protected] 1. Introduction Actually, the liquid sodium flows through the duct with the stainless steel as represented in Fig. 2, and so Electromagnetic pumps have been employed to the the resistance by it should be considered. Applying liquid metal experiments including transportation of Kirchhoff’s law for the circuit and balancing the electric liquid sodium in a sodium fast reactor (SFR). Recently, input and hydraulic output, the relation between the the approach to the heat exchange between sodium and input current and developed pressure including carbon dioxide, which is known to be less reactive with geometric variables was obtained in the Eq. (1). sodium than water, is being attempted in Korea. In the present study, the conceptual design of the DC ( ) electromagnetic (EM) pump, which has the flowrate of 3L/min and the developed pressure of 0.2 bar in the temperature of 500 , for circulating liquid sodium in Where the test loop for sodium-carbon dioxide reaction experiment is carried out. 2. Analysis { } The DC electromagnetic pump is divided into liquid sodium fluid with the high electrical conductivity, metal duct, magnet and electrode for generating electromagnetic force as shown in Fig.1. In Eq. (1), the input current is calculated on the change of the variables such as the length, width and height of the pump under the requirement of the flowrate of 3L/min and the developed pressure of 0.2bar. -
Electromagnetic Pump
^ ^ ^ ^ I ^ ^ ^ ^ ^ ^ II ^ II ^ ^ ^ ^ ^ ^ ^ ^ ^ ^ ^ ^ ^ I ^ European Patent Office Office europeen des brevets EP 0 711 025 A2 EUROPEAN PATENT APPLICATION (43) Date of publication: (51) |nt Cl.e: H02K 44/06 08.05.1996 Bulletin 1996/19 (21) Application number: 95307404.4 (22) Date of filing: 18.10.1995 (84) Designated Contracting States: • Dahl, Leslie Roy DE FR GB IT Livermore, California 94450 (US) • Patel, Mahadeo Ratilal (30) Priority: 04.11.1994 US 334644 San Jose, California 95111 (US) (71) Applicant: GENERAL ELECTRIC COMPANY (74) Representative: Pratt, Richard Wilson et al Schenectady, NY 12345 (US) London Patent Operation G.E. International Inc., (72) Inventors: Essex House, • Fanning, Alan Wayne 1 2/1 3 Essex Street San Jose, California 95112 (US) London WC2R 3AA (GB) • Olich, Eugene Ellsworth Aptos, California 95003 (US) (54) Electromagnetic pump (57) A support structure for clamping the inner coils and inner lamination rings of an inner stator column of an electromagnetic induction pump to prevent damag- ing vibration. A spine assembly, including a base plate, a center post and a plurality of ribs, serves as the struc- tural frame for the inner stator. Stacked alignment rings provide structure to the lamination rings and locate them concentrically around the spine assembly central axis. The alignment rings are made of a material having a high thermal expansion coefficient to compensate for the lower expansion of the lamination rings and, overall, provide an approximate match to the expansion of the inner flow duct. The net result is that the radial clamping provided by the duct around the stator iron is maintained (approximately) over a range of temperatures and op- erating conditions. -
Observations of Plasma Stimulated Electrostatic Sideband
CHINMOY MALLICK et.al OBSERVATIONS OF PLASMA STIMULATED ELECTROSTATIC SIDEBAND EMISSION AND HARMONIC DISTORTION: EVIDENCES OF OVER-DENSE PLASMA GENERATION INSIDE A MICROWAVE DISCHARGE ION SOURCE CHINMOY MALLICK Institute for Plasma Research, HBNI, Bhat, Gandhinagar, India E-mail: [email protected] MAINAK BANDYOPADHYAY ITER-India, Institute for Plasma Research, HBNI, Bhat, Gandhinagar, India RAJESH KUMAR Institute for Plasma Research, HBNI, Bhat, Gandhinagar, India Abstract Microwave discharge ion source (MDIS) is used in many applications including accelerators based neutron generators on suitable target through D-D or D-T fusion. In this device, the electromagnetic (EM) pump wave ( ) can propagate through plasma beyond cut-off plasma density by changing its polarity and/or decomposing into different daughter waves through which it transfer its energy and produces over dense plasma. In the present experiment, the plasma stimulated emission spectra was measured in the frequency range 0.5 to 3 to understand the different probable energy decay channels role; e.g. Electron Bernstein waves (EBWs), Ion cyclotron waves (ICWs), Lower hybrid oscillations (LHOs), Ion Bernstein waves (IBWs) and Ion Acoustic Waves (IAWs) etc. Present experimental device, MDIS contains eight distinct cavity modes under vacuum conditions (also called vacuum mode) within 300 MHz bandwidth around pump wave ( ) of the launched MW. Some of these vacuum modes are found to match with the plasma induced modes (plasma mode) and depends on the different plasma loading conditions. Resonant interaction between these two types of modes (vacuum mode and plasma mode) leads to the parametric decay into another lower frequency microwave and also electrostatic ion/electron type waves. -
Zero Emissions Power Cycles
Zero Emissions Power Cycles © 2009 by Taylor & Francis Group, LLC 87916_Book.indb 1 3/26/09 12:17:17 PM Zero Emissions Power Cycles E. Yantovsky J. Górski M. Shokotov Boca Raton London New York CRC Press is an imprint of the Taylor & Francis Group, an informa business © 2009 by Taylor & Francis Group, LLC 87916_Book.indb 3 3/26/09 12:17:17 PM CRC Press Taylor & Francis Group 6000 Broken Sound Parkway NW, Suite 300 Boca Raton, FL 33487-2742 © 2009 by Taylor & Francis Group, LLC CRC Press is an imprint of Taylor & Francis Group, an Informa business No claim to original U.S. Government works Printed in the United States of America on acid-free paper 10 9 8 7 6 5 4 3 2 1 International Standard Book Number-13: 978-1-4200-8791-8 (Hardcover) This book contains information obtained from authentic and highly regarded sources. Reasonable efforts have been made to publish reliable data and information, but the author and publisher can- not assume responsibility for the validity of all materials or the consequences of their use. The authors and publishers have attempted to trace the copyright holders of all material reproduced in this publication and apologize to copyright holders if permission to publish in this form has not been obtained. If any copyright material has not been acknowledged please write and let us know so we may rectify in any future reprint. Except as permitted under U.S. Copyright Law, no part of this book may be reprinted, reproduced, transmitted, or utilized in any form by any electronic, mechanical, or other means, now known or hereafter invented, including photocopying, microfilming, and recording, or in any information storage or retrieval system, without written permission from the publishers.